Einführung
Sinterkarbid besteht in der Regel aus einem Hartmetallskelett und einem Metallbindemittel. Es handelt sich um ein Material mit hervorragender Härte und ausgezeichneter Verschleißfestigkeit, das für die Herstellung von Schneidwerkzeugen, Bohrern, Verschleißteilen usw. geeignet ist. Im Allgemeinen wird Sinterkarbid durch herkömmliche Pulvermetallurgie (PM), heißisostatisches Pressen (HIP), selbstausbreitende Hochtemperatursynthese (SHS) und Funkenplasmasintern (SPS) hergestellt. Die meisten dieser Verfahren können jedoch nur Bauteile mit begrenzter geometrischer Komplexität herstellen. Darüber hinaus sind diese Verfahren aufgrund der langen technischen Prozesse nicht effizient und kostspielig.
UnserWC-12Co Sinterkarbid-Pulverdie durch Kugelmahlen, Sprühgranulation, Vorsintern, Sieben und Klassieren hergestellt wurden, können durch Laser Powder Bed Melting (LPBF) aufgebracht werden. Die Hartmetallteile durch LPBF durch unsere gemischteWC-12Co-Pulver mit fast kugelförmigen Partikeln mit einer Größe von 15-53 μm, und das Bindemittel Co ist gleichmäßig in der WC-Matrix dispergiert, zeigten hervorragende mechanische Eigenschaften und Verschleißverhalten durch die Einstellung geeigneter Scan-Geschwindigkeit.
Abbildung 1 zeigt die optische Mikrostruktur von LPBF-Teilen aus WC-12Co-Hartmetall, die aus WC-12Co-Pulvern bei einer Scangeschwindigkeit von 400 mm/s hergestellt wurden. Die roten und blauen Bereiche in Abbildung 1a stellen WC- bzw. Co-Klebstoffe (Lösungen auf Co-Basis) dar. Die WC-Körner weisen ein bimodales Gefüge auf, und die maximale, minimale und durchschnittliche Korngröße beträgt etwa 25, 1,5 bzw. 8,7 μm.

Abbildung 2zeigt die Rockwell-Härte (HRA) und die Querbruchfestigkeit (TRS) von WC-12Co-Sinterkarbid, das mit LPBF aus WC-12Co-Pulvern hergestellt wurde. Mit zunehmender Laserscangeschwindigkeit nimmt die HRA allmählich ab. Eine Erhöhung der Laserenergiedichte führt zu einer Zunahme der harten und spröden ƞ-Phase.
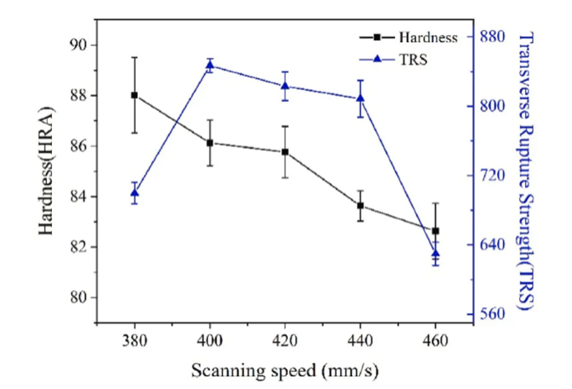
Um den Verschleißmechanismus des mit LPBF hergestellten WC-12Co-Hartmetalls zu analysieren, wird die Verschleißoberfläche in Abbildung 3. Bei WC-12Co-Hartmetall, das mit 380 mm/s geformt wurde, sind deutlich Verschleißspuren zu erkennen, und die WC-Matrix ist stark beschädigt. Bei Proben, die mit einer Geschwindigkeit von 400 mm/s hergestellt wurden, sind Rillen und Kratzer zu beobachten, die typische Merkmale des abrasiven Verschleißes sind:
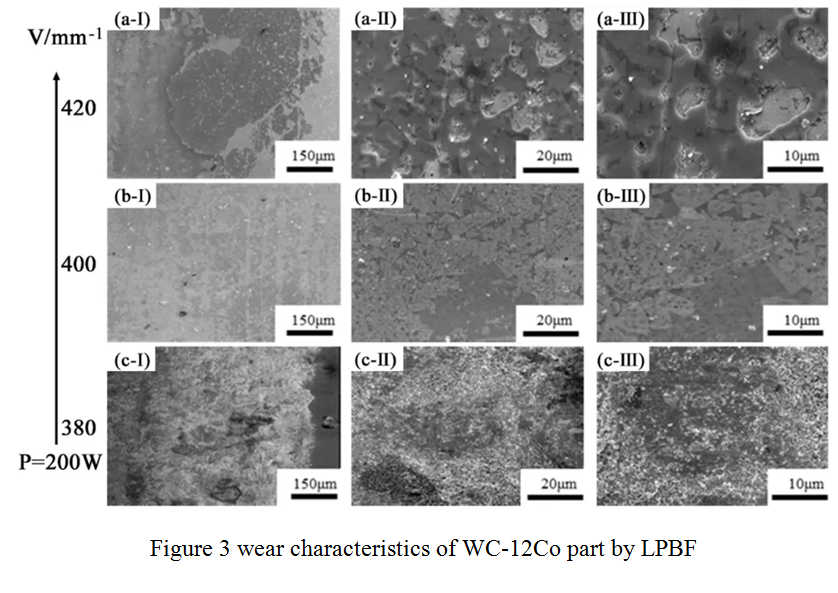
Schlussfolgerung
Das Mikrogefüge, die mechanischen Eigenschaften und die Verschleißeigenschaften von WC-12Co-Hartmetall, das durch LPBF aus WC-12Co-Pulvern hergestellt wurde, wurden untersucht.
Die wichtigsten Schlussfolgerungen lassen sich wie folgt zusammenfassen: (1) Die abwechselnde Verteilung von groben und feinen WC-Körnern wurde in dem durch LPBF hergestellten WC-12Co-Sinterkarbid beobachtet. (2) Mit der Erhöhung der Laserscangeschwindigkeit steigt TRS zunächst auf den Maximalwert und nimmt dann ab. Die Variation von TRS ist hauptsächlich auf die Entwicklung der spröden ƞ-Phase und metallurgische Defekte zurückzuführen. (3) Bei WC-12Co-Hartmetall, das bei niedrigen Abtastgeschwindigkeiten geformt wird, kann die spröde η-Phase während der Reibung brechen und die Matrix zerschneiden, was zu einem Verlust an Verschleißmasse führt. Bei Proben, die mit hohen Scangeschwindigkeiten hergestellt werden, beschleunigt die Bildung und Ablösung von Scherschichten den Reibungsprozess und zerstört die Verschleißfestigkeit von WC-12Co Hartmetall. Daher weisen Proben, die mit einer Abtastgeschwindigkeit von 400 mm/s hergestellt wurden, die beste Verschleißfestigkeit auf.