電気ビーム製造 は、レーザー、電子ビーム、プラズマアークなどの集中エネルギー源を利用して、材料を選択的に溶融、融解、気化させるさまざまな製造プロセスを指す。エネルギー源を精密に制御することで、これらのプロセスは、熱歪みを最小限に抑えながら、極めて正確で再現性の高い製造を可能にする。電気ビーム製造は、従来の減法的製造技術では達成できなかった複雑な形状やマイクロスケールの特徴の製造を可能にします。
電気ビーム製造プロセスの仕組み
電気ビーム製造は、エネルギー密度と熱伝導の原理に依存している。エネルギーを極めて狭いビームに集中させることにより、非常に高いエネルギー密度を達成することができる。この集中したエネルギーが材料と相互作用するとき、溶融または気化するのはわずかな体積だけです。熱は、この小さな相互作用体積から、より低温に保たれる周囲の材料へと素早く放散される。これにより、極めて正確かつ局所的な材料の溶融、融解、気化が可能になります。
電気ビームの製造にはいくつかの一般的なタイプがある:
レーザービーム製造
- 高集光レーザービームをエネルギー源として使用
- レーザービームは0.01mm以下に集光可能
- 非常に高い精度と熱歪みの最小化が可能
- 溶接、切断、クラッディング、積層造形などに使用。
電子ビーム製造
- エネルギー源として集束した電子ビームを使用
- 電子ビームは0.1mmまで集束可能
- 真空環境での作業が可能
- 溶接、積層造形などに使用。
プラズマアーク製造
- エネルギー源としてプラズマジェットを使用
- プラズマアークは高エネルギー密度
- 金属のキーホール溶接が可能
- 高浸透溶接および切断に使用
どのような場合でも、ワークピースやビーム源はCNC制御によって動かされ、目的の形状をトレースする。コンピュータ制御と自動化により、この工程は高い再現性と一貫性を保つことができる。
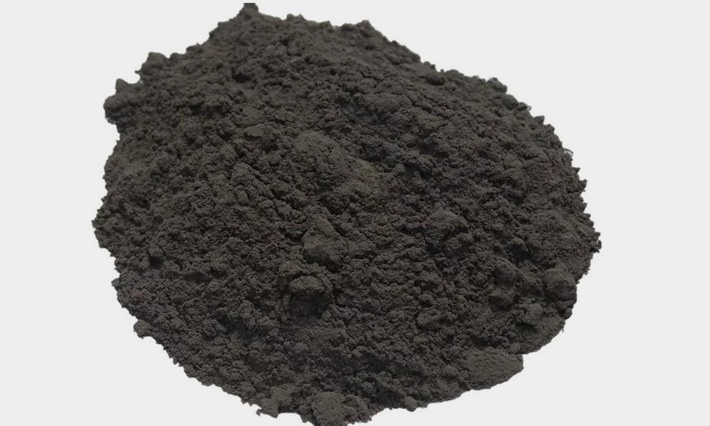
電気ビーム製造の利点とは?
従来の製造方法と比較して、電気ビーム製造にはいくつかの利点がある:
- 究極の精度 高度に集束されたエネルギー・ビームにより、0.01 mmまでのフィーチャー・サイズと公差が可能です。これにより、マイクロスケールのコンポーネントやエレクトロニクスが可能になります。
- 最小限の熱歪み 一度に溶融される材料は少量です。これにより、急速冷却が可能になり、有害な熱影響が最小限に抑えられます。部品の反りや歪みが少なくなります。
- 工具不要 エネルギー・ビームは本質的に工具の役割を果たし、物理的な工具を必要としません。これにより、迅速なプロトタイピングと設計の反復が可能になります。
- 高い再現性 – CNC制御のビームは、大量生産に適した極めて一貫性のある反復加工を可能にします。
- 力やストレスがない – 物理的な接触がないため、デリケートな構造を損傷することなく作ることができる。内部形状も可能です。
- 優れた冶金学的特性 急速な冷却速度は、微細な構造とユニークな材料特性を作り出すことができる。
- 幅広い材料適合性 – 金属、ポリマー、複合材料、およびセラミックは、適切なパラメータを選択することでうまく処理できます。
これらの利点により、電気ビーム製造は、他の方法では容易に製造できない幅広い用途に使用できる。このプロセスは、精度、再現性、費用対効果において改善され続けている。
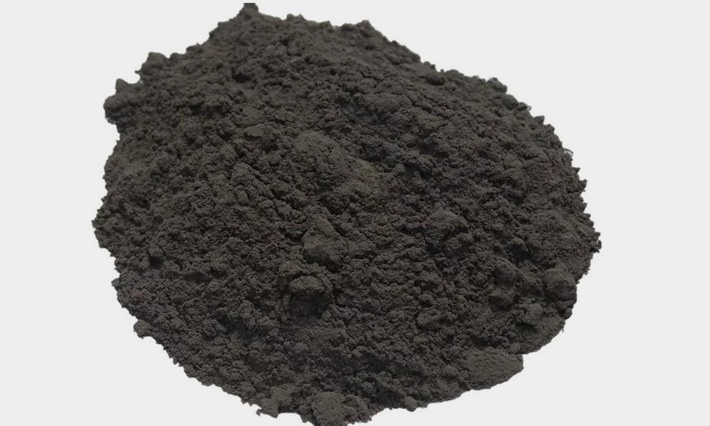
加工可能な素材は?
多くの異なる材料が電気ビーム製造に対応している:
金属 鋼鉄、アルミニウム、チタン、ニッケル合金など、一般的な金属はすべて加工できます。合金や温度が異なると、パラメータの調整が必要になる場合があります。ファイバーレーザーは、銅や金のような反射率の高い材料で利点を提供します。
ポリマー – 高出力レーザは、溶接や積層造形のために広範囲の熱可塑性ポリマーを選択的に溶融することができる。PTFEのような一部のポリマーは、特殊なビーム源を必要とします。
複合材料 繊維強化ポリマーは、繊維への熱損傷を避けるようにパラメータを制御すれば、限られた範囲で加工できる。
セラミックス セラミック材料は、耐火性で熱伝導性が低いため、加工には非常に特殊な高出力レーザが必要である。
シリコン – レーザーは、マイクロエレクトロニクス用途のシリコンウェーハをトリミング、穴あけ、切断できる。プラズマダイシングも採用されています。
ダイヤモンド ダイヤモンドは、その硬度と耐薬品性のため、レーザーを使用した実用的な加工しかできません。
適切なビームパラメータの選択と制御は、健全な加工を達成し、異なる材料を扱う際の制御不能な熱損傷を防ぐために極めて重要です。プロセス開発は重要な第一歩です。
一般的な電気ビーム加工とは?
電気ビームのエネルギー源を活用する製造プロセスは、いくつか確立されている:
レーザー切断
- レーザー切断は、集光された高出力レーザーを使用して材料を溶融/蒸発させ、切断を誘発する。
- シートメタル、プレート、パイプから複雑な2Dプロファイルを最小限の歪みで切断可能
- プロセスは非常に正確で、自動化のための再現性がある
レーザー溶接
- 集束されたレーザーエネルギーにより、小型化された部品や薄い材料の精密溶接が可能
- デリケートな部品に不可欠な低入熱で歪みを最小限に抑える
- 適切な継手設計により、異種材料や反応性材料の溶接が可能。
レーザードリル/アブレーション
- レーザーは、金属、ポリマー、複合材に穴を開けることができ、工具の摩耗はありません。
- パーカッションとトレパニングのテクニックは、微細な直径と仕上げの穴を作ることができる。
- マルチパルス加工により、非常に高いアスペクト比の穴加工が可能
レーザーマーキング
- レーザーマーキングは、識別、ブランディング、トレーサビリティのために部品にマーキングする非接触方法です。
- 材料を除去したり歪ませたりすることなく、永久的なサーフェスマークを作成します。
- 金属、プラスチック、セラミック、紙、皮革、その他多くの素材にマーキング可能
レーザークラッディング
- レーザークラッディングは、集光されたレーザビームを使用して、部品上にコーティング材料を堆積させる。
- クラッディングパウダーが基材に溶融し、冶金的接合を実現します。
- 耐摩耗性または耐腐食性コーティングの構築が可能
レーザーショックピーニング
- レーザーショックピーニングは、高出力パルスを使用して衝撃波を発生させ、圧縮応力を付与します。
- 圧縮応力は疲労亀裂の発生を抑制し、部品寿命を向上させる。
- 従来のショットピーニングと比較して、より深い圧縮応力が発生します。
レーザー積層造形
- レーザー粉末床溶融法、直接金属レーザー焼結法、選択的レーザー溶融法とも呼ばれる。
- 金属粉末とレーザー溶融によるレイヤー・バイ・レイヤー3Dプリントプロセス
- 3次元CADデータから直接、複雑な形状やカスタマイズパーツを作成可能
電子ビーム溶接
- 集束電子ビームを使用し、真空中で高い溶接溶け込みを実現
- 大気汚染を受けやすいチタンのような反応性金属の接合に最適
- 完全溶け込み能力により、非常に厚い部分でも溶接可能
電子ビーム積層造形
- 電子ビーム粉末床融合または電子ビーム溶解とも呼ばれる
- 電子ビーム熱源を使用して金属粉末から3D金属パーツを作り上げる
- 環境制御されたプロセスにより、材料の酸化問題を回避
プラズマアーク溶接
- プラズマアーク溶接は、狭窄したプラズマジェットを使用して熱エネルギーを集中させる。
- 従来の溶接とは異なり、1回のパスで厚い部分を完全に貫通させることができる。
- 歪みが少なく、優れた冶金特性を持つ溶接継ぎ目を形成します。
プラズマアーク切断
- 高温のプラズマジェットを使用して材料を溶融/酸化させ、切断を誘発する。
- 厚板でも高速切断が可能で、良好なエッジ品質が得られる。
- プラズマの流れが狭い範囲に熱を集中させ、精密な切断を実現
レーザーピーニング、レーザーグレージング、レーザーアニール、プラズマキーホールドリルなど、特殊な方法でビームエネルギーを利用するニッチな加工は他にも数多くある。ビーム発生技術と制御能力の進歩により、そのリストは増え続けています。
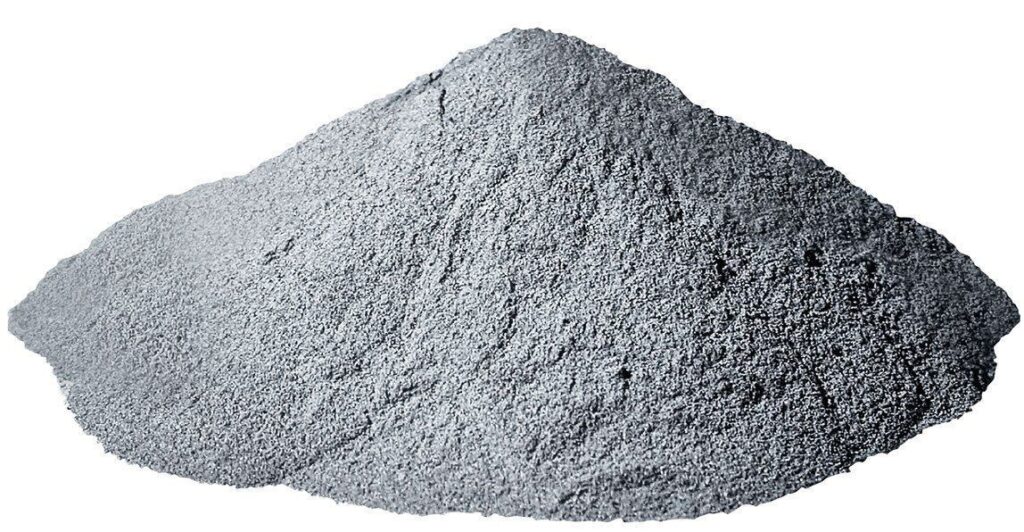
品質保証はこれらのプロセスでどのように機能するのか?
どのような製造プロセスにおいても、一貫した品質管理と品質保証の実践は重要である。電気ビームプロセスにおける重要な品質面には、以下のようなものがある:
- プロセス監視 多くの装置には、加工中のビームパワー、位置、フォーカス、ガスフロー、真空レベルなどをモニターするセンサーが搭載されている。データは記録され、分析される。
- 工程内検査 マシンビジョンシステムは、工程中の部品を光学的に検査し、欠陥や不適切な処理を見つけます。これにより、迅速な是正処置が可能になります。
- 後工程検査 – 部品は、光学測定、X線ラジオグラフィー、超音波検査、機械検査、金属組織学などを使用して、製造後に検査されます。
- パラメータ最適化 – 実験計画法は、要件を満たす理想的なパラメータを決定するのに役立ちます。パラメータは複数のビルドで検証されます。
- メンテナンス&キャリブレーション ビームジェネレーターと位置決めシステムは、安定した運転を保証するために、定期的なメンテナンスと再校正が必要です。
- オペレーター・トレーニング マシン・オペレーターとプロセス・エンジニアのための包括的なトレーニングが、適切な操作を保証します。
- トレーサビリティ 部品の識別と生産データは、最終部品をすべてのプロセス パラメータと原材料ロットまで遡るトレースを支援します。
- 規格遵守 – ISOおよび業界標準に基づく厳格な品質管理原則が実施されています。
- プロセス制御 管理図を使用した統計的プロセス制御は、プロセスの安定性を追跡し、公称条件からの逸脱を検出します。
適切な品質インフラがあれば、電気ビーム加工は非常に一貫した再現性のある加工を提供します。厳しい公差、材料特性、性能を容易に達成することができます。
どのような安全上の注意が必要ですか?
電気ビームの製造には独特の安全対策が必要だ:
- レーザーの安全性 – 直接目に触れたり、皮膚に火傷を負ったりしないように注意しなければならない。保護眼鏡、バリア、スキン、アラーム、インターロックが必要である。
- 電子ビームの危険性 ファラディックX線は遮蔽を必要とする。迷走電子ビームも封じ込めを必要とする。
- ヒューム抽出 – 多くのビームプロセスでは、溶接ヒューム、微粒子、または局所的なヒューム抽出を必要とする有害ガスが発生します。
- 電気的危険 ビームジェネレーターは、適切な絶縁、分離、アクセスインターロックを保証する高電圧を伴う。
- 火災の危険性 可燃性の蒸気、油、粉塵は、ビームエネルギーによる火災の危険性があります。適切なハウスキーピングが重要です。
- 騒音暴露 – プラズマアーク切断のような一部のビーム加工では、聴覚保護が必要な大きな騒音が発生します。
- 人間工学的リスク 不適切な持ち上げ、屈伸、反復運動は、ひずみやその他の怪我につながる可能性がある。
適切な工学的管理、管理方針、個人防護具(PPE)、訓練により、これらの危険は安全な職場のために効果的に管理することができる。ビームハザードを隔離するためには、施設や設備の慎重な設計も必要です。
ビームプロセス用の部品はどのように設計され、シミュレーションされるのか?
電気ビーム製造のための部品の設計とシミュレーションを支援するソフトウェアツールがいくつかある:
- CADソフトウェア CADプログラムでは、積層造形用に最適化されたコンポーネント形状の詳細な3Dモデリングが可能です。設計上の制約を組み込むことができます。
- トポロジー最適化 – アルゴリズムは、荷重下での性能を向上させるために材料のレイアウトを最適化することができます。これにより、大幅な軽量化が可能になります。
- シミュレーション・ソフトウェア 有限要素解析と数値流体力学は、応力、温度、歪み効果、熱と構造の相互作用、残留応力などをシミュレートします。これにより、設計の検証が可能になります。
- プロセス・モデリング – 専用のソフトウェアは、メルトプール、温度勾配、気化などをモデル化するために、エネルギービームとパウダーベッドとの相互作用をシミュレートすることができます。これにより、プロセスの実行可能性が保証されます。
- ビルド・プランニング – ビルド・プロセッサーがCADモデルをスライスし、サポート、熱蓄積、残留応力などを考慮した積層造形システムに最適なツールパスを生成します。
- 検査計画 検査要件はCADモデルで定義できます。このモデルによって、ロボットの検査ルーチンが駆動されます。
- マシンデータ 実機データをシミュレーションに組み込んで精度を向上。クローズドループ検証により、製造可能な設計を保証します。
シミュレーションの威力が増し、実機による検証と相まって、「製造可能性を考慮した設計」が可能になった。これにより、高い品質を確保しながら、開発時間とコストを削減することができます。
システムはどのように自動化され、制御されているのか?
近代的な電気ビームの工程は、広範な自動化と制御を活用している:
- CNC制御 多軸CNCシステムは、複雑な軌跡を通して、ビームやワークを高精度に位置決めします。
- モーション・コントロール 高精度の電磁ベアリング、リニアモーター、光学式エンコーディングにより、スムーズで正確なモーションを提供します。
- 高速処理 ガルバノミラー、ポリゴンミラー、その他の技術により、エネルギーを高速でスキャンして分配し、高い処理速度を実現する。
- シームトラッキング スルー・ザ・レンズとカメラを使用したモニタリングにより、溶接の継ぎ目に追従したり、リアルタイムで加工を修正したりする適応制御が可能になります。
- 高度なビーム操作 ダイナミック・フォーカス、ビーム・スプリッティング/シェーピング、特殊光学系により、ビーム・エネルギー分布を正確に制御。
- マシンビジョン – メルトプール形状、サーマルエミッション、ジオメトリのインプロセス光学モニタリングが品質を保証します。クローズドループ制御が可能。
- 精密パウダーハンドリング 注意深く制御された粉末堆積、平滑化、再コーティングにより、高精度の積層造形が可能になる。
- 不活性雰囲気 真空システムまたは不活性シュラウドガスは、材料の酸化を防ぎます。
- インプロセス計測 温度、排出ガス、および寸法測定データのその場モニタリングにより、プロセスのライブ・フィードバックが得られます。
- 統合ポスト処理 熱処理、CNC機械加工、表面仕上げ、検査などの工程を統合することで、完全な自動製造セルを実現できる。
これらのテクノロジーは、無人の消灯生産、迅速な処理、何百万もの生産サイクルを通じての一貫性を可能にする。データ収集と分析による継続的な改善も可能です。
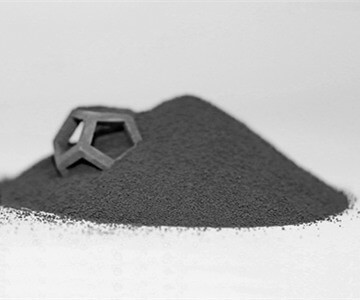
応用例と産業は?
電気ビームの製造は、多くの産業や製品に及んでいる:
航空宇宙 複雑なチタンおよびニッケル合金構造の積層造形、エンジンの精密穴あけおよび溶接。
メディカル 患者固有のインプラントの積層造形、ステントや手術器具のレーザー切断。
自動車 テーラードブランクの溶接、エアバッグパターンの切断、燃料噴射ノズルの穴あけ。
エレクトロニクス ウェハーおよび電子機器のレーザーダイシング、穴あけ、マーキング。相互接続の溶接
マイクロテクノロジー アディティブ・マニュファクチャリング(積層造形)または100ミクロン以下のマイクロスケール部品の機械加工。
金型 金型ツーリングのレーザー切断。ラピッドツールプロトタイピング。
ジュエリー&ウォッチ 超精密穴あけおよび切断。個々のシリアル番号のレーザーマーキング。
リサーチ 大学では、微細格子構造、制御研究、冶金学研究などにレーザー積層造形を使用している。
電気ビーム製造の柔軟性と利点のおかげで、商業および研究用途の範囲は急速に拡大し続けている。
電気ビームプロセスの未来は?
いくつかのエキサイティングな開発が、電気ビームの能力を拡張している:
- マルチビームおよびマルチレーザーシステム –複数のビームを活用することで、ビルドレートを高め、コントロールを強化することができる。
- 超高速レーザー ピコ秒およびフェムト秒レーザは、熱影響部を最小限に抑えた新しい材料加工の可能性を提供します。
- 高出力レーザー レーザーの出力は数十キロワットまで拡張され続け、より速い造形速度、より厚い断面、より大きなコンポーネントを可能にします。新しいレーザー設計は、ウォールプラグ効率も改善します。
- ハイブリッド製造 – レーザー蒸着とCNC機械加工や他の工程を1台の機械で組み合わせることで、新たな可能性が生まれます。
- 新素材 新しいアルミニウム合金、高エントロピー合金、金属マトリックス複合材料、その他の材料が、積層造形の特性を生かすために開発されている。
- インプロセス計測 – 高速センシングとクローズドループ制御の進歩により、造機中のリアルタイム修正と自己最適化が可能になる。
- シミュレーション シミュレーションの精度が向上し続ければ、モデリングと検証はより速く、より信頼できるものになるでしょう。
- システム・インテグレーション スキャンシステム、粉体ハンドリング、後処理、自動化、品質モニタリングの統合を強化することで、堅牢性が向上する。
電子ビーム製造は継続的な成長の態勢にあり、多くの技術分野における技術革新を推進する。レーザー、電子ビーム、プラズマプロセスのユニークな能力は、まだ想定されていない新しい方法で活用されるでしょう。エキサイティングな時代が待っている!
よくある質問
電気ビームの製造工程に関するよくあるご質問をご紹介します:
製造にはどのようなレーザーが使われているのですか?
一般的な産業用レーザーには、ファイバーレーザー、CO2レーザー、ダイオードレーザー、ディスクレーザー、ダイレクトダイオードレーザーなどがあります。それぞれ出力レベル、ビーム品質、波長、コストの面で異なる利点を提供します。レーザの種類を材料とアプリケーションに適合させることが重要です。
レーザー積層造形は他の方法と比べてどうですか?
レーザーAMは非常に高い解像度と優れた材料特性を提供する。しかし、電子ビームAMの方がわずかに速く、低コストで製造できる。バインダージェットAMは最も低コストだが、材料特性は劣る。正しい選択は、用途によって異なります。
どのような種類の電子ビーム装置が使われていますか?
熱電子フィラメントまたはタングステンカソードを使用した高真空システムは、安定した連続ビームを生成します。プラズマカソードを用いた低真空システムは、パルスビームを提供する。ビーム出力は、数キロワットから、アディティブ・マニュファクチャリング用の約100キロワットまで幅広い。
レーザーマーキングの仕組み
レーザーマーキングは、表面のコーティングを除去したり、基材をアニールしたり、あるいは表面の制御された酸化、炭化、化学変化によって色の変化を生じさせます。材料によって異なる波長が選択される。
レーザーやプラズマで切断や溶接ができる厚さは?
ファイバーレーザーは、厚さ1インチ程度までの鋼材を確実に切断できる。プラズマ切断はもっと厚く切断できます。レーザー溶接の深さは、完全溶け込みで約0.25インチが限界です。プラズマ・キーホール溶接は、6~8インチの鋼材をシングルパスで完全溶け込み溶接することができます。
レーザー溶接ではどのような欠陥が生じますか?
レーザー溶接の一般的な欠陥には、ガス巻き込みによるポロシティ、凝固収縮によるクラック、不完全融合、アンダーカット、歪み、スパッタなどがある。適切な接合設計、固定具、パラメーターおよび制御が必要である。
電子ビーム溶接にはどのような安全上の注意が必要ですか?
発生するファラディックX線には十分な遮蔽が必要である。高電圧ビームも適切に封じ込める必要がある。オペレーターやメンテナンス担当者は、電子ビームシステムを安全に扱うための専門的なトレーニングが必要である。
レーザーショックピーニングとショットピーニングの比較は?
レーザーショックピーニングは、ショットピーニングの最大6倍の深さまで圧縮応力を与えます。また、表面粗さも生じません。