Vue d'ensemble fabrication additive mim
Le moulage par injection de métal (MIM) est un processus de fabrication additive qui combine le moulage par injection de plastique et la métallurgie des poudres. Le MIM permet de produire en série des pièces métalliques complexes de forme nette avec une précision et une répétabilité élevées.
Le MIM présente des avantages décisifs par rapport aux autres procédés d'impression 3D de métaux :
- Production en grande quantité – ; Chaque lot peut produire jusqu'à des milliers de pièces. Le MIM est donc adapté aux applications de production finales.
- Faible coût par pièce – ; La méthode de moulage permet de réaliser des économies d'échelle. Le coût des pièces diminue considérablement avec l'augmentation des volumes.
- Large gamme de métaux – ; l'acier inoxydable, l'acier à outils, les alliages de titane et d'autres métaux peuvent être utilisés.
- Excellentes propriétés mécaniques – ; La densité est presque complète et la composition uniforme.
- Géométries complexes – ; Des formes complexes, des caractéristiques intérieures et des parois minces sont possibles.
- Plusieurs options de post-traitement – ; l'usinage, la gravure, le placage et d'autres finitions peuvent être appliqués.
- Processus établi – ; le MIM est utilisé depuis les années 1970. Il existe des normes et des bases de données sur les matériaux.
Le MIM est idéal pour les petites pièces métalliques complexes qui doivent être fabriquées en grande quantité et à moindre coût. Il comble le fossé entre l'impression 3D de prototypes et la fabrication en grande série.
Aperçu du processus MIM
Le processus de moulage par injection de métal comporte quatre étapes principales :
- Préparation des matières premières – ; La poudre de métal est mélangée à un matériau liant pour créer une matière première homogène. Ce mélange est granulé pour être utilisé dans la machine à injecter.
- Moulage par injection – ; La matière première est fondue et injectée dans un outil de moulage pour former la forme "verte" souhaitée. Un équipement de moulage par injection standard est utilisé.
- Débouclage – ; Le matériau liant est extrait du composant moulé par des moyens chimiques, thermiques ou catalytiques. Il en résulte une pièce brune.
- Frittage – ; Les pièces débitées sont frittées pour fusionner la poudre de métal en une pièce dense destinée à l'utilisation finale. Les pièces se rétractent pendant le frittage.
Des opérations secondaires telles que l'usinage, l'assemblage, le placage et la gravure peuvent encore améliorer les composants. Le processus de base du MIM est illustré ci-dessous :
Tableau 1 : Aperçu du processus de fabrication additive MIM
Étape | Description |
---|---|
Préparation des matières premières | Mélange de poudre métallique et de liant dans une matière première granulée |
Moulage par injection | Moulage des matières premières pour leur donner la forme verte souhaitée |
Débouclage | Enlever le liant pour laisser une partie brune |
Frittage | Fusion de la poudre métallique dans la pièce finale à l'aide de la chaleur |
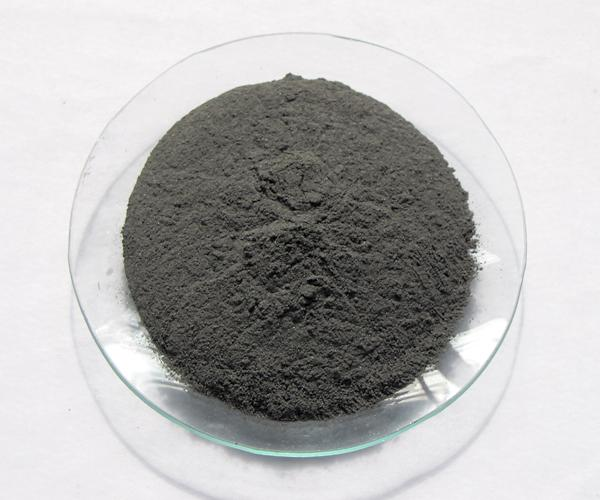
Applications des pièces MIM
Le MIM convient à la fabrication de petites pièces métalliques complexes de forme nette en volumes moyens à élevés. Les applications typiques du MIM sont les suivantes
Tableau 2 : Applications de la fabrication additive MIM
L'industrie | Exemples de composants |
---|---|
Automobile | Injecteurs de carburant, engrenages droits, pièces de turbocompresseurs |
Aérospatiale | Aubes de turbines, roues à aubes, initiateurs |
Médical | Brackets orthodontiques, poignées de bistouri, pinces |
Consommateur | Composants de montres, grilles, pièces décoratives |
Industrie | Lames de couteau, mécanismes de verrouillage, valves |
Armes à feu | Gâchettes, marteaux, sécurités, glissières |
Le MIM permet de consolider les pièces, de réduire le poids, d'améliorer les performances et de diminuer les coûts de fabrication dans de nombreuses industries. La combinaison de la liberté géométrique et de la productivité rend le MIM adapté à la production finale.
Par rapport à l'usinage CNC, la MIM permet de produire en série des formes plus complexes. La MIM permet de minimiser les étapes d'assemblage grâce à l'intégration des pièces.
Avantages de la fabrication additive MIM
Le MIM présente des avantages uniques qui en font un choix de fabrication populaire :
Tableau 3 : Avantages de la fabrication additive MIM
Bénéfice | Description |
---|---|
Production en grande quantité | Le MIM permet de produire jusqu'à des millions de pièces par an |
Faible coût par pièce | Réduction des coûts grâce à l'augmentation des volumes de production |
Flexibilité de la conception | Possibilité de géométries complexes et de microcaractéristiques |
Gamme de matériaux | La plupart des poudres d'alliage comme l'acier inoxydable, l'acier à outils et le titane peuvent être utilisées. |
Bonnes propriétés mécaniques | Densité presque totale et composition uniforme |
Variété de finitions | L'usinage, la gravure, le placage et d'autres finitions peuvent être appliqués. |
Processus établi | Normes, bases de données, années d'expérience disponibles |
La combinaison de la liberté de conception, des capacités des matériaux et de la rentabilité confère au MIM des avantages par rapport à d'autres procédés tels que l'impression 3D de métal, le moulage à la cire perdue ou l'usinage.
Les pièces peuvent être conçues avec des parois plus fines, des contre-dépouilles, des intérieurs creux et d'autres éléments complexes. Il est également possible de consolider plusieurs composants en une seule pièce MIM.
Limites de la fabrication additive MIM
Malgré ses nombreux avantages, la MIM présente certaines contraintes :
Tableau 4 : Limites de la fabrication additive MIM
Limitation | Description |
---|---|
Taille de la pièce | Généralement limité aux composants de petite taille (jusqu'à 70 pouces cubes) |
Matériaux à faible ductilité | Certains alliages ductiles comme l'aluminium ne sont pas facilement compatibles avec le MIM. |
Coûts initiaux | Investissement important dans l'outillage nécessaire pour les moules |
Production à faible mixité | Convient le mieux aux volumes moyens à élevés d'une même pièce |
Post-traitement | Un usinage ou une finition supplémentaire peut être nécessaire |
Le MIM a des limites géométriques puisqu'il implique un moulage. Les plastiques thermodurcissables permettent d'obtenir des pièces MIM plus grandes, mais leur résistance est moindre.
Tous les alliages métalliques ne peuvent pas être facilement formulés en matières premières pour le MIM. Les matériaux ductiles, en particulier, posent des problèmes.
Des moules en acier à outils dur doivent être fabriqués pour chaque nouvelle conception de pièce. Cela représente un surcroît de temps et d'argent.
Les modifications fréquentes de la conception sont moins adaptées au MIM en raison des outils de moulage fixes. D'autres méthodes d'impression 3D permettent une itération plus facile.
En fonction des exigences finales en matière de dimensions et de surface, des opérations de post-moulage peuvent être nécessaires.
Considérations relatives à la conception du MIM
Le MIM offre des libertés géométriques, mais les pièces doivent être conçues en tenant compte des limites du processus :
Tableau 5 : Considérations relatives à la conception du MIM
Paramètres | Lignes directrices |
---|---|
Epaisseur de la paroi | Minimum 0,3 mm, maximum 5 mm. Une épaisseur uniforme est idéale |
Tolérances | ±0,5% est typique mais dépend de la géométrie |
Finition de la surface | Le fritté asphalté est de l'ordre de Ra 10-15 microns. |
Angles d'ébauche | >Des angles de dépouille de 1° sont nécessaires pour faciliter le démoulage |
Complexité des formes | La consolidation des pièces ou l'optimisation de la topologie est possible |
Caractéristiques | Il est possible de réaliser des détails fins tels que des trous et des fentes de 0,1 mm. |
Textures | Possibilité d'incorporer des textures complexes dans le moule |
Inserts | Il est possible d'incorporer d'autres inserts dans le moule. |
Réduction du poids | Creusement, réduction de la masse grâce aux treillis et à l'optimisation de la topologie |
Le processus de moulage impose certaines règles de conception. Mais le MIM peut encore produire des géométries impossibles à réaliser avec d'autres méthodes.
Options de matériaux MIM
Une large gamme d'alliages, y compris des aciers très demandés et du titane, sont disponibles pour le MIM :
Tableau 6 : Options de matériaux MIM
Matériau | Applications |
---|---|
acier inoxydable | Médical, marine, produits de consommation |
Acier à outils | Outils de coupe, moules, pièces d'usure |
Acier faiblement allié | Automobile, composants de machines |
Alliages de titane | Aérospatiale, implants médicaux |
Alliages de nickel | Turbines aérospatiales, matériel maritime |
Alliages lourds de tungstène | Protection contre les rayonnements, amortissement des vibrations |
Les aciers inoxydables à haute résistance, résistants à la corrosion, tels que le 17-4PH et le 304L, sont couramment utilisés. Les qualités de durcissement par précipitation permettent d'améliorer encore la résistance.
Les aciers à outils comme le H13 sont idéaux pour le formage, l'emboutissage et les moules d'injection nécessitant une bonne dureté, une bonne ténacité et une bonne stabilité thermique.
Les alliages de titane pour la biocompatibilité, les alliages de nickel pour la résistance à la chaleur et les alliages de tungstène pour la densité sont facilement MIM.
De nouveaux matériaux tels que les alliages de cuivre et d'aluminium MIM sont également en cours de développement.
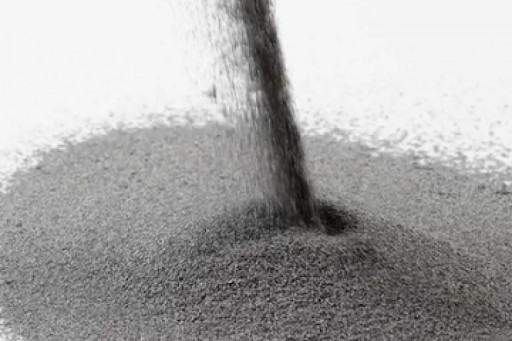
Options du logiciel de conception MIM
Il existe des logiciels de CAO et d'optimisation de la topologie pour répondre aux exigences de la conception MIM :
Tableau 7 : Options du logiciel de conception MIM
Logiciel | Description |
---|---|
SolidWorks | CAO populaire avec plugins d'analyse moldflow |
Autodesk Moldflow | Simulation dédiée aux moules d'injection |
nTopologie | Optimisation de la topologie et conception pour le logiciel AM |
Materialise 3-matic | Outil de conception de treillis et de structures légères |
Netfab | Logiciel d'optimisation des maillages 3D pour le MIM |
Solidworks est couramment utilisé pour la conception CAO. La simulation de l'écoulement du moule permet de vérifier la fabricabilité.
Des programmes spécialisés comme Moldflow ajoutent des capacités avancées d'analyse et de modélisation des processus.
Les logiciels d'optimisation de la topologie tels que nTopology permettent d'obtenir des formes organiques adaptées à l'AM et au MIM. L'allègement et la consolidation sont possibles.
Des logiciels tels que 3-matic permettent de concevoir des treillis à densité variable et de générer des structures de soutien.
Paramètres du processus MIM
Le MIM implique l'optimisation des matières premières, du moulage, du déliantage et du frittage. Les paramètres typiques sont les suivants
Tableau 8 : Paramètres du processus MIM
Étape | Gamme typique |
---|---|
Taille de la poudre | 5 – ; 25 microns |
Binder | 30 – ; 50% du volume des matières premières |
Chargement des solides | 55 – ; 70% dans les matières premières |
Température du moule | 150 – ; 185°C |
Pression d'injection | 60 – ; 110 MPa |
Taux de refroidissement du moulage | 20 – ; 50°C/s trempe |
Méthode de déliantage | Solvant, thermique, catalytique |
Temps de déliantage | Des jours aux heures |
Température de frittage | 50 – ; 80% du point de fusion |
Temps de frittage | Des heures aux jours |
Rétrécissement | 13 – ; 17% de rétrécissement linéaire |
Les paramètres dépendent du matériau, de la géométrie de la pièce, de la vitesse de production et des propriétés requises.
Les poudres fines et les charges solides élevées facilitent la résolution. Un refroidissement et des températures de moulage plus rapides améliorent la résistance à l'état vert. Des temps de déliantage plus courts et des températures de frittage plus élevées augmentent les taux de production.
Options de post-traitement du MIM
Les pièces frittées en MIM peuvent nécessiter un traitement supplémentaire :
Tableau 9 : Options de post-traitement de la MIM
Processus | Objectif |
---|---|
Traitement thermique | Modifier la microstructure pour améliorer les propriétés |
Placage | Appliquer des revêtements décoratifs tels que l'or ou le chrome |
Passivation | Création d'une couche d'oxyde protectrice sur les aciers |
Soudage | Assembler des pièces MIM entre elles ou avec d'autres composants |
Marquage au laser | Marques permanentes pour logos, textes ou codes d'identification |
Usinage et perçage | Dimensions de haute précision ou caractéristiques personnalisées |
Finition par vibration | Lisser la surface et arrondir les arêtes vives |
Les étapes de post-moulage permettent d'affiner l'aspect, les propriétés et les interfaces avec d'autres composants. Le placage, l'anodisation et la peinture sont des finitions courantes.
La connexion des pièces MIM par soudage, brasage ou collage peut être nécessaire pour certains assemblages. Un usinage supplémentaire peut permettre de créer des surfaces d'accouplement de précision.
Fournisseurs d'équipements MIM
Les entreprises de moulage par injection établies proposent des équipements et des services de MIM :
Tableau 10 : Fournisseurs d'équipements MIM
Entreprise | Equipement |
---|---|
ARBURG | Machines de moulage par injection électriques et hydrauliques |
Milacron | Lignes MIM intégrées complètes |
Toshiba | Machines de moulage hybrides et électriques |
Netstal | Moulage par injection de haute précision |
Nissei | Moulins à injection verticaux et horizontaux |
Sodick | Moulage à haute vitesse et à haute fréquence |
Des services spécialisés de MIM sont également disponibles auprès de :
- PIM International
- PPM
- MIMITAL
- CN Innovations
Ces fournisseurs de services complets proposent la formulation des matières premières, l'analyse, l'outillage, le moulage, le déliantage et le frittage.
Considérations sur les coûts de la fabrication additive MIM
Les coûts de démarrage du MIM sont relativement élevés, mais les coûts par pièce sont faibles pour les volumes de production :
Tableau 11 : Considérations sur les coûts de la MIM
Facteur de coût | Gamme typique |
---|---|
Outil de moulage | 10 000 $ – ; 100 000 $+ en fonction de la complexité, du matériel et de la taille |
Mise en place d'un petit lot | Moins de 10 000 |
Coût marginal des pièces | 0,5 – ; 5 $ coût du métal par pièce |
Taux de production | 5 000 – ; 500 000 pièces par an et par outil |
Finition | 0,1 – ; 2 $ par pièce en fonction du processus |
Taille du lot Seuil de rentabilité | 1 000 – ; 10 000+ pièces par rapport à d'autres processus |
Le fraisage d'un moule MIM à partir d'acier à outils peut prendre des semaines et coûter plus de 100 000 dollars pour des composants de grande taille. Les moules plus petits et moins complexes peuvent coûter moins de 10 000 dollars.
Une fois le moule fabriqué, les coûts du processus MIM sont très économiques pour des volumes de production moyens à élevés. Le MIM peut produire jusqu'à un million de pièces par an à partir d'un seul outil de moulage.
Choisir entre le MIM et d'autres procédés d'AM
Le MIM se situe entre l'impression 3D et les procédés à haut volume :
Tableau 12 : Comparaison entre le MIM et les autres procédés d'AM des métaux
Facteur | MIM | Impression 3D par jet de liant | DMLS | Moulage sous pression |
---|---|---|---|---|
Coût du capital | Élevé pour l'outillage | Moyen | Haut | Très élevé |
Coût par pièce | Plus bas au-dessus de 10 000 pièces | Faible à faible volume | Moyen | Plus faible à des volumes très élevés |
Matériaux | Large gamme d'alliages | Portée limitée | Portée limitée | Alliages d'aluminium et de zinc |
Résolution | Moyen ~0,1 – ; 0,3mm | Moyen ~0,3 – ; 0,5mm | Plus haut ~0,05mm | Inférieur ~0,5 mm |
Vitesse de production | Haut | Moyen | Slow | Très élevé |
Post-traitement | Moyen | Haut | Moyen | Faible |
Propriétés mécaniques | Bon | Variable | Meilleur | Bon |
Contraintes de conception | Quelques contraintes géométriques | Peu de contraintes | Quelques contraintes de surplomb | Niveau élevé de contraintes |
Le MIM offre les meilleures conditions économiques pour les géométries complexes dans les matériaux d'alliage nécessaires à des productions de plus de 10 000 pièces. Les procédés de production de masse moins coûteux deviennent favorables à des volumes beaucoup plus élevés.
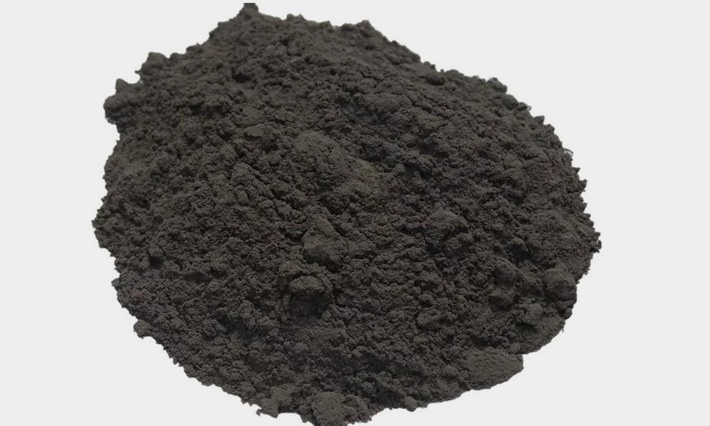
Conclusion
Le MIM est un procédé de fabrication additive métallique attrayant qui permet de produire en série des géométries complexes directement dans une gamme d'alliages techniques.
Elle associe la polyvalence de l'AM à une productivité proche de la fabrication conventionnelle. Cette fusion puissante permet de réduire le coût des pièces, de consolider les assemblages, d'améliorer les performances et d'alléger la construction.
Bien qu'il nécessite un investissement initial en moules, le MIM permet de réaliser de précieuses économies d'échelle. Il s'impose comme une technique complémentaire qui comble le fossé entre l'impression 3D de prototypes et la fabrication en grande série.
La poursuite du développement des matériaux et de l'intégration des logiciels permettra d'étendre les applications de la MIM aux secteurs médical, aérospatial, automobile, industriel et grand public.
Fabrication additive MIM – ; FAQ
Q : Quelle est la différence entre le MIM et le moulage sous pression ?
R : Le MIM permet de produire des géométries plus complexes et plus précises que le moulage sous pression, mais les taux et les volumes de production sont plus faibles. Le moulage sous pression est plus rapide et moins coûteux pour les formes plus simples produites en millions d'exemplaires.
Q : Quelles sont les dimensions des pièces que l'on peut fabriquer avec le MIM ?
R : Le poids des pièces MIM varie généralement entre 0,5 et 70 grammes. Des pièces plus grandes, jusqu'à 250 grammes, sont possibles avec des équipements capables de supporter des pressions et des tailles d'outillage plus élevées.
Q : Qu'est-ce qui détermine le coût d'un outil de moulage MIM ?
R : Le matériau du moule, sa complexité, sa taille, les finitions de surface et le délai d'exécution ont une incidence sur les coûts de fabrication du moule. Les moules simples en acier à outils peuvent coûter moins de 10 000 dollars, tandis que les moules de grande production en acier trempé peuvent dépasser 100 000 dollars.
Q : Le MIM nécessite-t-il un traitement ultérieur ?
R : Certaines applications nécessitent un traitement thermique supplémentaire, un usinage ou une finition de surface. Mais de nombreux composants peuvent être utilisés tels quels. Le post-traitement dépend des exigences finales en matière de dimensions et d'aspect.
Q : Combien de pièces un moule MIM peut-il produire ?
R : Les taux de production MIM sont généralement compris entre 5 000 et 500 000 pièces par an et par outil. Avec un entretien adéquat, il est possible de réaliser des millions de tirs au cours des années de vie de l'outil.
Q : Quelles sont les erreurs de conception les plus courantes à éviter en matière de MIM ?
R : Des angles de dépouille insuffisants, des contre-dépouilles importantes, des transitions entre parois épaisses et minces et le placement de détails fins sur les côtés opposés d'un noyau peuvent tous causer des problèmes de moulage. Il est recommandé de consulter des concepteurs expérimentés.
Q : Est-il possible de combiner plusieurs matériaux en MIM ?
R : Oui, le MIM permet d'obtenir des pièces multi-matériaux en utilisant des mélanges de poudres ou des matières premières multiples. Le moulage par insertion avec d'autres alliages ou matériaux durs est également possible pour les structures composites.
Q : Quel est l'état de surface des pièces MIM ?
R : Le fini tel que fritté a une rugosité d'environ 10 à 15 microns. Elle convient à de nombreuses applications. Un culbutage ou un polissage supplémentaire permet de lisser davantage les surfaces si nécessaire.
Q : Quelle est la durée du processus de MIM ?
R : Les délais de livraison sont généralement de 6 à 12 semaines. La fabrication des moules prend le plus de temps, le cas échéant. Une fois les outils fabriqués, la production par lots est assez rapide pour les petits composants.