Pó de CoCrMoW— pó de liga de Cobalto-Cromo-Molibdênio-Tungstênio — tornou-se um material muito procurado para indústrias como aeroespacial, implantes médicos e sistemas mecânicos de alto desempenho. Este pó metálico versátil, com suas excelentes propriedades mecânicas e resistência ao desgaste, corrosão e calor, o torna um elemento crucial em uma variedade de processos de fabricação avançados, como fabricação aditiva, moldagem por injeção de metal e revestimentos por pulverização térmica.
Mas o que torna o pó de CoCrMoW tão especial? Por que é uma escolha tão popular em ambientes exigentes? Se você está curioso sobre suas propriedades, aplicações e como ele se compara a outros pós, você veio ao lugar certo.
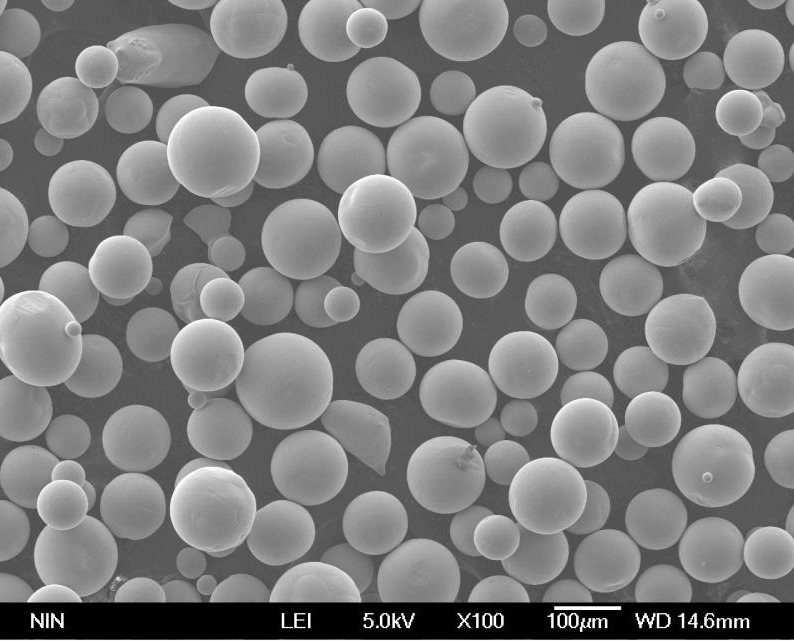
Visão geral do pó de CoCrMoW
Os pós de CoCrMoW pertencem a uma família de superligas compostas principalmente de cobalto, cromo, molibdênio e tungstênio, projetadas para oferecer excepcional resistência ao desgaste, resistência à corrosão e resistência a altas temperaturas. Esses pós são comumente usados em aplicações críticas onde os materiais convencionais podem ficar aquém devido a condições ambientais adversas.
Neste artigo, mergulharemos profundamente nos tipos específicos de pó de CoCrMoW, suas propriedades, aplicações e os prós e contras de usá-los em várias indústrias. Também abordaremos os principais fornecedores, preços e especificações técnicas.
Composição de Pó de CoCrMoW
A composição dos pós de CoCrMoW normalmente inclui uma mistura bem equilibrada de cobalto (Co), cromo (Cr), molibdênio (Mo) e tungstênio (W), com elementos de liga adicionais como carbono, silício e níquel para melhorar certas características. A composição precisa pode variar dependendo do tipo específico de pó, mas o cobalto forma a base da liga.
Abaixo está uma análise de uma composição típica de pó de CoCrMoW:
Elemento | Composição típica (%) |
---|---|
Cobalto (Co) | 55-65% |
Cromo (Cr) | 25-30% |
Molibdênio (Mo) | 5-10% |
Tungstênio (W) | 2-5% |
Carbono (C) | 0.1-0.5% |
Níquel (Ni) | 0-5% |
Principais elementos de liga e seu papel
- Cobalto (Co): Fornece excelente resistência à corrosão e mantém a resistência da liga em altas temperaturas.
- Cromo (Cr): Melhora a resistência à oxidação e a durabilidade geral.
- Molibdênio (Mo): Contribui para a resistência ao desgaste e aumenta a resistência da liga, particularmente sob estresse.
- Tungstênio (W): Melhora a capacidade da liga de suportar temperaturas extremas sem deformação.
Características do pó de CoCrMoW
O que torna o pó de CoCrMoW tão único? Vamos detalhar suas principais características:
1. Resistência a altas temperaturas
Devido à presença de cobalto e tungstênio, o pó de CoCrMoW mantém sua integridade estrutural mesmo em ambientes de alta temperatura. Isso o torna uma escolha ideal para peças usadas em motores a jato, turbinas e outras aplicações de alta temperatura.
2. Excelente resistência ao desgaste e à corrosão
Cobalto e cromo fornecem resistência robusta ao desgaste e à corrosão, o que é fundamental para aplicações no campo médico (por exemplo, implantes), petróleo e gás e ambientes marinhos.
3. Biocompatibilidade
As ligas de CoCrMoW são conhecidas por sua biocompatibilidade, tornando-as adequadas para aplicações médicas, especialmente implantes como articulações do quadril e restaurações dentárias. Eles não reagem com tecidos e fluidos corporais, o que minimiza o risco de rejeição.
4. Versatilidade na fabricação
O pó de CoCrMoW é adequado para uma variedade de técnicas de fabricação, incluindo moldagem por injeção de metal, impressão 3D e processos de fundição tradicionais. A capacidade do pó de fundir e solidificar com eficiência durante esses processos permite peças de alta precisão com geometrias complexas.
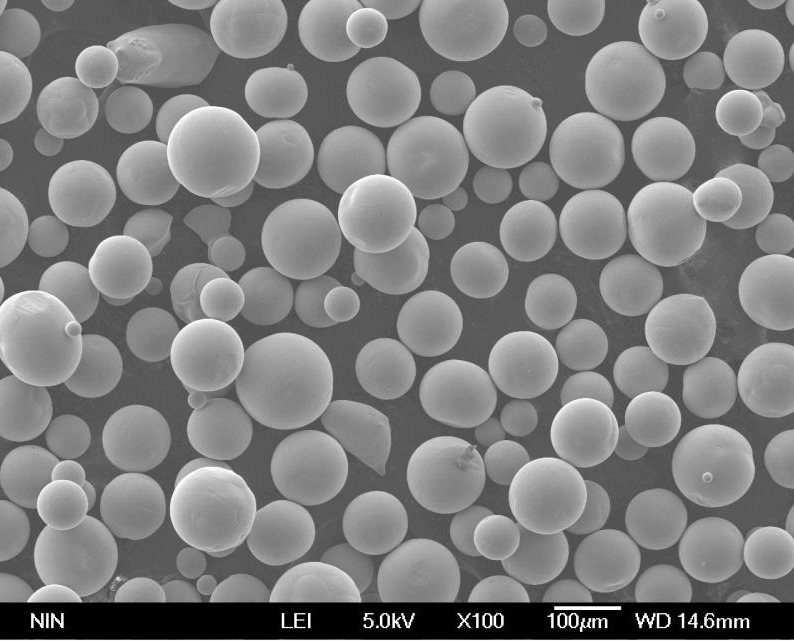
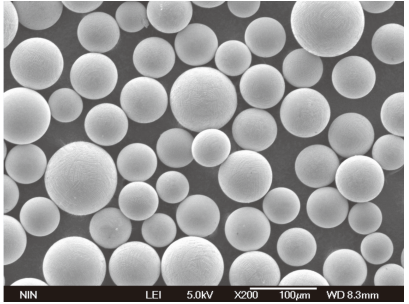
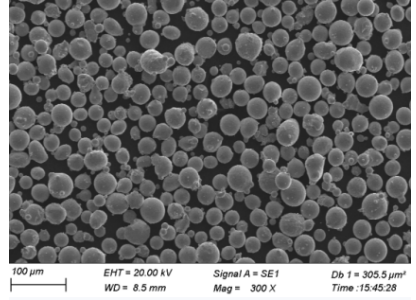

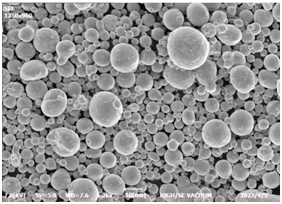
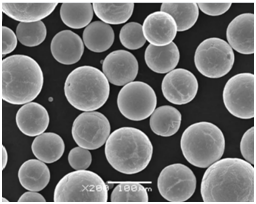
Aplicativos de Pó de CoCrMoW
Onde o pó de CoCrMoW é mais comumente usado? Vamos explorar suas principais aplicações em diferentes indústrias.
Setor | Aplicativo | Por que CoCrMoW? |
---|---|---|
Implantes médicos | Substituições de quadril e joelho, implantes dentários | Biocompatibilidade, resistência ao desgaste, resistência à corrosão |
Aeroespacial | Componentes de motores a jato, lâminas de turbina | Resistência a altas temperaturas, durabilidade |
Automotivo | Peças de motor de alto desempenho, engrenagens | Resistência ao desgaste, alta resistência mecânica |
Petróleo e gás | Ferramentas de perfuração, assentos de válvulas, bombas | Resistência à corrosão, capacidade de lidar com pressões extremas |
Geração de energia | Componentes da turbina, trocadores de calor | Resistência a altas temperaturas, confiabilidade em condições adversas |
Marinha | Eixos de hélice, componentes de bomba | Resistência à corrosão em ambientes de água salgada |
Os 10 principais modelos de pó de CoCrMoW
Vamos entrar nos detalhes de alguns modelos específicos de pó de CoCrMoW disponíveis no mercado. Cada um tem seu próprio conjunto de características exclusivas adaptadas para aplicações específicas.
1. Praxair CoCrMoW P231
Pó de alta qualidade projetado para revestimentos por pulverização térmica e fabricação aditiva. Oferece excelente resistência à corrosão e ao desgaste, tornando-o ideal para lâminas de turbinas e componentes de motores a jato.
2. Carpenter Technology CoCrMoW A2000
Este pó é amplamente utilizado em implantes médicos devido à sua alta biocompatibilidade. É conhecido por manter a resistência mecânica e a resistência à corrosão mesmo após exposição prolongada a fluidos corporais.
3. Höganäs CoCrMoW 1250
Especialmente projetado para processos de fabricação aditiva por fusão em leito de pó. Este modelo oferece excelente soldabilidade e produz peças com acabamentos de superfície elevados.
4. ATI CoCrMoW Superliga 21
Uma variante de CoCrMoW com maior teor de tungstênio, tornando-a uma escolha ideal para componentes sujeitos a temperaturas extremas em aplicações aeroespaciais.
5. Sandvik Osprey CoCrMoW 4502
Desenvolvido para moldagem por injeção de metal, este pó oferece excelentes características de fluxo e cria componentes com propriedades mecânicas superiores.
6. Arcam EBM CoCrMoW 4110
Utilizada principalmente nos processos de fusão por feixe de eletrões (EBM), esta pó fornece peças de alta resistência com geometrias complexas, tornando-a ideal para implantes médicos e aplicações dentárias.
7. Heraeus CoCrMoW BioPowder X500
Conhecida pela sua biocompatibilidade superior, esta pó é utilizada principalmente para impressão 3D de implantes ortopédicos. Resiste ao desgaste e à corrosão de forma excecional.
8. SLM Solutions CoCrMoW 2311
Concebida para processos de fusão seletiva a laser (SLM), esta pó tem uma estrutura de grão fino que permite peças de alta precisão com geometrias complexas.
9. EOS CoCrMoW SP2035
Esta pó é otimizada para tecnologias de fusão em leito de pó baseadas em laser. Apresenta uma excelente densidade e acabamento superficial, tornando-a adequada para componentes mecânicos de alto desempenho.
10. Renishaw CoCrMoW Plus
Conhecida pelo seu elevado ponto de fusão e resistência ao desgaste e à corrosão, esta pó é ideal para ambientes de alta tensão, como as indústrias aeroespacial e automóvel.
Vantagens da Pó CoCrMoW
Porque deve considerar a pó CoCrMoW para o seu próximo projeto? Aqui estão algumas vantagens de destaque:
- Resistência ao Desgaste Superior: Comparada com outras pós metálicas, como titânio ou alumínio, a CoCrMoW é muito mais resistente ao desgaste, tornando-a ideal para aplicações de alto impacto.
- Resistência à corrosão: O elevado teor de crómio proporciona uma excelente proteção contra a corrosão, especialmente em ambientes marinhos e químicos.
- Estabilidade Térmica: As ligas CoCrMoW podem suportar temperaturas extremas sem perder resistência, ao contrário de outras ligas que podem amolecer ou degradar-se.
- Versatilidade na fabricação: Quer a utilize para moldagem por injeção de metal ou impressão 3D, a pó CoCrMoW oferece uma excelente adaptabilidade.
Desvantagens da Pó de CoCrMoW
Embora a pó CoCrMoW apresente propriedades impressionantes, existem algumas limitações a considerar:
- Custo: A pó CoCrMoW pode ser mais cara do que outras pós de liga, como aço inoxidável ou titânio.
- Dificuldade de Processamento: Alguns processos de fabrico podem exigir equipamento ou técnicas especializadas para lidar com o elevado ponto de fusão da CoCrMoW.
- Ductilidade Limitada: Embora fortes e resistentes ao desgaste, as ligas CoCrMoW podem ser menos dúcteis, o que pode limitar a sua utilização em aplicações que exijam flexibilidade.
Especificações, tamanhos, classes e padrões
Vamos dar uma vista de olhos às especificações, tamanhos e normas típicas da pó CoCrMoW:
Especificação | Detalhes |
---|---|
Faixa de tamanho de partícula | 15-45 μm (Fabricação aditiva), 45-106 μm (Pulverização térmica) |
Densidade | 8,3-8,5 g/cm³ |
Ponto de fusão | 1330-1450°C |
Normas ASTM | F75, F1537, F799 (Para aplicações médicas) |
Padrões ISO | 5832-4, 5832-12 (Para biocompatibilidade) |
Fornecedores e Preços da Pó CoCrMoW
Aqui está uma tabela que lista alguns dos principais fornecedores de pó CoCrMoW, juntamente com preços aproximados:
Fornecedor | Modelo | Preço (por kg) | Disponibilidade |
---|---|---|---|
Praxair | CoCrMoW P231 | $200-250 | Em todo o mundo |
Tecnologia Carpenter | A2000 | $300-350 | América do Norte, Europa |
Höganäs | CoCrMoW 1250 | $180-220 | Global |
ATI | Superliga 21 | $250-300 | América do Norte, Ásia |
Sandvik Osprey | CoCrMoW 4502 | $220-270 | Europa, Ásia |
Prós e Contras da Pó CoCrMoW em Comparação com Outras Pós
Comparação | Pó de CoCrMoW | Pó de titânio | Pó de aço inoxidável |
---|---|---|---|
Resistência ao desgaste | Melhor | Menos | Moderado |
Resistência à corrosão | Excelente | Muito bom | Bom |
Resistência à temperatura | Melhor | Moderado | Bom |
Custo | Mais alto | Moderado | Inferior |
Biocompatibilidade | Excelente | Bom | Moderado |
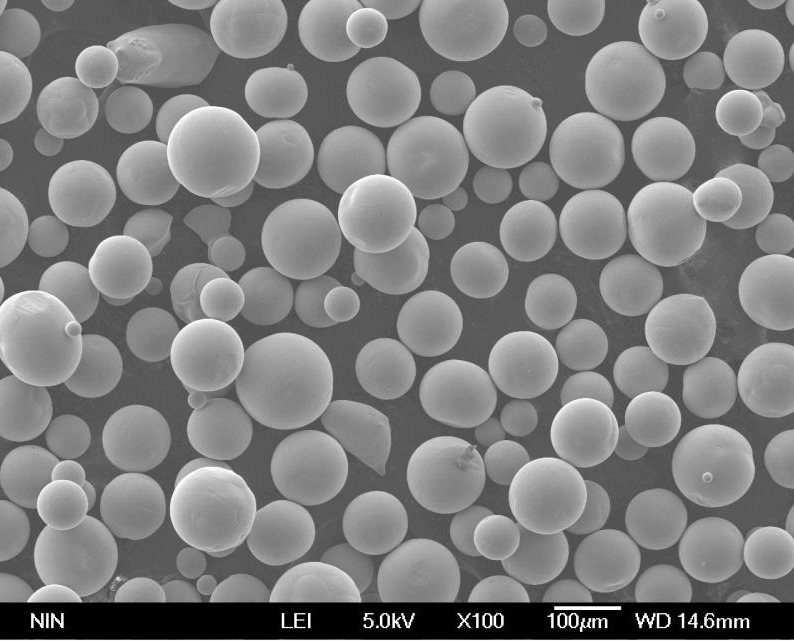
Perguntas frequentes
Pergunta | Resposta |
---|---|
Para que é utilizada a pó CoCrMoW? | A pó CoCrMoW é utilizada em implantes médicos, peças aeroespaciais, componentes automóveis e muito mais. |
Como é que a CoCrMoW se compara ao titânio? | A CoCrMoW oferece melhor resistência ao desgaste e estabilidade térmica, mas é mais cara. |
A CoCrMoW é biocompatível? | Sim, as ligas CoCrMoW são biocompatíveis e são normalmente utilizadas em implantes médicos. |
A CoCrMoW pode ser utilizada na impressão 3D? | Absolutamente! É amplamente utilizada no fabrico aditivo para produzir peças de alto desempenho. |
Quais são as limitações da CoCrMoW? | Pode ser cara e difícil de processar em algumas técnicas de fabrico. |