Visión general de Fabricación aditiva MIM
El moldeo por inyección de metales (MIM) es un proceso de fabricación aditiva que combina el moldeo por inyección de plásticos y la pulvimetalurgia. El MIM permite fabricar en serie piezas metálicas complejas con una forma neta, gran precisión y repetibilidad.
El MIM tiene ventajas clave sobre otros procesos de impresión 3D en metal:
- Producción de gran volumen: en cada lote pueden fabricarse hasta miles de piezas. Esto hace que el MIM sea adecuado para aplicaciones de producción de uso final.
- Bajo coste por pieza - El método de moldeo aporta economías de escala. El coste por pieza disminuye significativamente con mayores volúmenes.
- Amplia gama de metales: pueden utilizarse acero inoxidable, acero para herramientas, aleaciones de titanio y otros metales.
- Excelentes propiedades mecánicas - Se consigue una densidad casi total y una composición uniforme.
- Geometrías complejas: son posibles las formas intrincadas, las características interiores y las paredes finas.
- Múltiples opciones de postprocesado: se puede aplicar mecanizado, grabado, chapado y otros acabados.
- Proceso establecido: el MIM se utiliza desde los años setenta. Existen normas y bases de datos de materiales.
El MIM es ideal para piezas metálicas pequeñas y complejas que se necesitan en grandes volúmenes a bajo coste. Tiende un puente entre la impresión 3D de prototipos y la fabricación de grandes volúmenes.
Visión general del proceso MIM
El proceso de moldeo por inyección de metal consta de cuatro pasos principales:
- Preparación de la materia prima - El polvo metálico se mezcla con un material aglutinante para crear una materia prima homogénea. Esta mezcla se granula para su uso en la moldeadora por inyección.
- Moldeo por inyección - La materia prima se funde y se inyecta en un molde para darle la forma "verde" deseada. Se utiliza un equipo de moldeo por inyección estándar.
- Desbobinado - El material aglutinante se extrae del componente moldeado por medios químicos, térmicos o catalíticos. Esto deja una pieza "marrón".
- Sinterización - Las piezas deshuesadas se sinterizan para fundir el polvo metálico en una pieza densa de uso final. Las piezas se encogen durante la sinterización.
Operaciones secundarias como el mecanizado, la unión, el chapado y el grabado pueden mejorar aún más los componentes. A continuación se muestra el flujo básico del proceso MIM:
Tabla 1: Resumen del proceso de fabricación aditiva MIM
Paso | Descripción |
---|---|
Preparación de la materia prima | Mezcla de polvo metálico y aglutinante en una materia prima granulada |
Moldeo por inyección | Moldeado de la materia prima para darle la forma verde deseada |
Desbobinado | Eliminar el aglutinante para dejar una parte marrón |
Sinterización | Fusión del polvo metálico en la pieza final mediante calor |
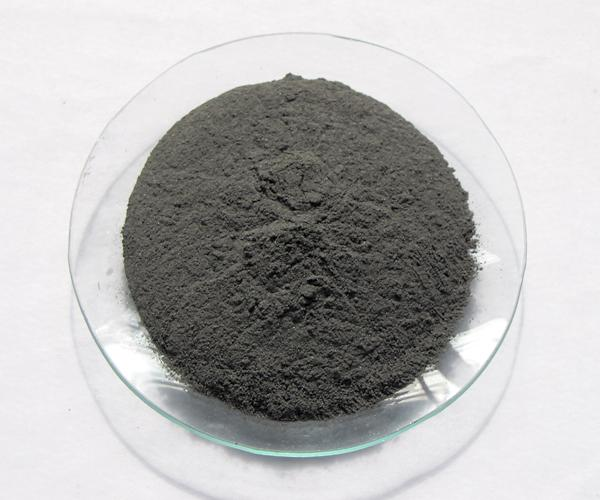
Aplicaciones de las piezas MIM
El MIM es adecuado para fabricar componentes metálicos pequeños, complejos y de forma neta en volúmenes medios y altos. Entre las aplicaciones típicas del MIM se incluyen:
Cuadro 2: Aplicaciones de la fabricación aditiva MIM
Industria | Componentes de ejemplo |
---|---|
Automotor | Boquillas de inyectores de combustible, engranajes rectos, piezas de turbocompresores |
Aeroespacial | Álabes de turbina, impulsores, iniciadores |
Médico | Brackets de ortodoncia, mangos de bisturí, pinzas |
Consumidores | Componentes de relojes, parrillas, piezas decorativas |
Industrial | Cuchillas, mecanismos de bloqueo, válvulas |
Armas de fuego | Gatillos, martillos, seguros, correderas |
El MIM permite consolidar piezas, reducir el peso, mejorar el rendimiento y disminuir los costes de fabricación en muchos sectores. La combinación de libertad geométrica y productividad hace que el MIM sea adecuado para la producción final.
En comparación con el mecanizado CNC, el MIM permite producir en serie formas más complejas. El MIM permite minimizar los pasos de montaje mediante la integración de piezas.
Ventajas de la fabricación aditiva MIM
El MIM ofrece ventajas únicas que lo convierten en una opción de fabricación muy popular:
Cuadro 3: Ventajas de la fabricación aditiva MIM
Beneficio | Descripción |
---|---|
Producción de gran volumen | MIM permite fabricar hasta millones de piezas al año |
Bajo coste por pieza | Reducción de costes con mayores volúmenes de producción |
Flexibilidad de diseño | Posibilidad de geometrías complejas y microcaracterísticas |
Gama de materiales | Pueden utilizarse la mayoría de las aleaciones en polvo, como acero inoxidable, acero para herramientas y titanio. |
Buenas propiedades mecánicas | Densidad casi total y composición uniforme |
Variedad de acabados | Pueden aplicarse mecanizados, grabados, chapados y otros acabados. |
Proceso establecido | Normas, bases de datos, años de experiencia disponibles |
La combinación de libertad de diseño, capacidad de los materiales y rentabilidad da al MIM ventajas sobre otros procesos como la impresión metálica en 3D, la fundición a la cera perdida o el mecanizado.
Las piezas pueden diseñarse con paredes más finas, rebajes, interiores huecos y otros elementos complejos. También es posible consolidar varios componentes en una pieza MIM.
Limitaciones de la fabricación aditiva MIM
Aunque tiene muchas ventajas, el MIM presenta algunas limitaciones:
Cuadro 4: Limitaciones de la fabricación aditiva MIM
Limitación | Descripción |
---|---|
Tamaño de la pieza | Normalmente se limita a componentes pequeños de hasta 70 pulgadas cúbicas |
Materiales de baja ductilidad | Algunas aleaciones dúctiles, como el aluminio, no son aptas para el MIM. |
Costes iniciales | Importante inversión en herramientas para los moldes |
Producción de mezcla baja | Más adecuado para volúmenes medios y altos de una misma pieza |
Postprocesado | Puede ser necesario un mecanizado o acabado adicional |
El MIM tiene límites geométricos, ya que implica moldeado. Los plásticos termoestables permiten fabricar piezas MIM más grandes, pero son menos resistentes.
No todas las aleaciones metálicas pueden convertirse fácilmente en materias primas para el MIM. Los materiales dúctiles, en particular, plantean dificultades.
Hay que fabricar moldes de acero duro para cada nuevo diseño de pieza. Esto añade tiempo y costes.
Los cambios frecuentes de diseño son menos adecuados para el MIM debido a las herramientas de molde fijas. Otros métodos de impresión 3D permiten una iteración más sencilla.
Dependiendo de los requisitos dimensionales y superficiales finales, pueden ser necesarias operaciones de postmoldeo.
Consideraciones sobre el diseño del MIM
El MIM permite libertades geométricas, pero las piezas deben diseñarse teniendo en cuenta las limitaciones del proceso:
Tabla 5: Consideraciones sobre el diseño del MIM
Parámetro | Directriz |
---|---|
Espesor de pared | Mínimo 0,3 mm, máximo 5 mm. Lo ideal es un grosor uniforme |
Tolerancias | ±0,5% es típico pero depende de la geometría |
Acabado superficial | As-sinterizado es alrededor de Ra 10-15 micras |
Ángulos de calado | Se requieren ángulos de tiro >1° para facilitar el desmoldeo |
Complejidad de la forma | Consolidar piezas u optimizar la topología es factible |
Características | Posibilidad de detalles finos, como orificios y ranuras de 0,1 mm. |
Texturas | Se pueden incorporar texturas complejas en el molde |
Insertos | Es posible incorporar otros insertos en el molde |
Reducción de peso | Ahuecamiento, reducción de masa mediante celosías y optimización de la topología |
El proceso de moldeo impone ciertas reglas de diseño. Pero el MIM puede producir geometrías inalcanzables con otros métodos.
Opciones de material MIM
Existe una amplia gama de aleaciones para el MIM, incluidos los aceros y el titanio más demandados:
Tabla 6: Opciones de material MIM
Material | Aplicaciones |
---|---|
Acero inoxidable | Productos médicos, marinos y de consumo |
Acero para herramientas | Herramientas de corte, moldes, piezas de desgaste |
Acero de baja aleación | Componentes de automoción y maquinaria |
Aleaciones de titanio | Aeroespacial, implantes médicos |
Aleaciones de níquel | Turbinas aeroespaciales, equipos marinos |
Aleaciones pesadas de wolframio | Protección contra radiaciones, amortiguación de vibraciones |
Se suelen utilizar aceros inoxidables de alta resistencia a la corrosión, como el 17-4PH y el 304L. Los grados de endurecimiento por precipitación permiten aumentar aún más la resistencia.
Los aceros para herramientas como el H13 son ideales para moldes de conformación, estampación e inyección que necesitan buena dureza, tenacidad y estabilidad térmica.
Las aleaciones de titanio para la biocompatibilidad, las aleaciones de níquel para la resistencia al calor y las aleaciones de tungsteno para la densidad son fácilmente MIM'able.
También se están desarrollando nuevos materiales, como las aleaciones MIM de cobre y aluminio.
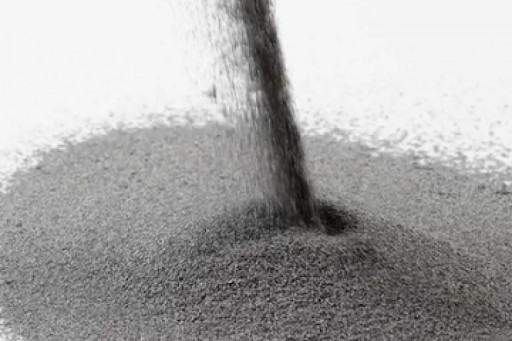
Opciones de software de diseño MIM
Para ayudar con los requisitos de diseño MIM, existen opciones de software CAD y de optimización topológica:
Tabla 7: Opciones de software de diseño MIM
Software | Descripción |
---|---|
SolidWorks | CAD popular con complementos de análisis de moldflow |
Autodesk Moldflow | Simulación específica de moldes de inyección |
nTopología | Optimización y diseño de topologías para software de AM |
Materialise 3-matic | Herramienta para diseñar celosías y estructuras ligeras |
Netfab | Software de optimización de mallas 3D para MIM |
Solidworks se utiliza habitualmente para el diseño CAD. La simulación de flujo de moldeo puede comprobar la fabricabilidad.
Programas especializados como Moldflow añaden funciones avanzadas de análisis y modelado de procesos.
Los programas de optimización topológica como nTopology permiten crear formas orgánicas a medida para AM y MIM. Permite aligerar y consolidar.
Programas como 3-matic ayudan a diseñar celosías de densidad variable y a generar estructuras de soporte.
Parámetros del proceso MIM
El MIM implica la optimización de las materias primas, el moldeo, el desbobinado y la sinterización. Los parámetros típicos son:
Tabla 8: Parámetros del proceso MIM
Paso | Alcance típico |
---|---|
Tamaño del polvo | 5 - 25 micras |
Carpeta | 30 - 50% de volumen de materia prima |
Carga de sólidos | 55 - 70% en materia prima |
Temperatura del molde | 150 - 185°C |
Presión de inyección | 60 - 110 MPa |
Velocidad de enfriamiento del moldeo | 20 - 50°C/s enfriamiento |
Método de desbobinado | Disolvente, térmico, catalítico |
Tiempo de desbobinado | De días a horas |
Temperatura de sinterización | 50 - 80% del punto de fusión |
Tiempo de sinterización | De horas a días |
Contracción | 13 - 17% encogimiento lineal |
Los parámetros dependen del material, la geometría de la pieza, el ritmo de producción y las propiedades necesarias.
Los polvos finos y las altas cargas de sólidos ayudan a la resolución. Un enfriamiento más rápido y temperaturas de molde más elevadas mejoran la resistencia en verde. Los menores tiempos de desbobinado y las mayores temperaturas de sinterización aumentan los índices de producción.
Opciones de postprocesado MIM
Dado que las piezas MIM sinterizadas pueden requerir un tratamiento adicional:
Tabla 9: Opciones de postprocesado del MIM
Proceso | Propósito |
---|---|
Tratamiento térmico | Cambiar la microestructura para mejorar las propiedades |
Revestimiento | Aplicar revestimientos decorativos como oro o cromo |
Pasivación | Crear una capa protectora de óxido en los aceros |
Soldadura | Unir piezas MIM entre sí o con otros componentes |
Marcado por láser | Marcas permanentes para logotipos, texto o códigos de identificación |
Mecanizado y taladrado | Dimensiones de mayor precisión o características personalizadas |
Acabado por vibración | Alisar la superficie y redondear los bordes afilados |
Los pasos posteriores al moldeo pueden mejorar el aspecto, las propiedades y las interfaces con otros componentes. Los acabados más populares son el chapado, el anodizado y la pintura.
En algunos ensamblajes puede ser necesario conectar las piezas MIM mediante soldadura, soldadura fuerte o pegado. El mecanizado adicional puede crear superficies de acoplamiento de precisión.
Proveedores de equipos MIM
Las empresas de moldeo por inyección establecidas ofrecen equipos y servicios MIM:
Cuadro 10: Proveedores de equipos MIM
Compañía | Equipamiento |
---|---|
ARBURG | Máquinas de moldeo por inyección eléctricas e hidráulicas |
Milacron | Líneas MIM integradas completas |
Toshiba | Moldeadoras híbridas y eléctricas |
Netstal | Moldeo por inyección de alta precisión |
Nissei | Inyectoras verticales y horizontales |
Sodick | Moldeo de alta velocidad y alta frecuencia |
También se ofrecen servicios especializados de MIM:
- PIM Internacional
- MPP
- MIMITAL
- Innovaciones CN
Estos proveedores de servicios completos ofrecen formulación de materias primas, análisis, utillaje, moldeo, desbobinado y sinterización.
Consideraciones sobre los costes de la fabricación aditiva MIM
El MIM tiene unos costes iniciales relativamente altos, pero unos costes por pieza bajos en volúmenes de producción:
Cuadro 11: Consideraciones sobre los costes del MIM
Factor de coste | Alcance típico |
---|---|
Herramienta para moldes | $10.000 - $100.000+ en función de la complejidad, el material y el tamaño |
Configuración de lotes pequeños | Menos de $10.000 |
Coste incremental de la pieza | $0,5 - $5 coste del metal por pieza |
Tasa de producción | 5.000 - 500.000 piezas al año por herramienta |
Acabado | $0,1 - $2 por pieza según el proceso |
Tamaño del lote Punto de equilibrio | 1.000 - 10.000+ piezas frente a otros procesos |
Fresar un molde MIM a partir de acero para herramientas puede llevar semanas y costar más de $100.000 si se trata de componentes grandes. Los moldes más pequeños y menos complejos pueden costar menos de $10.000.
Una vez fabricado el molde, los costes continuos del proceso MIM son muy económicos para volúmenes de producción medios y altos. El MIM puede producir hasta un millón de piezas al año a partir de un único molde.
Elegir entre MIM y otros procesos de AM
El MIM se sitúa entre la impresión 3D y los procesos de gran volumen:
Cuadro 12: Comparación entre el MIM y otros procesos de AM metálica
Factor | MIM | Impresión 3D Binder Jet | DMLS | Fundición a presión |
---|---|---|---|---|
Coste de capital | Alta para utillaje | Medio | Alta | Muy alta |
Coste por pieza | La más baja por encima de 10.000 piezas | Bajo a volúmenes bajos | Medio | Más bajo a volúmenes muy altos |
Materiales | Amplia gama de aleaciones | Alcance limitado | Alcance limitado | Aleaciones de aluminio y zinc |
Resolución | Medio ~0,1 - 0,3 mm | Medio ~0,3 - 0,5 mm | Máximo ~0,05 mm | Inferior ~0,5 mm |
Velocidad de producción | Alta | Medio | Lento | Muy alta |
Postprocesado | Medio | Alta | Medio | Bajo |
Propiedades mecánicas | Bien | Variable | Mejor | Bien |
Restricciones de diseño | Algunas limitaciones geométricas | Pocas limitaciones | Algunas limitaciones del voladizo | Alto nivel de restricciones |
El MIM ofrece la mejor rentabilidad para geometrías complejas en materiales de aleación necesarios en producciones de más de 10.000 unidades. Los procesos de producción en serie más económicos resultan más ventajosos con volúmenes mucho mayores.
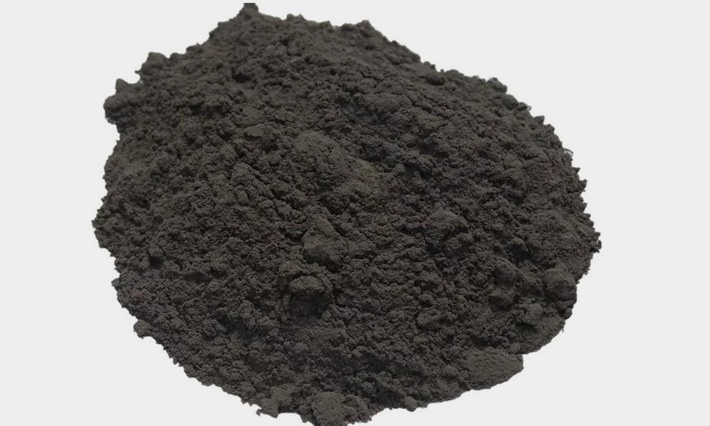
Conclusión
El MIM es un atractivo proceso de fabricación aditiva de metales que permite producir en serie geometrías complejas directamente en una serie de aleaciones de ingeniería.
Combina la versatilidad de la AM con una productividad cercana a la fabricación convencional. Esta potente fusión permite reducir los costes de las piezas, consolidar los ensamblajes, mejorar el rendimiento y aligerar la construcción.
Aunque requiere cierta inversión inicial en moldes, el MIM ofrece valiosas economías de escala. Se está consolidando como una técnica complementaria que salva la distancia entre la impresión 3D de prototipos y la fabricación de grandes volúmenes.
El desarrollo continuado de materiales y la integración de software ampliarán las aplicaciones del MIM en los sectores médico, aeroespacial, automovilístico, industrial y de consumo.
Fabricación aditiva MIM - FAQ
P: ¿En qué se diferencia el MIM de la fundición a presión?
R: El MIM puede producir geometrías más complejas y de mayor precisión que la fundición a presión, pero sus índices de producción y volúmenes son menores. La fundición a presión es más rápida y barata para formas más sencillas que se necesitan por millones.
P: ¿Qué tamaño de piezas pueden fabricarse con MIM?
R: Las piezas MIM suelen pesar entre 0,5 y 70 gramos. Es posible fabricar componentes más grandes, de hasta 250 gramos, con equipos capaces de soportar presiones y tamaños de utillaje más elevados.
P: ¿Qué determina el coste de un molde MIM?
R: El material del molde, la complejidad, el tamaño, los acabados superficiales y el tiempo de entrega afectan a los costes de fabricación del molde. Los moldes sencillos de acero para herramientas pueden costar menos de $10k, mientras que los moldes de acero templado para grandes producciones pueden superar $100k.
P: ¿Requiere el MIM algún tratamiento posterior?
R: Algunas aplicaciones requieren un tratamiento térmico adicional, mecanizado o acabado superficial. Pero muchos componentes pueden utilizarse sinterizados. El tratamiento posterior depende de los requisitos dimensionales y de aspecto finales.
P: ¿Cuántas piezas puede producir un molde MIM?
R: Los índices de producción de MIM suelen oscilar entre 5.000 y 500.000 piezas anuales por herramienta. Con un mantenimiento adecuado, es posible realizar millones de disparos durante años de vida útil.
P: ¿Qué errores de diseño MIM hay que evitar?
R: Los ángulos de desmoldeo insuficientes, los cortes severos, las transiciones de paredes gruesas a finas y la colocación de detalles finos en lados opuestos de un núcleo pueden causar problemas de moldeo. Se recomienda consultar con diseñadores experimentados.
P: ¿Se pueden combinar varios materiales en el MIM?
R: Sí, el MIM permite fabricar piezas multimaterial utilizando mezclas de polvos o múltiples materias primas. También es posible el moldeo por inserción con otras aleaciones o materiales duros para estructuras compuestas.
P: ¿Cómo es el acabado superficial de las piezas MIM?
R: El acabado sinterizado tiene una rugosidad de unas 10-15 micras. Es adecuado para muchas aplicaciones. Si es necesario, se pueden alisar aún más las superficies mediante volteo o pulido.
P: ¿Cuánto dura el proceso MIM?
R: Los plazos de entrega suelen oscilar entre 6 y 12 semanas. La fabricación de moldes es lo que más tiempo lleva, si es necesario. Una vez fabricadas las herramientas, la producción por lotes es bastante rápida para componentes pequeños.