Metal tozu atomizörü nedir ve nasıl çalışır?
A metal tozu atomizörü çeşitli atomizasyon teknikleri kullanarak dökme metalleri ince tozlara dönüştüren bir endüstriyel ekipman parçasıdır. Bu tozlar, eklemeli üretim, metalurji ve diğerleri gibi çeşitli uygulamalarda yaygın olarak kullanılmaktadır.
- Çalışma Prensibi: Atomizör, metali eriterek ve ardından ince parçacıklar üretmek için metal akışını hızla soğutup katılaştırarak çalışır.
- Atomizer Çeşitleri:
- Su Atomizasyonu: Erimiş metali parçalamak için yüksek basınçlı su kullanır.
- Gaz Atomizasyonu: Yüksek basınçlı inert gaz kullanır.
- Santrifüj Atomizasyonu: Dönme kuvvetlerini kullanır.
- Uygulamalar:
- Katmanlı Üretim
- Metalurji
- Kaplama süreçleri
- Havacılık ve uzay bileşenleri
- Avantajlar:
- Tek tip ve yüksek kaliteli tozlar üretir.
- Partikül boyutu ve dağılımı üzerinde kontrol sağlar.
- Büyük ölçekli üretim için verimli ve uygun maliyetli.
- Zorluklar:
- Önemli ölçüde enerji gerektirir.
- Elde edilen tozun özelliklerini etkileyebilecek kirletici maddelere karşı hassastır.
- Kullanılan Malzemeler: Titanyum, alüminyum, çelik ve değerli metaller dahil olmak üzere hemen hemen her metal atomize edilebilir.
Tip | Soğutma Ortamı | Uygulamalar |
---|---|---|
Su Atomizasyonu | Su | Genel metalurji, daha az reaktif metaller |
Gaz Atomizasyonu | İnert Gaz | Katmanlı üretim, reaktif metaller |
Santrifüj Atomizasyonu | Merkezkaç kuvveti | Yüksek saflıkta metaller, özel uygulamalar |
- Bir atomizörün seçimi, istenen partikül boyutuna, morfolojisine ve amaçlanan uygulamaya bağlıdır.
- Atomizörler sağlam olacak ve farklı erime noktalarına sahip farklı metal türlerini işleyebilecek şekilde tasarlanmıştır.
- Ekipmanın uzun ömürlü ve verimli olmasını sağlamak için bakım ve düzenli kontroller hayati önem taşır.
- Verimliliği artırmak ve maliyetleri düşürmek için bu alanda sürekli olarak yenilikler yapılmaktadır.
Modern endüstrilerde metal tozlarının üretimi neden önemlidir?
Metal tozlarının üretimi, çok yönlülüğü ve uyarlanabilirliği nedeniyle gelişmekte olan ve yerleşik birçok endüstri için bir köşe taşıdır.
- Katmanlı Üretim: Genellikle 3D baskı olarak bilinen bu yöntemde birincil hammadde olarak metal tozları kullanılır. Bu tozların katmanları, karmaşık tasarımlar oluşturmak için lazerler kullanılarak kaynaştırılır.
- Metal Enjeksiyon Kalıplama (MIM): Bir polimer bağlayıcı ile birleştirilmiş metal tozları parçalar halinde kalıplanabilir ve daha sonra sinterlenebilir.
- Havacılık ve Otomotiv: Hafif ve yüksek mukavemetli bileşenler genellikle metal tozlarından yapılır.
- Tıbbi Cihazlar: Titanyum tozlarından yapılan ortopedik implantlar, biyouyumlulukları nedeniyle popüler hale gelmektedir.
- Elektronik Bileşenler: Metal tozları, iletkenlik özellikleri nedeniyle elektronikte bileşen yapmak için kullanılır.
Endüstri | Metal Tozlarının Kullanımı |
---|---|
Katmanlı Üretim | Katman katman karmaşık parçalar oluşturma |
Havacılık ve Uzay | Hafif bileşenler |
Tıbbi | İmplantlar ve protezler |
Elektronik | İletken bileşenler |
- Tozların boyut ve şeklindeki homojenlik, tutarlı malzeme özellikleri sağlar.
- Metal tozları üretim süreçlerinde daha az atık oluşmasını sağlar.
- Hurda metallerin yeniden kullanımı ve geri dönüşümü için bir yol sunar.
- Metal tozlarının çok yönlülüğü, belirli özelliklere sahip malzemeler oluşturmak için birleştirilebilecekleri veya alaşım haline getirilebilecekleri anlamına gelir.
- 3D baskı gibi sektörlerdeki büyümeyle birlikte, yüksek kaliteli metal tozlarına olan talep de artacak.
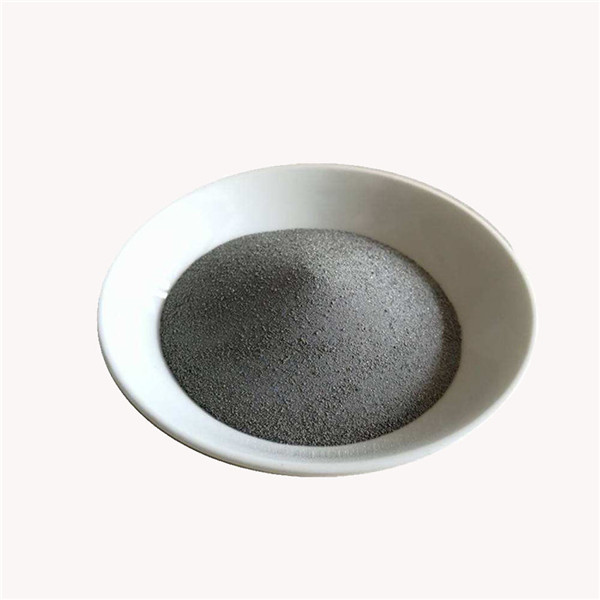
Metal tozları partikül boyutlarına ve morfolojilerine göre nasıl kategorize edilir?
Parçacık boyutu ve morfolojisi, çeşitli uygulamalarda metal tozlarının davranışını belirlemede çok önemli bir rol oynamaktadır.
- Partikül Boyut Aralıkları:
- Ultrafine: <5 mikrometre
- Güzel: 5-30 mikrometre
- Kaba: >30 mikrometre
- Morfolojiler:
- Küresel: Eşit paketleme ve akış nedeniyle birçok uygulama için tercih edilir.
- Düzensiz: Bazı atomizasyon yöntemlerinden veya öğütmeden elde edilen sonuçlar.
- Pul benzeri: İnce ve düz, genellikle boyalarda kullanılır.
- İstenen uygulama genellikle partikül boyutunu ve şeklini belirler. Örneğin, küresel tozlar akış özellikleri nedeniyle eklemeli üretim için idealdir.
- Farklı atomizasyon yöntemleri farklı morfolojiler ortaya çıkarır. Örneğin, gaz atomizasyonu genellikle küresel partiküllerle sonuçlanır.
- Partikül boyutu dağılımı hayati önem taşır. İşleme sırasında tutarlı davranışa yol açtığı için dar bir dağılım tercih edilir.
Morfoloji | Tipik Üretim Yöntemi | Uygulamalar |
---|---|---|
Küresel | Gaz Atomizasyonu | Katmanlı Üretim, MIM |
Düzensiz | Su Atomizasyonu, Frezeleme | Genel Metalurji |
Pul benzeri | Öğütme | Boyalar, Kaplamalar |
- Metal tozlarını karakterize etmek için lazer kırınımı ve mikroskopi gibi analitik yöntemler kullanılır.
- Partikül şekli sıkıştırılabilirlik, reaktivite ve sinterlenebilirlik gibi özellikleri etkiler.
- Bazı uygulamalar, istenen özellikleri elde etmek için farklı partikül boyutları ve şekillerinin bir karışımını gerektirir.
- Depolama ve taşıma yöntemleri partikül boyutuna göre değişir. Örneğin ultra ince tozlar aglomerasyona daha yatkındır.
- Üretim yöntemlerindeki yenilikler, daha tutarlı ve arzu edilen partikül boyutları ve şekilleri elde etmeyi amaçlamaktadır.
Metal tozu üretiminin çevresel etkileri nelerdir?
Metal tozu üretiminin çevresel etkileri çok yönlüdür, faydaları ve potansiyel dezavantajları ile iç içe geçmiştir.
- Atıklarda Azalma: Metal tozları kullanan eklemeli üretim gibi süreçlerin hassas yapısı, daha az malzeme israfına neden olur.
- Enerji Tüketimi: Atomizasyon prosesi, özellikle gaz atomizasyonu, enerji yoğundur ve karbon ayak izinin artmasına neden olur.
- Su Kullanımı: Su atomizasyonu önemli miktarda su kullanır, ancak birçok modern sistemde bu su geri dönüştürülür.
- Hava Emisyonları: Proses, hava kirliliğini önlemek için uygun şekilde yönetilmesi gereken metal dumanları ve partikülleri açığa çıkarabilir.
- Kaynak Tükenmesi: Toz üretimi için belirli metallere olan talebin artması, bu kaynakların daha hızlı tükenmesine yol açabilir, ancak geri dönüşüm bunu azaltabilir.
- Yan Ürünlerin Bertarafı: Cürufların ve diğer yan ürünlerin toprak ve su kirliliğini önlemek için uygun şekilde bertaraf edilmesi gerekir.
- Ulaşım: Ham metallerin ve bitmiş tozların taşınması karbon ayak izini artırır.
- Gürültü Kirliliği: Atomizasyon süreçleri, özellikle yeterince yönetilmediği takdirde, gürültü kirliliğine katkıda bulunabilir.
- Sürdürülebilirlik için Fırsatlar: Süreci daha enerji verimli ve sürdürülebilir hale getirmeyi amaçlayan sürekli araştırma ve yenilikler yapılmaktadır.
- Yönetmelikler: Birçok ülkede metal tozu üretiminin çevreye en az etkiyle yapılmasını sağlamak için katı düzenlemeler bulunmaktadır.
Metal tozlarının kalitesi nasıl sağlanabilir?
Metal tozlarında birinci sınıf kalitenin sağlanması, uygulamaları için çok önemlidir.
- Kaynak Malzeme: Başlangıç metalinin saflığı, elde edilen tozun kalitesini önemli ölçüde etkiler.
- Atomizasyon Süreci: Atomizasyon sırasında tutarlı sıcaklık ve basınç kontrolü çok önemlidir.
- Parçacık Boyutu Analizi: Lazer difraksiyonu gibi teknikler tutarlı partikül boyutlarını ölçer ve sağlar.
- Morfoloji İncelemesi: Mikroskobik teknikler partiküllerin şeklini ve yapısını inceler.
- Kimyasal Analiz: Bileşimi belirlemek ve istenmeyen unsurların bulunmadığından emin olmak için.
Kalite Kontrol | Teknik/Yöntem |
---|---|
Parçacık Boyutu | Lazer Kırınımı |
Morfoloji | Taramalı Elektron Mikroskobu |
Kompozisyon | Spektroskopi |
- Toplu Test: Üretilen her parti, sevkiyattan önce kalite açısından test edilebilir.
- Geri Bildirim Döngüsü: Son kullanıcılardan gelen sürekli geri bildirimler kaliteyi artırmak için kullanılabilir.
- Düzenli Ekipman Bakımı: Üretimde tutarlılığı sağlar.
- Eğitim: İşçiler ve teknisyenler iyi eğitimli olmalıdır.
- Sertifikalar: ISO ve diğer sertifikalar kaliteyi korumak için kılavuzlar sağlar.
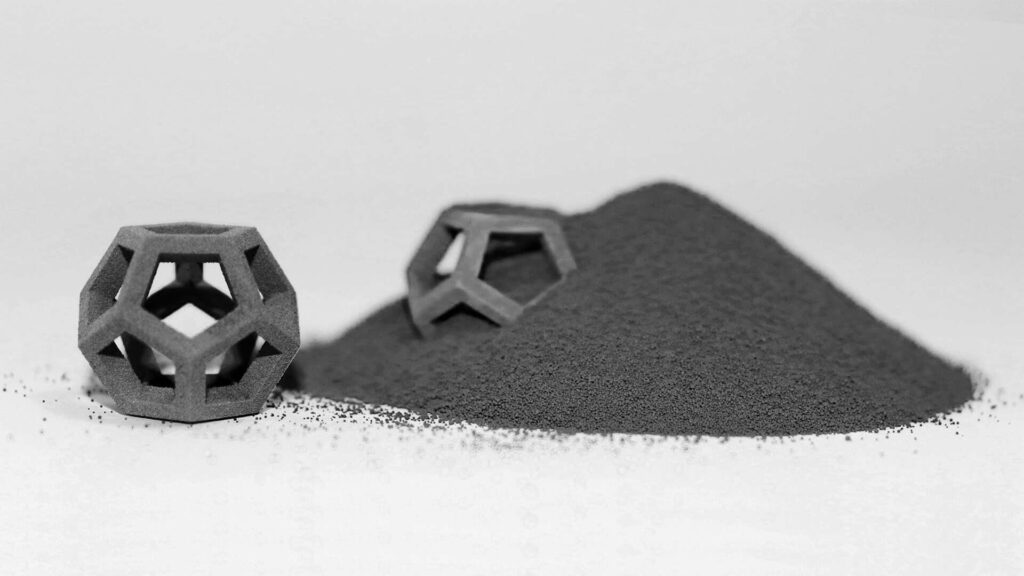
Metal tozları eklemeli imalatın büyümesine nasıl katkıda bulunuyor?
Genellikle 3D baskı olarak adlandırılan eklemeli üretim, özünde metal tozlarına bağlıdır.
- Malzeme Hassasiyeti: İnce tozlar, yüksek hassasiyetle karmaşık tasarımlara olanak tanır.
- Karmaşık Geometriler: Daha önce imkansız veya çok karmaşık olduğu düşünülen tasarımlar artık gerçekleştirilebilir.
- Azaltılmış Atık: Sadece gerekli miktarda malzeme kullanılır.
- Hızlı Prototipleme: Test ve doğrulama için prototiplerin hızlı üretimi.
- Özelleştirme: Medikalden havacılığa kadar sektörler için özel çözümler.
Avantaj | Metal Tozları Nasıl Katkıda Bulunur? |
---|---|
Tasarım Esnekliği | Geleneksel kısıtlamalar olmadan karmaşık geometrilere izin verir |
Hız | Hızlı katman katman yapı |
Malzeme Verimliliği | En aza indirilmiş atık |
- Malzeme Özellikleri: Metal tozlarının karıştırılmasıyla belirli özelliklerin elde edilmesi.
- Tedarik Zinciri Verimliliği: Yerelleştirilmiş üretim nakliye ihtiyaçlarını azaltır.
- Maliyet Verimliliği: Azaltılmış malzeme atığı, daha az maliyet anlamına gelir.
- Sürdürülebilirlik: Karbon ayak izini azaltma potansiyeli.
- Gelecek Potansiyeli: Yeni metal tozu alaşımlarının kombinasyonu, benzeri görülmemiş özelliklere sahip malzemelerin ortaya çıkmasını sağlayabilir.
Metal tozlarını taşırken ve depolarken güvenlikle ilgili endişeler nelerdir?
Metal tozlarının taşınması ve depolanması doğal riskleri de beraberinde getirir.
- Soluma Riski: İnce tozlar solunabilir ve sağlık riskleri oluşturabilir.
- Patlama Tehlikesi: Bazı metal tozları havada dağıldıklarında patlayıcı olabilirler.
- Yangın Riski: Bazı metal tozları tutuşabilir.
- Cilt Teması: Tahrişe veya alerjik reaksiyonlara yol açabilir.
- Göz Teması: Metal tozları gözde tahrişe veya yaralanmaya neden olabilir.
Risk | Önleme |
---|---|
Soluma | Maske ve havalandırma kullanımı |
Patlama | Uygun depolama, topraklama |
Yangın | Tutuşturucu kaynaklardan uzakta depolayın |
- Depolama Koşulları: Serin ve kuru yerlerde uygun etiketleme ile saklayın.
- Eğitim: Çalışanlar riskler ve güvenli kullanım prosedürleri konusunda eğitilmelidir.
- Ekipman: Eldiven, maske ve koruyucu gözlük kullanımı.
- Acil Durum Protokolleri: Dökülme, yangın veya maruz kalma durumunda açık prosedürler.
- Bertaraf: Kullanılmış veya dökülmüş tozlar yönetmeliklere uygun olarak bertaraf edilmelidir.
Metal tozlarının maliyeti nasıl belirlenir?
Metal tozlarının maliyetini birden fazla faktör belirler.
- Hammadde Maliyeti: Kaynak metalin maliyeti.
- İşlem Maliyetleri: Atomizasyona dahil olan enerji, ekipman ve işgücü.
- Saflık: Daha yüksek saflık genellikle daha yüksek bir fiyat anlamına gelir.
- Partikül Boyutu ve Dağılımı: İnce tozlar daha pahalı olabilir.
- Arz ve Talep: Ekonomik faktörler önemli bir rol oynamaktadır.
Faktör | Maliyet Üzerindeki Etkisi |
---|---|
Saflık | Daha yüksek saflık = Daha yüksek maliyet |
Üretim Hacmi | Toplu üretim = Düşük maliyet |
- Ulaşım: Nakliye ve taşıma ile ilgili maliyetler.
- Depolama: Özellikle belirli koşullar altında depolamaya ilişkin maliyetler.
- R&D: Yenilikler ve araştırmalar maliyeti artırabilir.
- Mevzuata Uygunluk: Standartları karşılamak üretim maliyetlerini artırabilir.
- Pazar Rakipleri: Rakiplerin varlığı fiyatlandırmayı etkileyebilir.
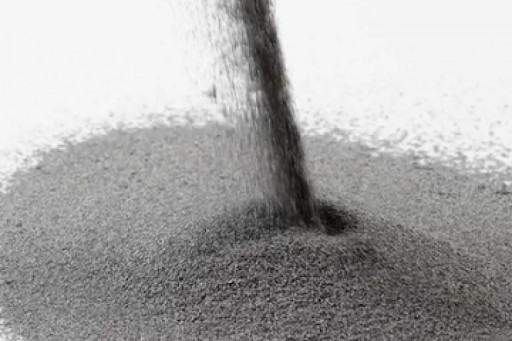
Metal tozu üretiminin geleceğini hangi yenilikler şekillendiriyor?
Metal tozu endüstrisi durağan değildir ve sürekli ilerlemeler geleceğini şekillendirmektedir.
- Geliştirilmiş Atomizasyon Teknikleri: Daha iyi partikül kontrolü ile daha verimli yöntemler.
- Sürdürülebilirlik: Karbon ayak izini azaltan çevre dostu yöntemler.
- Yeni Malzeme Kombinasyonları: Geliştirilmiş özelliklere sahip alaşımlar.
- Geri Dönüşüm Yenilikleri: Atıkları verimli bir şekilde tekrar kullanılabilir tozlara dönüştürür.
- Dijital Entegrasyon: Üretim ve kalite kontrolde IoT ve yapay zeka.
İnovasyon | Etki |
---|---|
YAPAY ZEKA | Geliştirilmiş kalite kontrol |
Çevre dostu yöntemler | Azaltılmış çevresel etki |
- Özel Üretim: Özel müşteri ihtiyaçları için tozların uyarlanması.
- Enerji Verimliliği: Atomizasyon için gereken enerjide azalma.
- Maliyet Azaltma Teknolojileri: Yüksek kaliteli tozları daha uygun fiyatlı hale getirmek.
- Kalite Kontrol Araçları: Daha iyi kalite güvencesi için gelişmiş analitik araçlar.
- Güvenlik İyileştirmeleri: Daha güvenli üretim ve kullanım sağlayan teknolojiler.
Metal tozu üretimi geleneksel metalürjiye kıyasla nasıldır?
Metal tozu üretimini geleneksel metalürji ile karşılaştırmak, her iki yöntemin kendine özgü nitelikleri hakkında fikir verir:
- Üretim Yöntemi: Geleneksel metalürjide genellikle döküm veya dövme kullanılırken, metal tozu üretimi atomizasyon süreçlerine odaklanır.
- Malzeme Kullanımı: Metal tozu üretimi, eklemeli imalat gibi uygulamalarda hassasiyet nedeniyle genellikle daha az malzeme israfına yol açabilir.
- Enerji Tüketimi: Her iki süreç de enerji yoğun olsa da, belirli atomizasyon yöntemleri daha fazla enerji tüketebilir.
- Tasarımda Esneklik: Metal tozları ile, özellikle eklemeli imalatta daha fazla esneklik vardır ve karmaşık tasarımlara izin verir.
- Malzeme Özellikleri: Geleneksel metalürji, dökme metallerin doğası gereği bazen daha iyi mekanik özellikler elde edebilir.
Karşılaştırma Noktası | Geleneksel Metalurji | Metal Tozu Üretimi |
---|---|---|
Üretim Yöntemi | Döküm, Dövme | Atomizasyon |
Tasarım Esnekliği | Sınırlı | Yüksek |
Malzeme Verimliliği | Değişken | Genellikle Daha Yüksek |
- Üretim Süresi: Metal tozu üretimi, özellikle hızlı eklemeli imalat teknikleriyle birleştirildiğinde daha hızlı olabilir.
- Maliyet: Maliyetler değişebilir, ancak ince metal tozları üretmek bazen dökme metal üretiminden daha pahalı olabilir.
- Uygulama Aralığı: Geleneksel metalürji temel endüstriyel ihtiyaçlara hizmet ederken, havacılık, medikal ve otomotiv gibi özel sektörlerde metal tozu kullanımı artmaktadır.
- Çevresel Etki: Her ikisinin de çevresel kaygıları vardır, ancak eklemeli üretimde metal tozunun yerelleştirilmiş doğası ulaşımla ilgili etkileri azaltabilir.
- Gelecek Potansiyeli: Endüstriler eklemeli üretimin potansiyelini fark ettikçe, metal tozu üretimine olan talebin ve öneminin artması muhtemeldir.
Metal tozlarının endüstrilerdeki başlıca uygulamaları nelerdir?
Metal tozları çeşitli sektörlerde sayısız uygulama alanı bulmuştur:
- Katmanlı Üretim: Nesnelerin katman katman inşa edildiği 3D baskı olarak da bilinir.
- Metalurjik Süreçler: Toz metalurjisi işlemleri, katı metal nesneler oluşturmak için sinterleme ve preslemeyi içerir.
- Tıbbi İmplantlar: Karmaşık tasarımlara sahip özelleştirilmiş tıbbi implantlar oluşturmak için.
- Havacılık ve Uzay: Hafif ancak dayanıklı bileşenlerin üretiminde.
- Otomotiv: Daha hafif ve aynı derecede sağlam olabilen parçalar üretmek için.
Endüstri | Uygulama |
---|---|
Tıbbi | İmplantlar, Protezler |
Havacılık ve Uzay | Motor parçaları, Yapısal bileşenler |
Otomotiv | Dişli parçaları, Yapısal çerçeveler |
- Elektronik: Bazı elektronik bileşenlerin ve lehim malzemelerinin üretiminde.
- Takı: Katmanlı üretim yoluyla karmaşık mücevher tasarımları oluşturma.
- Enerji: Özellikle yakıt hücreleri gibi yenilenebilir enerji bileşenlerinde.
- Araştırma ve Geliştirme: Yeni malzeme kombinasyonları ve özelliklerinin denenmesi.
- Kataliz: Metal tozları çeşitli kimyasal proseslerde katalizör görevi görebilir.
Makalelerdeki bilgileri özetleyen tablo:
Konu | Kısa Açıklama |
---|---|
Çevresel Etkiler | Metal tozu üretiminin ekolojik ayak izini ve azaltımlarını ele alır. |
Kalite Güvence | Metal tozlarında birinci sınıf kalite sağlamak için yöntem ve stratejileri tartışır. |
Katmanlı İmalata Katkı | Metal tozlarının 3D baskıda nasıl devrim yarattığını araştırıyor. |
Güvenlik Endişeleri | Metal tozlarıyla çalışırken karşılaşılabilecek riskleri ve güvenlik protokollerini vurgular. |
Maliyet Belirleyicileri | Metal tozlarının fiyatlandırılmasını etkileyen faktörleri araştırır. |
Gelecekteki Yenilikler | Metal tozu üretimindeki gelişmeleri tahmin eder. |
Geleneksel Metalurji ile Karşılaştırma | Metal tozu üretimini eski metal yapım teknikleriyle karşılaştırır. |
Endüstriyel Uygulamalar | Metal tozlarının gücünden yararlanan çeşitli sektörleri araştırır. |
SSS
1. Metal tozu üretiminde kullanılan başlıca yöntem nedir?
Kullanılan ana yöntem, sıvı bir metal akışının tozlar halinde katılaşan ince damlacıklara ayrıldığı atomizasyondur.
2. Metal tozu üretimi ile ilgili çevresel kaygılar var mı?
Evet, endişeler arasında enerji tüketimi, su kullanımı, hava emisyonları ve atık üretimi yer alıyor. Ancak, birçok süreç sürdürülebilirlik için iyileştirilmektedir.
3. Metal tozlarının kalitesi uygulamalarını nasıl etkiler?
Saflık ve partikül boyutu da dahil olmak üzere kalite, özellikle eklemeli imalatta nihai ürünün performansını, gücünü ve yüzeyini doğrudan etkiler.
4. Metal tozları eklemeli üretim için neden çok önemlidir?
Metal tozları, 3D baskıda yüksek hassasiyet, tasarım esnekliği ve karmaşık geometrilerin gerçekleştirilmesine olanak tanır.
5. Metal tozlarının işlenmesinde güvenlik riskleri var mı?
Evet, riskler arasında soluma, patlama veya yangın potansiyeli ve cilt veya göz teması yer alır.
daha fazla 3D baskı süreci öğrenin
Frequently Asked Questions (Supplemental)
1) Which atomization method should I choose for highly reactive alloys like Ti or Al?
- Inert gas atomization (IGA) or plasma/centrifugal routes. They provide low oxygen/nitrogen pickup and near-spherical morphology needed for additive manufacturing. Avoid water atomization for highly reactive metals due to oxidation and hydrogen pickup.
2) What powder specs matter most for LPBF vs MIM?
- LPBF: high sphericity, narrow PSD (e.g., D10/50/90 ≈ 15/30/45 μm), low satellites, very low O/N/H, good apparent/tap density. MIM: finer PSD (D50 ≈ 10–18 μm), flow stability (Hausner ≤1.20), controlled oxygen for sinterability.
3) How do I quantify and control oxygen/nitrogen in powders from a metal powder atomizer?
- Use inert-gas fusion per ASTM E1019 for O/N/H. Control via VIM feedstock, low O2/H2O in atomization gas (<10–20 ppm), hot gas filtration, and rapid post-atomization passivation under dry inert conditions.
4) Can recycled powder be safely blended back for AM?
- Yes, with a powder passport: sieve to spec, remove spatter/inclusions, monitor PSD, flow, O/N/H, and satellite content. Typical validated blend-back is 10–30% with mechanical/fatigue and CT confirmation.
5) What are typical yield and energy benchmarks for a modern metal powder atomizer?
- For gas atomization of AM-grade alloys: yield into target PSD often 45–65%; specific energy 4–9 kWh/kg depending on alloy, melt method, and gas recovery. Recirculating argon systems reduce gas cost and footprint.
2025 Industry Trends and Data
- Argon recirculation and O2/H2O scrubbing are mainstream, cutting gas usage 30–50% and lowering interstitials.
- Digital powder passports link lot chemistry, PSD, and morphology to in‑situ AM monitoring for faster qualification.
- Growth in copper and aluminum AM powders driven by green/blue laser adoption and electrification demand.
- ESG reporting expands: suppliers disclose recycled content (metal + packaging) and EPDs for atomized powders.
- AI-based process control: closed-loop adjustments of melt temperature, gas pressure, and nozzle ΔP stabilize PSD.
KPI (metal powder atomizer performance), 2025 | 2023 Baseline | 2025 Typical/Target | Why it matters | Sources/Notes |
---|---|---|---|---|
Oxygen in AM‑grade Ti/Al powders (wt%) | Ti: 0.12–0.18; Al: 0.08–0.12 | Ti: 0.08–0.12; Al: 0.04–0.08 | Mechanical integrity, porosity | ASTM E1019; supplier QC |
Target PSD yield (AM window, %) | 35–55 | 45–65 | Cost/yield | İşlem optimizasyonu |
Gas consumption (argon, Nm3/kg) | 8–12 | 5–8 | Operating cost/ESG | Argon recirc systems |
Satellite count (≥5 μm per 100 particles) | 4–6 | 2–3 | Spreadability, defects | SEM image analysis |
As‑atomized sphericity (aspect ratio) | 0.90–0.94 | 0.94–0.97 | Flow/packing | Optical/SEM metrics |
Disclosed recycled content in powders (%) | Sınırlı | 10–30 | ESG, cost | EPD/LCA reports |
Lot acceptance with digital passports | Gelişmekte olan | Ortak | Faster qualification | Aerospace/medical RFQs |
Authoritative resources:
- ISO/ASTM 52907 (metal powder characterization), 52904 (PBF practice): https://www.iso.org
- ASTM B822/B214 (PSD), B212/B213 (density/flow), B923 (helium pycnometry), E1019 (O/N/H): https://www.astm.org
- NIST AM Bench datasets and monitoring research: https://www.nist.gov/ambench
- NFPA 484 (combustible metals) and ISO 80079 (explosive atmospheres): https://www.nfpa.org
Latest Research Cases
Case Study 1: Argon‑Recirculating Gas Atomizer for Low‑Oxygen Aluminum AM Powders (2025)
- Background: An AM powder supplier needed to reduce oxygen and operating cost for 6xxx/2xxx Al powders.
- Solution: VIM feedstock + closed‑loop argon recirculation with dual-bed O2/H2O scrubbers; inline thermal mass flow control; rapid inert passivation; SPC on PSD and O/N/H.
- Results: Oxygen reduced from 0.10–0.12 wt% to 0.05–0.07 wt%; argon usage −38%; target PSD yield +9 pp; LPBF density 99.8–99.9% with improved melt stability.
Case Study 2: Hybrid Centrifugal + Gas Atomization for High‑Conductivity Copper Powders (2024)
- Background: Electrification customer sought highly spherical Cu powders for LPBF with green lasers.
- Solution: Pre‑atomization via centrifugal disk for coarse breakup, followed by fine gas atomization; hot gas drying and oxide control; surface oxide assessment via XPS.
- Results: Sphericity improved to AR 0.96; oxide thickness −35%; as‑built conductivity +8–10% vs. prior lot; defect rate −25% with identical LPBF parameters.
Expert Opinions
- Prof. Leif Karlsson, Professor of Materials and Manufacturing, University West
- Viewpoint: “Controlling the melt stream stability and gas‑to‑metal ratio is foundational—most PSD drift starts at the tundish and nozzle, not at the cyclone.”
- Dr. Brandon Lane, Research Engineer, NIST
- Viewpoint: “Linking atomizer lot data to in‑situ AM sensing shortens qualification and flags powder anomalies before costly builds.”
- Dr. Martina Zimmermann, Head of Additive Materials, Fraunhofer IWM
- Viewpoint: “ESG transparency—argon recirculation, recycled feed, and documented interstitial control—is becoming a purchasing criterion, not just a nice‑to‑have.”
Affiliation links:
- University West: https://www.hv.se/en
- NIST (Additive Manufacturing): https://www.nist.gov
- Fraunhofer IWM: https://www.iwm.fraunhofer.de
Practical Tools/Resources
- Process and QC: ISO/ASTM 52907; ASTM B212/B213/B214/B822; ASTM B923; ASTM E1019
- Monitoring/analytics: Inline O2/H2O analyzers for process gas; capillary rheometry for flow; SEM and image analysis for satellites/sphericity
- Design/simulation: Ansys/CFD for nozzle and gas‑flow design; Thermo‑Calc for alloy solidification; discrete element modeling (DEM) for spreadability
- Databases: Senvol Database (https://senvol.com/database); MatWeb (https://www.matweb.com); MPIF resources (https://www.mpif.org)
- Safety: NFPA 484 handling guidance; ISO 80079 explosive atmospheres; supplier SDS and PPE/SOP templates
Last updated: 2025-08-22
Changelog: Added 5 supplemental FAQs focusing on atomization selection, specs, interstitial control, and reuse; introduced 2025 KPI table and trend insights for metal powder atomizer performance; provided two case studies (argon‑recirculating Al powders; hybrid Cu atomization); included expert viewpoints with affiliations; compiled practical tools/resources.
Next review date & triggers: 2026-02-01 or earlier if ISO/ASTM/NFPA standards update, major OEMs revise AM powder oxygen/spec windows, or new datasets on argon recirculation and in‑situ monitoring links to powder quality are published.