Willkommen in der faszinierenden Welt der Additive Manufacturing (AM)-Maschinen! Diese unglaublichen Geräte revolutionieren die Art und Weise, wie wir Produkte herstellen, entwerfen und fertigen. Stellen Sie sich vor, Sie könnten Objekte Schicht für Schicht aufbauen und dabei Materialien wie Metalle, Kunststoffe und Keramiken direkt aus digitalen Modellen verwenden. Klingt nach Science-Fiction? Nun, es passiert gerade!
In diesem Artikel werden wir uns mit den Feinheiten von AM-Maschinenbefassen und uns dabei auf ihre Anwendungen, Vorteile und natürlich die Metallpulver konzentrieren, die ihre Magie befeuern. Wir werden die Arten der verwendeten Metallpulver, ihre Zusammensetzung, Eigenschaften und vieles mehr untersuchen. Also schnallen Sie sich an und machen Sie sich bereit für eine spannende Reise durch die Welt der AM-Maschinen.
Überblick über AM-Maschinen
Additive Manufacturing, allgemein bekannt als 3
What are AM Machines?
AM machines are advanced devices that use digital designs to build physical objects layer by layer. They work with a variety of materials, including metals, polymers, and ceramics. These machines can create complex geometries that are impossible to achieve with traditional manufacturing methods.
Wie funktionieren AM-Maschinen?
AM-Maschinen folgen einem einfachen, aber anspruchsvollen Verfahren:
- Gestaltung: Ein 3D-Modell wird mit Computer-Aided Design (CAD)-Software erstellt.
- Schneiden von: Das Modell wird in dünne Schichten zerlegt.
- Drucken: Die Maschine fügt Material Schicht für Schicht hinzu und folgt dabei dem digitalen Bauplan.
- Nachbearbeitung: Das gedruckte Objekt wird mit notwendigen Behandlungen wie Polieren oder Wärmebehandlung fertiggestellt.
Vorteile von AM-Maschinen
- Komplexe Geometrien: Erstellung komplexer Designs, die mit herkömmlichen Methoden nicht möglich sind.
- Materialeffizienz: Minimaler Abfall im Vergleich zur subtraktiven Fertigung.
- Personalisierung: Einfache Modifizierung von Designs für personalisierte Produkte.
- Geschwindigkeit: Schnelles Prototyping und Produktion.
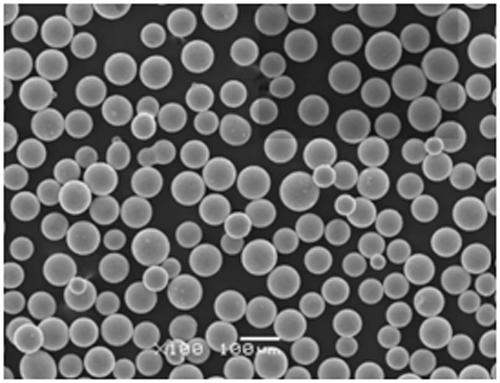
Arten von AM-Maschinen
Lassen Sie uns in die verschiedenen Arten von AM-Maschinen eintauchen, jede mit einzigartigen Fähigkeiten und Anwendungen.
1. Stereolithographie (SLA)
SLA verwendet einen Laser, um flüssiges Harz in feste Objekte auszuhärten. Sie ist ideal für die Erstellung detaillierter Prototypen mit glatten Oberflächen.
2. Selektives Lasersintern (SLS)
SLS verwendet einen Laser, um pulverförmiges Material zu verschmelzen. Es eignet sich hervorragend für die Herstellung haltbarer, funktionaler Teile aus einer Vielzahl von Materialien.
3. Fused Deposition Modeling (FDM)
FDM schmilzt und extrudiert thermoplastische Filamente, um Objekte zu erstellen. Es ist eine beliebte Wahl für Hobbyisten und industrielle Anwendungen.
4. Direct Metal Laser Sintering (DMLS)
DMLS verwendet einen Laser, um Metallpulver zu sintern und starke und komplizierte Metallteile zu erzeugen. Es wird häufig in der Luft- und Raumfahrt- sowie in der Medizinindustrie eingesetzt.
5. Elektronenstrahlschmelzen (EBM)
EBM verwendet einen Elektronenstrahl, um Metallpulver zu schmelzen. Es ist perfekt für Hochleistungs- und Hochtemperaturanwendungen.
Metallpulver für AM-Maschinen
Metallpulver sind das Herzstück vieler AM-Verfahren, insbesondere in Branchen, die hohe Festigkeit und Präzision erfordern. Hier sind einige wichtige Metallpulver, die in AM verwendet werden:
1. Titanlegierungen (Ti-6Al-4V)
Beschreibung: Titanlegierungen sind für ihre hohe Festigkeit, ihr geringes Gewicht und ihre hervorragende Korrosionsbeständigkeit bekannt.
Anwendungen: Luft- und Raumfahrt, medizinische Implantate, Automobilindustrie.
Eigenschaften: Hohes Festigkeits-Gewichts-Verhältnis, Biokompatibilität, ausgezeichnete Ermüdungsbeständigkeit.
2. Rostfreier Stahl (316L)
Beschreibung: Eine vielseitige Legierung, die für ihre Korrosionsbeständigkeit und Festigkeit bekannt ist.
Anwendungen: Medizinische Geräte, Lebensmittelverarbeitung, chemische Industrie.
Eigenschaften: Hohe Festigkeit, Korrosionsbeständigkeit, gute Duktilität.
3. Inconel (IN625)
Beschreibung: Eine Nickel-Chrom-Superlegierung mit ausgezeichneter Hochtemperaturfestigkeit und Korrosionsbeständigkeit.
Anwendungen: Luft- und Raumfahrt, Energieerzeugung, Meeresindustrie.
Eigenschaften: Hohe Temperatur- und Oxidationsbeständigkeit, hohe Festigkeit.
4. Aluminiumlegierungen (AlSi10Mg)
Beschreibung: Leichte und stabile Aluminiumlegierungen sind ideal für Teile, die gute thermische Eigenschaften erfordern.
Anwendungen: Automobilindustrie, Luft- und Raumfahrt, Unterhaltungselektronik.
Eigenschaften: Hohes Festigkeits-Gewichts-Verhältnis, gute Wärmeleitfähigkeit, Korrosionsbeständigkeit.
5. Werkzeugstahl (H13)
Beschreibung: Bekannt für seine Härte und Beständigkeit gegen Abrieb und Verschleiß.
Anwendungen: Werkzeuge, Formen und Gesenke.
Eigenschaften: Hohe Härte, Verschleißfestigkeit, thermische Stabilität.
6. Kobalt-Chrom (CoCr)
Beschreibung: Eine Superlegierung, die für ihre Verschleißfestigkeit und Biokompatibilität bekannt ist.
Anwendungen: Medizinische Implantate, Zahnprothetik, Luft- und Raumfahrt.
Eigenschaften: Hohe Verschleißfestigkeit, ausgezeichnete Biokompatibilität, hohe Festigkeit.
7. Kupferlegierungen (CuCr1Zr)
Beschreibung: Kupferlegierungen werden für ihre Wärme- und elektrische Leitfähigkeit geschätzt.
Anwendungen: Elektronische Bauteile, Wärmetauscher, Raketentriebwerkskomponenten.
Eigenschaften: Hohe Wärme- und elektrische Leitfähigkeit, gute Festigkeit.
8. Maraging-Stahl (1.2709)
Beschreibung: Ein hochfester Stahl mit ausgezeichneter Zähigkeit und Dimensionsstabilität.
Anwendungen: Luft- und Raumfahrt, Werkzeugbau, Hochleistungsmaschinenbau.
Eigenschaften: Hohe Festigkeit, gute Zähigkeit, ausgezeichnete Schweißbarkeit.
9. Nickellegierung (Hastelloy X)
Beschreibung: Bekannt für seine Beständigkeit gegen Oxidation und Hochtemperaturfestigkeit.
Anwendungen: Luft- und Raumfahrt, chemische Verarbeitung, Industriegasturbinen.
Eigenschaften: Hochtemperaturfestigkeit, Oxidationsbeständigkeit, Korrosionsbeständigkeit.
10. Wolframkarbid (WC-Co)
Beschreibung: Extrem hart und verschleißfest, wird in anspruchsvollen Umgebungen eingesetzt.
Anwendungen: Schneidwerkzeuge, verschleißfeste Teile, Bergbauausrüstung.
Eigenschaften: Hohe Härte, ausgezeichnete Verschleißfestigkeit, hohe Wärmeleitfähigkeit.
Zusammensetzung und Eigenschaften von Metallpulvern
Hier ist ein detaillierter Blick auf die Zusammensetzung und die Eigenschaften dieser Metallpulver:
Metall-Pulver | Zusammensetzung | Eigenschaften |
---|---|---|
Titan-Legierungen | Ti, Al, V | Hohes Festigkeits-Gewichts-Verhältnis, Biokompatibilität |
rostfreier Stahl | Fe, Cr, Ni, Mo | Korrosionsbeständigkeit, gute Duktilität |
Inconel | Ni, Cr, Mo, Nb | Hohe Temperaturbeständigkeit, Oxidationsbeständigkeit |
Aluminium-Legierungen | Al, Si, Mg | Leichtgewicht, Wärmeleitfähigkeit, Korrosionsbeständigkeit |
Werkzeugstahl | Fe, C, Cr, Mo | Härte, Verschleißfestigkeit, thermische Stabilität |
Kobalt-Chrom | Co, Cr, Mo | Abriebfestigkeit, Biokompatibilität |
Kupfer-Legierungen | Cu, Cr, Zr | Wärme- und elektrische Leitfähigkeit, Festigkeit |
Martensitaushärtender Stahl | Fe, Ni, Co, Mo | Hohe Festigkeit, Zähigkeit, Schweißbarkeit |
Nickellegierung | Ni, Cr, Mo, Fe | Oxidationsbeständigkeit, Hochtemperaturfestigkeit |
Wolframkarbid | WC, Co | Härte, Verschleißfestigkeit, Wärmeleitfähigkeit |
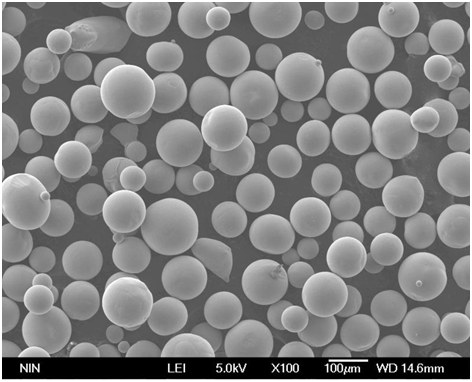
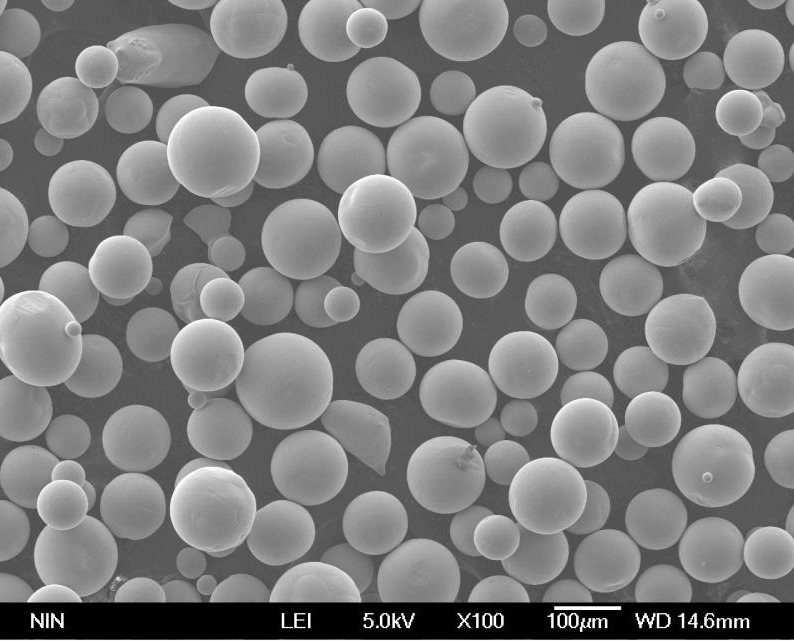
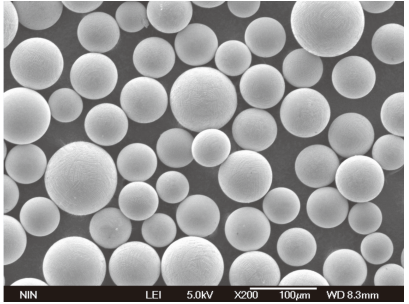
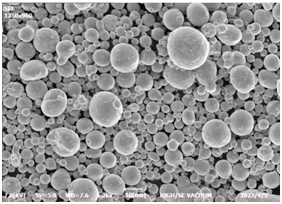
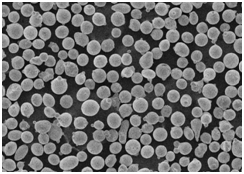

Anwendungen von Metallpulvern in AM
Die Vielseitigkeit von Metallpulvern in AM ermöglicht eine breite Palette von Anwendungen in verschiedenen Branchen:
Industrie | Anwendungen |
---|---|
Luft- und Raumfahrt | Motorkomponenten, Strukturteile, Wärmetauscher |
Medizinische | Implantate, Prothesen, chirurgische Instrumente |
Automobilindustrie | Leichte Teile, Motorkomponenten, kundenspezifische Teile |
Elektronik | Kühlkörper, Steckverbinder, Gehäuse |
Werkzeugbau | Formen, Gesenke, Schneidwerkzeuge |
Energie | Turbinenschaufeln, Wärmetauscher, Teile zur Energieerzeugung |
Konsumgüter | Schmuck, Brillen, kundenspezifische Produkte |
Spezifikationen, Größen, Güteklassen und Normen
Bei der Auswahl von Metallpulvern für AM ist es entscheidend, ihre Spezifikationen, Größen, Qualitäten und Standards zu berücksichtigen:
Metall-Pulver | Spezifikationen | Größen | Klassen | Normen |
---|---|---|---|---|
Titan-Legierungen | ASTM B348, AMS 4999 | 15-45 µm, 45-106 µm | Ti-6Al-4V ELI | ASTM F2924, ISO 5832-3 |
rostfreier Stahl | ASTM A276, ASTM F138 | 10-50 µm, 20-63 µm | 316L, 17-4 PH | ASTM F138, ISO 5832-1 |
Inconel | AMS 5666, UNS N06625 | 15-45 µm, 20-60 µm | IN625, IN718 | ASTM B443, AMS 5662 |
Aluminium-Legierungen | ASTM B209, AMS 4225 | 20-63 µm, 10-50 µm | AlSi10Mg, AlSi12 | ASTM B918, ISO 3522 |
Werkzeugstahl | ASTM A681, AISI H13 | 15-45 µm, 20-60 µm | H13, D2 | ASTM A681, DIN 1.2344 |
Kobalt-Chrom | ASTM F75, ISO 5832-12 | 15-4 | CoCrMo, CoCrW | ASTM F75, ISO 5832-12 |
Kupfer-Legierungen | ASTM B152, C18150 | 10-50µm, 15-45µm | CuCr1Zr, C18150 | ASTM B187, AMS 4980 |
Martensitaushärtender Stahl | AMS 6514, AISI 18Ni(300) | 10-45µm, 20-60µm | 1.2709, 18Ni(300) | AMS 6520, DIN 1.6358 |
Nickellegierung | ASTM B435, UNS N06002 | 10-45µm, 20-60µm | Hastelloy X, N06002 | ASTM B435, AMS 5754 |
Wolframkarbid | ISO 9001, ASTM B777 | 5-20µm, 10-45µm | WC-Co, Cobalt-bonded | ISO 9001, ASTM B777 |
Lieferanten und Preisangaben
Hier ist ein Blick auf einige führende Anbieter von Metallpulvern und deren Preisdetails:
Anbieter | Metallpulver | Preisspanne (pro kg) |
---|---|---|
Hoganas AB | Rostfreier Stahl, Werkzeugstahl | $50 – $200 |
Tischlertechnik | Titanlegierungen, Inconel | $300 – $600 |
Sandvik | Edelstahl, Maraging-Stahl | $100 – $400 |
LPW-Technologie | Kobalt-Chrom, Inconel | $250 – $700 |
GKN-Zusatzstoff | Aluminiumlegierungen, Titanlegierungen | $150 – $500 |
AP&C (GE-Zusatzstoff) | Titanlegierungen, Aluminiumlegierungen | $200 – $800 |
HC Starck | Wolframkarbid, Kobalt-Chrom | $100 – $300 |
Arcam AB | Titanlegierungen, Edelstahl | $200 – $600 |
Erasteel | Werkzeugstahl, Maraging-Stahl | $150 – $400 |
Aubert & Duval | Nickellegierungen, Werkzeugstahl | $200 – $500 |
Vorteile und Beschränkungen von AM-Maschinen
Wie jede Technologie haben auch AM-Maschinen ihre Stärken und Schwächen:
Vorteile
Vorteil | Erläuterung |
---|---|
Gestaltungsfreiheit | Erstellung komplexer Geometrien und komplizierter Designs. |
Materialeffizienz | Minimaler Abfall, da das Material Schicht für Schicht hinzugefügt wird. |
Personalisierung | Einfache Modifizierung von Designs für personalisierte Produkte. |
Schnelles Prototyping | Schnelle Abwicklung vom Design bis zum fertigen Produkt. |
On-Demand-Produktion | Herstellung von Teilen nach Bedarf, wodurch die Lagerkosten reduziert werden. |
Beschränkungen
Begrenzung | Erläuterung |
---|---|
Materielle Beschränkungen | Nicht alle Materialien sind für AM-Verfahren geeignet. |
Oberflächengüte | Kann eine Nachbearbeitung erfordern, um die gewünschte Oberflächenqualität zu erreichen. |
Größenbeschränkungen | Begrenztes Bauvolumen im Vergleich zu herkömmlichen Fertigungsverfahren. |
Kosten | Hohe Anfangsinvestition für Ausrüstung und Materialien. |
Geschwindigkeit | Langsamer als einige herkömmliche Fertigungsverfahren für die Großserienproduktion. |
Zusammensetzung und Eigenschaften von AM-Maschinen
Das Verständnis der Zusammensetzung und der Eigenschaften von AM-Maschinen ist entscheidend für die Auswahl der richtigen Maschine für Ihre Anforderungen.
Arten und Eigenschaften von AM-Maschinen
Typ | Material | Merkmale |
---|---|---|
SLA | Photopolymerharz | Hohe Präzision, glatte Oberflächenbeschaffenheit, ideal für Prototypen |
SLS | Nylon, Polyamid, Metall | Starke, langlebige Teile, geeignet für Funktionsprototypen |
FDM | Thermoplastisches Filament | Erschwinglich, gut für Rapid Prototyping und Hobbyisten |
DMLS | Metallpulver (Ti, Al, SS) | Hochfeste, komplizierte Metallteile, die in der Luft- und Raumfahrt und im medizinischen Bereich verwendet werden |
EBM | Metallpulver (Ti, CoCr) | Hochtemperatur-, hochfeste Teile, die in kritischen Industrien verwendet werden |
Eigenschaften von AM-Maschinen
Eigentum | Beschreibung |
---|---|
Volumen aufbauen | Die maximale Größe des Objekts, das gedruckt werden kann. |
Schichtauflösung | Dicke jeder Schicht, die sich auf die Oberflächenbeschaffenheit und die Details auswirkt. |
Kompatibilität der Materialien | Bandbreite der Materialien, die die Maschine verwenden kann. |
Druckgeschwindigkeit | Geschwindigkeit, mit der die Maschine drucken kann, was sich auf die Produktionszeit auswirkt. |
Präzision | Genauigkeit der gedruckten Teile, entscheidend für hochpräzise Anwendungen. |
Anwendungen und Anwendungsfälle von AM-Maschinen
AM-Maschinen sind vielseitige Werkzeuge, die in verschiedenen Branchen eingesetzt werden. Lassen Sie uns einige gängige Anwendungen untersuchen:
Luft- und Raumfahrt
AM-Maschinen werden zur Herstellung von leichten, hochfesten Komponenten wie Motorteilen und Strukturbauteilen verwendet. Die Fähigkeit, komplexe Geometrien herzustellen, reduziert das Gewicht und erhöht die Effizienz von Luft- und Raumfahrtkomponenten.
Medizinische
Im medizinischen Bereich stellen AM-Maschinen kundenspezifische Implantate, Prothesen und chirurgische Instrumente her. Die Präzision und die Anpassungsmöglichkeiten stellen sicher, dass medizinische Geräte perfekt zu den Patienten passen und die Ergebnisse und den Komfort verbessern.
Automobilindustrie
Die Automobilindustrie verwendet AM-Maschinen zur Herstellung von leichten Teilen, kundenspezifischen Komponenten und Prototypen. Diese Technologie ermöglicht ein schnelles Prototyping und Testen neuer Designs und beschleunigt so den Entwicklungsprozess.
Konsumgüter
AM-Maschinen ermöglichen die Herstellung von kundenspezifisch gestalteten Konsumgütern, von Schmuck bis hin zu Brillen. Die Fähigkeit, Produkte zu personalisieren, spricht Verbraucher an, die einzigartige und maßgeschneiderte Artikel suchen.
Elektronik
In der Elektronik stellen AM-Maschinen Gehäuse, Kühlkörper und Steckverbinder her. Die Präzision und die Materialeigenschaften von AM stellen sicher, dass elektronische Komponenten die erforderlichen Spezifikationen für Leistung und Haltbarkeit erfüllen.
Werkzeugbau
AM-Maschinen werden zur Herstellung von Formen, Matrizen und Schneidwerkzeugen mit komplexen Geometrien und hoher Präzision verwendet. Diese Anwendung reduziert die Vorlaufzeiten und die Kosten, die mit herkömmlichen Werkzeugverfahren verbunden sind.
Vergleich von Metallpulvern für AM-Maschinen
Bei der Auswahl von Metallpulvern für AM ist es wichtig, ihre Eigenschaften und ihre Eignung für bestimmte Anwendungen zu vergleichen.
Titanlegierungen vs. Edelstahl
Titan-Legierungen sind für ihr hohes Festigkeits-Gewichts-Verhältnis und ihre Biokompatibilität bekannt, was sie ideal für Anwendungen in der Luft- und Raumfahrt und im medizinischen Bereich macht. rostfreier Stahlbietet andererseits eine ausgezeichnete Korrosionsbeständigkeit und Festigkeit und eignet sich daher für eine Vielzahl von industriellen Anwendungen.
Inconel vs. Aluminiumlegierungen
Inconel ist eine Nickel-Chrom-Superlegierung, die für ihre Hochtemperaturfestigkeit und Oxidationsbeständigkeit bekannt ist und sich ideal für die Luft- und Raumfahrt und die Stromerzeugung eignet. Aluminium-Legierungen sind leicht und haben gute thermische Eigenschaften, wodurch sie sich für Anwendungen in der Automobilindustrie und der Unterhaltungselektronik eignen.
Werkzeugstahl vs. Kobalt-Chrom
Werkzeugstahl wird für seine Härte und Verschleißfestigkeit geschätzt, was ihn ideal für Werkzeuganwendungen macht. Kobalt-Chrom bietet eine hohe Verschleißfestigkeit und Biokompatibilität, die sich für medizinische Implantate und Zahnprothesen eignet.
Kupferlegierungen vs. Maraging-Stahl
Kupfer-Legierungen bieten eine ausgezeichnete Wärme- und elektrische Leitfähigkeit, wodurch sie sich für elektrische Komponenten und Wärmetauscher eignen. Martensitaushärtender Stahl bietet eine hohe Festigkeit und Zähigkeit, ideal für Anwendungen in der Luft- und Raumfahrt und im Hochleistungsmaschinenbau.
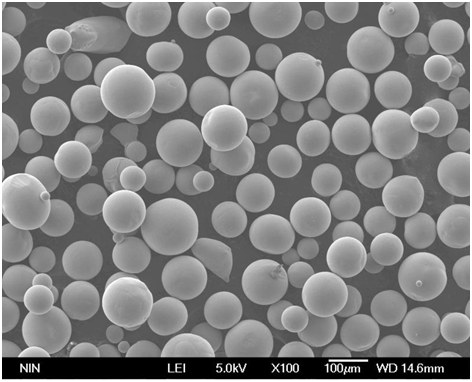
FAQ
Frage | Antwort |
---|---|
Was ist Additive Manufacturing? | Additive Manufacturing (AM) ist ein Verfahren zur Herstellung von Objekten durch schichtweises Hinzufügen von Material. |
Wie funktionieren AM-Maschinen? | AM-Maschinen verwenden digitale Designs, um Material schichtweise hinzuzufügen und so ein physisches Objekt zu erstellen. |
Welche Materialien können in AM-Maschinen verwendet werden? | AM-Maschinen können eine Vielzahl von Materialien verwenden, darunter Metalle, Polymere und Keramiken. |
Was sind die Vorteile von AM-Maschinen? | Zu den Vorteilen gehören Designfreiheit, Materialeffizienz, Anpassung, Rapid Prototyping und On-Demand-Produktion. |
Was sind die Einschränkungen von AM-Maschinen? | Zu den Einschränkungen gehören Materialbeschränkungen, Oberflächengüte, Größenbeschränkungen, Kosten und Geschwindigkeit. |
Welche Branchen nutzen AM-Maschinen? | Zu den Branchen gehören Luft- und Raumfahrt, Medizin, Automobilindustrie, Elektronik, Konsumgüter und Werkzeugbau. |
Wie wähle ich das richtige Metallpulver für AM aus? | Berücksichtigen Sie Faktoren wie Anwendungsanforderungen, Materialeigenschaften und Kompatibilität mit Ihrer AM-Maschine. |
Was sind einige gängige Metallpulver, die in AM verwendet werden? | Gängige Metallpul |
Können AM-Maschinen funktionale Teile herstellen? | Ja, AM-Maschinen können funktionale Teile mit hoher Präzision und Haltbarkeit herstellen. |
Wie sieht die Zukunft der AM-Maschinen aus? | Die Zukunft der AM-Maschinen ist vielversprechend, mit Fortschritten in Materialien, Verfahren und Anwendungen, die das Wachstum vorantreiben. |