A moldagem por injeção de metal (MIM) é um processo de metalurgia usado para fabricar peças pequenas e complexas usando metal em pó e plástico. A MIM combina a flexibilidade de design da moldagem por injeção de plástico com a resistência e a integridade dos metais usinados. Ele permite a fabricação econômica de componentes com dimensões que variam de 1 grama a 500 gramas.
O Processo MIM produz peças com excelentes propriedades mecânicas, tolerâncias de precisão e acabamentos de superfície suaves. Isso torna a MIM adequada para a fabricação de componentes metálicos pequenos, complexos e com formato de rede em grandes volumes para setores como o automotivo, médico, aeroespacial, eletrônico e outros.
Este guia oferece uma visão geral completa do processo MIM, suas aplicações, vantagens, considerações de projeto, equipamentos, materiais, pós-processamento, controle de qualidade e análise de custos. Ele inclui tabelas e comparações detalhadas para ajudar engenheiros, designers de produtos e gerentes de compras a conhecer e avaliar o processo MIM.
Visão geral do processo MIM
A moldagem por injeção de metal combina técnicas de moldagem por injeção de plástico com processos de metalurgia do pó. As etapas básicas do processo MIM são:
- Mixagem: Mistura de pó metálico fino com um aglutinante plástico para criar uma matéria-prima homogênea
- Moldagem por injeção: Aquecimento e injeção da matéria-prima em um molde para formar uma parte verde modelada
- Desbobinamento: Remoção do aglutinante plástico da peça verde moldada por meio de processos térmicos ou com solvente
- Sinterização: Aquecimento da peça desbastada até um pouco abaixo do ponto de fusão do pó para densificar a peça por meio de difusão atômica e formar uma peça metálica sólida.
A tabela a seguir resume os principais estágios do processo de MIM:
Estágio | Descrição |
---|---|
Mistura | Mistura de pó metálico fino com aglutinantes em uma matéria-prima homogênea |
Moldagem por injeção | Aquecimento e injeção de matéria-prima em um molde para formar uma peça verde |
Rebarbação | Remoção do aglutinante por meio de solventes ou processos térmicos |
Sinterização | Aquecimento da peça desbastada para densificar o pó e formar a peça metálica |
O processo MIM produz componentes metálicos consistentes e de alta qualidade, adequados para a fabricação de grandes volumes. O processo é altamente repetível e pode criar geometrias complexas com tolerâncias estreitas que não são possíveis com outras técnicas de fabricação.
Aplicações e uso de peças MIM no setor
A MIM é usada em muitos setores para fabricar componentes metálicos pequenos, complexos e com formato de rede, com tolerâncias rígidas.
A tabela a seguir descreve as principais áreas de aplicação e exemplos de peças fabricadas por MIM:
Setor | Exemplos de aplicativos |
---|---|
Automotivo | Engrenagens, rodas dentadas, balancins, bielas |
Aeroespacial | Lâminas de turbina, impulsores, bicos, válvulas |
Médico | Braquetes ortodônticos, instrumentos cirúrgicos, implantes |
Eletrônicos | Conectores, microgarras, telas, bicos de impressora |
Armas de fogo | Gatilhos, martelos, cofres, ejetores |
Relógios | Engrenagens, pinhões, ponteiros de relógio |
A MIM permite a produção de pequenas peças de precisão com geometrias complexas que, de outra forma, exigiriam usinagem extensiva ou outras operações secundárias. Ela oferece liberdade de projeto, consolidação de peças e redução de peso em comparação com as alternativas de fabricação.
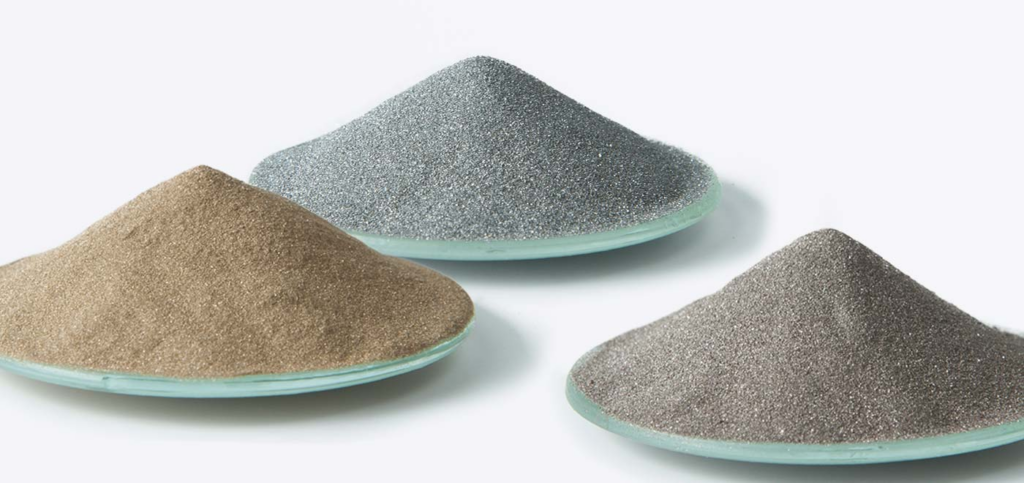
Vantagens e benefícios do MIM
O MIM oferece vários benefícios em relação a outros processos de fabricação de peças metálicas pequenas:
Liberdade de design
- É possível moldar geometrias e formas 3D complexas que são difíceis ou impossíveis com outros métodos.
- Recursos complexos como roscas, cavidades e furos podem ser facilmente incorporados aos projetos MIM.
- Permite a consolidação de peças e a redução da montagem em comparação com a usinagem de vários componentes.
Precisão e tolerâncias
- A precisão dimensional consistente e as tolerâncias de até ±0,1% podem ser mantidas usando MIM.
- É possível obter detalhes finos com bons acabamentos de superfície de até 0,5 μm Ra.
Propriedades do material
- As peças MIM sinterizadas normalmente atingem 95-99% das densidades dos metais forjados.
- É possível usar uma ampla variedade de materiais, como aço inoxidável, aço para ferramentas, ligas de titânio e ligas de tungstênio.
- Excelentes propriedades mecânicas com a rigidez, a força, a dureza e a resistência ao desgaste dos metais moldados.
Produtividade e custos
- É possível obter altas taxas de produção com tempos de ciclo rápidos usando MIM.
- Custos de peças mais baixos do que a usinagem CNC para volumes médios e altos.
- Custos mais baixos do que a fundição por cera perdida para projetos complexos e com vários componentes.
- Elimina as operações de usinagem secundária necessárias para componentes metálicos fabricados.
Sustentabilidade
- Desperdício mínimo de material, uma vez que o MIM usa processamento quase em forma de rede.
- Processo de metalurgia do pó com menor consumo de energia do que a usinagem ou fundição de metais.
- Permite a redução do peso por meio da otimização das geometrias, o que reduz a pegada ambiental.
A tabela a seguir resume as principais vantagens do MIM e o compara a outros processos:
Vantagens | Comparação com outros processos |
---|---|
Liberdade de design | Mais flexibilidade do que a usinagem ou a fundição de metais |
Precisão | Muito superior à fundição em areia ou fundição sob pressão |
Propriedades do material | Aborda os metais forjados de forma diferente da metalurgia do pó |
Produtividade | Volumes maiores do que a usinagem CNC |
Custo-benefício | Custos mais baixos do que a usinagem CNC ou a fundição por cera perdida para volumes médios ou maiores |
Sustentabilidade | Menos desperdício do que os processos subtrativos, como a usinagem CNC |
A MIM combina a liberdade geométrica da moldagem por injeção de plástico com propriedades materiais próximas às dos metais totalmente densos. Isso permite que os projetistas de produtos consolidem montagens, otimizem componentes e fabriquem peças metálicas complexas e de alto valor a custos competitivos.
Considerações sobre o design de peças MIM
O projeto adequado da peça é fundamental para maximizar os benefícios do processo MIM. Algumas considerações importantes sobre o projeto incluem:
Espessuras de parede - Recomenda-se espessuras de parede moderadas entre 0,8 mm e 5 mm. Seções excessivamente grossas ou finas podem causar defeitos.
Tolerâncias - Tolerâncias de precisão de ±0,1% das dimensões são possíveis, mas permitem o encolhimento da sinterização.
Acabamentos de superfície - É possível obter acabamentos finos de superfície abaixo de 1 μm Ra, dependendo da superfície da ferramenta, das geometrias e das operações de pós-moldagem.
Geometria - Evitar geometrias excessivamente delicadas e manter a integridade estrutural é importante para evitar defeitos. Preferencialmente, ângulos de inclinação mínimos acima de 1-2°.
Recursos - Furos de até 0,5 mm de diâmetro, roscas e recursos internos complexos podem ser incorporados ao design MIM.
Tamanho da peça - Componentes menores, entre 0,5 e 500 gramas, são ideais para o processamento MIM. Peças maiores podem exigir usinagem CNC.
Montagem - Projete para a consolidação de peças, combinando componentes e montagens complexas em peças MIM únicas.
O projeto adequado do componente MIM otimiza a capacidade de fabricação, minimiza os defeitos e aproveita as principais vantagens do processo MIM. É altamente recomendável consultar os fornecedores de MIM durante a fase de projeto.
Equipamentos e ferramentas MIM
Equipamentos especializados são usados nas etapas de preparação de matéria-prima, moldagem, desbobinamento e sinterização do processo MIM:
Mistura e preparação da matéria-prima
- Misturadores - Misturadores de alta intensidade para homogeneidade da matéria-prima
- Moinhos - Moinhos de cesto ou moinhos de rolos para redução de partículas finas
- Controladores de temperatura - Para regular as temperaturas da matéria-prima
- Desgaseificação - Unidades de vácuo para remover bolhas de ar presas
Moldagem por injeção
- Máquinas de moldagem por injeção - Máquinas modificadas para lidar com matérias-primas MIM
- Moldes - Normalmente feitos de aços para ferramentas/inoxidáveis tratados termicamente para resistir à sinterização
- Controles de temperatura do molde - Para regular as temperaturas do molde durante a moldagem
Rebarbação
- Câmaras de remoção de ligantes por solvente - Para extração de ligantes por solvente
- Autoclaves de remoção de resíduos a vapor - Para processos de remoção de resíduos a vapor
- Fornos de desbobinamento térmico - Para remover aglutinantes por meio de processos térmicos
Sinterização
- Fornos de sinterização - Fornos a vácuo, a hidrogênio ou a nitrogênio
- Sistemas de controle de atmosfera - Para regular as atmosferas do forno
- Controles de perfil de temperatura - Para execução de ciclos de sinterização otimizados
A configuração e a calibração adequadas do equipamento MIM são vitais para componentes de alta qualidade e sem defeitos. O estágio de moldagem por injeção requer os equipamentos mais especializados, como moldes de alta temperatura.
Materiais MIM
Uma grande variedade de metais, ligas e cerâmicas pode ser processada com a tecnologia MIM. Alguns dos materiais MIM comuns incluem:
Metais
- Aços inoxidáveis (316L, 17-4PH, 410)
- Aços para ferramentas (H13, P20, D2)
- Aços de baixa liga (4140)
- Ligas magnéticas
- Ligas de cobre
- Ligas de titânio
- Ligas pesadas de tungstênio
Cerâmica
- Alumina
- Zircônia
- Nitreto de silício
- Carbetos
A seleção do material depende de fatores como temperaturas de sinterização, custo, propriedades mecânicas e físicas e necessidades de processamento secundário. O aço inoxidável 316L é o material MIM mais comum devido à sua excelente sinterabilidade.
A tabela abaixo mostra os materiais MIM comuns e suas aplicações típicas:
Material | Formulários |
---|---|
Aço inoxidável 316L | Instrumentos cirúrgicos, bombas, válvulas |
Aço ferramenta H13 | Moldagem por injeção, extrusão, matrizes |
Titânio Ti-6Al-4V | Aeroespacial, implantes médicos |
Ligas pesadas de tungstênio | Proteção contra radiação, amortecimento de vibrações |
Ligas de cobre | Contatos elétricos, gerenciamento térmico |
Cerâmica | Ferramentas de corte, peças de desgaste, balística |
A MIM permite o uso de materiais de alto desempenho, como titânio e ligas de aço para ferramentas, em projetos de componentes pequenos e complexos. Ela amplia as possibilidades de design para aplicações médicas, aeroespaciais, automotivas e industriais.
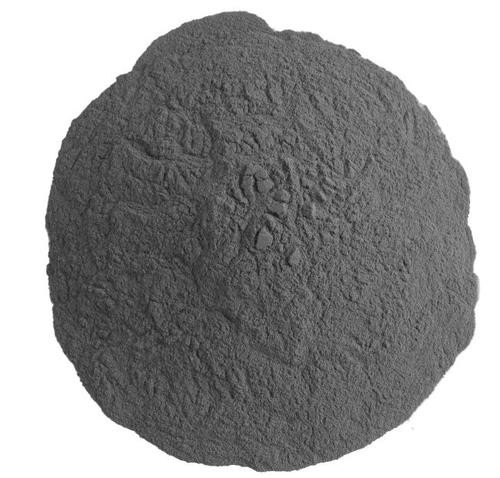
Operações de pós-processamento
As etapas de processamento secundário geralmente são necessárias após a sinterização MIM para obter a peça final:
- Recozimento - Tratamento térmico para alívio de tensões
- Endurecimento - Processo de endurecimento térmico, como austemperação
- Usinagem - Recursos de usinagem CNC, como diâmetros de furo de precisão
- Unir-se - Subcomponentes de soldagem a laser, solda ou colagem de epóxi
- Acabamento - Chapeamento, pintura, passivação ou outro acabamento de superfície
A tabela abaixo descreve os processos comuns pós-MIM e suas finalidades:
Pós-processo | Finalidade |
---|---|
Recozimento | Alívio de tensão, ductilidade |
Endurecimento | Melhoria da dureza e da resistência |
Usinagem | Dimensões e ajustes críticos |
Unir-se | Montagem de produtos com várias partes |
Acabamento | Aparência, resistência à corrosão |
O pós-processamento amplia as opções de aprimoramento de propriedades e usinagem de precisão. Isso amplia ainda mais a aplicabilidade do MIM em aplicações exigentes.
Controle de qualidade e inspeção
A qualidade consistente e o controle dimensional são essenciais para os componentes MIM. Os testes típicos de controle de qualidade incluem:
- Análise química - Para composição usando espectroscopia de emissão óptica ou de fluorescência de raios X
- Medições de densidade - Método de Arquimedes ou picnometria de gás para determinar a densidade sinterizada
- Testes mecânicos - propriedades de dureza, tração e fadiga de acordo com as normas ASTM
- Microscopia - Para análise de microestrutura, porosidade, tamanho de grão e defeitos
- Análise dimensional - Digitalização óptica ou por tomografia computadorizada para dimensões e conformidade com GD&T
- Análise de superfície - testes de rugosidade, corrosão e revestimento, conforme aplicável
A tabela a seguir descreve os principais testes de qualidade realizados durante os diferentes estágios do processamento de MIM:
Estágio | Testes de qualidade típicos |
---|---|
Matéria-prima | Viscosidade, torque, umidade |
Parte verde | Dimensões, inspeção de defeitos |
Rebarbação | Perda de peso, resíduos |
Sinterização | Densidade, ensaios químicos |
Acabamento | Dimensões, microscopia, propriedades mecânicas |
O controle de qualidade e a inspeção abrangentes em todas as etapas da MIM são necessários para obter componentes sem defeitos que atendam aos requisitos da aplicação.
Análise de custos
Os fatores a seguir determinam a economia do processo MIM:
- Ferramentas - O ferramental de matriz tem altos custos iniciais, dependendo das geometrias das peças. Várias cavidades nas ferramentas distribuem os custos em volumes maiores.
- Configurar - Configurações iniciais significativas da máquina e custos de desenvolvimento do processo.
- Material - Os metais em pó representam 10-15% do custo total da peça. Alto para materiais caros, como ligas de titânio.
- Trabalho - É necessária alguma mão de obra especializada, mas menos do que a usinagem CNC. Menor em grandes volumes.
- Processamento secundário - Pode aumentar significativamente os custos se houver necessidade de usinagem ou acabamento extensivos.
- Volume - Ideal para volumes de produção médios a altos, de 10.000 a milhões de peças. Oferece ótima vantagem de custo em relação a outros processos nessa faixa.
A tabela a seguir descreve os fatores indicativos de custo na fabricação de MIM:
Componente de custo do MIM | Detalhes |
---|---|
Ferramentas | $5.000 a $100.000+, dependendo da complexidade da peça |
Configuração | $10.000 a $50.000 para desenvolvimento de processos |
Materiais | 10-15% do custo da peça, maior para ligas caras |
Trabalho | Menor contribuição em relação à usinagem CNC |
Processamento secundário | $2 a $20 por peça, dependendo das operações |
Volume | Ideal para mais de 10.000 peças, custo mais baixo do que as alternativas |
A MIM oferece uma vantagem de custo em relação à usinagem e à fundição para volumes de produção médios a altos, desde que o processamento secundário seja mínimo. O processo oferece os maiores benefícios econômicos para projetos complexos e com vários componentes consolidados em uma única peça MIM.
Escolha de um fornecedor ou parceiro de MIM
A seleção de um fornecedor competente de MIM é fundamental para a produção econômica de componentes de alta qualidade. Alguns critérios para avaliar os fornecedores de MIM:
- Experiência - Número de anos no mercado e experiência em MIM. Os participantes de longa data tendem a ser mais confiáveis.
- Materiais -Variedade de ofertas de materiais, incluindo as principais ligas necessárias. Os recursos de nanopó melhoram as propriedades.
- Qualidade - Programa de qualidade robusto e certificações como ISO 9001 e ISO 13485. Evidência de controles de processo.
- Recursos de ferramentas - Oferecer ferramentas completas internamente proporciona uma melhor integração de custos e reduz os problemas.
- Processamento secundário - A disponibilidade de processos complementares, como usinagem e acabamento CNC, aumenta a conveniência.
- Prototipagem - A capacidade de prototipagem rápida em MIM reduz o tempo de execução e o custo.
- Competência em P&D - Ampla experiência em pesquisa e engenharia para inovação de processos.
A escolha de um fornecedor estabelecido com amplos recursos internos oferece uma solução robusta e contínua para projetos complexos de MIM. A proximidade geográfica também permite melhor colaboração e comunicação.
MIM em comparação com outros processos
MIM vs. usinagem CNC
- Custo - MIM com custo mais baixo em volumes médios e altos, CNC com custo efetivo em volumes baixos
- Design - Maior complexidade e melhor potencial de consolidação com o MIM
- Materiais - Maior variedade de materiais possível com MIM, incluindo aços para ferramentas e ligas de titânio
- Velocidade - Taxas de produção mais altas com MIM, tempos de ciclo mais lentos para usinagem CNC
- Desperdício - A MIM de formato quase líquido tem menor desperdício de material do que a usinagem CNC
MIM versus fundição de metal
- Resolução - Maior resolução e detalhes mais finos são possíveis com a MIM
- Complexidade - Maior complexidade geométrica possibilitada pela MIM
- Tolerâncias - Tolerâncias dimensionais muito mais rígidas que podem ser obtidas com a MIM
- Consistência - Propriedades e desempenho mais consistentes do material com MIM
- Usinagem secundária - Normalmente, a usinagem secundária necessária para peças MIM é menor
MIM vs. impressão 3D
- Custo - Atualmente, o MIM tem um custo mais baixo para produção de médio e alto volume
- Materiais - Maior variedade de ligas de alto desempenho, como aços para ferramentas, disponíveis no MIM
- Tolerâncias - Tolerâncias dimensionais mais precisas possíveis com MIM
- Propriedades mecânicas - Propriedades geralmente melhores e mais consistentes em comparação com os metais impressos em 3D
- Qualificação - Processo MIM já qualificado para aplicações aeroespaciais e médicas, ao contrário da impressão 3D
A MIM oferece benefícios em termos de complexidade, consistência e custo em relação a outros processos de fabricação de metal para componentes pequenos e de alta precisão fabricados em volumes médios ou superiores.
Limitações e desafios da MIM
Algumas das principais limitações e desvantagens do processo MIM incluem:
- Os altos custos iniciais de investimento em ferramentas impedem a produção de pequenas séries
- Capacidade limitada de tamanho, não ideal para peças acima de 500 gramas
- Geometria restrita devido à necessidade de desbastar e sinterizar os componentes
- Desafio de alcançar tolerâncias muito apertadas abaixo de ±0,5%
- Não recomendado para ligas exóticas que são difíceis de sinterizar
- Pode ser necessária uma usinagem secundária para obter ajustes e dimensões críticos
- Conhecimento significativo do processo necessário para a prevenção de defeitos durante a moldagem
- Os custos de equipamentos de capital para máquinas MIM podem ser substanciais
Para superar as limitações do MIM, é necessário fazer concessões no projeto, nos requisitos de tolerância e nas necessidades de processamento secundário. O processo é mais indicado para componentes pequenos complexos e de alta precisão do que para geometrias muito grandes ou básicas.
Desenvolvimentos da tecnologia MIM
Os desenvolvimentos recentes da tecnologia MIM que estão expandindo os recursos e a adoção incluem:
- Matérias-primas de nanopó - Melhoria da resistência e da microestrutura do sinterizado
- Ferramentas rápidas - Redução dos custos de moldes e dos prazos de entrega por meio de insertos impressos em 3D
- Jato de aglutinante - Permitindo a fabricação "print-then-sinter" na impressão 3D de metal
- MIM de titânio - Desenvolvimento de componentes de titânio com boa relação custo-benefício
- Injeção de baixa pressão - Para peças MIM maiores com tensões de ferramental reduzidas
- MIM de cerâmica - Ampliação para cerâmicas técnicas/estruturais além da alumina
- Integração com o setor 4.0 - Automatização e otimização do controle de qualidade
A inovação contínua no processo de MIM está ajudando a resolver as limitações, ampliar os recursos de materiais e expandir as aplicações em novos setores. Isso está permitindo que a MIM concorra efetivamente como uma tecnologia de fabricação de componentes metálicos de precisão.Copy
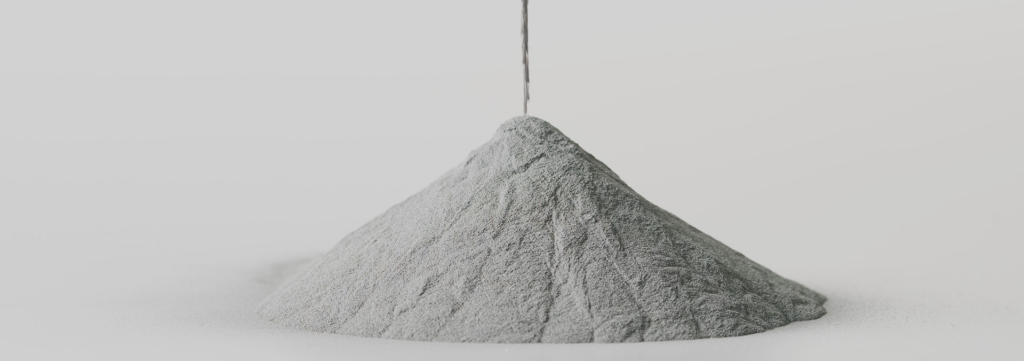
Perguntas frequentes
Aqui estão as respostas para algumas perguntas frequentes sobre o processo de moldagem por injeção de metal:
P: Que tipos de metais podem ser usados no MIM?
R: Uma grande variedade de metais e ligas pode ser processada com a tecnologia MIM, inclusive aços inoxidáveis, aços para ferramentas, ligas magnéticas, ligas de titânio, ligas pesadas de tungstênio e ligas de cobre. Os materiais comuns são o aço inoxidável 316L e 17-4PH, o aço para ferramentas H13 e o titânio Ti-6Al-4V.
P: Qual é o tamanho dos componentes que podem ser fabricados por MIM?
R: A faixa de tamanho ideal para MIM é de 0,5 a 500 gramas. Peças menores e maiores são possíveis, mas podem não ser econômicas. As peças em miniatura com menos de 0,5 gramas podem apresentar problemas de manuseio e processamento secundário. As peças maiores, acima de 500 gramas, exigem tensões mais altas nas ferramentas e tempos de ciclo mais longos.
P: Que precisão dimensional e tolerâncias são possíveis com o MIM?
R: A MIM pode alcançar tolerâncias dimensionais muito boas de até ±0,1% das dimensões. Entretanto, ±0,5% é mais comum para componentes de tolerância média. Tolerâncias abaixo de ±0,005 polegada (+/- 0,127 mm) exigem usinagem secundária. É necessário fazer concessões para a contração de sinterização.
P: Como o MIM se compara à moldagem por injeção de plástico?
R: O processo MIM é baseado na moldagem por injeção de plástico, mas usa matérias-primas de metal em pó em vez de resinas plásticas. O MIM permite a produção de componentes metálicos complexos e de alta resistência usando esse processo adaptado de moldagem por injeção com uma etapa adicional de sinterização.
P: Quais acabamentos de superfície podem ser produzidos em peças MIM?
R: A MIM é capaz de produzir acabamentos de superfície finos de até 0,5 mícron Ra, comparáveis a superfícies usinadas. Fatores como o sistema de aglutinação, o acabamento da ferramenta do molde, a geometria e o processamento secundário determinam a rugosidade final da superfície que pode ser alcançada.
P: Que tipos de geometrias complexas podem ser fabricadas por MIM?
R: Geometrias complexas com paredes finas, ângulos de inclinação negativos, rebaixos, cavidades cegas e formas não convencionais podem ser facilmente moldadas com MIM, pois a mistura de pó e aglutinante flui como um líquido para dentro do molde.
P: O MIM é bom para a fabricação de peças de protótipos?
R: A MIM não é ideal para prototipagem devido aos altos custos de ferramental e prazos de entrega envolvidos. Outros processos, como usinagem CNC, impressão 3D ou moldagem por injeção de alumínio, são mais adequados para peças de protótipos de baixo volume antes de se comprometer com o ferramental MIM.