Das Metall-Spritzgießen (MIM) ist ein Metallbearbeitungsverfahren zur Herstellung kleiner, komplexer Teile aus Metallpulver und Kunststoff. MIM kombiniert die Designflexibilität des Kunststoffspritzgießens mit der Festigkeit und Integrität von maschinell bearbeiteten Metallen. Es ermöglicht die kostengünstige Herstellung von Bauteilen mit Abmessungen von 1 Gramm bis 500 Gramm.
Die MIM-Verfahren produziert Teile mit ausgezeichneten mechanischen Eigenschaften, Präzisionstoleranzen und glatten Oberflächenoberflächen. Dadurch eignet sich MIM für die Herstellung kleiner, komplexer, netzförmiger Metallkomponenten in großen Mengen für Branchen wie Automobilbau, Medizintechnik, Luft- und Raumfahrt, Elektronik und andere.
Dieser Leitfaden bietet einen vollständigen Überblick über das MIM-Verfahren, seine Anwendungen, Vorteile, Designüberlegungen, Ausrüstung, Materialien, Nachbearbeitung, Qualitätskontrolle und Kostenanalyse. Er enthält detaillierte Tabellen und Vergleiche, die Ingenieuren, Produktdesignern und Beschaffungsmanagern helfen, das MIM-Verfahren kennenzulernen und zu bewerten.
Überblick über den MIM-Prozess
Beim Metall-Spritzgießen werden Kunststoff-Spritzgusstechniken mit pulvermetallurgischen Verfahren kombiniert. Die grundlegenden Schritte im MIM-Prozess sind:
- Mischen: Mischen von feinem Metallpulver mit einem Kunststoffbindemittel zur Herstellung eines homogenen Ausgangsmaterials
- Spritzgießen: Erhitzen und Einspritzen des Ausgangsmaterials in eine Form, um ein geformtes Grünteil herzustellen
- Entbinden: Entfernen des Kunststoffbindemittels aus dem geformten Grünteil durch Lösungsmittel oder thermische Verfahren
- Sintern: Erhitzen des entbinderten Teils bis knapp unter den Schmelzpunkt des Pulvers, um das Teil durch atomare Diffusion zu verdichten und ein festes Metallteil zu bilden.
In der folgenden Tabelle sind die wichtigsten Phasen des MIM-Prozesses zusammengefasst:
Stage | Beschreibung |
---|---|
Mischen | Mischen von feinem Metallpulver mit Bindemitteln zu einem homogenen Ausgangsmaterial |
Spritzgießen | Erhitzen und Einspritzen von Rohmaterial in eine Form zur Herstellung von Grünteilen |
Entbinden | Entfernung des Bindemittels durch Lösungsmittel oder thermische Verfahren |
Sintern | Erhitzen des entbinderten Teils zur Verdichtung des Pulvers und zum Formen des Metallteils |
Mit dem MIM-Verfahren werden gleichbleibend hochwertige Metallteile hergestellt, die sich für die Großserienfertigung eignen. Das Verfahren ist in hohem Maße wiederholbar und ermöglicht die Herstellung komplexer Geometrien mit engen Toleranzen, die mit anderen Fertigungsverfahren nicht möglich sind.
Anwendungen und industrielle Nutzung von MIM-Teilen
MIM wird in vielen Branchen zur Herstellung kleiner, komplexer, netzförmiger Metallteile mit engen Toleranzen eingesetzt.
In der folgenden Tabelle sind die wichtigsten Anwendungsbereiche und Beispiele für durch MIM hergestellte Teile aufgeführt:
Industrie | Anwendungsbeispiele |
---|---|
Automobilindustrie | Zahnräder, Zahnkränze, Kipphebel, Pleuelstangen |
Luft- und Raumfahrt | Turbinenschaufeln, Laufräder, Düsen, Ventile |
Medizinische | Kieferorthopädische Brackets, chirurgische Instrumente, Implantate |
Elektronik | Steckverbinder, Mikrozahnräder, Siebe, Druckerdüsen |
Feuerwaffen | Abzüge, Hämmer, Sicherungen, Ejektoren |
Uhren | Zahnräder, Triebe, Uhrzeiger |
MIM ermöglicht die Herstellung von kleinen Präzisionsteilen mit komplexen Geometrien, die andernfalls eine umfangreiche maschinelle Bearbeitung oder andere sekundäre Arbeitsgänge erfordern würden. Es bietet Designfreiheit, Teilekonsolidierung und Gewichtsreduzierung im Vergleich zu Fertigungsalternativen.
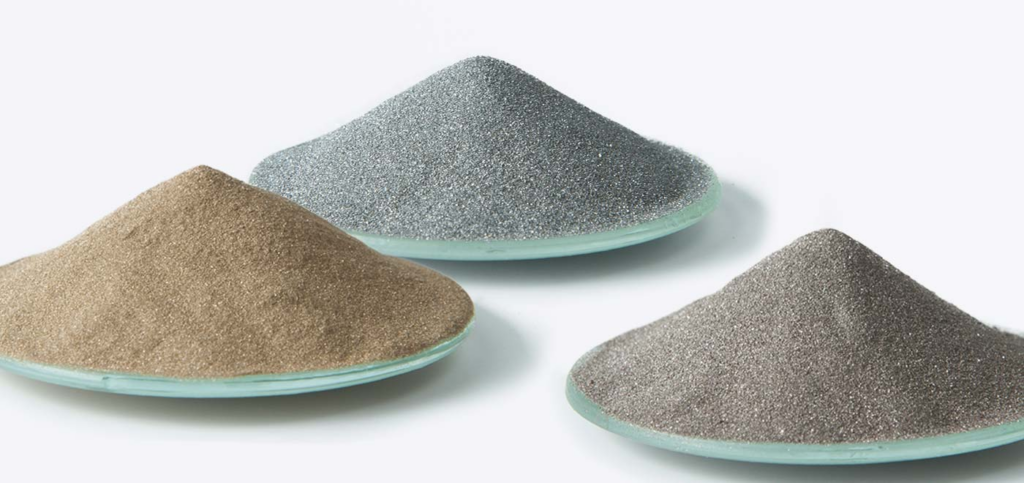
Vorteile und Nutzen von MIM
MIM bietet mehrere Vorteile gegenüber anderen Verfahren zur Herstellung kleiner Metallteile:
Gestaltungsfreiheit
- Es können komplexe 3D-Geometrien und Formen geformt werden, die mit anderen Methoden schwierig oder unmöglich sind.
- Komplizierte Merkmale wie Gewinde, Hohlräume und Löcher lassen sich leicht in MIM-Designs integrieren.
- Ermöglicht die Konsolidierung von Teilen und die Reduzierung der Anzahl von Baugruppen gegenüber der Bearbeitung mehrerer Komponenten.
Präzision und Toleranzen
- Mit MIM können gleichbleibende Maßgenauigkeit und Toleranzen bis zu ±0,1 % eingehalten werden.
- Feine Details mit guten Oberflächengüten bis hinunter zu 0,5 μm Ra sind realisierbar.
Materialeigenschaften
- Gesinterte MIM-Teile erreichen in der Regel 95-99 % der Dichten von Knetmetallen.
- Eine breite Palette von Materialien wie Edelstahl, Werkzeugstahl, Titan- und Wolframlegierungen kann verwendet werden.
- Hervorragende mechanische Eigenschaften mit der Steifigkeit, Festigkeit, Härte und Verschleißfestigkeit von gegossenen Metallen.
Produktivität und Kosten
- Hohe Produktionsraten mit schnellen Zykluszeiten durch MIM möglich.
- Niedrigere Teilekosten als bei der CNC-Bearbeitung bei mittleren und hohen Stückzahlen.
- Geringere Kosten als beim Feinguss für komplexe, mehrteilige Konstruktionen.
- Eliminiert sekundäre Bearbeitungsvorgänge, die für gefertigte Metallkomponenten erforderlich sind.
Nachhaltigkeit
- Minimaler Materialabfall, da bei MIM eine nahezu endkonturnahe Verarbeitung erfolgt.
- Pulvermetallurgisches Verfahren mit geringerem Energieverbrauch als Metallbearbeitung oder Gießen.
- Ermöglicht Leichtbau durch Optimierung der Geometrien, was den ökologischen Fußabdruck verringert.
Die folgende Tabelle fasst die wichtigsten Vorteile von MIM zusammen und vergleicht sie mit anderen Verfahren:
Vorteil | Vergleich mit anderen Prozessen |
---|---|
Gestaltungsfreiheit | Mehr Flexibilität als bei maschineller Bearbeitung oder Metallguss |
Präzision | Viel höher als bei Sand- oder Druckguss |
Materialeigenschaften | Ansätze für Knetmetalle im Gegensatz zur Pulvermetallurgie |
Produktivität | Höhere Stückzahlen als bei der CNC-Bearbeitung |
Kosten-Wirksamkeit | Geringere Kosten als CNC-Bearbeitung oder Feinguss für mittlere und größere Mengen |
Nachhaltigkeit | Weniger Abfall als bei subtraktiven Verfahren wie der CNC-Bearbeitung |
MIM kombiniert die geometrische Freiheit des Kunststoffspritzgießens mit Materialeigenschaften, die denen von Vollmetall nahe kommen. Dies ermöglicht es Produktdesignern, Baugruppen zu konsolidieren, Komponenten zu optimieren und komplizierte, hochwertige Metallteile zu wettbewerbsfähigen Kosten herzustellen.
Konstruktionsüberlegungen für MIM-Teile
Um die Vorteile des MIM-Verfahrens voll ausschöpfen zu können, ist die richtige Konstruktion der Teile entscheidend. Einige wichtige Designüberlegungen umfassen:
Wandstärken – Empfohlen werden mäßige Wandstärken zwischen 0,8 mm und 5 mm. Übermäßig dicke oder dünne Abschnitte können zu Defekten führen.
Toleranzen - Präzisionstoleranzen von ±0,1 % der Abmessungen sind möglich, wobei jedoch die Sinterschrumpfung zu berücksichtigen ist.
Oberflächenbeschaffenheit - Feine Oberflächengüten unter 1 μm Ra sind je nach Werkzeugoberfläche, Geometrien und Nachbearbeitungsvorgängen möglich.
Geometrie Vermeidung allzu filigraner Geometrien und Aufrechterhaltung der strukturellen Integrität wichtig, um Defekte zu vermeiden. Minimale Entformungsschrägen über 1-2° bevorzugt.
Eigenschaften - Löcher bis zu einem Durchmesser von 0,5 mm, Gewinde und komplexe interne Merkmale können in das MIM-Design integriert werden.
Größe des Teils - Kleinere Bauteile zwischen 0,5 und 500 Gramm sind ideal für die MIM-Verarbeitung. Größere Teile erfordern möglicherweise eine CNC-Bearbeitung.
Assembly - Design für die Teilekonsolidierung durch Kombination komplexer Komponenten und Baugruppen zu einzelnen MIM-Teilen.
Die richtige Konstruktion von MIM-Komponenten optimiert die Herstellbarkeit, minimiert Fehler und nutzt die wichtigsten Vorteile des MIM-Verfahrens. Die Beratung mit MIM-Anbietern während der Konstruktionsphase wird dringend empfohlen.
MIM-Ausrüstung und -Werkzeuge
Für die Aufbereitung des Rohmaterials, die Formgebung, das Entbindern und das Sintern des MIM-Prozesses werden spezielle Anlagen eingesetzt:
Mischen und Aufbereitung von Rohstoffen
- Mischer – Hochintensitätsmischer für die Homogenität von Rohstoffen
- Mühlen – Korbmühlen oder Walzenmühlen zur Zerkleinerung feiner Partikel
- Temperaturregler – Zur Regelung der Temperaturen von Rohstoffen
- Entgasung – Vakuumeinheiten zum Entfernen eingeschlossener Luftblasen
Spritzgießen
- Spritzgießmaschinen – Modifizierte Maschinen zur Verarbeitung von MIM-Rohstoffen
- Formen – Normalerweise aus Werkzeug-/Edelstahl, der für die Sinterung wärmebehandelt wurde
- Formtemperaturregler – Zur Regelung der Formtemperaturen während der Formgebung
Entbinden
- Lösemittel-Entbinderungskammern – Für die Lösemittelextraktion von Bindemitteln
- Dampfentbinderungsautoklaven – Für Dampfentbinderungsprozesse
- Thermische Entbinderungsöfen – Zur Entfernung von Bindemitteln durch thermische Prozesse
Sintern
- Sinteröfen – Öfen auf Vakuum-, Wasserstoff- oder Stickstoffbasis
- Atmosphärenkontrollsysteme – Zur Regelung von Ofenatmosphären
- Temperaturprofilsteuerung – Für die Ausführung optimierter Sinterzyklen
Die richtige Einstellung und Kalibrierung der MIM-Ausrüstung ist entscheidend für fehlerfreie, qualitativ hochwertige Bauteile. Die Spritzgießphase erfordert die speziellste Ausrüstung wie Hochtemperaturformen.
MIM-Materialien
Eine breite Palette von Metallen, Legierungen und Keramiken kann mit der MIM-Technologie verarbeitet werden. Einige der gängigen MIM-Materialien sind:
Metals
- Rostfreie Stähle (316L, 17-4PH, 410)
- Werkzeugstähle (H13, P20, D2)
- Niedrig legierte Stähle (4140)
- Magnetische Legierungen
- Kupfer-Legierungen
- Titan-Legierungen
- Wolfram-Schwermetall-Legierungen
Keramik
- Tonerde
- Zirkoniumdioxid
- Siliziumnitrid
- Hartmetalle
Die Auswahl des Materials hängt von Faktoren wie Sintertemperaturen, Kosten, mechanischen und physikalischen Eigenschaften sowie den Anforderungen an die Weiterverarbeitung ab. Edelstahl 316L ist aufgrund seiner hervorragenden Sinterfähigkeit das am häufigsten verwendete MIM-Material.
Die nachstehende Tabelle zeigt gängige MIM-Materialien und ihre typischen Anwendungen:
Material | Anwendungen |
---|---|
Rostfreier Stahl 316L | Chirurgische Instrumente, Pumpen, Ventile |
Werkzeugschaft H13 | Spritzgießen, Extrusion, Düsen |
Titanium Ti-6Al-4V | Luft- und Raumfahrt, medizinische Implantate |
Wolfram-Schwermetall-Legierungen | Strahlungsabschirmung, Schwingungsdämpfung |
Kupfer-Legierungen | Elektrische Kontakte, Wärmemanagement |
Keramik | Schneidwerkzeuge, Verschleißteile, Ballistik |
MIM ermöglicht die Verwendung von Hochleistungswerkstoffen wie Titan und Werkzeugstahllegierungen in kleinen, komplexen Bauteilkonstruktionen. Es erweitert die Konstruktionsmöglichkeiten für medizinische, Luft- und Raumfahrt-, Automobil- und Industrieanwendungen.
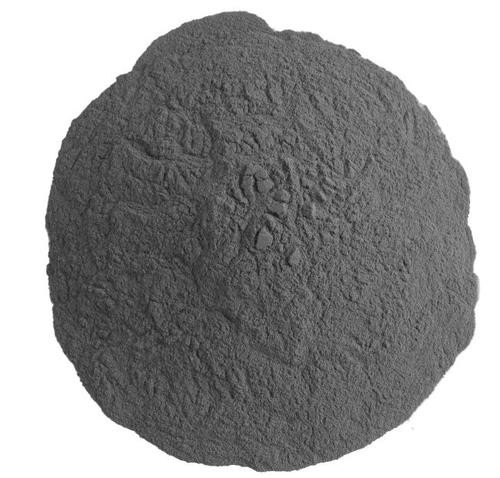
Nachbearbeitungsvorgänge
Nach dem MIM-Sintern sind häufig sekundäre Verarbeitungsschritte erforderlich, um das endgültige Teil zu erhalten:
- Glühen – Spannungsabbauende Wärmebehandlung
- Aushärtung – Thermisches Härteverfahren wie Bainitisieren
- Bearbeitung – CNC-Bearbeitungsmerkmale wie präzise Bohrungsdurchmesser
- Beitritt zu – Laserschweißen, Löten oder Epoxidkleben von Teilkomponenten
- Fertigstellung – Beschichtung, Lackierung, Passivierung oder andere Oberflächenbehandlung
Die nachstehende Tabelle gibt einen Überblick über gängige Post-MIM-Prozesse und deren Zweck:
Post-Process | Zweck |
---|---|
Glühen | Spannungsabbau, Duktilität |
Aushärtung | Verbesserung von Härte und Festigkeit |
Bearbeitung | Kritische Abmessungen und Passungen |
Beitritt zu | Montage von mehrteiligen Produkten |
Fertigstellung | Erscheinungsbild, Korrosionsbeständigkeit |
Die Nachbearbeitung erweitert die Möglichkeiten der Eigenschaftsverbesserung und der Präzisionsbearbeitung. Dadurch wird die Anwendbarkeit von MIM in anspruchsvollen Anwendungen weiter ausgebaut.
Qualitätskontrolle und Inspektion
Eine gleichbleibende Qualität und Maßkontrolle ist für MIM-Komponenten von entscheidender Bedeutung. Typische Tests zur Qualitätskontrolle umfassen:
- Chemische Analyse – Zur Zusammensetzung mittels optischer Emissions- oder Röntgenfluoreszenzspektroskopie
- Dichtemessungen – Archimedes-Methode oder Gaspyknometrie zur Bestimmung der Sinterdichte
- Mechanische Prüfungen – Härte-, Zug- und Ermüdungseigenschaften gemäß ASTM-Normen
- Mikroskopie – Für Mikrostruktur-, Porositäts-, Korngrößen- und Defektanalysen
- Dimensionsanalyse – Optisches oder CT-Scannen für Dimensionen und GD&T-Konformität
- Oberflächenanalyse – Rauhigkeits-, Korrosions- und Beschichtungstests, soweit zutreffend
Die folgende Tabelle gibt einen Überblick über die wichtigsten Qualitätsprüfungen, die in den verschiedenen Phasen der MIM-Verarbeitung durchgeführt werden:
Stage | Typische Qualitätstests |
---|---|
Ausgangsstoff | Viskosität, Drehmoment, Feuchtigkeit |
Grüner Teil | Abmessungen, Fehlerprüfung |
Entbinden | Gewichtsverlust, Rückstände |
Sintern | Dichte, chemische Tests |
Fertigstellung | Abmessungen, Mikroskopie, mechanische Eigenschaften |
Eine umfassende Qualitätskontrolle und Inspektion auf allen Stufen des MIM-Verfahrens ist erforderlich, um fehlerfreie Bauteile zu erhalten, die den Anwendungsanforderungen entsprechen.
Kostenanalyse
Die folgenden Faktoren bestimmen die Wirtschaftlichkeit des MIM-Verfahrens:
- Werkzeugbau - Die Herstellung von Werkzeugen verursacht je nach Teilegeometrie hohe Anschaffungskosten. Mehrere Kavitäten in Werkzeugen verteilen die Kosten auf höhere Stückzahlen.
- Einrichten - Erhebliche Kosten für anfängliche Maschineneinstellungen und Prozessentwicklung.
- Material – Metallpulver machen 10-15% der Gesamtkosten eines Teils aus. Hoch bei teuren Materialien wie Titanlegierungen.
- Arbeit - Einige Fachkräfte erforderlich, aber weniger als bei der CNC-Bearbeitung. Bei hohen Stückzahlen geringer.
- Sekundäre Verarbeitung - Kann die Kosten erheblich erhöhen, wenn umfangreiche Bearbeitungen oder Nacharbeiten erforderlich sind.
- Volumen Ideal für mittlere bis hohe Produktionsvolumen von 10.000 bis zu Millionen von Teilen. Bietet einen optimalen Kostenvorteil gegenüber anderen Verfahren in diesem Bereich.
Die folgende Tabelle gibt einen Überblick über die indikativen Kostenfaktoren bei der Herstellung von MIM:
MIM-Kostenkomponente | Einzelheiten |
---|---|
Werkzeugbau | $5.000 bis $100.000+ je nach Komplexität des Teils |
Einrichten | $10.000 bis $50.000 für die Verfahrensentwicklung |
Materialien | 10-15% der Teilekosten, bei teuren Legierungen höher |
Arbeit | Geringerer Beitrag gegenüber CNC-Bearbeitung |
Sekundäre Verarbeitung | $2 bis $20 pro Teil, je nach Tätigkeit |
Volumen | Ideal für mehr als 10.000 Teile, kostengünstiger als Alternativen |
MIM bietet einen Kostenvorteil gegenüber der maschinellen Bearbeitung und dem Gießen bei mittleren bis hohen Produktionsmengen, sofern die Nachbearbeitung minimal ist. Das Verfahren bietet die größten wirtschaftlichen Vorteile für komplexe, mehrteilige Konstruktionen, die in einem einzigen MIM-Teil zusammengefasst sind.
Auswahl eines MIM-Lieferanten oder -Partners
Die Auswahl eines kompetenten MIM-Lieferanten ist der Schlüssel zu einer kosteneffizienten Produktion von qualitativ hochwertigen Bauteilen. Einige Kriterien für die Bewertung von MIM-Lieferanten:
- Erleben Sie – Anzahl der Jahre im Geschäft und Erfahrung mit MIM. Langjährige Akteure sind in der Regel zuverlässiger.
- Materialien -Vielfältiges Materialangebot, einschließlich der benötigten Schlüssellegierungen. Nanopulver-Fähigkeiten verbessern die Eigenschaften.
- Qualität - Robustes Qualitätsprogramm und Zertifizierungen wie ISO 9001 und ISO 13485. Nachweis von Prozesskontrollen.
- Werkzeugtechnische Fähigkeiten - Die Bereitstellung sämtlicher Werkzeuge im eigenen Haus ermöglicht eine bessere Kostenintegration und reduziert Probleme.
- Sekundäre Verarbeitung - Die Verfügbarkeit von ergänzenden Verfahren wie CNC-Bearbeitung und -Endbearbeitung verbessert den Komfort.
- Prototyping – Die Fähigkeit zum Rapid Prototyping im MIM-Verfahren reduziert Vorlaufzeit und Kosten.
- R&D-Kompetenz - Starke Forschungs- und Ingenieurskompetenz für Prozessinnovationen.
Die Wahl eines etablierten Anbieters mit umfassenden internen Fähigkeiten bietet eine robuste, nahtlose Lösung für komplexe MIM-Projekte. Die räumliche Nähe ermöglicht zudem eine bessere Zusammenarbeit und Kommunikation.
MIM im Vergleich zu anderen Prozessen
MIM vs. CNC-Bearbeitung
- Kosten - MIM niedrigere Kosten bei mittleren und hohen Stückzahlen, CNC kosteneffektiv bei niedrigen Stückzahlen
- Gestaltung - Höhere Komplexität und besseres Konsolidierungspotenzial mit MIM
- Materialien - Breiteres Materialspektrum mit MIM möglich, einschließlich Werkzeugstählen und Titanlegierungen
- Geschwindigkeit - Höhere Produktionsraten mit MIM, langsamere Zykluszeiten bei der CNC-Bearbeitung
- Vergeudung - MIM hat einen geringeren Materialabfall als die CNC-Bearbeitung.
MIM vs. Metallguss
- Auflösung - Höhere Auflösung und feinere Details mit MIM möglich
- Komplexität - Erhöhte geometrische Komplexität durch MIM
- Toleranzen - Viel engere Maßtoleranzen mit MIM möglich
- Konsistenz - Einheitlichere Materialeigenschaften und Leistung mit MIM
- Sekundäre Bearbeitung - Für MIM-Teile sind in der Regel weniger Nachbearbeitungen erforderlich
MIM vs. 3D-Druck
- Kosten – MIM derzeit kostengünstiger für mittlere und größere Produktionsmengen
- Materialien – breiteres Spektrum an Hochleistungslegierungen wie Werkzeugstählen für MIM verfügbar
- Toleranzen – Genauere Maßtoleranzen mit MIM möglich
- Mechanische Eigenschaften – Generell bessere und gleichmäßigere Eigenschaften als bei 3D-gedruckten Metallen
- Qualifizierung – MIM-Verfahren im Gegensatz zum 3D-Druck bereits für Luft- und Raumfahrt und medizinische Anwendungen geeignet
MIM bietet Vorteile in Bezug auf Komplexität, Konsistenz und Kosten im Vergleich zu anderen Metallfertigungsverfahren für kleine, hochpräzise Bauteile, die in mittleren und größeren Stückzahlen hergestellt werden.
Beschränkungen und Herausforderungen von MIM
Zu den wichtigsten Einschränkungen und Nachteilen des MIM-Verfahrens gehören:
- Hohe anfängliche Investitionskosten für Werkzeuge verhindern kleine Produktionsläufe
- Begrenzte Größenkapazität, nicht ideal für Teile über 500 Gramm
- Eingeschränkte Geometrie aufgrund der Notwendigkeit, Komponenten zu entbindern und zu sintern
- Schwierig, sehr enge Toleranzen unter ±0,5% zu erreichen
- Nicht empfohlen für exotische Legierungen, die schwer zu sintern sind
- Um kritische Passungen und Abmessungen zu erreichen, kann eine sekundäre Bearbeitung erforderlich sein.
- Erhebliches Prozesswissen zur Fehlervermeidung beim Gießen erforderlich
- Die Investitionskosten für MIM-Maschinen können erheblich sein
Die Überwindung der Grenzen des MIM-Verfahrens erfordert Kompromisse bei der Konstruktion, den Toleranzanforderungen und den Anforderungen an die Sekundärverarbeitung. Das Verfahren eignet sich am besten für komplexe, hochpräzise kleine Bauteile und nicht für sehr große oder einfache Geometrien.
Entwicklungen in der MIM-Technologie
Zu den jüngsten Entwicklungen der MIM-Technologie, die die Möglichkeiten und die Akzeptanz erweitern, gehören:
- Rohstoffe für Nanopulver - Verbesserung der gesinterten Festigkeit und des Mikrogefüges
- Schneller Werkzeugbau – Senkung der Werkzeugkosten und Vorlaufzeiten durch 3D-gedruckte Einsätze
- Binder Jetting - Ermöglicht die Herstellung von Metall-3D-Drucken durch Drucken und Sintern
- MIM von Titan – Entwicklung von kostengünstigen Titanbauteilen
- Niederdruck-Einspritzung - Für größere MIM-Teile mit reduzierten Werkzeugspannungen
- MIM von Keramiken - Ausweitung auf technische/strukturelle Keramik über Tonerde hinaus
- Integration von Industrie 4.0 - Automatisieren und Optimieren der Qualitätskontrolle
Die kontinuierliche Innovation des MIM-Verfahrens trägt dazu bei, Einschränkungen zu überwinden, die Materialeigenschaften zu erweitern und die Anwendungsmöglichkeiten in neuen Branchen zu vergrößern. Dadurch wird MIM zu einer wettbewerbsfähigen Technologie für die Herstellung von Präzisionsmetallbauteilen.Copy
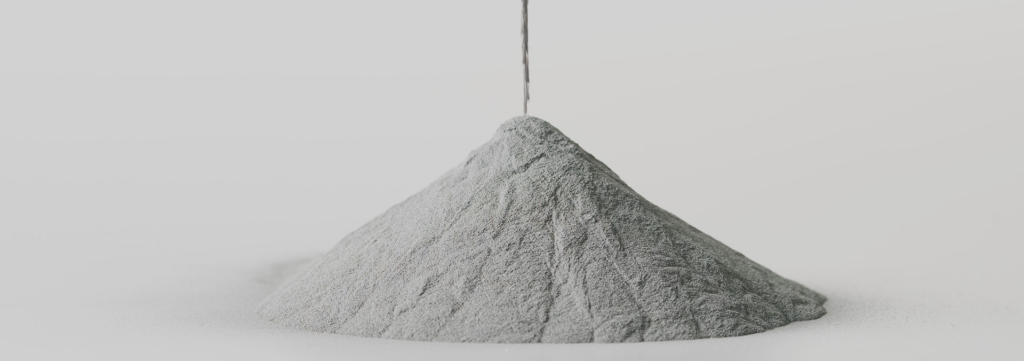
FAQ
Hier finden Sie Antworten auf einige häufig gestellte Fragen zum Metall-Spritzgießverfahren:
F: Welche Arten von Metallen können für MIM verwendet werden?
A: Mit der MIM-Technologie kann eine breite Palette von Metallen und Legierungen verarbeitet werden, darunter rostfreie Stähle, Werkzeugstähle, magnetische Legierungen, Titanlegierungen, schwere Wolframlegierungen und Kupferlegierungen. Gängige Werkstoffe sind rostfreier Stahl 316L und 17-4PH, Werkzeugstahl H13 und Titan Ti-6Al-4V.
F: Welche Größe von Bauteilen kann durch MIM hergestellt werden?
A: Der ideale Größenbereich für MIM liegt zwischen 0,5 Gramm und 500 Gramm. Sowohl kleinere als auch größere Teile sind möglich, aber möglicherweise nicht wirtschaftlich. Bei Miniaturteilen unter 0,5 Gramm können Probleme bei der Handhabung und Nachbearbeitung auftreten. Größere Teile über 500 Gramm erfordern höhere Werkzeugbelastungen und längere Zykluszeiten.
F: Welche Maßgenauigkeit und Toleranzen sind mit MIM möglich?
A: Mit MIM können sehr gute Maßtoleranzen von bis zu ±0,1 % der Abmessungen erreicht werden. Für Bauteile mit mittleren Toleranzen sind jedoch ±0,5 % typisch. Toleranzen unter ±0,005 Zoll (+/- 0,127 mm) erfordern eine Nachbearbeitung. Die Sinterschrumpfung muss berücksichtigt werden.
F: Was ist der Unterschied zwischen MIM und Kunststoffspritzgießen?
A: Das MIM-Verfahren basiert auf dem Kunststoff-Spritzgießen, verwendet jedoch Metallpulver anstelle von Kunststoffharzen. MIM ermöglicht die Herstellung komplexer, hochfester Metallteile durch dieses angepasste Spritzgussverfahren mit einem zusätzlichen Sinterungsschritt.
F: Welche Oberflächenbeschaffenheiten können bei MIM-Teilen hergestellt werden?
A: MIM ist in der Lage, feine Oberflächengüten bis zu 0,5 Mikrometer Ra zu erzeugen, vergleichbar mit bearbeiteten Oberflächen. Faktoren wie das Bindemittelsystem, die Werkzeugoberfläche, die Geometrie und die sekundäre Bearbeitung bestimmen die letztendlich erreichbare Oberflächenrauheit.
F: Welche Arten von komplexen Geometrien können mit MIM hergestellt werden?
A: Komplizierte Geometrien mit dünnen Wänden, negativen Entformungswinkeln, Hinterschneidungen, blinden Kavitäten und unkonventionellen Formen können mit MIM leicht geformt werden, da das Pulver-Binder-Gemisch wie eine Flüssigkeit in die Form fließt.
F: Ist MIM für die Herstellung von Prototypenteilen geeignet?
A: MIM ist aufgrund der hohen Werkzeugkosten und Vorlaufzeiten nicht ideal für die Herstellung von Prototypen. Andere Verfahren wie CNC-Bearbeitung, 3D-Druck oder Aluminium-Spritzguss eignen sich besser für Prototypenteile in kleinen Stückzahlen, bevor Sie sich für MIM-Werkzeuge entscheiden.
mehr über 3D-Druckverfahren erfahren
Frequently Asked Questions (Supplemental)
1) What feedstock solids loading is optimal in the MIM Process?
- Typically 58–64 vol% metal powder in the binder. Higher loading reduces shrinkage and distortion but increases viscosity; tune via capillary rheometry.
2) How do I control shrinkage and dimensional scatter in sintering?
- Use consistent PSD (D50 ≈ 12–20 μm), spherical morphology, tight O/N/H limits, uniform debind, and sinter setters/fixtures. Apply SPC on green density and use master shrinkage curves per alloy.
3) Can MIM achieve medical and aerospace qualifications?
- Yes. Implement ISO 13485 or AS9100 QMS, material traceability, validated debind/sinter cycles, and biocompatibility testing (ISO 10993) for relevant alloys; report properties per ASTM F2885 and F3122.
4) When is HIP recommended for MIM parts?
- For fatigue‑critical, leak‑tight, or thick‑section components (e.g., 17‑4PH, Ti‑6Al‑4V). HIP raises density to ≥99.7%, reducing internal porosity; follow with appropriate aging/anneal.
5) What are common root causes of MIM defects and how to mitigate?
- Jetting/short shots: adjust gate, viscosity, mold temps. Blisters/cracks: incomplete debind—extend solvent or thermal stage. Warpage: unbalanced cooling or nonuniform green density—optimize tooling, packing, and fixtures.
2025 Industry Trends and Data
- Digital powder passports: Chemistry, PSD, O/N/H, apparent/tap density, and lot history are now standard in RFQs, reducing incoming variability.
- Micro‑MIM growth: Wearables and micro‑mechanisms drive use of ultra‑fine powders (D50 5–10 μm) with low‑viscosity binders and precision tooling vents.
- Sustainability focus: Solvent recovery loops, lower‑energy sintering profiles, and recycled powder content disclosures (15–30%) gain traction.
- In‑process analytics: Cavity pressure/temperature sensors and inline viscosity checks cut scrap by double digits.
- Hybrid routes: Print‑then‑sinter (binder jet) and MIM share furnaces/inspection cells for mixed‑technology factories.
KPI (MIM Process Performance), 2025 | 2023 Baseline | 2025 Typical/Target | Why it matters | Sources/Notes |
---|---|---|---|---|
Solids loading (vol%) | 56–62 | 58–64 | Shrinkage control, strength | Vendor guides; rheometry |
Hausner ratio (–) | 1.22–1.28 | 1.12–1.20 | Flow stability | ASTM B212/B213 |
Oxygen in 316L MIM powder (wt%) | 0.25–0.45 | 0.15–0.30 | Corrosion, density | ASTM E1019 |
Green density Cpk | 1.1–1.3 | ≥1.5 | Dimensional capability | Plant SPC |
Post‑HIP density (%) | 99.5–99.7 | 99.7–99.9 | Fatigue/leak‑tightness | OEM data |
Scrap reduction with cavity sensing | - | 10–20% | Yield improvement | Vendor app notes |
Recycled content disclosed (%) | Begrenzt | 15–30 | ESG, cost | EPD/LCA reports |
Standards and references:
- ASTM F2885 (MIM components), ASTM B212/B213/B214/B822 (density/flow/PSD), ASTM E1019 (O/N/H), ASTM F3122 (mechanical property reporting): https://www.astm.org
- ISO 22068 (MIM powders/components), ISO 13485 (medical QMS): https://www.iso.org
- EPMA MIM Guide and Design for MIM: https://www.epma.com
- ASM Handbook, Powder Metallurgy and MIM: https://dl.asminternational.org
Latest Research Cases
Case Study 1: Micro‑MIM 17‑4PH Latching Mechanism with Cavity Pressure Control (2025)
- Background: A wearable OEM required sub‑2 mm latches with tight tolerances and high fatigue strength.
- Solution: Spherical 17‑4PH powder (D50 ≈ 9 μm, O = 0.18 wt%); low‑viscosity binder; multi‑cavity mold with cavity pressure sensors; two‑step debind; vacuum sinter + H900 aging; optional HIP.
- Results: Post‑HIP density 99.85%; dimensional Cpk 1.7 on critical features; fatigue life +28% vs. 2023 baseline; scrap −19%.
Case Study 2: Solvent‑Recovery Debind and Low‑Energy Sintering of 316L MIM Surgical Components (2024)
- Background: A medical supplier targeted ESG goals while maintaining corrosion resistance.
- Solution: Closed‑loop solvent debind with >95% solvent recovery; optimized ramp‑hold sintering profile in H2 to limit grain growth; passivation per ASTM A967.
- Results: Energy use −14% per kg; density 98.8–99.2%; pitting potential improved 10% vs. prior cycle; annual solvent purchases −60%.
Expert Opinions
- Prof. Randall M. German, Powder Metallurgy Scholar and Author
- Viewpoint: “In the MIM Process, packing—set by powder PSD and solids loading—drives shrinkage predictability more than marginal sintering tweaks.”
- Dr. Martina Zimmermann, Head of Additive Materials, Fraunhofer IWM
- Viewpoint: “Lot‑level powder passports and in‑mold sensing are now essential for regulated sectors, cutting qualification time and scrap.”
- Dr. Paul J. Davies, EPMA MIM Expert Group
- Viewpoint: “Micro‑MIM success hinges on ultra‑fine powders with tight oxygen control and tooling vent design to prevent binder‑rich defects.”
Affiliation links:
- Fraunhofer IWM: https://www.iwm.fraunhofer.de
- EPMA: https://www.epma.com
- ASM International: https://www.asminternational.org
Practical Tools/Resources
- QC/Standards: ASTM F2885, ISO 22068, ASTM B212/B213/B214/B822, ASTM E1019
- Metrology: LECO inert‑gas fusion (https://www.leco.com); laser diffraction PSD; helium pycnometry (ASTM B923); CT for internal defects; surface profilometry
- Process control: Capillary rheometers; cavity pressure/temperature sensors; SPC templates for shrinkage and dimensions
- Design: EPMA Design for MIM guide; MPIF standards (https://www.mpif.org); ASM Handbook MIM chapters
- Costing/DFM: aPriori for MIM cost models; vendor DFM checklists for gate/runner, venting, and ejection
Last updated: 2025-08-22
Changelog: Added 5 supplemental FAQs; inserted 2025 KPI table and trend notes; included two case studies (micro‑MIM 17‑4PH latch; ESG‑focused 316L flow); added expert viewpoints with affiliations; compiled standards, metrology, process control, and design resources for the MIM Process.
Next review date & triggers: 2026-02-01 or earlier if ASTM/ISO standards update, major suppliers change O/N/H or PSD specs, or new datasets on micro‑MIM capability and solvent‑recovery debinding are published.