Visão geral de Modelagem de rede de engenharia a laser (LENS)
O Laser Engineering Net Shaping, comumente conhecido como LENS, é uma técnica avançada de manufatura aditiva que utiliza lasers de alta potência para criar peças metálicas complexas e de alto desempenho. Diferentemente dos métodos tradicionais de fabricação, o LENS é conhecido por sua capacidade de construir diretamente estruturas 3D a partir de pós metálicos, que são derretidos e depositados camada por camada.
A versatilidade do LENS o torna particularmente valioso em setores que exigem peças metálicas complexas com propriedades mecânicas superiores, como os setores aeroespacial, de defesa e biomédico. Mas o que exatamente diferencia o LENS de outros métodos de fabricação? E por que você deve considerar usá-lo em seu próximo projeto? Vamos nos aprofundar no fascinante mundo do LENS.
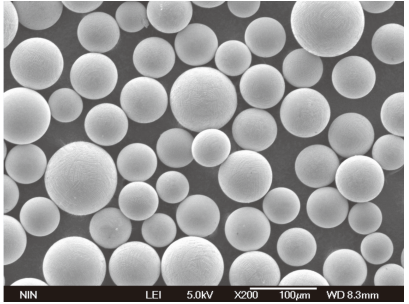
Como o LENS funciona?
Imagine construir uma escultura, mas, em vez de esculpir um bloco de pedra, você está adicionando material camada por camada até que a forma desejada surja. Essa é a essência do LENS. Veja a seguir um detalhamento passo a passo:
- Foco do feixe de laser: Um feixe de laser de alta potência é focalizado em um substrato.
- Injeção de pó metálico: O pó metálico é injetado no ponto focal do feixe de laser usando um bocal de distribuição de pó.
- Fusão e solidificação: O laser derrete o pó metálico e, ao esfriar, ele se solidifica para formar uma nova camada.
- Construção camada por camada: Esse processo se repete à medida que a peça é construída camada por camada, seguindo um design gerado por computador.
Vantagens da LENS:
- Precisão: O LENS pode produzir peças com geometrias complexas e detalhes finos.
- Eficiência do material: Como o material é adicionado somente onde é necessário, o desperdício é mínimo.
- Personalização: As peças podem ser personalizadas em tempo real, o que é ideal para prototipagem e fabricação sob medida.
Materiais usados na LENTE: Pós metálicos
Um dos aspectos mais interessantes do LENS é a ampla variedade de pós metálicos que podem ser usados. Esses pós são projetados especificamente para o processo LENS, garantindo desempenho consistente e produtos finais de alta qualidade.
Pós metálicos comuns usados em lentes
Pó metálico | Composição | Formulários | Propriedades exclusivas |
---|---|---|---|
Liga de titânio (Ti-6Al-4V) | 90% Titânio, 6% Alumínio, 4% Vanádio | Aeroespacial, implantes biomédicos | Alta relação força/peso, resistência à corrosão |
Inconel 718 | Níquel, cromo, ferro | Aeroespacial, Lâminas de turbina | Resistência a altas temperaturas, durabilidade |
Aço inoxidável 316L | Ferro, cromo, níquel | Dispositivos médicos, aplicativos marítimos | Resistência à corrosão, biocompatibilidade |
Alumínio 6061 | Alumínio, magnésio, silício | Automotivo, aeroespacial | Leve, com boas propriedades mecânicas |
Cobalto-cromo (CoCr) | Cobalto, cromo, molibdênio | Implantes dentários, turbinas a gás | Resistência ao desgaste, alta resistência |
Aço Maraging (18Ni300) | Ferro, níquel, cobalto | Ferramental, Aeroespacial | Resistência ultra-alta, fácil tratamento térmico |
Carbeto de tungstênio (WC-Co) | Tungstênio, Cobalto | Ferramentas de corte, equipamentos de mineração | Extrema dureza, resistência ao desgaste |
Liga de cobre (CuCrZr) | Cobre, cromo, zircônio | Componentes elétricos, trocadores de calor | Excelente condutividade térmica e resistência |
Hastelloy X | Níquel, molibdênio, cromo | Processamento químico, motores a jato | Resistência à oxidação, alta resistência |
Aço para ferramentas (H13) | Ferro, carbono, cromo | Moldes, matrizes, ferramentas | Dureza, resistência ao desgaste |
Composição de pós metálicos comuns para LENS
Ao selecionar um pó metálico para o LENS, é fundamental entender a composição específica de cada material, pois isso influencia diretamente as propriedades mecânicas e a adequação a várias aplicações.
Composição detalhada de pós metálicos
Pó metálico | Elementos primários | Elementos adicionais | Aplicativos comuns |
---|---|---|---|
Liga de titânio (Ti-6Al-4V) | Titânio (90%) | Alumínio (6%), vanádio (4%) | Aeroespacial, Implantes médicos |
Inconel 718 | Níquel (50-55%) | Cromo (17-21%), ferro (5-9%) | Turbinas, motores a jato |
Aço inoxidável 316L | Ferro (60-65%) | Cromo (16-18%), níquel (10-14%) | Marinha, dispositivos biomédicos |
Alumínio 6061 | Alumínio (97-98%) | Magnésio (0,8-1,2%), Silício (0,4-0,8%) | Automotivo, aeroespacial |
Cobalto-cromo (CoCr) | Cobalto (55-65%) | Cromo (26-30%), molibdênio (5-7%) | Odontológico, Turbinas a gás |
Aço Maraging (18Ni300) | Ferro (60-65%) | Níquel (18-20%), Cobalto (7-8%) | Ferramental, Aeroespacial |
Carbeto de tungstênio (WC-Co) | Tungstênio (85-90%) | Cobalto (6-10%) | Ferramentas de corte, mineração |
Liga de cobre (CuCrZr) | Cobre (96-98%) | Cromo (0,5-1,2%), Zircônio (0,1-0,2%) | Elétrica, trocadores de calor |
Hastelloy X | Níquel (47-52%) | Molibdênio (8-10%), cromo (20-23%) | Produtos químicos, motores a jato |
Aço para ferramentas (H13) | Ferro (85-90%) | Carbono (0,32-0,45%), cromo (4,75-5,5%) | Moldes, ferramentas |
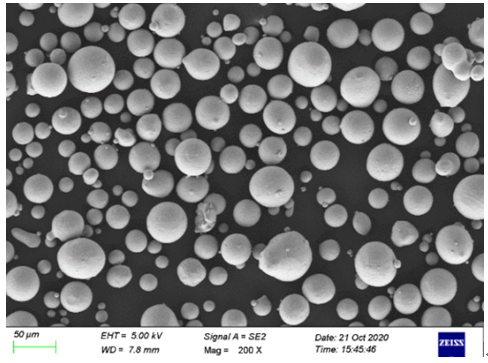
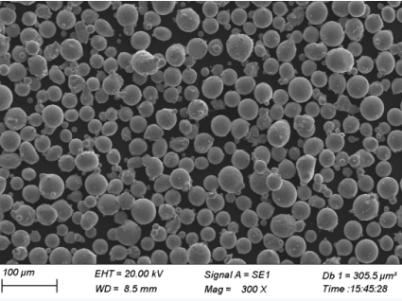
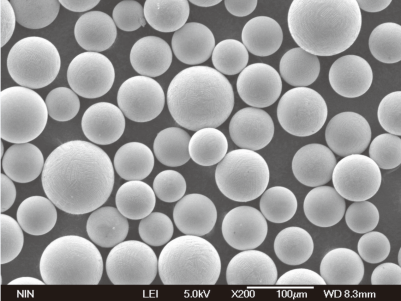
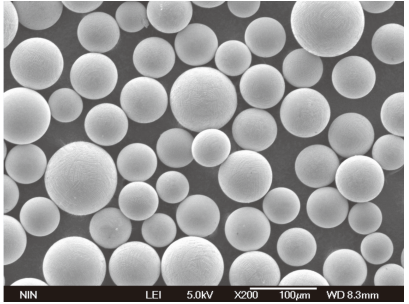
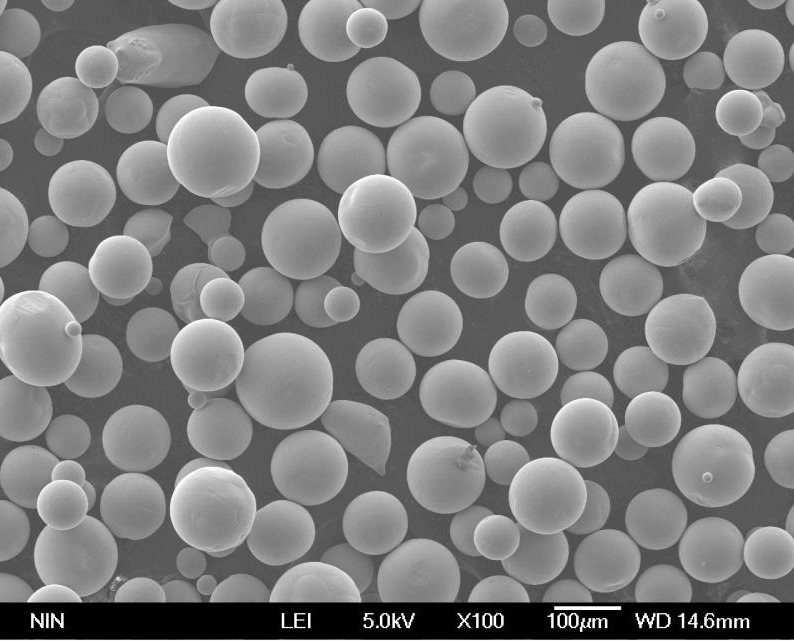
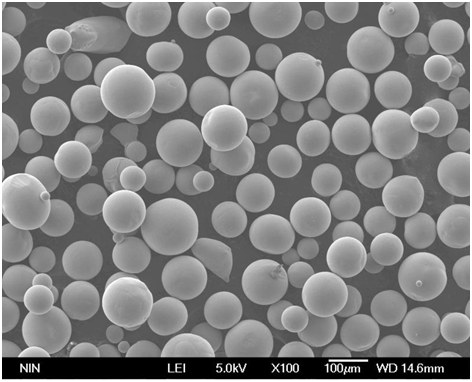
Características dos componentes produzidos pela LENS
A tecnologia LENS é conhecida por produzir peças com características exclusivas que as diferenciam daquelas produzidas por métodos tradicionais. Vamos explorar o que torna esses componentes especiais:
Principais características dos componentes do LENS
Característica | Descrição | Benefício |
---|---|---|
Alta precisão | O LENS pode produzir peças com detalhes intrincados e tolerâncias rígidas. | Ideal para projetos complexos. |
Propriedades superiores do material | O processo LENS pode aprimorar as propriedades do material, como resistência e durabilidade. | Melhor desempenho em aplicações exigentes. |
Pós-processamento mínimo | As peças LENS geralmente exigem pouco ou nenhum pós-processamento. | Reduz o tempo e os custos de produção. |
Versatilidade em materiais | Uma ampla variedade de pós metálicos pode ser usada no LENS. | Flexibilidade na escolha do material certo para o trabalho. |
Construção camada por camada | As peças são construídas camada por camada, o que permite um controle preciso da forma final. | Personalização e ajuste fino de projetos. |
Aplicações da tecnologia LENS
A tecnologia LENS está sendo adotada em vários setores devido aos seus recursos exclusivos. Abaixo está uma tabela que destaca as principais aplicações do LENS em diferentes setores:
Aplicações do setor da tecnologia LENS
Setor | Aplicativos específicos | Vantagens de usar o LENS |
---|---|---|
Aeroespacial | Lâminas de turbina, componentes estruturais, reparo de peças desgastadas | Componentes leves e de alta resistência, possibilidade de reparo |
Médico | Implantes personalizados, próteses dentárias | Materiais biocompatíveis, precisão, personalização |
Automotivo | Componentes leves, prototipagem | Prototipagem rápida, eficiência de material |
Defesa | Componentes de blindagem, sistemas de armas | Maior durabilidade, geometrias complexas |
Energia | Peças de turbina, trocadores de calor, células de combustível | Resistência a altas temperaturas, eficiência do material |
Ferramentas | Moldes, matrizes, ferramentas de corte | Durabilidade, resistência ao desgaste, prazos de entrega reduzidos |
Petróleo e gás | Ferramentas de fundo de poço, válvulas e bombas | Resistência à corrosão, força do material |
Eletrônicos | Dissipadores de calor, componentes condutores | Condutividade térmica, engenharia de precisão |
Marinha | Eixos de hélice, peças do leme, componentes da bomba | Resistência à corrosão, força |
Processamento químico | Componentes do reator, trocadores de calor | Resistência à corrosão, desempenho em altas temperaturas |
Especificações, tamanhos, graus e padrões da LENS
Ao trabalhar com a tecnologia LENS, é importante entender as especificações, os tamanhos, os graus e os padrões associados aos pós metálicos e aos componentes.
Especificações e padrões para materiais LENS
Material | Especificação/Grau | Padrão | Tamanhos típicos |
---|---|---|---|
Liga de titânio (Ti-6Al-4V) | ASTM F1472, Grau 5 | ASTM International | Pó: 15-45 µm |
Inconel 718 | AMS 5662, UNS N07718 | SAE Internacional | Pó: 10-53 µm |
Aço inoxidável 316L | ASTM A240, UNS S31603 | ASTM International | Pó: 10-45 µm |
Alumínio 6061 | ASTM B209, UNS A96061 | ASTM International | Pó: 15-63 µm |
Cobalto-cromo (CoCr) | ASTM F75, UNS R30075 | ASTM International | Pó: 15-45 µm |
Aço Maraging (18Ni300) | AMS 6514, UNS K93120 | SAE Internacional | Pó: 10-45 µm |
Carbeto de tungstênio (WC-Co) | ISO 9001:2008 | Padrões ISO | Pó: 20-70 µm |
Liga de cobre (CuCrZr) | ASTM B422, UNS C18150 | ASTM International | Pó: 10-45 µm |
Hastelloy X | AMS 5754, UNS N06002 | SAE Internacional | Pó: 15-53 µm |
Aço para ferramentas (H13) | ASTM A681, UNS T20813 | ASTM International | Pó: 10-45 µm |
Vantagens e limitações do LENS
A tecnologia LENS oferece inúmeros benefícios, mas também é importante reconhecer suas limitações. Veja a seguir uma comparação:
Vantagens e limitações do LENS
Vantagens | Limitações |
---|---|
Alta precisão | Custo: A LENS pode ser cara devido aos equipamentos e materiais envolvidos. |
Eficiência do material | Complexidade: O processo é tecnicamente complexo e requer operadores qualificados. |
Personalização | Acabamento da superfície: As peças podem exigir pós-processamento adicional para obter o acabamento de superfície desejado. |
Ampla gama de materiais | Limitação de tamanho: O LENS é normalmente limitado a peças menores devido à natureza do processo. |
Reparabilidade | Velocidade: A LENS pode ser mais lenta em comparação com outros métodos de fabricação para produção em larga escala. |
Propriedades mecânicas aprimoradas | Configuração inicial: Os altos custos iniciais de instalação podem ser um obstáculo para as pequenas empresas. |
Comparação do LENS com outras técnicas de manufatura aditiva
O LENS é frequentemente comparado a outros métodos de manufatura aditiva, como a sinterização direta a laser de metal (DMLS) e a fusão seletiva a laser (SLM). Vamos detalhar as diferenças:
LENS vs. outros métodos de manufatura aditiva
Recurso | LENTE | DMLS | SLM |
---|---|---|---|
Faixa de material | Ampla gama, incluindo ligas de alto desempenho | Principalmente metais, menos materiais exóticos | Ampla faixa, semelhante à LENS |
Precisão | Alta, com possibilidade de detalhes finos | Muito alta, ideal para designs complexos | Alto, comparável ao LENS |
Custo | Configuração cara, econômica para peças de alto valor | Moderadamente caro | Semelhante ao LENS, dependendo do material |
Velocidade | Moderado, adequado para peças complexas | Geralmente mais rápido para peças menores | Mais rápido que o LENS para determinadas aplicações |
Pós-processamento | Mínimo necessário | É necessário algum pós-processamento | Requer pós-processamento significativo |
Formulários | Aeroespacial, médico, ferramental | Aeroespacial, automotivo, médico | Aeroespacial, médico, industrial |
Detalhes de fornecedores e preços de materiais LENS
Entender onde obter os materiais LENS e seus custos associados é fundamental para o orçamento e o planejamento de seus projetos.
Fornecedores e preços para materiais LENS
Material | Fornecedor | Preço aproximado por kg |
---|---|---|
Liga de titânio (Ti-6Al-4V) | Carpenter Technology, Oerlikon AM | $300 – $500 |
Inconel 718 | Praxair Surface Technologies, Sandvik | $150 – $300 |
Aço inoxidável 316L | Sandvik, Carpenter Technology | $50 – $100 |
Alumínio 6061 | Oerlikon AM, Tecnologia LPW | $30 – $60 |
Cobalto-cromo (CoCr) | Arcam AB, Sandvik | $400 – $600 |
Aço Maraging (18Ni300) | LPW Technology, EOS GmbH | $200 – $350 |
Carbeto de tungstênio (WC-Co) | H.C. Starck, Global Tungsten & Powders | $500 – $700 |
Liga de cobre (CuCrZr) | Sandvik, Praxair Surface Technologies | $100 – $200 |
Hastelloy X | Tecnologia Carpenter, Tecnologia LPW | $300 – $500 |
Aço para ferramentas (H13) | EOS GmbH, Tecnologia LPW | $50 – $100 |
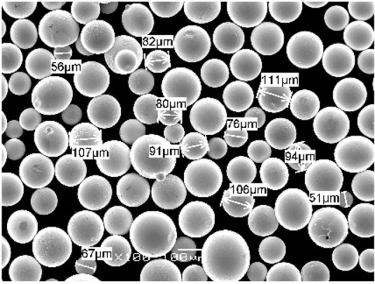
Perguntas frequentes
Pergunta | Resposta |
---|---|
Para que o LENS é usado? | O LENS é usado para fabricar peças metálicas de alto desempenho, reparar componentes desgastados e criar protótipos. |
Qual é a diferença entre a LENS e a manufatura tradicional? | O LENS constrói peças camada por camada a partir de pó metálico, oferecendo maior precisão e eficiência de material em comparação com os métodos tradicionais. |
Quais materiais podem ser usados no LENS? | É possível usar uma ampla variedade de pós metálicos, incluindo ligas de titânio, aço inoxidável, alumínio e superligas à base de níquel. |
O LENS é econômico? | O LENS pode ser econômico para peças complexas e de alto valor, mas pode ser caro para produção simples e em larga escala. |
Quais setores se beneficiam mais com o LENS? | Os setores aeroespacial, médico, automotivo e de defesa se beneficiam significativamente da precisão e da personalização oferecidas pelo LENS. |
Há alguma limitação de tamanho com o LENS? | Sim, o LENS é normalmente mais adequado para peças menores, embora os avanços na tecnologia estejam expandindo seus recursos. |
Como o LENS se compara a outros métodos de manufatura aditiva? | O LENS oferece propriedades de material e personalização superiores, mas pode ser mais lento e mais caro do que métodos como DMLS ou SLM. |
Quais são os principais desafios do LENS? | Os altos custos de configuração inicial, a complexidade técnica e a necessidade de operadores qualificados são desafios comuns. |
O LENS pode ser usado para produção em massa? | Embora o LENS seja ideal para peças especializadas e de alto valor, ele geralmente não é usado para produção em massa devido à sua velocidade mais lenta e ao custo mais alto. |
Que pós-processamento é necessário para as peças LENS? | As peças LENS normalmente exigem um pós-processamento mínimo, embora o acabamento da superfície possa ser necessário, dependendo da aplicação. |