La technologie de fabrication additive au laser est une méthode de fabrication qui utilise le laser comme source de chaleur et utilise l'effet de focalisation du faisceau à haute énergie du laser pour faire fondre rapidement la poudre de métal.
La densité énergétique élevée du laser permet de fabriquer des métaux difficiles à usiner, tels que les alliages de titane et les alliages à haute température utilisés dans l'aérospatiale, etc. La technologie de fabrication additive par laser présente également l'avantage de ne pas être limitée par la structure des pièces, ce qui permet de traiter et de fabriquer des structures complexes, des pièces difficiles à traiter et des pièces à parois minces.
À l'heure actuelle, la technologie de fabrication additive par laser a été appliquée à des matériaux tels que les alliages de titane, les alliages à haute température, les alliages à base de fer, les alliages d'aluminium, les alliages réfractaires, les alliages amorphes, les céramiques et les matériaux à gradient, etc. Elle présente des avantages significatifs dans la fabrication de composants complexes à haute performance dans le domaine aérospatial et de structures complexes poreuses dans le domaine de la biofabrication.
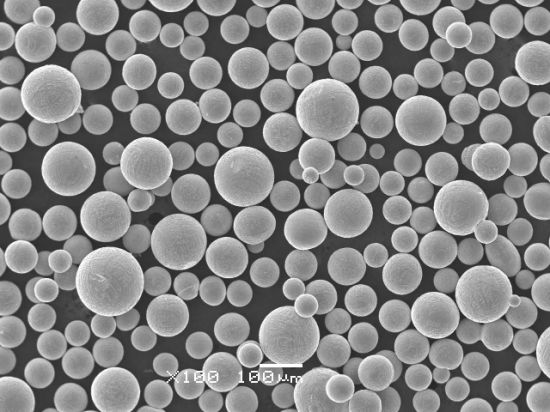
La technologie de fabrication additive utilisant le laser comme source de chaleur est principalement divisée en processus de dépôt laser basé sur l'alimentation en poudre et en technologie de fusion de zones sélectionnées par laser basée sur l'étalement de la poudre.
En raison des différents noms des unités, la technologie de dépôt par fusion laser basée sur l'alimentation en poudre est également connue sous le nom de dépôt par énergie dirigée (DED), de formage solide par laser (LSF), de dépôt direct de métal (DMD), de dépôt par fusion laser (LMD), etc. Quel que soit le nom, le principe consiste à utiliser le principe de base du prototypage rapide, en utilisant de la poudre métallique comme matière première, en utilisant un laser à haute énergie comme source d'énergie, conformément au chemin de traitement prédéterminé, la synchronisation de la poudre métallique donnée à la fusion couche par couche, la solidification rapide et le dépôt couche par couche, de manière à réaliser la fabrication directe de pièces métalliques.

En règle générale, la plate-forme du système de formage des métaux par laser se compose d'un laser, d'une table CNC, d'une buse d'alimentation en poudre, d'un chargeur de poudre réglable de haute précision et d'autres dispositifs auxiliaires, comme le montre la figure ci-dessous. Les lasers disponibles pour le processus de préparation du modèle sont principalement divisés en lasers continus à semi-conducteurs, lasers continus à fibres, lasers continus à CO2 et lasers pulsés YAG:Nd en fonction du modèle de faisceau. En fonction de l'emplacement des buses, on distingue principalement le groupe de buses d'alimentation en poudre coaxiales et les buses d'alimentation en poudre latérales.
La technologie de fusion sélective par laser utilise un laser à haute luminosité pour fondre directement des poudres métalliques sans liant. Les modèles 3D sont directement transformés en pièces structurelles complexes avec des performances comparables à celles des pièces forgées, et les pièces ne nécessitent qu'une finition de surface pour être utilisées. Les principales technologies additives laser comprennent la fusion sélective par laser (SLM), le processus de dépôt sur lit de poudre, etc.
Le principe de base de la fusion par zone laser est le suivant : le faisceau laser est balayé selon une trajectoire préétablie afin de faire fondre la poudre métallique déposée au préalable ; après avoir effectué un niveau de balayage, la chambre de travail descend d'une couche en hauteur et la couche de poudre repose sur une autre couche de poudre, et ainsi de suite, couche par couche, jusqu'à ce que les pièces métalliques requises soient fabriquées ; l'ensemble du processus se déroule dans un environnement sous vide, ce qui permet d'éviter efficacement l'influence d'impuretés nocives présentes dans l'air.
Le processus de fusion sélective par laser peut être directement transformé en produits métalliques finis, en éliminant la transition intermédiaire. Les pièces préparées ont une grande précision dimensionnelle et une bonne rugosité de surface (Ra 10~30μm), ce qui convient à diverses formes complexes de pièces, en particulier aux pièces complexes avec des structures internes complexes. Elle ne peut pas être fabriquée par les méthodes traditionnelles ; convient aux pièces structurelles complexes uniques et en petits lots sans moule, à la fabrication rapide La machine convient aux pièces structurelles complexes uniques et en petits volumes sans moule et à la fabrication à réponse rapide.
Additional FAQs: Laser Additive Manufacturing Technology
1) What are the main differences between Laser Powder Bed Fusion (LPBF/SLM) and Directed Energy Deposition (DED)?
- LPBF uses a powder bed and fine lasers to achieve high resolution and surface finish; best for complex, small-to-medium parts. DED feeds powder (or wire) into a laser melt pool; excels at larger parts, repairs, feature addition, and graded materials with higher deposition rates.
2) Which lasers are most common and how do they affect build quality?
- Fiber lasers (1070 nm) dominate for LPBF due to beam quality (M² ~1.1–1.5) and efficiency; high-power multimode fiber lasers (1–2 kW+) are common for DED. Shorter wavelengths (green, 515–532 nm) increasingly used for reflective metals like copper and precious alloys to improve absorptivity and reduce spatter.
3) How should powder specifications be chosen for laser additive manufacturing technology?
- Prefer spherical, gas/plasma-atomized powders with tight PSD: LPBF typically 15–45 µm; DED 45–150 µm. Control oxygen/nitrogen (e.g., Ti O ≤ 0.15–0.20 wt%, Al N ≤ 0.02 wt%), low satellites, high flowability, and consistent apparent/tap density to ensure repeatable melt behavior.
4) What post-processing is usually required to meet end-use properties?
- Stress relief and/or solution/aging heat treatments per alloy (e.g., IN718: solution + two-step age), Hot Isostatic Pressing (HIP) for defect closure, machining of interfaces, and surface finishing (blasting, chemical/electropolishing). NDT (CT, dye penetrant) is common for critical parts.
5) How do I minimize defects like porosity and lack-of-fusion?
- Calibrate volumetric energy density (ED = P/(v·h·t)), maintain dry/inert environments (O2 < 1000 ppm LPBF), optimize scan strategies (stripe/island, contour passes), ensure uniform powder spreading, and monitor recoater/optics health. For DED, maintain stable powder flow and coaxiality.
2025 Industry Trends: Laser Additive Manufacturing Technology
- Multi-laser LPBF mainstream: 8–12 laser systems become common, improving throughput 1.5–2.5× with advanced scan partitioning and interference mitigation.
- Green/blue laser adoption grows for copper, precious metals, and electronics heat spreaders, improving density and conductivity.
- Qualification momentum: More AMS/ASTM material allowables and OEM process specs for AlSi10Mg, Sc-modified Al, CuCrZr, IN718/625, and maraging steels.
- Closed-loop control: In-situ photodiodes, coaxial cameras, pyrometry, and melt-pool analytics enable adaptive parameter tuning and traceable quality records.
- Sustainability: Powder recycling programs and inert gas recirculation reduce consumables cost and footprint; recycled polymer and metal blends expand where certification allows.
2025 Snapshot: Performance, Cost, Adoption (Indicative)
Métrique | LPBF (2023) | LPBF (2025 YTD) | DED (2023) | DED (2025 YTD) | Notes |
---|---|---|---|---|---|
Typical build rate (Ti-6Al-4V) | 20–40 cm³/h per laser | 30–55 cm³/h per laser | 50–150 cm³/h | 80–220 cm³/h | Multi-laser + path optimization |
Feature size (min wall) | 150–300 µm | 120–250 µm | 800–1500 µm | 600–1200 µm | Optics + scan tuning |
As-built density (optimized) | 99.5–99.9% | 99.7–99.95% | 98.5–99.5% | 99.0–99.6% | Process window tightening |
System price (new) | $400k–$1.2M | $450k–$1.5M | $500k–$2.5M | $600k–$3.0M | Larger platforms lift cap |
Qualified alloys (commercial) | ~45–50 | ~60+ | ~20–25 | ~30+ | New Al, Cu, tool steels |
Gas/O2 spec (LPBF chamber) | <1000 ppm | <500 ppm typical | N/A | N/A | Better gas management |
Sources:
- ASTM/ISO AM standards updates: https://www.astm.org, https://www.iso.org
- OEM technical notes (EOS, SLM Solutions, Trumpf, Renishaw, DMG MORI)
- NIST AM-Bench and melt pool monitoring research: https://www.nist.gov/ambench
- ContextAM/Wohlers market trackers (industry reports)
Latest Research Cases
Case Study 1: High-Conductivity Copper Heat Exchangers via Green-Laser LPBF (2025)
Background: An EV OEM targeted improved thermal management for power electronics.
Solution: Deployed 515 nm green-laser LPBF with CuCrZr powder (15–35 µm), optimized hatch and contour strategies; applied precipitation hardening post-build.
Results: 99.9% density, electrical conductivity 90–94% IACS, 23% lower junction temperatures vs. machined baseline, cycle time reduced 28% using dual-laser toolpaths.
Case Study 2: Hybrid DED Repair of IN718 Turbine Seals (2024)
Background: An MRO provider sought life extension for worn seal segments.
Solution: Used high-power fiber-laser DED with argon shielding and IN718 powder (53–106 µm); implemented inline coaxial monitoring and closed-loop powder flow control; post H900 aging.
Results: Dimensional restoration within ±0.15 mm, repaired parts passed fluorescent penetrant and CT; low-cycle fatigue life improved 18% over prior weld-repair method, cost per repair down 22%.
Expert Opinions
- Dr. Todd Palmer, Professor of Engineering Science and Mechanics, Penn State
- “Beam shaping and real-time control are closing the gap between as-built and wrought properties, especially for reflective alloys in laser additive manufacturing technology.”
- Dr. Ellen Cerreta, Division Leader, Materials Science and Technology, Los Alamos National Laboratory
- “Qualification hinges on microstructure control—laser scan strategies that stabilize grain structure and defect populations are proving as important as alloy chemistry.”
- Stefan Zeidler, Head of AM Solutions, TRUMPF
- “In 2025, productivity gains come from smarter multi-laser coordination and automated powder/gas management as much as from raw laser power.”
Practical Tools and Resources
- ISO/ASTM 52900 (terminology), 52907 (metal powder specs), 52904 (LPBF process), 52910 (design guidelines). https://www.iso.org
- ASTM F2924 (Ti-6Al-4V), F3055 (IN718), A1085/AMS specs for AM alloys. https://www.astm.org
- NIST resources on in-situ sensing and qualification for LPBF/DED. https://www.nist.gov/ambench
- OEM application libraries: EOS, SLM Solutions, Renishaw, Trumpf, DMG MORI (process parameters, case studies)
- Senvol Database for machine–material–process mapping. https://senvol.com
- OSHA/NIOSH guidance on laser safety, metal powders, and ventilation. https://www.osha.gov, https://www.cdc.gov/niosh
- MatWeb and Granta EduPack for material datasheets and comparisons. https://www.matweb.com
Last updated: 2025-08-25
Changelog: Added 5 FAQs specific to LPBF/DED; included 2025 trend table with performance/cost metrics; provided two recent case studies; compiled expert opinions; curated tools/resources with standards and databases
Next review date & triggers: 2026-02-01 or earlier if major LPBF/DED standard updates publish, multi-laser coordination breakthroughs are announced, or reflective metal (Cu/Ag/Au) process windows materially change