소개
레이저 기반 파우더 베드 융합 (PBF)는 복잡한 금속 부품을 만드는 방식에 혁신을 가져온 첨단 적층 제조(AM) 공정입니다. 항공우주, 자동차, 의료 산업에 종사하는 사람이라면 이 기술을 사용하여 만든 제품을 접했을 가능성이 높습니다. 이 가이드에서는 사용되는 금속 분말의 종류, 공정의 기술적 세부 사항 및 응용 분야에 대해 자세히 살펴보면서 레이저 기반 PBF의 복잡성에 대해 살펴봅니다. 또한 다른 제조 방법과 비교하고 장단점을 논의하며 이 혁신적인 기술을 구현하거나 배우고자 하는 모든 사람에게 유용한 통찰력을 제공합니다.
레이저 기반 파우더 베드 융합 개요
레이저 기반 분말 베드 융합(PBF)은 고출력 레이저를 사용하여 금속 분말을 층별로 고체 구조로 융합하는 적층 제조의 한 형태입니다. 이 기술은 기존 제조 방법으로는 달성하기 어렵거나 불가능한 매우 복잡한 형상을 제작하는 것으로 유명합니다. 특히 항공우주, 자동차, 의료 기기 제조와 같이 높은 정밀도가 요구되는 산업에서 PBF의 가치가 높습니다.
- 기술: 레이저 기반 적층 제조
- 프로세스: 파우더 베드 융합
- 사용된 재료: 금속 분말
- 주요 산업: 항공우주, 자동차, 의료, 툴링
- 장점: 고정밀, 복잡한 형상, 재료 효율성
- 제한 사항: 높은 비용, 느린 생산 속도
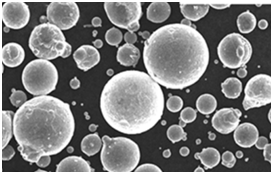
레이저 기반 분말 베드 용융에 사용되는 금속 분말의 종류
PBF 프로젝트의 성공을 위해서는 올바른 금속 분말을 선택하는 것이 중요합니다. 각 유형의 파우더는 최종 제품의 강도, 내구성 및 성능에 큰 영향을 미칠 수 있는 고유한 특성을 제공합니다.
금속 분말 | 구성 | 속성 | 애플리케이션 |
---|---|---|---|
티타늄(Ti-6Al-4V) | 90% 티타늄, 6% 알루미늄, 4% 바나듐 | 높은 중량 대비 강도, 내식성 | 항공우주, 의료용 임플란트 |
스테인리스 스틸(316L) | 철, 크롬, 니켈, 몰리브덴 | 부식 방지, 우수한 용접성 | 의료, 식품 가공 |
인코넬 718 | 니켈-크롬 합금 | 고온 저항성, 우수한 내크리프성 | 항공우주, 가스터빈 |
알루미늄(AlSi10Mg) | 알루미늄, 실리콘, 마그네슘 | 가볍고 우수한 열 전도성 | 자동차, 항공우주 |
코발트-크롬(CoCr) | 코발트, 크롬 | 높은 내마모성 및 내식성 | 치과, 정형외과 임플란트 |
마레이징 스틸 (1.2709) | 니켈, 몰리브덴, 코발트 | 높은 강도, 인성 | 툴링, 항공우주 |
구리(CuCrZr) | 구리, 크롬, 지르코늄 | 뛰어난 전기 및 열 전도성 | 전자 제품, 열교환기 |
하스텔로이 X | 니켈, 몰리브덴, 크롬, 철 | 높은 내산화성, 우수한 용접성 | 화학 처리, 항공 우주 |
공구강(H13) | 크롬, 몰리브덴, 바나듐 | 높은 인성, 내마모성 | 사출 금형, 다이캐스팅 |
니켈 합금(하스텔로이 C-276) | 니켈, 몰리브덴, 크롬 | 탁월한 내식성 | 화학 처리, 원자로 |
프로세스 레이저 기반 파우더 베드 융합
레이저 기반 PBF의 프로세스를 이해하는 것은 그 기능과 한계를 파악하는 데 필수적입니다. 다음 섹션에서는 분말 준비부터 후처리까지 공정의 각 단계를 세분화하여 설명합니다.
분말 준비
PBF 공정의 첫 번째 단계는 금속 분말을 준비하는 것입니다. 파우더는 입자 크기, 분포 및 순도에 관한 엄격한 사양을 충족해야 합니다. 이를 통해 파우더가 빌드 플랫폼 전체에 고르게 퍼지고 레이저가 파우더를 효과적으로 융착할 수 있도록 합니다.
- 입자 크기: 일반적으로 15-45미크론 범위
- 순도: 최종 부품의 결함을 방지하기 위해 오염 물질이 없어야 합니다.
- 수분 함량: 뭉치지 않도록 최소화해야 합니다.
레이어별 제작
파우더가 준비되면 빌드 플랫폼 전체에 고르게 퍼집니다. 그런 다음 레이저가 CAD 파일에서 제공한 설계 사양에 따라 파우더를 선택적으로 융합합니다.
- 레이저 유형: 일반적으로 파장이 1.064마이크론인 파이버 레이저를 사용합니다.
- 레이저 파워: 재료 및 부품 요구 사항에 따라 200W에서 1000W까지 다양합니다.
- 스캔 속도: 최대 7m/s
- 레이어 두께: 일반적으로 20-60미크론
후처리
부품이 완전히 제작되면 원하는 특성을 얻기 위해 몇 가지 후처리 단계를 거칩니다. 여기에는 열처리, 표면 마감, 잔여 분말 제거 등이 포함될 수 있습니다.
- 열처리: 응력 완화 및 기계적 특성 개선에 사용
- 표면 마감: 원하는 표면 마감을 얻기 위해 CNC 가공, 연마 또는 코팅과 같은 방법을 사용합니다.
- 파우더 제거: 융합되지 않은 파우더는 제거되어 향후 빌드에 재활용할 수 있습니다.
품질 관리
품질 관리는 PBF 프로세스의 필수적인 부분으로, 최종 부품이 필요한 사양을 충족하도록 보장합니다.
- 치수 정확도: 일반적으로 ±0.1mm 이내
- 표면 거칠기: 일반적으로 재료 및 레이어 두께에 따라 Ra 6~12µm 범위입니다.
- 기계적 테스트: 인장, 피로 및 경도 테스트는 종종 부품 무결성을 확인하기 위해 수행됩니다.
레이저 기반 파우더 베드 융합의 특성
PBF의 특성으로 인해 특정 애플리케이션에는 이상적인 선택이지만 다른 애플리케이션에서는 사용이 제한되기도 합니다. 아래에서 이러한 특성에 대해 자세히 살펴보겠습니다.
특징 | 설명 |
---|---|
정밀도 | 높은 치수 정확도와 세밀한 디테일의 부품을 생산할 수 있습니다. 복잡한 형상과 엄격한 공차에 이상적입니다. |
재료 효율성 | 파우더는 재활용이 가능하므로 폐기물을 최소화할 수 있습니다. 그러나 효율성은 융합되지 않은 파우더를 제거하고 재사용할 수 있는 능력에 달려 있습니다. |
표면 마감 | 일반적으로 전통적으로 제조된 부품보다 거칠습니다. 표면 마감 요구 사항을 충족하기 위해 후처리가 필요한 경우가 많습니다. |
속도 | 다른 제조 방식에 비해 상대적으로 느리기 때문에 대량 생산에는 적합하지 않습니다. |
비용 | 장비 및 재료에 대한 초기 비용이 높지만 소량 배치 또는 맞춤형 부품의 경우 비용 효율적일 수 있습니다. |
복잡성 | 기존 방식으로는 어렵거나 불가능한 복잡한 디자인을 제작하는 데 탁월합니다. |
머티리얼 속성 | 최종 부품의 속성은 재료 선택 및 후처리 기술을 통해 맞춤 설정할 수 있습니다. |
지원 구조 | 빌드 중 뒤틀림을 방지하고 파트의 안정성을 보장하기 위해 필요한 경우가 많습니다. 제작 후에는 신중하게 설계하고 제거해야 합니다. |
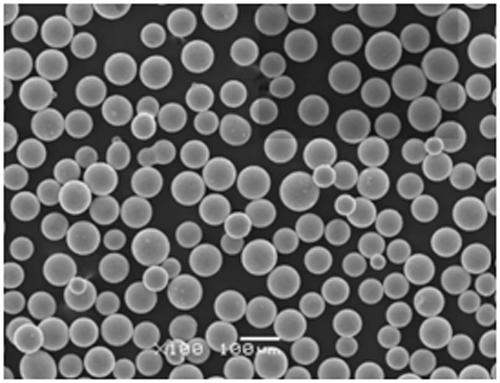
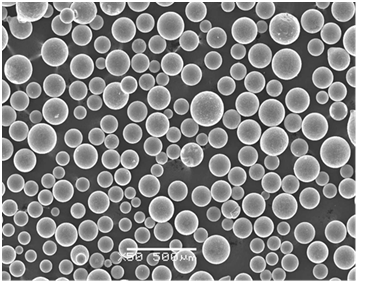
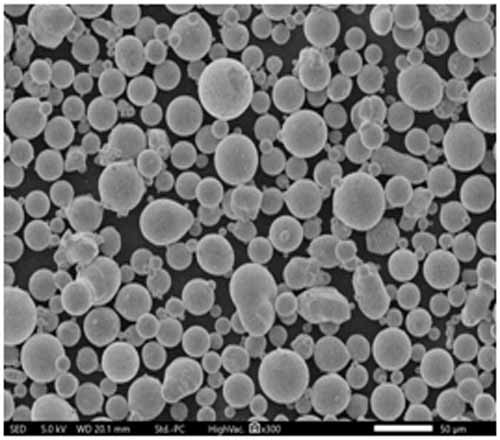
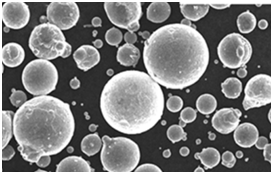
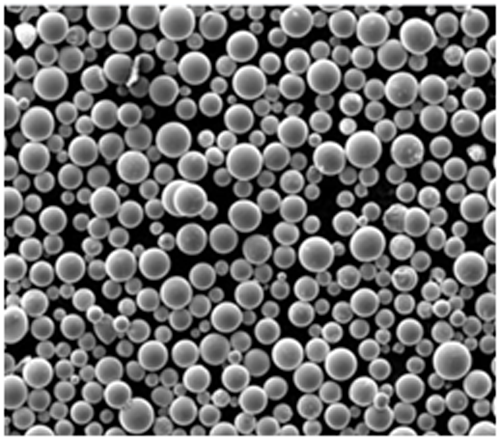
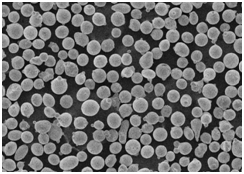
애플리케이션 레이저 기반 파우더 베드 융합
PBF의 다용도성 덕분에 다양한 산업 분야의 광범위한 애플리케이션에 적합합니다. 다음 표는 가장 일반적인 사용 사례 몇 가지를 보여줍니다.
산업 | 애플리케이션 | 구성 요소 예시 |
---|---|---|
항공우주 | 가볍고 복잡한 부품 | 터빈 블레이드, 브래킷, 연료 노즐 |
자동차 | 고성능 구성 요소 | 엔진 부품, 변속기 부품 |
의료 | 맞춤형 임플란트 및 보철물 | 고관절 임플란트, 치과 크라운, 수술 기구 |
툴링 | 고강도 공구 및 금형 | 사출 금형, 절삭 공구, 금형 |
전자 제품 | 열 관리 구성 요소 | 열교환기, 커넥터, 하우징 |
에너지 | 고온 부품 | 가스터빈 부품, 연료 전지, 열교환기 |
방어 | 전문 구성 요소 | 무기 시스템, 갑옷, 통신 장치 |
아키텍처 | 복잡하고 심미적인 디자인 | 맞춤형 비품, 예술적 설치물 |
보석 | 복잡한 맞춤형 디자인 | 반지, 목걸이, 팔찌 |
레이저 기반 파우더 베드 융합의 장점과 한계
다른 제조 방법과 마찬가지로 PBF에도 장단점이 있습니다. 이를 이해하면 이 기술이 프로젝트에 적합한지 결정하는 데 도움이 될 수 있습니다.
장점 | 제한 사항 |
---|---|
높은 정밀도 | 높은 비용 |
뛰어난 치수 정확도로 복잡하고 복잡한 부품을 생산할 수 있습니다. | 장비와 재료에 대한 초기 투자 비용이 상당하기 때문에 대량 생산에는 비용 효율성이 떨어집니다. |
재료 효율성 | 느린 생산 속도 |
사용하지 않은 파우더를 재활용할 수 있어 폐기물 및 자재 비용이 절감됩니다. | 레이어별 프로세스는 특히 큰 부품의 경우 시간이 많이 걸립니다. |
사용자 지정 기능 | 표면 거칠기 |
의료용 임플란트와 같이 세상에 단 하나뿐인 맞춤형 부품을 제작하는 데 이상적입니다. | 부품은 원하는 표면 마감을 얻기 위해 후처리가 필요한 경우가 많습니다. |
복잡한 지오메트리 | 지원 구조 요구 사항 |
기존 방식으로는 불가능한 디자인을 만들 수 있습니다. | 지지 구조가 필요한 경우가 많기 때문에 설계가 복잡해지고 후처리 시간이 늘어날 수 있습니다. |
다양한 소재 선택 | 재료 제한 |
다양한 금속 및 합금과 호환됩니다. | 모든 소재가 PBF를 사용하여 효과적으로 가공할 수 있는 것은 아니므로 특정 용도에 맞는 소재 선택이 제한될 수 있습니다. |
레이저 기반 파우더 베드 용융과 다른 제조 방법의 비교
레이저 기반 PBF는 다른 제조 기술과 어떻게 비교될까요? 기존의 기계 가공, 주조 및 기타 적층 제조 방법과 비교하여 분석해 보겠습니다.
방법 | PBF와 비교한 장점 | PBF와 비교한 단점 |
---|---|---|
가공 | 대량 생산에 더 빠르고 후처리 없이 표면 마감 개선 | 더 단순한 형상, 더 많은 재료 낭비, 더 낮은 재료 효율로 제한됨 |
캐스팅 | 크고 복잡한 부품에 적합, 재료 비용 절감 | 금형이 필요하고, 결함이 발생할 수 있으며, PBF에 비해 정밀도가 떨어질 수 있습니다. |
사출 성형 | 대량 생산을 위한 매우 빠른 속도, 부품당 매우 낮은 비용 | 더 단순한 디자인, 높은 초기 툴링 비용, 사용자 지정이 불가능함 |
전자 빔 용융(EBM) | 대형 부품의 제작 시간 단축, 지지 구조물 필요 없음 | 제한된 소재 선택, PBF에 비해 낮은 해상도 |
스테레오리소그래피(SLA) | 폴리머 부품의 뛰어난 표면 마감, 빠른 제작 시간 | 금속에는 적합하지 않음, PBF에 비해 제한된 재료 특성 |
레이저 기반 파우더 베드 융합의 주요 사양
레이저 기반 PBF를 고려할 때는 관련된 주요 사양과 표준을 이해하는 것이 중요합니다. 다음은 가장 중요한 매개변수를 요약한 것입니다.
사양 | 설명 |
---|---|
레이어 두께 | 일반적으로 20~60미크론 범위로 빌드 시간과 디테일에 영향을 미칩니다. |
볼륨 구축 | 기계에 따라 다르며, 일반적인 크기는 250x250x300mm 또는 500x500x500mm입니다. |
레이저 파워 | 빌드 속도와 품질에 영향을 미치는 200W~1000W 범위입니다. |
스캔 속도 | 최대 7m/s로 부품 제작 속도에 영향을 미칩니다. |
빌드 속도 | 일반적으로 부품 크기와 복잡성에 따라 다른 방법에 비해 속도가 느립니다. |
머티리얼 유형 | 티타늄, 스테인리스 스틸, 알루미늄, 코발트 크롬 등이 포함됩니다. |
후처리 | 열처리, 표면 마감, 파우더 제거가 포함됩니다. |
공급업체 및 가격 레이저 기반 파우더 베드 융합 시스템
장비와 자재를 어디서 조달할 수 있는지 아는 것은 프로젝트의 성공에 큰 차이를 만들 수 있습니다. 다음은 몇 가지 주요 공급업체와 가격 정보를 요약한 것입니다.
공급업체 | 장비 | 가격 범위 | 참고 |
---|---|---|---|
EOS | EOS M 290, EOS P 396 | $500,000 – $1,000,000 | 높은 정밀도와 신뢰성으로 잘 알려져 있습니다. |
SLM 솔루션 | SLM 280, SLM 500 | $450,000 – $1,200,000 | 대용량 빌드 볼륨과 빠른 속도를 제공합니다. |
Renishaw | RenAM 500Q, RenAM 500M | $400,000 – $1,000,000 | 유연성과 고해상도를 강조합니다. |
3D Systems | ProX DMP 320, ProX DMP 200 | $400,000 – $900,000 | 고급 자료 처리 및 정밀도가 특징입니다. |
GE 애디티브 | 컨셉 레이저 M2, Arcam A2X | $600,000 – $1,500,000 | 고성능과 광범위한 소재 옵션으로 유명합니다. |
트럼프 | TruPrint 1000, TruPrint 3000 | $350,000 – $1,000,000 | 컴팩트하고 확장 가능한 솔루션을 제공합니다. |
첨가제 산업 | MetalFAB1 | $500,000 – $1,200,000 | 확장 가능한 모듈식 시스템을 제공합니다. |
ExOne | 엑스원 X1-Lab, 엑스원 X1 160Pro | $300,000 – $800,000 | 바인더 분사 및 PBF에 중점을 둡니다. |
DMLS | DMS M2, DMS M1 | $500,000 – $1,000,000 | 정밀하고 고품질의 부품으로 유명합니다. |
Sinterit | Lisa X, Lisa PRO | $100,000 – $300,000 | 소규모 제작을 위한 저렴한 솔루션을 제공합니다. |
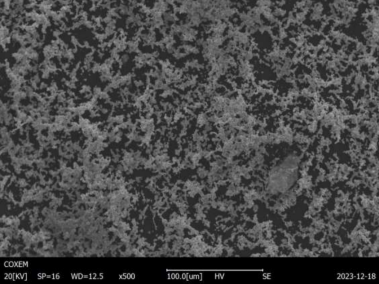
자주 묻는 질문
레이저 기반 파우더 베드 퓨전에 대해 자주 묻는 질문을 통해 불확실성을 해소하는 데 도움이 되는 몇 가지 사항을 알아보세요.
질문 | 답변 |
---|---|
기존 제조 방식에 비해 레이저 기반 PBF의 주요 장점은 무엇인가요? | 레이저 기반 PBF를 사용하면 기존 방법으로는 달성하기 어렵거나 불가능한 복잡한 형상을 만들 수 있습니다. 또한 사용하지 않은 파우더를 재활용하여 재료 낭비를 줄일 수 있습니다. |
레이저 기반 PBF의 비용은 다른 제조 기술과 어떻게 비교되나요? | 레이저 기반 PBF는 장비와 재료에 대한 초기 비용이 높지만 재료 효율성과 툴링의 필요성 감소로 인해 소량 배치 및 맞춤형 부품에 비용 효율적일 수 있습니다. |
레이저 기반 파우더 베드 융합의 일반적인 응용 분야는 무엇인가요? | 항공우주 부품, 의료용 임플란트, 자동차 부품, 툴링 등 다양한 분야에서 활용되고 있습니다. 이 기술은 정밀도와 복잡한 부품을 생산할 수 있는 능력으로 높은 평가를 받고 있습니다. |
레이저 기반 PBF를 사용하여 부품을 제작하는 데 시간이 얼마나 걸리나요? | 제작 시간은 부품 크기와 복잡성에 따라 다릅니다. 작고 덜 복잡한 부품은 몇 시간이 걸릴 수 있지만, 더 크고 복잡한 부품은 며칠이 걸릴 수 있습니다. |
레이저 기반 PBF에는 어떤 종류의 재료를 사용할 수 있나요? | 티타늄, 스테인리스 스틸, 알루미늄, 코발트 크롬 및 다양한 합금을 포함한 다양한 금속을 사용할 수 있습니다. 각 소재는 서로 다른 특성과 장점을 제공합니다. |
레이저 기반 PBF와 관련된 주요 과제는 무엇인가요? | 높은 장비 비용, 상대적으로 느린 생산 속도, 원하는 표면 마감을 얻기 위한 후처리가 필요하다는 점 등이 문제입니다. 또한 파우더를 효율적으로 관리하고 재활용하는 것도 복잡할 수 있습니다. |