Überblick über mim additive Fertigung
Das Metallspritzgießen (MIM) ist ein additives Fertigungsverfahren, das Kunststoffspritzguss und Pulvermetallurgie kombiniert. MIM ermöglicht die Massenproduktion komplexer Metallteile in Nettoform mit hoher Präzision und Wiederholbarkeit.
MIM hat entscheidende Vorteile gegenüber anderen 3D-Metalldruckverfahren:
- Großserienproduktion – In jeder Charge können bis zu Tausende von Teilen hergestellt werden. Dadurch eignet sich MIM für Endanwendungen in der Produktion.
- Niedrige Kosten pro Teil – Das Gießverfahren bringt Skaleneffekte. Die Kosten pro Teil sinken bei höheren Stückzahlen erheblich.
- Eine breite Palette von Metallen – Edelstahl, Werkzeugstahl, Titanlegierungen und andere Metalle können verwendet werden.
- Hervorragende mechanische Eigenschaften – Nahezu vollständige Dichte und gleichmäßige Zusammensetzung werden erreicht.
- Komplexe Geometrien – Komplizierte Formen, innere Merkmale und dünne Wände sind möglich.
- Mehrere Nachbearbeitungsoptionen – Bearbeitung, Ätzen, Galvanisieren und andere Veredelungen können angewendet werden.
- Etabliertes Verfahren – MIM wird seit den 1970er Jahren eingesetzt. Es gibt Normen und Materialdatenbanken.
MIM ist ideal für kleine, komplexe Metallteile, die in hohen Stückzahlen zu geringeren Kosten benötigt werden. Es schließt die Lücke zwischen dem 3D-Druck von Prototypen und der Großserienfertigung.
Überblick über den MIM-Prozess
Das Metall-Spritzgießverfahren besteht aus vier Hauptschritten:
- Vorbereitung von Rohstoffen Metallpulver wird mit einem Bindemittel gemischt, um ein homogenes Ausgangsmaterial zu erhalten. Dieses Gemisch wird für die Verwendung in der Spritzgießmaschine pelletiert.
- Spritzgießen Das Ausgangsmaterial wird geschmolzen und in ein Formwerkzeug gespritzt, um die gewünschte Form zu erhalten. Es wird eine Standard-Spritzgießausrüstung verwendet.
- Entbinden Das Bindemittel wird durch chemische, thermische oder katalytische Verfahren aus dem geformten Bauteil herausgelöst. Zurück bleibt ein “braunes” Teil.
- Sintern Die entbundenen Teile werden gesintert, um das Metallpulver zu einem dichten Endprodukt zu verschmelzen. Die Teile schrumpfen während des Sinterns.
Durch sekundäre Verfahren wie Bearbeitung, Fügen, Beschichten und Ätzen können die Bauteile weiter verbessert werden. Der grundlegende Ablauf des MIM-Prozesses ist unten dargestellt:
Tabelle 1: Überblick über den additiven Fertigungsprozess MIM
Schritt | Beschreibung |
---|---|
Vorbereitung von Rohstoffen | Mischen von Metallpulver und Bindemittel zu einem pelletierten Ausgangsmaterial |
Spritzgießen | Formung des Ausgangsmaterials in die gewünschte grüne Form |
Entbinden | Entfernen des Bindemittels, um einen braunen Teil zu hinterlassen |
Sintern | Verschmelzen des Metallpulvers zum fertigen Teil durch Hitze |
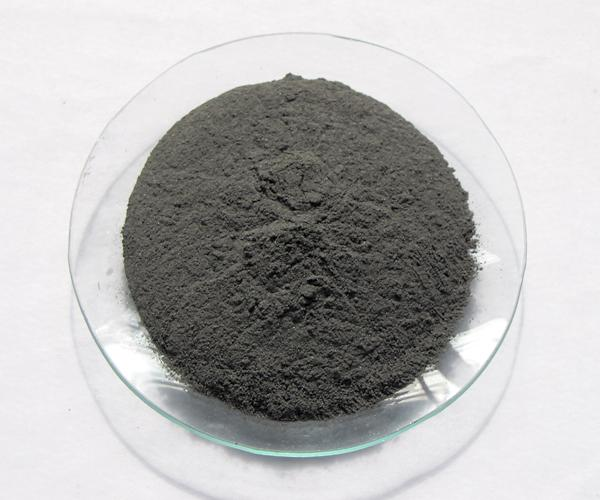
Anwendungen von MIM-Teilen
MIM eignet sich für die Herstellung kleiner, komplexer, netzförmiger Metallteile in mittleren bis hohen Stückzahlen. Typische MIM-Anwendungen sind:
Tabelle 2: Anwendungen der additiven MIM-Fertigung
Industrie | Beispiel Komponenten |
---|---|
Automobilindustrie | Einspritzdüsen, Stirnradgetriebe, Turboladerteile |
Luft- und Raumfahrt | Turbinenschaufeln, Laufräder, Initiatoren |
Medizinische | Kieferorthopädische Klammern, Skalpellgriffe, Pinzetten |
Verbraucher | Uhrenkomponenten, Grills, dekorative Teile |
Industriell | Messerklingen, Verriegelungsmechanismen, Ventile |
Feuerwaffen | Auslöser, Hämmer, Sicherungen, Schlitten |
MIM ermöglicht die Konsolidierung von Teilen, Gewichtsreduzierung, bessere Leistung und niedrigere Herstellungskosten in vielen Branchen. Die Kombination aus geometrischer Freiheit und Produktivität macht MIM für die Endproduktion geeignet.
Im Vergleich zur CNC-Bearbeitung lassen sich mit MIM komplexere Formen in Serie herstellen. Die Minimierung von Montageschritten durch die Integration von Teilen ist mit MIM möglich.
Vorteile der MIM Additiven Fertigung
MIM hat einzigartige Vorteile, die es zu einer beliebten Fertigungsoption machen:
Tabelle 3: Vorteile von MIM Additive Manufacturing
Nutzen Sie | Beschreibung |
---|---|
Produktion großer Mengen | Mit MIM können bis zu Millionen von Teilen pro Jahr hergestellt werden |
Niedrige Kosten pro Teil | Kostenreduzierung bei höherem Produktionsvolumen |
Flexibilität bei der Gestaltung | Komplexe Geometrien und Mikromerkmale sind möglich |
Auswahl an Materialien | Die meisten Legierungspulver wie rostfreier Stahl, Werkzeugstahl und Titan können verwendet werden. |
Gute mechanische Eigenschaften | Nahezu vollständige Dichte und einheitliche Zusammensetzung |
Vielfältige Verarbeitungen | Bearbeitungen, Ätzungen, Beschichtungen und andere Veredelungen können vorgenommen werden |
Etablierter Prozess | Standards, Datenbanken, langjährige Erfahrung verfügbar |
Die Kombination aus Designfreiheit, Materialeigenschaften und Kosteneffizienz verschafft MIM Vorteile gegenüber anderen Verfahren wie 3D-Metalldruck, Feinguss oder maschineller Bearbeitung.
Es können Teile mit dünneren Wänden, Hinterschneidungen, hohlen Innenräumen und anderen komplexen Elementen hergestellt werden. Auch die Konsolidierung mehrerer Komponenten in einem MIM-Teil ist möglich.
Grenzen der MIM Additiven Fertigung
MIM bietet zwar viele Vorteile, hat aber auch einige Einschränkungen:
Tabelle 4: Grenzen der additiven MIM-Fertigung
Begrenzung | Beschreibung |
---|---|
Größe des Teils | In der Regel auf kleinere Komponenten mit bis zu 70 Kubikzoll beschränkt |
Materialien mit geringer Duktilität | Einige duktile Legierungen wie Aluminium sind nicht ohne weiteres MIM’fähig |
Vorabkosten | Erhebliche Investitionen in Werkzeuge für Formen erforderlich |
Niedrige Mischproduktion | Am besten geeignet für mittlere bis hohe Stückzahlen desselben Teils |
Nachbearbeitung | Zusätzliche Bearbeitungen oder Nacharbeiten können erforderlich sein |
MIM hat geometrische Grenzen, da es sich um eine Formgebung handelt. Duroplastische Kunststoffe ermöglichen größere MIM-Teile, haben aber eine geringere Festigkeit.
Nicht alle Metalllegierungen lassen sich problemlos in MIM-Rohstoffe umwandeln. Insbesondere duktile Werkstoffe stellen eine Herausforderung dar.
Für jedes neue Teiledesign müssen Formen aus hartem Werkzeugstahl angefertigt werden. Das bedeutet zusätzlichen Zeit- und Kostenaufwand.
Häufige Designänderungen sind für MIM aufgrund der festen Formwerkzeuge weniger geeignet. Andere 3D-Druckverfahren ermöglichen einfachere Iterationen.
Je nach den endgültigen Abmessungen und Oberflächenanforderungen können Nachbearbeitungsschritte erforderlich sein.
Überlegungen zum MIM-Design
MIM ermöglicht geometrische Freiheiten, aber die Teile müssen unter Berücksichtigung der Prozessgrenzen konstruiert werden:
Tabelle 5: Überlegungen zum MIM-Design
Parameter | Leitfaden |
---|---|
Wandstärke | Mindestens 0,3 mm, höchstens 5 mm. Gleichmäßige Dicke ist ideal |
Toleranzen | ±0,5% ist typisch, hängt aber von der Geometrie ab |
Oberflächengüte | As-gesintert ist etwa Ra 10-15 Mikrometer |
Entwurfswinkel | 1° Entformungsschräge zur Unterstützung der Entformung erforderlich |
Komplexität der Form | Die Konsolidierung von Teilen oder die Optimierung der Topologie ist machbar |
Eigenschaften | Feine Details wie 0,1 mm Löcher und Schlitze sind möglich |
Texturen | Komplexe In-Mold-Texturen können eingearbeitet werden |
Inserts | Das Einbringen anderer Einsätze in die Form ist möglich |
Gewichtsreduzierung | Hohlraumbildung, Verringerung der Masse durch Gitter und Topologieoptimierung |
Der Formgebungsprozess erzwingt bestimmte Designregeln. Dennoch lassen sich mit MIM Geometrien herstellen, die mit anderen Verfahren nicht zu erreichen sind.
MIM-Materialoptionen
Für das MIM-Verfahren steht eine breite Palette von Legierungen zur Verfügung, darunter sehr gefragte Stähle und Titan:
Tabelle 6: MIM-Materialoptionen
Material | Anwendungen |
---|---|
rostfreier Stahl | Medizin, Schifffahrt, Konsumgüter |
Werkzeugstahl | Schneidwerkzeuge, Formen, Verschleißteile |
Niedrig legierter Stahl | Automobilindustrie, Maschinenbauteile |
Titan-Legierungen | Luft- und Raumfahrt, medizinische Implantate |
Nickel-Legierungen | Turbinen für die Luft- und Raumfahrt, Hardware für die Schifffahrt |
Wolfram-Schwermetall-Legierungen | Strahlungsabschirmung, Schwingungsdämpfung |
Hochfeste, korrosionsbeständige Edelstähle wie 17-4PH und 304L werden häufig verwendet. Ausscheidungsgehärtete Sorten ermöglichen eine weitere Festigkeitssteigerung.
Werkzeugstähle wie H13 sind ideal für Umform-, Stanz- und Spritzgussformen, die eine gute Härte, Zähigkeit und thermische Stabilität erfordern.
Titanlegierungen für die Biokompatibilität, Nickellegierungen für die Hitzebeständigkeit und Wolframlegierungen für die Dichte sind ohne weiteres MIM’fähig.
Neue Materialien wie MIM-Kupfer- und Aluminiumlegierungen befinden sich ebenfalls in der Entwicklung.
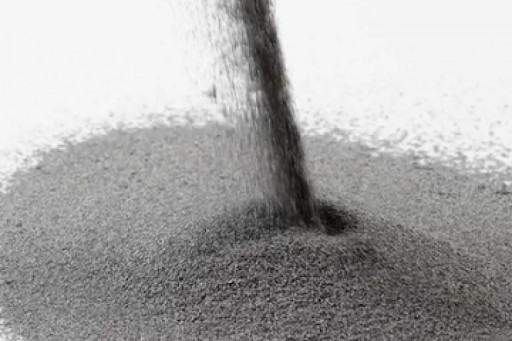
MIM Design Software Optionen
Zur Unterstützung der MIM-Designanforderungen gibt es CAD- und Topologieoptimierungssoftware:
Tabelle 7: Optionen der MIM-Design-Software
Software | Beschreibung |
---|---|
SolidWorks | Beliebte CAD mit Moldflow-Analyse-Plugins |
Autodesk Moldflow | Dedizierte Spritzgussformsimulation |
nTopologie | Topologieoptimierung und Design für AM-Software |
Materialise 3-matic | Werkzeug für den Entwurf von Gittern und leichten Strukturen |
Netfab | Software zur Optimierung von 3D-Netzen für MIM |
Solidworks wird in der Regel für die CAD-Konstruktion verwendet. Mit der Moldflow-Simulation kann die Herstellbarkeit geprüft werden.
Spezialisierte Programme wie Moldflow bieten zusätzlich erweiterte Analyse- und Prozessmodellierungsfunktionen.
Topologieoptimierungssoftware wie nTopology ermöglicht organische Formen, die für AM und MIM maßgeschneidert sind. Leichtbau und Konsolidierung werden ermöglicht.
Software wie 3-matic hilft beim Entwurf von Gittern mit variabler Dichte und bei der Erstellung von Stützstrukturen.
MIM-Prozess-Parameter
MIM umfasst die Optimierung von Rohstoffen, Formgebung, Entbinderung und Sinterung. Typische Parameter sind:
Tabelle 8: MIM-Prozessparameter
Schritt | Typischer Bereich |
---|---|
Größe des Pulvers | 5 – 25 Mikrometer |
Binder | 30 – 50% der Rohstoffmenge |
Beladung mit Feststoffen | 55 – 70% im Ausgangsmaterial |
Temperatur der Form | 150 – 185°C |
Einspritzdruck | 60 – 110 MPa |
Formgebung Abkühlungsrate | 20 – 50°C/s Abschrecken |
Entbindungsmethode | Lösungsmittel, thermisch, katalytisch |
Entbindungszeit | Tage bis Stunden |
Sintertemperatur | 50 – 80% des Schmelzpunkts |
Sinterzeit | Stunden bis Tage |
Schrumpfung | 13 – 17% linear schrumpfen |
Die Parameter hängen vom Material, der Teilegeometrie, der Produktionsrate und den benötigten Eigenschaften ab.
Feine Pulver und hohe Feststoffgehalte unterstützen die Auflösung. Schnellere Abkühl- und Formtemperaturen sorgen für eine bessere Grünfestigkeit. Niedrigere Entbinderungszeiten und höhere Sintertemperaturen erhöhen die Produktionsraten.
MIM-Nachbearbeitungsoptionen
Da gesinterte MIM-Teile zusätzliche Bearbeitung erfordern können:
Tabelle 9: MIM-Nachbearbeitungsoptionen
Prozess | Zweck |
---|---|
Wärmebehandlung | Veränderung der Mikrostruktur für verbesserte Eigenschaften |
Beschichtung | Aufbringen dekorativer Beschichtungen wie Gold oder Chrom |
Passivierung | Erzeugung einer schützenden Oxidschicht auf Stählen |
Schweißen | Verbinden von MIM-Teilen miteinander oder mit anderen Komponenten |
Laser Marking | Dauerhafte Markierungen für Logos, Text oder ID-Codes |
Spanende Bearbeitung und Bohren | Präzisere Abmessungen oder kundenspezifische Merkmale |
Gleitschleifen | Oberfläche glätten und scharfe Kanten abrunden |
Durch Nachbearbeitungsschritte können Aussehen, Eigenschaften und Schnittstellen zu anderen Bauteilen verfeinert werden. Plattieren, Eloxieren und Lackieren sind beliebte Veredelungen.
Die Verbindung von MIM-Teilen durch Schweißen, Löten oder Kleben kann bei einigen Baugruppen erforderlich sein. Durch zusätzliche Bearbeitung können präzise Passflächen geschaffen werden.
Lieferanten von MIM-Ausrüstung
Etablierte Spritzgießunternehmen bieten MIM-Anlagen und -Dienstleistungen an:
Tabelle 10: Anbieter von MIM-Ausrüstung
Unternehmen | Ausrüstung |
---|---|
ARBURG | Elektrische und hydraulische Spritzgießmaschinen |
Milacron | Vollständig integrierte MIM-Linien |
Toshiba | Hybride und elektrische Spritzgießmaschinen |
Netstal | Hochpräzises Spritzgießen |
Nissei | Vertikale und horizontale Spritzgießmaschinen |
Sodick | Hochgeschwindigkeit, Hochfrequenz-Formenbau |
Spezialisierte MIM-Dienste sind ebenfalls erhältlich bei:
- PIM International
- MPP
- MIMITAL
- CN-Innovationen
Diese Full-Service-Anbieter bieten die Formulierung von Rohstoffen, die Analyse, die Werkzeugherstellung, das Formen, Entbindern und Sintern an.
Kostenüberlegungen für MIM Additive Manufacturing
MIM hat relativ hohe Anfangskosten, aber niedrige Kosten pro Teil bei Produktionsvolumen:
Tabelle 11: MIM-Kostenüberlegungen
Kostenfaktor | Typischer Bereich |
---|---|
Formwerkzeug | $10.000 – $100.000+ je nach Komplexität, Material und Größe |
Kleine Batch-Einrichtung | Unter $10.000 |
Inkrementelle Teilkosten | $0,5 – $5 Metallkosten pro Stück |
Produktionsrate | 5.000 – 500.000 Teile pro Jahr und Werkzeug |
Fertigstellung | $0,1 – $2 pro Teil je nach Verfahren |
Chargengröße Breakeven | 1.000 – 10.000+ Teile gegenüber anderen Verfahren |
Das Fräsen eines MIM-Werkzeugs aus Werkzeugstahl kann Wochen dauern und bei großen Bauteilen über 100.000 $ kosten. Kleinere, weniger komplexe Formen können weniger als 10.000 $ kosten.
Sobald die Form hergestellt ist, sind die laufenden Kosten des MIM-Prozesses bei mittleren bis hohen Produktionsmengen sehr wirtschaftlich. MIM kann bis zu einer Million Teile pro Jahr aus einem einzigen Formwerkzeug herstellen.
Die Wahl zwischen MIM und anderen AM-Verfahren
MIM ist zwischen 3D-Druck und Großserienverfahren angesiedelt:
Tabelle 12: Vergleich zwischen MIM und anderen Metall-AM-Verfahren
Faktor | MIM | Binder Jet 3D-Druck | DMLS | Druckgießen |
---|---|---|---|---|
Kapitalkosten | Hoch für Werkzeuge | Mittel | Hoch | Sehr hoch |
Kosten pro Teil | Niedrigste über 10k Teile | Niedrig bei geringen Lautstärken | Mittel | Niedriger bei sehr hohem Volumen |
Materialien | Breite Palette von Legierungen | Begrenzte Reichweite | Begrenzte Reichweite | Aluminium- und Zinklegierungen |
Auflösung | Mittel ~0,1 – 0,3mm | Mittel ~0,3 – 0,5mm | Höchste ~0,05mm | Untere ~0,5mm |
Produktionsgeschwindigkeit | Hoch | Mittel | Slow | Sehr hoch |
Nachbearbeitung | Mittel | Hoch | Mittel | Niedrig |
Mechanische Eigenschaften | Gut | Variabel | Best | Gut |
Design-Zwänge | Einige geometrische Zwänge | Wenige Zwänge | Einige Überhangzwänge | Hoher Grad an Zwängen |
MIM bietet die beste Wirtschaftlichkeit für komplexe Geometrien aus legierten Werkstoffen, die für Produktionen von 10.000+ benötigt werden. Kostengünstigere Massenproduktionsverfahren werden erst bei wesentlich höheren Stückzahlen interessant.
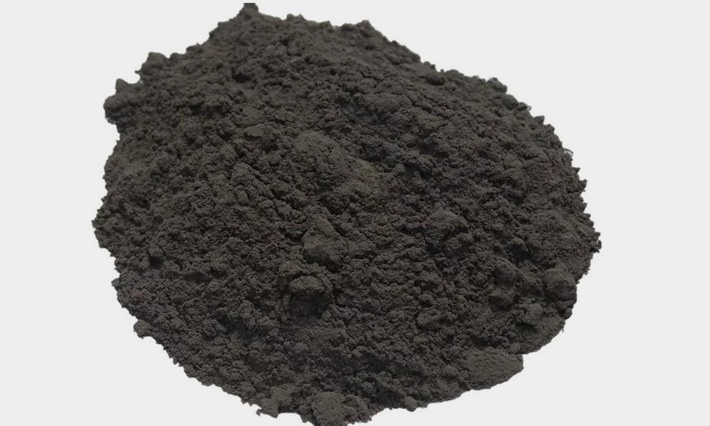
Schlussfolgerung
MIM ist ein attraktives Verfahren zur additiven Fertigung von Metallen, mit dem komplexe Geometrien direkt in einer Reihe von technischen Legierungen in Serie hergestellt werden können.
Es kombiniert die Vielseitigkeit von AM mit einer Produktivität, die der konventionellen Fertigung nahe kommt. Diese leistungsstarke Fusion führt zu niedrigeren Teilekosten, Konsolidierung von Baugruppen, besserer Leistung und Leichtbau.
MIM erfordert zwar eine gewisse Anfangsinvestition in die Form, bietet aber wertvolle Größenvorteile. Es etabliert sich als ergänzende Technik, die die Lücke zwischen dem 3D-Druck von Prototypen und der Großserienfertigung überbrückt.
Die fortgesetzte Materialentwicklung und Softwareintegration wird die MIM-Anwendungen in den Bereichen Medizin, Luft- und Raumfahrt, Automobil, Industrie und Konsumgüter erweitern.
MIM Additive Fertigung – FAQ
F: Was ist der Unterschied zwischen MIM und Druckguss?
A: MIM kann komplexere, präzisere Geometrien herstellen als Druckguss, hat aber geringere Produktionsraten und -mengen. Druckguss ist schneller und billiger für einfachere Formen, die in Millionenhöhe benötigt werden.
F: Welche Teilegrößen können mit MIM hergestellt werden?
A: MIM-Teile haben in der Regel ein Gewicht von 0,5 bis 70 Gramm. Größere Bauteile bis zu 250 Gramm sind möglich, wenn die Ausrüstung für höhere Drücke und Werkzeuggrößen geeignet ist.
F: Wodurch werden die Kosten für ein MIM-Werkzeug bestimmt?
A: Formenmaterial, Komplexität, Größe, Oberflächenbeschaffenheit und Durchlaufzeit beeinflussen die Kosten für die Formenherstellung. Einfache Formen aus Werkzeugstahl können weniger als 10.000 $ kosten, während große Produktionsformen aus gehärtetem Stahl 100.000 $ übersteigen können.
F: Ist bei MIM eine Nachbearbeitung erforderlich?
A: Einige Anwendungen erfordern eine zusätzliche Wärmebehandlung, Bearbeitung oder Oberflächenbehandlung. Viele Bauteile können jedoch im gesinterten Zustand verwendet werden. Die Nachbearbeitung hängt von den endgültigen Anforderungen an die Abmessungen und das Aussehen ab.
F: Wie viele Teile kann ein MIM-Werkzeug herstellen?
A: MIM-Produktionsraten liegen in der Regel zwischen 5.000 und 500.000 Teilen pro Jahr und Werkzeug. Bei ordnungsgemäßer Wartung sind Millionen von Schüssen über eine jahrelange Lebensdauer möglich.
F: Welche häufigen MIM-Designfehler sind zu vermeiden?
A: Unzureichende Entformungswinkel, starke Hinterschneidungen, Übergänge von dicken zu dünnen Wänden und die Platzierung feiner Details auf gegenüberliegenden Seiten eines Kerns können zu Problemen bei der Formgebung führen. Es wird empfohlen, sich von erfahrenen Konstrukteuren beraten zu lassen.
F: Können beim MIM mehrere Materialien kombiniert werden?
A: Ja, MIM ermöglicht Multimaterialteile durch die Verwendung von Pulvermischungen oder mehreren Ausgangsmaterialien. Das Spritzgießen mit anderen Legierungen oder harten Materialien ist auch für Verbundstrukturen möglich.
F: Wie ist die Oberflächengüte von MIM-Teilen?
A: Die Oberfläche im gesinterten Zustand hat eine Rauheit von etwa 10-15 Mikrometern. Dies ist für viele Anwendungen geeignet. Durch zusätzliches Trommeln oder Polieren können die Oberflächen bei Bedarf weiter geglättet werden.
F: Wie lange dauert das MIM-Verfahren?
A: Die Vorlaufzeiten liegen in der Regel zwischen 6 und 12 Wochen. Die meiste Zeit nimmt die Herstellung von Formen in Anspruch. Sobald die Werkzeuge hergestellt sind, ist die Serienproduktion für kleine Komponenten recht schnell.