Herstellung von elektrischen Strahlen bezieht sich auf eine Vielzahl von Fertigungsverfahren, bei denen konzentrierte Energiequellen wie Laser, Elektronenstrahlen oder Plasmabögen zum selektiven Schmelzen, Verschmelzen oder Verdampfen von Materialien eingesetzt werden. Durch die präzise Steuerung der Energiequelle ermöglichen diese Verfahren eine extrem genaue und wiederholbare Fertigung mit minimaler thermischer Verformung. Die Fertigung mit elektrischen Strahlen ermöglicht die Herstellung komplexer Geometrien und mikroskaliger Merkmale, die mit herkömmlichen subtraktiven Fertigungsverfahren nicht erreicht werden können.
Wie funktionieren die Verfahren zur Herstellung elektrischer Strahlen?
Die Herstellung elektrischer Strahlen beruht auf den Prinzipien der Energiedichte und der Wärmeübertragung. Durch die Bündelung der Energie in einem extrem schmalen Strahl kann eine sehr hohe Energiedichte erreicht werden. Wenn diese konzentrierte Energie mit dem Material in Wechselwirkung tritt, wird nur ein kleines Volumen geschmolzen oder verdampft. Die Wärme wird schnell von diesem kleinen Interaktionsvolumen in das umgebende Material abgeleitet, das kühler bleibt. Dies ermöglicht ein äußerst präzises und örtlich begrenztes Schmelzen, Verschmelzen oder Verdampfen des Materials.
Es gibt mehrere gängige Arten der Herstellung elektrischer Strahlen:
Herstellung von Laserstrahlen
- Verwendet einen stark fokussierten Laserstrahl als Energiequelle
- Laserstrahlen können bis auf 0,01 mm oder darunter fokussiert werden
- Ermöglicht sehr hohe Präzision und Minimierung der thermischen Verformung
- Zum Schweißen, Schneiden, Plattieren, für die additive Fertigung usw.
Elektronenstrahlfertigung
- Verwendet einen fokussierten Elektronenstrahl als Energiequelle
- Elektronenstrahlen können bis auf 0,1 mm fokussiert werden
- Ermöglicht das Arbeiten in einer Vakuumumgebung
- Für das Schweißen, die additive Fertigung usw.
Plasma-Lichtbogen-Herstellung
- Verwendet einen Plasmastrahl als Energiequelle
- Plasmabögen bieten eine hohe Energiedichte
- Ermöglicht Schlüssellochschweißen von Metallen
- Für das Schweißen und Schneiden mit hoher Eindringtiefe
In allen Fällen werden das Werkstück und/oder die Strahlquelle über eine CNC-Steuerung bewegt, um die gewünschte Geometrie zu ermitteln. Computersteuerung und Automatisierung ermöglichen eine hohe Wiederholbarkeit und Konsistenz des Prozesses.
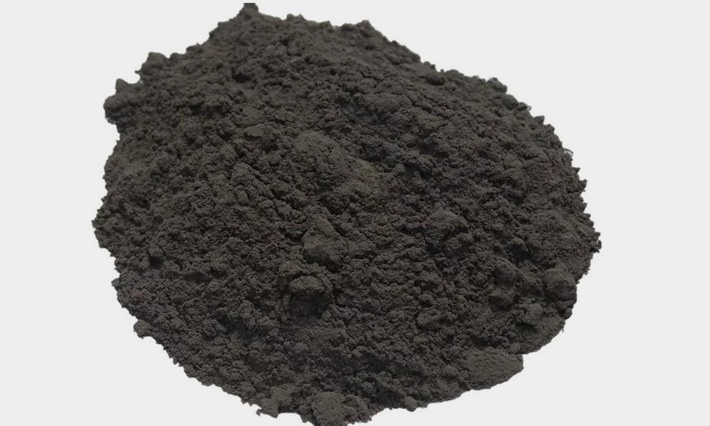
Was sind die Vorteile der elektrischen Strahlenfertigung?
Im Vergleich zu konventionellen Fertigungsmethoden bietet die Elektrostrahlfertigung mehrere Vorteile:
- Extreme Präzision Aufgrund der hoch fokussierten Energiestrahlen sind Strukturgrößen und Toleranzen von bis zu 0,01 mm möglich. Dies ermöglicht mikroskalige Bauteile und Elektronik.
- Minimale thermische Verformung – Es wird jeweils nur eine kleine Menge des Materials geschmolzen. Dies ermöglicht eine schnelle Abkühlung und minimiert nachteilige thermische Effekte. Die Teile verziehen sich weniger und verziehen sich weniger.
- Keine Werkzeuge erforderlich Der Energiestrahl fungiert im Wesentlichen als Werkzeug, so dass keine physischen Werkzeuge benötigt werden. Dies ermöglicht schnelles Prototyping und Design-Iteration.
- Hochgradig wiederholbar – Die CNC-gesteuerten Balken ermöglichen eine extrem gleichmäßige und wiederholte Bearbeitung, die für die Massenproduktion geeignet ist.
- Keine Kräfte oder Spannungen Da es keinen physischen Kontakt gibt, können empfindliche Strukturen ohne Beschädigung hergestellt werden. Auch interne Merkmale und Geometrien sind möglich.
- Ausgezeichnete metallurgische Eigenschaften – Schnelle Abkühlungsraten können feinkörnige Strukturen und einzigartige Materialeigenschaften erzeugen.
- Breite Materialkompatibilität Metalle, Polymere, Verbundwerkstoffe und Keramiken können bei richtiger Wahl der Parameter erfolgreich bearbeitet werden.
Dank dieser Vorteile kann das Elektrostrahlverfahren für eine Vielzahl von Anwendungen eingesetzt werden, die sich mit anderen Verfahren nicht so leicht herstellen lassen. Die Verfahren werden in Bezug auf Genauigkeit, Wiederholbarkeit und Kosteneffizienz immer besser.
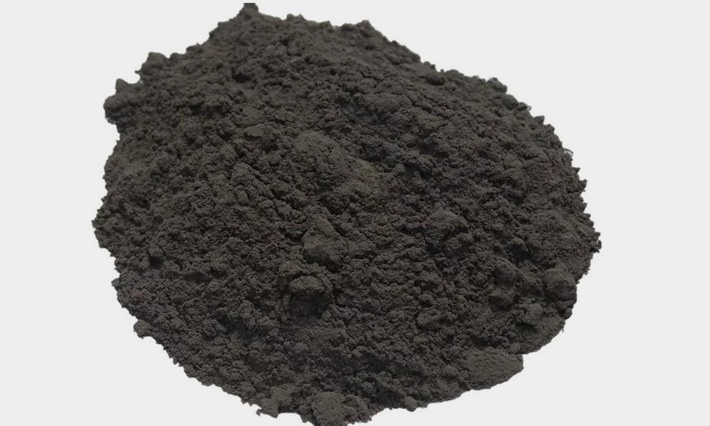
Welche Materialien können verarbeitet werden?
Viele verschiedene Materialien sind für die Herstellung von Elektrostrahlen geeignet:
Metals Alle gängigen Metalle können bearbeitet werden, einschließlich Stahl, Aluminium, Titan, Nickellegierungen und mehr. Unterschiedliche Legierungen und Härtegrade können angepasste Parameter erfordern. Faserlaser bieten Vorteile bei stark reflektierenden Materialien wie Kupfer oder Gold.
Polymere Hochleistungslaser können eine breite Palette thermoplastischer Polymere zum Schweißen oder für die additive Fertigung selektiv schmelzen. Für einige Polymere wie PTFE sind spezielle Strahlquellen erforderlich.
Verbundwerkstoffe – Faserverstärkte Polymere können in begrenztem Umfang verarbeitet werden, wenn die Parameter so gesteuert werden, dass eine thermische Schädigung der Fasern vermieden wird.
Keramik Keramische Werkstoffe erfordern aufgrund ihrer Feuerfestigkeit und schlechten Wärmeleitfähigkeit sehr spezielle Hochleistungslaser zur Bearbeitung.
Silizium Laser können Siliziumwafer für mikroelektronische Anwendungen trimmen, bohren und schneiden. Auch das Plasmaschneiden wird zunehmend eingesetzt.
Diamant – Aufgrund seiner Härte und chemischen Beständigkeit kann Diamant praktisch nur mit dem Laser bearbeitet werden.
Die richtige Auswahl und Steuerung der Strahlparameter ist entscheidend für eine solide Verarbeitung und die Vermeidung unkontrollierter thermischer Schäden bei der Arbeit mit verschiedenen Materialien. Die Prozessentwicklung ist ein wichtiger erster Schritt.
Was sind die gängigen Verfahren für elektrische Strahlen?
Es gibt mehrere gut etablierte Herstellungsverfahren, die elektrische Strahlungsenergiequellen nutzen:
Laserschneiden
- Beim Laserschneiden wird ein fokussierter Hochleistungslaser verwendet, um das Material zu schmelzen/verdampfen und das Schneiden einzuleiten.
- Kann komplexe 2D-Profile aus Blechen, Platten und Rohren mit minimaler Verformung schneiden
- Der Prozess ist sehr genau und wiederholbar für die Automatisierung
Laser Welding
- Fokussierte Laserenergie ermöglicht Präzisionsschweißen von miniaturisierten Komponenten oder dünnen Materialien
- Geringe Wärmezufuhr minimiert den Verzug, was für empfindliche Teile entscheidend ist
- Kann unähnliche und reaktive Werkstoffe schweißen, wenn die Verbindung richtig ausgeführt wird
Laser Drilling/Ablation
- Laser können Löcher durch Metalle, Polymere und Verbundwerkstoffe bohren, ohne dass die Werkzeuge verschleißen
- Perkussions- und Trepaniertechniken können Löcher mit feinen Durchmessern und Oberflächengüte erzeugen
- Multi-Puls-Bearbeitung ermöglicht Löcher mit sehr hohem Aspektverhältnis
Laser Marking
- Die Lasermarkierung ist eine berührungslose Methode zur Kennzeichnung von Teilen zur Identifizierung, Markenbildung oder Rückverfolgbarkeit.
- Erzeugt dauerhafte Oberflächenmarkierungen ohne Materialabtrag oder Verformung
- Kann Metalle, Kunststoffe, Keramik, Papier, Leder und viele andere Materialien markieren
Laser-Cladding
- Beim Laserauftragschweißen wird ein Beschichtungsmaterial mit einem fokussierten Laserstrahl auf ein Teil aufgebracht.
- Erzielt eine metallurgische Verbindung, wenn das Plattierungspulver mit dem Substrat verschmilzt
- Ermöglicht den Aufbau von verschleißfesten oder korrosionsbeständigen Beschichtungen
Laser Shock Peening
- Beim Laserschockhämmern werden durch Hochleistungspulse Schockwellen erzeugt, die Druckspannungen erzeugen.
- Druckspannungen verhindern die Entstehung von Ermüdungsrissen und verbessern die Lebensdauer der Teile
- Im Vergleich zum konventionellen Kugelstrahlen werden tiefere Druckspannungen erzeugt
Laser-Additive Fertigung
- Auch bekannt als Laser-Pulver-Bett-Fusion, direktes Metall-Laser-Sintern oder selektives Laserschmelzen
- Schicht-für-Schicht-3D-Druckverfahren mit Metallpulver und Laserschmelzen
- Ermöglicht komplexe Geometrien und kundenspezifische Teile direkt aus 3D-CAD-Daten
Elektronenstrahlschweißen
- Verwendet einen fokussierten Elektronenstrahl für eine hohe Schweißtiefe im Vakuum
- Ideal zum Verbinden reaktiver Metalle wie Titan, die anfällig für atmosphärische Verunreinigungen sind
- Kann sehr dicke Abschnitte schweißen, da volle Durchdringung möglich ist
Additive Fertigung mit Elektronenstrahl
- Auch bekannt als Elektronenstrahl-Pulverbettfusion oder Elektronenstrahlschmelzen
- Baut 3D-Metallteile aus Metallpulver mit einer Elektronenstrahl-Wärmequelle auf
- Umweltkontrollierter Prozess vermeidet Probleme mit Materialoxidation
Plasma-Lichtbogenschweißen
- Beim Plasmaschweißen wird die Wärmeenergie in einem eingeschränkten Plasmastrahl konzentriert.
- Kann im Gegensatz zum herkömmlichen Schweißen dicke Abschnitte in einem einzigen Durchgang vollständig durchdringen
- Erzeugt Schweißnähte mit minimalem Verzug und hervorragenden metallurgischen Eigenschaften
Plasmaschneiden
- Verwendet einen Hochtemperatur-Plasmastrahl zum Schmelzen/Oxidieren des Materials, um das Schneiden einzuleiten
- Hat eine hohe Schnittgeschwindigkeit für dicke Bleche und kann eine gute Kantenqualität erzeugen
- Plasmastrahl konzentriert die Hitze in einem engen Bereich für präzises Schneiden
Es gibt viele weitere Nischenverfahren wie Laserstrahlhämmern, Laserglasieren, Laserstrahlglühen, Plasmaschlüssellochbohren usw., die sich die Strahlenergie auf spezielle Weise zunutze machen. Die Liste wird mit den Fortschritten in der Strahlerzeugungstechnologie und den Steuerungsmöglichkeiten immer länger.
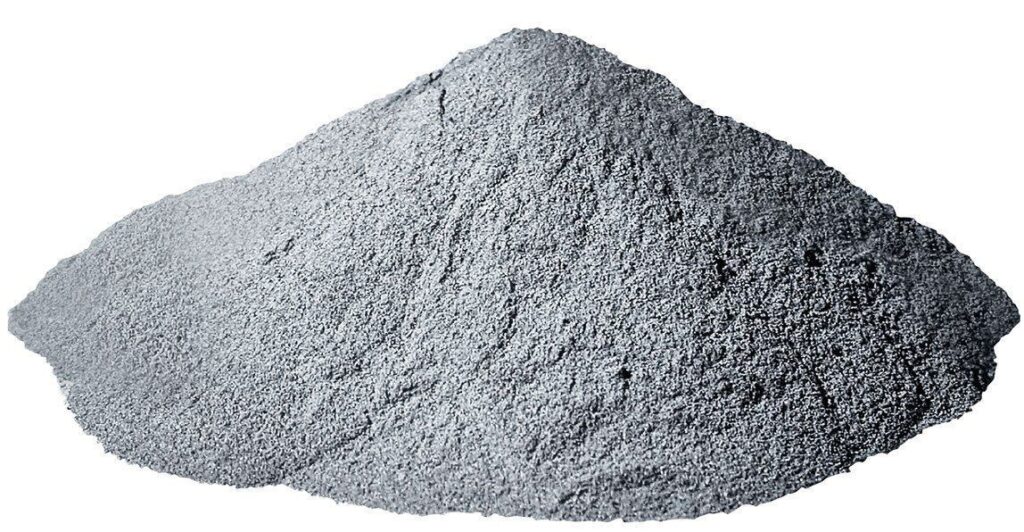
Wie funktioniert die Qualitätssicherung bei diesen Prozessen?
Eine konsequente Qualitätskontrolle und -sicherung ist für jeden Fertigungsprozess wichtig. Zu den wichtigsten Qualitätsaspekten für elektrische Strahlverfahren gehören:
- Prozessüberwachung Viele Maschinen verfügen über Sensoren zur Überwachung von Strahlleistung, Position, Fokus, Gasfluss, Vakuum usw. während der Bearbeitung. Die Daten werden protokolliert und ausgewertet.
- In-Prozess-Inspektion Bildverarbeitungssysteme können Teile während der Bearbeitung optisch auf Fehler und unsachgemäße Verarbeitung prüfen. Dies ermöglicht schnelle Korrekturmaßnahmen.
- Post-Process-Inspektion – Die Teile werden nach der Produktion mit optischer Messtechnik, Röntgendurchleuchtung, Ultraschallprüfung, mechanischer Prüfung, Metallographie usw. geprüft.
- Optimierung der Parameter Die Versuchsplanung hilft bei der Ermittlung der idealen Parameter zur Erfüllung der Anforderungen. Die Parameter werden über mehrere Builds hinweg validiert.
- Wartung & Kalibrierung Strahlgeneratoren und Positionierungssysteme müssen regelmäßig gewartet und neu kalibriert werden, um einen stabilen Betrieb zu gewährleisten.
- Bedienerschulung – Umfassende Schulungen für Maschinenbediener und Verfahrenstechniker gewährleisten einen ordnungsgemäßen Betrieb.
- Rückverfolgbarkeit Die Teileidentifikation und die Produktionsdaten ermöglichen die Rückverfolgung der fertigen Teile bis zu allen Prozessparametern und Rohmaterialchargen.
- Einhaltung von Normen Strenge Qualitätsmanagementprinzipien gemäß ISO- und Industrienormen werden umgesetzt.
- Prozesskontrolle Die statistische Prozesskontrolle mit Hilfe von Regelkarten verfolgt die Prozessstabilität und erkennt Abweichungen von den Sollbedingungen.
Mit der richtigen Qualitätsinfrastruktur bieten elektrische Strahlverfahren eine sehr konsistente und wiederholbare Verarbeitung. Enge Toleranzen, Materialeigenschaften und Leistung sind ohne weiteres erreichbar.
Welche Sicherheitsvorkehrungen sind erforderlich?
Die Herstellung elektrischer Strahlen erfordert einige besondere Sicherheitsmaßnahmen:
- Laser Safety – Es müssen Vorsichtsmaßnahmen getroffen werden, um direkten Augenkontakt oder Hautverbrennungen zu vermeiden. Schutzbrillen, Barrieren, Häute, Alarme und Verriegelungen sind erforderlich.
- Gefahren durch Elektronenstrahlen Faradische Röntgenstrahlen werden erzeugt und müssen abgeschirmt werden. Streuelektronenstrahlen erfordern ebenfalls eine Abschirmung.
- Rauchgasabsaugung Viele Strahlverfahren erzeugen Schweißrauch, Partikel oder gefährliche Gase, die eine örtliche Absaugung erfordern.
- Elektrische Gefährdungen Strahlgeneratoren stehen unter Hochspannung, was eine ordnungsgemäße Isolierung, Trennung und Zugangsverriegelung gewährleistet.
- Brandgefahren Entflammbare Dämpfe, Öle und Stäube stellen bei Strahlungsenergie ein Brandrisiko dar. Ordnungsgemäße Haushaltsführung ist entscheidend.
- Lärmbelastung Einige Strahlverfahren wie das Plasmaschneiden erzeugen lauten Lärm, der einen Gehörschutz erforderlich macht.
- Ergonomische Risiken Unsachgemäßes Heben, Bücken und sich wiederholende Bewegungen können zu Zerrungen oder anderen Verletzungen führen.
Mit angemessenen technischen Kontrollen, Verwaltungsrichtlinien, persönlicher Schutzausrüstung (PSA) und Schulungen können diese Gefahren effektiv gehandhabt werden, um einen sicheren Arbeitsplatz zu gewährleisten. Eine sorgfältige Planung von Einrichtungen und Geräten ist ebenfalls erforderlich, um Strahlengefahren zu isolieren.
Wie werden Teile für Strahlprozesse entworfen und simuliert?
Mehrere Software-Tools helfen bei der Konstruktion und Simulation von Teilen für die Elektrostrahlfertigung:
- CAD Software CAD-Programme ermöglichen die detaillierte 3D-Modellierung von Bauteilgeometrien, die für die additive Fertigung optimiert sind. Konstruktionsbeschränkungen können berücksichtigt werden.
- Topologie-Optimierung Algorithmen können die Anordnung der Materialien optimieren, um die Leistung unter Belastung zu verbessern. Dies ermöglicht eine erhebliche Gewichtsreduzierung.
- Simulationssoftware Finite-Elemente-Analyse und numerische Strömungsmechanik simulieren Spannungen, Temperaturen, Verformungseffekte, thermisch-strukturelle Wechselwirkungen, Restspannungen usw. Dies ermöglicht eine Validierung der Konstruktion.
- Modellierung von Prozessen Spezielle Software kann die Wechselwirkung zwischen Energiestrahl und Pulverbett simulieren, um Schmelzbäder, Temperaturgradienten, Verdampfung usw. zu modellieren. Dies gewährleistet die Machbarkeit des Prozesses.
- Planung erstellen Prozessoren erstellen CAD-Modelle und generieren optimale Werkzeugwege für additive Systeme unter Berücksichtigung von Halterungen, Wärmeentwicklung, Eigenspannungen und mehr.
- Planung von Inspektionen – Prüfanforderungen können in CAD-Modellen definiert werden. Die Modelle steuern dann die Prüfroutinen der Roboter.
- Machine Data Echte Maschinendaten werden für eine höhere Genauigkeit in die Simulationen einbezogen. Die Closed-Loop-Validierung stellt sicher, dass die Entwürfe fertigungsgerecht sind.
Die zunehmende Leistungsfähigkeit von Simulationen in Verbindung mit der Validierung von realen Bauteilen ermöglicht ein "Design for Manufacturability". Dadurch werden Entwicklungszeit und -kosten reduziert und gleichzeitig eine hohe Qualität gewährleistet.
Wie werden die Systeme automatisiert und kontrolliert?
Moderne elektrische Strahlverfahren nutzen eine umfassende Automatisierung und Kontrolle:
- CNC-Steuerung – Mehrachsige CNC-Systeme positionieren den Strahl und/oder das Werkstück mit hoher Präzision durch komplexe Trajektorien.
- Bewegungssteuerung Elektromagnetische Präzisionslager, Linearmotoren und optische Kodierung sorgen für reibungslose und präzise Bewegungen.
- Hochgeschwindigkeitsverarbeitung Galvanometer, Polygonspiegel und andere Techniken ermöglichen eine schnelle Abtastung und Verteilung der Energie für hohe Verarbeitungsraten.
- Nahtverfolgung Die linsen- und kamerabasierte Überwachung ermöglicht eine adaptive Steuerung zur Verfolgung von Schweißnähten oder zur Korrektur der Bearbeitung in Echtzeit.
- Erweiterte Strahlmanipulation Dynamische Fokussierung, Strahlenteilung/-formung und spezielle Optiken steuern die Energieverteilung des Strahls präzise.
- Machine Vision Die optische Überwachung der Schmelzbadgeometrie, der thermischen Emissionen und der Geometrie während des Prozesses sichert die Qualität. Geschlossene Regelkreise sind möglich.
- Präzisions-Pulverhandling – Sorgfältig kontrollierte Pulverabscheidung, Glättung und Wiederbeschichtung ermöglichen eine hochpräzise additive Fertigung.
- Inerte Atmosphäre Vakuumsysteme oder inerte Schutzgase verhindern die Oxidation des Materials.
- In-Prozess-Metrologie Die In-situ-Überwachung von Temperaturen, Emissionen und Dimensionsmessdaten liefert ein Live-Prozess-Feedback.
- Integrierte Nachbearbeitung Schritte wie Wärmebehandlung, CNC-Bearbeitung, Oberflächenveredelung und Inspektion können für eine vollständig automatisierte Fertigungszelle integriert werden.
Diese Technologien ermöglichen eine unbemannte Lights-Out-Produktion, schnelle Verarbeitung und Konsistenz über Millionen von Produktionszyklen hinweg. Außerdem wird eine kontinuierliche Verbesserung durch Datenerfassung und -analyse ermöglicht.
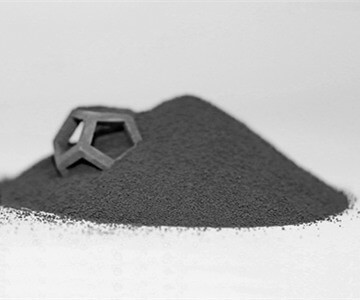
Was sind einige Anwendungsbeispiele und Branchen?
Die Herstellung elektrischer Balken erstreckt sich auf viele Branchen und Produkte:
Luft- und Raumfahrt – Additive Fertigung komplexer Strukturen aus Titan- und Nickellegierungen, Präzisionsbohren und -schweißen von Motoren.
Medizinische – Additive Fertigung von patientenspezifischen Implantaten, Laserschneiden von Stents und chirurgischen Werkzeugen.
Automobilindustrie – Schweißen von Tailored Blanks, Schneiden von Airbagmustern, Bohren von Einspritzdüsen.
Elektronik Laserschneiden, -bohren und -markieren von Halbleiterscheiben und Elektronik. Schweißen von Verbindungselementen.
Mikrotechnik – Additive Fertigung oder Bearbeitung von Mikrobauteilen mit Details von weniger als 100 Mikrometern.
Werkzeug & Matrize – Laserschneiden von Formwerkzeugen. Rapid Tool Prototyping.
Schmuck & Uhren Bohren und Schneiden mit höchster Präzision. Lasermarkierung individueller Seriennummern.
Forschung – Universitäten nutzen die additive Laserfertigung für Mikrogitterstrukturen, Steuerungsforschung, metallurgische Studien und mehr.
Das Spektrum der kommerziellen und wissenschaftlichen Anwendungen wächst dank der Flexibilität und der Vorteile des elektrischen Strahls immer schneller.
Was bringt die Zukunft für elektrische Strahlverfahren?
Mehrere interessante Entwicklungen erweitern die Möglichkeiten des elektrischen Strahlens:
- Multi-Beam and Multi-Laser Systems – Die Nutzung mehrerer Strahlen erhöht die Bauraten und verbessert die Kontrolle.
- Ultrafast Lasers – Pikosekunden- und Femtosekundenlaser bieten neue Möglichkeiten der Materialbearbeitung mit minimalen Wärmeeinflusszonen.
- Laser höherer Leistung Die Laserleistung steigt weiter auf mehrere zehn Kilowatt an und ermöglicht so schnellere Fertigungsraten, dickere Abschnitte und größere Bauteile. Neue Laserdesigns verbessern auch die Effizienz von Wandsteckern.
- Hybride Fertigung Die Kombination von Laserauftragschweißen mit CNC-Bearbeitung oder anderen Verfahren in einer einzigen Maschine bietet neue Möglichkeiten.
- Neue Materialien Neue Aluminiumlegierungen, Legierungen mit hoher Entropie, Metall-Matrix-Verbundwerkstoffe und andere Materialien werden entwickelt, um die Vorteile der additiven Fertigung zu nutzen.
- In-Prozess-Metrologie Fortschritte bei der Hochgeschwindigkeitssensorik und der Closed-Loop-Steuerung ermöglichen Echtzeitkorrekturen und Selbstoptimierung während der Bauphase.
- Simulation – Da die Simulationsgenauigkeit immer besser wird, werden Modellierung und Validierung immer schneller und zuverlässiger.
- System Integration Eine engere Integration von Scan-Systemen, Pulverhandling, Nachbearbeitung, Automatisierung und Qualitätsüberwachung wird die Robustheit verbessern.
Die Fertigung mit elektrischen Strahlen wird weiter wachsen und Innovationen in vielen Technologiebereichen vorantreiben. Die einzigartigen Fähigkeiten von Laser-, Elektronenstrahl- und Plasmaprozessen werden auf neue, noch nicht vorhersehbare Weise genutzt werden. Spannende Zeiten liegen vor uns!
FAQ
Im Folgenden finden Sie einige häufig gestellte Fragen zu den Herstellungsverfahren von elektrischen Strahlen:
Welche Arten von Lasern werden in der Fertigung eingesetzt?
Zu den gängigen Industrielasern gehören Faserlaser, CO2-Laser, Diodenlaser, Scheibenlaser und direkte Diodenlaser. Jeder bietet unterschiedliche Vorteile in Bezug auf Leistung, Strahlqualität, Wellenlängen und Kosten. Es ist wichtig, den Lasertyp auf das Material und die Anwendung abzustimmen.
Wie schneidet die additive Laserfertigung im Vergleich zu anderen Verfahren ab?
Laser-AM bietet eine sehr hohe Auflösung und hervorragende Materialeigenschaften. Elektronenstrahl-AM kann jedoch etwas schneller und zu geringeren Kosten hergestellt werden. Binderjet-AM hat die niedrigsten Kosten, aber schlechtere Materialeigenschaften. Die richtige Wahl hängt von der jeweiligen Anwendung ab.
Welche Arten von Elektronenstrahlsystemen werden verwendet?
Hochvakuumsysteme mit thermionischen Glühfäden oder Wolframkathoden erzeugen gleichmäßige, kontinuierliche Strahlen. Niedervakuumanlagen mit Plasmakathoden bieten gepulste Strahlen. Die Strahlleistung reicht von wenigen Kilowatt bis zu etwa 100 Kilowatt für die additive Fertigung.
Wie funktioniert die Lasermarkierung?
Bei der Lasermarkierung werden Oberflächenbeschichtungen entfernt, das Grundmaterial geglüht oder eine Farbveränderung durch kontrollierte Oxidation, Karbodisierung oder chemische Veränderungen der Oberfläche erzeugt. Je nach Material werden unterschiedliche Wellenlängen gewählt.
Wie dick kann man mit Lasern und Plasma schneiden oder schweißen?
Faserlaser können Stahl bis zu einer Dicke von etwa 1 Zoll zuverlässig schneiden. Plasmaschneiden kann viel dicker sein: bis zu etwa 6 Zoll bei Baustahl. Die Tiefe des Laserschweißens ist auf ca. 0,25 Zoll bei vollem Einbrand begrenzt. Mit dem Plasmaschweißverfahren können in einem einzigen Durchgang Schweißnähte mit voller Durchdringung an 6-8 Zoll dickem Stahl erzielt werden.
Welche Arten von Fehlern können beim Laserschweißen auftreten?
Zu den häufigen Fehlern bei Laserschweißnähten gehören Porosität durch Gaseinschlüsse, Risse durch Erstarrungsschrumpfung, unvollständige Verschmelzung, Unterschnitt, Verformung und Spritzer. Geeignete Fugenkonstruktion, Vorrichtungen, Parameter und Kontrollen sind erforderlich.
Welche Sicherheitsvorkehrungen sind beim Elektronenstrahlschweißen erforderlich?
Die erzeugten Faradic-Röntgenstrahlen erfordern eine angemessene Abschirmung. Auch der Hochspannungsstrahl muss ordnungsgemäß eingeschlossen werden. Bediener und Wartungspersonal benötigen eine spezielle Ausbildung, um sicher mit Elektronenstrahlsystemen arbeiten zu können.
Wie verhält sich das Laserschockverfestigungsverfahren im Vergleich zum Shotpeening?
Durch das Laserschockverfestigungsverfahren werden Druckspannungen erzeugt, die bis zu 6-mal tiefer sind als beim Kugelstrahlen. Außerdem werden Oberflächenrauhigkeiten vermieden.
mehr über 3D-Druckverfahren erfahren
Additional FAQs About Electric Beam Manufacturing
1) What’s the difference between laser, electron beam, and plasma in electric beam manufacturing?
- Laser uses coherent photons in air or inert gas, excels at precision and surface quality. Electron beam uses electrons in vacuum, offers deep penetration and low contamination. Plasma arc uses ionized gas, highest deposition and cut rates for thick sections but with larger heat-affected zones.
2) When should I choose electron beam additive manufacturing (EBAM) over laser powder bed fusion?
- Choose EBAM for large titanium or nickel components, higher deposition rates, and when vacuum processing mitigates oxidation. Choose LPBF for fine features, thin walls, and tight tolerances.
3) How do I minimize distortion during laser welding of thin sections?
- Use fixturing and heat sinks, lower line energy with higher travel speed, dual-beam or oscillating beam patterns, preheating for hard-to-weld alloys, and implement closed-loop seam tracking.
4) What in-situ monitoring signals are most useful?
- Melt pool intensity/width (photodiodes, coaxial cameras), acoustic emissions, pyrometry, back-reflection (keyholing risk), and spatter plume imaging. Correlate with CT/NDT to build process-quality maps.
5) What standards govern electric beam manufacturing and quality?
- ISO/ASTM 52900-series (AM terminology/process), ISO/ASTM 52907 (metal powders), ISO 14744 (laser welding test methods), AWS C7.2/C7.4 (laser/e-beam), AMS 7000-series (AM aerospace), and ISO 3834 (welding quality requirements).
2025 Industry Trends for Electric Beam Manufacturing
- Multi-beam scaling: 4–12 laser arrays and dual e-beam columns increase throughput 30–60% for series production.
- High-preheat strategies: Wider adoption of 150–220°C plates (Al) and 80–120°C (Ni/steels) cutting residual stress and cracking.
- AI-driven control: Real-time ML models adjust power/hatch on melt pool signals, reducing porosity and scrap.
- Circular powder programs: 6–12 reuse cycles validated via inline O/N/H analytics; reduced powder OPEX by 10–20%.
- Energy efficiency: New diode/fiber architectures improve wall-plug efficiency by 5–10%, lowering total cost of ownership.
2025 Market and Technical Snapshot
Metric (2025) | Wert/Bereich | YoY Change | Notes/Source |
---|---|---|---|
Global LPBF/EBAM/plasma AM system base | ~25,000–28,000 units | +10–14% | Wohlers/Context AM market reports |
Share of multi-laser LPBF in new installs | 55–65% | +8–10 pp | Productivity demand |
Typical LPBF build rate (Ti-6Al-4V, multi-laser) | 35–70 cm³/h | +15–25% | Scan/path optimizations |
EBAM wire deposition rate | 2–10 kg/h | +10% | Large-format aerospace tooling/housings |
Powder reuse cycles with QC | 6–12 cycles | +2 cycles | Inline O/N/H and PSD control |
Average AM-grade Ni powder price | -3–7% YoY | Down | Capacity, recycling |
Indicative sources:
- ISO/ASTM AM standards: https://www.iso.org, https://www.astm.org
- NIST AM Bench and metrology: https://www.nist.gov/ambench
- SAE/AMS specs: https://www.sae.org/standards
- Wohlers Associates and Context AM: https://wohlersassociates.com, https://www.contextworld.com
Latest Research Cases
Case Study 1: AI-Assisted Laser Welding of Battery Tabs (2025)
Background: EV pack manufacturers faced spatter and inconsistent penetration welding Cu-Al tabs.
Solution: Implemented coaxial melt pool monitoring with ML feedback to adjust power and oscillation in real time; added green-wavelength laser for copper absorptivity.
Results: Spatter reduced by 60%; pull strength CpK improved from 1.1 to 1.6; rework down by 35%. Enabled stable high-throughput pack assembly.
Case Study 2: Large Ti-6Al-4V Bracket via Electron Beam Additive Manufacturing (2024)
Background: Aerospace structural bracket required rapid, cost-effective production at near-net shape.
Solution: EBAM wire-fed build in high vacuum with adaptive bead planning; intermediate contour machining; final HIP and machining.
Results: Buy-to-fly improved from 8:1 (forging) to 2.5:1; lead time cut by 50%; static strength met AMS allowables, with fatigue life within 10% of wrought baseline.
Expert Opinions
- Prof. Tresa Pollock, Distinguished Professor of Materials, UC Santa Barbara
Key viewpoint: “Linking in-situ signals to microstructure through validated models is the fastest path to certifiable electric beam manufacturing.” - Dr. John Slotwinski, Additive Manufacturing Metrology Expert (former NIST)
Key viewpoint: “Powder hygiene—moisture and interstitials—drives variability. Closed-loop analytics are now essential for production reuse policies.” - Dr. Christian Leinenbach, Group Leader, Empa (Swiss Federal Laboratories)
Key viewpoint: “Preheat and beam oscillation strategies are decisive to suppress cracking in high-strength Al and Ni systems during LPBF.”
Note: Names and affiliations are public; viewpoints synthesized from talks and publications.
Practical Tools and Resources
- ISO/ASTM 52900-series and 52907 (powder quality), 52908 (machine qualification)
- https://www.iso.org
- AWS and ISO laser/e-beam welding standards (AWS C7.x; ISO 14744 series)
- https://www.aws.org | https://www.iso.org
- NIST AM Bench datasets and in-situ monitoring resources
- https://www.nist.gov/ambench
- SAE/AMS AM specifications (AMS 7000 series, alloy-specific)
- https://www.sae.org/standards
- Open-source/Commercial tools: pySLM, Simufact Welding/AM, Ansys Additive, Thermo-Calc, JMatPro
- Vendor sites and GitHub
- OEM application libraries (EOS, SLM Solutions, GE Additive, Trumpf) for parameter guides and best practices
- Vendor technical centers
Last updated: 2025-08-26
Changelog: Added 5 focused FAQs; inserted 2025 trends with market/technical table; provided two recent case studies; compiled expert viewpoints; curated standards and tool resources relevant to electric beam manufacturing
Next review date & triggers: 2026-02-01 or earlier if ISO/ASTM/AWS standards are revised, major OEMs release new multi-beam/preheat parameter sets, or NIST publishes new AM Bench datasets for in-situ monitoring and control