Pó de ligas de ferro refere-se a formas de metalurgia do pó de ferro misturado com elementos de liga como níquel, cromo, manganês e carbono. A metalurgia do pó de ferro permite a fabricação de peças e componentes com densidade, porosidade, resistência, propriedades magnéticas e outras propriedades controladas por meio da compactação e sinterização de misturas de pó à base de ferro.
Visão geral das ligas de ferro em pó
Os pós de liga de ferro oferecem várias vantagens em relação às formas convencionais de ferro e aço:
- Alta precisão dimensional e repetibilidade com recursos quase em forma de rede
- Capacidade de obter porosidade e densidades controladas
- Custos de fabricação mais baixos devido à redução da usinagem
- Alta utilização de material com menor geração de resíduos
- Capacidade de produção em massa de peças complexas
O pó de liga de ferro está normalmente disponível em ferro puro, aços de baixa liga, aços para ferramentas, aços inoxidáveis e ligas magnéticas macias, conforme descrito abaixo:
Tipos de pós de liga de ferro
Tipo de pó | Elementos de liga | Características | Formulários |
---|---|---|---|
Ferro puro | Carbono < 0,008%, Oxigênio | Alta resistência verde, baixo custo | Automotivo, maquinário |
Aços de baixa liga | C, Mn, Si, Cr, Mo | Maior resistência e temperabilidade | Automotivo, petróleo/gás |
Aços para ferramentas | C, W, Mo, V, Co | Alta dureza, resistência ao desgaste | Ferramentas de corte, matrizes |
Aços inoxidáveis | Cr, Ni, Mo | Resistência à corrosão, força | Válvulas, marítimas |
Magnético macio | Ni, Mo, Cu, Nb | Alta permeabilidade, baixa perda | Eletroímãs, motores |
Características do pó de liga de ferro
As propriedades do pó de liga de ferro podem ser personalizadas com a seleção de elementos de liga e condições de processamento adequados:
Parâmetro | Características | Método de controle |
---|---|---|
Composição | Elementos de liga, resíduos | Método de produção de pó |
Tamanho da partícula | Fino, ultrafino, microfino | Atomização de gás/água, moagem |
Forma da partícula | Irregular, esférico, escamoso | Atomização de gás/água, condições |
Pureza | Níveis de oxigênio, nitrogênio e carbono | Recozimento, atmosferas protetoras |
Densidade aparente | Densidade verde, densidade sinterizada | Pressão de compactação, sinterização |
Porosidade | Poros abertos e fechados | Compactação, composição da liga |
Área de superfície | Área de superfície específica | Distribuição do tamanho das partículas |
Aplicações do pó de liga de ferro
O pó de liga de ferro é utilizado em uma ampla variedade de aplicações nos seguintes setores:
Setor | Formulários | Exemplo de componentes |
---|---|---|
Automotivo | Engrenagens, rolamentos, filtros, peças do motor | Bielas, eixos de comando de válvulas, anéis de pistão |
Aeroespacial | Peças estruturais, componentes de aeronaves e turbinas | Trem de pouso, discos de turbina, fixadores |
Maquinário | Peças de desgaste, componentes de ferramentas, sistemas de acionamento | Buchas, eixos, cames, polias |
Elétrica | Núcleos magnéticos macios, rotores, peças de motores elétricos | Transformadores, indutores, estatores, rotores |
Consumidor | Peças de fechaduras, lâminas de barbear, ímãs | Cadeados, conjuntos magnéticos |
Médico | Instrumentos cirúrgicos, implantes, dispositivos | Bisturis, implantes ortopédicos, máquinas de ressonância magnética |
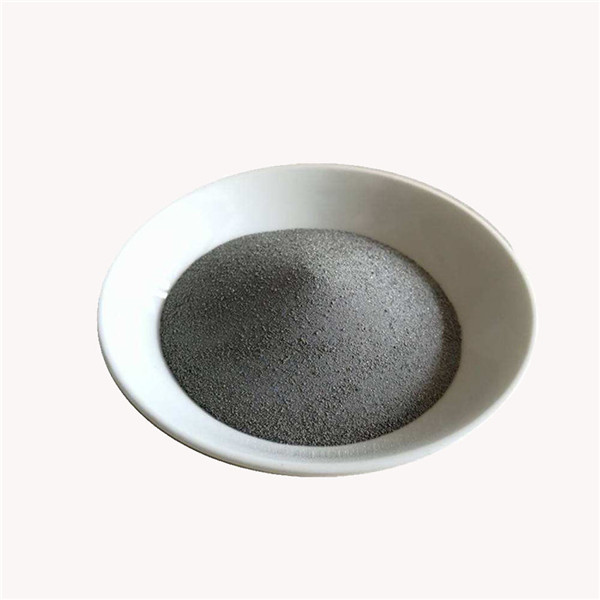
Especificações e padrões de projeto
As peças em pó de liga de ferro devem estar em conformidade com as especificações de composição, propriedades mecânicas, dimensões, acabamento de superfície e métodos de teste. As normas importantes incluem:
Padrão | Descrição |
---|---|
ISO 4492 | Pós metálicos - Testes de flexibilidade e dureza |
ISO 2738 | Materiais metálicos sinterizados - Peças de teste de tração |
ISO 3995 | Pós metálicos - Determinação da resistência verde |
ISO 4490 | Medição da densidade aparente de pós metálicos |
Padrões MPIF | Padrões de materiais, métodos de teste publicados pela Metal Powder Industries Federation |
ASTM B783 | Especificação de peças de metalurgia do pó (PM) à base de ferro |
Os padrões mínimos para o pó fornecido são pureza, distribuição do tamanho das partículas, densidade aparente e taxa de fluxo. Para componentes acabados, existem especificações de densidade, propriedades mecânicas, energia de impacto, dureza, usinabilidade, resistência à corrosão e propriedades magnéticas.
Os padrões de projeto fornecem diretrizes sobre fatores como tolerâncias dimensionais, acabamento de superfície, tolerância de flash, espessura da seção, raios de filete, colocação de nervuras e espessura da parede. As regras para o projeto de peças de metal em pó estão definidas na Norma MPIF 35.
Fabricação e processamento de pós
O processo de fabricação de pó de liga de ferro tem as seguintes etapas principais:
Produção de pó
O pó de liga de ferro pode ser produzido por meio de:
- Atomização - Derreter a liga e desintegrar o fluxo fundido em gotículas finas usando jatos de gás ou água. O pó atomizado a gás tem partículas esféricas ideais para prensagem.
- Fresagem mecânica - Soldagem a frio, fratura e ressoldagem repetidas da matéria-prima em moinhos de bolas de alta energia. Produz pó fino com formato irregular.
- Eletrólise - Deposição eletrolítica de pós de ferro a partir de soluções aquosas.
- Redução - Redução química de pós de óxido de ferro a ferro usando hidrogênio ou gás monóxido de carbono.
- Outros métodos - Decomposição de carbonila, atomização rotativa, atomização por plasma, condensação de vapor.
Método | Forma da partícula | Tamanho da partícula | Pureza | Custo |
---|---|---|---|---|
Atomização de gás | Esférico | 15 - 150 μm | Alta | Alta |
Atomização de água | Irregular | 150 - 300 μm | Médio | Baixa |
Fresagem mecânica | Escamoso | 1 - 100 μm | Baixa | Médio |
Mistura de pós
O pó de ferro básico é misturado com elementos de liga, lubrificantes e agentes de fluxo de acordo com a composição final da liga necessária. A mistura de pó é homogeneizada em um misturador para obter uma composição uniforme.
Compactação
A compactação pressiona a mistura de pó em uma cavidade de matriz sob altas pressões para produzir um compacto verde com o formato desejado. Os métodos comuns de compactação incluem:
- Pressionamento de ação única: Simples, de baixo custo, adequado para baixas taxas de produção. Pressões de até 600 MPa.
- Prensagem de ação dupla: O pó é comprimido a partir de punções superiores e inferiores. Pressões de até 1000 MPa. Melhor uniformidade da peça.
- Prensagem isostática: Pressão uniforme aplicada em todas as superfícies em um fluido. Formas complexas, densidades uniformes. Requer encapsulamento.
- Compactação por rolo: O pó é comprimido entre dois rolos para formar uma folha. A folha é granulada para ser prensada. Melhora o fluxo de pó.
Sinterização
A sinterização densifica o compacto por meio do aquecimento abaixo do ponto de fusão para induzir a ligação entre as partículas. A sinterização ativa processos de difusão que eliminam os poros e aumentam a resistência. A sinterização é feita em atmosferas controladas para evitar a oxidação.
Operações secundárias
Operações adicionais como cunhagem, recalque, infiltração, usinagem e tratamento de superfície são usadas para obter a geometria final da peça e as propriedades exigidas pela aplicação.
Instalação, operação e manutenção
As diretrizes a seguir se aplicam a prensas de pó e fornos de sinterização:
- Instale o equipamento em fundações planas e sem vibrações, de acordo com as especificações do fabricante
- Nivele o aríete e o suporte do equipamento de prensagem para evitar compactação irregular
- Garantir a lubrificação adequada de prensas e punções de acordo com o manual de operação
- Configure sistemas adequados de ventilação de exaustão e resfriamento
- Calibrar sensores de temperatura, controladores e dispositivos de registro em fornos
- Use gases inertes, como nitrogênio ou amônia dissociada, para minimizar a oxidação
- Desenvolver cronogramas e procedimentos para manutenção preventiva de equipamentos
- Inspecione regularmente as ferramentas de prensagem e os punções quanto a desgaste, rachaduras ou danos
- Verifique periodicamente o isolamento do forno e os elementos de aquecimento
- Validar processos rotineiramente para garantir aquecimento uniforme e conformidade com os padrões
- Treinar os operadores em procedimentos operacionais adequados, precauções de segurança e verificações de qualidade
- Siga as diretrizes do fabricante para inspeções, lubrificação, ajustes e reparos do equipamento
- Manter registros de todas as atividades de manutenção de equipamentos e dados de produção de peças
Escolha de um fornecedor de pó de liga de ferro
Os principais fatores na seleção de um fornecedor de pó de liga de ferro são:
Parâmetro | Descrição |
---|---|
Qualidade do pó | Química, formato da partícula, distribuição de tamanho, pureza |
Faixa de composição | Variedade de classes de materiais e sistemas de ligas |
Recursos de fabricação | Atomização, moagem, mistura, peneiramento, secagem |
Instalações de teste | Para análise química, tamanho de partícula, densidade verde, propriedades sinterizadas |
Certificações de qualidade | ISO 9001, IATF 16949, AS9100, ISO 13485 |
Conhecimento técnico | Conhecimento de ligas, entradas de design de peças, engenharia de aplicação |
Suporte ao cliente | Capacidade de resposta a solicitações, gerenciamento de projetos |
Entrega | Registro de entrega no prazo, flexibilidade de quantidade |
Localização | Proximidade das operações para reduzir os prazos de entrega |
Preços | Competitividade, descontos por volume, estabilidade |
Os fornecedores devem fornecer certificados de análise detalhando a composição, a distribuição do tamanho das partículas, a densidade aparente e a análise da peneira. Eles devem ter equipes técnicas para colaborar no projeto da peça e na seleção do pó. O processo e os controles de qualidade do fornecedor devem garantir a consistência de lote para lote do pó.
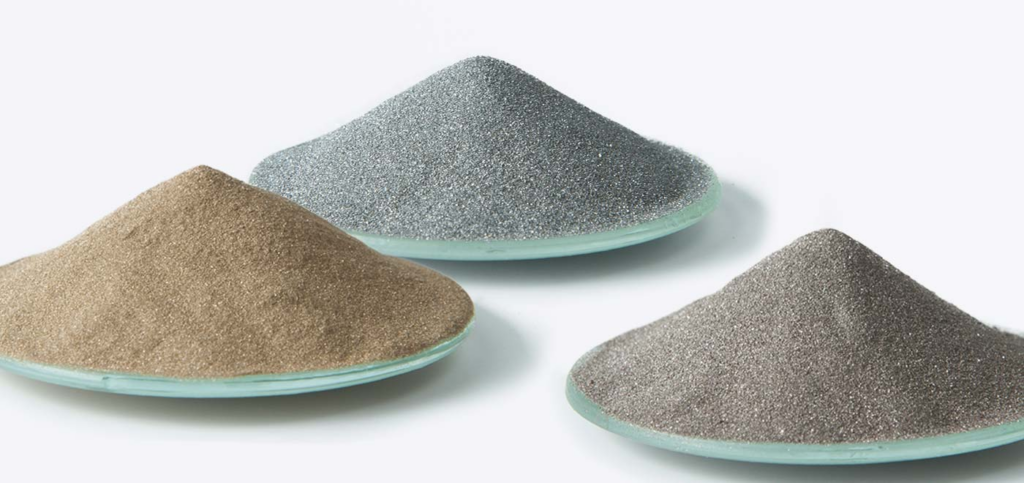
Prós e contras da metalurgia do pó
Vantagens | Desvantagens |
---|---|
Forma quase líquida, usinagem mínima | Resistência limitada do material em comparação com as ligas forjadas |
Boa precisão dimensional | Limitações de tamanho com base na capacidade da prensa |
Geometrias complexas viáveis | Restrições quanto à complexidade da forma, espessura da parede |
Econômico para produção em massa | Operações secundárias aumentam o custo para volumes menores |
Ampla gama de ligas disponíveis | Propriedades anisotrópicas devido à prensagem |
Mínimo desperdício em comparação com a usinagem | É necessária a sinterização em atmosfera controlada |
Menor consumo de energia do que a usinagem de metais | Investimento de capital para produção de pó |
Controle de porosidade para filtros, rolamentos | Necessidade de experiência em manuseio e mistura de pós |
Perguntas frequentes
P: Quais são os diferentes graus de pó de ferro disponíveis?
R: As principais classes incluem ferro puro, aços de baixa liga, aços para ferramentas, aços inoxidáveis e ligas magnéticas macias. Cada um tem composições específicas adaptadas para propriedades mecânicas, magnéticas ou outras.
P: Qual distribuição de tamanho de partícula é ideal para a prensagem de pó de ferro?
R: É preferível uma faixa de tamanho de partícula de 15 a 150 μm, com a maioria entre 45 e 75 μm. O pó mais fino empacota melhor, mas pode ter baixo fluxo para o preenchimento da matriz. O pó mais grosso tem bom fluxo, mas afeta a densificação.
P: Como melhorar as propriedades de fluxo do pó para prensagem?
R: A adição de lubrificantes como estearato de zinco ou etileno bis-estearamida em 0,5-1% melhora a taxa de fluxo do pó. O recozimento do pó ou o uso de pó atomizado esférico também melhora o fluxo.
P: O que causa rachaduras em peças de ferro sinterizado?
R: Partículas grandes, ampla distribuição de partículas, alto teor de liga, altas taxas de aquecimento/resfriamento e seções espessas podem causar defeitos de rachadura durante a sinterização. É necessário otimizar a composição, as características do pó, o projeto da peça e o ciclo de sinterização.
P: O que afeta a tolerância dimensional das peças de metal em pó?
R: Os principais fatores são o desgaste da matriz, o retorno elástico após a prensagem, a uniformidade da temperatura de sinterização, a geometria da peça, as operações secundárias e a usinagem final. Os controles de processo e o projeto da matriz são essenciais.
P: Como melhorar a resistência ao desgaste dos componentes da metalurgia do pó de ferro?
R: Aumentar a dureza por meio de liga com carbono, cromo, molibdênio, vanádio, tungstênio ou por impregnação. A menor porosidade e a maior densificação também melhoram a resistência ao desgaste.
P: Qual é o benefício da infiltração de cobre em peças de ferro?
R: O cobre fundido preenche a porosidade interna por ação capilar, melhorando a resistência, o módulo de elasticidade, a energia de impacto, a vida útil à fadiga e a condutividade elétrica.
P: Os pós de aço inoxidável podem ser processados como os pós de aço para ferramentas?
R: Não, o aço inoxidável requer atmosferas protetoras durante a compactação e a sinterização para evitar a oxidação. Os parâmetros de processamento devem ser otimizados separadamente.
P: O que causa a alteração dimensional durante a sinterização?
R: Os principais motivos são o encolhimento à medida que os poros se fecham, as transformações de fase que causam mudanças de volume e a distribuição não uniforme da temperatura que leva à distorção. A configuração adequada do forno e a seleção do ciclo de sinterização são necessárias para minimizar a alteração dimensional.