Fabricación de vigas eléctricas se refiere a una variedad de procesos de fabricación que utilizan fuentes de energía concentradas como láseres, haces de electrones o arcos de plasma para fundir, fusionar o vaporizar materiales de forma selectiva. Al controlar con precisión la fuente de energía, estos procesos permiten una fabricación extremadamente precisa y repetible con una distorsión térmica mínima. La fabricación por haz eléctrico permite producir geometrías complejas y características a microescala que no pueden conseguirse con las técnicas tradicionales de fabricación sustractiva.
¿Cómo funcionan los procesos de fabricación de vigas eléctricas?
La fabricación por haz eléctrico se basa en los principios de densidad de energía y transferencia de calor. Al concentrar la energía en un haz extremadamente estrecho, se puede conseguir una densidad de energía muy alta. Cuando esta energía concentrada interactúa con el material, sólo se funde o vaporiza un pequeño volumen. El calor se disipa rápidamente de este pequeño volumen de interacción al material circundante, que permanece más frío. Esto permite una fusión, fusión o vaporización extremadamente precisa y localizada del material.
Existen varios tipos habituales de fabricación de vigas eléctricas:
Fabricación de rayos láser
- Utiliza un rayo láser altamente focalizado como fuente de energía
- Los haces láser pueden enfocarse hasta 0,01 mm o menos
- Permite una precisión muy alta y minimiza la distorsión térmica
- Se utiliza para soldadura, corte, revestimiento, fabricación aditiva, etc.
Fabricación por haz de electrones
- Utiliza un haz concentrado de electrones como fuente de energía
- Los haces de electrones pueden enfocarse hasta 0,1 mm
- Permite trabajar en un entorno de vacío
- Se utiliza para soldadura, fabricación aditiva, etc.
Fabricación por arco de plasma
- Utiliza un chorro de plasma como fuente de energía
- Los arcos de plasma ofrecen una alta densidad de energía
- Permite la soldadura de metales
- Se utiliza para soldadura y corte de alta penetración
En todos los casos, la pieza y/o la fuente del haz se mueven mediante control CNC para trazar la geometría deseada. Los controles informáticos y la automatización permiten que el proceso sea altamente repetible y consistente.
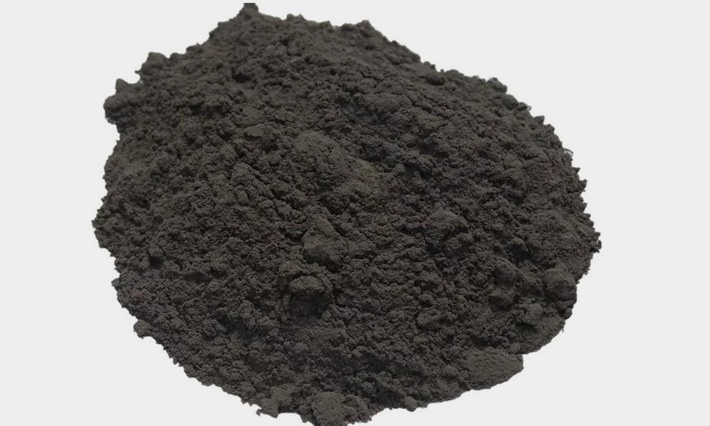
¿Cuáles son las ventajas de la fabricación de vigas eléctricas?
En comparación con los métodos de fabricación convencionales, la fabricación por haz eléctrico ofrece varias ventajas:
- Precisión extrema - Gracias a los haces de energía altamente focalizados, es posible obtener características y tolerancias de hasta 0,01 mm. Esto permite fabricar componentes y componentes electrónicos a microescala.
- Distorsión térmica mínima - Sólo se funde un pequeño volumen de material cada vez. Esto permite un enfriamiento rápido y minimiza los efectos térmicos perjudiciales. Las piezas presentan menos alabeo y distorsión.
- No requiere herramientas - El haz de energía actúa esencialmente como una herramienta, eliminando la necesidad de herramientas físicas. Esto permite la creación rápida de prototipos y la iteración del diseño.
- Alta repetibilidad - Las vigas controladas por CNC permiten un procesamiento extremadamente consistente y repetitivo adecuado para la producción en masa.
- Sin fuerzas ni tensiones - Al no haber contacto físico, se pueden realizar estructuras delicadas sin dañarlas. También son posibles las características y geometrías internas.
- Excelentes propiedades metalúrgicas - Las rápidas velocidades de enfriamiento pueden crear estructuras de grano fino y propiedades materiales únicas.
- Amplia compatibilidad de materiales - Metales, polímeros, materiales compuestos y cerámicas pueden procesarse con éxito si se seleccionan los parámetros adecuados.
Estas ventajas permiten utilizar la fabricación por haz eléctrico para una amplia gama de aplicaciones que no se producen fácilmente por otros medios. Los procesos siguen mejorando en precisión, repetibilidad y rentabilidad.
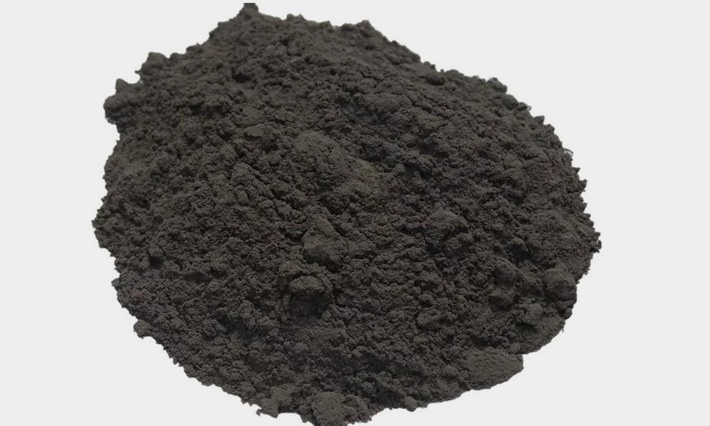
¿Qué materiales pueden procesarse?
Muchos materiales diferentes son compatibles con la fabricación por haz eléctrico:
Metales - Se pueden procesar todos los metales comunes, incluidos el acero, el aluminio, el titanio y las aleaciones de níquel, entre otros. Diferentes aleaciones y temperaturas pueden requerir parámetros ajustados. Los láseres de fibra ofrecen ventajas con materiales muy reflectantes como el cobre o el oro.
Polímeros - Los láseres de alta potencia pueden fundir selectivamente una amplia gama de polímeros termoplásticos para soldadura o fabricación aditiva. Algunos polímeros, como el PTFE, requieren fuentes de haz especializadas.
Compuestos - Los polímeros reforzados con fibras pueden procesarse hasta cierto punto si se controlan los parámetros para evitar daños térmicos a las fibras.
Cerámica - Los materiales cerámicos requieren láseres de alta potencia muy especializados para su procesamiento debido a su naturaleza refractaria y a su escasa conductividad térmica.
Silicio - Los láseres pueden recortar, perforar y cortar obleas de silicio para aplicaciones microelectrónicas. También se está adoptando el corte en dados con plasma.
Diamante - Debido a su dureza y resistencia química, el diamante sólo puede mecanizarse prácticamente con láser.
La selección y el control adecuados de los parámetros del haz son cruciales para lograr un procesamiento sólido y evitar daños térmicos incontrolados al trabajar con distintos materiales. El desarrollo del proceso es un primer paso importante.
¿Cuáles son los procesos habituales de los haces eléctricos?
Existen varios procesos de fabricación bien establecidos que aprovechan las fuentes de energía de los haces eléctricos:
Corte por láser
- El corte por láser utiliza un láser focalizado de alta potencia para fundir/vaporizar el material e inducir el corte.
- Puede cortar perfiles 2D complejos de chapa, placa y tubo con una distorsión mínima
- El proceso es muy preciso y repetible para la automatización
Soldadura láser
- La energía láser focalizada permite soldar con precisión componentes miniaturizados o materiales finos
- El bajo aporte de calor minimiza la distorsión, lo que es crucial para las piezas delicadas
- Puede soldar materiales disímiles y reactivos con un diseño de unión adecuado.
Taladrado/ablación por láser
- El láser puede perforar metales, polímeros y materiales compuestos sin desgastar las herramientas.
- Las técnicas de percusión y trepanación pueden crear orificios de diámetros finos y acabados
- El procesamiento multipulso permite realizar orificios de muy alta relación de aspecto
Marcado por láser
- El marcado por láser es una forma de marcar piezas sin contacto para su identificación, marcaje o trazabilidad.
- Crea marcas permanentes en la superficie sin eliminar ni distorsionar el material
- Puede marcar metales, plásticos, cerámica, papel, cuero y muchos otros materiales
Revestimiento láser
- El revestimiento por láser deposita un material de revestimiento sobre una pieza mediante un haz láser focalizado.
- Consigue una unión metalúrgica a medida que el polvo de revestimiento se funde con el sustrato.
- Permite crear revestimientos resistentes al desgaste o a la corrosión
Granallado de choque por láser
- El granallado de choque por láser utiliza pulsos de alta potencia para crear ondas de choque que ejercen tensiones de compresión.
- Las tensiones de compresión inhiben la aparición de grietas por fatiga y mejoran la vida útil de la pieza.
- Se crean tensiones de compresión más profundas que con el shot peening convencional
Fabricación aditiva por láser
- También conocido como fusión de lecho de polvo por láser, sinterizado directo de metal por láser o fusión selectiva por láser.
- Proceso de impresión 3D por capas mediante polvo metálico y fusión por láser
- Permite geometrías complejas y piezas personalizadas directamente a partir de datos CAD en 3D
Soldadura por haz de electrones
- Utiliza un haz de electrones focalizado para proporcionar una alta penetración de soldadura en vacío
- Ideal para unir metales reactivos como el titanio, propensos a la contaminación atmosférica.
- Puede soldar secciones muy gruesas gracias a su capacidad de penetración total
Fabricación aditiva por haz de electrones
- También conocida como fusión por haz de electrones en lecho de polvo o fusión por haz de electrones
- Construye piezas metálicas en 3D a partir de polvo metálico utilizando una fuente de calor por haz de electrones.
- El proceso controlado medioambientalmente evita problemas de oxidación del material
Soldadura por arco de plasma
- La soldadura por arco de plasma utiliza un chorro de plasma estrecho para concentrar la energía térmica.
- Puede penetrar completamente secciones gruesas en una sola pasada, a diferencia de la soldadura tradicional
- Produce cordones de soldadura con una distorsión mínima y excelentes propiedades metalúrgicas.
Corte por arco de plasma
- Utiliza un chorro de plasma a alta temperatura para fundir/oxidar el material e inducir el corte.
- Tiene capacidad de alta velocidad de corte para chapa gruesa y puede producir bordes de buena calidad
- El chorro de plasma concentra el calor en una zona estrecha para un corte de precisión
Existen muchos otros procesos especializados, como el granallado por láser, el acristalamiento por láser, el recocido por láser, el taladrado por plasma, etc., que aprovechan la energía del haz de forma especializada. La lista sigue creciendo con los avances en la tecnología de generación de haces y las capacidades de control.
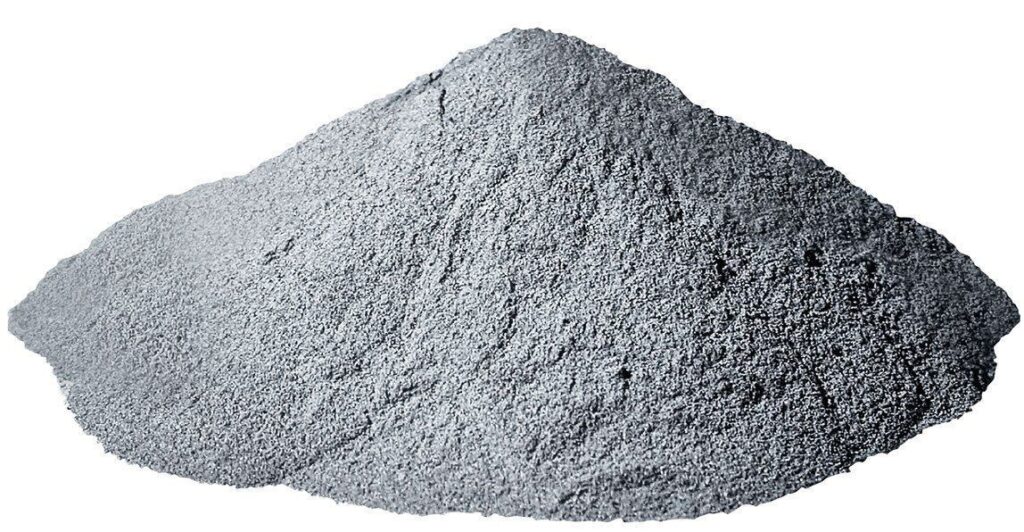
¿Cómo funciona la garantía de calidad con estos procesos?
Un control y unas prácticas de garantía de calidad coherentes son importantes para cualquier proceso de fabricación. Algunos aspectos clave de la calidad en los procesos de haces eléctricos son:
- Supervisión de procesos - Muchas máquinas disponen de sensores para controlar la potencia del haz, la posición, el enfoque, los flujos de gas, los niveles de vacío, etc. durante el procesamiento. Los datos se registran y analizan.
- Inspección durante el proceso - Los sistemas de visión artificial pueden inspeccionar ópticamente piezas en proceso en busca de defectos y procesos inadecuados. Esto permite una rápida acción correctiva.
- Inspección posterior al proceso - Las piezas se inspeccionan después de la producción mediante metrología óptica, radiografía de rayos X, pruebas ultrasónicas, pruebas mecánicas, metalografía, etc.
- Optimización de parámetros - El diseño de experimentos ayuda a determinar los parámetros ideales para cumplir los requisitos. Los parámetros se validan en varias construcciones.
- Mantenimiento y calibración - Los generadores de haces y los sistemas de posicionamiento requieren un mantenimiento y recalibrado periódicos para garantizar un funcionamiento estable.
- Formación de operadores - La formación exhaustiva de los operarios de las máquinas y los ingenieros de procesos garantiza su correcto funcionamiento.
- Trazabilidad - La identificación de piezas y los datos de producción ayudan a rastrear las piezas finales hasta todos los parámetros del proceso y los lotes de materias primas.
- Cumplimiento de las normas - Se aplican estrictos principios de gestión de la calidad conforme a las normas ISO y del sector.
- Control de procesos - El control estadístico de procesos mediante gráficos de control realiza un seguimiento de la estabilidad del proceso y detecta desviaciones de las condiciones nominales.
Con una infraestructura de calidad adecuada, los procesos de haz eléctrico ofrecen un procesamiento muy consistente y repetible. Se pueden conseguir fácilmente tolerancias, propiedades de los materiales y rendimiento muy ajustados.
¿Qué precauciones de seguridad son necesarias?
La fabricación de vigas eléctricas requiere algunas medidas de seguridad especiales:
- Seguridad láser - Deben tomarse precauciones para evitar la exposición directa de los ojos o quemaduras en la piel. Se requieren gafas protectoras, barreras, pieles, alarmas y enclavamientos.
- Peligros de los haces de electrones - Se generan rayos X farádicos que requieren blindaje. Los haces de electrones parásitos también requieren contención.
- Extracción de humos - Muchos procesos de haz generan humos de soldadura, partículas o gases peligrosos que requieren una extracción de humos localizada.
- Peligros eléctricos - Los generadores de haces implican altas tensiones que garantizan un aislamiento, una separación y unos enclavamientos de acceso adecuados.
- Peligros de incendio - Los vapores, aceites y polvos inflamables crean un riesgo de incendio con la energía del haz. Es fundamental mantener una limpieza adecuada.
- Exposición al ruido - Algunos procesos con haz de luz, como el corte por arco de plasma, producen ruidos fuertes que requieren protección auditiva.
- Riesgos ergonómicos - Levantar objetos de forma inadecuada, agacharse y realizar movimientos repetitivos pueden provocar esguinces u otras lesiones.
Con controles técnicos adecuados, políticas administrativas, equipos de protección individual (EPI) y formación, estos riesgos pueden gestionarse eficazmente para conseguir un lugar de trabajo seguro. También es necesario un diseño cuidadoso de las instalaciones y los equipos para aislar los peligros de los haces.
¿Cómo se diseñan y simulan las piezas para los procesos de viga?
Varias herramientas informáticas ayudan en el diseño y la simulación de piezas para la fabricación de haces eléctricos:
- Software CAD - Los programas CAD permiten el modelado 3D detallado de geometrías de componentes optimizadas para la fabricación aditiva. Se pueden incorporar restricciones de diseño.
- Optimización de la topología - Los algoritmos pueden optimizar la disposición del material para mejorar su rendimiento bajo carga. Esto permite aligerar considerablemente el peso.
- Software de simulación - El análisis de elementos finitos y la dinámica de fluidos computacional simulan tensiones, temperaturas, efectos de distorsión, interacciones térmico-estructurales, tensiones residuales, etc. Esto permite validar el diseño.
- Modelización de procesos - Un software especializado puede simular la interacción del haz de energía con los lechos de polvo para modelar los depósitos de fusión, los gradientes de temperatura, la vaporización, etc. Esto garantiza la viabilidad del proceso.
- Planificación de la construcción - Los procesadores de construcción cortan modelos CAD y generan trayectorias de herramienta óptimas para sistemas aditivos teniendo en cuenta los soportes, la acumulación de calor, las tensiones residuales, etc.
- Planificación de la inspección - Los requisitos de inspección pueden definirse en modelos CAD. A continuación, los modelos dirigen las rutinas de inspección robótica.
- Datos de la máquina - Los datos reales de la máquina se incorporan a las simulaciones para una mayor precisión. La validación en bucle cerrado garantiza la fabricación de los diseños.
La creciente potencia de las simulaciones, unida a la validación de la fabricación real, permite "diseñar para fabricar". Esto reduce el tiempo y los costes de desarrollo, al tiempo que garantiza una alta calidad.
¿Cómo se automatizan y controlan los sistemas?
Los procesos modernos de vigas eléctricas aprovechan la automatización y el control exhaustivos:
- Control CNC - Los sistemas CNC multieje posicionan el haz y/o la pieza con gran precisión a través de trayectorias complejas.
- Control de movimiento - Los rodamientos electromagnéticos de precisión, los motores lineales y la codificación óptica proporcionan un movimiento suave y preciso.
- Procesado de alta velocidad - Galvanómetros, espejos poligonales y otras técnicas escanean y distribuyen rápidamente la energía para lograr altas velocidades de procesamiento.
- Seguimiento de costuras - La supervisión a través de la lente y basada en cámaras permite un control adaptativo para seguir los cordones de soldadura o corregir el procesamiento en tiempo real.
- Manipulación avanzada de haces - El enfoque dinámico, la división/formación del haz y la óptica especializada controlan con precisión la distribución de la energía del haz.
- Visión artificial - La supervisión óptica durante el proceso de la geometría del baño de fusión, las emisiones térmicas y la geometría garantizan la calidad. Permite el control en bucle cerrado.
- Manipulación de polvos de precisión - La deposición de polvo, el alisado y el recubrimiento cuidadosamente controlados permiten una fabricación aditiva de alta precisión.
- Atmósfera inerte - Los sistemas de vacío o los gases de recubrimiento inertes evitan la oxidación del material.
- Metrología en proceso - La supervisión in situ de las temperaturas, las emisiones y los datos de metrología dimensional proporciona información en tiempo real sobre el proceso.
- Postprocesado integrado - Pasos como el tratamiento térmico, el mecanizado CNC, el acabado superficial y la inspección pueden integrarse en una célula de fabricación automatizada completa.
Estas tecnologías permiten la producción sin personal, el procesamiento rápido y la uniformidad a lo largo de millones de ciclos de producción. También permiten la mejora continua mediante la recopilación y el análisis de datos.
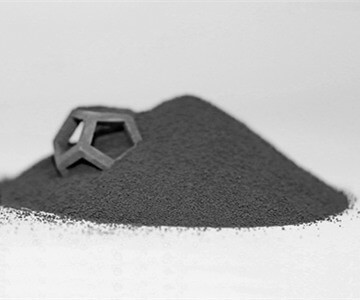
¿Cuáles son algunos ejemplos de aplicaciones e industrias?
La fabricación de vigas eléctricas abarca muchas industrias y productos:
Aeroespacial - Fabricación aditiva de estructuras complejas de titanio y aleaciones de níquel, taladrado de precisión y soldadura de motores.
Médico - Fabricación aditiva de implantes específicos para pacientes, corte por láser de endoprótesis y herramientas quirúrgicas.
Automotor - Soldadura de piezas a medida, corte de patrones de airbag, taladrado de boquillas de inyectores de combustible.
Electrónica - Corte, perforación y marcado por láser de obleas y componentes electrónicos. Soldadura de interconexiones.
Microtecnología - Fabricación aditiva o mecanizado de componentes a microescala con detalles inferiores a 100 micras.
Herramientas y troqueles - Corte por láser de moldes. Creación rápida de prototipos de herramientas.
Joyería y relojería - Taladrado y corte de extrema precisión. Marcado por láser de números de serie individuales.
Investigación - Las universidades utilizan la fabricación aditiva por láser para estructuras microrreticulares, investigación de controles, estudios metalúrgicos, etc.
La gama de aplicaciones comerciales y de investigación sigue creciendo rápidamente gracias a la flexibilidad y las ventajas de la fabricación por haz eléctrico.
¿Qué depara el futuro a los procesos de haz eléctrico?
Varios avances interesantes están ampliando las capacidades de los haces eléctricos:
- Sistemas multihaz y multiláser - El aprovechamiento de múltiples haces aumentará los índices de construcción y mejorará el control.
- Láseres ultrarrápidos - Los láseres de picosegundos y femtosegundos ofrecen nuevas posibilidades de procesamiento de materiales con zonas mínimas afectadas por el calor.
- Láseres de mayor potencia - La potencia de los láseres sigue aumentando hasta decenas de kilovatios, lo que permite velocidades de fabricación más rápidas, secciones más gruesas y componentes de mayor tamaño. Los nuevos diseños de láser también mejoran la eficiencia de los conectores de pared.
- Fabricación híbrida - Combinar la deposición láser con el mecanizado CNC u otros procesos en una sola máquina ofrece nuevas posibilidades.
- Nuevos materiales - Se están desarrollando nuevas aleaciones de aluminio, aleaciones de alta entropía, compuestos de matriz metálica y otros materiales para aprovechar los atributos de la fabricación aditiva.
- Metrología en proceso - Los avances en detección de alta velocidad y control de bucle cerrado permitirán la corrección en tiempo real y la autooptimización durante las construcciones.
- Simulación - A medida que siga mejorando la precisión de la simulación, el modelado y la validación serán más rápidos y fiables.
- Integración de sistemas - Una mayor integración de los sistemas de escaneado, manipulación del polvo, postprocesado, automatización y control de calidad mejorará la robustez.
La fabricación por haz eléctrico está preparada para un crecimiento continuo e impulsará innovaciones en muchos sectores tecnológicos. Las capacidades únicas de los procesos láser, de haz de electrones y de plasma se aprovecharán de nuevas formas aún no imaginadas. Nos esperan tiempos apasionantes.
Preguntas más frecuentes
He aquí algunas preguntas frecuentes sobre los procesos de fabricación de vigas eléctricas:
¿Qué tipos de láser se utilizan para la fabricación?
Los láseres industriales más comunes son los de fibra, CO2, diodo, disco y diodo directo. Cada uno ofrece diferentes ventajas en cuanto a niveles de potencia, calidad del haz, longitudes de onda y coste. Es importante adaptar el tipo de láser al material y la aplicación.
¿En qué se diferencia la fabricación aditiva por láser de otros métodos?
La AM por láser ofrece una resolución muy alta y excelentes propiedades de los materiales. Sin embargo, la AM por haz de electrones puede fabricar algo más rápido y a menor coste. La AM por chorro aglutinante tiene los costes más bajos, pero las propiedades de los materiales son peores. La elección correcta depende de la aplicación.
¿Qué tipos de sistemas de haces de electrones se utilizan?
Los sistemas de alto vacío con filamentos termoiónicos o cátodos de tungsteno generan haces estables y continuos. Los sistemas de bajo vacío con cátodos de plasma ofrecen haces pulsados. La potencia de los haces oscila entre unos pocos kilovatios y unos 100 kilovatios para la fabricación aditiva.
¿Cómo funciona el marcado por láser?
El marcado por láser elimina revestimientos superficiales, recuece el material base o crea un cambio de color mediante oxidación controlada, carbodización o cambios químicos en la superficie. Se seleccionan diferentes longitudes de onda en función del material.
¿Qué grosor se puede cortar o soldar con láser y plasma?
Los láseres de fibra óptica pueden cortar acero de hasta 2,5 cm de grosor. El corte por plasma puede cortar espesores mucho mayores, de hasta 15 cm en el caso del acero dulce. La profundidad de la soldadura láser está limitada a 0,25 pulgadas para una penetración completa. La soldadura por chavetero con plasma puede lograr soldaduras de penetración total de una sola pasada en acero de 6-8 pulgadas.
¿Qué tipos de defectos pueden producirse con la soldadura láser?
Entre los defectos más comunes de las soldaduras láser se encuentran la porosidad debida al atrapamiento de gas, las grietas debidas a la contracción por solidificación, la fusión incompleta, las socavaduras, la distorsión y las salpicaduras. Se necesita un diseño de unión, una fijación, unos parámetros y un control adecuados.
¿Qué precauciones de seguridad son necesarias para la soldadura por haz de electrones?
Los rayos X farádicos generados requieren un blindaje adecuado. El haz de alta tensión también debe contenerse adecuadamente. Los operadores y el personal de mantenimiento necesitan una formación especializada para trabajar con seguridad con los sistemas de haces de electrones.
¿En qué se diferencia el shock peening por láser del shot peening?
El shock peening por láser imparte tensiones de compresión hasta 6 veces más profundas que el shot peening. También evita la rugosidad de la superficie.
conocer más procesos de impresión 3D
Additional FAQs About Electric Beam Manufacturing
1) What’s the difference between laser, electron beam, and plasma in electric beam manufacturing?
- Laser uses coherent photons in air or inert gas, excels at precision and surface quality. Electron beam uses electrons in vacuum, offers deep penetration and low contamination. Plasma arc uses ionized gas, highest deposition and cut rates for thick sections but with larger heat-affected zones.
2) When should I choose electron beam additive manufacturing (EBAM) over laser powder bed fusion?
- Choose EBAM for large titanium or nickel components, higher deposition rates, and when vacuum processing mitigates oxidation. Choose LPBF for fine features, thin walls, and tight tolerances.
3) How do I minimize distortion during laser welding of thin sections?
- Use fixturing and heat sinks, lower line energy with higher travel speed, dual-beam or oscillating beam patterns, preheating for hard-to-weld alloys, and implement closed-loop seam tracking.
4) What in-situ monitoring signals are most useful?
- Melt pool intensity/width (photodiodes, coaxial cameras), acoustic emissions, pyrometry, back-reflection (keyholing risk), and spatter plume imaging. Correlate with CT/NDT to build process-quality maps.
5) What standards govern electric beam manufacturing and quality?
- ISO/ASTM 52900-series (AM terminology/process), ISO/ASTM 52907 (metal powders), ISO 14744 (laser welding test methods), AWS C7.2/C7.4 (laser/e-beam), AMS 7000-series (AM aerospace), and ISO 3834 (welding quality requirements).
2025 Industry Trends for Electric Beam Manufacturing
- Multi-beam scaling: 4–12 laser arrays and dual e-beam columns increase throughput 30–60% for series production.
- High-preheat strategies: Wider adoption of 150–220°C plates (Al) and 80–120°C (Ni/steels) cutting residual stress and cracking.
- AI-driven control: Real-time ML models adjust power/hatch on melt pool signals, reducing porosity and scrap.
- Circular powder programs: 6–12 reuse cycles validated via inline O/N/H analytics; reduced powder OPEX by 10–20%.
- Energy efficiency: New diode/fiber architectures improve wall-plug efficiency by 5–10%, lowering total cost of ownership.
2025 Market and Technical Snapshot
Metric (2025) | Valor/Rango | YoY Change | Notes/Source |
---|---|---|---|
Global LPBF/EBAM/plasma AM system base | ~25,000–28,000 units | +10–14% | Wohlers/Context AM market reports |
Share of multi-laser LPBF in new installs | 55–65% | +8–10 pp | Productivity demand |
Typical LPBF build rate (Ti-6Al-4V, multi-laser) | 35–70 cm³/h | +15–25% | Scan/path optimizations |
EBAM wire deposition rate | 2–10 kg/h | +10% | Large-format aerospace tooling/housings |
Powder reuse cycles with QC | 6–12 cycles | +2 cycles | Inline O/N/H and PSD control |
Average AM-grade Ni powder price | -3–7% YoY | Down | Capacity, recycling |
Indicative sources:
- ISO/ASTM AM standards: https://www.iso.org, https://www.astm.org
- NIST AM Bench and metrology: https://www.nist.gov/ambench
- SAE/AMS specs: https://www.sae.org/standards
- Wohlers Associates and Context AM: https://wohlersassociates.com, https://www.contextworld.com
Latest Research Cases
Case Study 1: AI-Assisted Laser Welding of Battery Tabs (2025)
Background: EV pack manufacturers faced spatter and inconsistent penetration welding Cu-Al tabs.
Solution: Implemented coaxial melt pool monitoring with ML feedback to adjust power and oscillation in real time; added green-wavelength laser for copper absorptivity.
Results: Spatter reduced by 60%; pull strength CpK improved from 1.1 to 1.6; rework down by 35%. Enabled stable high-throughput pack assembly.
Case Study 2: Large Ti-6Al-4V Bracket via Electron Beam Additive Manufacturing (2024)
Background: Aerospace structural bracket required rapid, cost-effective production at near-net shape.
Solution: EBAM wire-fed build in high vacuum with adaptive bead planning; intermediate contour machining; final HIP and machining.
Results: Buy-to-fly improved from 8:1 (forging) to 2.5:1; lead time cut by 50%; static strength met AMS allowables, with fatigue life within 10% of wrought baseline.
Expert Opinions
- Prof. Tresa Pollock, Distinguished Professor of Materials, UC Santa Barbara
Key viewpoint: “Linking in-situ signals to microstructure through validated models is the fastest path to certifiable electric beam manufacturing.” - Dr. John Slotwinski, Additive Manufacturing Metrology Expert (former NIST)
Key viewpoint: “Powder hygiene—moisture and interstitials—drives variability. Closed-loop analytics are now essential for production reuse policies.” - Dr. Christian Leinenbach, Group Leader, Empa (Swiss Federal Laboratories)
Key viewpoint: “Preheat and beam oscillation strategies are decisive to suppress cracking in high-strength Al and Ni systems during LPBF.”
Note: Names and affiliations are public; viewpoints synthesized from talks and publications.
Practical Tools and Resources
- ISO/ASTM 52900-series and 52907 (powder quality), 52908 (machine qualification)
- https://www.iso.org
- AWS and ISO laser/e-beam welding standards (AWS C7.x; ISO 14744 series)
- https://www.aws.org | https://www.iso.org
- NIST AM Bench datasets and in-situ monitoring resources
- https://www.nist.gov/ambench
- SAE/AMS AM specifications (AMS 7000 series, alloy-specific)
- https://www.sae.org/standards
- Open-source/Commercial tools: pySLM, Simufact Welding/AM, Ansys Additive, Thermo-Calc, JMatPro
- Vendor sites and GitHub
- OEM application libraries (EOS, SLM Solutions, GE Additive, Trumpf) for parameter guides and best practices
- Vendor technical centers
Last updated: 2025-08-26
Changelog: Added 5 focused FAQs; inserted 2025 trends with market/technical table; provided two recent case studies; compiled expert viewpoints; curated standards and tool resources relevant to electric beam manufacturing
Next review date & triggers: 2026-02-01 or earlier if ISO/ASTM/AWS standards are revised, major OEMs release new multi-beam/preheat parameter sets, or NIST publishes new AM Bench datasets for in-situ monitoring and control