As máquinas VIGA (Vacuum Inert Gas Atomization) se tornaram essenciais na produção de pós metálicos de alta qualidade. Essas máquinas são amplamente utilizadas em vários setores, incluindo aeroespacial, médico e automotivo, graças à sua capacidade de produzir pós metálicos finos e uniformes. Neste guia detalhado, exploraremos todos os aspectos da Máquinas VIGAa VIGA oferece uma visão geral das máquinas VIGA, desde sua visão geral até modelos específicos de pós metálicos, suas aplicações e muito mais. Prepare-se para dar uma olhada em profundidade no mundo das máquinas VIGA!
Visão geral das máquinas VIGA
A atomização a gás inerte a vácuo (VIGA) é um método usado para produzir pós metálicos por meio da atomização de metal fundido em um ambiente controlado. O processo envolve a fusão do metal no vácuo e, em seguida, a atomização usando um gás inerte, como argônio ou nitrogênio. Isso resulta em pós metálicos de alta pureza com excelentes propriedades, tornando-os adequados para vários processos avançados de fabricação.
Principais detalhes da VIGA Machines
- Processo: Fusão e atomização em ambiente de vácuo/gás inerte
- Saída: Pós metálicos esféricos de alta pureza
- Formulários: Manufatura aditiva, metalurgia, metalurgia do pó, tecnologias de revestimento
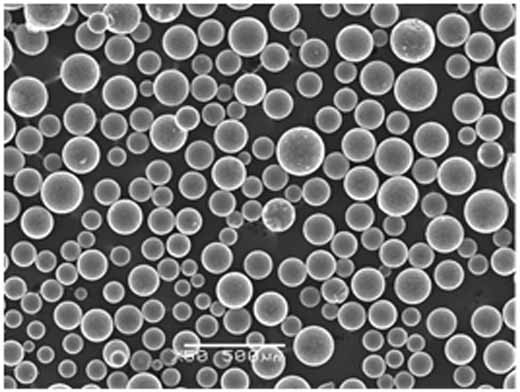
Tipos de pós metálicos produzidos pelas máquinas VIGA
A versatilidade das máquinas VIGA permite que elas produzam uma ampla gama de pós metálicos. Abaixo está uma lista de modelos específicos de pós metálicos produzidos com a tecnologia VIGA, juntamente com descrições detalhadas.
1. Pó de aço inoxidável (316L)
Descrição: O pó de aço inoxidável 316L é conhecido por sua excelente resistência à corrosão e propriedades mecânicas. Ele é amplamente utilizado nos setores médico e aeroespacial.
Características:
- Composição: Ferro, cromo, níquel, molibdênio
- Propriedades: Alta resistência à corrosão, boa resistência mecânica
2. Pó de liga de titânio (Ti-6Al-4V)
Descrição: O Ti-6Al-4V é o pó de liga de titânio mais comumente usado, conhecido por sua alta relação resistência-peso e excelente biocompatibilidade.
Características:
- Composição: Titânio, alumínio, vanádio
- Propriedades: Alta resistência, leve, biocompatível
3. Pó de Inconel (Inconel 718)
Descrição: O pó de Inconel 718 é uma liga de níquel-cromo com excelente força em altas temperaturas e resistência à corrosão, ideal para aplicações aeroespaciais.
Características:
- Composição: Níquel, cromo, ferro, nióbio
- Propriedades: Estabilidade em alta temperatura, resistência à corrosão
4. Pó de liga de alumínio (AlSi10Mg)
Descrição: O pó AlSi10Mg é uma liga de alumínio-silício-magnésio com boa condutividade térmica e propriedades leves, o que o torna adequado para aplicações automotivas e aeroespaciais.
Características:
- Composição: Alumínio, silício, magnésio
- Propriedades: Leve, boa condutividade térmica
5. Pó de liga de cobalto-cromo (CoCrMo)
Descrição: O pó da liga CoCrMo é conhecido por sua excelente resistência ao desgaste e biocompatibilidade, sendo amplamente utilizado em implantes médicos.
Características:
- Composição: Cobalto, cromo, molibdênio
- Propriedades: Alta resistência ao desgaste, biocompatibilidade
6. Pó de liga de cobre (CuCrZr)
Descrição: O pó de CuCrZr é uma liga de cobre-cromo e zircônio com excelente condutividade elétrica e térmica, adequada para aplicações elétricas e térmicas.
Características:
- Composição: Cobre, cromo, zircônio
- Propriedades: Alta condutividade, boa resistência mecânica
7. Pó de aço maraging (18Ni300)
Descrição: O pó de aço Maraging 18Ni300 é conhecido por sua alta resistência e tenacidade, comumente usado nos setores de ferramentas e aeroespacial.
Características:
- Composição: Ferro, níquel, cobalto, molibdênio
- Propriedades: Alta resistência e tenacidade
8. Pó de aço ferramenta (H13)
Descrição: O pó de aço para ferramentas H13 é conhecido por sua alta dureza e resistência ao calor, o que o torna adequado para a fabricação de ferramentas e moldes.
Características:
- Composição: Ferro, cromo, molibdênio, vanádio
- Propriedades: Alta dureza, resistência ao calor
9. Pó de liga de níquel (NiCr8020)
Descrição: O pó NiCr8020 é uma liga de níquel-cromo com excelente resistência à oxidação e estabilidade em alta temperatura, usada em elementos de aquecimento e fornos industriais.
Características:
- Composição: Níquel, cromo
- Propriedades: Resistência à oxidação, estabilidade em altas temperaturas
10. Pó de carboneto de tungstênio (WC-Co)
Descrição: O pó de carboneto de tungstênio é conhecido por sua extrema dureza e resistência ao desgaste, sendo amplamente utilizado em ferramentas de corte e revestimentos resistentes ao desgaste.
Características:
- Composição: Carbeto de tungstênio, cobalto
- Propriedades: Extrema dureza, resistência ao desgaste
Composição e características dos pós metálicos VIGA
Abaixo está uma tabela que resume a composição e as características dos pós metálicos produzidos pela Máquinas VIGA.
Pó metálico | Composição | Propriedades |
---|---|---|
Aço inoxidável 316L | Ferro, cromo, níquel, molibdênio | Alta resistência à corrosão e resistência mecânica |
Ti-6Al-4V | Titânio, alumínio, vanádio | Alta resistência, leveza e biocompatibilidade |
Inconel 718 | Níquel, cromo, ferro, nióbio | Estabilidade em altas temperaturas, resistência à corrosão |
AlSi10Mg | Alumínio, silício, magnésio | Leve, com boa condutividade térmica |
CoCrMo | Cobalto, cromo, molibdênio | Alta resistência ao desgaste, biocompatibilidade |
CuCrZr | Cobre, cromo, zircônio | Alta condutividade, boa resistência mecânica |
18Ni300 | Ferro, níquel, cobalto, molibdênio | Alta resistência e tenacidade |
H13 | Ferro, cromo, molibdênio, vanádio | Alta dureza, resistência ao calor |
NiCr8020 | Níquel, cromo | Resistência à oxidação, estabilidade em altas temperaturas |
WC-Co | Carbeto de tungstênio, cobalto | Extrema dureza, resistência ao desgaste |
Aplicações dos pós metálicos VIGA
Os pós metálicos produzidos pelas máquinas VIGA têm uma ampla gama de aplicações em vários setores. A tabela a seguir destaca algumas dessas aplicações.
Setor | Formulários | Pós metálicos usados |
---|---|---|
Aeroespacial | Componentes do motor, peças estruturais | Ti-6Al-4V, Inconel 718, AlSi10Mg |
Médico | Implantes, próteses | Aço inoxidável 316L, CoCrMo, Ti-6Al-4V |
Automotivo | Peças leves, gerenciamento térmico | AlSi10Mg, CuCrZr |
Ferramentas | Moldes, ferramentas de corte | H13, WC-Co, 18Ni300 |
Elétrica | Componentes condutores, gerenciamento térmico | CuCrZr, NiCr8020 |
Industrial | Elementos de aquecimento, revestimentos resistentes ao desgaste | NiCr8020, WC-Co |
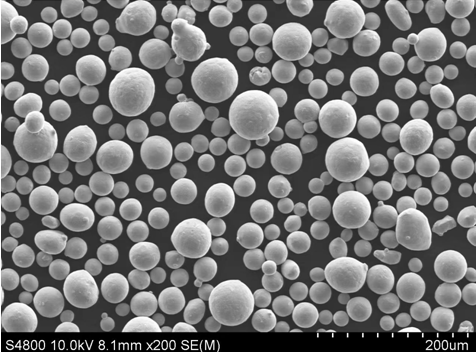
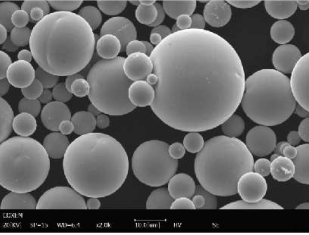
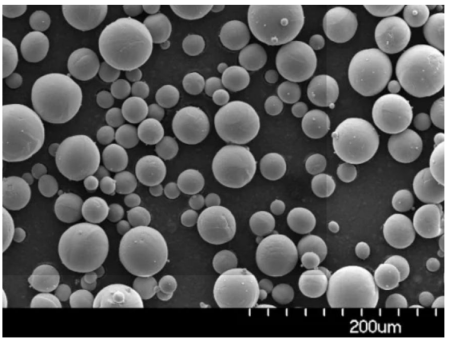
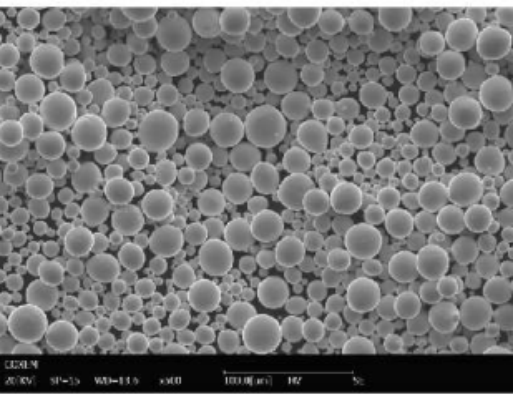
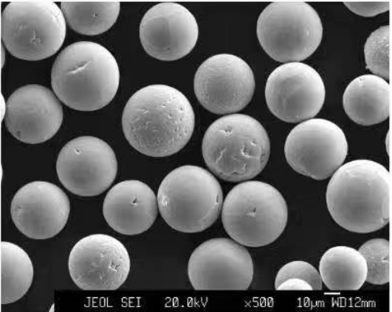
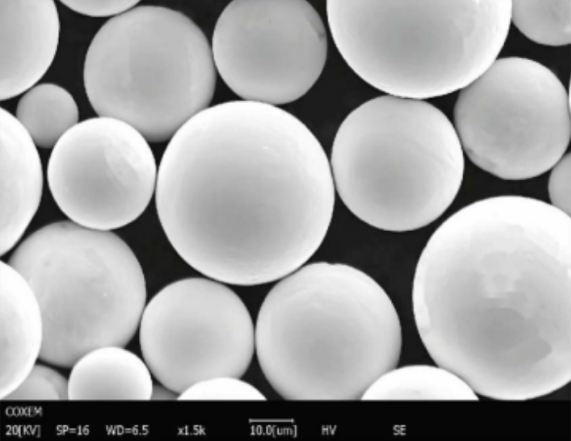
Especificações, tamanhos, classes e padrões
A tabela a seguir fornece especificações, tamanhos, graus e padrões para alguns pós metálicos comumente produzidos pelas máquinas VIGA.
Pó metálico | Faixa de tamanho (µm) | Grau | Padrões |
---|---|---|---|
Aço inoxidável 316L | 10-45 | AISI 316L | ASTM F138, ISO 5832-1 |
Ti-6Al-4V | 15-45 | Grau 5 | ASTM F136, ISO 5832-3 |
Inconel 718 | 15-53 | AMS 5662 | ASTM B637 |
AlSi10Mg | 20-63 | AlSi10Mg | EN AC-43400, ISO 3522 |
CoCrMo | 10-45 | ASTM F75 | ASTM F75, ISO 5832-4 |
CuCrZr | 20-63 | CuCrZr | ASTM B505, DIN 17670 |
18Ni300 | 10-53 | Aço Maraging 300 | AMS 6521 |
H13 | 15-45 | H13 | ASTM A681 |
NiCr8020 | 20-63 | NiCr8020 | ASTM B163, DIN 17742 |
WC-Co | 10-45 | WC-Co | ISO 3327 |
Detalhes de fornecedores e preços
Aqui está uma tabela que lista alguns dos fornecedores e detalhes de preços aproximados para vários pós metálicos produzidos pelas máquinas VIGA.
Pó metálico | Fornecedor | Preço (por kg) | Notas |
---|---|---|---|
Aço inoxidável 316L | Tecnologia Carpenter | $50 – $70 | Descontos para grandes quantidades |
Ti-6Al-4V | AP&C | $200 – $250 | Qualidade premium, grau aeroespacial |
Inconel 718 | Tecnologias de superfície da Praxair | $150 – $200 | Aplicações de alta temperatura |
AlSi10Mg | ECKART | $30 – $50 | Comum na manufatura aditiva |
CoCrMo | Arcam AB | $300 – $350 | Grau de implante médico |
CuCrZr | Aditivo GKN | $40 – $60 | Alta condutividade |
18Ni300 | Höganäs AB | $80 – $100 | Alta resistência, aplicações de ferramentas |
H13 | Tecnologia Carpenter | $70 – $90 | Ferramentas resistentes ao calor |
NiCr8020 | Oerlikon Metco | $100 – $130 | Fornos industriais |
WC-Co | Kennametal | $250 – $300 | Dureza extrema, ferramentas de corte |
Comparação dos prós e contras dos pós metálicos da VIGA
A tabela a seguir compara os prós e os contras de vários pós metálicos produzidos pelas máquinas VIGA.
Pó metálico | Vantagens | Limitações |
---|---|---|
Aço inoxidável 316L | Excelente resistência à corrosão e força mecânica | Custo mais alto em comparação com o aço comum |
Ti-6Al-4V | Alta relação resistência/peso, biocompatibilidade | Caro, difícil de usinar |
Inconel 718 | Resistência a altas temperaturas, resistência à corrosão | Caro, usinabilidade limitada |
AlSi10Mg | Leve, com boas propriedades térmicas | Menor resistência em comparação com outras ligas |
CoCrMo | Resistência ao desgaste, biocompatibilidade | Caro, disponibilidade limitada |
CuCrZr | Excelente condutividade elétrica e térmica | Menor resistência mecânica |
18Ni300 | Alta resistência e tenacidade | Caro, requer manuseio especial |
H13 | Alta dureza, resistência ao calor | Propenso a rachaduras |
NiCr8020 | Resistência à oxidação, estabilidade em altas temperaturas | Caro, disponibilidade limitada |
WC-Co | Extrema dureza, resistência ao desgaste | Muito caro, quebradiço |
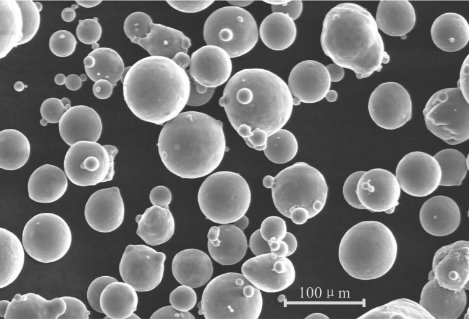
Perguntas frequentes
O que é o processo VIGA?
O processo VIGA envolve a fusão de metal em um vácuo e sua atomização usando gás inerte para produzir pós metálicos finos.
Quais setores utilizam os pós metálicos da VIGA?
Setores como o aeroespacial, médico, automotivo, de ferramentas e elétrico utilizam os pós metálicos da VIGA.
Quais são as vantagens de usar os pós metálicos da VIGA?
Os pós metálicos da VIGA oferecem alta pureza, tamanho de partícula uniforme e excelentes propriedades adequadas para processos de fabricação avançados.
Como as máquinas VIGA se comparam a outros métodos de atomização?
As máquinas VIGA oferecem melhor controle sobre a qualidade e a pureza do pó em comparação com outros métodos, como atomização com água ou atomização com gás.
Os pós metálicos da VIGA são caros?
O custo dos pós metálicos da VIGA pode ser mais alto devido à tecnologia avançada e à produção de alta qualidade, mas os benefícios geralmente superam os custos.
Quais são alguns pós metálicos comuns produzidos pelas máquinas VIGA?
Os pós comuns incluem aço inoxidável 316L, Ti-6Al-4V, Inconel 718, AlSi10Mg, CoCrMo, CuCrZr, 18Ni300, H13, NiCr8020 e WC-Co.
Conclusão
Máquinas VIGA representam o auge no campo da produção de pós metálicos, fornecendo materiais de alta qualidade para uma ampla gama de setores. Sua capacidade de produzir pós com controle preciso sobre a composição e o tamanho das partículas os torna indispensáveis na fabricação moderna. Quer se trate de componentes aeroespaciais, implantes médicos ou ferramentas industriais, a versatilidade e a confiabilidade dos pós produzidos pela VIGA garantem que eles continuem a ser um recurso crítico em aplicações de materiais avançados.