Aleaciones de hierro en polvo se refiere a las formas pulvimetalúrgicas del hierro mezclado con elementos de aleación como níquel, cromo, manganeso y carbono. La pulvimetalurgia del hierro permite fabricar piezas y componentes con densidad, porosidad, resistencia, propiedades magnéticas y otras propiedades controladas mediante la compactación y sinterización de mezclas de polvo a base de hierro.
Visión general de las aleaciones de hierro en polvo
Los polvos de aleaciones de hierro ofrecen varias ventajas sobre las formas convencionales de hierro y acero:
- Elevada precisión dimensional y repetibilidad con capacidades cercanas a la forma de red
- Capacidad para obtener porosidad y densidades controladas
- Menores costes de fabricación gracias a la reducción del mecanizado
- Alto aprovechamiento del material con menor generación de residuos
- Capacidad de producción en serie de piezas complejas
El polvo de aleación de hierro suele estar disponible en hierro puro, aceros de baja aleación, aceros para herramientas, aceros inoxidables y aleaciones magnéticas blandas, como se indica a continuación:
Tipos de aleaciones de hierro en polvo
Tipo de polvo | Elementos de aleación | Caracteristicas | Aplicaciones |
---|---|---|---|
Hierro puro | Carbono < 0,008%, Oxígeno | Alta resistencia en verde, bajo coste | Automoción, maquinaria |
Aceros de baja aleación | C, Mn, Si, Cr, Mo | Mayor resistencia, templabilidad | Automoción, petróleo/gas |
Aceros para herramientas | C, W, Mo, V, Co | Gran dureza, resistencia al desgaste | Herramientas de corte, troqueles |
Aceros inoxidables | Cr, Ni, Mo | Resistencia a la corrosión, solidez | Válvulas marinas |
Magnético blando | Ni, Mo, Cu, Nb | Alta permeabilidad, baja pérdida | Electroimanes, motores |
Características del polvo de aleación de hierro
Las propiedades del polvo de aleación de hierro pueden ajustarse seleccionando los elementos de aleación y las condiciones de procesado adecuados:
Parámetro | Caracteristicas | Método de control |
---|---|---|
Composición | Elementos de aleación, residuos | Método de producción de polvo |
Tamaño de las partículas | Fino, ultrafino, microfino | Atomización gas/agua, fresado |
Forma de las partículas | Irregular, esférica, escamosa | Atomización gas/agua, condiciones |
Pureza | Niveles de oxígeno, nitrógeno y carbono | Recocido, atmósferas protectoras |
Densidad aparente | Densidad verde, densidad sinterizada | Presión de compactación, sinterización |
Porosidad | Poros abiertos y cerrados | Compactación, composición de la aleación |
Superficie | Superficie específica | Distribución granulométrica |
Aplicaciones del polvo de aleaciones de hierro
El polvo de aleación de hierro se utiliza en una amplia gama de aplicaciones en los siguientes sectores:
Industria | Aplicaciones | Componentes de ejemplo |
---|---|---|
Automotor | Engranajes, cojinetes, filtros, piezas del motor | Bielas, árboles de levas, segmentos de pistón |
Aeroespacial | Piezas estructurales, componentes de aeronaves y turbinas | Tren de aterrizaje, discos de turbina, fijaciones |
Maquinaria | Piezas de desgaste, componentes de herramientas, sistemas de accionamiento | Bujes, ejes, levas, poleas |
Eléctrico | Núcleos magnéticos blandos, rotores, piezas de motores eléctricos | Transformadores, inductores, estatores, rotores |
Consumidores | Piezas de cerraduras, cuchillas de afeitar, imanes | Candados, conjuntos magnéticos |
Médico | Instrumentos quirúrgicos, implantes, dispositivos | Bisturíes, implantes ortopédicos, máquinas de resonancia magnética |
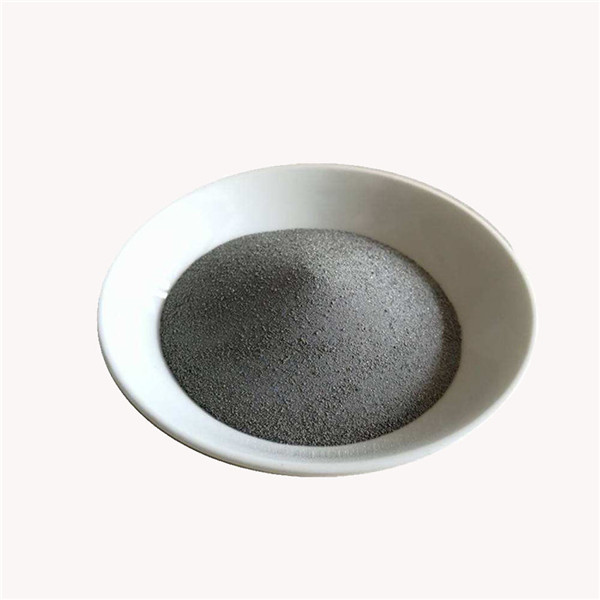
Especificaciones y normas de diseño
Las piezas de aleación de hierro en polvo deben ajustarse a las especificaciones de composición, propiedades mecánicas, dimensiones, acabado superficial y métodos de ensayo. Algunas normas importantes son:
Estándar | Descripción |
---|---|
ISO 4492 | Polvos metálicos - Pruebas de flexibilidad y dureza |
ISO 2738 | Materiales metálicos sinterizados - Probetas de tracción |
ISO 3995 | Polvos metálicos - Determinación de la resistencia en verde |
ISO 4490 | Medición de la densidad aparente de polvos metálicos |
Normas MPIF | Normas de materiales, métodos de ensayo publicados por la Federación de Industrias de Polvos Metálicos |
ASTM B783 | Especificación de piezas de pulvimetalurgia (PM) a base de hierro |
Las normas mínimas para el polvo suministrado son la pureza, la distribución granulométrica, la densidad aparente y el caudal. Para los componentes acabados, existen especificaciones de densidad, propiedades mecánicas, energía de impacto, dureza, maquinabilidad, resistencia a la corrosión y propiedades magnéticas.
Las normas de diseño proporcionan directrices sobre factores como las tolerancias dimensionales, el acabado superficial, la tolerancia de rebabas, el espesor de sección, los radios de redondeo, la colocación de nervaduras y el espesor de pared. Las reglas para el diseño de piezas de polvo metálico se establecen en la norma MPIF 35.
Fabricación y procesamiento de polvos
El proceso de fabricación del polvo de aleación de hierro consta de los siguientes pasos clave:
Producción de polvo
El polvo de aleación de hierro puede producirse mediante:
- Atomización - Fundir la aleación y desintegrar la corriente fundida en finas gotitas mediante chorros de gas o agua. El polvo atomizado con gas tiene partículas esféricas ideales para el prensado.
- Fresado mecánico - Repetidas soldaduras en frío, fracturas y refundiciones de la materia prima en molinos de bolas de alta energía. Produce polvo fino de forma irregular.
- Electrólisis - Deposición electrolítica de polvos de hierro a partir de soluciones acuosas.
- Reducción - Reducción química de polvos de óxido de hierro a hierro utilizando hidrógeno o gas monóxido de carbono.
- Otros métodos - Descomposición carbonílica, atomización rotativa, atomización por plasma, condensación de vapor.
Método | Forma de las partículas | Tamaño de partícula | Pureza | Coste |
---|---|---|---|---|
Atomización de gases | Esférica | 15 - 150 μm | Alta | Alta |
Atomización del agua | Irregular | 150 - 300 μm | Medio | Bajo |
Fresado mecánico | Flaky | 1 - 100 μm | Bajo | Medio |
Mezcla de polvos
El polvo de hierro base se mezcla con elementos de aleación, lubricantes y agentes de flujo según la composición de aleación final requerida. La mezcla de polvo se homogeneiza en un mezclador para obtener una composición uniforme.
Compactación
La compactación presiona la mezcla de polvo en una cavidad de la matriz bajo altas presiones para producir un compacto verde con la forma deseada. Los métodos de compactación habituales son:
- Prensado de acción simple: Sencillas, de bajo coste, adecuadas para bajos índices de producción. Presiones de hasta 600 MPa.
- Prensado de doble acción: El polvo se comprime desde los punzones superior e inferior. Presiones de hasta 1000 MPa. Mejor uniformidad de la pieza.
- Prensado isostático: Presión uniforme aplicada en todas las superficies de un fluido. Formas complejas, densidades uniformes. Requiere encapsulación.
- Compactación de rodillos: El polvo se comprime entre dos rodillos para formar una hoja. La hoja se granula para prensarla. Mejora el flujo del polvo.
Sinterización
La sinterización densifica el compacto calentándolo por debajo del punto de fusión para inducir la unión entre partículas. La sinterización activa procesos de difusión que eliminan los poros y aumentan la resistencia. La sinterización se realiza en atmósferas controladas para evitar la oxidación.
Operaciones secundarias
Para obtener la geometría final de la pieza y las propiedades requeridas por la aplicación, se utilizan operaciones adicionales como acuñado, reprimido, infiltración, mecanizado y tratamiento superficial.
Instalación, funcionamiento y mantenimiento
Las siguientes directrices se aplican a las prensas de polvo y a los hornos de sinterización:
- Instale el equipo sobre bases planas y sin vibraciones de acuerdo con las especificaciones del fabricante.
- Nivele el cilindro y el cabezal del equipo de prensado para evitar una compactación desigual.
- Garantizar una lubricación adecuada de las prensas y los punzones de acuerdo con el manual de instrucciones.
- Instalar sistemas adecuados de ventilación y refrigeración
- Calibración de sensores de temperatura, controladores y dispositivos de registro en hornos
- Utilizar gases inertes como el nitrógeno o el amoníaco disociado para minimizar la oxidación.
- Elaborar calendarios y procedimientos para el mantenimiento preventivo de los equipos.
- Inspeccione periódicamente las herramientas de prensado y los punzones en busca de desgaste, grietas o daños.
- Compruebe periódicamente el aislamiento del horno y los elementos calefactores
- Validar los procesos de forma rutinaria para garantizar un calentamiento uniforme y el cumplimiento de las normas.
- Formar a los operarios sobre los procedimientos operativos adecuados, las precauciones de seguridad y los controles de calidad.
- Siga las directrices del fabricante para las inspecciones, lubricación, ajustes y reparaciones del equipo.
- Mantener registros de todas las actividades de mantenimiento de los equipos y de los datos de producción de piezas.
Elegir un proveedor de aleaciones de hierro en polvo
Los factores clave en la selección de un proveedor de polvo de aleación de hierro son:
Parámetro | Descripción |
---|---|
Calidad del polvo | Química, forma de las partículas, distribución del tamaño, pureza |
Gama de composición | Variedad de grados de material y sistemas de aleación |
Capacidad de fabricación | Atomización, molienda, mezcla, tamizado, secado |
Instalaciones de ensayo | Para el análisis químico, el tamaño de las partículas, la densidad en verde, las propiedades sinterizadas |
Certificaciones de calidad | ISO 9001, IATF 16949, AS9100, ISO 13485 |
Conocimientos técnicos | Conocimiento de aleaciones, aportaciones al diseño de piezas, ingeniería de aplicaciones |
Atención al cliente | Capacidad de respuesta a las solicitudes, gestión de proyectos |
Entrega | Registro de entregas puntuales, flexibilidad cuantitativa |
Ubicación | Proximidad a las operaciones para reducir los plazos de entrega |
Precios | Competitividad, descuentos por volumen, estabilidad |
Los proveedores deben proporcionar certificados de análisis que detallen la composición, la distribución granulométrica, la densidad aparente y el análisis por tamizado. Deben disponer de equipos técnicos que colaboren en el diseño de las piezas y la selección del polvo. El proceso y los controles de calidad del proveedor deben garantizar la coherencia entre lotes de polvo.
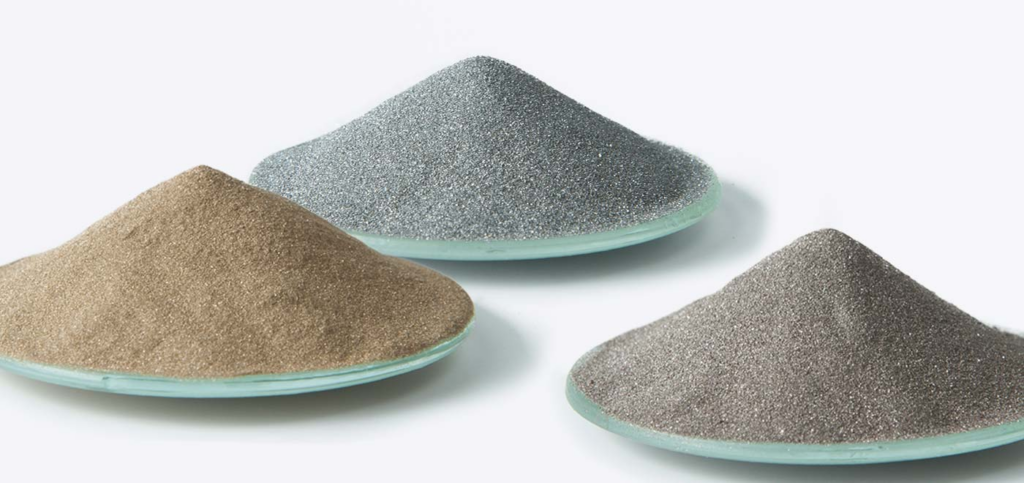
Ventajas e inconvenientes de la pulvimetalurgia
Ventajas | Desventajas |
---|---|
Forma casi neta, mecanizado mínimo | Resistencia limitada del material en comparación con las aleaciones forjadas |
Buena precisión dimensional | Limitaciones de tamaño en función de la capacidad de la prensa |
Posibilidad de geometrías complejas | Restricciones en la complejidad de la forma y el grosor de las paredes |
Económico para la producción en serie | Las operaciones secundarias aumentan el coste por menores volúmenes |
Amplia gama de aleaciones disponibles | Propiedades anisótropas debidas al prensado |
Desperdicio mínimo en comparación con el mecanizado | Requiere sinterización en atmósfera controlada |
Menor consumo de energía que la metalurgia | Inversión de capital para la producción de polvo |
Control de la porosidad de filtros y cojinetes | Se necesita experiencia en manipulación y mezcla de polvos |
Preguntas más frecuentes
P: ¿Cuáles son las distintas calidades de polvo de hierro disponibles?
R: Las principales calidades son el hierro puro, los aceros de baja aleación, los aceros para herramientas, los aceros inoxidables y las aleaciones magnéticas blandas. Cada uno tiene una composición específica adaptada a sus propiedades mecánicas, magnéticas o de otro tipo.
P: ¿Qué distribución granulométrica es ideal para el prensado de polvo de hierro?
R: Se prefiere un rango de tamaño de partícula de 15-150 μm, con la mayoría entre 45-75 μm. El polvo más fino se empaqueta mejor pero puede tener poca fluidez para el llenado de troqueles. El polvo más grueso tiene buena fluidez pero afecta a la densificación.
P: ¿Cómo mejorar las propiedades de fluidez del polvo para el prensado?
R: La adición de lubricantes como el estearato de zinc o la bisestearamida de etileno en 0,5-1% mejora la fluidez del polvo. El recocido del polvo o el uso de polvo atomizado esférico también mejoran el flujo.
P: ¿Qué causa las grietas en las piezas de hierro sinterizado?
R: Las partículas grandes, la amplia distribución de las partículas, el alto contenido de aleación, las altas velocidades de calentamiento/enfriamiento y las secciones gruesas pueden provocar defectos de agrietamiento durante la sinterización. Es necesario optimizar la composición, las características del polvo, el diseño de la pieza y el ciclo de sinterización.
P: ¿Qué afecta a la tolerancia dimensional de las piezas de polvo metálico?
R: Los factores clave son el desgaste de la matriz, el springback elástico tras el prensado, la uniformidad de la temperatura de sinterización, la geometría de la pieza, las operaciones secundarias y el mecanizado final. Los controles del proceso y el diseño de la matriz son fundamentales.
P: ¿Cómo mejorar la resistencia al desgaste de los componentes pulvimetalúrgicos de hierro?
R: Aumentar la dureza mediante aleación con carbono, cromo, molibdeno, vanadio, wolframio o por impregnación. Una menor porosidad y una mayor densificación también mejoran la resistencia al desgaste.
P: ¿Qué ventajas tiene la infiltración de cobre en las piezas de hierro?
R: El cobre fundido rellena la porosidad interna por acción capilar, mejorando la resistencia, el módulo elástico, la energía de impacto, la vida a fatiga y la conductividad eléctrica.
P: ¿Pueden procesarse los polvos de acero inoxidable como los polvos de acero para herramientas?
R: No, el acero inoxidable requiere atmósferas protectoras durante la compactación y la sinterización para evitar la oxidación. Los parámetros de procesamiento deben optimizarse por separado.
P: ¿Qué causa el cambio dimensional durante la sinterización?
R: Las principales razones son la contracción al cerrarse los poros, las transformaciones de fase que provocan cambios de volumen y la distribución no uniforme de la temperatura que provoca distorsiones. Para minimizar los cambios dimensionales, es necesario configurar correctamente el horno y seleccionar el ciclo de sinterización.