Visão geral
No âmbito da ciência e da engenharia de materiais, o "pó esferoidizante" tornou-se um componente essencial, principalmente na fabricação de aditivos metálicos, na metalurgia do pó e em campos relacionados. Esse tipo de pó passa por um processo exclusivo que altera sua morfologia, resultando em partículas esféricas que melhoram a fluidez, a densidade de empacotamento e o desempenho geral em várias aplicações. Mas o que é exatamente o pó esferoidizante? Por que ele é tão importante na fabricação avançada? Neste guia abrangente, exploraremos os prós e contras do pó esferoidizante, abordando tudo, desde sua composição e características até suas diversas aplicações e as vantagens que ele oferece. Também nos aprofundaremos em modelos específicos de pó metálico, garantindo que, ao final deste artigo, você tenha uma compreensão profunda desse material fascinante.
Entendendo o pó esferoidizante
O que é o pó esferoidizante?
O pó esferoidizado é um tipo de pó metálico que foi processado para obter um formato esférico. O processo de esferoidização normalmente envolve tratamento térmico ou técnicas de atomização que transformam partículas de formato irregular em partículas lisas e redondas. Essa modificação melhora significativamente a fluidez do pó, reduz a relação entre a área da superfície e o volume e aumenta sua densidade de empacotamento. Essas características tornam os pós esferoidizados altamente desejáveis em setores como manufatura aditiva, metalurgia do pó e aplicações de revestimento.
Por que a esferoidização é importante?
Você pode se perguntar: por que se dar ao trabalho de tornar o pó metálico esférico? A resposta está no desempenho aprimorado que esses pós oferecem. Os pós esféricos têm melhores características de fluxo, o que é crucial para processos como a impressão 3D, em que o fluxo consistente de material é essencial para a criação de peças de alta qualidade. Além disso, esses pós são mais densos, o que pode melhorar as propriedades mecânicas do produto final. A área de superfície reduzida também significa menos oxidação e contaminação, levando a produtos finais mais puros.
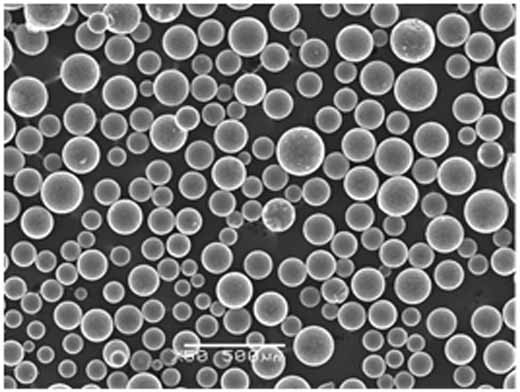
Aplicações do pó esferoidizante
O pó esferoidizante não é uma solução única para todos os casos. Sua aplicação depende do tipo de metal, das propriedades desejadas do produto final e do processo de fabricação. Aqui está uma rápida olhada em algumas das principais áreas em que os pós esferoidizados são usados:
Aplicativo | Descrição |
---|---|
Manufatura aditiva (impressão 3D) | Usado para produzir componentes altamente detalhados e resistentes com fluxo de material e deposição de camadas consistentes. |
Metalurgia do pó | Essencial na produção de peças metálicas densas e resistentes por meio de processos de compactação e sinterização. |
Revestimentos por spray térmico | Melhora a qualidade dos revestimentos, garantindo distribuição uniforme e forte adesão ao substrato. |
Moldagem por injeção de metal (MIM) | Melhora a fluidez da matéria-prima e a densidade e as propriedades mecânicas do produto final. |
Tratamento de superfície | Usado em técnicas de modificação de superfície para melhorar a resistência ao desgaste, a dureza e a resistência à corrosão. |
Composição do pó esferoidizante
Elementos-chave do pó esferoidizante
A composição do pó de esferoidização é feita sob medida para atender aos requisitos de aplicações específicas. Em geral, esses pós consistem em um metal de base, elementos de liga e, ocasionalmente, pequenas quantidades de outros compostos para melhorar determinadas propriedades. Aqui está um detalhamento dos elementos comuns encontrados em vários pós de esferoidização:
Elemento | Papel na esferoidização do pó |
---|---|
Ferro (Fe) | Comum em pós à base de aço e ferro, proporcionando resistência e dureza. |
Alumínio (Al) | Leve e resistente à corrosão, geralmente usado em aplicações aeroespaciais e automotivas. |
Titânio (Ti) | Alta relação resistência/peso, ideal para aplicações de alto desempenho, como aeroespacial e médica. |
Níquel (Ni) | Aumenta a resistência à corrosão e a tenacidade, sendo frequentemente usado em superligas para aplicações de alta temperatura. |
Cobre (Cu) | Oferece excelente condutividade elétrica, usada em eletrônicos e gerenciamento térmico. |
Cobalto (Co) | Melhora a resistência ao desgaste e a dureza, comumente usado em ferramentas de corte e aplicações de alta resistência. |
Cromo (Cr) | Adiciona resistência à corrosão e dureza, usado em aço inoxidável e aplicações resistentes ao desgaste. |
Cada um desses elementos pode ser combinado em várias proporções para criar pós com características específicas adequadas a diferentes aplicações industriais.
Características do pó esferoidizante
Propriedades físicas e químicas
As propriedades do pó para esferoidização são influenciadas por sua composição e pelo processo de esferoidização. Veja a seguir algumas das principais características:
Propriedade | Descrição |
---|---|
Distribuição do tamanho das partículas | Normalmente, varia de 15 a 150 mícrons, afetando a fluidez e a densidade de empacotamento. |
Morfologia | Formato esférico com superfícies lisas, o que aumenta a fluidez e reduz o atrito. |
Fluidez | Alta taxa de fluxo devido ao formato esférico, crucial para o fornecimento consistente de material em processos de AM. |
Densidade aparente | Maior densidade em comparação com pós irregulares, melhorando as propriedades mecânicas do produto final. |
Resistência à oxidação | A área de superfície reduzida minimiza a oxidação, crucial para manter a pureza durante o processamento. |
Estabilidade térmica | Estáveis em altas temperaturas, o que os torna adequados para aplicações em altas temperaturas. |
Essas propriedades tornam os pós esferoidizantes ideais para processos que exigem alta precisão, repetibilidade e desempenho superior do material.
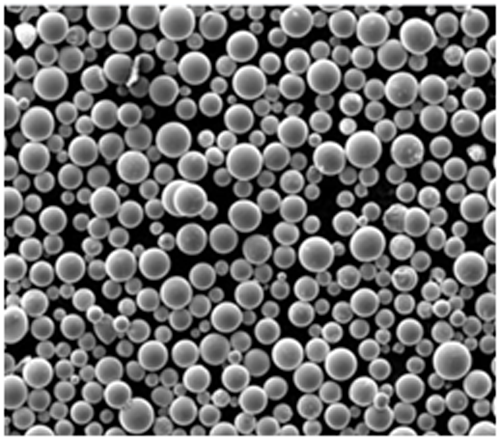
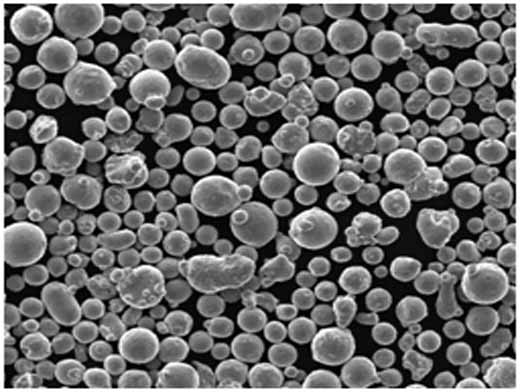
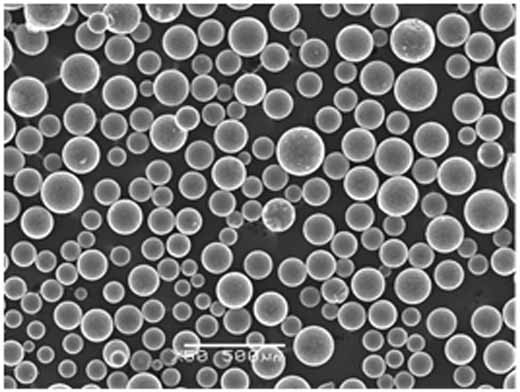
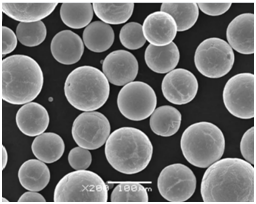
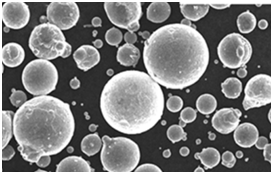
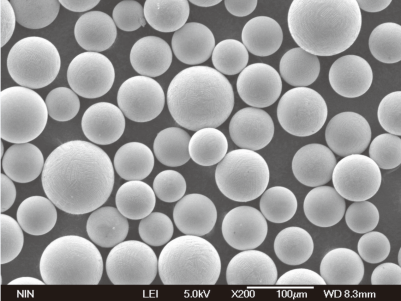
Modelos específicos de pós metálicos
Para lhe dar uma visão mais clara do que está disponível no mercado, aqui estão dez modelos específicos de pós esferoidizantes, cada um deles projetado para aplicações e setores específicos:
1. Pó esférico à base de Fe
- Composição: Principalmente ferro, com traços de carbono e outros elementos de liga.
- Propriedades: Alta resistência, boa resistência ao desgaste e estabilidade térmica.
- Formulários: Metalurgia do pó, componentes automotivos, ferramentas industriais.
2. Pó esférico de AlSi10Mg
- Composição: Alumínio com 10% de silício e 0,4% de magnésio.
- Propriedades: Leve, excelente condutividade térmica e boas propriedades mecânicas.
- Formulários: Componentes estruturais aeroespaciais, automotivos e leves.
3. Pó esférico de Ti6Al4V
- Composição: Titânio ligado com alumínio 6% e vanádio 4%.
- Propriedades: Alta relação resistência/peso, excelente resistência à corrosão.
- Formulários: Aeroespacial, implantes médicos, componentes de engenharia de alto desempenho.
4. Pó esférico de aço inoxidável 316L
- Composição: Ferro, cromo, níquel e molibdênio.
- Propriedades: Resistente à corrosão, boas propriedades mecânicas, biocompatível.
- Formulários: Dispositivos médicos, equipamentos de processamento de alimentos, processamento químico.
5. Pó esférico de Inconel 718
- Composição: Superliga à base de níquel com cromo, nióbio e molibdênio.
- Propriedades: Excelente resistência a altas temperaturas, oxidação e corrosão.
- Formulários: Aeroespacial, turbinas a gás, aplicações de alta temperatura.
6. Pó esférico de CuCrZr
- Composição: Cobre ligado com cromo e zircônio.
- Propriedades: Alta condutividade elétrica e térmica, boas propriedades mecânicas.
- Formulários: Componentes elétricos, gerenciamento térmico, trocadores de calor.
7. Pó esférico de CoCrMo
- Composição: Cobalto, cromo e molibdênio.
- Propriedades: Excelente resistência ao desgaste, biocompatível, resistente à corrosão.
- Formulários: Implantes médicos, próteses dentárias, ferramentas de corte.
8. Pó esférico de aço maraging
- Composição: Liga de ferro-níquel com cobalto, molibdênio e titânio.
- Propriedades: Alta resistência, boa tenacidade, capacidade de endurecimento por envelhecimento.
- Formulários: Aeroespacial, ferramentas, aplicações de alta tensão.
9. Pó esférico de AlSi12
- Composição: Alumínio com silicone 12%.
- Propriedades: Leve, boa resistência à corrosão, fácil de fundir.
- Formulários: Componentes automotivos, aeroespaciais e de engenharia em geral.
10. Pó esférico de aço inoxidável 17-4 PH
- Composição: Ferro, cromo, níquel e cobre.
- Propriedades: Alta resistência, resistência à corrosão, boa soldabilidade.
- Formulários: Aeroespacial, processamento químico, ambientes marinhos.
Cada um desses pós foi projetado especificamente para atender às demandas de sua aplicação pretendida, demonstrando a versatilidade e a adaptabilidade dos pós esferoidizantes na fabricação moderna.
Vantagens do pó esferoidizante
Por que escolher os pós esferoidizados?
Os pós esferoidizados oferecem uma série de benefícios que os fazem se destacar em comparação com seus equivalentes irregulares. Vamos detalhar algumas das principais vantagens:
Vantagens | Descrição |
---|---|
Fluidez aprimorada | O formato esférico permite melhores características de fluxo, o que é crucial em processos como a impressão 3D. |
Maior densidade de embalagem | As partículas esféricas se agrupam mais estreitamente, melhorando a densidade e as propriedades mecânicas da peça final. |
Oxidação reduzida | A menor área de superfície reduz as chances de oxidação, levando a uma maior pureza e a produtos finais de melhor qualidade. |
Estabilidade térmica aprimorada | Os pós esféricos são mais estáveis em altas temperaturas, o que os torna ideais para aplicações em ambientes extremos. |
Melhor acabamento de superfície | As partículas esféricas lisas produzem melhores acabamentos de superfície em processos de revestimento e impressão. |
Qualidade consistente | A forma uniforme e a distribuição de tamanho levam a resultados mais previsíveis e repetíveis em diferentes lotes. |
Essas vantagens fazem com que os pós esferoidizados sejam a escolha preferida nos setores em que a precisão, o desempenho e a confiabilidade são fundamentais.
Comparação entre o pó esferoidizante e os pós metálicos tradicionais
Pó esferoidizante vs. pó irregular
Quando se trata de selecionar o pó certo para sua aplicação, é essencial entender as diferenças entre os pós esferoidizados e os pós irregulares tradicionais. Veja a seguir uma comparação:
Aspecto | Pó para esferoidização | Pó Irregular Tradicional |
---|---|---|
Forma | Esférico, liso | Formas irregulares e variadas |
Fluidez | Excelente | Moderado a ruim, dependendo da forma e do tamanho |
Densidade da embalagem | Alta | Menor, devido a formas irregulares |
Resistência à oxidação | Melhor, devido à menor área de superfície | Maior potencial de oxidação, mais área de superfície exposta |
Estabilidade térmica | Geralmente mais alto | Varia de acordo com a composição |
Qualidade do acabamento da superfície | Superior, devido ao formato consistente das partículas | Menor, devido à morfologia mais áspera das partículas |
Custo | Geralmente mais alto devido ao processamento adicional | Processo de produção menor e mais simples |
Embora os pós esferoidizantes tendam a ser mais caros, seu desempenho superior em áreas importantes geralmente justifica o custo adicional, especialmente em setores de alta precisão.
Aplicações do pó esferoidizante
Manufatura aditiva (impressão 3D)
Uma das aplicações mais importantes do pó esferoidizante é a manufatura aditiva, especialmente na impressão 3D de metais. A alta fluidez e a densidade de empacotamento desses pós permitem a deposição precisa de camadas de material, o que é fundamental para a produção de componentes detalhados e estruturalmente sólidos.
- Benefícios: Fluxo de material consistente, propriedades mecânicas aprimoradas e acabamento superficial superior.
- Setores: Aeroespacial, automotivo, dispositivos médicos.
Metalurgia do pó
Na metalurgia do pó, a capacidade de produzir peças densas e resistentes é fundamental. Os pós esferoidizantes oferecem as características necessárias para atingir esses objetivos por meio de processos de compactação e sinterização.
- Benefícios: Maior densidade, propriedades mecânicas aprimoradas e qualidade consistente.
- Setores: Automotivo, ferramentas industriais, maquinário.
Revestimentos por spray térmico
Os pós esferoidizantes também são amplamente utilizados em revestimentos de spray térmico, em que seu formato esférico garante uma distribuição uniforme e uma forte adesão ao substrato.
- Benefícios: Maior resistência ao desgaste, proteção contra corrosão e revestimentos mais duradouros.
- Setores: Aeroespacial, maquinário industrial, marítimo.
Moldagem por injeção de metal (MIM)
Na moldagem por injeção de metal, a fluidez da matéria-prima é fundamental para a produção de peças complexas com alta precisão. Os pós esferoidizantes fornecem as características necessárias para atingir esse objetivo.
- Benefícios: Melhor fluidez, densidade de peças aprimorada e propriedades mecânicas superiores.
- Setores: Dispositivos médicos, eletrônicos de consumo, automotivos.
Tratamento de superfície
Os pós esferoidizantes são usados em processos de tratamento de superfície para melhorar a resistência ao desgaste, a dureza e a resistência à corrosão dos componentes. Seu formato esférico garante um revestimento uniforme e melhora o desempenho geral da superfície tratada.
- Benefícios: Maior durabilidade, vida útil prolongada dos componentes e desempenho aprimorado.
- Setores: Maquinário industrial, automotivo, aeroespacial.
Especificações e padrões para pó esferoidizante
Principais especificações e padrões
Ao selecionar o pó esferoidizante para sua aplicação, é importante considerar as especificações e os padrões aplicáveis. Aqui está uma tabela que resume alguns dos principais aspectos:
Especificação | Descrição |
---|---|
Distribuição do tamanho das partículas | Normalmente, varia de 15 a 150 mícrons, dependendo dos requisitos da aplicação. |
Pureza | Altos níveis de pureza, geralmente 99% ou superior, para minimizar impurezas e defeitos no produto final. |
Vazão | Medido em segundos para um determinado volume, indicando a capacidade do pó de fluir suavemente. |
Densidade aparente | Uma medida de quão apertado é o empacotamento do pó, normalmente maior para pós esferoidizados. |
Esfericidade | Medida de quão esféricas são as partículas, normalmente próxima de 1 para pós de alta qualidade. |
Padrões | Os padrões comuns incluem ASTM, ISO e DIN, que especificam os requisitos de tamanho, composição e qualidade das partículas. |
A adesão a essas especificações garante que o pó escolhido atenda aos critérios de desempenho necessários para a sua aplicação específica.
Fornecedores e preços
Principais fornecedores e detalhes de preços
Encontrar o fornecedor certo de pó esferoidizante é fundamental para garantir qualidade consistente e fornecimento confiável. Veja aqui alguns dos principais fornecedores e detalhes de preços:
Fornecedor | Localização | Linha de produtos | Preços (aproximados) | Clientes notáveis |
---|---|---|---|---|
Manufatura aditiva da Sandvik | Suécia | Ampla gama de pós metálicos | $50 - $150/kg | Aeroespacial, médico, industrial |
Höganäs AB | Suécia | Pós metálicos de alta qualidade | $40 - $120/kg | Automotivo, Industrial, Eletrônico |
Tecnologia Carpenter | EUA | Pós de ligas especiais | $60 - $180/kg | Aeroespacial, Energia, Industrial |
AP&C (GE Additive) | Canadá | Pós à base de titânio e níquel | $70 - $200/kg | Aeroespacial, médico, automotivo |
Tecnologia LPW (Tecnologia Carpenter) | REINO UNIDO | Pós específicos para AM | $55 - $160/kg | Aeroespacial, médico, industrial |
Os preços podem variar de acordo com fatores como composição do pó, distribuição do tamanho das partículas e volume do pedido. É sempre uma boa ideia solicitar amostras e realizar testes completos para garantir que o pó atenda às suas necessidades específicas.
Prós e contras do pó esferoidizante
Vantagens e desvantagens
Embora os pós esferoidizantes ofereçam muitas vantagens, eles têm suas desvantagens. Aqui está uma análise equilibrada dos prós e contras:
Prós | Contras |
---|---|
Fluidez aprimorada | Custo mais alto: O processo de esferoidização aumenta o custo total. |
Maior densidade de embalagem | Fabricação complexa: Requer equipamentos e tecnologia avançados. |
Oxidação reduzida | Disponibilidade limitada: Nem todos os metais são facilmente esferoidizados. |
Acabamento de superfície aprimorado | Potencial de contaminação: O manuseio deve ser cuidadosamente gerenciado para evitar contaminação. |
Qualidade consistente | Prazos de entrega mais longos: Os pós personalizados podem ter tempos de produção mais longos. |
A compreensão desses prós e contras pode ajudá-lo a tomar uma decisão informada ao selecionar o pó esferoidizante para o seu projeto.
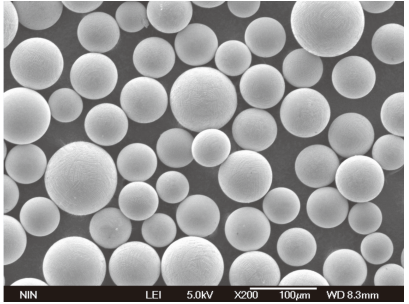
Perguntas frequentes
Pergunta | Resposta |
---|---|
O que é pó esferoidizante? | O pó esferoidizante é um tipo de pó metálico processado para obter um formato esférico para melhorar a fluidez e a densidade de empacotamento. |
Por que o pó esférico é melhor? | Os pós esféricos oferecem melhor fluidez, maior densidade de empacotamento, redução da oxidação e melhor acabamento superficial em comparação com os pós irregulares. |
Quais setores utilizam o pó esferoidizante? | Setores como o aeroespacial, automotivo, médico e de manufatura industrial usam pó esferoidizante para várias aplicações. |
Como o pó esferoidizante é fabricado? | O pó esferoidizante é normalmente produzido por meio de processos de atomização ou tratamento térmico que arredondam as partículas em um formato esférico. |
Quais são as principais especificações a serem consideradas? | As principais especificações incluem distribuição do tamanho das partículas, pureza, taxa de fluxo, densidade aparente e esfericidade. |
O pó esferoidizante é mais caro? | Sim, os pós esferoidizantes geralmente são mais caros devido ao processamento adicional necessário para atingir o formato esférico. |