Visão geral da deposição de metal a laser (LMD)
Deposição de metal a laser (LMD) é uma tecnologia inovadora de manufatura aditiva (AM) que usa um laser de alta potência para derreter e fundir pó ou fio metálico em um substrato, camada por camada, para criar estruturas tridimensionais. Seja no setor aeroespacial, automotivo ou médico, a LMD oferece uma solução robusta para peças metálicas complexas que exigem precisão, durabilidade e eficiência.
Imagine a necessidade de reparar uma lâmina de turbina desgastada ou criar um implante personalizado. Os métodos tradicionais de fabricação podem ser muito lentos, muito caros ou simplesmente não serem suficientemente precisos. A LMD entra em cena como um super-herói, usando lasers para soldar pós metálicos na forma perfeita, camada por camada meticulosa. O resultado? Componentes altamente precisos e resistentes que podem até superar os originais.
Mas como ele funciona? Quais são os materiais utilizados? E, o mais importante, como isso pode beneficiar sua empresa? Neste guia detalhado, vamos nos aprofundar nas vantagens e desvantagens da LMD, desde os pós metálicos específicos que ela usa até seus prós e contras, e até mesmo uma seção útil de perguntas frequentes para esclarecer qualquer dúvida.
Portanto, prepare-se para explorar o fascinante mundo do Laser Metal Deposition!
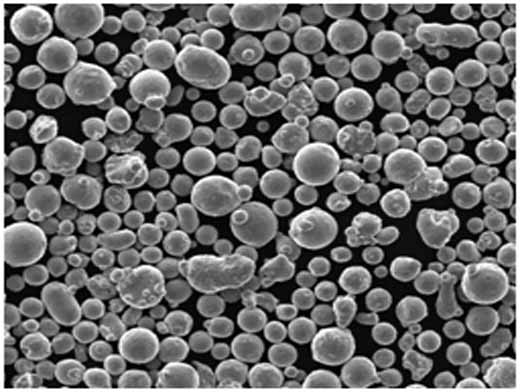
O que é Laser Metal Deposition (LMD)?
A LMD é um tipo de manufatura aditiva, também conhecida como impressão 3D, em que os materiais são adicionados em vez de removidos. O processo envolve o uso de um feixe de laser focalizado para derreter pó ou fio de metal, que é então depositado em um substrato. Essa tecnologia permite o controle preciso do material, possibilitando a criação de geometrias complexas e componentes metálicos de alto desempenho.
Como funciona a deposição de metal a laser?
A deposição de metal a laser funciona com o fornecimento de pó metálico por meio de um bocal em um feixe de laser, que derrete o pó e o funde a um material de base (substrato). À medida que o laser se move, ele constrói camadas de metal para formar o formato desejado. É como construir uma parede, mas em vez de tijolos, você está usando minúsculos grãos de metal e, em vez de argamassa, um laser de alta energia une tudo.
- Fonte de laser: O tipo e a potência do laser determinam como o pó metálico será derretido e solidificado. Os lasers de fibra são comumente usados por sua eficiência e precisão.
- Sistema de alimentação de pó: Os pós metálicos são alimentados no feixe de laser por meio de um bocal. A consistência do fluxo de pó é fundamental para a obtenção de camadas uniformes.
- Controle de movimento: O movimento do laser e do sistema de alimentação de pó é controlado com precisão, geralmente com sistemas CNC ou robóticos, para criar a geometria desejada.
Essa precisão significa que a LMD não se limita à construção de novas peças. Ela também pode reparar as existentes adicionando material onde for necessário, o que é particularmente útil para componentes caros em setores como o aeroespacial.
Aplicativos de Deposição de metal a laser (LMD)
O Laser Metal Deposition é um processo versátil com uma ampla gama de aplicações em vários setores. Desde o reparo de componentes de alto valor até a criação de peças complexas e personalizadas, a LMD está causando impacto na fabricação.
Principais aplicativos:
Setor | Aplicativo | Benefícios |
---|---|---|
Aeroespacial | Reparo da lâmina da turbina, componentes do motor | Redução do tempo de inatividade e aumento da vida útil das peças |
Automotivo | Reparos de engrenagens e virabrequins, peças personalizadas | Desempenho aprimorado, produção econômica |
Médico | Implantes personalizados, componentes odontológicos | Alta precisão, biocompatibilidade |
Ferramentas | Reparo de moldes, restauração de matrizes | Vida útil mais longa da ferramenta, tempo de produção reduzido |
Petróleo e gás | Assentos de válvulas, componentes de perfuração | Resistência a ambientes agressivos, custo de substituição reduzido |
Geração de energia | Reparos de turbinas, fabricação de componentes | Melhoria da eficiência e redução dos custos de manutenção |
Defesa | Componentes de armamento, reparo de equipamentos críticos | Alta resistência, durabilidade em condições extremas |
Energia | Componentes de turbinas eólicas, peças de reatores nucleares | Sustentabilidade e alto desempenho em operações críticas |
Construção | Componentes estruturais personalizados, reparos de máquinas pesadas | Força, flexibilidade, custo-benefício |
Marinha | Reparos de hélices, componentes de motores de navios | Resistência à corrosão, longevidade em ambientes marinhos |
Cada um desses setores tem requisitos exclusivos, e a flexibilidade da LMD permite que ela atenda a todos eles com facilidade. Quer se trate de materiais de alta resistência necessários para o setor aeroespacial ou de metais biocompatíveis usados em implantes médicos, a LMD pode atendê-los.
Pós metálicos específicos usados em LMD
A escolha do pó metálico é crucial na LMD, pois afeta diretamente a qualidade, a durabilidade e a funcionalidade do produto final. Aqui, exploramos alguns dos pós metálicos específicos comumente usados em LMD, juntamente com suas composições e características.
Os 10 principais pós metálicos para LMD:
Pó metálico | Composição | Propriedades | Características |
---|---|---|---|
Inconel 625 | Liga de níquel-cromo-molibdênio-nióbio | Alta resistência, excelente resistência à corrosão | Usado nos setores aeroespacial, marítimo e químico |
Titânio Ti-6Al-4V | Liga de titânio-alumínio-vanádio | Alta relação resistência/peso, biocompatibilidade | Ideal para implantes médicos, aeroespaciais |
Aço inoxidável 316L | Liga de ferro-cromo-níquel-molibdênio | Resistência à corrosão, boas propriedades mecânicas | Comum nos setores médico e de processamento de alimentos |
Cobalto-cromo (Co-Cr) | Liga de cobalto-cromo | Resistência ao desgaste, biocompatibilidade | Usado em implantes dentários e ortopédicos |
Alumínio AlSi10Mg | Liga de alumínio-silício-magnésio | Leve, com boas propriedades térmicas | Popular em aplicações automotivas e aeroespaciais |
Hastelloy X | Liga de níquel-cromo-ferro-molibdênio | Resistência ao calor, resistência à oxidação | Adequado para ambientes de alta temperatura |
Aço Maraging 18Ni300 | Liga de níquel-cobalto-molibdênio-titânio | Resistência ultra-alta, boa tenacidade | Usado em ferramentas, no setor aeroespacial |
Níquel 718 | Liga de níquel-cromo e ferro | Alta resistência à tração, resistência à fluência | Amplamente utilizado em motores de turbina, no setor aeroespacial |
Aço ferramenta H13 | Liga de cromo-molibdênio-vanádio | Alta dureza, resistência ao desgaste | Ideal para ferramentas, moldes de fundição sob pressão |
Cobre-CrZr | Liga de cobre, cromo e zircônio | Excelente condutividade térmica e resistência | Usado em trocadores de calor, componentes elétricos |
Esses pós metálicos são cuidadosamente escolhidos com base nos requisitos específicos da aplicação, incluindo fatores como força, resistência à corrosão e biocompatibilidade.
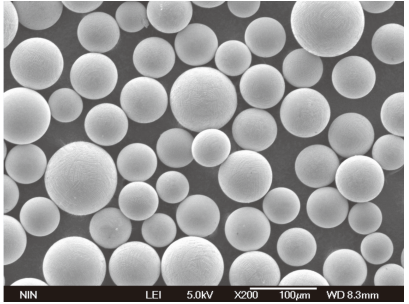
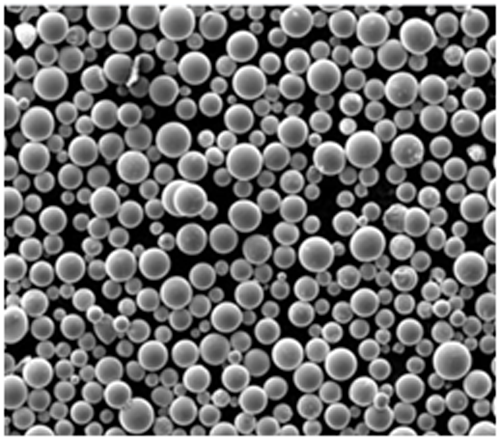
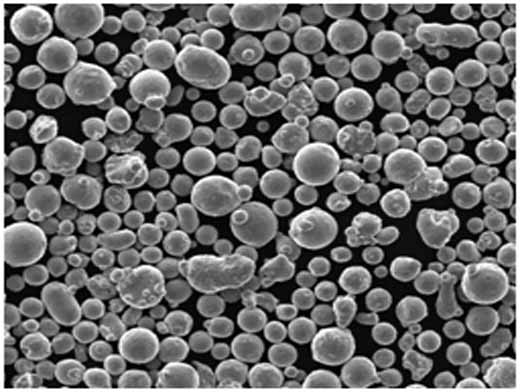
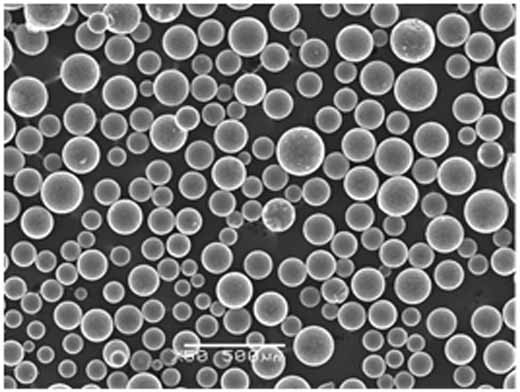
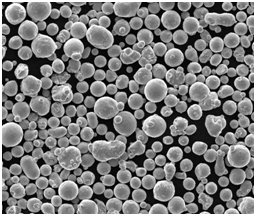
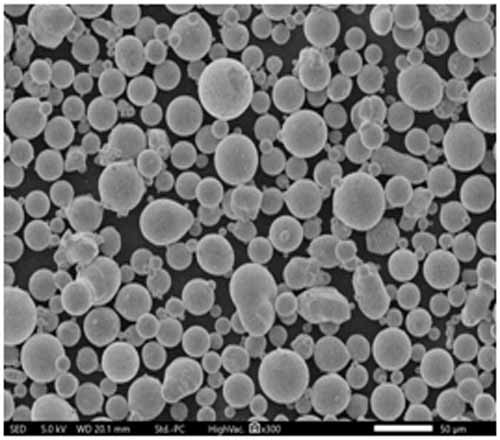
Propriedades e características de Deposição de metal a laser (LMD)
Compreender as propriedades e as características da LMD é essencial para avaliar plenamente seus recursos e possíveis limitações. Vamos detalhar esses aspectos para ter uma visão mais clara do que faz a LMD funcionar.
Propriedades do material:
Propriedade | Descrição |
---|---|
Densidade | Os componentes da LMD normalmente têm alta densidade, comparável à de peças forjadas. |
Microestrutura | É possível obter microestruturas finas, o que resulta em alta resistência e tenacidade. |
Acabamento da superfície | O acabamento da superfície pode variar de acordo com o pó e os parâmetros do processo, o que geralmente exige pós-processamento. |
Porosidade | É possível obter uma porosidade mínima com parâmetros otimizados, embora isso possa variar de acordo com o material e a aplicação. |
Tensões residuais | A LMD pode introduzir tensões residuais, que talvez precisem ser aliviadas por meio de tratamento térmico. |
Características do processo:
Característica | Detalhes |
---|---|
Espessura da camada | Normalmente, varia de 50 a 500 mícrons, dependendo da aplicação. |
Taxa de deposição | Varia de 0,5 a 3 kg/hora, influenciado pelo material e pela potência do laser. |
Precisão | Alta precisão com tolerâncias na faixa de ±0,1 mm ou melhor. |
Flexibilidade | Capaz de lidar com geometrias complexas e vários materiais em uma única construção. |
Escalabilidade | Adequado para componentes pequenos e grandes, desde protótipos até a produção. |
A combinação dessas propriedades e características torna a LMD uma ferramenta poderosa para a fabricação e o reparo de componentes metálicos de alto desempenho.
Vantagens e limitações da deposição de metal a laser (LMD)
Como qualquer processo de fabricação, a LMD tem seus pontos fortes e fracos. Aqui está um detalhamento das vantagens e limitações para ajudá-lo a determinar se a LMD é a opção certa para suas necessidades.
Vantagens:
Vantagens | Explicação |
---|---|
Precisão e exatidão | A LMD pode produzir componentes altamente detalhados com tolerâncias rígidas. |
Eficiência do material | É gerado um mínimo de resíduos, o que o torna uma opção econômica. |
Versatilidade | Capaz de processar uma ampla variedade de materiais, inclusive metais difíceis de usinar. |
Capacidades de reparo | A LMD é excelente no reparo de componentes de alto valor, prolongando sua vida útil e reduzindo o tempo de inatividade. |
Personalização | Facilmente personalizável para pequenas séries de produção ou peças sob medida. |
Limitações:
Limitação | Explicação |
---|---|
Custos iniciais elevados | Os custos de equipamento e instalação podem ser significativos, o que torna o investimento considerável. |
Acabamento da superfície | Geralmente requer pós-processamento para obter uma superfície lisa. |
Complexidade da operação | Requer operadores qualificados e controle preciso dos parâmetros. |
Zonas afetadas pelo calor | O laser pode introduzir zonas afetadas pelo calor que podem alterar as propriedades do material. |
Limitações materiais | Nem todos os materiais são adequados para LMD, especialmente aqueles com baixa absortividade do laser. |
A compreensão desses prós e contras o ajudará a tomar uma decisão informada ao considerar a LMD para suas necessidades de fabricação.
Parâmetros de processo que influenciam a deposição de metal a laser (LMD)
A qualidade dos componentes produzidos por meio da deposição de metal a laser é altamente dependente de vários parâmetros do processo. Esses parâmetros devem ser cuidadosamente controlados para garantir as propriedades mecânicas desejadas, o acabamento da superfície e o desempenho geral do produto final.
Parâmetros-chave do processo:
Parâmetro | Descrição | Influência no produto final |
---|---|---|
Potência do laser | A quantidade de energia fornecida pelo laser, normalmente medida em watts. | Uma potência mais alta aumenta a taxa de deposição, mas pode causar superaquecimento. |
Velocidade de digitalização | A velocidade com que o laser se move pelo substrato. | Velocidades mais rápidas podem reduzir a entrada de calor, mas podem levar a uma fusão incompleta. |
Taxa de alimentação de pó | A taxa na qual o pó metálico é fornecido à poça de fusão. | Taxas mais altas aumentam a eficiência da deposição, mas podem levar à porosidade se não forem controladas. |
Fluxo de gás de proteção | A taxa de fluxo do gás inerte usado para proteger a poça de fusão da oxidação. | Uma blindagem adequada evita a oxidação e a contaminação. |
Tamanho do ponto de laser | O diâmetro do feixe de laser no substrato. | Um tamanho de ponto menor melhora a precisão, mas pode retardar o processo. |
Taxa de sobreposição | O grau de sobreposição entre passagens de laser adjacentes. | Uma sobreposição maior garante a uniformidade, mas pode aumentar o tempo de processamento. |
Pré-aquecimento do substrato | A temperatura do substrato antes do início da deposição. | O pré-aquecimento reduz as tensões residuais e as rachaduras. |
Cada um desses parâmetros desempenha um papel fundamental na determinação da qualidade e da consistência do processo de LMD. Por exemplo, a potência inadequada do laser ou a velocidade de varredura podem resultar em defeitos como porosidade, rachaduras ou má adesão entre as camadas.
Otimização dos parâmetros da LMD para obter os melhores resultados
Para obter os melhores resultados com a LMD, é fundamental otimizar esses parâmetros para cada aplicação e material específicos. Isso geralmente envolve uma combinação de experimentação e simulação para encontrar o ponto ideal onde o processo é eficiente e produz peças de alta qualidade.
Por exemplo, ao trabalhar com uma liga de alta resistência, como o Inconel 625, o controle da potência do laser e da velocidade de varredura é essencial para evitar o superaquecimento, que pode levar a alterações microestruturais indesejáveis. Por outro lado, ao usar um material mais tolerante, como o aço inoxidável 316L, o foco pode estar mais na otimização da taxa de alimentação de pó e no fluxo de gás de proteção para maximizar a eficiência da deposição.
Materiais avançados usados na deposição de metal a laser
Além dos pós metálicos comuns listados anteriormente, a LMD também pode trabalhar com materiais mais especializados. Esses materiais avançados são usados em aplicações em que os metais padrão podem não atender aos critérios de desempenho necessários, como temperaturas extremas, ambientes corrosivos ou requisitos mecânicos específicos.
Pós metálicos avançados adicionais para LMD:
Pó metálico | Composição | Propriedades | Características |
---|---|---|---|
Liga de níquel 263 | Liga de níquel-cromo-calcário-molibdênio | Resistência a altas temperaturas, resistência à oxidação | Ideal para lâminas de turbina, revestimentos de combustão |
Haynes 282 | Liga de níquel-ferro-cromo-molibdênio-titânio | Alta resistência à fluência, excelente soldabilidade | Usado no setor aeroespacial, geração de energia |
Tântalo (Ta) | Tântalo puro | Excelente resistência à corrosão, biocompatibilidade | Adequado para processamento químico, dispositivos médicos |
Nióbio (Nb) | Nióbio puro | Alto ponto de fusão, boas propriedades supercondutoras | Usado em supercondutores, componentes aeroespaciais |
Tungstênio (W) | Tungstênio puro | Ponto de fusão extremamente alto, alta densidade | Ideal para aplicações de alta temperatura |
Inconel 738 | Liga de níquel-cromo-calcário-alumínio | Excepcional resistência à oxidação, alta resistência | Usado em componentes de turbinas a gás de seção quente |
Rene 41 | Liga de níquel-cromo-calcário-alumínio | Resistência superior a altas temperaturas e resistência à oxidação | Comum no setor aeroespacial, turbinas a gás |
Ti-5553 | Liga de titânio-alumínio-molibdênio-vanádio-cromo | Alta resistência, tenacidade e boa resistência à corrosão | Usado em aplicações aeroespaciais e militares |
Liga de cobalto Stellite 6 | Liga de cobalto-cromo-tungstênio-carbono | Excelente resistência ao desgaste, boa resistência à corrosão | Ideal para assentos de válvulas, ferramentas de corte |
Ni-Cr-B-Si (Colmonoy 88) | Liga de níquel-cromo-boro-silício | Dureza, resistência ao desgaste, boa resistência à corrosão | Usado em revestimento de superfícies, aplicações de reparo |
Esses materiais avançados são escolhidos por suas propriedades exclusivas que os tornam adequados para aplicações altamente exigentes. Por exemplo, a excelente resistência à corrosão do tântalo o torna ideal para equipamentos de processamento químico, enquanto o ponto de fusão extremo do tungstênio o torna a melhor opção para componentes expostos a temperaturas muito altas.
Comparação de materiais avançados
A comparação desses materiais avançados revela como ligas específicas podem superar outras em determinadas condições, tornando-as mais adequadas para aplicações específicas.
Material | Força | Resistência à temperatura | Resistência à corrosão | Resistência ao desgaste | Adequação do aplicativo |
---|---|---|---|---|---|
Liga de níquel 263 | Alta | Excelente | Moderado | Bom | Turbinas, componentes de alta temperatura |
Tântalo | Moderado | Alta | Excelente | Moderado | Processamento químico, dispositivos médicos |
Tungstênio | Extremamente alta | Excepcional | Moderado | Excelente | Aplicações de alta temperatura, aeroespacial |
Liga de cobalto Stellite 6 | Moderado | Bom | Bom | Excelente | Ferramentas de corte, assentos de válvulas |
Inconel 738 | Muito alta | Excelente | Bom | Moderado | Componentes de turbina a gás, aeroespacial |
Essas comparações podem ajudar os fabricantes a escolher o material certo com base em suas necessidades específicas, equilibrando fatores como força, resistência à temperatura e custo.
Aplicações de materiais avançados em LMD
O uso de materiais avançados em LMD estende sua aplicabilidade a campos altamente especializados em que os métodos de fabricação ou materiais tradicionais falhariam. Esses materiais podem atender a requisitos rigorosos, oferecendo melhor desempenho, longevidade e confiabilidade em aplicações críticas.
Aplicativos especializados:
Setor | Aplicativo | Material utilizado | Vantagens |
---|---|---|---|
Aeroespacial | Revestimentos da câmara de combustão, lâminas de turbina | Liga de níquel 263, Haynes 282 | Resistência a altas temperaturas, excelentes propriedades mecânicas |
Médico | Implantes personalizados, ferramentas cirúrgicas | Tântalo, Cobalto-Cromo (Co-Cr) | Biocompatibilidade, resistência à corrosão |
Energia | Componentes de reatores nucleares, eixos de turbinas eólicas | Tungstênio, Rene 41 | Resistência à radiação, força sob tensão |
Defesa | Veículos blindados, hardware de nível militar | Ti-5553, tungstênio | Alta resistência, tenacidade e redução de peso |
Automotivo | Componentes de motores de alto desempenho, trocadores de calor | Inconel 738, titânio Ti-6Al-4V | Resistência ao calor, força, peso reduzido |
Petróleo e gás | Ferramentas de fundo de poço, assentos de válvulas | Liga de cobalto Stellite 6, Ni-Cr-B-Si | Resistência ao desgaste, durabilidade em ambientes adversos |
Eletrônicos | Componentes semicondutores, dissipadores de calor | Nióbio, tungstênio | Condutividade térmica, capacidade para altas temperaturas |
Cada aplicação se beneficia das propriedades específicas dos materiais avançados utilizados. Por exemplo, no setor aeroespacial, a resistência a altas temperaturas da liga de níquel 263 garante que as lâminas da turbina mantenham sua integridade mesmo em condições operacionais extremas.
Padrões e especificações para materiais de LMD
Ao selecionar materiais para Deposição de metal a laserPara garantir a qualidade, o desempenho e a segurança, é essencial a adesão aos padrões e às especificações do setor. Diferentes setores têm requisitos específicos que os materiais devem atender, e esses padrões orientam o processo de seleção.
Padrões do setor para materiais de LMD:
Material | Padrão/Especificação | Setor | Principais requisitos |
---|---|---|---|
Inconel 625 | ASTM B443, AMS 5599 | Aeroespacial, petróleo e gás | Alta temperatura, resistência à corrosão, propriedades mecânicas |
Titânio Ti-6Al-4V | ASTM F136, AMS 4911 | Médico, aeroespacial | Biocompatibilidade, força mecânica, resistência à fadiga |
Aço inoxidável 316L | ASTM A240, ISO 5832-1 | Médico, processamento de alimentos | Resistência à corrosão, propriedades mecânicas |
Cobalto-cromo (Co-Cr) | ASTM F75, ISO 5832-4 | Médico | Resistência ao desgaste, biocompatibilidade |
Tungstênio (W) | ASTM B777, MIL-T-21014 | Defesa, Aeroespacial | Alta densidade, resistência a altas temperaturas |
Alumínio AlSi10Mg | ASTM B209, EN 485 | Automotivo, aeroespacial | Leve, com boa condutividade térmica |
Liga de níquel 263 | AMS 5872, ASTM B637 | Aeroespacial | Resistência à oxidação, alta resistência a temperaturas elevadas |
Rene 41 | AMS 5545, ASTM B435 | Aeroespacial | Propriedades mecânicas em alta temperatura |
Nióbio (Nb) | ASTM B392, AMS 7850 | Eletrônica, aeroespacial | Supercondutividade, estabilidade térmica |
Tântalo (Ta) | ASTM B708, AMS 7831 | Médico, processamento químico | Resistência à corrosão, biocompatibilidade |
Essas normas garantem que os materiais usados em LMD sejam de qualidade consistente e atendam aos critérios de desempenho necessários para suas aplicações pretendidas. Por exemplo, a ASTM F136 garante que o titânio Ti-6Al-4V usado em implantes médicos é seguro e eficaz para uso a longo prazo no corpo humano.
Escolhendo o pó metálico certo para a deposição de metal a laser
A seleção do pó metálico correto é uma etapa essencial do processo de LMD. A escolha do pó afeta diretamente a qualidade, o desempenho e o custo do produto final. Fatores como propriedades do material, requisitos de aplicação e considerações de custo desempenham um papel importante nesse processo de tomada de decisão.
Fatores a serem considerados:
Fator | Descrição | Impacto na seleção |
---|---|---|
Requisitos do aplicativo | As necessidades específicas do produto final, incluindo propriedades mecânicas, condições ambientais e vida útil. | Determina a seleção de materiais com base em critérios de desempenho. |
Propriedades do material | Propriedades como ponto de fusão, condutividade térmica e resistência. | Determina os parâmetros do processo e a qualidade da peça final. |
Morfologia do Pó | A forma e a distribuição de tamanho das partículas de pó. | Afeta a fluidez, a densidade de empacotamento e a uniformidade da camada. |
Considerações sobre custos | O custo do pó metálico em relação ao orçamento do projeto. | Equilibra o desempenho do material com a viabilidade econômica. |
Disponibilidade do fornecedor | A disponibilidade do pó metálico de fornecedores confiáveis. | Garante o fornecimento e a qualidade consistentes para a produção. |
Conformidade com os padrões | Aderência aos padrões e especificações do setor. | Garante a qualidade e a segurança do produto final. |
Tomar uma decisão informada sobre o pó metálico requer um equilíbrio entre os requisitos técnicos e o custo. Por exemplo, embora o tungstênio ofereça resistência superior à temperatura, ele também é mais caro do que outras opções, como o aço inoxidável 316L, o que o torna mais adequado para aplicações de ponta em que o desempenho justifica o custo.
Fornecedores e preços para pós metálicos de LMD
Obter o pó metálico certo de um fornecedor confiável é fundamental para o sucesso da LMD. Os fornecedores oferecem uma ampla variedade de pós com preços variáveis, dependendo de fatores como composição do material, pureza e distribuição do tamanho das partículas.
Principais fornecedores e preços:
Fornecedor | Pó metálico | Faixa de preço (por kg) | Recursos especiais |
---|---|---|---|
Tecnologia Carpenter | Liga de níquel 263, Haynes 282 | $300 – $500 | Pós de grau aeroespacial de alta qualidade, tamanho de partícula consistente. |
Höganäs AB | Aço inoxidável 316L, Inconel 625 | $50 – $200 | Ampla variedade de ligas, excelente fluidez. |
Tecnologia LPW | Titânio Ti-6Al-4V, alumínio AlSi10Mg | $250 – $450 | Pós personalizados, controle de qualidade rigoroso para manufatura aditiva. |
Oerlikon Metco | Liga de cobalto Stellite 6, Rene 41 | $400 – $600 | Pós de alto desempenho, otimizados para resistência ao desgaste. |
AP&C (GE Additive) | Ti-5553, Tântalo | $500 – $800 | Pós de grau aeroespacial e médico, biocompatibilidade. |
Sandvik | Inconel 738, tungstênio | $200 – $700 | Ligas de alta temperatura, testes e certificações abrangentes. |
Tecnologia de pós Praxis | Nióbio, Cobalto-Cromo (Co-Cr) | $300 – $600 | Pós especializados para aplicações médicas e eletrônicas. |
Aditivo GKN | Liga de níquel 263, Haynes 282 | $300 – $500 | Misturas de pó personalizadas, excelente resistência à oxidação. |
Tekna | Alumínio AlSi10Mg, aço inoxidável 316L | $50 – $150 | Pós esféricos, otimizados para manufatura aditiva. |
VIGA | Tântalo, tungstênio | $500 – $900 | Pós de alta pureza, adaptados para aplicações específicas. |
Os preços variam muito de acordo com o material e o fornecedor, refletindo as diferenças de pureza, o método de produção e a demanda do mercado. Por exemplo, os pós de tântalo e tungstênio estão na extremidade mais alta do espectro de preços devido ao seu processamento complexo e à alta demanda em setores especializados.
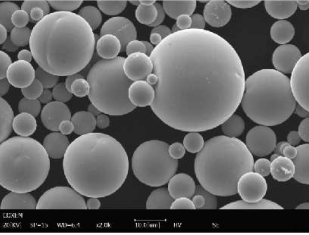
Comparação Deposição de metal a laser a outras técnicas de manufatura aditiva
O Laser Metal Deposition é apenas uma das muitas técnicas de manufatura aditiva disponíveis atualmente. Entender como o LMD se compara a outros métodos pode ajudá-lo a escolher o melhor processo para suas necessidades específicas.
Comparação com outras técnicas de manufatura aditiva:
Técnica | : Com menores requisitos de energia e a capacidade de reutilizar o pó não ligado, o Jato de Aglutinante é frequentemente mais econômico do que outros métodos de impressão 3D. | Acabamento da superfície | Velocidade | Precisão | Custo | Formulários |
---|---|---|---|---|---|---|
Deposição de metal a laser | Alta | Moderado | Médio | Alta | Alta | Aeroespacial, reparos, geometrias complexas |
Sinterização seletiva a laser (SLS) | Alta | Moderado | Médio | Alta | Moderado | Prototipagem, produção de pequenos lotes |
Fusão por feixe de elétrons (EBM) | Médio | Moderado | Médio | Alta | Alta | Aeroespacial, implantes médicos |
Modelagem por deposição fundida (FDM) | Baixa | Baixa | Alta | Baixa | Baixa | Prototipagem, produtos de consumo |
Sinterização direta a laser de metal (DMLS) | Alta | Alta | Médio | Muito alta | Alta | Peças médicas, aeroespaciais e complexas |
Jateamento de ligantes | Médio | Baixa | Alta | Médio | Moderado | Peças grandes, moldes de fundição |
Deposição de energia direcionada (DED) | Alta | Moderado | Médio | Alta | Alta | Reparo, componentes grandes, aeroespacial |
A LMD se destaca por sua capacidade de trabalhar com uma ampla variedade de materiais e por sua precisão na criação de geometrias complexas. No entanto, ela tende a ser mais cara e mais lenta em comparação com outras técnicas, como a FDM, que é mais adequada para a prototipagem rápida com requisitos de materiais menos exigentes.