Atomização de metais é um processo em que o metal é convertido de uma forma sólida a granel em um pó fino. O pó metálico fino produzido por atomização tem propriedades exclusivas e desempenha um papel importante em vários setores e aplicações.
Por que atomizar o metal?
A atomização permite a produção de pós metálicos com características e tamanhos de partículas precisos. Alguns dos principais benefícios dos pós metálicos atomizados incluem:
- Aumento da reatividade - Devido à alta relação entre a área de superfície e o volume, os pós atomizados são mais reativos quimicamente, permitindo um melhor desempenho em aplicações como catalisadores.
- Propriedades mecânicas aprimoradas - O pó atomizado pode ser usado para fabricar peças com propriedades mecânicas superiores em comparação com aquelas feitas de metal fundido ou forjado.
- Melhor combinação - A mistura homogênea e fina de diferentes metais e elementos de liga é possível com pós atomizados. Isso permite a obtenção de ligas e microestruturas exclusivas.
- Melhoria da fluidez - Os pós atomizados esféricos têm excelentes características de fluxo, o que ajuda no manuseio, no transporte e na medição de precisão automatizados.
- Maior densidade - As peças fabricadas com pós atomizados podem atingir uma densidade próxima à total. Isso permite a fabricação de peças mais leves para aplicações sensíveis ao peso.
- Fabricação em forma de rede - A atomização seguida da consolidação do pó permite a fabricação em formato de rede. Isso reduz os custos de usinagem e o desperdício de material.
- Composições puras - Pós metálicos de alta pureza podem ser produzidos por atomização a vácuo, onde elementos reativos, como o alumínio, são protegidos da oxidação.
Em resumo, a atomização converte metais em pós extremamente finos com composições, tamanhos e morfologias personalizados. Isso abre uma ampla gama de técnicas e aplicações de fabricação nos setores automotivo, aeroespacial, biomédico, químico, de defesa e outros setores importantes.
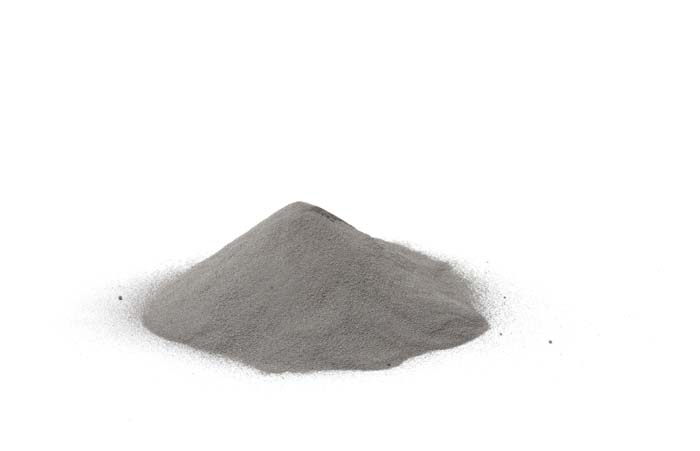
Métodos de atomização de metais
Há duas técnicas amplamente utilizadas para atomizar metais em pós finos:
Atomização de gás
Esse método usa ar comprimido ou um gás inerte, como nitrogênio ou argônio, para converter o metal em pó. O processo envolve:
- Aquecimento do metal a cerca de 30-50% acima do ponto de fusão. Exemplos comuns são níquel, cobalto, alumínio, aços, titânio, superligas etc.
- Forçar o fluxo de metal fundido através de um bocal a altas pressões de 5 a 20 bar.
- Quebrando o fluxo de metal em gotículas finas usando jatos de gás comprimido de alta velocidade.
- Solidificar as gotículas em pó, extraindo calor rapidamente à medida que elas caem na câmara de atomização.
- Coleta do pó atomizado em recipientes na parte inferior. A distribuição do tamanho das partículas é controlada pela taxa de fluxo de gás.
Os pós atomizados a gás têm um formato esférico e são populares para moldagem por injeção de metal (MIM), revestimentos por spray térmico e peças de metalurgia do pó.
Atomização da água
Nesse método, jatos de água de alta pressão são usados para atomizar ligas metálicas fundidas em pós finos. As etapas envolvem:
- Aquecimento por indução da carga metálica acima do ponto de fusão. As ligas de ferro, níquel, cobalto e cobre são comumente atomizadas.
- Despejar o metal líquido na câmara de atomização, onde vários jatos de água atingem o fluxo de metal a pressões superiores a 150 bar.
- Os jatos de água quebram o metal fundido em gotículas finas que se solidificam em pó.
- Coleta do pó depois que a água é drenada. Formam-se pós irregulares e mais angulares.
Os pós atomizados em água com maior captação de oxigênio são usados em peças sinterizadas, materiais de fricção e eletrodos de solda.
A atomização centrífuga e a atomização de gás por ultrassom são alguns outros métodos usados para aplicações especializadas.
Principais parâmetros do processo
Alguns parâmetros importantes que influenciam as propriedades e a qualidade dos pós atomizados são:
- Composição do metal - Os elementos de liga, as impurezas e a volatilidade dos componentes afetam a formação de partículas.
- Temperatura de superaquecimento - O superaquecimento mais alto do metal promove uma atomização mais fina. Porém, temperaturas muito altas podem causar a vaporização do elemento de liga.
- Projeto do bocal - O diâmetro do bico, o número de bicos e a geometria do bico afetam a taxa de fluxo do metal fundido, o tamanho da gota e a taxa de resfriamento.
- Fluido de atomização - A vazão de gás ou água determina o grau de atomização e o tamanho das partículas de pó.
- Distância de voo da gota - O maior tempo de voo da gota na câmara de atomização melhora a solidificação e a esfericidade.
- Taxa de resfriamento - Taxas de solidificação rápidas (~104-106 K/s) produzem microestruturas metaestáveis mais finas no pó.
Ao otimizar esses parâmetros, o processo de atomização pode ser adaptado para obter pós com tamanho de grão, distribuição de tamanho de partícula, forma e microestrutura desejados.
Principais aplicativos
Algumas das principais aplicações que utilizam pós metálicos atomizados são:
Moldagem por injeção de metal (MIM)
O MIM é um processo de metalurgia do pó para fabricar peças pequenas e complexas em grandes volumes. A matéria-prima feita com pós ultrafinos (<10 μm) atomizados com gás ou água é moldada por injeção e depois sinterizada. São produzidos componentes de alta resistência mecânica com excelente precisão dimensional para aplicações automotivas e de produtos de consumo.
Manufatura aditiva
Também conhecida como impressão 3D, os pós atomizados especialmente projetados são usados na sinterização seletiva a laser, na sinterização direta a laser de metal e em outras tecnologias aditivas para fabricar diretamente peças acabadas a partir de modelos CAD. Com esses métodos, é possível produzir peças quase em formato de rede com ligas e microestruturas personalizadas.
Revestimentos por spray térmico
Nessa técnica, os pós atomizados são aquecidos até as condições de fusão ou quase fusão e pulverizados em uma superfície em altas velocidades para formar um revestimento protetor. Ligas de revestimento duro e revestimentos resistentes ao desgaste são aplicados em lâminas de turbinas, componentes de motores, implantes biomédicos etc. usando pulverização térmica.
Compostos de matriz metálica
Os pós atomizados podem ser misturados com cerâmicas de reforço, como o carbeto de silício, para sintetizar compostos avançados de matriz metálica. Isso resulta em materiais com altíssimas taxas de resistência em relação ao peso, adequados para aplicações aeroespaciais.
Consumíveis de soldagem
Os eletrodos de soldagem para fins especiais e os arames de enchimento são fabricados com pós irregulares atomizados com água. As microestruturas de rápida solidificação proporcionam excelente soldabilidade.
Peças estruturais P/M
Os pós de ferro e aço atomizados com água são compactados e sinterizados para produzir rolamentos autolubrificantes e outras peças estruturais com boa tolerância dimensional e propriedades mecânicas.
Outros aplicativos
Hidretos metálicos finos, ímãs, catalisadores, agentes de administração de medicamentos e composições pirotécnicas são sintetizados usando pós atomizados altamente reativos. Eles também são usados em matérias-primas MIM, pastas de brasagem, contatos elétricos etc.
Portanto, em resumo, os pós atomizados atendem a uma seção transversal diversificada de técnicas de fabricação avançadas e aplicações de alto desempenho nos principais setores.
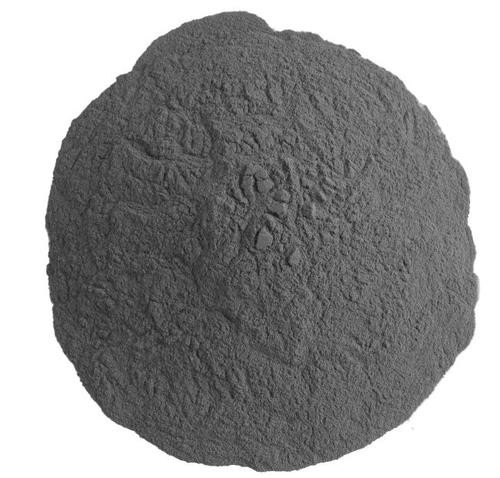
Benefícios econômicos e ambientais
Alguns dos principais benefícios econômicos e ambientais obtidos com a atomização de metais são:
- Usinagem reduzida - A fabricação de formas quase líquidas usando MIM e AM reduz os custos de matéria-prima e usinagem.
- Reutilização de sucata - A atomização acomoda sucata e lotes pequenos, inadequados para fundição.
- Eficiência energética - As peças fabricadas com pó atomizado requerem menos energia de fusão. O mínimo de desperdício de material também melhora a sustentabilidade.
- Produção just-in-time - Os pós atomizados podem ser rapidamente produzidos sob demanda, permitindo estoques e produção flexíveis.
- Desempenho superior - As propriedades mecânicas aprimoradas dos componentes de pó atomizado reduzem o desgaste, as falhas e as substituições de peças.
- Menos etapas de processamento - A fusão, a liga e a atomização combinadas em uma cadeia de processos reduzem o uso de energia e as emissões de carbono.
- Menores estoques - A atomização no local permite estoques enxutos de pó Just-In-Time, evitando custos de armazenamento e logística.
Portanto, a otimização dos parâmetros de atomização de metal proporciona benefícios significativos em termos de custo, além de minimizar o desperdício de material, o consumo de energia e a pegada de carbono.
Perspectivas futuras
Várias tendências apontam para o aumento da adoção da tecnologia de atomização:
- Novas ligas com propriedades e desempenho aprimorados impulsionarão a necessidade de pós atomizados. Há pesquisas em andamento sobre ligas de titânio, compostos de alumínio, ligas de alta entropia, ligas amorfas etc.
- A manufatura aditiva de metal continuará com um forte crescimento de dois dígitos à medida que novos componentes impressos em 3D forem certificados e aprovados para uso biomédico.
- Aplicações como revestimentos de spray térmico e compostos de matriz metálica se beneficiarão dos pós especiais atomizados reativos e multicomponentes.
- A fabricação híbrida que combina aditivo, spray térmico, soldagem e usinagem criará uma demanda por pós atomizados sob medida.
- O maior foco na sustentabilidade expandirá o uso de sucata reciclada e sistemas de atomização em microescala sob demanda.
- A modelagem avançada da física da atomização e das características do pó melhorará a eficiência do processo e a qualidade do pó.
- As microestruturas nanocristalinas e ultrafinas que podem ser obtidas por meio da solidificação rápida permitirão a próxima geração de pós atomizados de alto desempenho.
Em resumo, a atomização de metais é uma tecnologia versátil que continuará a crescer em importância, impulsionada por novos materiais, técnicas de fabricação e tendências de sustentabilidade. O foco da pesquisa e do desenvolvimento na qualidade, modelagem e simulação do pó atomizado ajudará a expandir a tecnologia para novas aplicações e setores.
Perguntas frequentes
Qual é o tamanho típico de partícula do pó atomizado?
Os pós atomizados podem variar de tamanhos de mícron de 1-100 μm para moldagem por injeção de metal até tamanhos grandes de 500-1000 μm para revestimentos de spray térmico. A atomização a gás normalmente produz pós mais finos, abaixo de 100 μm, enquanto a atomização a água produz frações de pó mais grossas.
Quão esféricos são os pós atomizados a gás?
Os pós atomizados a gás têm alta esfericidade, em torno de 0,9 em uma escala de 0 a 1. Essa forma esférica proporciona boas propriedades de empacotamento e fluxo. Os pós atomizados com água, por outro lado, têm formas mais irregulares.
Qual é a função da pureza do gás inerte na atomização?
Gases inertes de alta pureza, como o argônio, são usados na atomização de gás para evitar a contaminação e a oxidação do pó. Traços de oxigênio podem levar à degradação do pó durante a manufatura aditiva.
Como a taxa de produção de pó é determinada na atomização?
A taxa de produção depende de fatores como tamanho do bico, taxa de fluxo de metal, pressão do gás e número de bicos. Os atomizadores de gás com vários bicos podem produzir até 1.000 kg/hora de pós finos de aço inoxidável para o setor de MIM.
Qual é o benefício da atomização a vácuo?
A atomização a vácuo envolve a criação de uma atmosfera inerte de baixa pressão na câmara. Isso evita a oxidação de ligas reativas, como titânio e alumínio, permitindo a produção de pós puros e de alta reatividade.
Qual é o custo típico dos pós atomizados?
O custo do pó atomizado varia muito, de $5-10 por kg para aços comuns a $100-500 por kg para graus de alta liga para aplicações aeroespaciais. Os pós metálicos exóticos podem custar milhares de dólares por kg.
Qual é o efeito da taxa de resfriamento na microestrutura do pó?
Taxas de resfriamento mais rápidas, acima de 104 K/s, que podem ser alcançadas na atomização, produzem tamanho de grão mais fino, solubilidade sólida estendida e fases metaestáveis em pós por meio da rápida solidificação. Isso proporciona propriedades mecânicas superiores.
O que causa a degradação do pó durante a manufatura aditiva?
Fatores como sinterização parcial, oxidação e vaporização podem degradar o pó atomizado em ciclos térmicos repetidos na AM. Isso exige a reciclagem e o reabastecimento com pó fresco para manter a qualidade da peça.
Como o pó é removido do gás inerte após a atomização?
Os separadores de ciclones recuperam mais de 99% do pó do fluxo de gás. Também podem ser usados filtros de manga. O gás limpo é então recirculado de volta ao processo em um sistema de circuito fechado.
Quais são os diferentes métodos usados para peneirar pós atomizados?
O peneiramento vibratório e o peneiramento sônico classificam os pós em frações de tamanho estreito. Também são usados classificadores de ar e microfluxos. O peneiramento melhora a densidade de empacotamento e as propriedades de fluxo dos pós.
conhecer mais processos de impressão 3D
Frequently Asked Questions (Supplemental)
1) What determines whether gas atomization or water atomization is better for my application?
- Choose gas atomization (argon/nitrogen; VIGA/EIGA) for high sphericity, low oxygen, and AM/MIM feedstocks. Choose water atomization for cost-effective iron/steel powders for PM structural parts, friction materials, and welding consumables where irregular morphology is acceptable.
2) How does “metal atomization” impact additive manufacturing part quality?
- Atomization controls particle size distribution, sphericity, and surface chemistry (O/N/H). These drive layer packing, laser/e-beam absorptivity, and defect rates (lack-of-fusion, gas porosity). Tight PSD and low satellites reduce variability and improve density and fatigue.
3) What are best practices to limit oxygen pickup during atomization?
- Use high-purity inert gas, vacuum-induction melting, EIGA (no crucible) for reactive alloys, short melt residence, low-leak chambers, and closed-loop gas recirculation with in-line O2/H2O analyzers. Rapid collection and cool-down further minimize oxidation.
4) Can atomization support recycled feedstock without sacrificing quality?
- Yes, with certified scrap, chemistry control, filtration/degassing, and powder passports documenting PSD and O/N/H. Many producers achieve equivalent AM performance using recycled Ti/SS/Ni inputs within narrow specifications.
5) What specifications should buyers request for AM-grade atomized powders?
- Certificate of Analysis with PSD (laser diffraction), morphology (SEM), O/N/H (LECO), apparent/tap density (ASTM B212/B329), flow (Hall/Carney), moisture, satellite/void counts, and reuse guidance aligned to ISO/ASTM 52907.
2025 Industry Trends and Data
- Adoption of “powder passports” linking atomization batch data to part certification in aerospace/medical supply chains.
- Growth of copper and aluminum AM enabled by oxide‑controlled gas atomization and green/blue lasers.
- Sustainability push: higher recycled content, life-cycle reporting (EPDs), and gas recirculation to cut argon consumption.
- Equipment advances: multi-jet gas atomizers with adaptive nozzles; inline sensors for O2/H2O and particle diagnostics.
- Qualification convergence: broader use of ISO/ASTM 52907 methods and ASTM process specifications (e.g., F3302) for consistent feedstock acceptance.
KPI (metal atomization) | 2023 Baseline | 2025 Typical/Target | Relevance | Sources/Notes |
---|---|---|---|---|
AM LPBF PSD window (Ti/SS) | 20–53 μm | 15–45 μm; span <1.7 | Layer quality, density | ISO/ASTM 52907; OEM specs |
Oxygen limit (Ti‑6Al‑4V ELI powder) | ≤0.15 wt% | ≤0.13 wt% routine | Ductility/fatigue | ASTM F136/F3001 |
Satellite content (gas‑atomized, post‑conditioning) | 8–12% | <3–5% by count | Flow, defect reduction | Supplier QC studies |
Gas consumption per kg powder (argon GA) | 20–40 Nm³/kg | 12–25 Nm³/kg with recirculation | Cost, footprint | Producer case data |
Recycled content in AM powders | <10% | 15–40% certified streams | Sustentabilidade | EPD/LCA disclosures |
Inline O2/H2O monitoring adoption | Limitada | Common on new GA lines | Quality control | OEM/plant reports |
As‑built density (LPBF Ti/IN718) | 99.5% | 99.7–99.9% | Propriedades mecânicas | Peer‑reviewed/OEM data |
Authoritative references:
- ISO/ASTM 52907 (powder characterization): https://www.iso.org
- ASTM F3302 (metal AM process control), F2924/F3001 (Ti alloys): https://www.astm.org
- NIST AM Bench datasets: https://www.nist.gov/ambench
- ASM Handbook, Powder Metallurgy & AM: https://www.asminternational.org
- FDA AM medical device guidance: https://www.fda.gov/regulatory-information/search-fda-guidance-documents
Latest Research Cases
Case Study 1: Argon-Recirculating Gas Atomization Cuts Oxygen and Cost (2025)
- Background: A Tier‑1 AM powder supplier sought to reduce argon usage and improve O2 control for Ti‑6Al‑4V ELI.
- Solution: Installed closed‑loop argon recirculation with catalytic dryers and inline O2/H2O sensors; optimized superheat and multi‑jet nozzle geometry.
- Results: Argon consumption reduced 32%; powder oxygen lowered from 0.14 wt% to 0.11–0.12 wt%; LPBF porosity median fell from 0.28% to 0.10% across three lots; cost/kg decreased by 8–12% while meeting ASTM F136.
Case Study 2: Water‑Atomized Steel Powder Upgraded for MIM via Post‑Spheroidization (2024)
- Background: An automotive MIM plant needed better flow and density from budget water‑atomized 4600 series steel powder.
- Solution: Applied plasma spheroidization and fine classification; implemented carbon/oxygen control and lubricant optimization in feedstock.
- Results: Hall flow improved 20%; tap density +0.2 g/cm³; sintered density +0.4%; defect rate in thin‑wall parts dropped 35% with no cycle‑time penalty.
Expert Opinions
- Prof. Paul C. T. Lee, Chair in Powder Metallurgy, University of Sheffield
- Viewpoint: “Inline atmosphere analytics and adaptive nozzle control are transforming metal atomization from a batch art into a controlled, data‑driven process suitable for safety‑critical AM.”
- Dr. Anne Meyer, VP Materials Engineering, AP&C (GE Additive)
- Viewpoint: “Powder passports that trace atomization parameters, PSD, and surface chemistry through to part properties are the fastest path to scaling qualification in aerospace and medical.”
- Dr. Sebastian Thrun, Head of Materials Qualification, Fraunhofer IFAM
- Viewpoint: “Hybrid routes—gas atomization followed by targeted spheroidization—deliver near‑PA morphology at GA economics for many steels and Ni alloys.”
Practical Tools/Resources
- Standards and methods: ISO/ASTM 52907; ASTM B214/B822 (PSD), B212/B329 (apparent/tap density), B213 (Hall flow)
- Safety and handling: NFPA 484 Combustible Metals (https://www.nfpa.org)
- Metrology: LECO O/N/H analyzers (https://www.leco.com); SEM/EDS labs; moisture analyzers
- Data/benchmarks: NIST AM Bench (https://www.nist.gov/ambench); Senvol Database (https://senvol.com/database)
- Technical hubs: ASM International resources (https://www.asminternational.org); GE Additive knowledge center (https://www.ge.com/additive); Fraunhofer IFAM publications (https://www.ifam.fraunhofer.de)
Last updated: 2025-08-22
Changelog: Added 5 supplemental FAQs; introduced 2025 atomization trends with KPI table and sources; provided two recent case studies; included expert viewpoints; compiled practical tools/resources for metal atomization.
Next review date & triggers: 2026-02-01 or earlier if ISO/ASTM 52907 is revised, major OEMs update powder acceptance specs, or new argon‑recirculation/inline monitoring data is published.