Was sind die industriellen Anwendungen von Additive Fertigung für die Hüfte?
Die additive Fertigung der Hüfte, auch bekannt als 3D-Druck, revolutioniert die Produktion in allen Branchen. Ein Bereich, in dem sich die additive Fertigung als besonders vielversprechend erwiesen hat, ist die Hüftprothetik. Die additive Fertigung bringt mehrere Vorteile für Hüftprothesen mit sich, darunter individuelle Anpassung, vereinfachte Logistik und innovative Geometrien. Infolgedessen gewinnt die additive Fertigung von Hüftprothesen in der Medizintechnik immer mehr an Bedeutung.
Eine Einführung in die additive Fertigung für Hüftprothesen
Bei der additiven Fertigung werden Teile schichtweise aus Materialien wie Metallen, Kunststoffen und Keramiken aufgebaut. Dies ermöglicht eine Produktion auf Abruf, ohne dass Formen, Gesenke oder Spezialwerkzeuge benötigt werden. Die Teile können auf Bestellung gefertigt werden, was die Logistik vereinfacht. Die additive Fertigung ermöglicht auch komplexe Geometrien, die mit subtraktiven Methoden wie der CNC-Bearbeitung nicht hergestellt werden können.
Für Hüften eröffnet die additive Fertigung neue Möglichkeiten. Hüftgelenke stellen hohe mechanische Anforderungen – sie müssen zyklische Belastungen über Jahre hinweg aushalten. Additiv gefertigte Hüften können fortschrittliche Konstruktionen enthalten, die die Festigkeit, Flexibilität und Langlebigkeit verbessern. Zu den beliebten additiven Verfahren für Hüften gehören das Laser-Pulverbettschmelzen (LPBF) von Titanlegierungen und das Elektronenstrahlschmelzen (EBM) von Kobalt-Chrom. Diese Verfahren ermöglichen komplizierte poröse Strukturen und funktionell abgestufte Zusammensetzungen.
Additive Verfahren sorgen für leistungsfähigere und langlebigere Hüftprothesen. Lassen Sie uns einige der wichtigsten industriellen Anwendungen untersuchen, die die Einführung vorantreiben.
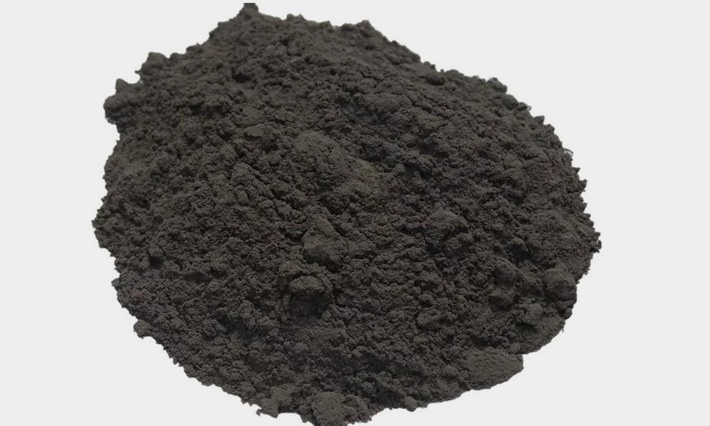
Maßgeschneiderte Implantate basierend auf der Anatomie des Patienten
Ein großer Vorteil der additiven Fertigung ist die Möglichkeit, maßgeschneiderte Teile wirtschaftlich herzustellen. Dies ist ideal für Hüften, da die Anatomie jedes Patienten leicht unterschiedlich ist. Maßgeschneiderte Implantate passen sich besser an die Knochenkonturen des Patienten an und verbessern die kurz- und langfristige Fixierung.
LPBF wird in der Regel für die Herstellung von patientenspezifischen Titan-Hüftimplantaten verwendet. CT-Scans erfassen die genaue Form des Gelenks eines Patienten. Anhand dieser Daten kann das Additivsystem Titanpulver zu einer perfekt auf den Patienten zugeschnittenen Hüfte verschmelzen.
Maßgefertigte Hüften minimieren invasive Rasuren und Änderungen während der Operation. Durch die präzise Passform kann mehr natürlicher Knochen des Patienten erhalten werden. Personalisierte Hüften haben in der Regel auch bessere klinische Ergebnisse, zum Beispiel bei der Wiederherstellung der natürlichen Gelenkausrichtung.
Große Hersteller von orthopädischen Geräten wie Zimmer Biomet und Stryker haben damit begonnen, 3D-gedruckte patientenspezifische Hüftprothesenkomponenten anzubieten. Es wird erwartet, dass die Nachfrage nach maßgeschneiderten Implantaten steigen wird, da Krankenhäuser fortschrittliche Bildgebungs- und Designsoftware einsetzen.
Funktional abgestufte Materialien
Ein weiterer Vorteil der additiven Fertigung ist die Herstellung von Bauteilen aus funktionell abgestuften Werkstoffen (FGM). Bei FGM werden die Eigenschaften wie Porosität und Legierungszusammensetzung schrittweise verändert. Dadurch können Hüften verschiedene strukturelle Anforderungen wie Stoßdämpfung, Steifigkeit und Knocheneinwuchs in einem einzigen Teil erfüllen.
LPBF kann Metalle in komplexe FGM-Strukturen einbinden. Ein Femurschaft kann am Hals dicht gepackt sein, um die Steifigkeit zu erhöhen, und dann an der Schnittstelle zum Knochen in einen porösen Schaum übergehen. Dies hilft bei der Verteilung der Lasten und verhindert gefährliche Steifigkeitsgradienten. EBM von Kobaltchrom hat FGM-Hüften mit knochenähnlicher Flexibilität und Festigkeit ermöglicht.
FGM-Hüftimplantate bilden die Leistung des natürlichen Knochens besser nach. Sie helfen, Probleme wie Knochenschwund und Oberschenkelschmerzen zu vermeiden, die mit herkömmlichen Implantaten verbunden sind. Orthopädische Unternehmen wie Akahi bringen additiv hergestellte FGM-Hüften auf den Markt. Kliniker experimentieren auch mit geschichteten FGM-Strukturen, die durch die Kombination unterschiedlicher gedruckter Metalle hergestellt werden.
Gitterstrukturen und topologische Optimierung
Die additive Fertigung ermöglicht radikal neue Konstruktionen, die anders nicht herstellbar sind. Ein Beispiel sind zelluläre Gitterstrukturen mit knochenähnlicher Porosität. Gitter weisen ein außergewöhnliches Verhältnis von Festigkeit zu Gewicht auf und können die Steifigkeit von natürlichem Gewebe erreichen.
Für die Hüfte fördern Gitterfemurschäfte und Hüftpfannen das Einwachsen von Knochen zur biologischen Fixierung. LPBF fertigt gedruckte Strukturen aus Titan und Tantalschaum, die auf die Nachgiebigkeit des Oberschenkels abgestimmt sind. Gitter geben Chirurgen zusätzliche Flexibilität bei der individuellen Anpassung von Implantaten während der Operation. Überschüssiges Material kann entfernt werden, während die Knochenintegrationsbereiche erhalten bleiben.
Software zur Topologieoptimierung ermöglicht weitere Verbesserungen im Hüftdesign. Algorithmen iterieren Tausende von Layouts, um ideale mechanische Eigenschaften zu finden. Das Ergebnis sind organische, bionische Formen, die auf die Kräfte des Patienten und die Knochenstruktur zugeschnitten sind. Mehrere Unternehmen bieten inzwischen topologieoptimierte Hüftimplantate mit stoßdämpfenden Gittern an.
Vor-Ort-Fertigung für eine bessere Bestandsverwaltung
Die additive Fertigung bietet bahnbrechende Vorteile für die Lieferkette und das Bestandsmanagement von Hüften. Bei der herkömmlichen Fertigung produzieren die Hersteller eine Reihe von Standardgrößen, die weltweit gelagert werden müssen. Dies führt zu erheblichen Lagerkosten.
Die additive Fertigung ermöglicht eine Just-in-Time-Produktion von Hüftgelenken in der Nähe von Krankenhäusern auf Abruf. Drucker können vor Ort installiert werden, um Implantate zu fertigen, wenn Eingriffe geplant sind. Chirurgen erhalten mehr Flexibilität bei der Größenauswahl. Die Krankenhäuser sparen außerdem Kosten für die Bestellung, den Versand und die Entsorgung unbenutzter Implantatbestände.
Das Interesse an krankenhausbasierten 3D-Drucklabors zur Herstellung patientenspezifischer Produkte steigt. Im Jahr 2021 übernahm Zimmer Biomet das Unternehmen Additive Orthopaedics, das weltweit Fertigungsdienstleistungen vor Ort anbietet. Andere medizinische Drucker wie Jabil’s Health sind speziell für Krankenhäuser entwickelt worden. Lokal gedruckte Implantate tragen dazu bei, die Hüftprothesenchirurgie zu verändern.
Additive Fertigung von Instrumenten und chirurgischen Führungen
Neben den Hüftkomponenten selbst wird die additive Fertigung auch zur Verbesserung der chirurgischen Versorgung eingesetzt. LPBF kann maßgeschneiderte Instrumente wie Raspeln und Reibahlen herstellen, die auf die Anatomie eines Patienten abgestimmt sind. Patientenspezifische Führungen werden aus Nylonpulver gedruckt, wobei Schlitze und Öffnungen anhand von Scandaten entworfen werden.
Die Schablonen zeigen genau an, wo die Knochenschnitte und Bohrlöcher ausgerichtet werden müssen. Dadurch wird der digitale Implantatplan direkt in den Operationssaal übertragen und dort präzise ausgeführt. Die Schablonen haben nachweislich die Genauigkeit von Hüftprothesen verbessert und die OP-Zeiten verkürzt.
Additive Instrumenten-Kits ermöglichen Chirurgen eine größere Flexibilität bei der Behandlung. Führungen und einzigartige Werkzeuge helfen den Chirurgen, das Implantat in engen Gelenkspalten richtig zu positionieren. Der 3D-Druck ermöglicht es Krankenhäusern außerdem, Instrumente kosteneffizient auf Abruf zu produzieren. Diese Vorteile machen die additive Werkzeugherstellung zu einem wesentlichen Bestandteil der Hüftchirurgie.
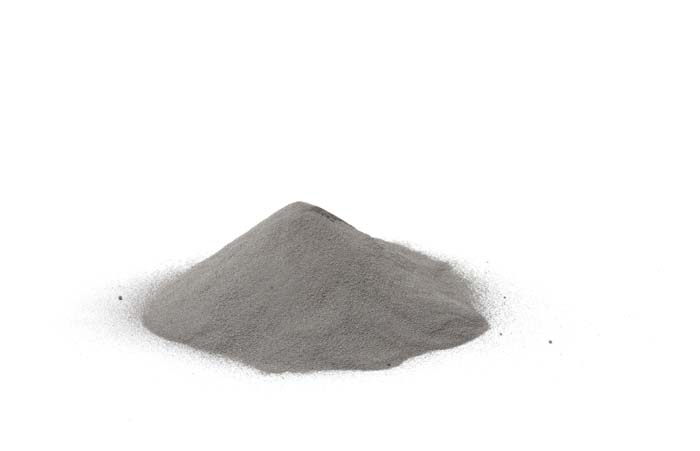
Neue Kobalt-Chrom-Legierungen
Die meisten Hüftprothesen bestehen aus Kobalt-Chrom- oder Titan-Legierungen, die mit einer Kunststoffschale aus ultrahochmolekularem Polyethylen verbunden sind. Ingenieure entwickeln fortschrittliche neue CoCr-Materialien, die auf den Bedarf an Zusatzstoffen zugeschnitten sind.
Führend ist die Hüftlegierung BIOCOR von Carpenter’. BIOCOR wurde für EBM optimiert und zeichnet sich durch eine feine Mikrostruktur mit hoher Ermüdungsfestigkeit aus. Dies ermöglicht Designverbesserungen wie dünne Wände und Gitter, während die Lebensdauer des Implantats über 20 Jahre beträgt. BIOCOR hat sich klinisch sehr bewährt und wurde von der FDA zugelassen.
Andere Unternehmen bringen neuartige Verbundwerkstoffe in die additive Fertigung ein. So wurde beispielsweise durch die Optimierung von Zimaloy CoCr mit Niob die Verschleißfestigkeit um 30 % gegenüber herkömmlichen Legierungen verbessert. Die additive Fertigung macht es wirtschaftlich, solche maßgeschneiderten Elemente in Konzentrationen einzubringen, die mit anderen Methoden schwierig sind.
Gelenkmobilität und Artikulationen neu denken
Mit Blick auf die nächsten Jahrzehnte eröffnet die additive Fertigung die Möglichkeit für Hüftprothesen der nächsten Generation. Die Fortschritte könnten zu Implantaten führen, die langfristig eine natürlichere und gesündere Gelenkumgebung bieten.
Eine Möglichkeit sind geriffelte modulare Schäfte mit Mikrobewegungen, um die Belastung besser auf den Knochen zu übertragen. Nachgiebige Strukturen entkoppeln unerwünschte starre Schnittstellen zwischen Implantat und Gewebe. Gelenkige Hüftpfannen aus Schaumstoff können auch den schmierenden Flüssigkeitsfilm des natürlichen Knorpels nachbilden. Weitere Material- und Simulationsentwicklungen könnten Gelenke ermöglichen, die die echte Funktion des Bewegungsapparats nachahmen.
Die additive Fertigung ist zwar noch ein Konzept, aber sie ist das fehlende Herstellungsverfahren, um die Möglichkeiten einer künstlichen Hüfte neu zu überdenken. Neue Paradigmen der Gelenkwiederherstellung sind in Sicht.
Erleichterung von Forschung und Entwicklung
Ein großer Vorteil der additiven Fertigung ist die Möglichkeit, Designs schnell zu iterieren und Prototypen nach Bedarf zu drucken. Dies ist ein Segen für die orthopädische Forschung und Ausbildung. Ingenieure können Dutzende von Hüftkonzepten testen und von Chirurgen praktisches Feedback erhalten.
LPBF-Drucker geben effizient Testgeometrien aus Metall aus, die die Implantatleistung vollständig simulieren. Prototypen können an Kadavern oder Schaumstoffknochenmodellen getestet werden, bevor in die Werkzeugherstellung investiert wird. Für akademische Labore ermöglicht die additive Fertigung kostengünstige Forschungsarbeiten.
Die Agilität der additiven Fertigung beschleunigt die Entwicklung von Hüftimplantaten. Was früher Monate dauerte, um zwischen CAD und CNC zu wechseln, kann mit einem einzigen Drucker in wenigen Tagen geschehen. Es ist zu erwarten, dass die Verbindungen zwischen Universitäten und Geräteherstellern zunehmen werden, um 3D-gedruckte Innovationen in der Hüftchirurgie voranzutreiben.
Herausforderungen bei der additiven Fertigung von Hüftimplantaten
Die additive Fertigung ist zwar vielversprechend, doch stehen der vollständigen Einführung in der Hüftchirurgie noch technische Hürden im Wege:
- $erhöhte-Präzision$ Die Maßgenauigkeit und die Oberflächengüte müssen bei der additiven Fertigung verbessert werden, um den Normen für orthopädische Geräte zu entsprechen. Manchmal sind strengere Prozesskontrollen und Nachbearbeitungen erforderlich.
- $Materialien-Entwicklung$ – Es müssen mehr validierte, hüftspezifische Legierungen eingeführt werden. Diese benötigen maßgeschneiderte Zusammensetzungen und Eigenschaften für additive Verfahren.
- $Einhaltung der Rechtsvorschriften$ Additiv hergestellte Implantate erfordern strenge Testdaten und klinische Studien, um eine behördliche Zulassung zu erhalten und das Vertrauen der Patienten zu gewinnen.
- $design-expertise$ Um die Vorteile der additiven Fertigung zu maximieren, braucht man Erfahrung im Design für AM. Orthopädische Unternehmen brauchen Ingenieure und Analysten für additive Verfahren in ihren Reihen.
Die Zukunft der additiven Fertigung für Hüften
Die additive Fertigung spielt in der Hüftprothesenchirurgie eine immer wichtigere Rolle. Alles deutet darauf hin, dass die Akzeptanz mit fortschreitender technischer Verfeinerung zunimmt. Verbesserungen bei der Wiederholbarkeit, der Qualität und den Materialien werden es ermöglichen, dass die additive Fertigung das Design, den Bestand und die Lieferung von Implantaten vollständig verändert.
In Zukunft werden die meisten Hüftkomponenten personalisiert und auf Bestellung in 3D gedruckt werden. Krankenhäuser werden in der Regel eigene Produktionslabors für Implantate einrichten und sogar mobile Drucksysteme einsetzen. Die additive Fertigung wird sich von Hüften auf andere Gelenkersatzteile und Wirbelsäulenimplantate ausweiten. Der Durchsatz wird sich verbessern, da die Metall-3D-Drucker größer und schneller werden.
Insgesamt bietet das additive Verfahren ein enormes Potenzial für leistungsfähigere, langlebigere und leichter zugängliche Hüftprothesen. Der 3D-Druck bringt die nächste Innovationswelle zur Wiederherstellung einer natürlichen, schmerzfreien Gelenkfunktion. Die Zukunft sieht besser aus für die Millionen von Menschen weltweit, die an Hüftarthrose und -verschleiß leiden.
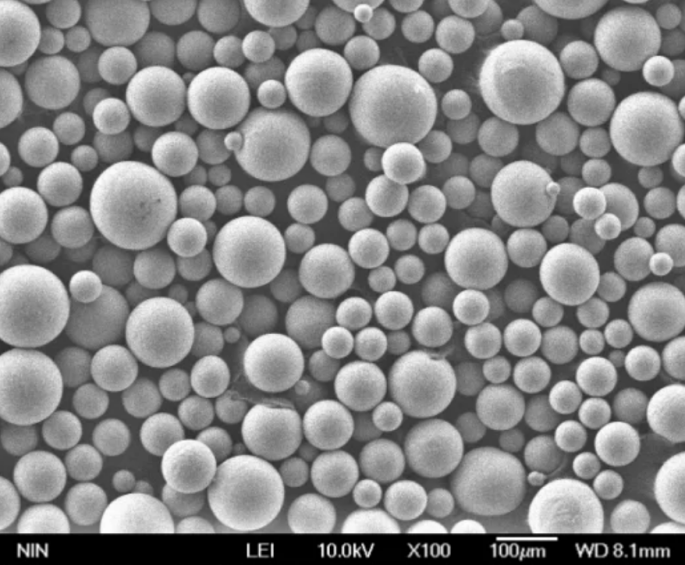
FAQ
Was sind die wichtigsten Vorteile des 3D-Drucks von Hüftimplantaten?
Die wichtigsten Vorteile der additiven Fertigung für Hüftimplantate sind:
- Individuelle Anpassung an die Anatomie und Knochenkonturen des Patienten
- Fähigkeit, komplexe Gitterstrukturen und Topologien zu erstellen
- Dezentralisierte Fertigung in Krankenhäusern auf Abruf
- Verbesserte Bestandsverwaltung ohne Überbestände an Implantatgrößen
- Fortschrittliche neue Legierungen und Materialzusammensetzungen
- Schnellere Design-Iteration durch Rapid Prototyping
Wie genau sind additiv gefertigte Hüftimplantate?
Die Maßgenauigkeit gedruckter Hüftimplantate aus Metall ist inzwischen mit der konventionellen Fertigung vergleichbar. Eine Nachbearbeitung wie die CNC-Bearbeitung verbessert die Toleranz und die Oberflächengüte weiter. Aktuelle Druckerauflösungen von 30-50 Mikrometern ermöglichen Implantate, die orthopädischen Standards entsprechen.
Sind 3D-gedruckte Hüftimplantate von der FDA zugelassen?
Mehrere additiv gefertigte Hüftprothesenkomponenten haben die 510(k)-Zulassung der FDA erhalten. Bemerkenswerte Beispiele sind die personalisierten Tritanium-Hüften von Zimmer Biomet, das Tritanium-C-Hüftsystem von Stryker und die Jazz-Implantate von Adler Ortho. Weitere Zulassungen sind zu erwarten, da sich die Qualität der Additive und die Daten weiter verbessern.
Übernimmt die Versicherung individuelle 3D-gedruckte Hüften?
Viele Versicherer übernehmen die Kosten für patientenangepasste Hüften, die im 3D-Metalldruckverfahren hergestellt werden. Sie gelten immer noch als Spezialimplantate, so dass bei Tarifen mit höherem Selbstbehalt mehr Kosten anfallen können. Mit zunehmender Akzeptanz wird erwartet, dass die Kostenübernahme wie bei herkömmlichen Hüftkomponenten von der Stange zur Routine wird.
Kann man Hybridhüften aus Metall und Polymer im 3D-Druck herstellen?
Ja, führende orthopädische Unternehmen entwickeln aktiv hybride additive Verfahren zur Herstellung von Metall-Kunststoff-Hüftimplantaten. Der direkte Metalldruck für den Femurschaft wird mit dem Spritzgießen einer gedruckten Kunststoffschale kombiniert. Dadurch wird eine Knochenintegration auf der Schaftseite erreicht. Die hybride Fertigung zielt darauf ab, die konventionellen Hüftkonstruktionsmethoden zu verändern.
Wie viel kostet eine 3D-gedruckte Hüftprothese?
Die derzeitigen Preise für eine 3D-gedruckte Hüftprothese liegen in den Vereinigten Staaten bei durchschnittlich 5000-7500 $. Das sind 15-20 % mehr als für ein herkömmliches Implantat. Die Vorteile wie schnellere Operationen, weniger Instrumente und keine unnötigen Lagerbestände gleichen diesen Aufpreis jedoch aus. Mit zunehmender Verbreitung werden die Preise für gedruckte Implantate voraussichtlich mit denen herkömmlicher Methoden gleichziehen.