Überblick über das Laser Metal Deposition (LMD)
Laser-Metallabscheidung (LMD) ist eine bahnbrechende Technologie der additiven Fertigung (AM), bei der mit einem Hochleistungslaser Metallpulver oder -draht Schicht für Schicht auf ein Substrat aufgeschmolzen und verschmolzen wird, um dreidimensionale Strukturen zu erzeugen. Ob in der Luft- und Raumfahrt, in der Automobilindustrie oder in der Medizintechnik - LMD ist eine robuste Lösung für komplexe Metallteile, die Präzision, Haltbarkeit und Effizienz erfordern.
Stellen Sie sich vor, Sie müssen eine verschlissene Turbinenschaufel reparieren oder ein maßgeschneidertes Implantat herstellen. Herkömmliche Fertigungsmethoden sind vielleicht zu langsam, zu teuer oder einfach nicht präzise genug. LMD kommt wie ein Superheld daher und schweißt mit Hilfe von Lasern Metallpulver Schicht für Schicht in die perfekte Form. Das Ergebnis? Hochpräzise und stabile Komponenten, die sogar die Originale in den Schatten stellen können.
Aber wie funktioniert es? Was sind die verwendeten Materialien? Und vor allem, wie kann Ihr Unternehmen davon profitieren? In diesem ausführlichen Leitfaden gehen wir auf die Besonderheiten von LMD ein, angefangen bei den verwendeten Metallpulvern bis hin zu den Vor- und Nachteilen und einem praktischen FAQ-Bereich, der alle offenen Fragen klärt.
Also, schnallen Sie sich an, wenn wir die faszinierende Welt des Laser Metal Deposition erkunden!
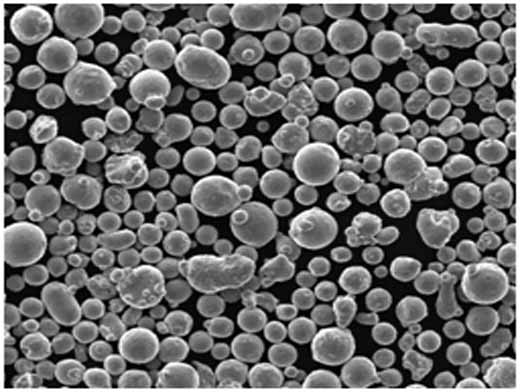
Was ist Laser Metal Deposition (LMD)?
LMD ist eine Art der additiven Fertigung, auch bekannt als 3D-Druck, bei der Materialien hinzugefügt statt entfernt werden. Bei diesem Verfahren wird ein fokussierter Laserstrahl verwendet, um Metallpulver oder -draht zu schmelzen, das dann auf ein Substrat aufgebracht wird. Diese Technologie ermöglicht eine präzise Kontrolle über das Material und damit die Herstellung komplexer Geometrien und leistungsstarker Metallkomponenten.
Wie funktioniert die Laser-Metallabscheidung?
Beim Laserauftragschweißen wird Metallpulver durch eine Düse in einen Laserstrahl geleitet, der das Pulver schmilzt und mit einem Grundmaterial (Substrat) verschmilzt. Während sich der Laser bewegt, baut er Metallschichten auf, die die gewünschte Form bilden. Es ist, als würde man eine Mauer bauen, nur dass man statt Ziegeln winzige Metallkörner verwendet und statt Mörtel einen Hochenergielaser, der alles miteinander verbindet.
- Laser Quelle: Der Typ und die Leistung des Lasers bestimmen, wie das Metallpulver schmilzt und erstarrt. Faserlaser werden häufig wegen ihrer Effizienz und Präzision eingesetzt.
- Pulverzufuhrsystem: Metallpulver wird über eine Düse dem Laserstrahl zugeführt. Die Konsistenz des Pulverflusses ist entscheidend für das Erreichen gleichmäßiger Schichten.
- Bewegungssteuerung: Die Bewegung des Lasers und des Pulverzufuhrsystems wird präzise gesteuert, häufig mit CNC- oder Robotersystemen, um die gewünschte Geometrie zu erzeugen.
Diese Präzision bedeutet, dass LMD nicht nur für die Herstellung neuer Teile geeignet ist. Es kann auch bestehende Teile reparieren, indem es bei Bedarf Material hinzufügt, was besonders für teure Komponenten in Branchen wie der Luft- und Raumfahrt nützlich ist.
Anwendungen von Laser-Metallabscheidung (LMD)
Das Laser Metal Deposition (LMD) ist ein vielseitiges Verfahren mit einer breiten Palette von Anwendungen in verschiedenen Branchen. Von der Reparatur hochwertiger Komponenten bis hin zur Herstellung komplexer, kundenspezifischer Teile - das LMD-Verfahren schlägt in der Fertigung hohe Wellen.
Wichtigste Anwendungen:
Industrie | Anmeldung | Vorteile |
---|---|---|
Luft- und Raumfahrt | Reparatur von Turbinenschaufeln, Triebwerkskomponenten | Geringere Ausfallzeiten, längere Lebensdauer der Teile |
Automobilindustrie | Getriebe- und Kurbelwellenreparaturen, Sonderteile | Verbesserte Leistung, kostengünstige Produktion |
Medizinische | Individuelle Implantate, zahnmedizinische Komponenten | Hohe Präzision, Biokompatibilität |
Werkzeugbau | Reparatur von Formen, Restaurierung von Stümpfen | Längere Lebensdauer der Werkzeuge, kürzere Durchlaufzeit |
Öl & Gas | Ventilsitze, Bohrkomponenten | Widerstandsfähigkeit gegen raue Umgebungen, geringere Ersatzteilkosten |
Stromerzeugung | Turbinenreparaturen, Komponentenfertigung | Verbesserte Effizienz, geringere Wartungskosten |
Verteidigung | Waffenkomponenten, Reparatur kritischer Ausrüstung | Hohe Festigkeit, Haltbarkeit unter extremen Bedingungen |
Energie | Komponenten für Windkraftanlagen, Teile für Kernreaktoren | Nachhaltigkeit, hohe Leistung bei kritischen Operationen |
Bauwesen | Kundenspezifische Bauteile, Reparatur von Schwermaschinen | Stärke, Flexibilität, Kosteneffizienz |
Marine | Propellerreparaturen, Schiffsmaschinenteile | Korrosionsbeständigkeit, Langlebigkeit in Meeresumgebungen |
Jede dieser Branchen hat ihre eigenen Anforderungen, und LMD kann sie dank seiner Flexibilität problemlos erfüllen. Ob es sich nun um hochfeste Werkstoffe für die Luft- und Raumfahrt oder um biokompatible Metalle für medizinische Implantate handelt - LMD kann sie alle verarbeiten.
Spezifische Metallpulver, die in LMD verwendet werden
Die Wahl des Metallpulvers ist bei LMD von entscheidender Bedeutung, da sie sich direkt auf die Qualität, Haltbarkeit und Funktionalität des Endprodukts auswirkt. Im Folgenden werden einige der bei LMD üblicherweise verwendeten Metallpulver sowie deren Zusammensetzung und Eigenschaften vorgestellt.
Die 10 besten Metallpulver für LMD:
Metall-Pulver | Zusammensetzung | Eigenschaften | Merkmale |
---|---|---|---|
Inconel 625 | Nickel-Chrom-Molybdän-Niob-Legierung | Hohe Festigkeit, ausgezeichnete Korrosionsbeständigkeit | Einsatz in der Luft- und Raumfahrt, Schifffahrt und chemischen Industrie |
Titanium Ti-6Al-4V | Titan-Aluminium-Vanadium-Legierung | Hohes Festigkeits-Gewichts-Verhältnis, Biokompatibilität | Ideal für medizinische Implantate, Luft- und Raumfahrt |
Rostfreier Stahl 316L | Eisen-Chrom-Nickel-Molybdän-Legierung | Korrosionsbeständigkeit, gute mechanische Eigenschaften | Üblich in der medizinischen und lebensmittelverarbeitenden Industrie |
Kobalt-Chrom (Co-Cr) | Kobalt-Chrom-Legierung | Abriebfestigkeit, Biokompatibilität | Verwendung in zahnmedizinischen und orthopädischen Implantaten |
Aluminium AlSi10Mg | Aluminium-Silizium-Magnesium-Legierung | Leichtes Gewicht, gute thermische Eigenschaften | Beliebt in der Automobil-, Luft- und Raumfahrtindustrie |
Hastelloy X | Nickel-Chrom-Eisen-Molybdän-Legierung | Hitzebeständigkeit, Oxidationsbeständigkeit | Geeignet für Umgebungen mit hohen Temperaturen |
Martensitaushärtender Stahl 18Ni300 | Nickel-Kobalt-Molybdän-Titan-Legierung | Ultrahohe Festigkeit, gute Zähigkeit | Einsatz im Werkzeugbau, in der Luft- und Raumfahrt |
Nickel 718 | Nickel-Chrom-Eisen-Legierung | Hohe Zugfestigkeit, Kriechstromfestigkeit | Weit verbreitet in Turbinentriebwerken, in der Luft- und Raumfahrt |
Werkzeugstahl H13 | Chrom-Molybdän-Vanadium-Legierung | Hohe Härte, Verschleißfestigkeit | Ideal für Werkzeugbau, Druckgussformen |
Kupfer-CrZr | Kupfer-Chrom-Zirkonium-Legierung | Ausgezeichnete Wärmeleitfähigkeit, Festigkeit | Verwendung in Wärmetauschern, elektrischen Komponenten |
Diese Metallpulver werden sorgfältig nach den spezifischen Anforderungen der jeweiligen Anwendung ausgewählt, einschließlich Faktoren wie Festigkeit, Korrosionsbeständigkeit und Biokompatibilität.
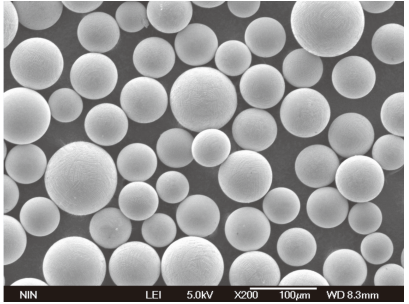
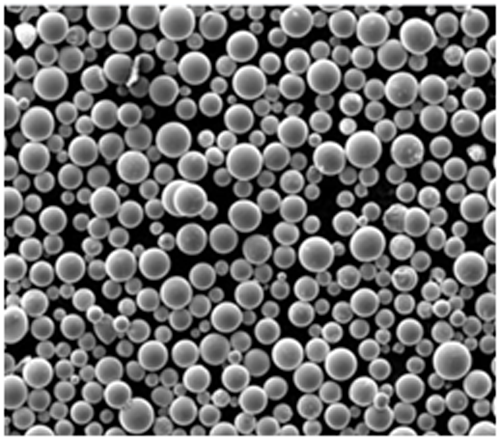
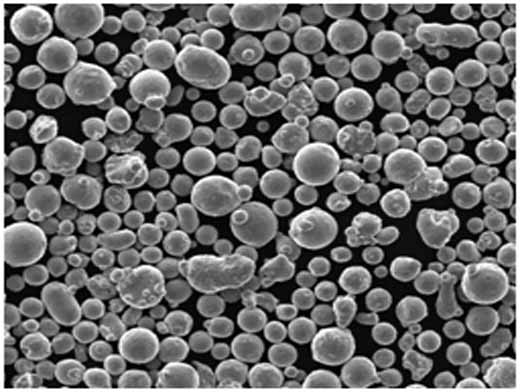
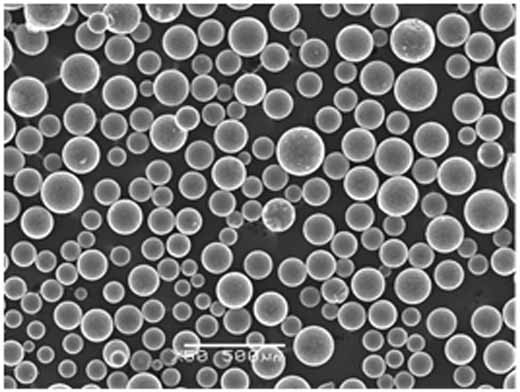
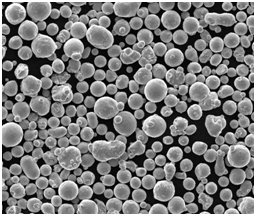
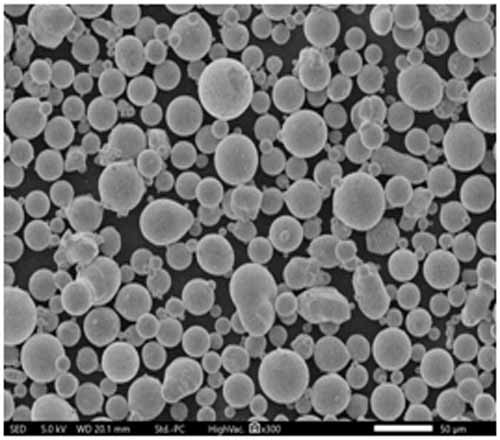
Eigenschaften und Merkmale von Laser-Metallabscheidung (LMD)
Ein Verständnis der Eigenschaften und Merkmale von LMD ist unerlässlich, um die Möglichkeiten und potenziellen Grenzen von LMD zu verstehen. Im Folgenden werden diese Aspekte aufgeschlüsselt, um ein klareres Bild der Funktionsweise von LMD zu erhalten.
Materialeigenschaften:
Eigentum | Beschreibung |
---|---|
Dichte | LMD-Bauteile haben in der Regel eine hohe Dichte, die mit der von Schmiedeteilen vergleichbar ist. |
Mikrostruktur | Es können feine Mikrostrukturen erzielt werden, die zu hoher Festigkeit und Zähigkeit führen. |
Oberflächengüte | Die Oberflächengüte kann je nach Pulver und Prozessparametern variieren und erfordert häufig eine Nachbearbeitung. |
Porosität | Mit optimierten Parametern kann eine minimale Porosität erreicht werden, die jedoch je nach Material und Anwendung variieren kann. |
Eigenspannungen | LMD kann zu Eigenspannungen führen, die möglicherweise durch eine Wärmebehandlung abgebaut werden müssen. |
Prozessmerkmale:
Charakteristisch | Einzelheiten |
---|---|
Schichtdicke | Je nach Anwendung liegt sie in der Regel zwischen 50 und 500 Mikrometern. |
Ablagerungsrate | Bereich von 0,5 bis 3 kg/Stunde, abhängig von Material und Laserleistung. |
Genauigkeit | Hohe Präzision mit Toleranzen im Bereich von ±0,1 mm oder besser. |
Flexibilität | Kann komplexe Geometrien und mehrere Materialien in einem einzigen Bauvorgang verarbeiten. |
Skalierbarkeit | Geeignet für kleine und große Bauteile, von Prototypen bis zur Produktion. |
Die Kombination dieser Eigenschaften und Merkmale macht LMD zu einem leistungsstarken Werkzeug für die Herstellung und Reparatur von Hochleistungsmetallkomponenten.
Vorteile und Grenzen des Laser Metal Deposition (LMD)
Wie jedes Herstellungsverfahren hat auch LMD seine Stärken und Schwächen. Im Folgenden finden Sie eine Aufschlüsselung der Vorteile und Einschränkungen, damit Sie feststellen können, ob LMD die richtige Lösung für Ihre Anforderungen ist.
Vorteile:
Vorteil | Erläuterung |
---|---|
Präzision und Genauigkeit | LMD kann hochdetaillierte Bauteile mit engen Toleranzen herstellen. |
Materialeffizienz | Es fällt nur wenig Abfall an, so dass es sich um eine kostengünstige Option handelt. |
Vielseitigkeit | Geeignet für die Bearbeitung einer Vielzahl von Materialien, einschließlich schwer zu bearbeitender Metalle. |
Reparaturfähigkeiten | LMD zeichnet sich durch die Reparatur hochwertiger Komponenten aus, verlängert deren Lebensdauer und reduziert Ausfallzeiten. |
Personalisierung | Leicht anpassbar für kleine Produktionsserien oder maßgefertigte Teile. |
Beschränkungen:
Begrenzung | Erläuterung |
---|---|
Hohe Anfangskosten | Die Kosten für Ausrüstung und Einrichtung können beträchtlich sein, so dass es sich um eine erhebliche Investition handelt. |
Oberflächengüte | Oft ist eine Nachbearbeitung erforderlich, um eine glatte Oberfläche zu erhalten. |
Komplexität der Operation | Erfordert geschultes Personal und eine genaue Kontrolle der Parameter. |
Von der Hitze betroffene Zonen | Der Laser kann wärmebeeinflusste Zonen einführen, die die Materialeigenschaften verändern können. |
Materielle Beschränkungen | Nicht alle Materialien sind für LMD geeignet, insbesondere solche mit geringem Laserabsorptionsvermögen. |
Die Kenntnis dieser Vor- und Nachteile wird Ihnen helfen, eine fundierte Entscheidung zu treffen, wenn Sie LMD für Ihre Produktionsanforderungen in Betracht ziehen.
Prozessparameter, die die Laser-Metallabscheidung (LMD) beeinflussen
Die Qualität der mittels Laser Metal Deposition hergestellten Bauteile hängt in hohem Maße von mehreren Prozessparametern ab. Diese Parameter müssen sorgfältig kontrolliert werden, um die gewünschten mechanischen Eigenschaften, die Oberflächengüte und die Gesamtleistung des Endprodukts zu gewährleisten.
Wichtige Prozessparameter:
Parameter | Beschreibung | Einfluss auf das Endprodukt |
---|---|---|
Laserleistung | Die vom Laser gelieferte Energiemenge, normalerweise in Watt gemessen. | Eine höhere Leistung erhöht die Abscheidungsrate, kann aber zu Überhitzung führen. |
Scan-Geschwindigkeit | Die Geschwindigkeit, mit der sich der Laser über das Substrat bewegt. | Schnellere Geschwindigkeiten können die Wärmezufuhr verringern, können aber zu einer unvollständigen Fusion führen. |
Pulverfördermenge | Die Geschwindigkeit, mit der das Metallpulver dem Schmelzbad zugeführt wird. | Höhere Raten erhöhen die Abscheidungseffizienz, können aber zu Porosität führen, wenn sie nicht kontrolliert werden. |
Abschirmgasfluss | Die Durchflussmenge des Inertgases, das zum Schutz des Schmelzbades vor Oxidation verwendet wird. | Eine angemessene Abschirmung verhindert Oxidation und Verschmutzung. |
Laser Spot Size | Der Durchmesser des Laserstrahls auf dem Substrat. | Eine kleinere Punktgröße verbessert die Präzision, kann aber den Prozess verlangsamen. |
Überschneidungsverhältnis | Der Grad der Überlappung zwischen benachbarten Laserdurchgängen. | Eine größere Überlappung gewährleistet Gleichmäßigkeit, kann aber die Bearbeitungszeit erhöhen. |
Vorwärmen des Substrats | Die Temperatur des Substrats vor Beginn der Abscheidung. | Das Vorwärmen reduziert Eigenspannungen und Rissbildung. |
Jeder dieser Parameter spielt eine entscheidende Rolle bei der Bestimmung der Qualität und Konsistenz des LMD-Prozesses. So können beispielsweise eine ungeeignete Laserleistung oder Scangeschwindigkeit zu Defekten wie Porosität, Rissbildung oder schlechter Haftung zwischen den Schichten führen.
Optimierung der LMD-Parameter für beste Ergebnisse
Um mit LMD die besten Ergebnisse zu erzielen, müssen diese Parameter für jede spezifische Anwendung und jedes Material optimiert werden. Dies erfordert häufig eine Kombination aus Experimenten und Simulationen, um den optimalen Punkt zu finden, an dem das Verfahren sowohl effizient ist als auch qualitativ hochwertige Teile erzeugt.
Bei der Arbeit mit einer hochfesten Legierung wie Inconel 625 ist beispielsweise die Steuerung der Laserleistung und der Scangeschwindigkeit von entscheidender Bedeutung, um eine Überhitzung zu vermeiden, die zu unerwünschten Gefügeveränderungen führen kann. Umgekehrt liegt der Schwerpunkt bei einem nachgiebigeren Material wie Edelstahl 316L eher auf der Optimierung der Pulverzufuhr und des Schutzgasflusses, um die Abscheidungseffizienz zu maximieren.
Moderne Materialien für die Laser-Metallabscheidung
Neben den oben genannten gängigen Metallpulvern kann LMD auch mit spezielleren Werkstoffen arbeiten. Diese fortschrittlichen Werkstoffe werden in Anwendungen eingesetzt, bei denen Standardmetalle die erforderlichen Leistungskriterien nicht erfüllen, z. B. bei extremen Temperaturen, korrosiven Umgebungen oder besonderen mechanischen Anforderungen.
Zusätzliche fortschrittliche Metallpulver für LMD:
Metall-Pulver | Zusammensetzung | Eigenschaften | Merkmale |
---|---|---|---|
Nickellegierung 263 | Nickel-Chrom-Kobalt-Molybdän-Legierung | Hochtemperaturfestigkeit, Oxidationsbeständigkeit | Ideal für Turbinenschaufeln, Verbrennungsauskleidungen |
Haynes 282 | Nickel-Eisen-Chrom-Molybdän-Titan-Legierung | Hohe Kriechfestigkeit, ausgezeichnete Schweißbarkeit | Einsatz in der Luft- und Raumfahrt, Energieerzeugung |
Tantal (Ta) | Reines Tantal | Ausgezeichnete Korrosionsbeständigkeit, Biokompatibilität | Geeignet für chemische Verarbeitung, medizinische Geräte |
Niobium (Nb) | Reines Niobium | Hoher Schmelzpunkt, gute supraleitende Eigenschaften | Verwendung in Supraleitern, Komponenten für die Luft- und Raumfahrt |
Tungsten (W) | Pure tungsten | Extrem hoher Schmelzpunkt, hohe Dichte | Ideal für Hochtemperaturanwendungen |
Inconel 738 | Nickel-Chrom-Kobalt-Aluminium-Legierung | Außergewöhnliche Oxidationsbeständigkeit, hohe Festigkeit | Verwendet in Komponenten von Gasturbinen mit heißem Abschnitt |
Rene 41 | Nickel-Chrom-Kobalt-Aluminium-Legierung | Hervorragende Hochtemperaturfestigkeit, Oxidationsbeständigkeit | Üblich in der Luft- und Raumfahrt, Gasturbinen |
Ti-5553 | Titan-Aluminium-Molybdän-Vanadium-Chrom-Legierung | Hohe Festigkeit, Zähigkeit, gute Korrosionsbeständigkeit | Einsatz in der Luft- und Raumfahrt, militärische Anwendungen |
Kobaltlegierung Stellit 6 | Kobalt-Chrom-Wolfram-Kohlenstoff-Legierung | Ausgezeichnete Verschleißfestigkeit, gute Korrosionsbeständigkeit | Ideal für Ventilsitze, Schneidwerkzeuge |
Ni-Cr-B-Si (Colmonoy 88) | Nickel-Chrom-Bor-Silizium-Legierung | Härte, Verschleißfestigkeit, gute Korrosionsbeständigkeit | Verwendet für Oberflächenbeschichtungen, Reparaturanwendungen |
Diese fortschrittlichen Materialien werden aufgrund ihrer einzigartigen Eigenschaften ausgewählt, die sie für äußerst anspruchsvolle Anwendungen geeignet machen. So ist Tantal aufgrund seiner ausgezeichneten Korrosionsbeständigkeit ideal für chemische Verarbeitungsgeräte, während Wolfram aufgrund seines extremen Schmelzpunkts die erste Wahl für Bauteile ist, die sehr hohen Temperaturen ausgesetzt sind.
Vergleich fortschrittlicher Materialien
Der Vergleich dieser fortschrittlichen Werkstoffe zeigt, dass bestimmte Legierungen unter bestimmten Bedingungen besser abschneiden können als andere, wodurch sie für bestimmte Anwendungen besser geeignet sind.
Material | Stärke | Temperaturbeständigkeit | Korrosionsbeständigkeit | Verschleißfestigkeit | Eignung der Anwendung |
---|---|---|---|---|---|
Nickellegierung 263 | Hoch | Ausgezeichnet | Mäßig | Gut | Turbinen, Hochtemperaturkomponenten |
Tantal | Mäßig | Hoch | Ausgezeichnet | Mäßig | Chemische Verarbeitung, medizinische Geräte |
Tungsten | Extrem hoch | Herausragend | Mäßig | Ausgezeichnet | Hochtemperaturanwendungen, Luft- und Raumfahrt |
Kobaltlegierung Stellit 6 | Mäßig | Gut | Gut | Ausgezeichnet | Schneidwerkzeuge, Ventilsitze |
Inconel 738 | Sehr hoch | Ausgezeichnet | Gut | Mäßig | Gasturbinenkomponenten, Luft- und Raumfahrt |
Diese Vergleiche können den Herstellern helfen, das richtige Material für ihre spezifischen Anforderungen auszuwählen und dabei Faktoren wie Festigkeit, Temperaturbeständigkeit und Kosten abzuwägen.
Anwendungen fortgeschrittener Materialien in LMD
Die Verwendung fortschrittlicher Werkstoffe bei LMD erweitert die Einsatzmöglichkeiten auf hochspezialisierte Bereiche, in denen herkömmliche Fertigungsmethoden oder Werkstoffe versagen würden. Diese Materialien können strenge Anforderungen erfüllen und bieten verbesserte Leistung, Langlebigkeit und Zuverlässigkeit in kritischen Anwendungen.
Spezialisierte Anwendungen:
Industrie | Anmeldung | Verwendetes Material | Vorteile |
---|---|---|---|
Luft- und Raumfahrt | Brennkammerauskleidungen, Turbinenschaufeln | Nickellegierung 263, Haynes 282 | Hohe Temperaturbeständigkeit, hervorragende mechanische Eigenschaften |
Medizinische | Kundenspezifische Implantate, chirurgische Werkzeuge | Tantal, Kobalt-Chrom (Co-Cr) | Biokompatibilität, Korrosionsbeständigkeit |
Energie | Komponenten von Kernreaktoren, Wellen von Windkraftanlagen | Wolfram, Rene 41 | Strahlungsbeständigkeit, Festigkeit unter Belastung |
Verteidigung | Gepanzerte Fahrzeuge, militärische Ausrüstung | Ti-5553, Wolfram | Hohe Festigkeit, Zähigkeit, Gewichtsreduzierung |
Automobilindustrie | Hochleistungsmotorenkomponenten, Wärmetauscher | Inconel 738, Titan Ti-6Al-4V | Hitzebeständigkeit, Festigkeit, geringes Gewicht |
Öl & Gas | Bohrlochwerkzeuge, Ventilsitze | Kobaltlegierung Stellit 6, Ni-Cr-B-Si | Verschleißfestigkeit, Haltbarkeit in rauen Umgebungen |
Elektronik | Halbleiterkomponenten, Wärmesenken | Niob, Wolfram | Wärmeleitfähigkeit, Hochtemperaturfähigkeit |
Jede Anwendung profitiert von den spezifischen Eigenschaften der verwendeten modernen Werkstoffe. In der Luft- und Raumfahrtindustrie beispielsweise sorgt die Hochtemperaturbeständigkeit der Nickellegierung 263 dafür, dass Turbinenschaufeln auch unter extremen Betriebsbedingungen ihre Integrität behalten.
Normen und Spezifikationen für LMD-Materialien
Bei der Auswahl von Materialien für Laser-MetallabscheidungUm Qualität, Leistung und Sicherheit zu gewährleisten, ist die Einhaltung von Industrienormen und Spezifikationen unerlässlich. Verschiedene Industriezweige haben spezifische Anforderungen, die Materialien erfüllen müssen, und diese Normen bestimmen den Auswahlprozess.
Industrienormen für LMD-Materialien:
Material | Norm/Spezifikation | Industrie | Zentrale Anforderungen |
---|---|---|---|
Inconel 625 | ASTM B443, AMS 5599 | Luft- und Raumfahrt, Öl und Gas | Hohe Temperatur, Korrosionsbeständigkeit, mechanische Eigenschaften |
Titanium Ti-6Al-4V | ASTM F136, AMS 4911 | Medizin, Luft- und Raumfahrt | Biokompatibilität, mechanische Festigkeit, Ermüdungsfestigkeit |
Rostfreier Stahl 316L | ASTM A240, ISO 5832-1 | Medizin, Lebensmittelverarbeitung | Korrosionsbeständigkeit, mechanische Eigenschaften |
Kobalt-Chrom (Co-Cr) | ASTM F75, ISO 5832-4 | Medizinische | Abriebfestigkeit, Biokompatibilität |
Tungsten (W) | ASTM B777, MIL-T-21014 | Verteidigung, Luft- und Raumfahrt | Hohe Dichte, hohe Temperaturbeständigkeit |
Aluminium AlSi10Mg | ASTM B209, EN 485 | Automobilindustrie, Luft- und Raumfahrt | Leichtes Gewicht, gute Wärmeleitfähigkeit |
Nickellegierung 263 | AMS 5872, ASTM B637 | Luft- und Raumfahrt | Oxidationsbeständigkeit, hohe Festigkeit bei erhöhter Temperatur |
Rene 41 | AMS 5545, ASTM B435 | Luft- und Raumfahrt | Mechanische Eigenschaften bei hohen Temperaturen |
Niobium (Nb) | ASTM B392, AMS 7850 | Elektronik, Luft- und Raumfahrt | Supraleitfähigkeit, thermische Stabilität |
Tantal (Ta) | ASTM B708, AMS 7831 | Medizinische, chemische Verarbeitung | Korrosionsbeständigkeit, Biokompatibilität |
Diese Normen gewährleisten, dass die in LMD verwendeten Werkstoffe von gleichbleibender Qualität sind und die erforderlichen Leistungskriterien für die vorgesehenen Anwendungen erfüllen. Die Norm ASTM F136 gewährleistet beispielsweise, dass das in medizinischen Implantaten verwendete Titan Ti-6Al-4V für den langfristigen Einsatz im menschlichen Körper sicher und wirksam ist.
Die Wahl des richtigen Metallpulvers für die Laser-Metallabscheidung
Die Auswahl des richtigen Metallpulvers ist ein entscheidender Schritt im LMD-Prozess. Die Wahl des Pulvers wirkt sich direkt auf die Qualität, die Leistung und die Kosten des Endprodukts aus. Faktoren wie Materialeigenschaften, Anwendungsanforderungen und Kostenüberlegungen spielen bei diesem Entscheidungsprozess eine Rolle.
Zu berücksichtigende Faktoren:
Faktor | Beschreibung | Auswirkungen auf die Auswahl |
---|---|---|
Anforderungen an die Bewerbung | Die spezifischen Anforderungen an das Endprodukt, einschließlich mechanischer Eigenschaften, Umweltbedingungen und Lebensdauer. | Bestimmt die Materialauswahl anhand von Leistungskriterien. |
Materialeigenschaften | Eigenschaften wie Schmelzpunkt, Wärmeleitfähigkeit und Festigkeit. | Bestimmt die Prozessparameter und die Qualität des Endprodukts. |
Morphologie des Pulvers | Die Form und Größenverteilung der Pulverpartikel. | Beeinflusst die Fließfähigkeit, die Packungsdichte und die Gleichmäßigkeit der Schicht. |
Kostenüberlegungen | Die Kosten des Metallpulvers im Verhältnis zum Budget des Projekts. | Gleichgewicht zwischen Materialleistung und wirtschaftlicher Machbarkeit. |
Verfügbarkeit der Lieferanten | Die Verfügbarkeit des Metallpulvers bei zuverlässigen Lieferanten. | Gewährleistet eine gleichbleibende Versorgung und Qualität der Produktion. |
Einhaltung von Normen | Einhaltung von Industrienormen und Spezifikationen. | Gewährleistet die Qualität und Sicherheit des Endprodukts. |
Eine fundierte Entscheidung über das Metallpulver erfordert ein Gleichgewicht zwischen den technischen Anforderungen und den Kosten. So bietet Wolfram zwar eine höhere Temperaturbeständigkeit, ist aber auch teurer als andere Optionen wie Edelstahl 316L, so dass es sich eher für High-End-Anwendungen eignet, bei denen die Leistung die Kosten rechtfertigt.
Lieferanten und Preisgestaltung für LMD-Metallpulver
Die Beschaffung des richtigen Metallpulvers von einem zuverlässigen Lieferanten ist entscheidend für eine erfolgreiche LMD. Die Lieferanten bieten eine breite Palette von Pulvern mit unterschiedlichen Preisen an, die von Faktoren wie Materialzusammensetzung, Reinheit und Partikelgrößenverteilung abhängen.
Führende Anbieter und Preisgestaltung:
Anbieter | Metall-Pulver | Preisspanne (pro kg) | Besondere Merkmale |
---|---|---|---|
Tischlertechnik | Nickellegierung 263, Haynes 282 | $300 – $500 | Hochwertige Pulver für die Luft- und Raumfahrt, gleichmäßige Partikelgröße. |
Hoganas AB | Rostfreier Stahl 316L, Inconel 625 | $50 – $200 | Breites Spektrum an Legierungen, hervorragende Fließfähigkeit. |
LPW-Technologie | Titan Ti-6Al-4V, Aluminium AlSi10Mg | $250 – $450 | Kundenspezifische Pulver, strenge Qualitätskontrolle für die additive Fertigung. |
Oerlikon Metco | Kobaltlegierung Stellit 6, Rene 41 | $400 – $600 | Hochleistungspulver, optimiert auf Verschleißfestigkeit. |
AP&C (GE-Zusatzstoff) | Ti-5553, Tantal | $500 – $800 | Pulver für die Luft- und Raumfahrt und für medizinische Zwecke, Biokompatibilität. |
Sandvik | Inconel 738, Wolfram | $200 – $700 | Hochtemperaturlegierungen, umfangreiche Tests und Zertifizierungen. |
Praxis Pulvertechnologie | Niob, Kobalt-Chrom (Co-Cr) | $300 – $600 | Spezialisierte Pulver für medizinische und elektronische Anwendungen. |
GKN-Zusatzstoff | Nickellegierung 263, Haynes 282 | $300 – $500 | Kundenspezifische Pulvermischungen, hervorragende Oxidationsbeständigkeit. |
Tekna | Aluminium AlSi10Mg, Edelstahl 316L | $50 – $150 | Sphärische Pulver, optimiert für die additive Fertigung. |
VIGA | Tantal, Wolfram | $500 – $900 | Hochreine Pulver, maßgeschneidert für spezifische Anwendungen. |
Die Preise variieren je nach Material und Anbieter stark und spiegeln die Unterschiede in der Reinheit, der Produktionsmethode und der Marktnachfrage wider. So liegen beispielsweise Tantal- und Wolframpulver aufgrund ihrer komplexen Verarbeitung und hohen Nachfrage in spezialisierten Branchen am oberen Ende des Preisspektrums.
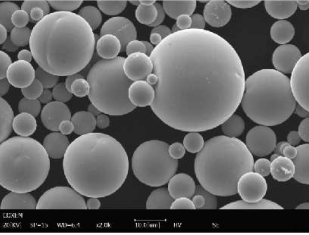
Vergleich von Laser-Metallabscheidung zu anderen additiven Fertigungstechniken
Laser Metal Deposition (LMD) ist nur eines der vielen heute verfügbaren additiven Fertigungsverfahren. Wenn Sie wissen, wie LMD im Vergleich zu anderen Verfahren abschneidet, können Sie das beste Verfahren für Ihre spezifischen Anforderungen auswählen.
Vergleich mit anderen additiven Fertigungstechniken:
Technik | Flexibles Material | Oberflächengüte | Geschwindigkeit | Präzision | Kosten | Anwendungen |
---|---|---|---|---|---|---|
Laser-Metallabscheidung | Hoch | Mäßig | Mittel | Hoch | Hoch | Luft- und Raumfahrt, Reparatur, komplexe Geometrien |
Selektives Laser-Sintern (SLS) | Hoch | Mäßig | Mittel | Hoch | Mäßig | Prototyping, Kleinserienfertigung |
Elektronenstrahlschmelzen (EBM) | Mittel | Mäßig | Mittel | Hoch | Hoch | Luft- und Raumfahrt, medizinische Implantate |
Fused Deposition Modeling (FDM) | Niedrig | Niedrig | Hoch | Niedrig | Niedrig | Prototyping, Konsumgüter |
Direktes Metall-Laser-Sintern (DMLS) | Hoch | Hoch | Mittel | Sehr hoch | Hoch | Medizin, Luft- und Raumfahrt, komplizierte Teile |
Binder Jetting | Mittel | Niedrig | Hoch | Mittel | Mäßig | Große Teile, Gussformen |
Gerichtete Energieabscheidung (DED) | Hoch | Mäßig | Mittel | Hoch | Hoch | Reparatur, Großkomponenten, Luft- und Raumfahrt |
Das LMD-Verfahren zeichnet sich durch seine Fähigkeit aus, mit einer Vielzahl von Materialien zu arbeiten, und durch seine Präzision bei der Herstellung komplexer Geometrien. Allerdings ist es im Vergleich zu anderen Verfahren wie FDM, das sich eher für das Rapid Prototyping mit weniger anspruchsvollen Materialanforderungen eignet, tendenziell teurer und langsamer.