플라즈마 회전 전극 분무, 분말 제조 장비, 준비, 분말 제조 시스템
금속 분말은 기계적(볼 밀링, 분쇄 등), 물리적(원자화), 화학적(환원, 전기 분해, 카보닐 및 변위법 등) 등 다양한 방법으로 제조할 수 있습니다. 그러나 구형 금속 분말에 대한 SEBM 기술의 요구 사항을 충족하기 위해 분무화는 금속 분말의 제조에 사용되는 주요 방법이며, 특히 물 분무화, WA, 가스 분무화, GA, 플라즈마 분무화, PA 및 플라즈마 회전 전극 공정, PREP. 공정 및 때로는 분말 제조 비용을 절감하기 위해 수화물-탈수화물, HDH를 사용하는 경우가 있습니다.
PREP 파우더 제조 기술
플라즈마 회전 전극 분무 방법은 플라즈마 아크를 열원으로 사용하여 고속 회전 금속 막대의 끝면을 지속적으로 녹이고 원심력의 작용으로 녹은 금속 방울이 날아가고 불활성 가스 (아르곤 또는 헬륨)의 냉각 효과로 빠르게 응고되어 구형 금속 분말을 형성합니다. 물 분무 및 가스 분무에 비해 플라즈마 회전 전극 분무 방식은 냉각 속도가 낮고 구형도가 높고 유동성이 좋으며 산소 함량이 낮고 중공 및 위성 분말이 거의 없는 분말을 생산합니다. 도가니의 오염이 방지되므로 준비된 분말은 순수합니다. 또한 이 방법으로 제조된 분말은 입자 크기 분포가 좁습니다.
신청 현황
PREP 분말 기술은 미국 원자력 금속공사에서 처음 개발하여 1963년 특허로 보고되었고, 1974년 플라즈마 토치가 텅스텐 전극 아크를 열원으로 대체하여 플라즈마 회전 전극 원자화(PREP) 방식이 개발되었습니다.
1974년 플라즈마 토치가 텅스텐 전극 아크를 열원으로 대체하고 플라즈마 회전 전극 원자화(PREP) 방식이 탄생했습니다. 1983년 북서 비철금속연구소의 분말 야금 연구소에서 중국 최초의 PREP 장비를 설계 및 개발했으며, 이후 많은 중국 기업과 기관에서도 이 기술에 대한 연구 개발을 수행했습니다. 원심 분무 방식인 PREP 방식은 다른 방식에 비해 구형성, 높은 활력 밀도, 우수한 유동성, 낮은 가스 함량 및 좁은 입자 크기 분포의 장점을 가지고 있습니다. 40년 이상의 개발을 통해 플라즈마 회전 전극 분무법은 장비 개선, 공정 제어 및 분말 품질 측면에서 빠르게 발전했으며 구형 금속 분말 제조에 없어서는 안 될 방법이 되었습니다.
PREP 장비는 일반적으로 진공 시스템, 가스 시스템, 냉각 시스템, 전원 공급 시스템, 플라즈마 발생기, 공급 장치, 분무 챔버 및 수집 시스템으로 구성됩니다.
공급 장치, 분무 챔버 및 수집 시스템. 일반적으로 아르곤, 헬륨 또는 아르곤과 헬륨의 혼합물인 불활성 가스는 분무 공정 중에 분말을 보호하고 냉각하며 품질에 핵심적인 역할을 합니다. 러시아 분말 생산 시설에서는 일반적으로 헬륨과 아르곤의 비율을 4:1로 설정합니다.
플라즈마 토치는 일반적으로 전달 아크 모드와 비 전달 아크 모드의 두 가지 모드로 작동하며 러시아 장비는 주로 비 전달 아크 모드, 즉 전극과 노즐 사이에서 아크가 생성됩니다. Xi’an Sailong Metals는 봉재에 더 많은 열을 전달하여 봉재 끝면의 용융 속도를 높이고 생산 효율성을 향상시키는 전사 아크 작동 모드를 사용합니다.
최근 몇 년 동안 Xi’an Sailong Metals는 최초의 수직 산업 등급 SLPA-V를 개발했습니다. 준비 기계 세계 최고 수준입니다. 이 기계는 수직 전극 바 배치 구조로 작동 중 진동을 줄이고 작업 속도를 높이며 고품질 분말을 안정적으로 생산할 수 있습니다.
또한 최대 60,000rpm의 작업 속도를 갖춘 탁상형 플라즈마 회전 전극 분무 설비 SLPA-D는 소량 및 다양한 종류의 고품질 구형 금속 분말의 개발 및 생산에 적합합니다. 산업용 등급의 SLPA-H PREP 기계는 새로운 동적 씰 구조로 대구경 전극봉의 고속 회전을 위한 동력 지원을 제공할 수 있습니다. 새로운 고토크 고속 전극 회전 드라이브 및 전원 공급 시스템은 13,000~18,000rpm에서 Φ75mm 전극의 개발 및 생산에 사용할 수 있습니다.
새로운 고토크, 고속 로드 회전 드라이브 및 전원 공급 시스템을 통해 Φ75mm 로드를 13,000-18,000 r/min으로 정상 작동하고 3000A의 고전류에서도 안정적인 전원 공급이 가능합니다.
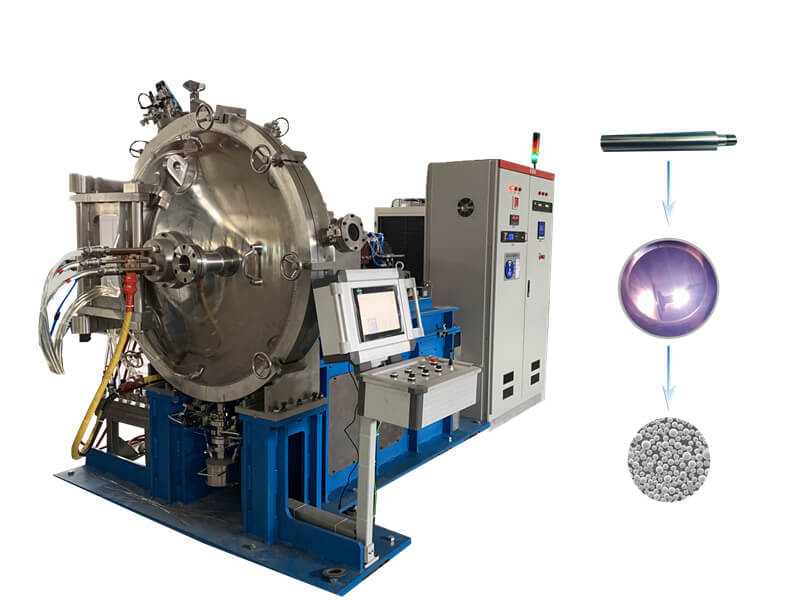
PREP 금속 분말의 입자 크기
분말의 입자 크기와 그 분포는 후속 응용 분야에서 가장 중요한 관심사 중 하나이며 분말 특성과 궁극적으로 성형 부품의 품질에 영향을 미치는 경우가 많으므로 입자 크기 분포가 가능한 한 필요한 범위 내에 있도록 PREP 공정 파라미터를 합리적으로 결정해야 합니다.
일반적으로 분말의 입자 크기 분포에 영향을 미치는 주요 공정 파라미터는 전극봉 재료, 전극봉 회전 속도, 봉 직경, 플라즈마 건 출력, 이송 속도, 플라즈마 건과 봉 사이의 거리, 플라즈마 가스 유량 등입니다. PREP 분말 제조 공정에서는 원심력이 표면장력보다 클 때 방울이 배출되므로 전극봉 회전 속도를 높이거나 전극봉 직경을 늘려 원심력을 높이면 분말 입자 크기가 작아질 수 있습니다. 또한 봉재 끝면의 용융 속도는 이송 속도와 가능한 한 같아야 합니다. 용융 속도가 이송 속도보다 크면 아크 파손이 발생하고 이송 속도가 용융 속도보다 크면 용융 불량이 발생하여 플라잉 에지 및 기타 문제가 발생합니다. 플라즈마 건과 바 사이의 거리는 분말의 과열에 영향을 미치고 플라즈마 가스 흐름은 냉각 효과에 영향을 미칩니다. 분말의 평균 입자 크기는 주로 바와 관련이 있는 것으로 밝혀졌습니다.
바 속도 또는 직경이 클수록 재료가 특정 크기일 때 분말이 더 미세해지며, 입자 크기 분포는 바 속도, 전류 및 플라즈마 건과 바 끝 사이의 거리 등과 관련이 있습니다. 속도를 높이거나 전류 또는 플라즈마 건과 봉재 끝 사이의 거리를 줄이면 입자 크기 분포 곡선이 좁아집니다.
재료가 다른 경우 평균 입자 크기와 그 분포는 종종 재료의 밀도 및 표면 장력과 같은 요소와 관련이 있습니다.
파우더 제조 및 적용 준비
PREP 기술의 발달로 점점 더 많은 신소재 분말을 제조할 수 있게 되었습니다. 관련된 분말의 유형은 티타늄 합금, 1018 강철, 고질소 강철, Ni-Ti-Fe, 인코넬 718, FGH95, Ti, TiNb 등입니다.
Xi’an Sailong에서 생산하는 대부분의 분말은 티타늄 합금 분말, 고온 합금 분말 및 스테인리스 스틸 분말입니다.
지금까지 티타늄 합금 분말, 코발트계 고온 합금 분말, 니켈계 고온 합금 분말, 내화 금속 분말 (예 : W, Mo Ta, Nb 및 그 합금), 스테인리스 스틸 분말 및 알루미늄 합금 분말 및 은 합금 분말 등, 분말은 성능이 우수하고 제조 후 생산이 가능하며 분말은 항공 우주, 기계 및 생물 의학 분야에서 널리 사용되거나 고온 등압 압착 후 생산됩니다.