Visão geral de Manufatura aditiva MIM
A moldagem por injeção de metal (MIM) é um processo de manufatura aditiva que combina moldagem por injeção de plástico e metalurgia do pó. A MIM permite a produção em massa de peças metálicas complexas em formato de rede com alta precisão e repetibilidade.
O MIM tem vantagens importantes em relação a outros processos de impressão 3D de metal:
- Produção de alto volume - Até milhares de peças podem ser produzidas em cada lote. Isso torna o MIM adequado para aplicações de produção de uso final.
- Baixo custo por peça - O método de moldagem proporciona economias de escala. O custo da peça diminui significativamente com volumes maiores.
- Ampla variedade de metais - Podem ser usados aço inoxidável, aço para ferramentas, ligas de titânio e outros metais.
- Excelentes propriedades mecânicas - Obtém-se densidade quase total e composição uniforme.
- Geometrias complexas - Formas complexas, características internas e paredes finas são possíveis.
- Múltiplas opções de pós-processamento - Podem ser aplicadas usinagem, gravação, galvanização e outros acabamentos.
- Processo estabelecido - o MIM está em uso desde a década de 1970. Existem padrões e bancos de dados de materiais.
A MIM é ideal para peças metálicas pequenas e complexas necessárias em grandes volumes a custos mais baixos. Ela preenche a lacuna entre a impressão 3D de protótipos e a fabricação de grandes volumes.
Visão geral do processo MIM
O processo de moldagem por injeção de metal tem quatro etapas principais:
- Preparação da matéria-prima - O pó metálico é misturado com um material aglutinante para criar uma matéria-prima homogênea. Essa mistura é peletizada para uso na moldadora por injeção.
- Moldagem por injeção - A matéria-prima é derretida e injetada em uma ferramenta de molde para formar a forma "verde" desejada. É usado o equipamento padrão de moldagem por injeção.
- Rebarbação - O material aglutinante é extraído do componente moldado por meios químicos, térmicos ou catalíticos. Isso deixa uma peça "marrom".
- Sinterização - As peças desbastadas são sinterizadas para fundir o pó metálico em uma peça densa de uso final. As peças encolhem durante a sinterização.
Operações secundárias como usinagem, união, galvanização e gravação podem aprimorar ainda mais os componentes. O fluxo básico do processo MIM é mostrado abaixo:
Tabela 1: Visão geral do processo de manufatura aditiva MIM
Etapa | Descrição |
---|---|
Preparação da matéria-prima | Mistura de pó metálico e aglutinante em uma matéria-prima peletizada |
Moldagem por injeção | Moldagem da matéria-prima no formato verde desejado |
Rebarbação | Remoção do aglutinante para deixar uma parte marrom |
Sinterização | Fusão de pó metálico na peça final por meio de calor |
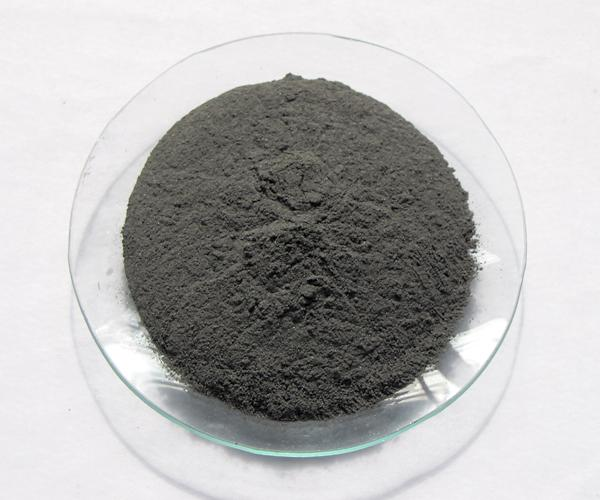
Aplicações de peças MIM
A MIM é adequada para a fabricação de componentes metálicos pequenos, complexos e de formato líquido em volumes médios a altos. As aplicações típicas de MIM incluem:
Tabela 2: Aplicações da manufatura aditiva MIM
Setor | Exemplo de componentes |
---|---|
Automotivo | Bicos injetores de combustível, engrenagens de dentes retos, peças de turbocompressores |
Aeroespacial | Lâminas de turbina, impulsores, iniciadores |
Médico | Braquetes ortodônticos, cabos de bisturi, fórceps |
Consumidor | Componentes de relógios, grades, peças decorativas |
Industrial | Lâminas de faca, mecanismos de travamento, válvulas |
Armas de fogo | Gatilhos, martelos, cofres, corrediças |
A MIM permite a consolidação de peças, a redução de peso, o melhor desempenho e a redução dos custos de fabricação em muitos setores. A combinação de liberdade geométrica e produtividade torna o MIM adequado para a produção de uso final.
Em comparação com a usinagem CNC, a MIM permite que formas mais complexas sejam produzidas em massa. A minimização das etapas de montagem por meio da integração de peças se torna viável com a MIM.
Vantagens da manufatura aditiva MIM
A MIM tem benefícios exclusivos que a tornam uma opção popular de fabricação:
Tabela 3: Vantagens da manufatura aditiva MIM
Benefício | Descrição |
---|---|
Produção de alto volume | Até milhões de peças podem ser produzidas por ano por meio do MIM |
Baixo custo por peça | Redução de custos com maiores volumes de produção |
Flexibilidade de design | São possíveis geometrias complexas e microcaracterísticas |
Variedade de materiais | A maioria das ligas em pó, como aço inoxidável, aço para ferramentas e titânio, pode ser usada |
Boas propriedades mecânicas | Densidade quase total e composição uniforme |
Variedade de acabamentos | Usinagem, gravação, galvanização e outros acabamentos podem ser aplicados |
Processo estabelecido | Padrões, bancos de dados, anos de experiência disponíveis |
A combinação de liberdade de design, recursos de material e custo-benefício oferece vantagens ao MIM em relação a outros processos, como impressão 3D de metal, fundição de investimento ou usinagem.
As peças podem ser projetadas com paredes mais finas, cortes inferiores, interiores ocos e outros elementos complexos. A consolidação de vários componentes em uma peça MIM também é viável.
Limitações da manufatura aditiva MIM
Embora tenha muitos benefícios, a MIM tem algumas restrições:
Tabela 4: Limitações da manufatura aditiva MIM
Limitação | Descrição |
---|---|
Tamanho da peça | Normalmente limitado a componentes menores, de até 70 polegadas cúbicas |
Materiais de baixa ductilidade | Algumas ligas dúcteis, como o alumínio, não são prontamente compatíveis com MIM |
Custos iniciais | É necessário um investimento significativo em ferramentas para os moldes |
Produção de baixa mistura | Mais adequado para volumes médios a altos da mesma peça |
Pós-processamento | Pode ser necessário usinagem ou acabamento adicional |
A MIM tem limites de geometria, pois envolve moldagem. Os plásticos termofixos permitem peças MIM maiores, mas têm menor resistência.
Nem todas as ligas metálicas podem ser facilmente formuladas em matérias-primas de MIM. Os materiais dúcteis, em particular, apresentam desafios.
Os moldes de aço duro para ferramentas devem ser fabricados para cada novo projeto de peça. Isso aumenta o tempo e o custo.
Mudanças frequentes no design são menos adequadas para o MIM devido às ferramentas de molde fixas. Outros métodos de impressão 3D permitem uma iteração mais fácil.
Dependendo dos requisitos dimensionais e de superfície finais, podem ser necessárias operações de pós-moldagem.
Considerações sobre o design do MIM
A MIM permite liberdade geométrica, mas as peças devem ser projetadas levando em conta as limitações do processo:
Tabela 5: Considerações sobre o projeto do MIM
Parâmetro | Diretriz |
---|---|
Espessura da parede | Mínimo de 0,3 mm, máximo de 5 mm. A espessura uniforme é ideal |
Tolerâncias | ±0,5% é típico, mas depende da geometria |
Acabamento da superfície | O as-sinterizado está em torno de Ra 10-15 mícrons |
Ângulos de inclinação | Ângulos de inclinação >1° necessários para ajudar na desmoldagem |
Complexidade da forma | A consolidação de peças ou a otimização da topologia é viável |
Recursos | Detalhes finos, como furos e ranhuras de 0,1 mm, são possíveis |
Texturas | Podem ser incorporadas texturas complexas no molde |
Inserções | É possível incorporar outros insertos no molde |
Redução de peso | Oco, redução de massa por meio de redes e otimização de topologia |
O processo de moldagem impõe certas regras de design. Mas o MIM ainda pode produzir geometrias inatingíveis por outros métodos.
Opções de material MIM
Uma ampla variedade de ligas, incluindo aços e titânio altamente exigidos, está disponível para MIM:
Tabela 6: Opções de material MIM
Material | Formulários |
---|---|
Aço inoxidável | Produtos médicos, marítimos e de consumo |
Aço para ferramentas | Ferramentas de corte, moldes, peças de desgaste |
Aço de baixa liga | Automotivo, componentes de máquinas |
Ligas de titânio | Aeroespacial, implantes médicos |
Ligas de níquel | Turbinas aeroespaciais, equipamentos marítimos |
Ligas pesadas de tungstênio | Proteção contra radiação, amortecimento de vibrações |
O aço inoxidável de alta resistência e resistente à corrosão, como o 17-4PH e o 304L, é comumente usado. Os graus de endurecimento por precipitação permitem um aumento adicional da resistência.
Os aços para ferramentas, como o H13, são ideais para moldes de conformação, estampagem e injeção que necessitam de boa dureza, resistência e estabilidade térmica.
As ligas de titânio para biocompatibilidade, as ligas de níquel para resistência ao calor e as ligas de tungstênio para densidade são prontamente compatíveis com MIM.
Novos materiais, como ligas de cobre e alumínio MIM, também estão sendo desenvolvidos.
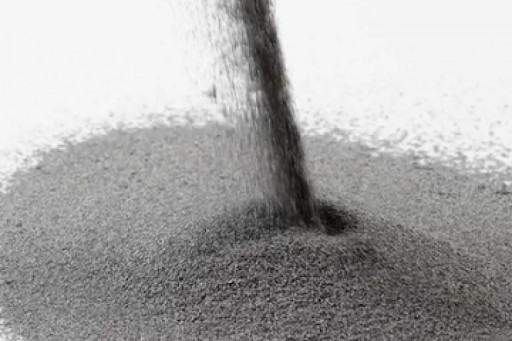
Opções de software de design MIM
Para auxiliar nos requisitos de projeto do MIM, existem opções de software de otimização de topologia e CAD:
Tabela 7: Opções do software de design MIM
Software | Descrição |
---|---|
SolidWorks | CAD popular com plug-ins de análise de fluxo de molde |
Autodesk Moldflow | Simulação de molde de injeção dedicado |
nTopologia | Otimização e design de topologia para software AM |
Materialise 3-matic | Ferramenta para projetar treliças e estruturas leves |
Netfab | Software para otimização de malhas 3D para MIM |
O Solidworks é comumente usado para projetos de CAD. A simulação de fluxo de molde pode verificar a capacidade de fabricação.
Programas especializados, como o Moldflow, acrescentam recursos avançados de análise e modelagem de processos.
O software de otimização de topologia, como o nTopology, permite formas orgânicas adaptadas para AM e MIM. A redução de peso e a consolidação são possíveis.
Softwares como o 3-matic ajudam a projetar treliças de densidade variável e a gerar estruturas de suporte.
Parâmetros do processo MIM
O MIM envolve a otimização de matérias-primas, moldagem, desbobinamento e sinterização. Os parâmetros típicos são:
Tabela 8: Parâmetros do processo MIM
Etapa | Faixa típica |
---|---|
Tamanho do pó | 5 - 25 mícrons |
Fichário | 30 - 50% de volume de matéria-prima |
Carregamento de sólidos | 55 - 70% em matéria-prima |
Temperatura do molde | 150 - 185°C |
Pressão de injeção | 60 - 110 MPa |
Taxa de resfriamento da moldagem | 20 - 50°C/s de resfriamento |
Método de desbobinamento | Solvente, térmico, catalítico |
Tempo de desbobinamento | Dias a horas |
Temperatura de sinterização | 50 - 80% do ponto de fusão |
Tempo de sinterização | De horas a dias |
Encolhimento | 13 - 17% contração linear |
Os parâmetros dependem do material, da geometria da peça, da taxa de produção e das propriedades necessárias.
Os pós finos e as altas cargas de sólidos ajudam na resolução. Resfriamento e temperaturas de molde mais rápidos criam melhor resistência verde. Tempos de debinding menores e temperaturas de sinterização mais altas aumentam as taxas de produção.
Opções de pós-processamento do MIM
Como as peças MIM sinterizadas podem exigir processamento adicional:
Tabela 9: Opções de pós-processamento do MIM
Processo | Finalidade |
---|---|
Tratamento térmico | Altere a microestrutura para obter propriedades aprimoradas |
Revestimento | Aplique revestimentos decorativos como ouro ou cromo |
Passivação | Criar uma camada protetora de óxido em aços |
Soldagem | Unir peças MIM umas às outras ou a outros componentes |
Marcação a laser | Marcas permanentes para logotipos, textos ou códigos de identificação |
Usinagem e perfuração | Dimensões de maior precisão ou recursos personalizados |
Acabamento vibratório | Alisa a superfície e arredonda as bordas afiadas |
As etapas de pós-moldagem podem refinar a aparência, as propriedades e as interfaces com outros componentes. Chapeamento, anodização e pintura são acabamentos populares.
A conexão de peças MIM por meio de soldagem, brasagem ou colagem pode ser necessária para algumas montagens. A usinagem adicional pode criar superfícies de acoplamento de precisão.
Fornecedores de equipamentos MIM
Empresas estabelecidas de moldagem por injeção oferecem equipamentos e serviços de MIM:
Tabela 10: Fornecedores de equipamentos MIM
Empresa | Equipamentos |
---|---|
ARBURG | Máquinas de moldagem por injeção elétrica e hidráulica |
Milacron | Linhas MIM integradas completas |
Toshiba | Máquinas de moldagem híbridas e elétricas |
Netstal | Moldagem por injeção de alta precisão |
Nissei | Moldadores de injeção verticais e horizontais |
Sodick | Moldagem de alta velocidade e alta frequência |
Serviços especializados de MIM também estão disponíveis em:
- PIM International
- MPP
- MIMITAL
- Inovações CN
Esses prestadores de serviços completos oferecem formulação de matéria-prima, análise, ferramentas, moldagem, desbobinamento e sinterização.
Considerações sobre o custo da manufatura aditiva MIM
O MIM tem custos de inicialização relativamente altos, mas baixos custos por peça em volumes de produção:
Tabela 11: Considerações sobre o custo do MIM
Fator de custo | Faixa típica |
---|---|
Ferramenta de molde | $10.000 - $100.000+, dependendo da complexidade, do material e do tamanho |
Configuração de lotes pequenos | Abaixo de $10.000 |
Custo incremental da peça | Custo do metal $0.5 - $5 por peça |
Taxa de produção | 5.000 a 500.000 peças por ano por ferramenta |
Acabamento | $0.1 - $2 por peça, dependendo do processo |
Tamanho do lote Breakeven | 1.000 - 10.000+ peças versus outros processos |
A fresagem de uma ferramenta de molde MIM a partir de aço para ferramentas pode levar semanas e custar mais de $100.000 para componentes grandes. Os moldes menores e menos complexos podem custar menos de $10.000.
Depois que o molde é feito, os custos contínuos do processo MIM são muito econômicos para volumes de produção médios a altos. A MIM pode produzir até um milhão de peças por ano com uma única ferramenta de molde.
Escolha entre MIM e outros processos de AM
O MIM está posicionado entre a impressão 3D e os processos de alto volume:
Tabela 12: Comparação entre MIM e outros processos de AM de metal
Fator | MIM | Impressão 3D com jato de aglutinante | DMLS | Fundição sob pressão |
---|---|---|---|---|
Custo de capital | Alta para ferramentas | Médio | Alta | Muito alta |
Custo por peça | Menor valor acima de 10 mil peças | Baixo em volumes baixos | Médio | Menor em volumes muito altos |
Materiais | Ampla gama de ligas | Alcance limitado | Alcance limitado | Ligas de alumínio e zinco |
Resolução | Médio ~0,1 - 0,3 mm | Médio ~0,3 - 0,5 mm | Maior ~0,05 mm | Inferior ~0,5 mm |
Velocidade de produção | Alta | Médio | Lento | Muito alta |
Pós-processamento | Médio | Alta | Médio | Baixa |
Propriedades mecânicas | Bom | Variável | Melhor | Bom |
Restrições de design | Algumas restrições geométricas | Poucas restrições | Algumas restrições de saliência | Alto nível de restrições |
O MIM oferece a melhor economia para geometrias complexas em materiais de liga necessários em produções de mais de 10.000 unidades. Os processos de produção em massa de custo mais baixo tornam-se favoráveis em volumes muito maiores.
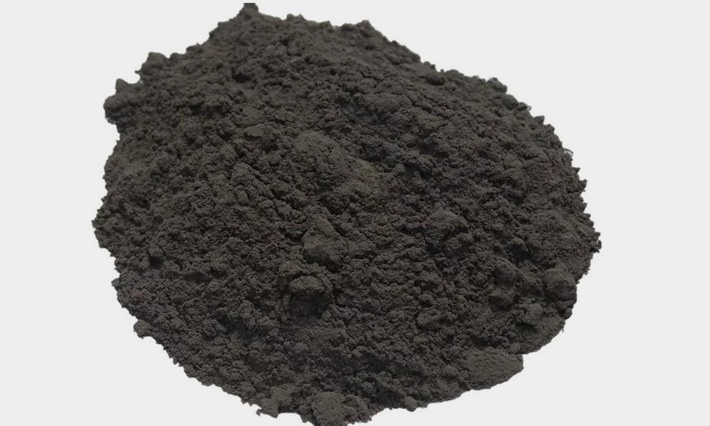
Conclusão
O MIM é um processo atraente de manufatura aditiva de metal que permite que geometrias complexas sejam produzidas em massa diretamente em uma variedade de ligas de engenharia.
Ele combina a versatilidade da AM com a produtividade próxima à da fabricação convencional. Essa fusão poderosa leva a custos menores de peças, consolidação de montagens, melhor desempenho e construção leve.
Embora necessite de algum investimento inicial em molde, o MIM proporciona economias de escala valiosas. Ela está se estabelecendo como uma técnica complementar que preenche a lacuna entre a impressão 3D de protótipos e a fabricação de alto volume.
O desenvolvimento contínuo de materiais e a integração de software expandirão as aplicações de MIM nos setores médico, aeroespacial, automotivo, industrial e de consumo.
Manufatura aditiva MIM - Perguntas frequentes
P: Como o MIM se compara à fundição sob pressão?
R: A MIM pode produzir geometrias mais complexas e de maior precisão do que a fundição sob pressão, mas tem taxas e volumes de produção menores. A fundição sob pressão é mais rápida e barata para formas mais simples, necessárias aos milhões.
P: Que tamanho de peças pode ser feito com MIM?
R: As peças MIM normalmente variam de 0,5 a 70 gramas de peso. Componentes maiores, de até 250 gramas, são possíveis com equipamentos para lidar com pressões mais altas e tamanhos de ferramentas.
P: O que determina o custo de uma ferramenta de molde MIM?
R: O material do molde, a complexidade, o tamanho, os acabamentos de superfície e o tempo de resposta afetam os custos de fabricação do molde. Os moldes simples de aço para ferramentas podem ser inferiores a $10k, enquanto os moldes de aço temperado de grande produção podem exceder $100k.
P: O MIM requer algum pós-processamento?
R: Algumas aplicações precisam de tratamento térmico adicional, usinagem ou acabamento de superfície. Mas muitos componentes podem ser usados como sinterizados. O pós-processamento depende dos requisitos dimensionais e de aparência finais.
P: Quantas peças um molde MIM pode produzir?
R: As taxas de produção de MIM normalmente variam de 5.000 a 500.000 peças por ano por ferramenta. Com a manutenção adequada, milhões de disparos são possíveis ao longo de anos de vida útil.
P: Quais são os erros comuns de projeto de MIM que devem ser evitados?
R: Ângulos de inclinação insuficientes, cortes severos, transições de paredes grossas para finas e colocação de detalhes finos em lados opostos de um núcleo podem causar problemas de moldagem. Recomenda-se consultar projetistas experientes.
P: Vários materiais podem ser combinados no MIM?
R: Sim, a MIM permite peças multimateriais usando misturas de pós ou várias matérias-primas. A moldagem por inserção com outras ligas ou materiais duros também é possível para estruturas compostas.
P: Como é o acabamento da superfície das peças MIM?
R: O acabamento como sinterizado tem cerca de 10 a 15 mícrons de rugosidade. Isso é adequado para muitas aplicações. O tombamento ou polimento adicional pode suavizar ainda mais as superfícies, se necessário.
P: Quanto tempo leva o processo de MIM?
R: Normalmente, os prazos de entrega variam de 6 a 12 semanas. A fabricação do molde leva mais tempo, se necessário. Depois que as ferramentas são feitas, a produção em lote é bastante rápida para componentes pequenos.