Einführung
Der 3D-Druck, auch bekannt als additive Fertigung, hat die Produktion in allen Branchen revolutioniert. Die Technologie baut Objekte Schicht für Schicht aus Materialien wie Kunststoffen, Metallen, Keramiken und sogar lebenden Zellen auf. Der 3D-Druck bietet Vorteile wie Massenanpassung, schnelles Prototyping und dezentrale Fertigung. Eines der vielversprechendsten Materialien für den 3D-Druck ist Metall, das die Herstellung von Endverbrauchsteilen mit hoher Festigkeit und Haltbarkeit ermöglicht.
Molybdändisilicid-Pulver ist ein fortschrittliches keramisches Material, das als Metallpulver für den 3D-Druck immer beliebter wird. MoSi2 bietet außergewöhnliche Eigenschaften, die es für 3D-gedruckte Teile in der Luft- und Raumfahrt, im Automobilbau, in der Medizin und in der Industrie gut geeignet machen.
Was ist Molybdändisilicidpulver?
Molybdändisilicid (MoSi2) ist eine intermetallische Keramikverbindung, die aus Molybdän- und Siliciumatomen im Verhältnis 1:2 besteht. Sie hat eine tetragonale Kristallstruktur und wird aufgrund ihres hohen Schmelzpunkts von 2.030°C als feuerfeste Keramik eingestuft.
Zu den wichtigsten Eigenschaften von Molybdändisilicid gehören:
- Hoher Schmelzpunkt – Ermöglicht den Einsatz in Hochtemperaturanwendungen bis zu 1.700°C in oxidierenden Umgebungen
- Geringe Dichte – ca. 6,24 g/cm3, dadurch Gewichtseinsparung
- Ausgezeichnete Oxidationsbeständigkeit – Bildet bei hohen Temperaturen eine schützende SiO2-Schicht
- Wärmeleitfähigkeit – Bis zu 125 W/mK, für gute Wärmeableitung
- Temperaturwechselbeständigkeit – Widerstandsfähigkeit gegen Rissbildung durch thermische Spannungen
- Hohe Festigkeit – Biegefestigkeit um 700 MPa bei Raumtemperatur
Dank dieser Eigenschaften eignet sich MoSi2 für anspruchsvolle Anwendungen in extremen Umgebungen. Das Material wird seit Jahrzehnten für Hochtemperatur-Heizelemente und Wärmemanagement-Anwendungen verwendet. In jüngerer Zeit hat es sich als außergewöhnliches Pulverbettmaterial für den 3D-Druck von Hochleistungsmetallteilen erwiesen.
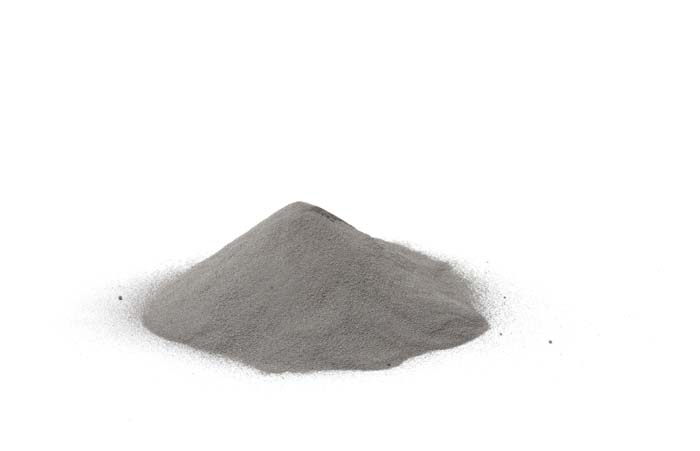
Warum MoSi2-Pulver für den 3D-Druck verwenden?
Molybdändisilicid verfügt über eine einzigartige Kombination von Eigenschaften, die es zu einem erstklassigen Kandidaten für den 3D-Druck von hochfesten, thermisch stabilen Metallkomponenten machen.
Hoher Schmelzpunkt
Der sehr hohe Schmelzpunkt von MoSi2 ermöglicht es, dass 3D-gedruckte Teile ihre Festigkeit und Form bei hohen Temperaturen von über 1500 °C beibehalten. Dies ermöglicht den Einsatz des Materials in extrem heißen Umgebungen.
Oxidationsbeständigkeit
MoSi2 bildet eine schützende Siliziumdioxidschicht (SiO2), wenn es bei hohen Temperaturen Sauerstoff ausgesetzt wird. Diese Oxidschicht schützt das Material vor weiterer Oxidation und Korrosion. Dank der Oxidationsbeständigkeit können 3D-gedruckte MoSi2-Bauteile an der Luft oder in oxidierenden Atmosphären bei hohen Temperaturen betrieben werden.
Thermische Eigenschaften
Der niedrige Wärmeausdehnungskoeffizient minimiert thermische Spannungen, während die hohe Wärmeleitfähigkeit eine effektive Wärmeableitung von 3D-gedruckten Metallteilen ermöglicht. Dies führt zu einer ausgezeichneten Temperaturwechselbeständigkeit bei zyklischen Erwärmungsanwendungen.
Hohe Festigkeit
MoSi2 weist auch bei hohen Temperaturen eine gute Festigkeit und Kriechbeständigkeit auf. Seine Biegefestigkeit bei Raumtemperatur beträgt über 700 MPa und ist damit stärker als viele Stahllegierungen. Dies ermöglicht den 3D-Druck von leichten, hochfesten Teilen.
Niedrige Dichte
Mit einer Dichte von etwa 6,2 g/cm3 ist MoSi2 deutlich leichter als herkömmliche Hochtemperaturlegierungen auf Wolfram- oder Molybdänbasis. Dank der geringeren Dichte können leichtere Bauteile hergestellt werden.
Verarbeitbarkeit
MoSi2-Pulver kann mit Standard-Pulverbettschmelzverfahren für Metalle verarbeitet werden, so dass sich komplexe Geometrien leicht herstellen lassen. Die Teile können durch heißisostatisches Pressen (HIP) nachbearbeitet werden, um die Verdichtung und die Eigenschaften weiter zu verbessern.
Die Kombination dieser Eigenschaften macht MoSi2 zu einem außergewöhnlichen Material für den 3D-Druck von Hochleistungskomponenten für den Einsatz in extremen Umgebungen und fortschrittlichen Anwendungen.
Wie wird MoSi2-Pulver hergestellt?
Molybdändisilicid-Pulver für den 3D-Druck wird kommerziell mit verschiedenen Verfahren hergestellt, wobei es sich meist um Hochtemperaturreaktionen zwischen Molybdän und Silizium handelt.
Einige wichtige Produktionswege sind:
Reaktion der Elemente Mo und Si
MoSi2-Pulver kann durch direkte Reaktion von Molybdänpulver mit Siliziumpulver bei Temperaturen von über 1.400 °C im Vakuum oder unter Schutzgasatmosphäre hergestellt werden. Die Pulver werden zusammen gemahlen und durchlaufen die folgende Reaktion:
Mo (s) + 2Si (s) → MoSi2 (s)
Reduktion von MoO3
MoSi2-Pulver kann durch Reduktion von Molybdäntrioxid (MoO3)-Pulver mit Silizium, Kohlenstoff oder Wasserstoffgas hergestellt werden. Dabei wird eine Mischung aus MoO3- und Si-Pulver auf über 1.000 °C erhitzt, um die Reduktion einzuleiten:
MoO3 (s) + Si (s) → MoSi2 (s) + SiO2 (g)
MoO3 (s) + 3C (s) → MoSi2 (s) + 3CO (g)
MoO3 (s) + 3H2 (g) → MoSi2 (s) + 3H2O (g)
Siliziumisierung von Mo
MoSi2 wird durch Erhitzen von Molybdänmetallpulver mit Siliziumdampf oder siliziumhaltigen Gasen wie Silan (SiH4) gebildet. Das gasförmige Silizium diffundiert in die Mo-Pulverteilchen und erzeugt an den Teilchenoberflächen MoSi2.
Mo (s) + 2SiH4 (g) → MoSi2 (s) + 4H2 (g)
Das so entstandene MoSi2-Pulver wird weiter gemahlen und gesiebt, um die gewünschten Partikelgrößenverteilungen für 3D-Druckanwendungen zu erreichen.
Eigenschaften von MoSi2-Pulver für den 3D-Druck
Molybdändisilicid-Pulver für den 3D-Druck müssen strenge Spezifikationen für Eigenschaften wie Partikelgröße, Form und Reinheit erfüllen, um eine hohe Druckdichte zu ermöglichen.
Partikelgröße
Typische Größenverteilungen sind 10-45 μm oder 15-53 μm. Feine Pulver fördern die Ausbreitung und Dichte des Pulvers, während große Partikel die Fließfähigkeit des Pulvers verbessern. Die Partikelgröße beeinflusst die Mindestauflösung der Merkmale.
Morphologie der Partikel
Kugelförmige, abgerundete Pulverpartikel ermöglichen eine gleichmäßige Verteilung und Verdichtung des Pulvers während des Drucks. Unregelmäßig geformte Partikel behindern den Pulverfluss und können die Dichte negativ beeinflussen.
Reinheit
Eine hohe chemische Reinheit (>99,5% MoSi2) ist erforderlich, um Probleme mit Verunreinigungen zu vermeiden, die die Verdichtung und die Eigenschaften beeinträchtigen. Die wichtigsten zu kontrollierenden Verunreinigungen sind Sauerstoff, Kohlenstoff und metallische Elemente.
Fließfähigkeit
Das Pulver muss über Fließeigenschaften verfügen, die auf das Pulverhandhabungssystem des Druckers abgestimmt sind. Fließraten, Scherkräfte und Verteilbarkeit sind wichtige Parameter.
Zapfstellendichte
Bei höheren Schöpfdichten kann mehr Pulver in ein bestimmtes Volumen gepackt werden, was die Druckauflösung erhöht und die Porosität verringert. Typisch sind Abstichdichten von 4-5 g/cm3.
Eine strenge Kontrolle dieser Pulvereigenschaften gewährleistet einen zuverlässigen, hochwertigen Druck mit MoSi2-Rohstoffen. Auch die Druckparameter und die Nachbearbeitung sind entscheidend, um vollständig dichte Teile zu erhalten.
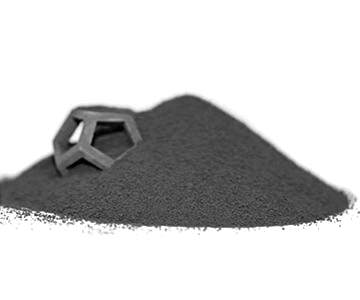
Schlüsselanwendungen von 3D-gedruckten MoSi2-Komponenten
Die außergewöhnlichen Hochtemperatureigenschaften von Molybdändisilicid ermöglichen viele neue Anwendungen von 3D-gedruckten Metallteilen unter Verwendung von MoSi2-Pulverrohstoffen.
Luft- und Raumfahrt
- Motorkomponenten – Turbinenschaufeln, Düsen, Brennkammern
- Hyperschallfahrzeuge – Vorderkanten, Antriebssysteme
- Raumfahrzeuge – Triebwerke, Motoren, Spiegel
Energie
- Kernreaktoren – Brennstoffhüllrohre, Wärmetauscher
- Fossile Brennstoffsysteme – Bohrlochkomponenten, Ventile, Werkzeuge
- Solarkonzentratoren – Reflektoren, Wärmetauscher
Automobilindustrie
- Rennsportkomponenten – Kolben, Turbolader, Auspuff
- Sensoren – Hochtemperatur-Druck- und Gassensoren
- Heizelemente – Zünder, Glühkerzen
Industriell
- Glasformen – Präzisionsgussteile, die gegen geschmolzenes Glas beständig sind
- Strangpresswerkzeuge – Für Keramik, Metalle, Polymere
- Heizelemente – Komponenten für Hochtemperaturöfen
Medizinische
- Orthopädische Implantate – Verschleißfeste Gelenkprothesen
- Zahnimplantate – Zahnersatz und Brücken
Der hohe Schmelzpunkt, die Festigkeit und die Oxidationsbeständigkeit von MoSi2 ermöglichen es den Bauteilen, in anspruchsvollen Umgebungen von über 1.500 °C zu überleben und zu funktionieren. Der 3D-Druck erleichtert die Herstellung komplexer, leistungsstarker Teile, die auf diese anspruchsvollen Anwendungen zugeschnitten sind.
Das 3D-Druckverfahren für MoSi2
Molybdändisilicid-Komponenten werden mit Hilfe von Standard-Pulverbettschmelzverfahren hergestellt, die für Hochtemperaturwerkstoffe angepasst sind. Dabei werden Schichten von MoSi2-Pulver mit einer fokussierten Wärmequelle in einer inerten Atmosphäre selektiv geschmolzen.
Pulverbettfusion
Beim Pulverbettschmelzen (Powder Bed Fusion, PBF) wird entweder ein Laser- oder ein Elektronenstrahl verwendet, um selektiv Material zu schmelzen und zu verschmelzen, das in einer dünnen Schicht auf einer Bauplatte verteilt ist. Das Verfahren findet in einer abgedichteten Kammer statt, die mit einem Inertgas wie Argon oder Stickstoff gefüllt ist.
Zu den gängigen PBF-Techniken, die bei MoSi2 eingesetzt werden, gehören:
- Selektives Laserschmelzen (SLM) – Verwendet einen Hochleistungslaser als Wärmequelle
- Elektronenstrahlschmelzen (EBM) – Verwendung eines fokussierten Elektronenstrahls zum Schmelzen
Druckverfahren
Das allgemeine 3D-Druckverfahren für MoSi2 umfasst:
- Das MoSi2-Pulver wird in einer dünnen Schicht mit Hilfe eines Rakels oder eines Pulverstreuersystems auf die Bauplattform aufgetragen.
- Der Laser oder E-Beam scannt und schmilzt selektiv Bereiche des Pulverbettes, die dem Teilequerschnitt entsprechen
- Die Bauplattform senkt sich, eine weitere Schicht Pulver wird darüber gestreut, und der Vorgang wiederholt sich
- Nachdem alle Schichten fertiggestellt sind, wird das 3D-gedruckte Teil aus dem Pulverbett entfernt.
- Ungeschmolzenes Pulver wird zurückgewonnen und zur Wiederverwendung in nachfolgenden Drucken gesiebt
Inerte Atmosphäre
Der Druck erfolgt unter Vakuum oder in inerter Atmosphäre mit einem Sauerstoffgehalt unter 50 ppm, um eine Oxidation des MoSi2-Pulvers zu verhindern. Übliche Atmosphären sind Argon, Stickstoff oder Mischungen wie Ar-5%H2.
Nachbearbeitung
Bereits gedruckte MoSi2-Teile werden häufig einer Nachbearbeitung unterzogen, wie z. B. dem heißisostatischen Pressen (HIP), um die Dichte zu erhöhen und die Materialeigenschaften nach dem Druck zu verbessern. Dadurch wird die Restporosität verdichtet.
Wichtige Druckparameter für MoSi2
Das Drucken von hochwertigen, vollständig dichten MoSi2-Bauteilen erfordert eine Optimierung der Druckparameter, die auf die einzigartigen Eigenschaften des Materials und des Pulvers zugeschnitten sind.
Laserleistung
- Typischer Bereich von 50-500 W
- Höhere Leistungsdichten fördern das Schmelzen und Verdichten
- Eine zu hohe Leistung kann zu Verdampfung oder Ablation führen
Scan-Geschwindigkeit
- Geschwindigkeiten von 100-1000 mm/s
- Langsamere Scans erhöhen den Energieaufwand und die Verdichtung
- Schnelle Scans können Porositätsfehler erzeugen
Abstand zwischen den Luken
- Abstände von ~50-200 μm zwischen den Scanlinien
- Größere Abstände verursachen Porosität zwischen den Schmelzbecken
- Engere Abstände erhöhen die Dichte
Schichtdicke
- Schichtdicke von 20-100 μm
- Dünnere Schichten verbessern Auflösung und Genauigkeit
- Dickere Schichten bauen Teile schneller auf
Inertgasfluss
- Niedrige Durchflussraten <10 L/min während des Drucks
- Entfernt Prozessnebenprodukte wie Kieselsäure
- Höherer Durchfluss kann ungeschmolzenes Pulver stören
Vorwärmtemperatur
- Vorwärmen des Substrats auf 300-1000°C
- Verbessert die Sinterung des Pulvers und die Wärmeleitfähigkeit
- Reduziert Eigenspannungen und Rissbildung
Eine Optimierung dieser Parameter ist erforderlich, um vollständig dichte, lunkerfreie MoSi2-Druckteile mit guter struktureller Integrität und guten Eigenschaften zu erhalten.
Nachbearbeitungsmethoden für MoSi2-Teile
Vorgedruckte Molybdändisilizid-Komponenten werden häufig einer zusätzlichen Nachbearbeitung unterzogen, um ihre Materialeigenschaften und Leistung zu verbessern.
Heiß-Isostatisches Pressen (HIP)
Beim HIP werden gleichzeitig Wärme und hoher isostatischer Druck angewendet, um innere Hohlräume zu schließen und die Dichte zu erhöhen. Typische HIP-Bedingungen sind 1.200°C bei 100-200 MPa für 2-4 Stunden in einer inerten Atmosphäre. Dadurch kann die Dichte auf über 99 % erhöht werden.
Wärmebehandlung
Eine Wärmebehandlung bei 1.400-1.600 °C unter Schutzgas oder im Vakuum verdichtet die Teile weiter, indem sie das Sintern und das Kornwachstum fördert. Dadurch werden auch Restspannungen aus dem Druck abgebaut.
Oberflächenbearbeitung
Bearbeitungsvorgänge wie Fräsen oder Schleifen können angewandt werden, um die Oberflächengüte und die Maßhaltigkeit der gedruckten Teile zu verbessern. Auf diese Weise werden auch alle Oberflächenfehler beseitigt.
Beschichtungen
Das Aufbringen keramischer Beschichtungen durch chemische oder physikalische Abscheidung aus der Dampfphase dient dem Umweltschutz. Aluminid- und Silizidbeschichtungen verbessern die Oxidations- und Korrosionsbeständigkeit.
Infiltration
Bei hochporösen Drucken erhöht die Infiltration von Füllmetallen wie Kupfer oder Nickel die Verdichtung und Festigkeit. Dadurch wird das Bauteil zu einem MoSi2-Metall-Verbundwerkstoff umgewandelt.
Die Kombination aus der Verfeinerung des Druckprozesses und einer geeigneten Nachbearbeitung ermöglicht MoSi2-Bauteile mit optimaler Mikrostruktur und den gewünschten Materialeigenschaften.
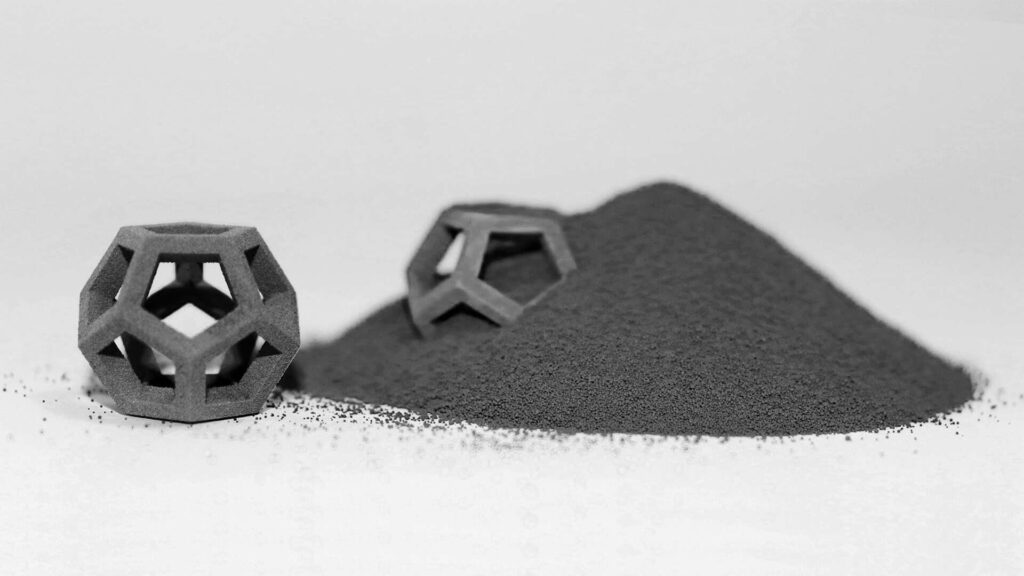
Mikrostruktur von gedrucktem MoSi2
Die Mikrostruktur von gedrucktem MoSi2 unterscheidet sich deutlich von herkömmlichen MoSi2-Keramiken, die durch Pulververarbeitung und Sintern hergestellt werden. Dies hat wichtige Auswirkungen auf die Eigenschaften des Materials.
Struktur der Körner
- Vorwiegend längliche, säulenförmige Körner, die in der Aufbaurichtung ausgerichtet sind
- Epitaxiales Wachstum über Schmelzbäder hinweg erzeugt kristalline Kontinuität
- Gleichachsige feine Körner in einigen Regionen
- Gesamtkorngröße typischerweise 10-100 μm
Defekte
- Porosität aufgrund fehlender Schmelzfehler
- Risse zwischen den Schichten durch Eigenspannungen
- Gelegentlich ungeschmolzene Partikel entlang der Korngrenzen
Phasen
- Überwiegend tetragonale β-MoSi2-Phase
- Kleine Anteile von hexagonalem α-MoSi2 in einigen Fällen
- Spuren von Molybdän und Silizid-Unterphasen
Zusammensetzung
- Nahe der nominalen MoSi2-Stöchiometrie
- Ein gewisser Si-Verlust durch Verdunstung führt zu einer leicht Mo-reichen Zusammensetzung
- Sauerstoffaufnahme bis zu einem Gehalt von 0,5-1 Gew.-%
Die einzigartige Mikrostruktur im Druckverfahren resultiert aus dem schnellen Schmelzen und Erstarren während des schichtweisen Druckprozesses. Die Maximierung der Dichte und die Optimierung der Kornstruktur sind aktive Forschungsbereiche.
Mechanische Eigenschaften von gedrucktem MoSi2
Molybdändisilicid, das durch Pulverbettschmelzen gedruckt wird, weist dank seiner starken atomaren Bindung, seiner Feuerfestigkeit und seines Mikrostrukturaufbaus gute mechanische Eigenschaften auf.
Stärke
- Hohe Biegefestigkeit bis zu ~850 MPa
- Druckfestigkeit über 1.500 MPa
- Die Zugfestigkeit reicht von 200-450 MPa
Härte
- Vickershärte von 5-9 GPa je nach Dichte
- Annäherung an die Härte von gesintertem MoSi2
Bruchzähigkeit
- Gemeldete Werte von 4-7 MPafm^1/2
- Niedriger als gesintertes MoSi2 aufgrund von Mikrorissen
Hohe Temperaturbeständigkeit
- Festigkeiten von mehr als 500 MPa bei 1.000°C
- Allmähliche Abnahme über 1.200°C
- Besser als gesintertes MoSi2
Widerstandsfähigkeit gegen thermische Schocks
- Temperaturschockparameter von 250-400 W/m
- Widerstandsfähig gegen Rissbildung bei Temperaturschwankungen
Mit der weiteren Verfeinerung des Drucks und der Nachbearbeitung verbessern sich die Eigenschaften der 3D-gedruckten MoSi2-Teile weiter in Richtung ihrer theoretischen Grenzen.
Vorteile und mögliche Probleme des MoSi2-Pulverdrucks
Molybdändisilicid besitzt zweifellos hervorragende Eigenschaften, die es für den Druck von Hochleistungsmetallkomponenten sehr attraktiv machen. Allerdings gibt es auch einige Nachteile und technische Herausforderungen, die es zu bewältigen gilt.
Vorteile
- Hohe Festigkeit bis über 1500°C
- Ausgezeichnete Oxidationsbeständigkeit an der Luft
- Geringere Dichte als Wolfram- oder Molybdän-Legierungen
- Komplexe Geometrien können gedruckt werden
- Eigenschaften überschrittener gesinterter MoSi2
Mögliche Probleme
- Sprödigkeit und Anfälligkeit für Risse
- Ausmaß der Porosität in den gedruckten Teilen
- Schwierigkeiten bei der Handhabung des Pulvers durch unregelmäßige Partikel
- Relativ hohe Materialkosten
- Mangelnde Legierungsentwicklung im Vergleich zu Superlegierungen
Weitere Forschungsarbeiten zur Optimierung der Druckparameter, zur Entwicklung neuer Legierungszusammensetzungen und zur Verbesserung der Nachbearbeitung werden dazu beitragen, die derzeitigen Grenzen der additiven Fertigung von MoSi2 zu überwinden.
Kostenanalyse von MoSi2-Pulver
Molybdändisilicid-Pulver für den 3D-Druck ist deutlich teurer als herkömmliche Metallpulver wie Edelstahl. Der Preisunterschied ist jedoch für extrem anspruchsvolle Hochtemperaturanwendungen gerechtfertigt.
Kosten für Rohmaterial
- Die Preise für Molybdän-Metall liegen zwischen $25-40/lb
- Die Preise für Siliziummetall liegen zwischen $1-2/lb
- Die Ausbeute bei der Pulverproduktion beträgt 70-90 %.
MoSi2-Pulver Kosten
- Typische Kosten für MoSi2-Pulver sind $75-150/lb
- Ungefähr 3-5 mal mehr als 316L Edelstahlpulver
Komponente Kosteneinsparungen
- Reduzierter Abfall durch optimierte Geometrien
- Geringere Einkaufskosten im Vergleich zur maschinellen Bearbeitung
- Verringerung der Durchlaufzeiten und der Lagerbestände
Einzigartige Fähigkeiten
- Zugang zu neuen Geometrien und Leistungen
- Komponenten arbeiten unter extremen Temperaturen
- Ermöglicht neue Produktinnovationen
Trotz der höheren Anschaffungskosten bietet MoSi2-Pulver einen langfristigen Nutzen für die Herstellung spezieller Hochtemperaturkomponenten mit verbesserter Leistung.
Gesundheits- und Sicherheitshinweise für MoSi2
Als hochentwickeltes keramisches Material erfordert Molybdändisilizidpulver ähnlich wie andere feine Metallpulver, die im 3D-Druck verwendet werden, entsprechende Vorsichtsmaßnahmen.
Gefahren durch Pulver
- Geringe Partikelgröße stellt eine Gefahr beim Einatmen dar
- Mögliche Sensibilisierung durch wiederholte Exposition
- Pulver immer in gut belüfteten Bereichen handhaben
Druck-Emissionen
- Beim Schmelzen können reizende Dämpfe und Partikel entstehen
- Verwenden Sie eine Abluftanlage für Drucker
Schutz der Arbeitnehmer
- Schutzausrüstung tragen – Atemschutz, Handschuhe, Augenschutz
- Hautkontakt mit Puder minimieren
- Einhaltung der empfohlenen Expositionsgrenzwerte
Umweltfreigabe
- Verhindern Sie das Verschütten von Pulver und den Verlust von Rückhaltemitteln
- Entsorgungsvorschriften beachten
Forschungsfortschritt beim MoSi2-Druck
Die aktive Forschung treibt die Technologie der additiven MoSi2-Fertigung an mehreren Fronten voran, von neuartigen Methoden der Pulverherstellung bis hin zu Inline-Überwachungsverfahren.
Neuartige Pulversynthese
- Die ultraschallgestützte Synthese ermöglicht die Kontrolle der Morphologie und Größenverteilung von MoSi2-Pulver
- Verbrennungssynthese von Molybdän- und Silizium-Nanopulver-Vorläufern ergibt ultrafeine <50 nm-Pulver
- Plasmasphäroidisierung von unregelmäßigen Pulvern verbessert die Fließfähigkeit des Pulvers für den Druck
- Selektives Laserschmelzen ermöglicht die direkte Synthese von MoSi2-Pulver aus Molybdän und Silizium
Defektkontrolle
- Inline-Überwachung mit Hochgeschwindigkeits-Bildgebung erkennt Defekte, sobald sie entstehen
- Modellierung von thermischen Spannungen und Verformungen minimiert die Rissbildung
- Kornstrukturmanipulation mit geimpften Kernen kontrolliert Anisotropie
- Optimierte Scan-Strategien steuern präzise die Abmessungen des Schmelzepools
In-Situ-Legierung
- Reaktiver Druck durch Infiltration von Molybdänpulver mit Silikonschmelzen
- Zusätzliche Legierungselemente wie Wolfram oder Rhenium, die in das Pulverbett eingebracht werden
- Gradierte Zusammensetzungen und funktionell gradierte Teile, die durch die Steuerung von Schmelzbädern gedruckt werden
Modifizierung der Oberfläche
- Laserauftragsschweißen von metallischen Schichten wie Nickelaluminid als Oxidationsschutz
- Pulverbettinfiltration mit Kupfer verbessert die thermische und elektrische Leitfähigkeit
- Das Einbringen von Nanopartikeln in Pulverschichten verändert das Kornwachstum und die Eigenschaften
In Entwicklung befindliche Anwendungen
Zukunftsweisende Anwendungen von 3D-gedrucktem Molybdändisilizid werden in sehr anspruchsvollen Bereichen wie Hyperschall, Kernenergie und 3D-Druck von Metallen entwickelt.
Hyperschall
- Leichte Brennkammern und Düsen für Scramjet-Triebwerke
- Scharfe Vorderkanten für Wiedereintrittsfahrzeuge und Hyperschallflugzeuge
- Heiße Strukturen für Antriebssysteme und Wärmeschutz
Kernenergie
- Brennstoffhüllen mit erhöhter Unfalltoleranz
- Komplexe Geometrien für gasgekühlte Reaktorkomponenten
- Systeme zur Lagerung und Entsorgung radioaktiver Abfälle
Additive Fertigung
- Gitterstrukturen mit negativem Wärmeausdehnungskoeffizienten
- Hochtemperatursuszeptoren für das Sintern im Mikrowellenbereich
- Präzisionsdüsenanordnungen für Pulverbettschmelzdruckköpfe
Die einzigartigen Eigenschaften von 3D-gedrucktem MoSi2 erweitern die Grenzen der Hochtemperatur-Materialtechnologie und ermöglichen Bauteildesigns der nächsten Generation.
Ausblick auf die Zukunft
Molybdändisilicid besitzt außergewöhnliche Eigenschaften, die es zu einem hochgeschätzten Pulvermaterial für den Druck spezieller Metallkomponenten machen.
- Die Einführung wird sich bei Hyperschall-, Weltraum- und Nuklearanwendungen beschleunigen.
- Die Entwicklung von Legierungen wird die mechanischen Eigenschaften und die Bruchzähigkeit verbessern
- Die Kosten werden mit der Ausweitung der Pulverherstellung sinken
- Verstärkter Wettbewerb wird die Qualität verbessern und das Materialangebot erweitern
- Design-Tools optimieren Geometrien für thermische und strukturelle Leistung
- Der Hybriddruck mit abgestuften Zusammensetzungen wird eine verbesserte Funktionalität bieten
- Es werden Normen zur Qualifizierung von Teilen für die Luft- und Raumfahrt sowie für die Kerntechnik entwickelt.
- Großserienproduktion wird durch mehrere Großformatdrucker ermöglicht
Durch die Nutzung der Vorteile von MoSi2 und 3D-Druck können Hersteller die Leistungsgrenzen und den Designumfang für die anspruchsvollsten Betriebsumgebungen erweitern.
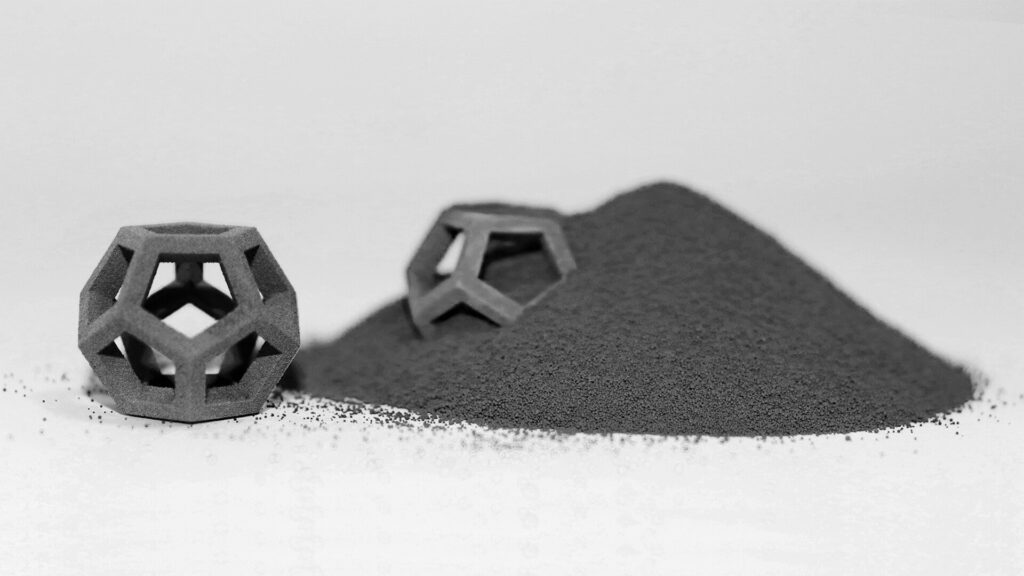
Schlussfolgerung
Molybdändisilicid verfügt über eine einzigartige Kombination von Eigenschaften wie hohe Festigkeit, Kriechfestigkeit, Oxidationsbeständigkeit und Wärmeleitfähigkeit bis zu extrem hohen Temperaturen von über 1500 °C. Diese Attribute in Verbindung mit den neuen Möglichkeiten des 3D-Drucks komplexer Geometrien aus MoSi2-Pulver eröffnen spannende neue Anwendungen in der Luft- und Raumfahrt, im Energiesektor, in der Automobilindustrie, in der Medizin und in der Industrie.
Die Herstellung von hochreinen, kugelförmigen Pulvern, die für die additive Fertigung optimiert sind, stellt jedoch noch eine technische Herausforderung dar. Die Verfeinerung der Druckparameter zur Erzielung von Teilen mit hoher Dichte und die Entwicklung von Nachbearbeitungsverfahren zur Verbesserung der Eigenschaften und der Leistung werden weiterhin angestrebt. Legierungen und Nanotechnologie werden weitere Verbesserungen ermöglichen.
Aber die Zukunftsaussichten für die additive Fertigung von MoSi2 sind sehr gut. Durch die Nutzung der Synergien zwischen diesem außergewöhnlichen Material und der geometrischen Freiheit des 3D-Drucks werden die Hersteller die Leistungsgrenzen immer weiter nach oben verschieben. Dies wird zu leichteren, stärkeren und leistungsfähigeren Komponenten führen, die auch in den extremsten Umgebungen eingesetzt werden können.
FAQ
Was ist Molybdändisilicid (MoSi2)?
Molybdändisilicid (MoSi2) ist ein fortschrittliches keramisches Material, das aus Molybdän und Silicium besteht. Es hat eine tetragonale Kristallstruktur und einen sehr hohen Schmelzpunkt von 2030°C. Zu den wichtigsten Eigenschaften gehören hohe Festigkeit, Oxidationsbeständigkeit, Wärmeleitfähigkeit und Temperaturwechselbeständigkeit.
Warum ist MoSi2 für den 3D-Druck geeignet?
MoSi2 verfügt über Eigenschaften, die sich ideal für den 3D-Druck von Hochtemperaturkomponenten eignen. Dazu gehören ein hoher Schmelzpunkt, eine ausgezeichnete Oxidationsbeständigkeit, eine gute Festigkeit bei hohen Temperaturen, eine geringe Dichte und thermische Eigenschaften, die thermische Spannungen minimieren. Dadurch können die gedruckten Teile in extremen Umgebungen eingesetzt werden.
Wie wird MoSi2-Pulver hergestellt?
MoSi2-Pulver wird kommerziell durch Reaktion von Molybdän und Silizium bei hohen Temperaturen von über 1400 °C hergestellt. Andere Methoden umfassen die Reduktion von MoO3 mit Silizium oder die Herstellung von MoSi2-Beschichtungen auf Molybdänpartikeln durch Dampfphasenreaktionen. Das Pulver wird gemahlen und klassifiziert, um eine für den 3D-Druck geeignete Partikelgröße zu erhalten.
Welches 3D-Druckverfahren wird bei MoSi2 verwendet?
MoSi2 wird fast ausschließlich durch Pulverbettschmelzverfahren wie selektives Laserschmelzen (SLM) und Elektronenstrahlschmelzen (EBM) hergestellt. Bei diesen Verfahren werden Pulverschichten mithilfe einer fokussierten Wärmequelle in einer inerten Atmosphäre selektiv geschmolzen.
Muss MoSi2 nach dem 3D-Druck nachbearbeitet werden?
Ja, gedruckte MoSi2-Teile werden häufig nachbearbeitet, z. B. durch heißisostatisches Pressen (HIP) oder Wärmebehandlung, um die Dichte zu erhöhen, Spannungen abzubauen und die Materialeigenschaften zu verbessern. Es können auch zusätzliche Oberflächenbehandlungen oder Beschichtungen vorgenommen werden.
Was sind die wichtigsten Anwendungen für 3D-gedrucktes MoSi2?
Zu den wichtigsten Anwendungen, die von den Hochtemperaturfähigkeiten von MoSi2 profitieren, gehören Komponenten für die Luft- und Raumfahrt wie Hyperschallantriebe und Strukturen für Wiedereintrittsfahrzeuge, Teile für Kernreaktoren, Sensoren und Turbolader für die Automobilindustrie, Komponenten für den 3D-Druck aus Metall und industrielle Werkzeuge.
Was sind die größten Herausforderungen beim Drucken von MoSi2?
Zu den entscheidenden Herausforderungen gehören die Herstellung von hochreinem Pulver, das für die additive Fertigung optimiert ist, die Minimierung von Porosität und Rissbildung in gedruckten Teilen, die Verbesserung der Bruchzähigkeit und die Senkung der Kosten. Auch die Entwicklung von Legierungen ist im Vergleich zu herkömmlichen Hochtemperaturlegierungen relativ unreif.
Ist der Druck mit MoSi2 sicher?
Wie bei jedem feinen Metallpulver sind beim Umgang mit MoSi2-Pulver bestimmte Vorsichtsmaßnahmen erforderlich, um die Staubentwicklung zu minimieren. Das Drucken sollte unter angemessener Belüftung und in einer inerten Atmosphäre erfolgen. Die Bediener der Drucker sollten persönliche Schutzausrüstung tragen und gute Arbeitspraktiken anwenden.