L'alliage d'aluminium 7050 est un alliage à haute résistance couramment utilisé dans les applications aérospatiales. Sous forme de poudre, l'alliage d'aluminium 7050 offre des avantages uniques pour la fabrication additive et la métallurgie des poudres. Cet article fournit un aperçu approfondi des éléments suivants alliage d'aluminium 7050 en poudrey compris ses propriétés, ses applications et ses méthodes de traitement.
Introduction à l'alliage d'aluminium 7050
L'alliage d'aluminium 7050, également connu sous le nom d'AA7050, appartient à la série 7xxx des alliages d'aluminium. Il contient du zinc, du magnésium, du cuivre, du zirconium et d'autres éléments d'alliage qui lui confèrent une résistance supérieure à celle d'alliages plus conventionnels comme le 6061.
Les principaux éléments d'alliage de l'aluminium 7050 sont les suivants :
- Zinc : jusqu'à 6,2
- Magnésium : 2.0-2.6%
- Cuivre : 1,7-2,4
- Zirconium : 0,08-0,15 %.
De petites quantités de fer, de silicium, de manganèse et de titane peuvent également être présentes.
La combinaison de ces éléments d'alliage permet à l'aluminium 7050 d'atteindre une résistance à la traction de 530-570 MPa à l'état T6. Il présente également une excellente résistance à la fissuration par corrosion sous contrainte par rapport aux autres alliages 7xxx.
Les principales propriétés de l'aluminium 7050 sont les suivantes
- Rapport résistance/poids élevé
- Bonne résistance à la rupture
- Excellente résistance à la fatigue
- Bonne résistance à la corrosion
- Conductivité thermique élevée
- Bonne usinabilité
La résistance de l'aluminium 7050 est proche de celle de nombreux aciers, tout en conservant la légèreté de l'aluminium. Il s'agit donc d'un choix idéal pour les applications structurelles aérospatiales visant à réduire le poids.
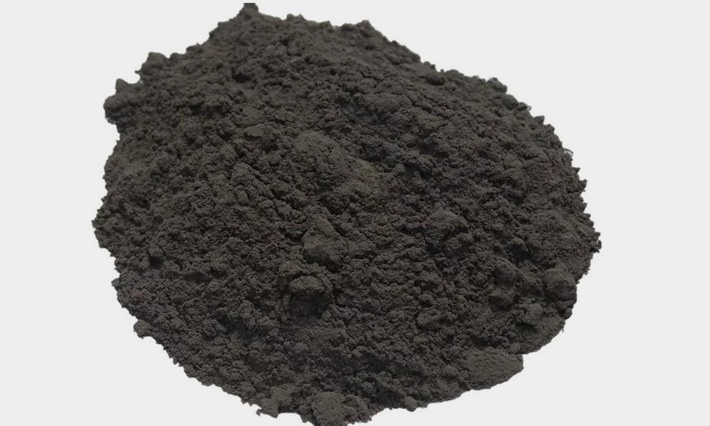
Applications de l'alliage d'aluminium 7050
Les caractéristiques exceptionnelles de résistance et de tolérance aux dommages de l'aluminium 7050 le rendent idéal pour les applications suivantes :
Structures aérospatiales
Les degrés de résistance les plus élevés de l'aluminium 7050, tels que T7451 et T7651, sont largement utilisés dans les pièces structurelles des avions, telles que les peaux d'ailes, les nervures, les longerons et les cadres. La combinaison de la légèreté et de la résistance de l'aluminium permet de réduire le poids total de l'avion.
Les composants tels que les cloisons, les revêtements de fuselage et les pièces de train d'atterrissage utilisent également l'aluminium 7050. Il peut résister aux charges répétées subies lors de l'exploitation d'un aéronef.
Raccords aérospatiaux
L'aluminium 7050-T7451 est utilisé pour fabriquer des raccords à haute résistance pour les systèmes aérospatiaux. Il s'agit notamment de raccords pour l'hydraulique, le carburant, le pneumatique et d'autres composants.
Cet alliage constitue une alternative au titane tout en offrant les performances mécaniques requises. Il permet aux ingénieurs de réduire les coûts des pièces et la complexité de la fabrication.
Cadres de motos et de vélos
La légèreté et la bonne résistance à la fatigue de l'aluminium 7050 lui ont valu d'être utilisé dans des cadres de moto et de bicyclette haut de gamme. Des marques comme Cannondale utilisent des tubes en alliage 7050 pour construire des cadres pour le cyclisme de compétition.
Cet alliage permet d'obtenir un cadre à la fois léger et capable de supporter les contraintes répétées du pédalage et les vibrations de la route. L'alliage avancé permet d'améliorer l'accélération, la capacité à grimper et la maniabilité.
Pièces pour châssis et suspensions automobiles
L'aluminium 7050 est parfois utilisé dans des applications automobiles performantes où la réduction du poids non suspendu est une priorité. Il s'agit notamment des bras de suspension, des moyeux, des rotules et d'autres composants du châssis.
La résistance de l'alliage permet d'utiliser des sections plus fines et plus légères. Il résiste également aux charges et aux vibrations subies par les pièces de suspension pendant des millions de cycles.
Applications marines et nucléaires
L'excellente résistance à la corrosion fissurante sous contrainte de l'aluminium 7050 le rend utile pour le matériel maritime et l'équipement des centrales nucléaires. Il peut fonctionner de manière fiable dans l'eau salée corrosive et les environnements radioactifs courants dans ces industries.
Fabrication additive
En tant que poudre, l'aluminium 7050 est idéal pour les techniques de fabrication additive telles que la fusion sélective par laser (SLM) et la fusion par faisceau d'électrons (EBM). Cela permet d'imprimer en 3D des pièces complexes et légères en 7050 pour l'aérospatiale et d'autres applications.
Les fines particules de poudre uniformes favorisent la fluidité, l'étalement et la qualité métallurgique des composants imprimés finaux.
Propriétés de l'alliage d'aluminium 7050
Il est important de comprendre les propriétés de l'AA7050 lorsque l'on envisage de l'utiliser pour des applications structurelles :
La force
Dans des conditions de vieillissement maximal comme T7651, l'aluminium 7050 a une résistance à la traction d'environ 570 MPa et une limite d'élasticité de 505 MPa. Ces valeurs sont nettement supérieures à celles de l'aluminium 6061-T6, dont les résistances à la traction et à l'élasticité sont respectivement de 310 MPa et 275 MPa.
La résistance des tôles en alliage 7050 peut diminuer légèrement pendant le soudage en raison d'un ramollissement localisé dans la zone affectée thermiquement. Des procédures de soudage appropriées sont utilisées pour minimiser cet effet.
Solidité
L'aluminium 7050 conserve une résistance raisonnablement bonne pour un alliage d'aluminium, mais n'atteint pas les niveaux d'autres alliages courants comme le 5083 et le 5454. Les sections plus épaisses seront plus sensibles aux entailles.
L'augmentation des niveaux de résistance est également corrélée à une réduction de la ténacité. Ainsi, le matériau 7050-T7651 aura une ténacité plus faible que le matériau 7050-T7451.
Résistance à la fatigue
L'un des principaux avantages de l'aluminium 7050 est son excellente résistance à la fatigue. Sa résistance aux charges cycliques est supérieure à celle des autres alliages 7xxx. Cela lui confère une meilleure tolérance aux dommages et une longue durée de vie.
Les microstructures à grain fin et le grenaillage de précontrainte sont utilisés pour améliorer encore la résistance à la fatigue des pièces finies en 7050. L'alliage est capable de résister à plus de 500 000 cycles de fatigue dans les applications aérospatiales.
Ténacité à la rupture
L'aluminium 7050 possède une assez bonne résistance à la rupture grâce aux mécanismes d'émoussement des pointes de fissures. Des valeurs de 35-40 MPa√m sont typiques pour les tôles plus épaisses.
Là encore, ce niveau de ténacité à la rupture reste inférieur aux alliages de la série 5xxx qui peuvent atteindre des niveaux de ténacité à la rupture supérieurs à 60 MPa√m.
Résistance à la corrosion
Dans les températures T7 les plus élevées, l'aluminium 7050 offre une bonne résistance à l'exfoliation et à la fissuration par corrosion sous contrainte (SCC). Il surpasse les autres alliages 7xxx à cet égard.
Il s'appuie sur le cuivre et le zirconium en solution solide pour améliorer la résistance à la fissuration par corrosion sous tension. Un bon traitement est important pour redistribuer correctement ces éléments.
La résistance générale à la corrosion du 7050 est modérée. Le revêtement avec de l'aluminium de haute pureté ou l'anodisation sont utilisés pour améliorer la résistance à la corrosion lorsque cela est nécessaire.
Soudabilité
La soudabilité de l'aluminium 7050 est considérée comme satisfaisante avec le soudage à l'arc sous gaz métallique (GMAW) ou le soudage à l'arc sous gaz tungstène (GTAW). La résistance de la soudure atteint généralement 60 à 80 % du métal de base.
Il faut faire attention aux risques de distorsion et de formation de fissures dans la zone affectée thermiquement pendant le soudage. Le préchauffage est recommandé pour ralentir la vitesse de refroidissement.
Le soudage par friction-malaxage peut également produire des soudures 7050 de haute qualité lorsqu'il est optimisé de manière adéquate. Un traitement thermique après soudage peut être utilisé pour récupérer les propriétés de la trempe.
Conductivité thermique
La conductivité thermique de l'aluminium 7050 est modérément élevée, de l'ordre de 121 W/m.K, mais inférieure à celle des alliages 1xxx plus purs. Cela favorise la dissipation de la chaleur dans les applications électroniques et de gestion de la chaleur.
Usinabilité
L'aluminium 7050 présente une bonne usinabilité pour un alliage à haute résistance, bien qu'elle soit encore inférieure à celle des alliages 5xxx et 6xxx. Le choix de l'outil et les paramètres d'usinage appropriés permettent de tenir compte de la résistance plus élevée.
Les outils de coupe doivent être suffisamment résistants pour supporter les contraintes élevées générées pendant l'usinage. Il est également important de mettre en place des machines rigides afin d'éviter les problèmes de broutage.
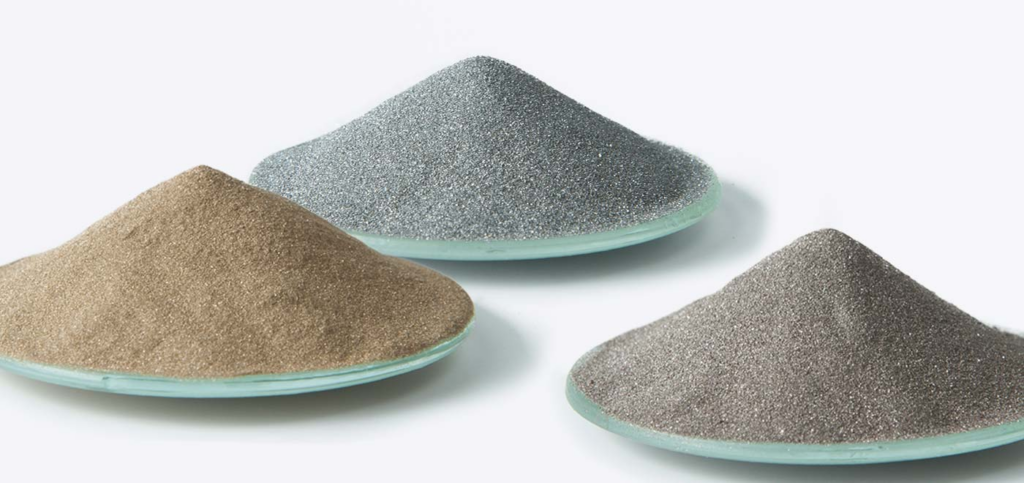
Températures pour l'aluminium 7050
Pour obtenir des performances optimales, l'aluminium 7050 est traité thermiquement à différentes températures en fonction de l'application :
- T7351 - Cette trempe offre une résistance moyenne à élevée avec une certaine ductilité et une certaine ténacité. Les niveaux typiques de résistance à la traction se situent autour de 490 MPa.
- T7451 - La trempe T7451 offre la résistance la plus élevée tout en conservant une ductilité et une résistance à la rupture raisonnables. La résistance à la traction atteint environ 520 MPa.
- T7651 - La résistance maximale pour les applications critiques en matière de tolérance aux dommages est obtenue en utilisant la trempe T7651. La résistance à la traction atteint environ 570 MPa.
- T736 – ; Cet état est sur-vieilli pour améliorer la ténacité à la rupture et la résistance à la corrosion tout en réduisant légèrement la résistance. Les niveaux de résistance à la traction d'environ 400 MPa sont atteints avec le T736.
Les numéros indiquent la séquence des traitements thermiques de base :
- 7xxx = Traitement thermique de mise en solution + trempe
- 3xx = Étirement après trempe
- 5x ou 6x = vieillissement artificiel
L'étirement permet d'améliorer la ténacité à la rupture dans les états T7451 et T7651. La durée et la température du vieillissement déterminent l'équilibre entre la résistance et la ténacité.
Transformation de l'alliage d'aluminium 7050
Pour obtenir un équilibre optimal des propriétés, l'alliage d'aluminium 7050 doit être soigneusement traité en suivant les étapes clés suivantes :
Fusion
La fusion à l'air n'est pas recommandée pour l'alliage 7050 en raison du risque élevé d'oxydation et d'accumulation d'hydrogène. La fusion par induction sous vide est principalement utilisée. Une grande fluidité pendant la coulée est obtenue avec des températures de fusion d'environ 750°C.
Le dégazage à l'argon ou à l'azote est essentiel pour minimiser la porosité. La fusion sous un gaz de couverture inerte réduit encore l'absorption d'hydrogène.
Des affineurs de grain tels que le titane et le bore sont ajoutés pour améliorer la structure du grain à la sortie de la coulée. Du zirconium peut également être ajouté à la matière fondue pour améliorer encore les propriétés de résistance à la traction.
Formation
La résistance plus élevée de l'aluminium 7050 signifie qu'une plus grande puissance est nécessaire pour les processus de transformation à chaud et de formage. Des températures comprises entre 370 et 440°C sont généralement utilisées.
Le refroidissement doit être suffisamment rapide pour obtenir des grains plus fins et des propriétés optimales. Mais pas trop rapide pour éviter les fissures de trempe. Pour la production de tôles, une température de finition de laminage à chaud supérieure à 260°C est recommandée.
Les extrusions nécessitent également une chaleur suffisante pendant le formage pour éviter les points faibles locaux associés à des températures d'extrusion plus basses.
Traitement thermique en solution
Le traitement thermique de mise en solution dissout les particules solubles telles que CuAl2 et MgZn2 en solution solide. Il est réalisé en chauffant l'aluminium 7050 à 465-485°C pendant environ 1 heure avant de le tremper dans l'eau.
Des vitesses de chauffage et de refroidissement lentes sont utilisées pour minimiser la distorsion et les contraintes thermiques pendant le traitement. La modification de la trempe avec une intensité de refroidissement réduite peut également être appliquée pour minimiser la fissuration par trempe.
Travail à froid
L'aluminium 7050 est souvent soumis à un travail à froid de 5 à 10 % entre la trempe et le vieillissement. Cela permet d'améliorer les propriétés mécaniques grâce à l'écrouissage à froid et à la formation accrue de précipités lors du durcissement par vieillissement.
L'étirement est une méthode courante de transformation à froid des produits 7050 tels que les plaques et les extrusions. Le laminage à froid peut également être utilisé pour les tôles et les feuilles.
Durcissement par l'âge
Le durcissement par vieillissement est effectué en chauffant le 7050 à 121°C pendant 24 heures pour obtenir un état de trempe T7. Les températures de vieillissement peuvent varier de 100 à 150°C en fonction de la résistance souhaitée.
Des températures de vieillissement plus élevées produisent une résistance plus faible mais améliorent la stabilité et la résistance à la corrosion. Le vieillissement en plusieurs étapes peut encore améliorer la résistance grâce à l'optimisation des précipités.
Lissage
Les étapes de trempe et de vieillissement produisent souvent des gauchissements et des déformations dans les pièces en aluminium 7050. Le redressage permet de garantir que les pièces respectent les tolérances dimensionnelles finales et les exigences en matière d'état de surface.
Le redressage par étirement est couramment utilisé pour les extrusions et les produits en feuilles laminés. Les sections de tôles peuvent utiliser des processus de nivellement par presse ou par rouleau pour corriger les distorsions.
Microstructure de l'alliage d'aluminium 7050
La microstructure de l'aluminium 7050 consiste en une matrice d'aluminium alliée à de fines particules de précipités secondaires :
Micrographie d'un alliage d'aluminium 7050 vieilli au maximum montrant de fins précipités (points sombres) dans la matrice d'aluminium. Crédit photo : ASTM International
Les principaux précipités sont les suivants :
- MgZn2 – ; Ce précipité de phase β′ apporte la contribution la plus substantielle au renforcement de l'aluminium 7050. Il se forme sous forme de particules finement dispersées à l'intérieur des grains et le long des joints de grains.
- Al2CuMg - Ces précipités de la phase T apportent un durcissement supplémentaire par précipitation. Ils se forment sur les dislocations et les limites de sous-grains.
- Al7Cu2Fe - Les particules d'Al7Cu2Fe contenant du fer servent de sites de nucléation pour la recristallisation pendant le traitement thermique. Certaines phases grossières d'Al7Cu2Fe sont également présentes.
- Al3Zr - Les dispersoïdes Al3Zr sont utilisés pour contrôler la structure des grains. Ils limitent la croissance des grains et la recristallisation, ce qui contribue à maintenir la résistance.
Une structure de grain fine et uniforme permet d'atteindre l'équilibre requis entre la résistance, la ténacité et d'autres propriétés mécaniques. La taille des grains est généralement de l'ordre de 25 μm.
Métallurgie des poudres Alliage d'aluminium 7050
Les techniques d'atomisation permettent de produire des poudres fines d'alliage d'aluminium 7050 adaptées à la fabrication additive ou au compactage de poudres :
atomisation du gaz
L'atomisation sous gaz inerte est la méthode la plus courante pour produire de la poudre d'aluminium 7050. De l'azote ou de l'argon à haute pression sont utilisés pour diviser un flux de métal en fusion en fines gouttelettes.
Les gouttelettes se solidifient rapidement en particules de poudre sphériques avec une distribution contrôlée de la taille des particules. La taille des particules de la poudre 7050 atomisée au gaz est généralement comprise entre 20 et 150 microns.
Atomisation par plasma
L'atomisation par plasma utilise un gaz plasma pour faire fondre et atomiser l'alliage. Elle produit des poudres plus sphériques dont la taille des particules est plus fine, de l'ordre de 5 à 45 microns.
Cela améliore l'écoulement et la densification de la poudre. Mais la poudre est généralement plus chère que les alternatives atomisées au gaz.
Alliage mécanique
Les poudres d'aluminium élémentaire et d'éléments d'alliage sont alliées mécaniquement pour synthétiser la poudre d'alliage 7050 dont la taille des particules est encore plus fine.
Des techniques de broyage à haute énergie sont utilisées pour créer une distribution homogène des ajouts d'alliage dans la matrice d'aluminium. Elles permettent la synthèse de poudres 7050 nanostructurées et amorphes.
Quelle que soit la méthode de production, une pureté élevée est essentielle pour la poudre 7050 destinée à la fabrication additive, au moulage par injection de métaux ou à d'autres procédés de métallurgie des poudres. Des contrôles stricts des niveaux d'oxygène et d'humidité, en particulier, permettent d'éviter les défauts.
Il est tout aussi important de manipuler et de stocker correctement la poudre et de contrôler l'atmosphère afin d'éviter toute contamination de la poudre avant son utilisation.
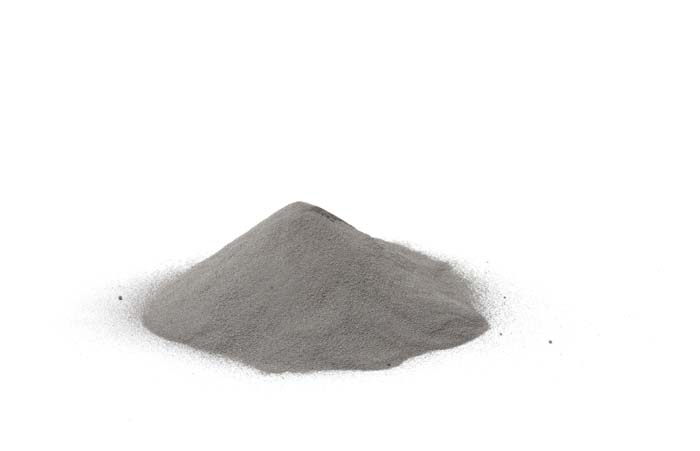
Fabrication additive avec de l'aluminium 7050
La poudre d'alliage d'aluminium 7050 est de plus en plus utilisée pour imprimer en 3D des composants légers et très résistants pour l'aérospatiale et la défense, grâce à des techniques de fusion sur lit de poudre.
La fusion sélective par laser (SLM) et la fusion par faisceau d'électrons (EBM) permettent toutes deux de traiter la poudre d'aluminium 7050. Les principales considérations sont les suivantes :
Optimisation des paramètres
Les paramètres de la machine doivent être optimisés pour obtenir des pièces 7050 entièrement denses avec les propriétés mécaniques souhaitées. Il s'agit d'aspects tels que l'épaisseur de la couche, la vitesse de balayage, la puissance du faisceau et l'espacement des hachures.
Pour minimiser la porosité tout en évitant la fissuration à chaud et la distorsion, il faut équilibrer les effets de chauffage et de refroidissement pendant l'impression.
Haute réflectivité
La surface polie et réfléchissante de la poudre d'aluminium 7050 peut refléter le rayonnement laser pendant le SLM au lieu de l'absorber efficacement. Des densités de puissance plus élevées et le prépolissage de chaque couche permettent de compenser ce problème.
Oxydation
Les films d'oxyde à la surface des particules de poudre doivent être brisés pendant la fusion pour éviter qu'ils ne soient piégés dans la pièce finale. Dans le cas contraire, ces oxydes entraîneront une réduction de la résistance.
Le traitement sous atmosphère inerte à l'aide d'argon ou d'azote minimise l'oxydation.
Contraintes résiduelles
Les contraintes résiduelles dues aux cycles de chauffage et de refroidissement localisés restent un problème lors des processus de construction AM en aluminium 7050. Une optimisation minutieuse des structures de support est nécessaire.
Les traitements thermiques post-production peuvent également contribuer à réduire les contraintes résiduelles dans la pièce imprimée. Le pressage isostatique à chaud (HIP) peut en outre améliorer les propriétés de traction en éliminant les vides internes.
Applications de la poudre d'aluminium 7050
Outre la fabrication additive, la poudre d'aluminium 7050 répond également aux besoins de.. :
Moulage par injection de métal (MIM)
La poudre d'alliage 7050 convient au moulage par injection de métaux pour créer des composants aérospatiaux et de défense de forme nette avec une résistance et une précision élevées.
Les poudres de 5 microns ou moins sont préférées pour le MIM afin d'obtenir un bon écoulement du moule et une bonne résistance des pièces vertes. Les étapes suivantes sont le mélange des liants, le moulage par injection, le déliantage et le frittage.
Forgeage des poudres
La poudre d'aluminium 7050 peut être forgée directement pour obtenir des pièces de forme presque nette. Après compactage en une forme préformée, le forgeage en matrice fermée crée des composants complexes en 3D grâce à une déformation contrôlée.
Les poudres Al-Zn-Mg-Cu facilitent l'écoulement et la cohésion pendant le compactage. La microstructure forgée finale présente des grains et des précipités fins et uniformes.
Pulvérisation thermique
La poudre d'aluminium 7050 est appliquée comme matériau de revêtement à l'aide de techniques de pulvérisation thermique telles que la pulvérisation à haute vitesse d'oxygène (HVOF). Cela permet d'obtenir une couche résistante à l'usure et à la corrosion.
Le revêtement offre une protection légère aux composants en aluminium ou en magnésium sans altérer leurs propriétés de base.
Soudage par poudres
La poudre d'aluminium 7050 spécialisée est utilisée pour les processus de soudage par poudrage visant à réparer ou à ajouter des matériaux aux pièces en aluminium. La technique produit des dépôts liés métallurgiquement avec une résistance similaire à celle de l'alliage de base.
L'apport à basse température permet d'éviter les dommages lors du soudage de pièces en aluminium sensibles à la chaleur. La poudre fine remplit les fissures et les zones endommagées.
Poudres pyrotechniques
La poudre d'aluminium 7050 sphérique avec une distribution granulométrique contrôlée sert de source de combustible dans les compositions pyrotechniques pour les fusées éclairantes, les allumeurs et d'autres dispositifs.
La poudre brûle facilement à haute température lorsqu'elle est combinée à des oxydants appropriés. Une contamination minimale par des particules étrangères est essentielle pour les poudres pyrotechniques.
FAQ sur la poudre d'alliage d'aluminium 7050
Q : Quels sont les types de poudre 7050 disponibles ?
R : Les poudres d'aluminium 7050 atomisées au gaz et au plasma sont les plus courantes. La taille des poudres varie de 5 à 150 microns. La morphologie sphéroïdale et la faible teneur en oxygène sont typiques. Des distributions granulométriques personnalisées peuvent être produites.
Q : Quelles sont les précautions à prendre lors de la manipulation de la poudre 7050 ?
R : L'exposition à l'air et à l'humidité doit être réduite au minimum pour éviter l'oxydation et l'absorption d'hydrogène. Il est recommandé de stocker le produit dans des récipients hermétiques munis d'un dessiccateur. Une mise à la terre appropriée et un environnement antidéflagrant peuvent être nécessaires pour les poudres inflammables.
Q : Quels sont les exemples d'applications de la poudre 7050 ?
R : Les principales applications de la poudre d'aluminium 7050 sont les suivantes :
- Fabrication additive par SLM ou EBM – ; Pour fabriquer des pièces aérospatiales et de défense à géométrie complexe.
- Moulage par injection de métal – ; Pour les petits composants de haute précision tels que les pales de turbines.
- Forgeage par poudrage – ; Production de pièces structurelles légères avec des caractéristiques intégrées.
- Pulvérisation thermique – ; Comme revêtement protecteur pour les composants en aluminium.
- Soudage par poudre – ; Pour réparer les fissures ou les dommages sur les pièces aérospatiales en aluminium.
Q : Quelle est la composition chimique typique de l'alliage d'aluminium 7050 ?
R : Une composition typique est la suivante :
- Zinc : 6,0-6,7
- Magnésium : 2.0-2.6%
- Cuivre : 2,0-2,5
- Zirconium : 0,08-0,15 %.
- Fer : 0,10 % maximum
- Silicium : 0,12 % maximum
- Manganèse : 0,10% max
- Titane : 0,06% max
- Chrome : 0,04% max
D'autres oligo-éléments peuvent également être présents jusqu'à des limites spécifiées.
Q : Quelle est la différence entre les alliages d'aluminium 7050 et 7075 ?
R : Les principales différences sont les suivantes :
- Le 7050 a une résistance plus élevée, jusqu'à 570 MPa contre 510 MPa pour le 7075.
- Le 7050 offre une meilleure résistance à la corrosion fissurante sous contrainte.
- 7050 contient du zirconium pour le contrôle de la structure du grain.
- L'alliage 7075 présente une résistance à la rupture légèrement supérieure.
- Le 7075 est plus largement utilisé dans des applications où les contraintes sont légèrement moindres.
en savoir plus sur les procédés d'impression 3D
Additional FAQs: Aluminium Alloy 7050 Powder
1) What particle size distribution works best for AM with Aluminium Alloy 7050 Powder?
- LPBF/SLM: typically 15–45 µm spherical (gas/plasma atomized) for stable flow and packing.
- EBM: 45–106 µm to match larger melt pools and high preheat. Maintain low satellites and high sphericity (>90%).
2) How critical is oxygen content in 7050 powder?
- Very. Elevated oxygen thickens surface oxides, increasing lack‑of‑fusion risk and reducing ductility. AM-grade 7050 often targets O ≤ 0.20 wt% (tighter is better) with dry room handling, sealed containers, and inert gas backfill.
3) Can 7050 be reliably printed without hot cracking?
- Yes, with tuned scan strategies, preheat, and hatch spacing. However, 7xxx Al-Zn-Mg-Cu systems are crack-prone; platform preheats, contour remelts, and tailored scan rotation reduce thermal gradients. Post-build HIP can further close pores.
4) What post-processing is recommended for printed 7050 parts?
- Stress relief, HIP (for density and fatigue), solution heat treatment + quench, controlled cold work/stretch (if applicable), and T7x aging to balance strength and SCC resistance. Surface finishing and anodizing/passivation may be used for corrosion control.
5) How does 7050 compare to 7075 for powder-bed AM?
- 7050 generally offers better stress corrosion cracking resistance and higher peak strengths in T7x than 7075. For AM, 7050 can provide improved damage tolerance; both require careful cracking mitigation and heat-treatment optimization.
2025 Industry Trends: Aluminium Alloy 7050 Powder
- AM qualification growth: More aerospace brackets, ribs, and fittings in 7050 qualified on LPBF with standardized parameter sets and HIP routes.
- Throughput and yield: Multi-laser systems and adaptive scan strategies cut build times by 10–18% and improve first-pass yield via reduced hot cracking.
- Powder genealogy: Wider adoption of digital material passports tracking oxygen pickup, PSD shifts, and reuse cycles.
- Sustainability: Increased closed-loop powder recovery and Environmental Product Declarations (EPDs) requested by primes.
- Heat treatment convergence: Standardized AM-specific T7x schedules tuned for SCC resistance without overaging strength loss.
2025 Snapshot for Aluminium Alloy 7050 Powder (Indicative)
Métrique | 2023 | 2024 | 2025 YTD (Aug) | Notes |
---|---|---|---|---|
Global 7050 AM powder demand (t) | ~850 | ~940 | ~1,050 | Aerospace + defense tooling |
AM-grade spherical 7050 price (USD/kg) | 70–140 | 65–130 | 60–125 | Competition + reuse programs |
Typical O spec (wt%) | ≤0.22 | ≤0.20 | ≤0.18 | Better atomization/handling |
LPBF build-rate improvement vs. 2023 | - | +8–12% | +10–18% | Multi-laser/process tuning |
HIP usage for flight-critical 7050 AM (%) | ~68 | ~72 | ~76 | Density + fatigue needs |
Reused powder share in AM builds (%) | 20–30 | 25-35 | 30–40 | With sieving + O/N monitoring |
Sources:
- ASTM/ISO AM standards: https://www.astm.org, https://www.iso.org
- MPIF design and powder characterization guides: https://www.mpif.org
- Industry market trackers (Context/Wohlers-type reports) and OEM notes (EOS, SLM Solutions, Renishaw, Carpenter Additive)
Latest Research Cases
Case Study 1: Crack-Resistant LPBF 7050 Brackets Using Adaptive Scan (2025)
Background: An aerospace tier-1 needed to reduce hot cracking and rework on thin-wall 7050 brackets.
Solution: Gas-atomized 7050 powder (D50 ~30 µm, O=0.17 wt%); applied 120–160°C platform preheat, contour remelts, and adaptive hatch rotation; post-build HIP and T7x aging.
Results: Lack-of-fusion defects reduced 40%; crack incidence down 60%; tensile strength after aging met targets (UTS ~540–560 MPa), first-pass yield +12%.
Case Study 2: EBM 7050 Lattice Stiffeners with Tailored Heat Treatment (2024)
Background: A defense OEM sought lightweight lattice stiffeners with SCC resistance comparable to wrought T7451.
Solution: EBM with 45–106 µm powder; high preheat minimized residual stress; selective HIP on dense regions; AM‑specific T7451-like schedule validated by SCC testing.
Results: Density ≥99.6% in dense zones; SCC performance matched wrought baseline in chloride exposure tests; mass reduced 15% vs. machined plate design.
Expert Opinions
- Prof. Kevin J. Hemker, Professor of Mechanical Engineering, Johns Hopkins University
- “For 7xxx Al powders like 7050, controlling thermal gradients and oxygen is as decisive as chemistry—both drive cracking susceptibility and final fatigue behavior.”
- Dr. Martina Zimmermann, Head of AM Materials, Sandvik Additive Manufacturing
- “Digital powder genealogy—tracking O/N and PSD across reuse—has become a qualification requirement for 7050 in flight hardware.”
- Dr. Brandon A. Lane, Additive Manufacturing Researcher, NIST
- “Process maps integrating scan strategy, preheat, and layer energy density are enabling repeatable 7050 builds with fewer hot cracks and tighter property scatter.”
Practical Tools and Resources
- ASTM F3302 (standard for AM material specs), F3122 (property data reporting), and relevant fatigue/SCC test methods: https://www.astm.org
- ISO/ASTM 52907 (feedstock requirements) and 52904 (LPBF of metals): https://www.iso.org
- MPIF standards for powder characterization and flow testing: https://www.mpif.org
- NIST AM-Bench datasets and process-mapping tools: https://www.nist.gov/ambench
- Senvol Database for machine–material qualifications: https://senvol.com
- OEM application/parameter notes (EOS, SLM Solutions, Renishaw; Carpenter Additive powder datasheets)
Last updated: 2025-08-25
Changelog: Added 5 targeted FAQs; inserted a 2025 snapshot table with indicative metrics and sources; provided two recent case studies; included expert viewpoints; compiled practical standards and resources
Next review date & triggers: 2026-02-01 or earlier if ASTM/ISO/MPIF standards update, major aerospace OEMs publish new 7050 AM qualifications, or market demand/price shifts >10%