Impressão 3D do Inconel 625 é uma liga de níquel-cromo-molibdênio com excelente resistência a altas temperaturas e à corrosão. Isso a torna adequada para a impressão 3D de geometrias complexas para aplicações exigentes. Este guia fornece uma visão geral da composição, propriedades, parâmetros e usos do Inconel 625 impresso em 3D.
Introdução à impressão 3D em inconel 625
O Inconel 625 é uma superliga de alto desempenho frequentemente usada para manufatura aditiva nos setores aeroespacial, marítimo, nuclear e químico. As principais propriedades incluem:
Tabela 1: Visão geral do material Inconel 625 impresso em 3D
Propriedades | Detalhes |
---|---|
Conteúdo de níquel | 58-63% |
Alta resistência | Resistência à tração 1.310 MPa |
Resistência à temperatura | Até 1.400°F ou 760°C |
Resistência à corrosão | Altamente resistente ao calor, ácidos e alcalinos |
Resistência a rachaduras | Excelente resistência à fadiga e tenacidade |
Capacidade de trabalho | Prontamente soldável para união |
Usos comuns | Aplicações aeroespaciais, marítimas e industriais |
A impressão 3D permite a fabricação de peças complexas de Inconel 625 que não podem ser obtidas com métodos tradicionais. Continue lendo para obter detalhes sobre a composição, as características, os parâmetros do processo de impressão, as aplicações e muito mais.
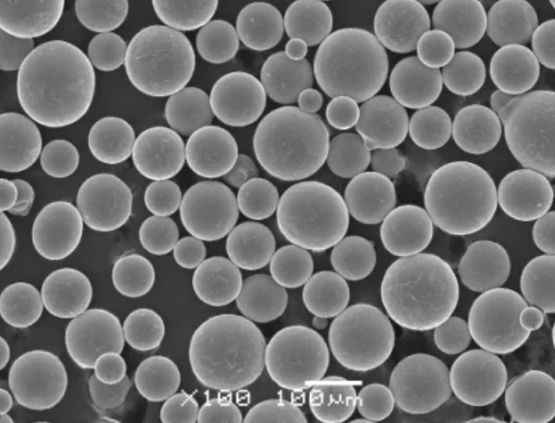
Composição química do inconel 625 para impressão 3D
A química da liga Inconel 625 inclui níquel, cromo, molibdênio, nióbio e ferro:
Tabela 2: Composição da liga Inconel 625
Elemento | Peso % |
---|---|
Níquel (Ni) | 58.0 – 63.0 % |
Cromo (Cr) | 20.0 – 23.0 % |
Molibdênio (Mo) | 8.0 – 10.0 % |
Nióbio (Nb) | 3.15 – 4.15 % |
Ferro (Fe) | Restante |
Carbono (C) | ≤ 0.10% |
Manganês (Mn) | ≤ 0,50 por cento |
Silício (Si) | ≤ 0,50 por cento |
Fósforo (P) | ≤ 0.015%. |
Enxofre (S) | ≤ 0.015%. |
Alumínio (Al) | ≤ 0,40 por cento |
Titânio (Ti) | ≤ 0,40 por cento |
Cobalto (Co) | ≤ 1.0% |
Essa matriz de níquel-cromo cuidadosamente otimizada oferece uma combinação excepcional de resistência ao calor e à corrosão, mantendo a ductilidade, a resistência à fadiga e a soldabilidade.
Propriedades mecânicas do Inconel 625 impresso em 3D
As propriedades mecânicas do Inconel 625 o tornam adequado para aplicações exigentes:
Tabela 3: Propriedades mecânicas do Inconel 625
Propriedade | Valor |
---|---|
Densidade | 8,44 g/cm3 |
Ponto de fusão | 2.300-2.460°F (1.260-1.350°C) |
Resistência à tração | 125.000 - 240.000 psi |
Resistência ao escoamento (recozido) | 110.000 psi min |
Alongamento | 30% no mínimo |
Módulo de Young | 29 x 10^6 psi |
Índice de Poission’s | 0.29 |
Resistência à fadiga | 110 - 129 ksi |
Resistência à fratura | 200 ksi√in |
Dureza | ~35 HRC |
A combinação de força, resistência a rachaduras, propriedades térmicas e resistência à corrosão permite que o Inconel 625 resista a ambientes extremos.
Principais benefícios do Inconel 625 para impressão 3D
O Inconel 625 impresso em 3D oferece grandes vantagens:
Tabela 4: Vantagens de Impressão 3D do Inconel 625 peças
Benefícios | Descrição |
---|---|
Alta relação resistência/peso | Tão resistente quanto o aço com uma fração do peso, economizando custos |
Resiste a temperaturas extremas | Mantém as propriedades mecânicas de criogênico a 1.400°F |
Resistência à corrosão | Excelente resistência química a ácidos e soluções alcalinas de até 1.400°F |
Resistência a rachaduras | A alta resistência à fadiga resiste à falha por fratura |
Estabilidade térmica | O baixo coeficiente de expansão térmica evita a distorção |
Seguro para alimentos | Aprovado para equipamentos de processamento de alimentos sem lixiviação |
Ligas personalizadas | Pode personalizar os produtos químicos de acordo com os requisitos da aplicação |
Geometrias complexas | Imprima formas complexas que não podem ser obtidas com a fabricação |
Montagens consolidadas | Imprima montagens complexas sem soldagem, reduzindo os custos |
Iteração rápida | Projetar, testar e adaptar peças por meio de protótipos rápidos |
Essas vantagens ampliam as possibilidades de design e permitem componentes mais leves, resistentes e duradouros.
Parâmetros de impressão 3D recomendados para Inconel 625
Aqui estão os parâmetros típicos do processo de impressão de peças de Inconel 625 em sistemas de fusão de leito de pó a laser e de deposição de energia direcionada:
Tabela 5: Parâmetros de impressão 3D padrão do Inconel 625
Parâmetro | Valor típico |
---|---|
Espessura da camada | 20 - 100 mícrons |
Potência do laser | Até 500 W |
Velocidade de digitalização | 800 - 1200 mm/s |
Diâmetro do feixe | 50 – 200 mícrons |
Tamanho do pó | 15 - 45 mícrons |
Orientação da impressão | Ângulos de 45° |
Estruturas de suporte | Obrigatório |
Recozimento | Opcional 2.100 - 2.300°F por 2 horas |
As configurações devem equilibrar a densidade com as tensões residuais. Seguir métodos estabelecidos, como o ASTM F3056, minimiza rachaduras e distorções. A seguir, vamos dar uma olhada em aplicações comuns.
Aplicações de peças de Inconel 625 impressas em 3D
Os usos comuns do Inconel 625 fabricado de forma aditiva em todos os setores incluem:
Tabela 6: Aplicações de impressão 3D do Inconel 625
Setor | Formulários | Componentes |
---|---|---|
Aeroespacial | Suportes estruturais, componentes do motor, sistemas hidráulicos | Lâminas de turbina, bicos de foguete, coletores de escapamento, elementos de combustível |
Petróleo e gás | Ferramentas de fundo de poço, válvulas, sistemas de cabeça de poço | Bits de perfuração, ferramentas de linha de arame, árvores de Natal |
Automotivo | Turbocompressores, componentes de escapamento | Coletor, carcaça do rotor do superalimentador, impulsores do turbo |
Processamento químico | Trocadores de calor, vasos de reação, acessórios para tubos | Carretéis e cotovelos de tubulação, lâminas de mistura, equipamentos de processo |
Alimentos e produtos farmacêuticos | Misturadores, secadores, aquecedores, transportadores | Rolamentos, eixos, fixadores, conectores |
Marinha | Componentes de propulsão, sistemas de dessalinização | Bombas, impulsores, acoplamentos, válvulas |
Geração de energia | Trocadores de calor, componentes do sistema de vapor | Cabeçotes, tubulação do superaquecedor, tubos do condensador |
A impressão 3D permite peças de Inconel 625 mais leves, mais resistentes e personalizadas, consolidando montagens complexas em aplicações exigentes, impulsionando a adoção em sistemas críticos.
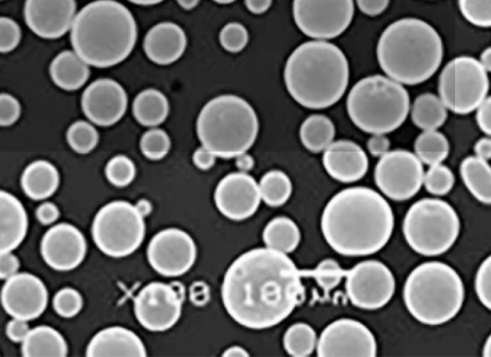
Opções de material para impressão 3D de Inconel 625
As opções populares de liga Inconel 625 para manufatura aditiva incluem:
Tabela 7: Comum Impressão 3D do Inconel 625 formatos de material
Tipo | Descrição | Principais propriedades |
---|---|---|
Inconel 625 padrão | Grau mais amplamente usado para aditivos | Resistência à tração de 1050 MPa, resistência à ruptura de 760 MPa a 980°C |
Inconel 625 Ultra | Maior densidade e ductilidade | Aumento de 30% no rendimento e na resistência à tração |
Inconel 718 | Grau aeroespacial resistente ao calor | Excelente resistência e dureza >540°C |
Ligas 625 personalizadas | Química personalizada para aplicações específicas | Aumento da emissividade, condutividade, magnetismo etc. |
Os pós especializados de Inconel otimizam o formato, o tamanho e a química das partículas para aumentar o sucesso da impressão 3D.
Padrões de impressão 3D Inconel 625
Principais padrões para a qualificação de peças e pós de Inconel 625 impressos em 3D:
Tabela 8: Padrões de impressão 3D da liga Inconel 625
Padrão | Descrição |
---|---|
ASTM F3056 | Especificação padrão para fabricação aditiva de liga de níquel |
ASTM B946 | Padrão para detecção de defeitos |
AMS 2801 | Tratamento térmico de ligas de níquel |
AMS 5662 | Requisitos do processo de fusão de leito de pó a laser |
ISO/ASTM 52900 | Princípios gerais de projeto e fabricação |
A certificação de componentes Inconel impressos de acordo com essas especificações garante alta qualidade e confiabilidade para o serviço.
Fornecedores de Inconel 625 para impressão 3D
Os principais fornecedores de pós metálicos de Inconel 625 incluem:
Tabela 9: Fornecedores de pó de Inconel 625
Fornecedor | Descrição | Preços |
---|---|---|
Tecnologia LPW | Ampla gama de ligas, otimização personalizada de partículas | $$$ |
Sandvik Osprey | Pós de liga de níquel padrão e personalizados | $$$ |
Erasteel | Amplo portfólio de materiais de superligas | $$ |
AMG Superalloys Reino Unido | Especializada em ligas de níquel | $-$$ |
Tekna | Processo avançado de esferoidização por plasma | $$$ |
Esses especialistas em ligas premium fazem o ajuste fino do tamanho, da forma, da química e dos defeitos das partículas de Inconel 625 para garantir o sucesso da impressão.
Prós e contras do Inconel 625 impresso em 3D
Tabela 10: Vantagens e limitações da impressão 3D do Inconel 625
Prós | Contras |
---|---|
Suporta variações de temperatura de 1800°F | Mais caro do que o aço ou o alumínio |
Cinco vezes mais resistente a fraturas do que o aço | Requer tratamento térmico para aliviar as tensões |
Metade da densidade do aço | Suscetível a microfissuras sem otimização |
Resiste à corrosão a quente e à corrosão por pite | Superfícies difíceis de imprimir que exigem suportes |
Biocompatível para usos alimentícios e médicos | Limitação de fornecedores e impressoras de grande porte |
Imprimir geometrias complexas consolidando montagens | O pós-processamento pode ser desafiador |
Com boas práticas de processo, os enormes benefícios de desempenho do Inconel 625 impresso em 3D superam os custos mais altos das peças.
Perguntas frequentes
P: O que causa rachaduras na impressão do Inconel 625?
R: Altas tensões de resfriamento causadas por grandes gradientes térmicos levam a rachaduras. Estruturas de suporte adequadas, configurações de processo otimizadas, tratamento pré/pós-aquecimento e relevos de usinagem ajudam a minimizar as rachaduras.
P: O Inconel 625 impresso em 3D requer tratamento térmico?
R: O tratamento térmico opcional alivia as tensões internas, melhorando as propriedades mecânicas e a resistência a rachaduras. O recozimento a 1900-2100°F por 1-3 horas é típico com base na espessura da seção.
P: Que acabamento de superfície pode ser esperado em peças de Inconel 625 impressas?
R: O acabamento da superfície bruta varia de 250 a 500 mícrons Ra, dependendo dos parâmetros de impressão. Usinagem, retificação, polimento ou eletropolimento adicionais podem melhorar os requisitos de acabamento da superfície.
P: É possível soldar Inconel 625 impresso em 3D?
R: Sim, o Inconel 625 pode ser prontamente soldado usando GTAW, feixe de elétrons ou métodos de soldagem a laser para unir montagens impressas em 3D ou modificar componentes. A fixação adequada é fundamental para evitar distorções.