Einführung
Der 3D-Druck, auch bekannt als additive Fertigung, hat die Fertigung und das Design revolutioniert. Er bietet nie dagewesene Möglichkeiten zur schnellen Herstellung komplexer Geometrien mit wenig Abfall. Viele 3D-gedruckte Teile weisen jedoch aufgrund von Porosität und anderen Defekten, die mit dem Druckverfahren einhergehen, schlechte mechanische Eigenschaften auf.
Heiß-Isostatisches Pressen (HIP) ist ein Herstellungsverfahren, bei dem 3D-gedruckte Teile sowohl hohen Temperaturen als auch isostatischem Druck ausgesetzt werden, um ihre Dichte, Leistung und Zuverlässigkeit zu verbessern. Die Kombination aus Hitze und Druck ermöglicht das Schließen innerer Hohlräume und verschmilzt innere Defekte und Partikel in Metallen und Keramiken.
HIP, das nach dem 3D-Druck angewendet wird, verbessert die Eigenschaften der gedruckten Teile und ermöglicht so neue Anwendungen und verbesserte Leistungen. Die synergetische Kombination von 3D-Druck und HIP verschiebt die Grenzen von Designkomplexität und hoher Leistung.
Was ist heißisostatisches Pressen?
Heißisostatisches Pressen ist ein fortschrittliches Fertigungsverfahren zur Verringerung der Porosität und Erhöhung der Dichte von Metallen, Keramiken, Polymeren und Verbundwerkstoffen. Beim HIP-Verfahren wird das Bauteil in einem Hochdruckbehälter sowohl einer erhöhten Temperatur als auch einem isostatischen Druck ausgesetzt.
Isostatisch bedeutet, dass ein gleichmäßiger Druck aus allen Richtungen gleichzeitig ausgeübt wird. Dies wird erreicht, indem das Bauteil mit einem Inertgas, einer Flüssigkeit oder Glaskugeln umgeben wird, die den Druck gleichmäßig auf die Oberfläche des Teils übertragen.
Durch die gleichzeitige Anwendung von Wärme und Druck werden die inneren Poren und Hohlräume des Materials geschlossen und das Teil verdichtet. Die Verdichtung hängt von den viskoplastischen Eigenschaften des Materials bei der gewählten Temperatur ab und davon, wie leicht sich die Poren verformen und Lücken zwischen den Partikeln schließen können.
Der typische HIP-Prozess umfasst folgende Schritte:
- Einbringen von Teilen in einen Druckaufnahmebehälter
- Evakuieren der Luft und Auffüllen mit einem Inertgas wie Argon
- Aufheizen auf die Prozesstemperatur, oft zwischen 1040-1200°C (1900-2200°F)
- Anwendung von isostatischem Druck bis zu 30.000 PSI (200 MPa)
- Abkühlung unter Druck vor der Freigabe und Entnahme
Beim HIP-Verfahren wird das Material diffundiert, um innere Poren zu schließen, innere Hohlräume zu minimieren oder zu beseitigen und innere Defekte metallurgisch zu verbinden. Dies verbessert die Qualität, Leistung und Zuverlässigkeit der hergestellten Teile in Branchen wie Luft- und Raumfahrt, Verteidigung, Automobil und Energie.
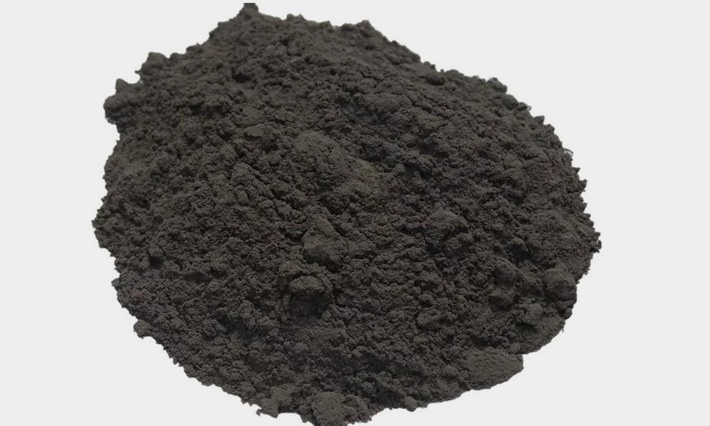
Wie verbessert das heißisostatische Pressen 3D-gedruckte Teile?
Die meisten Metall-3D-Druckverfahren wie das selektive Laserschmelzen (SLM) und das Elektronenstrahlschmelzen (EBM) erzeugen Teile mit einem gewissen Grad an Porosität. Das liegt an der Art, wie die Teile Schicht für Schicht aus Metallpulver aufgebaut werden.
Defekte wie Mikrorisse und Mikroporen von bis zu 100 μm bilden sich zwischen Pulverpartikeln und angrenzenden verfestigten Schichten. Je nach Material und Druckparametern können die Teile bis zu 5 % Porosität aufweisen.
Diese inhärente Porosität verursacht mehrere Probleme:
- Mechanische Eigenschaften wie Ermüdungsfestigkeit und Bruchzähigkeit sind stark reduziert
- Es entstehen Leckagepfade, die dazu führen, dass Teile die Dichtheitsprüfung nicht bestehen.
- Die Funktionsfähigkeit ist insbesondere bei Flüssigkeitsströmungen und unter Druck stehenden Systemen beeinträchtigt.
- Die Korrosionsbeständigkeit und chemische Verträglichkeit leidet durch das Eindringen in die Poren
- Die Maßgenauigkeit wird beeinträchtigt, da die Poren während der nachfolgenden Wärmebehandlung weiter wachsen können.
- Die Qualität der Oberflächen verschlechtert sich, da die Poren nahe der Oberfläche als Spannungskonzentratoren wirken.
Das heißisostatische Pressen eliminiert diese Poren und verbessert die Material- und Leistungseigenschaften von 3D-gedruckten Metallen erheblich. HIP erreicht:
- Erhöhte Dichte – das Schließen der inneren Hohlräume und Lücken verbindet das Material metallurgisch, um eine 100%ige Dichte zu erreichen
- Verbesserte mechanische Eigenschaften – beseitigt durch Defekte verursachte Spannungskonzentrationen, um die Festigkeit, Duktilität und Bruchfestigkeit zu verbessern
- Undurchlässige Strukturen – schließt mikroskopisch kleine Pfade für Flüssigkeiten, die durch das Material sickern
- Bessere Oberflächenqualität – zerkleinert die Poren in der Nähe der Oberfläche und verbessert dadurch die Oberflächenglätte
- Stabilität der Abmessungen – verhindert das weitere Wachstum von Poren bei zukünftigen thermischen Prozessen
- Höhere Zuverlässigkeit – Beseitigung von Fehlern zur Verbesserung der Qualität und Konsistenz der gedruckten Teile
So überwindet HIP die wichtigsten Einschränkungen des 3D-Drucks von Metall und ermöglicht die Herstellung von Hochleistungsendprodukten.
HIP-Verfahren für 3D-gedruckte Teile
Das typische HIP-Verfahren für additiv gefertigte Teile umfasst folgende Schritte:
HIP-Dose und Versiegelung
Die 3D-gedruckten Teile werden in einer HIP-Dose, die in der Regel aus Glas, Stahl oder Aluminium besteht, zusammen mit einem Füllstoff aus Keramik oder Glasperlen platziert. Die HIP-Dose stützt das Teil gegen Druck und überträgt den Druck gleichmäßig auf alle Oberflächen.
Die Dose wird dann durch Verschweißen oder Verpressen des Deckels hermetisch verschlossen. Dadurch wird das später zur Druckbeaufschlagung verwendete Inertgas zurückgehalten. Die Dose verhindert auch eine Verunreinigung während des HIP-Prozesses.
Entgasung
Die HIP-Dosenbaugruppe wird in den Hochdruckbehälter eingesetzt. Dieser Behälter wird versiegelt und abgepumpt, um ein Vakuum zu erzeugen. Durch das Vakuum werden Luft und Feuchtigkeit entfernt, die während des HIP-Prozesses zu Oxidation führen können.
Der Behälter wird dann mit einem Inertgas wie Argon gefüllt, das die Teile umgibt. Die inerte Atmosphäre verhindert chemische Reaktionen beim Erhitzen.
Heizung und Druckbeaufschlagung
Das Gefäß wird kontrolliert auf bis zu 1040-1200°C (1900-2200°F) erhitzt - die typische HIP-Temperatur für Metalle. Durch die Erhitzung werden Diffusions- und Kriechmechanismen im Material aktiviert, die zum Schließen der Poren beitragen.
Sobald die Temperatur erreicht ist, wird mit Hilfe des Inertgases isostatisch ein hoher Druck von bis zu 15.000-30.000 PSI (100-200 MPa) ausgeübt. Dieser Druck lässt die inneren Hohlräume kollabieren und drückt das Material in die Lücken.
Kühlung und Freigabe
Nach einer vorbestimmten Zeit bei Temperatur und Druck (in der Regel 3-6 Stunden) wird der Behälter mit kontrollierter Geschwindigkeit abgekühlt. Der Druck wird während der Abkühlung aufrechterhalten, um eine vollständige Verdichtung zu ermöglichen.
Nach dem Abkühlen wird der Druck allmählich abgelassen. Die HIP-Dose wird entfernt und geöffnet, um die behandelten Teile zu bergen. Durch zusätzliche Bearbeitung können die ursprünglichen Abmessungen wiederhergestellt werden.
Vorteile von HIP für 3D-gedruckte Teile
Die wichtigsten Vorteile der Nachbearbeitung von 3D-gedruckten Metallen mit HIP:
Erhöhte Dichte
HIP erreicht eine 100%ige Dichte in gedruckten Metallen, indem es Hohlräume und Diffusionsbindungsschichten kollabieren lässt. Dies verbessert die Integrität für tragende Strukturen und dichte Systeme.
Höhere Festigkeit
Durch die Beseitigung von Defekten wie Mikrorissen und Poren werden Spannungskonzentrationen beseitigt. Dies erhöht die Festigkeit und Duktilität im Vergleich zu konventionell verarbeiteten Materialien.
Bessere Oberflächenqualität
Mikrohohlräume in der Nähe der Oberfläche werden zerkleinert, um eine glattere Oberfläche mit verbessertem Finish und Aussehen zu schaffen. Dadurch wird auch die Ermüdungsbeständigkeit erhöht.
Stabilität der Abmessungen
Die Poren werden kollabiert, anstatt bei der anschließenden Wärmebehandlung zu wachsen. Dies verbessert die Maßhaltigkeit und die geometrischen Toleranzen.
Größere Teile
HIP ermöglicht den 3D-Druck und die Konsolidierung größerer Teile, die mit anderen Techniken nicht möglich sind. Es können Teile mit einem Durchmesser von bis zu 50 Zoll hergestellt werden.
Gestaltungsfreiheit
HIP bewahrt die Designfreiheit des 3D-Drucks für Teile mit komplexer Geometrie. Es erweitert die Anwendung von gedruckten Metallen auf kritische strukturelle und fluidtechnische Anwendungen.
Kürzere Vorlaufzeiten
Die Kombination von 3D-Druck und HIP verkürzt die Fertigungszeiten im Vergleich zu herkömmlichen mehrstufigen Verfahren. Sie ermöglicht die schnelle Herstellung komplexer, leistungsstarker Teile.
Branchen, die HIP für 3D-gedruckte Teile verwenden
HIP wird in allen wichtigen Branchen eingesetzt, um 3D-gedruckte Metallteile für robuste Endanwendungen zu verbessern:
Luft- und Raumfahrt
HIP verbessert die Dichte, Festigkeit und Oberflächenbeschaffenheit von gedruckten Bauteilen für die Luft- und Raumfahrt wie Turbinenschaufeln, Düsen für Raketentriebwerke und Satellitenhalterungen. Dies ermöglicht leichte, komplexe Geometrien für extreme mechanische Belastungen und Temperaturbeständigkeit.
Medizinische
Medizinische Implantate wie Hüftgelenke und Knochengerüste werden nach dem 3D-Druck mit HIP bearbeitet, um interne Hohlräume vollständig zu beseitigen. Dies verbessert die Biokompatibilität und Ermüdungsfestigkeit bei der Implantation in den Körper.
Automobilindustrie
HIP wird bei 3D-gedruckten Automobilteilen wie Turboladern und Zylindern für den Flüssigkeitstransport eingesetzt. So entstehen 100 % dichte Strukturen, die zyklischen Drücken und Belastungen standhalten.
Verteidigung
Der Verteidigungssektor verwendet HIP zur Herstellung von gedruckten Teilen wie Raketengehäusen und konformen Kühlkanälen für Gussformen. HIP ermöglicht komplexe Geometrien, die ballistischen Aufschlägen standhalten.
Energie
Bei Nuklear-, Ölbohr- und anderen Energieanwendungen sorgt HIP für eine vollständige Verdichtung der gedruckten Komponenten und damit für Bruchfestigkeit bei extremen Drücken und Temperaturen.
Mit der zunehmenden Verbreitung des 3D-Drucks in allen Branchen wird auch HIP wachsen und für mehr Leistung, Zuverlässigkeit und Konsistenz sorgen.
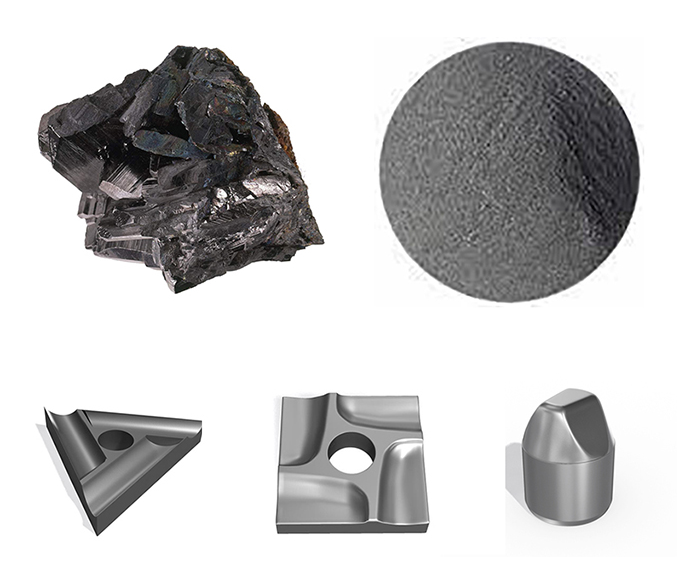
Materialien für HIP von 3D-gedruckten Teilen
HIP wurde für eine breite Palette von Metallen und Legierungen nachgewiesen, die im kommerziellen 3D-Druck verwendet werden:
- Titan und Titanlegierungen wie Ti-6Al-4V sind in der Luft- und Raumfahrt sehr beliebt. HIP erreicht eine Dichte von 100 % und verbessert die Ermüdungseigenschaften.
- Aluminium-Legierungen wie AlSi10Mg können gedruckt und HIP-verarbeitet werden, um eine leichtere Alternative zu Titan mit ähnlich verbesserten Eigenschaften zu erhalten.
- Superlegierungen auf Nickelbasis wie Inconel 718 und 625 werden häufig in Düsentriebwerken und Gasturbinen verwendet. HIP beseitigt Defekte und bewahrt gleichzeitig die Festigkeit bei hohen Temperaturen.
- Rostfreie Stähle einschließlich 316L und 17-4PH, werden häufig für den Druck starker, korrosionsbeständiger Teile in verschiedenen Branchen verwendet. HIP beseitigt die Porosität für eine verbesserte strukturelle Integrität.
- Werkzeugstähle wie H13 und D2 bieten nach dem HIP-Verfahren eine ausgezeichnete Härte für den Druck von langlebigen Werkzeugen wie Formen mit konformen Kühlkanälen.
- Hochschmelzende Metalle einschließlich Wolfram, Tantal und Molybdän, sind von Natur aus porös, können aber durch HIP vollständig verdichtet werden.
- Kobalt-Chrom-Legierungen bieten eine hervorragende Verschleißfestigkeit für orthopädische Implantate, wenn sie nach dem 3D-Druck mit HIP behandelt werden.
Sowohl Standard- als auch kundenspezifische Legierungen werden kontinuierlich für die additive Fertigung in Kombination mit HIP qualifiziert, um die Möglichkeiten zu erweitern.
HIP-Prozessparameter
Die wichtigsten HIP-Prozessparameter, die für verschiedene 3D-Druckteile optimiert werden können, sind:
- Temperatur – Typischer Bereich von 1850-2200°F. Höhere Temperaturen erhöhen die Diffusionsraten und schließen die Poren schneller. Zu hohe Temperaturen können jedoch mikrostrukturelle Veränderungen verursachen.
- Druck – Standarddrücke von 15.000-30.000 PSI werden verwendet. Höhere Drücke lassen die Poren bei niedrigeren Temperaturen kollabieren. Zu hohe Drücke können jedoch die Oberflächenbeschaffenheit beschädigen.
- Zeit – Standardhaltezeiten von 3-6 Stunden bei Spitzentemperatur und -druck. Längere Zeiten ermöglichen eine stärkere Verdichtung, erhöhen aber die Kosten.
- Heiz-/Kühlraten - Schnelleres Erhitzen erhöht die Produktivität, birgt aber die Gefahr von Verformungen. Langsameres Erhitzen (~50-100°F/min) und Abkühlen vermeiden thermische Spannungen.
- Verweilzeit - Das Halten bei Höchsttemperatur ermöglicht eine ausreichende Diffusionsbindung. Bei kürzeren Zeiten besteht die Gefahr einer unvollständigen Verdichtung.
Die Parameter des HIP-Prozesses werden entsprechend der spezifischen Zusammensetzung der 3D-Drucklegierung, der Teilegeometrie, der Pulvergröße und der erforderlichen Materialeigenschaften optimiert.
Herausforderungen bei der Verwendung von HIP mit 3D-gedruckten Teilen
Das HIP bietet zwar erhebliche Vorteile, doch gibt es auch einige Einschränkungen und Herausforderungen:
- Geänderte Abmessungen HIP kann 2-5% Schrumpfung verursachen. Die Teile müssen möglicherweise nach dem HIP nachbearbeitet werden, um die Abmessungen wiederherzustellen.
- Oberflächengüte HIP kann die Oberflächenrauhigkeit von AM reduzieren, erzielt aber möglicherweise nicht die glattesten Oberflächen. Zusätzliches Polieren kann erforderlich sein.
- Geometrische Grenzen HIP-Dosen begrenzen die maximale Teilegröße. Sehr komplexe Geometrien lassen sich mit HIP-Raupen nur schwer gleichmäßig füllen.
- Kosten – HIP verursacht gegenüber der herkömmlichen Wärmebehandlung erhebliche Mehrkosten. Der wirtschaftliche Nutzen hängt von der verbesserten Leistung ab, die die Investition rechtfertigt.
- Prozessentwicklung Optimale HIP-Protokolle müssen für jede spezifische Legierungszusammensetzung, Pulvergröße und jeden AM-Prozess entwickelt werden, um eine vollständige Verdichtung ohne Defekte zu gewährleisten.
Weitere Forschungen und Prozessverfeinerungen konzentrieren sich auf die Anpassung von HIP für größere geometrische Freiheit, Oberflächenqualität, Durchlaufzeiten und Kosteneffizienz.
Die Zukunft von HIP und 3D-Druck
HIP hat sich als Technologie zur Qualifizierung von 3D-gedruckten Metallen für hochwertige, kritische Anwendungen in den Bereichen Luft- und Raumfahrt, Medizin, Automobil und Verteidigung bewährt.
Mit der Ausweitung des 3D-Drucks vom Prototyping auf die Großserienproduktion wird HIP für Branchen, die auf Teile mit hoher struktureller Integrität und Leistung angewiesen sind, von entscheidender Bedeutung sein. Mit Verbesserungen bei der Automatisierung, den Durchlaufzeiten und den Kosten wird mit einer zunehmenden Verbreitung beider Technologien gerechnet.
Zu den neuen Entwicklungen bei HIP zur Unterstützung von AM gehören:
- Kürzere Radfahrzeiten Neuartige Erhitzungsmethoden und eine schnellere Abkühlung sollen die typischen HIP-Zyklen von über 6 Stunden auf unter 3 Stunden reduzieren. Dies verbessert den Durchsatz.
- Größere Bauvolumen – Die Behälter werden immer größer, um größere gedruckte Teile mit einem Durchmesser von bis zu 50 Zoll aufzunehmen. Dies erweitert die Möglichkeiten.
- Hybrides HIP Spezielle HIP-Zyklen mit kontrollierten Abkühlungsraten oder In-situ-Wärmebehandlungen werden derzeit entwickelt, um die Eigenschaften weiter zu optimieren.
- Sicherung der Qualität – Inline-Überwachungs- und Inspektionswerkzeuge für HIP helfen bei der Charakterisierung der Verdichtung und der Validierung der Teilequalität.
- Modellierungswerkzeuge Die Simulationssoftware ermöglicht bessere Vorhersagen über die Verformung und die Verbesserung der Eigenschaften von HIP.
Die synergetische Weiterentwicklung von 3D-Druck und HIP wird neue Wege für die Entwicklung und effiziente Herstellung komplexer, leistungsstarker Komponenten in wichtigen Branchen eröffnen.
Die wichtigsten Erkenntnisse über HIP und 3D-Druck
- Beim heißisostatischen Pressen (HIP) werden die inneren Hohlräume in 3D-gedruckten Metallen durch hohe Temperaturen und gleichmäßigen Druck kollabiert, wodurch Dichte, Leistung und Zuverlässigkeit verbessert werden.
- HIP beseitigt Porositätsdefekte wie Mikrorisse, die bei 3D-Druckverfahren mit Pulverbettfusion auftreten.
- Zu den wichtigsten Vorteilen von HIP für den 3D-Druck gehören eine höhere Dichte, eine höhere Festigkeit, eine bessere Oberflächenbeschaffenheit, Dimensionsstabilität und verbesserte Designs.
- HIP ermöglicht leichtere Konstruktionen, komplexe Geometrien und innovative konforme Merkmale für Anwendungen in der Luft- und Raumfahrt, der Medizintechnik, der Automobilindustrie und der Verteidigung.
- Mit Verbesserungen bei der Automatisierung, der Geschwindigkeit und den Kosten wird HIP zunehmend eingesetzt, um die Qualität und die Möglichkeiten des 3D-Metalldrucks in Produktionsumgebungen zu verbessern.
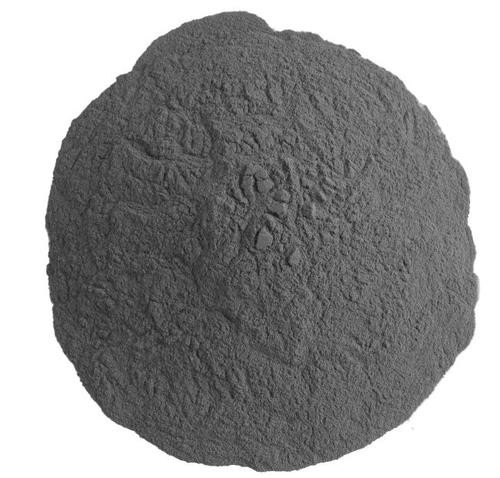
FAQ
Wozu dient das heißisostatische Pressen beim 3D-Druck?
Heißisostatisches Pressen (HIP) wird als Nachbearbeitungsmethode für 3D-gedruckte Metallteile verwendet. HIP hilft bei der Beseitigung von Porositätsdefekten, indem hohe Temperaturen und isostatischer Druck angewendet werden, um Hohlräume zu kollabieren und die Teile zu verdichten. Dies verbessert die Dichte, Leistung und Zuverlässigkeit von additiv gefertigten Bauteilen.
Wie verbessert HIP die Eigenschaften von 3D-gedruckten Metallen?
HIP verbessert die Eigenschaften von 3D-gedruckten Metallen auf verschiedene Weise:
- Erhöht die Dichte auf nahezu 100 % durch Diffusionsverschweißung von Schichten und Schließen interner Lücken
- Beseitigt Mikrorisse und Poren, um die Ermüdungslebensdauer und Festigkeit deutlich zu verbessern
- Bietet eine hervorragende Oberflächengüte durch Zerkleinern oberflächennaher Defekte
- Bietet eine bessere Dimensionsstabilität, indem es ein weiteres Wachstum von Hohlräumen während der Wärmebehandlung verhindert
- Ermöglicht den Druck und die Konsolidierung größerer und komplexerer Geometrien
Welche Arten von Materialien können nach dem 3D-Druck HIP-verarbeitet werden?
Die meisten Legierungen, die im Pulverbettschmelzverfahren gedruckt werden, können mit dem HIP-Verfahren hergestellt werden:
- Titanlegierungen wie Ti-6Al-4V
- Nickel-Superlegierungen wie Inconel 718 & 625
- Rostfreie Stähle, einschließlich 316L und 17-4PH
- Aluminiumlegierungen wie AlSi10Mg
- Werkzeugstähle wie H13 und D2
- Kobalt-Chrom-Legierungen für medizinische Zwecke
- Refraktärmetalle wie Wolfram und Tantal
Sowohl Standard- als auch kundenspezifische Legierungen werden kontinuierlich für die additive Fertigung und HIP qualifiziert.
Welche Branchen verwenden HIP für 3D-gedruckte Teile?
Zu den wichtigsten Branchen, die HIP für die Nachbearbeitung von 3D-gedruckten Teilen einsetzen, gehören:
- Luft- und Raumfahrt – Turbinenschaufeln, Raketendüsen
- Medizinische – Orthopädische Implantate wie Hüftgelenke
- Automotive - Teile für die Fluidtechnik, Turbolader
- Verteidigung - Raketenhüllen, Panzerung
- Energie – Komponenten für die Nuklear-, Öl- und Gasindustrie
In dem Maße, in dem sich der 3D-Druck in allen Sektoren ausbreitet, wird auch die Akzeptanz von HIP zunehmen, um die Produktion von Hochleistungsteilen für den Endverbraucher zu ermöglichen.
Wie funktioniert das HIP-Verfahren für 3D-gedruckte Teile?
Zu den wichtigsten Schritten im typischen HIP-Prozess für 3D-gedruckte Teile gehören:
- Die Teile werden zusammen mit dem Füllmaterial in einer HIP-Dose eingeschlossen
- Dose wird versiegelt und in den HIP-Behälter gestellt
- Das Gefäß wird evakuiert, mit Inertgas gefüllt und dann auf 1900-2200°F erhitzt.
- Isostatischer Druck bis zu 30.000 PSI wird angewendet
- Verweilzeit bei Spitzentemperatur und -druck verdichtet Teile
- Das Gefäß wird vor der Freigabe unter Druck abgekühlt
Die HIP-Parameter werden auf die jeweilige Legierung, Geometrie und Eigenschaften des Teils zugeschnitten.
Welche Herausforderungen sind mit der Verwendung von HIP für 3D-Druckteile verbunden?
Zu den wichtigsten Herausforderungen gehören:
- Maßänderungen bis zu 5% Schrumpfung, die eine Nachbearbeitung erfordern
- Begrenzung der maximalen Teilegröße auf der Grundlage der Kapazität des HIP-Behälters
- Ungleichmäßige Verdichtung für komplexe Geometrien
- Lange Prozesszyklen von 6+ Stunden
- Kosten höher als bei konventioneller Wärmebehandlung
- Entwicklung von optimierten Protokollen für verschiedene Legierungssysteme
mehr über 3D-Druckverfahren erfahren
Additional FAQs: HIP
1) Does HIP always eliminate all porosity in AM parts?
- HIP can close most internal pores and lack‑of‑fusion defects, often achieving >99.9% relative density. However, surface‑connected porosity or gas‑entrapment in sealed cavities may persist unless capsules/cans or surface sealing are used pre‑HIP.
2) How should HIP parameters be chosen for common AM alloys?
- Typical starting points: Ti‑6Al‑4V (920–930°C, 100–170 MPa, 2–4 h), Inconel 718 (1120–1180°C, 100–170 MPa, 2–4 h, followed by aging), 316L (1100–1150°C, 100–150 MPa, 2–3 h), AlSi10Mg (480–520°C, 70–120 MPa, 1–3 h). Final settings depend on initial porosity, microstructure, and downstream heat treatments.
3) Can HIP replace heat treatment?
- Sometimes. HIP provides densification and stress relief, and “HIP + heat‑treat” cycles can be combined (HIP‑Q/HT‑HIP). But precipitation‑hardening alloys (e.g., 17‑4PH, IN718) still require tailored solution/aging to meet strength specs.
4) What design considerations improve HIP outcomes for 3D printed parts?
- Avoid sealed voids unless intentional; add vent holes or use sacrificial cans. Maintain uniform wall thickness where possible, minimize inaccessible internal surfaces that might trap contamination, and account for 0.1–0.5% dimensional change (after scaling and machining stock).
5) How is HIP quality verified?
- NDT (X‑ray CT for pore size/volume, ultrasonic, dye penetrant for surface‑breaking defects), density by Archimedes, tensile/fatigue coupons co‑printed and HIPed with parts, leak testing for pressure components, and metallography to confirm pore closure and microstructure.
2025 Industry Trends: HIP for Additive Manufacturing
- Integrated HIP lines: More service bureaus install in‑house HIP with automated handling to cut queue time from weeks to days.
- Combined cycles: Adoption of “HIP plus heat treatment” recipes to compress process steps and reduce distortion.
- Data‑driven qualification: Digital passports link AM build parameters, CT porosity before/after HIP, and mechanical results to accelerate certification.
- Lower‑temp/high‑pressure HIP: For Al and Cu alloys, higher pressures at reduced temperatures mitigate grain growth while closing pores.
- Sustainability: Energy recovery on furnaces/compressors and argon recycling reduce HIP cost/carbon intensity.
2025 HIP Outcomes for AM Parts (Indicative Benchmarks)
Metrisch | 2023 | 2024 | 2025 YTD (Aug) | Anmerkungen |
---|---|---|---|---|
Typical relative density after HIP (%) | 99.7–99.9 | 99.8–99.95 | 99.9–~100 | CT-confirmed |
Median fatigue life gain vs. as‑built (Ti‑6Al‑4V, R=0.1) | 3–6× | 4–7× | 5–8× | Surface finish still key |
CT‑detected pore volume reduction (%) | 85–95 | 90–97 | 92–98 | Pre‑seal improves results |
Turnaround (print→HIP→HT→ship, days) | 12–18 | 9–14 | 6–11 | In‑house HIP adoption |
Lots with digital genealogy/passports (%) | ~40 | ~55 | ~70 | Regulated sectors |
Energy per HIP cycle (MWh, large vessel) | 6.5–8.0 | 6.0–7.5 | 5.5–7.0 | Heat recovery, scheduling |
Sources:
- ISO/ASTM AM and post‑processing guidance (e.g., 52920/52930 series): https://www.iso.org
- ASTM F3301/F3302 and E10xx CT/NDT practices: https://www.astm.org
- NIST AM‑Bench and measurement science for porosity/fatigue links: https://www.nist.gov/ambench
- OEM/application notes (e.g., Quintus, EPSI, Bodycote) and aerospace specs (SAE/AMS)
Latest Research Cases
Case Study 1: Combined HIP + Aging for IN718 Impellers (2025)
Background: An aero supplier needed to shorten qualification time for LPBF IN718 impellers with strict fatigue targets.
Solution: Implemented a combined HIP + direct‑age cycle (1160°C/150 MPa/3 h → controlled cool → 720°C/8 h + 620°C/8 h) in one workflow; added pre‑HIP surface sealing on as‑built external skins.
Results: CT pore volume −96%; LCF life at 650°C improved 5.4× vs. stress‑relieved only; total lead time −28%; dimensional change limited to 0.18% with pre‑scale compensation.
Case Study 2: Low‑Temperature High‑Pressure HIP for AlSi10Mg Heat Exchangers (2024)
Background: An EV OEM experienced microleaks in thin‑wall LPBF Al heat exchangers after standard stress relief.
Solution: Employed 500°C/120 MPa/2.5 h HIP, followed by artificial aging; temporary vacuum impregnation to seal surface‑connected porosity before HIP.
Results: Leak rate dropped below 1×10⁻⁶ mbar·L/s (He); burst pressure +22%; grain coarsening minimized; yield +7% by reducing scrap.
Expert Opinions
- Dr. Thomas E. Lolla, Senior Fellow, Materials & Processes, GE Aerospace
- “Linking pre‑HIP CT with tailored HIP cycles allows us to right‑size pressure and dwell, achieving pore closure without unnecessary grain growth.”
- Prof. Amy J. Clarke, Professor of Metallurgy, Colorado School of Mines
- “For precipitation‑strengthened alloys, integrating HIP with the correct thermal path is essential—sequence dictates precipitate size and thus fatigue.”
- Katarina Nilsson, VP Technology, Quintus Technologies
- “Process intelligence—load thermography, gas‑flow modeling, and argon recovery—has made HIP both faster and greener for serial AM production.”
Practical Tools and Resources
- ISO/ASTM 52920/52930 (AM qualification and post‑processing), 52904 (LPBF of metals): https://www.iso.org
- ASTM F3301/F3302 for AM practice and qualification; E1447/E1409/E1019 for O/N/H analysis; E1570, E2698 for CT/NDT: https://www.astm.org
- SAE/AMS aerospace specs for AM post‑processing (e.g., AMS7011/7032 series): https://www.sae.org
- NIST AM‑Bench datasets and fatigue/porosity correlation resources: https://www.nist.gov/ambench
- OEM HIP application notes and parameter guides (Quintus, Bodycote, EPSI)
- CT analysis software (Volume Graphics, Simpleware) for pore quantification pre/post HIP
Last updated: 2025-08-25
Changelog: Added 5 focused HIP FAQs; introduced a 2025 benchmark table with indicative metrics and sources; provided two recent case studies; included expert viewpoints; compiled practical tools/resources
Next review date & triggers: 2026-02-01 or earlier if ISO/ASTM/SAE standards update, major OEMs release new combined HIP/HT cycles, or CT-driven HIP optimization changes accepted practices by >10%**