Einführung
CuAl10-Pulver ist ein Hochleistungsmetallpulver, das aus einer Legierung aus Kupfer (Cu) und Aluminium (Al) hergestellt wird und in der Regel etwa 10% Aluminium nach Gewicht enthält. CuAl10-Pulver ist für seine hervorragenden mechanischen Eigenschaften und seine Korrosionsbeständigkeit bekannt und wird in zahlreichen Branchen eingesetzt, von der Luft- und Raumfahrt über die Elektronik bis hin zur additiven Fertigung. Wenn Sie sich fragen, was CuAl10 so besonders macht, lesen Sie weiter - wir werden uns mit seiner einzigartigen Zusammensetzung, seinen Eigenschaften und Anwendungen beschäftigen.
Zusammensetzung von CuAl10-Pulver
Das Verständnis der Zusammensetzung von CuAl10-Pulver ist der Schlüssel zur Erkenntnis, warum es ein so vielseitiges Material ist. Diese Legierung kombiniert die Leitfähigkeit von Kupfer mit den leichten Eigenschaften von Aluminium und eignet sich daher ideal für Anwendungen, die Festigkeit und Korrosionsbeständigkeit erfordern, ohne zu viel zusätzliches Gewicht.
Element | Prozentsatz nach Gewicht | Eingetragene Eigenschaften |
---|---|---|
Kupfer (Cu) | 90% | Bietet Leitfähigkeit, Duktilität |
Aluminium (Al) | 10% | Fügt Festigkeit hinzu, leichte Eigenschaft |
Spurenelemente | <1% | Stabilisierung und Feinabstimmung der Leistung |
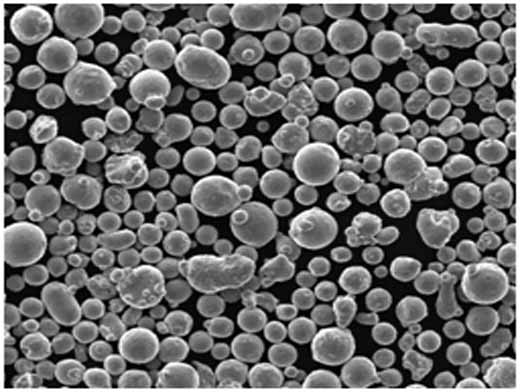
Herstellungsprozess von CuAl10-Pulver
Es gibt verschiedene Möglichkeiten zur Herstellung von CuAl10-Pulver, die sich jeweils auf die endgültigen Eigenschaften des Materials auswirken. Sehen wir uns die wichtigsten Herstellungsverfahren an und wie sie Eigenschaften wie Partikelgröße, Dichte und Reinheit beeinflussen.
Herstellungsverfahren | Prozessbeschreibung | Daraus resultierende Merkmale |
---|---|---|
Gaszerstäubung | Geschmolzene CuAl10-Legierung, besprüht mit Inertgas | Feine, kugelförmige Partikel; hohe Reinheit |
Wasserzerstäubung | Mit Hochdruckwasser besprühte Legierung | Unregelmäßige Form; kosteneffektiv; dicht |
Plasma-Zerstäubung | Legierung mit Plasmabogen für hohe Präzision | Ultrafeine Partikel; stark kontrollierte Größe |
Die Wahl des richtigen Herstellungsverfahrens hängt weitgehend von der geplanten Anwendung ab. So wird beispielsweise gaszerstäubtes Pulver aufgrund seiner kugelförmigen Partikelform und seines gleichmäßigen Flusses für den 3D-Druck bevorzugt.
Eigenschaften von CuAl10-Pulver
Die einzigartige Kombination von Kupfer und Aluminium in CuAl10-Pulver sorgt für ein ausgewogenes Verhältnis von mechanischer Festigkeit, Korrosionsbeständigkeit und Wärmeleitfähigkeit. Im Folgenden sind einige der wichtigsten Merkmale aufgeführt, die die Leistung dieser Legierung bestimmen.
Eigentum | Wert | Bedeutung |
---|---|---|
Dichte | ~7,3 g/cm³ | Leicht genug für Anwendungen in der Luft- und Raumfahrt |
Schmelzpunkt | 1,030°C | Geeignet für Umgebungen mit hohen Temperaturen |
Zugfestigkeit | Bis zu 280 MPa | Bietet Haltbarkeit für strukturelle Anwendungen |
Wärmeleitfähigkeit | ~125 W/mK | Hervorragende Wärmeableitung, nützlich in der Elektronik |
Diese Eigenschaften machen CuAl10-Pulver ideal für Anwendungen, bei denen ein ausgewogenes Verhältnis von Festigkeit und Gewicht entscheidend ist und bei denen die Wärmeableitung eine wichtige Rolle spielt.
Arten und Modelle von CuAl10-Pulver
CuAl10-Pulver ist in verschiedenen Modellen erhältlich, die jeweils durch Anpassung von Parametern wie Partikelgröße und Reinheit auf bestimmte Anwendungen zugeschnitten sind. Nachstehend finden Sie eine Übersicht über einige häufig verwendete Modelle von CuAl10-Pulver.
Modell | Partikelgrößenbereich | Reinheitsgrad | Gemeinsame Nutzung |
---|---|---|---|
CuAl10-40S | 40-60 Mikrometer | 99% | Sinterverfahren |
CuAl10-25F | 25-45 Mikrometer | 99.5% | Metall-Spritzgießen (MIM) |
CuAl10-80M | 80-100 Mikrometer | 98% | Thermische Spritzschichten |
CuAl10-15P | 10-20 Mikrometer | 99.9% | 3D-Druck, hohe Präzision |
CuAl10-Nano | <1 Mikron | 99.8% | Leitfähige Tinten, Elektronik |
CuAl10-MAX300 | 250-300 Mikrometer | 98.5% | Strukturelle Anwendungen |
CuAl10-HF45 | 45-75 Mikrometer | 99.7% | Induktive Hochfrequenz-Erwärmung |
CuAl10-XP40 | 40-60 Mikrometer | 99% | Additive Fertigung |
CuAl10-LowO2 | 40-60 Mikrometer | Niedrige Oxidation | Oxidationsempfindliche Anwendungen |
CuAl10-HP20 | 20-30 Mikrometer | 99.5% | Hochleistungs-Schweißzusatzwerkstoff |
Jedes Modell bietet je nach Anwendung unterschiedliche Vorteile, so dass die Wahl der richtigen Variante eine optimale Leistung und Effizienz gewährleistet.
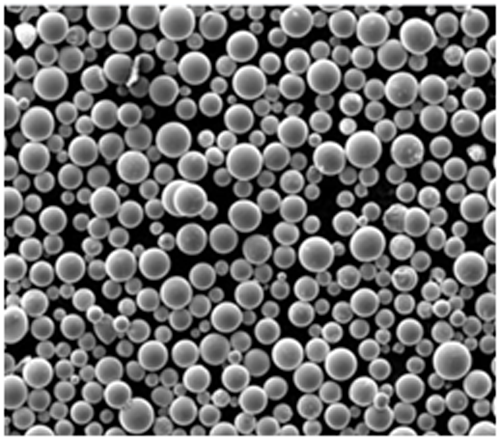
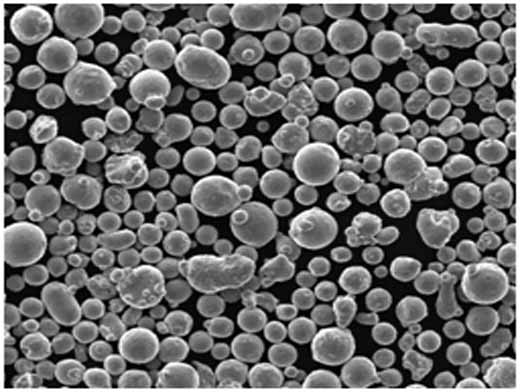
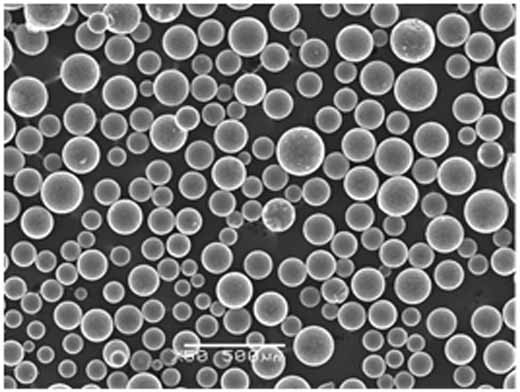
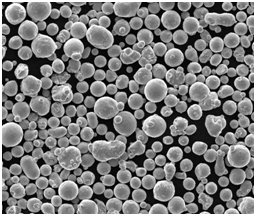
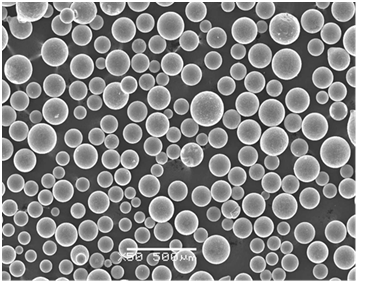
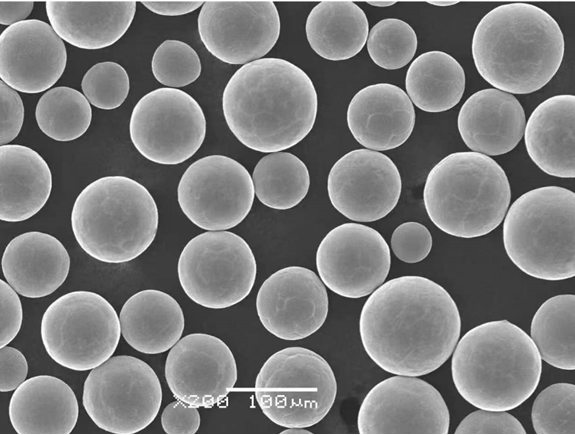
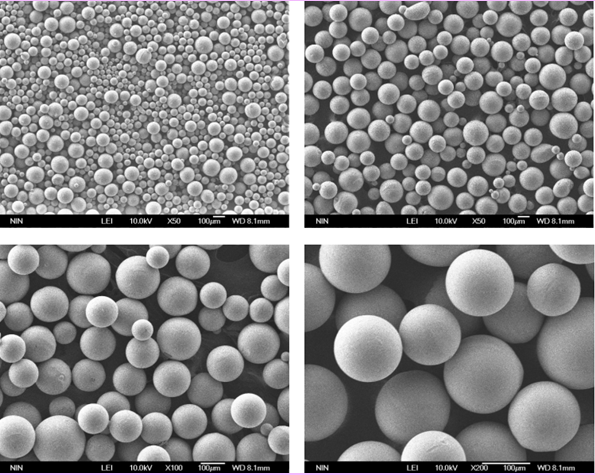
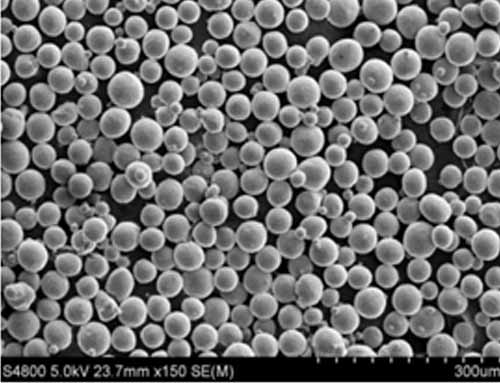
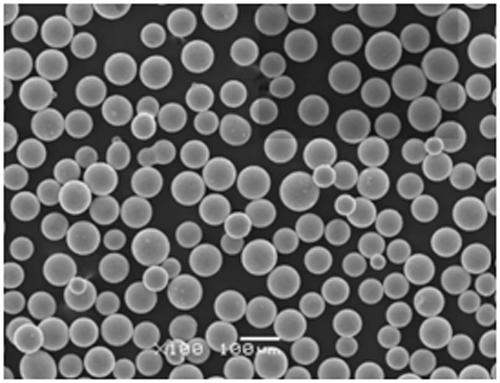
Anwendungen und Einsatzmöglichkeiten von CuAl10-Pulver
CuAl10-Pulver wird aufgrund seiner vielseitigen Eigenschaften in zahlreichen Branchen eingesetzt. Von komplexen Komponenten für die Luft- und Raumfahrt bis hin zum Wärmemanagement in der Elektronik - sehen wir uns an, wie CuAl10-Pulver in verschiedenen Bereichen eingesetzt wird.
Anwendungsbereich | Die Rolle von CuAl10-Pulver | Bemerkenswerte Modelle |
---|---|---|
Additive Fertigung | Ermöglicht präzise, leichte und langlebige 3D-gedruckte Teile | CuAl10-P15, CuAl10-40S |
Luft- und Raumfahrt | Einsatz in Bauteilen, die eine hohe Festigkeit bei geringem Gewicht erfordern | CuAl10-MAX300, CuAl10-25F |
Elektronik | Hervorragend geeignet für Wärmesenken, leitfähige Druckfarben | CuAl10-Nano, CuAl10-LowO2 |
Thermische Spritzschichten | Bietet korrosionsbeständige, thermische Schutzschichten | CuAl10-80M, CuAl10-40S |
Metall-Spritzgießen | Geeignet für die Erstellung kleiner, komplexer Formen | CuAl10-25F, CuAl10-15P |
Ob in der hochmodernen additiven Fertigung oder bei thermischen Spritzschichten, CuAl10-Pulver zeichnet sich durch seine Festigkeit und Leitfähigkeit aus.
Technische Spezifikationen, Größen und Normen für CuAl10-Pulver
Die Einhaltung von Industriestandards ist bei Metallpulvern wie CuAl10 von entscheidender Bedeutung. Die Einhaltung der ASTM- und ISO-Spezifikationen gewährleistet Qualität und Kompatibilität mit anderen Materialien.
Spezifikation | Norm (ISO/ASTM) | Partikelgröße (Mikron) | Reinheit |
---|---|---|---|
Additive Fertigung | ISO/ASTM 52900 | 10-100 | 99.5% |
Sintern | ASTM B212 | 20-60 | 99% |
Metall-Spritzgießen | ASTM B243 | 25-45 | 99.5% |
Thermische Spritzschichten | ISO 14919 | 50-100 | 98% |
Lieferanten, Preisgestaltung und Verfügbarkeit
CuAl10-Pulver wird von mehreren Anbietern weltweit angeboten, die jeweils unterschiedliche Branchen und Anforderungen bedienen.
Anbieter | Standort | Preisgestaltung (USD/kg) | Vorlaufzeit | Spezialisierung |
---|---|---|---|---|
PowderMet Inc. | USA | $40-$60 | 2-4 Wochen | Hochreine Pulver |
Global Alloys Co. | Deutschland | $50-$70 | 3-6 Wochen | Industrietauglich, Großaufträge |
Nippon Alloys Ltd. | Japan | $45-$65 | 2-3 Wochen | Nano- und Hochpräzisions-Pulver |
EuroPulver GmbH | Deutschland | $55-$75 | 4-6 Wochen | Thermische und strukturelle Anwendungen |
Die Preisgestaltung hängt von Faktoren wie Modell, Reinheit und Großabnahmemenge ab. Große Anbieter gewähren oft Rabatte für Großbestellungen und Sondergrößen.
Vorteile und Beschränkungen von CuAl10-Pulver
CuAl10-Pulver bietet zahlreiche Vorteile, ist aber auch nicht ohne Herausforderungen. Das Verständnis beider Aspekte kann helfen, fundierte Kauf- und Anwendungsentscheidungen zu treffen.
Vorteile | Beschränkungen |
---|---|
Stark und korrosionsbeständig | Teurer im Vergleich zu Basislegierungen |
Leicht und dennoch langlebig | Nicht ideal für Hochtemperaturoxidation |
Ausgezeichnete Leitfähigkeit | Begrenzte Anzahl von Lieferanten für Nanopulver |
Erhältlich in verschiedenen Partikelgrößen | Einige Modelle haben eine längere Vorlaufzeit |
Vergleich von CuAl10-Pulver zu ähnlichen Legierungen
Möchten Sie wissen, wie CuAl10 im Vergleich zu ähnlichen Legierungen wie CuAl8 oder CuAl15 abschneidet? Hier ist ein schneller Vergleich:
Legierung | Cu Inhalt | Zum Inhalt | Eignung des Anwendungsfalls | Kosten |
---|---|---|---|---|
CuAl10 | 90% | 10% | Ausgewogene Anwendungen | Mäßig |
CuAl8 | 92% | 8% | Hohe Duktilität, mittlere Festigkeit | Unter |
CuAl15 | 85% | 15% | Hohe Korrosionsbeständigkeit | Etwas höher |
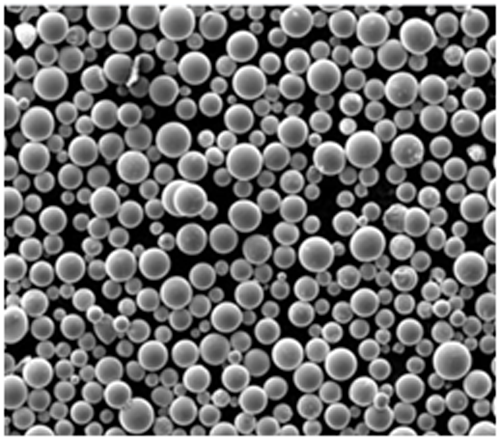
FAQ
Frage | Antwort |
Wofür wird CuAl10-Pulver verwendet? | CuAl10-Pulver wird wegen seiner Festigkeit, Leitfähigkeit und Korrosionsbeständigkeit im 3D-Druck, in der Elektronik und in der Luft- und Raumfahrt verwendet. |
Wie wird CuAl10-Pulver hergestellt? | Es wird hauptsächlich durch Gas-, Wasser- oder Plasmazerstäubung hergestellt, wobei jede Methode unterschiedliche Partikeleigenschaften erzeugt. |
Ist CuAl10-Pulver teuer? | Die Preise variieren, aber im Allgemeinen ist es aufgrund seiner besonderen Eigenschaften teurer als einfachere Legierungen. |
Kann CuAl10-Pulver zum Schweißen verwendet werden? | Ja, bestimmte Modelle wie CuAl10-HP20 sind für Schweißzusatzwerkstoffe geeignet. |
Wie ist CuAl10 im Vergleich zu reinem Kupfer? | CuAl10 ist aufgrund seines Aluminiumgehalts leichter und fester, bietet aber eine etwas geringere Leitfähigkeit als reines Kupfer. |
Schlussfolgerung
CuAl10-Pulver ist aufgrund seiner Langlebigkeit, Korrosionsbeständigkeit und Anpassungsfähigkeit in zahlreichen Branchen nach wie vor ein sehr begehrtes Material. Vom 3D-Druck über die Luft- und Raumfahrt bis hin zur Elektronik ist CuAl10-Pulver unverzichtbar für Anwendungen, bei denen Festigkeit, Leitfähigkeit und Korrosionsbeständigkeit entscheidend sind. Mit der Weiterentwicklung der Fertigungstechniken wächst die Palette der Modelle und Anwendungen für CuAl10-Pulver weiter und festigt seinen Platz als vielseitige Hochleistungslegierung in der modernen Technik.