Pulver auf Nickelbasis, winzige Metallteilchen mit einer Vielzahl von Verwendungsmöglichkeiten, spielen in verschiedenen Branchen eine entscheidende Rolle. Aber wie genau werden diese vielseitigen Materialien hergestellt? Schnallen Sie sich an, denn wir begeben uns auf eine Reise in das faszinierende Reich der Produktionsmethoden für nickelbasierte Pulver und erfahren mehr über ihre Anwendungen, Eigenschaften und vieles mehr.
Die wichtigsten Produktionsmethoden von Pulver auf Nickelbasis
Nickelpulver kann mit verschiedenen Methoden hergestellt werden, die jeweils ihre eigenen Vorteile und Einschränkungen haben. Im Folgenden werden einige der gängigsten Verfahren vorgestellt:
Carbonyl-Verfahren: Bei dieser Methode wird Nickel mit Kohlenmonoxid zu Nickelcarbonylgas umgesetzt, das sich dann bei kontrollierten Temperaturen zersetzt, um kugelförmiges, hochreines Nickelpulver zu bilden. Stellen Sie sich vor, dass Nickelatome auf Kohlenmonoxidmoleküle aufgesprungen sind, um dann bei einer bestimmten Temperatur sanft abgestoßen zu werden, so dass eine Wolke winziger, gleichmäßiger Nickelkugeln entsteht. Dieses Verfahren ist bekannt für seine hervorragende Kontrolle über die Partikelgröße und -form und eignet sich daher ideal für Anwendungen, die hohe Präzision erfordern.
Wasserzerstäubung: Bei diesem Verfahren wird geschmolzenes Nickel durch einen Hochdruck-Wasserstrahl gepresst, wodurch es in feine Tröpfchen zerfällt, die sich zu unregelmäßig geformten Partikeln verfestigen. Stellen Sie sich vor, Sie gießen geschmolzenes Nickel durch einen kräftigen Duschkopf, und der entstehende Strahl verfestigt sich zu einer Ansammlung von Nickelpulverkörnern. Diese Methode ist kostengünstig und eignet sich für die Produktion in großem Maßstab, aber die Partikelgröße und -form lassen sich im Vergleich zum Carbonylverfahren weniger gut kontrollieren.
Elektrolytische Abscheidung: Bei diesem Verfahren werden Nickelionen mit Hilfe von elektrischem Strom aus einer Lösung herausgelöst und auf einer Kathode abgeschieden, so dass Nickelplättchen entstehen. Stellen Sie sich eine nickelhaltige Lösung vor, in der die Nickelionen unter dem Einfluss von Elektrizität zu einer negativ geladenen Oberfläche gezogen werden und sich allmählich Schicht für Schicht zu dünnen, plättchenförmigen Nickelpartikeln aufbauen. Diese Methode bietet eine gute Kontrolle über die Reinheit der Partikel, führt aber zu nicht kugelförmigen Formen, was sich auf die Fließfähigkeit und die Packungsdichte auswirken kann.
Reduktion von Nickelsalzen: Bei dieser Methode werden Nickelverbindungen wie Nickeloxid oder Nickelsulfat mit einem Reduktionsmittel wie Wasserstoff reduziert, um Nickelpulver zu bilden. Stellen Sie sich vor, Sie nehmen Nickel, das in einer Verbindung eingeschlossen ist, und verwenden Wasserstoff als Schlüssel, um es aufzuschließen und in winzige Nickelpartikel zu verwandeln. Diese Methode ist weniger verbreitet, kann aber zur Herstellung spezieller Nickellegierungen oder Pulver mit maßgeschneiderten Eigenschaften verwendet werden.
Gaszerstäubung: Diese Methode ähnelt der Wasserzerstäubung, aber statt Wasser wird ein inertes Gas wie Stickstoff verwendet, um das geschmolzene Metall aufzubrechen. Das Ergebnis sind sauberere und kugelförmigere Partikel als bei der Wasserzerstäubung, allerdings zu einem höheren Preis. Stellen Sie sich vor, Sie ersetzen den Wasserduschkopf durch einen Stickstoffduschkopf und erhalten so einen saubereren und gleichmäßigeren Sprühnebel aus Nickeltröpfchen, die zu Pulver erstarren.
Dies sind nur einige der wichtigsten Methoden zur Herstellung von Nickelpulvern. Die Wahl des Verfahrens hängt von Faktoren wie den gewünschten Pulvereigenschaften, den Kosten und dem Produktionsumfang ab.
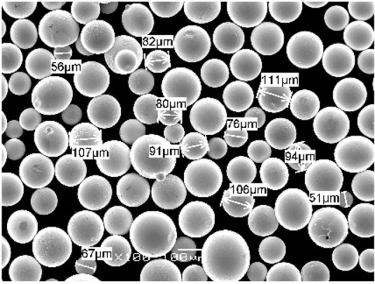
Vielfältige Landschaft von Nickel-Pulver
Nickelpulver gibt es in einer Vielzahl von Formen, Größen und Zusammensetzungen, die jeweils auf bestimmte Anwendungen zugeschnitten sind. Hier sind einige bemerkenswerte Beispiele:
INCO 123: Dieses aus Carbonyl hergestellte Nickelpulver ist für seine hohe Reinheit, seine kugelförmige Gestalt und seine hervorragende Fließfähigkeit bekannt. Es wird häufig in Hartlötlegierungen, Batterieelektroden und elektronischen Komponenten verwendet.
INCO 255: INCO 255 ist ein weiteres Carbonylpulver, das im Vergleich zu INCO 123 eine gröbere Partikelgröße aufweist. Dadurch eignet es sich für Anwendungen, die eine gute Packungsdichte erfordern, wie z. B. in Elektroden und Katalysatoren.
AZL 64: Dieses wasserverdüste Pulver hat eine unregelmäßige Form und eine breitere Partikelgrößenverteilung. Es wird häufig für Anwendungen verwendet, bei denen die Kosteneffizienz im Vordergrund steht, z. B. bei pulvermetallurgischen Komponenten und beim thermischen Spritzen.
NiFe: Dieses Pulver ist eine Legierung aus Nickel und Eisen, die in der Regel durch Reduktion von Mischmetalloxiden hergestellt wird. Es wird in verschiedenen magnetischen Anwendungen wie weichmagnetischen Kernen und zur Abschirmung elektromagnetischer Störungen verwendet.
NiCu: Dieses Pulver aus einer Nickel-Kupfer-Legierung bietet im Vergleich zu reinem Nickel eine bessere Korrosionsbeständigkeit. Es wird in Lötlegierungen, elektronischen Komponenten und verschleißfesten Beschichtungen verwendet.
Sphärische Nickel-Pulver: Diese Pulver, die häufig durch Karbonyl- oder Gaszerstäubung hergestellt werden, weisen eine nahezu perfekte Kugelform auf. Das macht sie ideal für additive Fertigungsverfahren wie den 3D-Druck, bei denen ein gleichmäßiger Fluss und eine gleichmäßige Packung entscheidend sind.
Elektrolytische Nickel-Pulver: Diese Pulver, die sich durch ihre flockige Form auszeichnen, werden in Batterieelektroden und Katalysatoren verwendet. Die große Oberfläche der Flocken verbessert ihre Wechselwirkung mit anderen Materialien, was zu einer besseren Leistung führt.
Superlegierungspulver auf Nickelbasis: Diese komplexen Legierungen, die oft zusätzliche Elemente wie Chrom, Kobalt und Aluminium enthalten, werden durch verschiedene Verfahren wie Gas- oder Plasmazerstäubung hergestellt. Sie bieten eine außergewöhnliche Hochtemperaturfestigkeit und werden in anspruchsvollen
Tiefer eintauchen: Anwendungen, Eigenschaften und mehr
Die Anwendungen von Nickelpulvern sind so vielfältig wie ihre Produktionsmethoden und Eigenschaften. Hier erhalten Sie einen Einblick in die bemerkenswerte Vielseitigkeit dieser winzigen Materialien:
Anwendungen:
- Batterieelektroden: Nickelpulver spielen eine wichtige Rolle bei der Herstellung von Lithium-Ionen-Batterien, einer Technologie, die unsere tragbare Elektronik und Elektrofahrzeuge antreibt. Dank ihrer hohen elektrischen Leitfähigkeit und spezifischen Oberfläche eignen sie sich ideal für die effiziente Speicherung und Abgabe von Energie.
- Additive Fertigung (3D-Druck): Sphärische Nickelpulver werden zunehmend im 3D-Druck eingesetzt, um komplexe, endkonturnahe Komponenten für verschiedene Branchen wie die Luft- und Raumfahrt, die Automobilindustrie und die Medizintechnik herzustellen. Ihre hervorragende Fließfähigkeit und Packungsdichte ermöglichen einen präzisen schichtweisen Auftrag und damit die Herstellung komplizierter Objekte mit den gewünschten Eigenschaften.
- Galvanische Beschichtung: Nickelpulver wird zur Herstellung von Galvanikbädern verwendet, einer Technik zur Beschichtung anderer Materialien mit einer dünnen Nickelschicht. Diese Beschichtung verbessert die Korrosionsbeständigkeit, die Leitfähigkeit und die Verschleißfestigkeit und findet in verschiedenen Bereichen wie der Automobilindustrie, der Elektronik und dem Schmuckbereich Anwendung.
- Lötlegierungen: Nickelpulver wird in Hartlötlegierungen eingesetzt, um Metallteile mit einem Zusatzwerkstoff zu verbinden, der bei einer niedrigeren Temperatur schmilzt als die Grundmetalle. Diese Legierungen bieten eine hervorragende Festigkeit, Duktilität und Korrosionsbeständigkeit, was sie für verschiedene Anwendungen in der Luft- und Raumfahrt, der Automobilindustrie und dem Baugewerbe unverzichtbar macht.
- Katalysatoren: Nickelpulver werden aufgrund ihrer großen Oberfläche und ihrer katalytischen Eigenschaften in verschiedenen chemischen Reaktionen eingesetzt. Sie können die Reaktionsgeschwindigkeit beschleunigen und die Effizienz von Prozessen wie Hydrierung, Hydrocracking und Reformierung verbessern und spielen daher eine wichtige Rolle in der Chemie- und Erdölindustrie.
- Thermisches Spritzen: Nickelpulver werden bei thermischen Spritzverfahren wie Plasmaspritzen und Hochgeschwindigkeitsflammspritzen (HVOF) eingesetzt, um Schutzschichten auf verschiedenen Oberflächen zu erzeugen. Diese Beschichtungen erhöhen die Verschleißfestigkeit, die Korrosionsbeständigkeit und die thermischen Eigenschaften, verlängern die Lebensdauer und verbessern die Leistung von Bauteilen in verschiedenen Industriezweigen wie Energieerzeugung, Öl und Gas sowie Luft- und Raumfahrt.
Eigenschaften:
Die Eigenschaften von Nickelpulvern haben einen erheblichen Einfluss auf ihre Eignung für verschiedene Anwendungen. Hier sind einige wichtige Merkmale zu beachten:
- Partikelgröße und -verteilung: Die Größe und Verteilung der Nickelpulverpartikel wirkt sich auf Faktoren wie Fließfähigkeit, Packungsdichte und Oberfläche aus. Feinere Pulver bieten eine größere Oberfläche, können aber eine schlechtere Fließfähigkeit aufweisen, während gröbere Pulver besser fließen, aber eine geringere Oberfläche haben.
- Die Form: Die Form der Nickelpulverpartikel, die von kugelförmig bis unregelmäßig reichen kann, beeinflusst die Packungsdichte, Fließfähigkeit und Leistung in bestimmten Anwendungen. Kugelförmige Partikel bieten eine bessere Packungsdichte und Fließfähigkeit, während unregelmäßige Formen bei bestimmten Anwendungen eine bessere mechanische Verzahnung ermöglichen können.
- Reinheit: Der Reinheitsgrad von Nickelpulver bezieht sich auf den Prozentsatz des vorhandenen Nickels und den Grad der Verunreinigungen. Hochreine Pulver werden häufig in Anwendungen eingesetzt, die hohe Leistung und minimale Verunreinigungen erfordern, z. B. in der Elektronik und in Batterieelektroden.
- Fläche: Die Oberfläche von Nickelpulverpartikeln spielt eine entscheidende Rolle bei Anwendungen wie Katalyse und Elektrochemie. Eine größere Oberfläche bietet mehr Plätze für Reaktionen, was ihre Wirksamkeit erhöht.

Die Wahl des richtigen Nickel-Pulver Produktionsverfahren
Bei der Auswahl der am besten geeigneten Methode zur Herstellung von Nickelpulver kommt es darauf an, die spezifischen Anforderungen Ihrer Anwendung zu verstehen und die Vorteile und Grenzen der einzelnen Verfahren sorgfältig abzuwägen. Hier finden Sie einen umfassenden Leitfaden, der Sie bei dieser wichtigen Entscheidung unterstützt:
Identifizierung der wichtigsten Anwendungsanforderungen:
Der erste Schritt besteht darin, die kritischen Anforderungen Ihrer geplanten Anwendung zu ermitteln. Berücksichtigen Sie die folgenden Faktoren:
- Gewünschte Partikelgröße und -verteilung: Feinere Pulver bieten eine größere Oberfläche, können aber Probleme mit der Fließfähigkeit bereiten, während gröbere Pulver eine bessere Fließfähigkeit, aber eine geringere Oberfläche aufweisen.
- Die Form: Kugelförmige Formen bieten im Allgemeinen eine bessere Packungsdichte und Fließfähigkeit, während unregelmäßige Formen für Anwendungen bevorzugt werden können, bei denen die mechanische Verriegelung entscheidend ist.
- Reinheit: Hochreine Pulver sind unverzichtbar für Anwendungen, die eine minimale Verunreinigung erfordern, wie z. B. in der Elektronik und bei Batterieelektroden.
- Kosten: Produktionsmethoden wie das Carbonylverfahren bieten eine hohe Reinheit und Kontrolle, sind aber mit höheren Kosten verbunden, während die Wasserzerstäubung kostengünstiger ist, aber weniger präzise Partikeleigenschaften liefert.
- Produktion Volumen: Wenn eine Produktion in großem Maßstab erforderlich ist, könnte die Wasserzerstäubung aufgrund ihrer Kosteneffizienz und Skalierbarkeit die erste Wahl sein.
Vertiefung der Vor- und Nachteile jeder Methode:
Nun, lassen Sie uns tiefer in die Vor- und Nachteile der einzelnen prominenten Nickel-Pulver-Produktionsverfahren zu vertiefen:
- Carbonyl-Verfahren:
Vorteile: * Außergewöhnlich hohe Reinheit * Enge Kontrolle über Partikelgröße und -form (sphärisch) * Ausgezeichnete Fließfähigkeit und Packungsdichte
Nachteile: * Höchste Kosten unter den gängigen Methoden * Komplexer und energieintensiver Prozess
- Wasserzerstäubung:
Vorteile: * Kostengünstigste Methode * Geeignet für Großserienproduktion
Nachteile: * Weniger Kontrolle über Partikelgröße und -form (unregelmäßig) * Kann aufgrund des verwendeten Wassers Verunreinigungen enthalten
- Elektrolytische Abscheidung:
Vorteile: * Gute Kontrolle der Reinheit * Umweltfreundliches Verfahren
Nachteile: * Nicht sphärische Partikelform, die die Fließfähigkeit beeinträchtigt * Begrenztes Produktionsvolumen im Vergleich zu anderen Methoden
- Reduktion von Nickelsalzen:
Vorteile: * Ermöglicht die Herstellung spezifischer Nickellegierungen oder Pulver mit maßgeschneiderten Eigenschaften
Nachteile: * Weniger verbreitete Methode mit begrenzter Verfügbarkeit * Kann zusätzliche Verarbeitungsschritte erfordern
- Gaszerstäubung:
Vorteile: * Sauberere und kugelförmigere Partikel im Vergleich zur Wasserzerstäubung * Bietet eine gute Kontrolle über Partikelgröße und -form
Nachteile: * Höhere Kosten als bei der Wasserzerstäubung, aber niedriger als beim Carbonylverfahren
3. Das perfekte Gleichgewicht finden:
Wägen Sie die Vor- und Nachteile der einzelnen Methoden sorgfältig gegen Ihre spezifischen Anwendungsanforderungen ab. Berücksichtigen Sie Faktoren wie:
- Haushaltszwänge: Wenn die Kosten im Vordergrund stehen, könnte die Wasserzerstäubung die praktikabelste Option sein, während für hochreine Anwendungen in der Elektronik das Carbonylverfahren trotz seiner höheren Kosten erforderlich sein könnte.
- Produktion Volumen: Für die Produktion in großem Maßstab ist die Wasserzerstäubung aufgrund ihrer Skalierbarkeit und Kosteneffizienz oft die bevorzugte Wahl.
- Gewünschte Eigenschaften: Wenn es darauf ankommt, eine bestimmte Partikelgröße, -form oder -reinheit zu erreichen, kann die Auswahl auf Verfahren eingeschränkt werden, die das erforderliche Maß an Kontrolle bieten.
Denken Sie daran, dass es keine einzelne beste Methode gibt; die optimale Wahl hängt von Ihren individuellen Anwendungsanforderungen und Prioritäten ab. Wenn Sie die Merkmale, Vorteile und Grenzen der einzelnen Produktionsmethoden kennen, können Sie eine fundierte Entscheidung treffen, die sicherstellt, dass das resultierende Nickelpulver die gewünschten Eigenschaften für Ihre spezifische Anwendung besitzt.