3D-DruckDer 3D-Druck, auch bekannt als additive Fertigung, hat das Produktdesign und die Herstellungsprozesse revolutioniert. Durch den schichtweisen Aufbau von Objekten von unten nach oben ermöglicht der 3D-Druck eine Produktion auf Abruf ohne spezielle Werkzeuge oder Formen. Inzwischen gibt es zahlreiche Arten von 3D-Drucktechnologien, die jeweils ihre eigenen Vorteile und Einschränkungen haben. Dieser Leitfaden bietet einen umfassenden Überblick über die wichtigsten 3D-Druckverfahren, die heute eingesetzt werden.
Überblick über die wichtigsten 3D-Druckverfahren
Die 3D-Drucktechnologien lassen sich grob in 7 Typen einteilen:
Tabelle: Überblick über die wichtigsten 3D-Druckverfahren
Methode | Materialien | Wesentliche Merkmale | Typische Anwendungen |
---|---|---|---|
Fused Deposition Modeling (FDM) | Thermoplaste wie PLA, ABS | Geringe Kosten, gute Festigkeit | Prototypen, Druck für Hobbyisten |
Stereolithographie (SLA) | Fotopolymere | Hohe Genauigkeit, glatte Oberfläche | Prototypen, Herstellung |
Selektives Laser-Sintern (SLS) | Thermoplaste, Metalle | Gute mechanische Eigenschaften | Funktionsprototypen, Herstellung |
Multi Jet Fusion (MJF) | Thermoplastische Kunststoffe | Schnelles Drucken, gute Genauigkeit | Fertigung, Massenanpassung |
Elektronenstrahlschmelzen (EBM) | Metals | Vollständig dichte Metallteile | Fertigung, Luft- und Raumfahrt |
Herstellung laminierter Objekte (LOM) | Papier, Metall, Kunststoffplatten | Niedrige Kosten, große Teile | Konzeptmodelle, Werkzeugbau |
Gerichtete Energieabscheidung (DED) | Metall-Legierungen | Große Metallteile, Reparaturen | Luft- und Raumfahrt, Automobilindustrie |
Wie in der Tabelle zu sehen ist, hängt die Wahl des 3D-Druckverfahrens von Faktoren wie Zielanwendung, geeignete Materialien, Genauigkeit, Geschwindigkeit und Kosten ab. Jedes Verfahren hat Vor- und Nachteile, die es für bestimmte Anwendungen vorteilhafter machen als andere.
Der Rest dieses Leitfadens befasst sich mit jeder dieser Techniken eingehender.
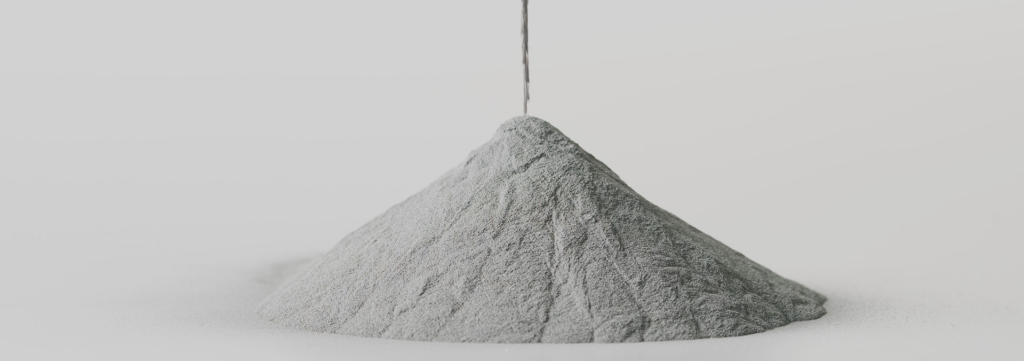
Fused Deposition Modeling (FDM)
FDM (Fused Deposition Modeling) ist die gängigste und erschwinglichste Art des 3D-Drucks, die heute verwendet wird. Bei FDM erhitzt ein Extruder thermoplastisches Filament in einen halbflüssigen Zustand und trägt es Schicht für Schicht auf, um ein Objekt zu erstellen.
So funktioniert der FDM-3D-Druck
Das FDM-Verfahren umfasst:
- Erhitzen eines thermoplastischen Filaments über seine Glasübergangstemperatur, um es geschmeidig zu machen
- Extrudieren des halbgeschmolzenen Materials durch eine Düse auf die Bauplatte
- Eine 2D-Schicht aufzeichnen, abkühlen und aushärten lassen
- Verschieben der Bauplatte nach unten und Wiederholung mit der nächsten Schicht
FDM-Drucker haben einen beweglichen Extruderkopf, der einem Werkzeugweg in X-Y-Koordinaten folgt, während er Material aufträgt. Die am häufigsten verwendeten Materialien sind ABS- und PLA-Kunststoffe. Dual-Extrusionsmaschinen können mit auflösbaren Trägern und mehreren Farben drucken.
Anwendungen von FDM
Tabelle: FDM 3D-Druck – Anwendungen und Möglichkeiten
Attribut | Beschreibung |
---|---|
Kosten | Kostengünstiger 3D-Druck, Maschinen unter 300 $ |
Materialien | ABS, PLA, PETG, flexibles TPU, Verbundwerkstoffe |
Genauigkeit | ±100 Mikrometer, mittlere Auflösung |
Geschwindigkeit | Mäßig, 30-100 mm/s Extrusion |
Größe des Teils | Klein bis mittelgroß, maximal etwa 1 Kubikfuß |
Wichtige Anwendungen | Konzeptmodelle, Prototyping, Hobbydrucker |
FDM wird für unkritische Anwendungen bevorzugt, die von einer kostengünstigen, schnellen und abfallarmen Prototyping-Fähigkeit profitieren. Aufgrund der durchschnittlichen Genauigkeit und Oberflächengüte eignet es sich eher für Form- und Passformtests als für Funktionsprototypen. Die Teile können nach der Bearbeitung gebohrt, geschliffen, lackiert oder galvanisch beschichtet werden.
Vorteile des FDM-Drucks
- Niedrige Maschinen- und Materialkosten machen es auch für kleine Unternehmen zugänglich
- Minimaler Abfall im Vergleich zu subtraktiven Methoden
- Einfache Bedienung mit minimalem Schulungsaufwand oder Fachwissen
- Möglichkeit zum Anhalten und Wechseln des Filaments für mehrfarbige Drucke
- Funktionsteile mit guten mechanischen Eigenschaften und thermischer Beständigkeit
Beschränkungen des FDM-Drucks
- Mittlere Genauigkeit von 100 Mikrometern begrenzt die Präzision von feinen Details
- Sichtbare Schichtlinien beeinträchtigen die Qualität der Oberfläche
- Begrenzte Anzahl von Materialien im Vergleich zu anderen Verfahren
- Überhänge und Brücken erfordern Stützkonstruktionen
Insgesamt bietet FDM ein ausgewogenes Verhältnis von Erschwinglichkeit und Leistungsfähigkeit, das es zu einem vielseitigen Ausgangspunkt für Unternehmen macht, die die Vorteile der additiven Fertigung erkunden wollen.
Stereolithographie (SLA)
Die Stereolithografie (SLA) war das erste kommerzielle 3D-Druckverfahren, das in den 1980er Jahren erfunden wurde. Es ist nach wie vor eine beliebte Wahl für seine hohe Genauigkeit und Oberflächenqualität.
So funktioniert der SLA-Druck
Beim SLA-Verfahren wird ein Bottich mit flüssigem Photopolymerharz verwendet, das mit einem Ultraviolettlaser selektiv Schicht für Schicht ausgehärtet wird.
Die wichtigsten Schritte sind:
- Eine Bauplattform senkt sich in den Behälter mit dem flüssigen Harz
- Ein Laserstrahl zeichnet den Querschnitt des Modells nach und härtet das Harz aus
- Die Plattform hebt sich, so dass frisches Harz unter die Plattform fließen kann.
- Die nächste Ebene wird direkt über der vorherigen Ebene gezeichnet
- Nach der Fertigstellung wird das Modell abgespült und weiter ausgehärtet.
Durch das Licht werden die Polymere im Harz vernetzt und das flüssige Harz wird zu festem Kunststoff in der gewünschten Form. Mit SLA lassen sich sehr detaillierte Modelle mit hervorragender Oberflächengüte herstellen.
Anwendungen des SLA-Drucks
Tabelle: SLA 3D-Druck – Anwendungen und Möglichkeiten
Attribut | Beschreibung |
---|---|
Kosten | Moderate Maschinenkosten, Harz kostet 100-200 $/Liter |
Materialien | Standard- und Spezialharze, klar, flexibel, gießbar |
Genauigkeit | Sehr hoch, bis zu 25 Mikrometer |
Geschwindigkeit | Schnell, bis zu 110 mm/Stunde |
Größe des Teils | Mittel, maximal etwa 1 Kubikfuß |
Wichtige Anwendungen | Detaillierte Prototypen, Endverbrauchsteile, Dental- und Schmuckwaren |
Die feine Auflösung macht SLA ideal für Anwendungen wie Konzeptmodelle, Visualisierungsprototypen, zahnmedizinische Aligner, Schmuckguss und präzise Endverbrauchsteile in der Luft- und Raumfahrt, im Gesundheitswesen und bei Verbraucherprodukten.
Vorteile des SLA-Drucks
- Hervorragende Oberflächengüte und winzige Details bis zu einer Auflösung von 25 Mikron
- Hohe Maßhaltigkeit für präzise Passungen
- Gute mechanische Eigenschaften, vergleichbar mit Spritzgießen
- Die Stützen können nach dem Druck leicht abgenommen werden
Nachteile des SLA-Drucks
- Photopolymerharz ist teurer als FDM-Filament
- Nachbearbeitungen wie Spülstationen und UV-Härtungskammern erforderlich
- Harz ist empfindlich gegenüber Licht und Feuchtigkeit
- Begrenzte Auswahl an Materialien im Vergleich zu anderen Verfahren
Insgesamt bietet SLA ein attraktives Gleichgewicht zwischen Geschwindigkeit, Detailgenauigkeit und Festigkeit, was es zu einem vielseitigen Rapid-Prototyping-Verfahren macht.
Selektives Laser-Sintern (SLS)
Beim selektiven Lasersintern (SLS) wird ein Hochleistungslaser verwendet, um pulverförmiges Material Schicht für Schicht zu einem 3D-Objekt zu verschmelzen. Das Verfahren wurde in den 1980er Jahren von Carl Deckard an der Universität von Texas entwickelt.
So funktioniert der SLS-3D-Druck
SLS-Druck beinhaltet:
- Mit einer Walze wird eine dünne Schicht Pulver auf der Arbeitsfläche verteilt.
- Ein Laser sintert das Pulver selektiv und zeichnet den Schichtquerschnitt nach
- Die Bauplattform senkt sich, eine weitere Schicht Pulver wird aufgetragen
- Der Vorgang wiederholt sich, bis das Teil fertig ist.
- Überschüssiges Pulver unterstützt Überhänge beim Drucken
- Fertige Teile werden aus dem Pulverbett entnommen
In SLS-Maschinen kann eine Vielzahl von thermoplastischen und metallischen Pulvern verwendet werden. Der Laser schmilzt das Pulver knapp unter seinem Siedepunkt und lässt die Partikel fest miteinander verschmelzen.
Anwendungen des SLS-Drucks
Tabelle: SLS 3D-Druck – Verwendungen und Möglichkeiten
Attribut | Beschreibung |
---|---|
Kosten | Hohe Maschinenkosten, moderate Materialkosten |
Materialien | Nylon, TPU, PEEK, Aluminium, Stahl, Legierungen |
Genauigkeit | ±100 Mikrometer für Kunststoffe, ±50 μm für Metalle |
Geschwindigkeit | Mäßig, 5-7 in3/Stunde |
Größe des Teils | Mittel bis groß, bis zu 15 x 13 x 18 Zoll |
Wichtige Anwendungen | Funktionsprototypen, Teile für den Endgebrauch, Werkzeugbau |
Zu den wichtigsten Vorteilen von SLS gehören gute mechanische Eigenschaften, minimale Träger und der Druck mehrerer Materialien. Es wird häufig für funktionale Prototypen in der Automobil-, Luft- und Raumfahrt- und Medizinbranche eingesetzt.
Vorteile des SLS-Drucks
- Ausgezeichnete Festigkeit und thermische Eigenschaften mit Nylon 12-Pulver
- Keine Notwendigkeit für spezielle Unterstützungsstrukturen
- Große Teile in einem einzigen Arbeitsgang druckbar
- Vielfältige Materialien von Kunststoffen bis zu Verbundwerkstoffen
- Poröse Metallstrukturen möglich
Nachteile des SLS-Drucks
- Ein pulverförmiges Verfahren ist unordentlich und erfordert Handhabungssysteme
- Geringere Auflösung um 100 Mikrometer
- Poröse und körnige Oberfläche, die geglättet werden muss
- Begrenzte Anzahl von Metalllegierungen derzeit verfügbar
- Hohe Ausrüstungskosten, insbesondere bei Metallpulvern
Insgesamt können mit SLS hochfunktionale Prototypen und Endverbrauchsteile hergestellt werden, die von den meisten anderen 3D-Druckverfahren nicht erreicht werden. Weitere Fortschritte bei den Materialien werden die Möglichkeiten noch erweitern.
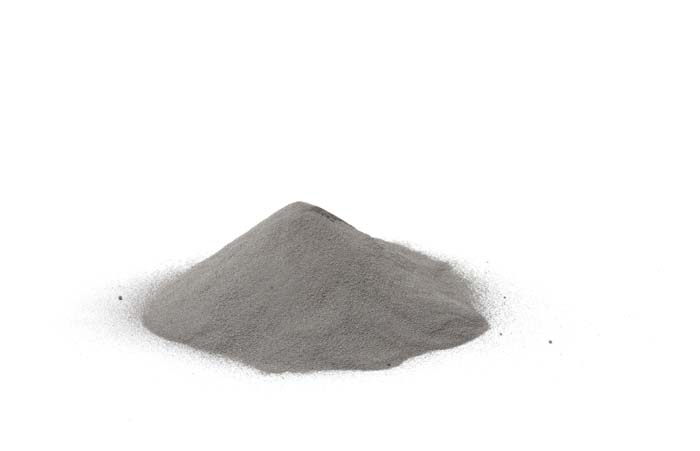
Multi Jet Fusion (MJF)
Das von HP entwickelte Multi Jet Fusion-Verfahren ist ein industrielles 3D-Druckverfahren, das für seine hohen Produktionsgeschwindigkeiten bekannt ist. Es verwendet einen Tintenstrahldruckkopf und Infrarotlaser, um Polymerpulver Schicht für Schicht zusammenzuschmelzen.
So funktioniert Multi Jet Fusion
Das MJF-Druckverfahren umfasst:
- Eine Schicht Pulver wird auf der Bauplattform verteilt
- Tintenstrahldruckköpfe tragen selektiv Fixier- und Detaillierungsmittel auf
- Infrarotlampen schmelzen und verschmelzen Pulver dort, wo Schmelzmittel aufgetragen wird
- Frische Pulverschicht darüber streuen, Vorgang wiederholen
- Ungeschmolzenes Pulver unterstützt Überhänge beim Druck
- Fertige Teile werden aus dem Pulverbett entnommen
MJF produziert Teile in hervorragender Qualität und in Farbe, bis zu 10 Mal schneller als SLS. Der schichtweise Ansatz ermöglicht auch funktionale Farbverläufe und flexible Eigenschaften.
Anwendungen des MJF-Drucks
Tabelle: Multi Jet Fusion-Fähigkeiten
Attribut | Beschreibung |
---|---|
Kosten | Hohe Maschinenkosten, moderate Materialkosten |
Materialien | Nylon 12, PBT, TPU-Kunststoffe |
Genauigkeit | Bis zu 80 Mikrometer |
Geschwindigkeit | Sehr schnell, 5-15 cm/Stunde |
Größe des Teils | Mittel bis groß, 380 x 284 x 380 mm Bauvolumen |
Wichtige Anwendungen | Teile für den Endverbrauch, kundenspezifische Massenfertigung, Werkzeugbau |
Die wichtigsten Stärken von MJF sind seine Geschwindigkeit, Qualität und Funktionalität. Er ist ideal für die Produktion von Kleinserien in der Automobil-, Industrie-, Medizin- und Konsumgüterindustrie.
Vorteile des MJF 3D-Drucks
- Extrem hohe Baugeschwindigkeit durch schichtweisen Ansatz
- Hervorragende mechanische Eigenschaften und Detailgenauigkeit
- Vollfarbdrucke in CMYK mit Voxelkontrolle möglich
- Funktionsgradienten und Durometer anpassbar
- Hohe Wiederverwendbarkeit von ungeschmolzenem Pulver
Beschränkungen des MJF
- Relativ neues Verfahren, Drucker kostet über 200 000 Dollar
- Begrenzte Materialverfügbarkeit über Nylon 12 hinaus
- Erfordert die Handhabung von ungesintertem Pulver
- Geringere Genauigkeit im Vergleich zu SLA oder PolyJet (~80 Mikrometer)
- Kleineres Bauvolumen als SLS-Systeme
Wenn die Technologie ausgereift ist, verspricht MJF eine produktionsreife Lösung für die additive Fertigung zu werden, die Geschwindigkeit, Qualität und Funktionalität vereint.
Elektronenstrahlschmelzen (EBM)
Beim Elektronenstrahlschmelzen (EBM) wird ein leistungsstarker Elektronenstrahl im Vakuum eingesetzt, um Metallpulver Schicht für Schicht zu vollständig dichten Teilen zu schmelzen und zu verschmelzen. Das Verfahren wurde in den 1990er Jahren in Schweden von Arcam AB entwickelt.
Wie EBM 3D-Druck funktioniert
Das EBM-Druckverfahren funktioniert wie folgt:
- Metallpulver wird in einem Vakuum gleichmäßig über eine Bauplattform verteilt
- Ein Elektronenstrahl schmilzt selektiv Pulver, um jede Schicht zu verfolgen
- Niedrigere Temperaturen erhitzen das Pulver bis knapp unter den Schmelzpunkt
- Die Bauplatte senkt sich und der Pulverstreuer trägt eine neue Schicht auf
- Nach der Fertigstellung werden die Teile abgekühlt, bevor sie aus der Maschine genommen werden.
Jedes leitfähige Metall kann mit EBM 3D-gedruckt werden, am häufigsten werden jedoch Titanlegierungen und Kobaltchrom verwendet. Die hohe Leistung sorgt für hervorragende Materialeigenschaften.
Anwendungen des EBM-Drucks
Tabelle: Elektronenstrahlschmelzen – Verwendungszwecke und Einsatzmöglichkeiten
Attribut | Beschreibung |
---|---|
Kosten | Sehr hohe Maschinenkosten, moderate Materialkosten |
Materialien | Titanlegierungen, rostfreier Stahl, Nickel, Kobalt-Chrom |
Genauigkeit | ±100 Mikrometer oder besser |
Geschwindigkeit | Mäßig, ca. 40-50 cm3/Std. |
Größe des Teils | Mittel bis groß, bis zu 275 x 275 x 380 mm |
Wichtige Anwendungen | Orthopädische Implantate, Teile für die Luft- und Raumfahrt, Automobilindustrie |
EBM stellt vollständig dichte Metallteile für Endanwendungen her, die hohe Festigkeit, Hitzebeständigkeit und Biokompatibilität erfordern. Die Luft- und Raumfahrtindustrie war ein früher Anwender.
Vorteile des EBM 3D-Drucks
- Vollständig geschmolzene Metalle mit hervorragenden Materialeigenschaften
- Gute Genauigkeit und Oberflächengüte
- Geringe innere Spannungen reduzieren den Verzug
- Hohe Strahlkraft führt zu einer guten Baugeschwindigkeit
- Ungenutztes Pulver kann wiederverwendet werden, was die Materialkosten minimiert
Nachteile des EBM-Drucks
- Sehr hohe Gerätekosten, die die Akzeptanz einschränken
- Begrenzt auf leitfähige Materialien, meist Metalle
- Nachbearbeitung wie Entfernen von Stützen erforderlich
- Mäßige Baugeschwindigkeiten, langsamer als andere Methoden
- Vakuumsysteme erhöhen die technische Komplexität
Insgesamt kann EBM komplexe Geometrien in Hochleistungsmetallen herstellen, die von der konventionellen Fertigung nicht erreicht werden. Sie wird in der Luft- und Raumfahrt, in der Medizin und in der Automobilindustrie weiter wachsen.
Herstellung laminierter Objekte (LOM)
Bei der Herstellung laminierter Objekte (Laminated Object Manufacturing, LOM) werden Materialschichten durch Hitze oder Klebstoff miteinander verbunden, um ein 3D-Objekt herzustellen. Das Verfahren wurde 1985 von Helisys Inc. eingeführt, das später von Cubic Technologies übernommen wurde.
So funktioniert der LOM 3D-Druck
Der LOM-Prozess funktioniert wie folgt:
- Materialplatten werden zu einem Block zusammengeklebt
- Eine beheizte Walze laminiert jedes neue Blatt auf den Stapel
- Ein Laser oder ein Messer schneidet die Umrisse der einzelnen Schichten in das Blech
- Überschüssiges Material bleibt an Ort und Stelle, um Überhänge zu stützen
- Nach Abschluss des Druckvorgangs wird das Teil vom zusätzlichen Material getrennt
Als Laminiermaterial können Papier, Kunststoff, Verbundstoffe und Metalle verwendet werden. LOM ist relativ kostengünstig und kann große geschichtete Objekte herstellen.
Anwendungen des LOM-Drucks
Tabelle: Herstellung laminierter Objekte – Attribute
Attribut | Beschreibung |
---|---|
Kosten | Niedrige Maschinenkosten, niedrige Materialkosten |
Materialien | Papier, Kunststoff, Verbundwerkstoffe, Bleche |
Genauigkeit | Mittel, etwa 200 Mikrometer |
Geschwindigkeit | Langsam, abhängig vom Schichtverbund |
Größe des Teils | Groß, bis zu 16 Fuß x unbegrenzte Länge |
Wichtige Anwendungen | Konzeptmodelle, Formstudien, Werkzeugbau |
Der Hauptvorteil von LOM ist die Möglichkeit, große geschichtete Objekte schnell und kostengünstig herzustellen. Es ist eine großartige Möglichkeit, ästhetische Prototypen und Modelle in Originalgröße zu bewerten, was mit anderen Methoden nicht möglich ist.
Vorteile des LOM-Drucks
- Niedrige Maschinen- und Materialkosten machen LOM zugänglich
- Das Bauvolumen ist theoretisch unbegrenzt
- Minimaler Materialabfall oder Nachbearbeitung
- Erfordert keine Stützstrukturen
- Einfache Integration von Holz, Papier und Verbundwerkstoffen
Nachteile des LOM
- Geringe Genauigkeit um 200 Mikrometer
- Sichtbare Schichtlinien beeinträchtigen die Oberflächengüte
- Mühsame Endtrennung des gedruckten Teils
- Begrenzte Materialien und Materialeigenschaften
- Das Verkleben von Schichten kann zeitaufwändig sein
Die Qualität ist zwar nicht für Funktionsteile geeignet, aber für ästhetische Modelle in Originalgröße zu verbraucherfreundlichen Preisen ist LOM nach wie vor eine überzeugende Technologie.
Gerichtete Energieabscheidung (DED)
Bei der gerichteten Energieabscheidung (DED) wird eine fokussierte Wärmequelle wie ein Laser, ein Elektronenstrahl oder ein Plasmalichtbogen verwendet, um Material zu schmelzen und gleichzeitig abzuscheiden. Es handelt sich um ein additives Fertigungsverfahren, mit dem große Metallteile hergestellt werden können.
So funktioniert der DED 3D-Druck
Der DED wendet das folgende allgemeine Verfahren an:
- Eine Düse trägt Metallpulver an einer bestimmten Stelle auf
- Eine Energiequelle wie ein Laser schmilzt das Pulver und bildet eine metallurgische Verbindung.
- Das Teil wird Schicht für Schicht durch Auftragen und Schmelzen von Material aufgebaut
- DED-Systeme werden in der Regel an mehrachsigen Armen montiert, um eine vollständige Abdeckung zu gewährleisten.
- Manipulatoren drehen und positionieren das Teil, während es sich aufbaut
- Während des Drucks sind nur minimale Stützstrukturen erforderlich
DED kann Merkmale auf vorhandene Komponenten wie Werkzeugmaschinen oder Motorblöcke drucken. Dies ermöglicht eine schnelle Reparatur, Verbesserung und Änderung von Metallteilen.
Anwendungen des DED-Drucks
Tabelle: Gerichtete Energieabscheidung – Anwendungen
Attribut | Beschreibung |
---|---|
Kosten | Hohe Ausrüstungskosten, hohe Materialkosten |
Materialien | Rostfreier Stahl, Titan, Inconel, Kobaltlegierungen |
Genauigkeit | ±100 Mikrometer |
Geschwindigkeit | Hohe Ablagerungsrate von 0,1-0,5 kg/Stunde |
Größe des Teils | Sehr groß, unbegrenzt, da sich das Gerät bewegt |
Wichtige Anwendungen | Metallbeschichtung, Reparatur, Werkzeugbau, Luft- und Raumfahrt, Verteidigung |
Der Hauptvorteil von DED ist die Möglichkeit, große Metallteile in praktisch unbegrenzter Größe zu fertigen und bestehende Anlagen zu modifizieren.
Vorteile des DED-Drucks
- Kann extragroße Metallteile, gemessen in Fuß, herstellen
- Hochgradig mobil, Fähigkeiten werden über einen mehrachsigen Arm zum Objekt gebracht
- Schneller Durchlauf gemessen in Stunden statt Wochen
- Hinzufügen von Merkmalen zu vorhandenen Metallteilen möglich
- Geringerer Materialabfall im Vergleich zur maschinellen Bearbeitung
Nachteile des DED-Drucks
- Sehr hohe Ausrüstungskosten in Millionenhöhe
- Langsame Zykluszeiten, gemessen in Stunden
- Begrenzte Genauigkeit und Oberflächengüte
- Erfordert umfangreiche Bedienerschulung
- Nachbearbeitung wie z. B. maschinelle Bearbeitung zur Fertigstellung der Teile erforderlich
DED eignet sich besser für das schnelle Hinzufügen von Metallmaterial als für die Produktion von Fertigteilen. Mit der Verbesserung der Technologie verspricht sie, die Reparatur und Modifikation vor Ort in vielen Branchen zu verändern.
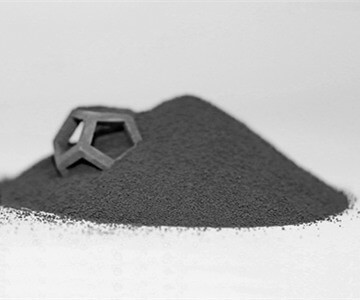
Wie man eine 3D-Drucktechnologie auswählt
Wie wählt man bei so vielen 3D-Druckverfahren die richtige Methode für eine Anwendung aus?
Schritt 1: Verstehen der Designanforderungen
Analysieren Sie zunächst die wichtigsten Anforderungen Ihrer Anwendung:
- Welche Zielmaterialien werden benötigt: Kunststoff, Metall, Polymer?
- Welche Genauigkeit und Toleranzen werden erwartet?
- Wie groß ist die gewünschte Teilegröße und das gewünschte Bauvolumen?
- Soll die Oberfläche glatt oder rau sein?
- Benötigt das Teil bestimmte mechanische Eigenschaften? Festigkeit, Flexibilität, Härte?
- Welche Menge wird benötigt: einige wenige Prototypen oder größere Produktionsserien?
- Wie schnell muss das Projekt abgeschlossen werden?
Dokumentieren Sie die Eigenschaften, die Sie für Ihre Anwendung benötigen. Dies bildet die Grundlage für die Auswahl eines 3D-Druckverfahrens.
Schritt 2: Zuordnung von Anforderungen zu Drucktechnologien
Als Nächstes ordnen Sie Ihre Anforderungen den Fähigkeiten der einzelnen 3D-Drucktechnologien zu:
- Wenn Metalle erforderlich sind, sollten Sie DMLS, SLS oder EBM in Betracht ziehen.
- Für eine glatte Oberfläche kommen SLA, DMLS, PolyJet in Frage.
- FDM kann gute Festigkeit und funktionales Prototyping bieten
- LOM ermöglicht das Drucken großer Hohlkörper
- SLA, SLS, Material Jetting ermöglichen Multimaterialteile
- Binder Jetting ist optimal für eine hohe Mischgutproduktion
Erstellen Sie eine Tabelle, in der Sie die Anforderungen den möglichen 3D-Druckverfahren zuordnen, um die Übereinstimmung zu visualisieren.
Schritt 3: Rangfolge nach Wichtigkeit und Kompatibilität
Ordnen Sie Ihre Anforderungen nach Prioritäten, vom absolut Notwendigen bis zum "Nice-to-have".
Bewerten Sie dann jede Technologie auf einer Skala von 1 bis 5 danach, wie gut sie Ihren Prioritäten entspricht.
So erhalten Sie eine objektive Bewertung, mit der Sie Prozesse vergleichen können. Die beste Übereinstimmung bringt die wichtigsten Anforderungen und Fähigkeiten ins Gleichgewicht.
Schritt 4: Bewertung von Kosten, Vorlaufzeit und Erfahrung
Berücksichtigen Sie auch praktische Erwägungen:
- Über welche Erfahrungen und Fähigkeiten im 3D-Druck verfügen Sie? Ist eine Schulung erforderlich?
- Welche Geräte-, Betriebs- und Materialkosten sind für Ihr Budget sinnvoll?
- Können Sie die Nachbearbeitungsanforderungen der Methode bewältigen?
- Welcher Termin ist für Ihr Projekt vorgesehen? Passt die Ausführungsgeschwindigkeit zu Ihrem Zeitplan?
Wägen Sie die qualitativen und quantitativen Faktoren zusammen ab, um die optimale Technologie zu wählen. Nutzen Sie bei Bedarf 3D-Druckdienste, um das Risiko einer Einführung zu verringern.
Schritt 5: Validierung durch Prototyping
Vor der endgültigen Entscheidung sollten Sie einige Testprototypen für die in die engere Wahl gezogenen Technologien erstellen, um die Kompatibilität zu prüfen.
Prüfen Sie, ob die Genauigkeit, das Finish und die mechanische Leistung den erwarteten Ergebnissen entsprechen, und wiederholen Sie sie bei Bedarf.
Das Prototyping schützt vor Überraschungen und hilft, das beste 3D-Druckverfahren für eine Anwendung zu finden.
Die Befolgung dieser strukturierten Kriterien stellt sicher, dass Ihre Investitionen in den 3D-Druck auf maximale Wertschöpfung und Produktivitätssteigerung ausgerichtet sind.
Die Zukunft des 3D-Drucks
Die 3D-Drucktechnologie hat seit ihren Anfängen vor über 30 Jahren rasante Fortschritte gemacht. Prognosen zufolge wird der Markt weiterhin um durchschnittlich 25 % pro Jahr wachsen und bis 2024 weltweit die Marke von 34 Mrd. USD übersteigen.
Mehrere Trends treiben die Einführung in allen Branchen voran:
Fortschritte bei den Materialien
Neue 3D-druckbare Fotopolymere, Verbundwerkstoffe, flexible Filamente und Metalllegierungen erweitern die Möglichkeiten für die Produktion von Hochleistungsbauteilen.
Hybride Fertigung
Die Kombination von 3D-Druck mit maschineller Bearbeitung, Robotik und anderen Verfahren auf einer einzigen Plattform erhöht die Automatisierung.
Massenanpassung
Der agile 3D-Druck ermöglicht maßgeschneiderte Endprodukte in großem Maßstab und nicht nur die Herstellung von Prototypen.
Metalle Wachstum
Die Nachfrage nach 3D-Metalldruck steigt jährlich um mehr als 50 % in den Bereichen Luft- und Raumfahrt, Zahnmedizin und Medizin.
Verteilte Fertigung
3D-Druckanlagen, die näher am Ort der Nutzung angesiedelt sind, reduzieren die Logistikkosten und die Umweltbelastung.
Die additive Fertigung wird in den kommenden zehn Jahren Design, Prototyping, Produktion und Geschäftsmodelle in der Fertigungs-, Gesundheits-, Konsumgüter- und Bauindustrie verändern.
Wichtige Erkenntnisse und Zusammenfassung
Die wichtigsten Erkenntnisse aus diesem Überblick über 3D-Drucktechnologien:
- Es gibt zahlreiche 3D-Druckverfahren, jedes mit einzigartigen Fähigkeiten
- Die Auswahl der optimalen Methode hängt von Faktoren wie Zielmaterial, Genauigkeit, Teilegröße, Produktionsmengen usw. ab.
- FDM ist die erschwinglichste und FFF die meistgenutzte Technologie
- SLA bietet hervorragende Oberflächengüte und feine Details
- SLS ermöglicht funktionale Prototypen mit guten Eigenschaften
- MJF kombiniert Geschwindigkeit und Qualität für die Kleinserienproduktion
- EBM und DED werden für den 3D-Druck großer Metallteile verwendet
- Hybride Fertigung nutzt den 3D-Druck mit anderen Verfahren für maximale Flexibilität
- Fortschritte bei den Materialien und Methoden werden die Anwendungen weiter ausweiten
Zusammenfassend lässt sich sagen, dass das Verständnis der Prinzipien hinter jeder additiven Fertigungstechnologie die Identifizierung des besten Verfahrens für eine bestimmte Produktanforderung ermöglicht. Das Prototyping der wichtigsten Optionen ermöglicht eine weitere Validierung, um das Risiko zu minimieren. Aufgrund seiner Vielseitigkeit, Produktivität und des Potenzials zur Abfallreduzierung wird der 3D-Druck in Zukunft in allen Branchen eine wichtige Fertigungstechnologie sein.
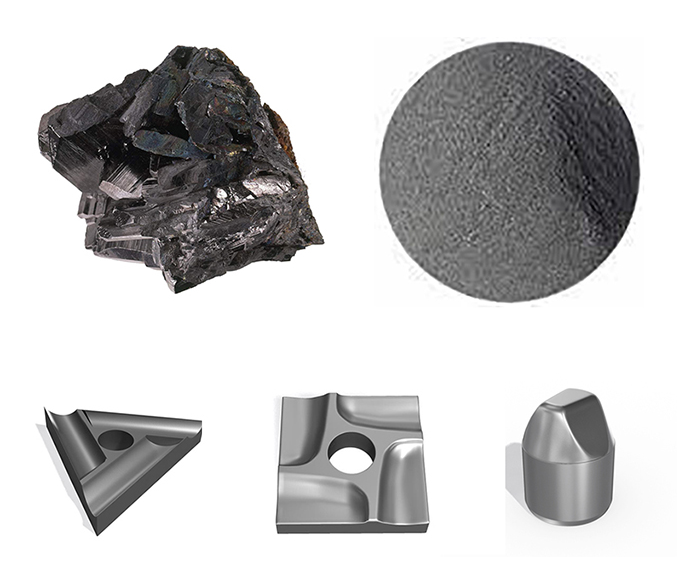
FAQ
Hier finden Sie Antworten auf einige häufig gestellte Fragen zu 3D-Drucktechnologien:
F: Welche 3D-Drucktechnologie ist die günstigste?
A: Fused Deposition Modeling (FDM) ist die günstigste 3D-Drucktechnologie. Sowohl die Geräte- als auch die Materialkosten sind bei FDM am niedrigsten, wenn gängige Thermoplaste wie PLA und ABS verwendet werden.
F: Welche 3D-Druckmethode hat die beste Genauigkeit?
A: Die Stereolithografie (SLA) bietet die höchste Genauigkeit aller gängigen 3D-Drucktechnologien, die bei den meisten Fotopolymeren zwischen 25 und 100 Mikrometern liegt. Das macht sie ideal für Anwendungen, die enge Toleranzen erfordern.
F: Welches 3D-Druckverfahren ermöglicht mehrfarbige Drucke?
A: Pulverbettfusionsverfahren wie Full Color Binder Jetting und Multi Jet Fusion (MJF) unterstützen mehrfarbige Drucke durch präzise Steuerung des Materialauftrags. Thermoplastische Extrusionsverfahren wie FDM ermöglichen auch Farbmischungen mit mehreren Druckköpfen.
F: Welche Metalle können in 3D gedruckt werden?
A: Titanlegierungen, rostfreier Stahl, Kobalt-Chrom, Aluminium und Nickellegierungen sind die gebräuchlichsten Metalle, die mit Hilfe von Pulverbett- oder gerichteten Energiedepositionsverfahren 3D-gedruckt werden können.
F: Welche 3D-Druckmethode eignet sich am besten für Gewebe oder flexible Materialien?
A: Fused Deposition Modeling mit flexiblem TPU-Filament ist der einfachste Weg, um flexibles Material mit elastischen Eigenschaften ähnlich wie Gewebe und Gummi in 3D zu drucken. Mit dem SLS-Druck können auch flexible Teile aus pulverförmigem Polyurethan hergestellt werden.
F: Wie groß kann ein 3D-gedrucktes Teil sein?
A: Großformatige 3D-Drucker für das Bauwesen können Teile mit einer Länge von über 50 Fuß herstellen. Für die meisten industriellen Systeme ist die maximale Teilegröße jedoch begrenzt:
- SLS: 15 x 13 x 18 Zoll
- SLA: 1 Kubikfuß
- FDM: 12 x 12 x 12 Zoll
- DED: Praktisch unbegrenzte Größe
F: Welches 3D-Druckverfahren ist das schnellste?
A: In Bezug auf die Fertigungsgeschwindigkeit kann Multi Jet Fusion von HP Geschwindigkeiten erreichen, die bis zu 10-100 Mal schneller sind als SLS- und SLA-Verfahren. DED-Verfahren haben ebenfalls hohe Abscheideraten von bis zu 0,5 kg/Stunde, erfordern aber mehr Durchgänge, um ein komplettes Teil herzustellen.
F: Welche 3D-Druckverfahren werden für die Massenproduktion verwendet?
A: Binder Jetting und Material Jetting eignen sich am besten für die Großserienproduktion. FDM, SLS und MJF eignen sich für die Herstellung von Kleinserien bis zu 10.000 Stück. DED ermöglicht die Herstellung großer Mengen von Metallteilen.
F: Wie genau ist der 3D-Druck von Metall?
A: Durch das Schmelzen von Metallen im Pulverbett kann eine Genauigkeit von etwa 50 bis 100 Mikrometern erreicht werden, wobei die Präzision durch maschinelle Bearbeitung und Endbearbeitung weiter erhöht werden kann. Das Kaltgasspritzen von DED hat eine geringere Genauigkeit von etwa 200 Mikrometern.