Estudo sobre revestimento a laser de revestimento em pó à base de níquel
Introdução
Revestimento a laser é o uso da tecnologia a laser para revestir a superfície do substrato a fim de obter as propriedades necessárias. O sistema de ligas de revestimento a laser inclui principalmente ligas à base de ferro, ligas à base de níquel, ligas à base de cobalto e cermet. O revestimento a laser de pó de liga à base de ferro é adequado para peças que precisam ser parcialmente desgastadas e fáceis de deformar. O substrato do revestimento de liga à base de ferro é principalmente ferro fundido e aço de baixo carbono. Os revestimentos de liga à base de níquel são adequados para componentes que exigem resistência parcial ao desgaste, resistência à corrosão térmica e resistência à fadiga térmica, e a densidade de potência do laser necessária é um pouco maior do que a do revestimento de ligas à base de ferro. Os revestimentos de liga à base de cobalto são adequados para peças que exigem resistência ao desgaste, à corrosão e à fadiga térmica. O revestimento cerâmico tem alta resistência a altas temperaturas, boa estabilidade térmica, alta estabilidade química e uma ampla variedade de materiais de matriz. Neste artigo, são discutidos os materiais em pó de liga autofusível à base de níquel usados no revestimento a laser.
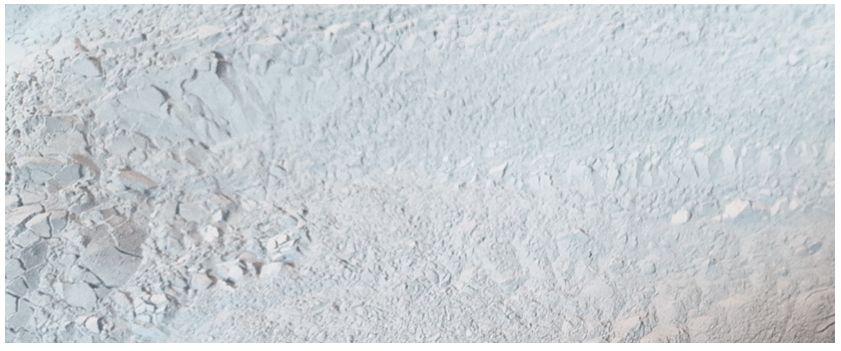
Materiais e métodos
O Pó de liga de autofusão à base de níquel usado neste experimento foi preparado e fundido por atomização de gás. Os fatores a serem considerados no projeto da composição do pó e no projeto da formulação da matéria-prima de fundição incluem principalmente: tanto o desempenho do pó quanto o processo de revestimento a laser, o pó deve ter um baixo ponto de fusão e teor de oxigênio. Para evitar rachaduras no revestimento, a camada de revestimento e o substrato devem ser combinados o máximo possível, ou seja, o coeficiente de expansão térmica do revestimento e do substrato deve ser o mais próximo possível. A molhabilidade e a reação do pó devem ser boas.
Com base nos fatores acima, por meio do projeto repetido da composição do material e do teste de desempenho do processo de soldagem por pulverização, o seguinte pó de liga autofusível à base de níquel BNi-3 (AMS 4778) com tamanho de partícula de 45-105um é selecionado como o material de revestimento do laser (fração de massa %), sua composição química é mostrada em Tabela 1. O material de base para o revestimento a laser é aço carbono médio. E a espessura da camada de revestimento é de 0,6 mm.
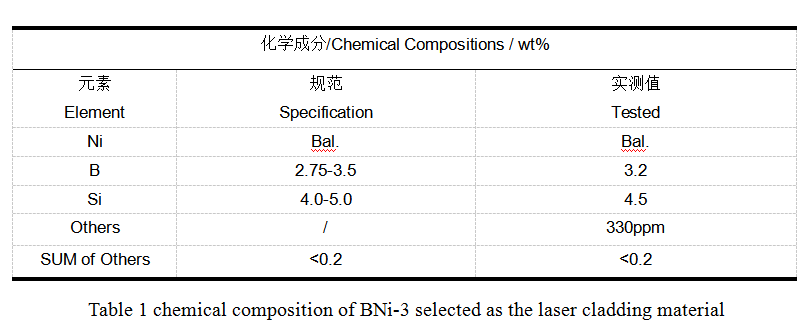
Figura 1 mostra a morfologia da partícula de BNi-3 selecionada como o material de revestimento a laser. É possível observar que as partículas de pó são esféricas. O pó esférico faz com que o pó tenha boa fluidez, de modo que o pó possa atingir a superfície da peça de trabalho de maneira uniforme e suave a partir do alimentador de pó, sem bloquear o bocal de pó. Se o formato do pó for complexo, a fluidez é ruim, o que facilita o transporte da pulsação do pó. Além disso, se a área da superfície do pó aumentar, o pó será oxidado quando for aquecido em alta temperatura, de modo que a qualidade da camada de revestimento será afetada.
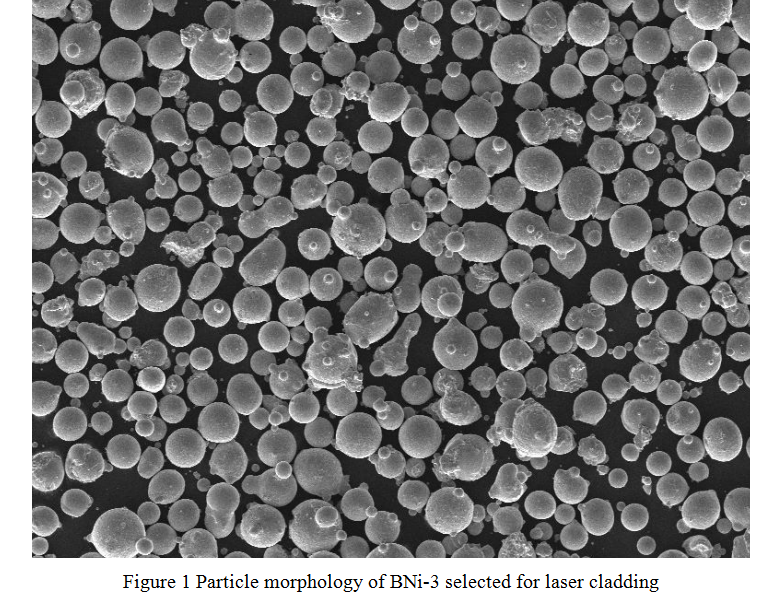
O teste de processo mostra que o níquel faz com que o pó tenha um bom desempenho no processo de revestimento e pode melhorar o desempenho em altas temperaturas e a resistência a rachaduras do pó. O silício na liga aumenta a dureza do revestimento, e o boro e o silício podem tornar o pó da liga autofusível. No pó de liga autofusível, o boro e o silício podem formar escória por si mesmos, o que tem efeito de autoproteção. A análise mostra que o Ni2B e o Ni3B com baixo ponto de fusão são formados por boro e níquel, o que reduz o ponto de fusão da liga e melhora o desempenho do processo do pó. No entanto, se o teor de boro na liga for muito alto, haverá mais compostos de boro e compostos de óxido de silicato frágeis no limite do grão, de modo que a plasticidade e a tenacidade do revestimento serão reduzidas, a fragilidade será aumentada e a camada de revestimento estará propensa a rachaduras, portanto, o teor de boro deve ser controlado dentro da faixa adequada.
Figura 2 mostra a seção transversal da camada de revestimento. Da camada superficial até o núcleo, a zona da camada de revestimento, a zona afetada pelo calor e a matriz são sucessivas. A zona da camada de revestimento é uma zona brilhante muito estreita, que é mais estreita do que a zona de ligação metalúrgica obtida por pulverização térmica, soldagem de superfície e outros métodos. A zona afetada pelo calor é equivalente ao tratamento térmico devido à condução de calor. Com o aumento da distância da zona da camada de revestimento, a temperatura de aquecimento diminui continuamente, portanto, da zona de transição de fase, parte da zona de transição de fase e, finalmente, para a estrutura original da matriz.
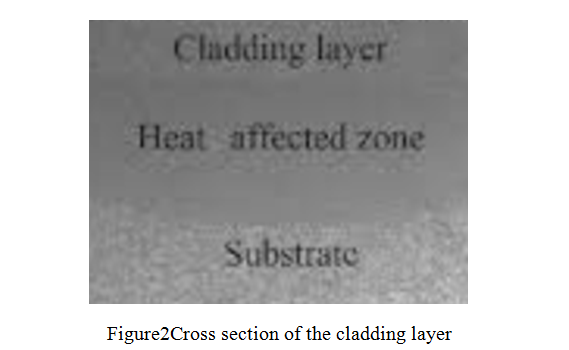
Nesse projeto, a resistência ao desgaste da amostra revestida com esse pó foi comparada com o bloco de teste padrão AISI 52100 com 62 HRC nas condições de teste da máquina de teste de desgaste doméstica MM-200, com velocidade de 380 r/min, atrito seco, tempo de 1,5 h. A resistência ao desgaste é determinada pela medição da perda de peso das amostras após o desgaste. Os resultados mostraram que a resistência ao desgaste da camada de reforço da superfície de revestimento a laser do pó de BNi-3 à base de níquel é melhor do que o do AISI 52100, de modo que a vida útil das peças resistentes ao desgaste será significativamente melhorada.