Aperçu des poudres REP
Les poudres métalliques sont l'épine dorsale de la fabrication moderne, en particulier dans les industries où la précision et la qualité sont primordiales. Parmi elles, les poudres REP (Rapid Engineering Powder) se distinguent par leurs propriétés exceptionnelles et leurs applications polyvalentes. Ces poudres, souvent utilisées dans la fabrication additive et la métallurgie des poudres, se déclinent en différentes compositions et spécifications, chacune adaptée à des besoins industriels spécifiques. Mais qu'est-ce qui rend les poudres REP si spéciales ? Plongeons dans leur univers, en explorant leurs types, leurs compositions, leurs caractéristiques, leurs applications, et bien plus encore.
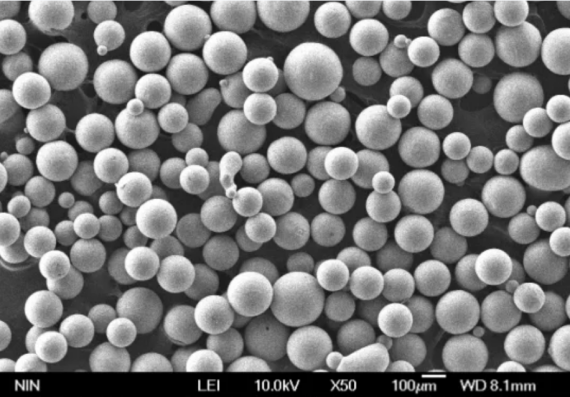
Types et compositions des poudres REP
Il existe une grande variété de poudres REP, chacune ayant des propriétés uniques découlant de sa composition spécifique. Voici un aperçu détaillé de quelques-uns des principaux types de poudres :
Type | Composition | Propriétés | Caractéristiques |
---|---|---|---|
Alliage d'aluminium | Al, Cu, Mg, Si | Léger, résistant à la corrosion | Rapport résistance/poids élevé |
Alliage de titane | Ti, Al, V | Haute résistance, biocompatible | Excellente résistance à la fatigue |
acier inoxydable | Fe, Cr, Ni, Mo | Résistant à la corrosion, durable | Résistance élevée à la traction |
Alliage de nickel | Ni, Cr, Mo | Résistant à la chaleur, résistant à la corrosion | Excellente performance à haute température |
Cobalt-Chrome | Co, Cr, Mo | Résistant à l'usure, biocompatible | Dureté et résistance élevées |
Alliage de cuivre | Cu, Zn, Sn | Conducteur, résistant à la corrosion | Excellente conductivité électrique et thermique |
poudre de fer | Fe, C | Propriétés magnétiques, durables | Rentable et polyvalent |
Carbure de tungstène | W, C | Extrêmement dur, résistant à l'usure | Point de fusion élevé, excellente résistance à l'abrasion |
Inconel | Ni, Cr, Fe, Nb | Résistant à l'oxydation, haute résistance | Performances supérieures dans les environnements extrêmes |
Acier à outils | Fe, C, Cr, Mo, V | Dur, résistant à l'usure | Dureté et ténacité élevées |
Chacune de ces poudres apporte quelque chose d'unique, ce qui les rend adaptées à différentes applications industrielles. Mais quelles sont exactement ces applications ?
Applications des poudres REP
Les poudres REP sont utilisées dans une multitude d'industries, grâce à leurs diverses propriétés. Voici un aperçu de leurs applications :
L'industrie | Applications |
---|---|
Aérospatiale | Aubes de turbines, composants structurels |
Automobile | Pièces de moteur, composants de transmission |
Médical | Implants, instruments chirurgicaux |
Électronique | Encres conductrices, connecteurs |
Pétrole et gaz | Outils de forage, pipelines |
Soins dentaires | Couronnes, bridges, implants dentaires |
Défense | Armures, composants d'armes |
Outil et matrice | Moules, outils de coupe |
L'énergie | Composants de production d'énergie, batteries |
Biens de consommation | Bijoux, lunettes, accessoires de mode |
De l'industrie aérospatiale de haut vol au secteur médical de précision, les poudres REP jouent un rôle crucial dans l'amélioration des performances et de la fiabilité. Mais comment choisir la bonne poudre pour vos besoins ?
Spécifications, tailles, qualités et normes des poudres REP
Il est essentiel de comprendre les spécifications et les normes des poudres REP pour prendre des décisions éclairées. Voici un tableau détaillé :
Type | Gamme de taille des particules (µm) | Notes | Normes |
---|---|---|---|
Alliage d'aluminium | 15-45, 45-106 | 2024, 6061, 7075 | ASTM B928, AMS 4286 |
Alliage de titane | 15-45, 45-105 | Ti-6Al-4V, Ti-5Al-2,5Sn | ASTM F2924, AMS 4999 |
acier inoxydable | 15-45, 45-106 | 316L, 17-4PH | ASTM A564, AMS 5643 |
Alliage de nickel | 15-45, 45-106 | Inconel 718, 625 | ASTM B637, AMS 5662 |
Cobalt-Chrome | 15-45, 45-105 | CoCrMo | ASTM F75, ISO 5832-4 |
Alliage de cuivre | 15-45, 45-106 | C11000, C93200 | ASTM B170, AMS 4500 |
poudre de fer | 15-45, 45-106 | FC-0205, FN-0208 | MPIF Standard 35, ASTM B783 |
Carbure de tungstène | 15-45, 45-105 | WC-6Co, WC-10Co | ASTM B777, AMS 7876 |
Inconel | 15-45, 45-106 | 625, 718 | ASTM B443, AMS 5666 |
Acier à outils | 15-45, 45-106 | M2, D2 | ASTM A681, AMS 6437 |
La taille des particules, la qualité et la norme de chaque poudre garantissent qu'elle répond aux exigences spécifiques de l'industrie, garantissant ainsi la qualité et la performance.
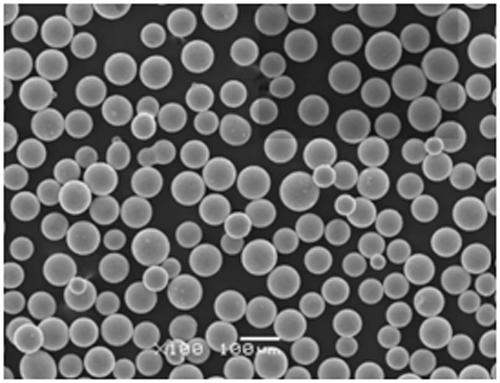
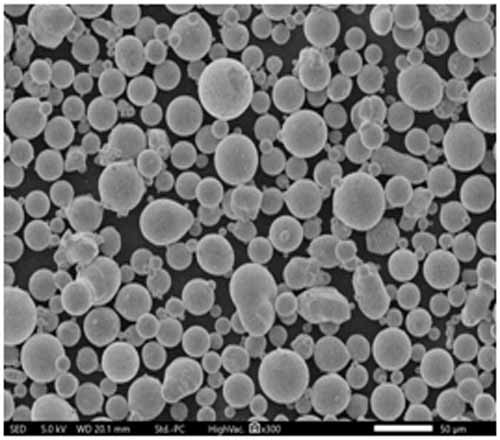
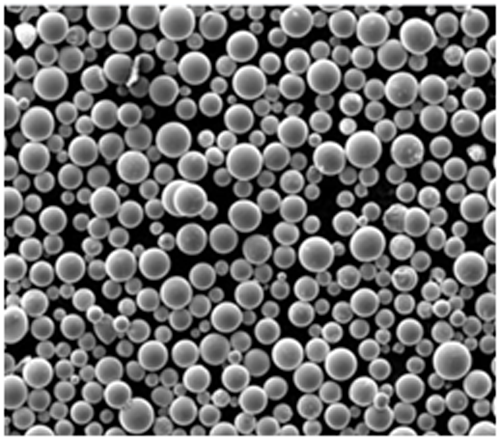
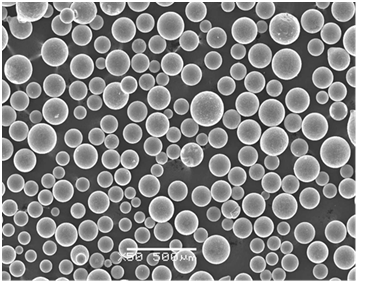
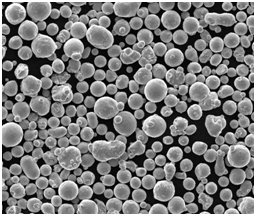
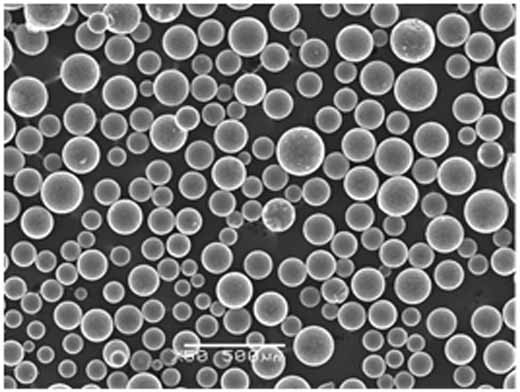
Fournisseurs et prix des poudres REP
Il est essentiel pour les entreprises de trouver le bon fournisseur et de comprendre les prix. Voici un aperçu des principaux fournisseurs et de leurs tarifs :
Fournisseur | Localisation | Types de poudres disponibles | Fourchette de prix (par kg) |
---|---|---|---|
Praxair | ÉTATS-UNIS | Aluminium, Titane, Nickel | $50 – $200 |
Höganäs | Suède | Fer, acier inoxydable, cuivre | $20 – $100 |
Technologie des charpentiers | ÉTATS-UNIS | Acier à outils, titane, cobalt | $100 – $300 |
Sandvik | Suède | Acier inoxydable, Nickel, Inconel | $80 – $250 |
Oerlikon Metco | Suisse | Titane, nickel, aluminium | $90 – $280 |
GKN Additive | ROYAUME-UNI | Fer, acier inoxydable, acier à outils | $30 – $120 |
Technologie LPW | ROYAUME-UNI | Acier inoxydable, nickel, cuivre | $70 – $220 |
AP&C (GE Additive) | Canada | Titane, aluminium, Inconel | $100 – $350 |
Advanced Powder & Coatings | Canada | Nickel, Inconel, Acier à outils | $80 – $300 |
Erasteel | France | Acier à outils, acier inoxydable | $60 – $180 |
Grâce à ces informations, les entreprises peuvent prendre des décisions éclairées concernant leurs achats, en équilibrant la qualité et le coût.
Comparaison des avantages et des inconvénients des poudres REP
Les différentes poudres REP offrent des avantages et des limites variés. Voici un aperçu comparatif :
Type | Avantages | Limites |
---|---|---|
Alliage d'aluminium | Léger, résistant à la corrosion | Résistance moindre par rapport à d'autres alliages |
Alliage de titane | Haute résistance, biocompatible | Coûteux, difficile à usiner |
acier inoxydable | Durable, résistant à la corrosion | Plus lourd que certains autres alliages |
Alliage de nickel | Résistance à la chaleur, performance à haute température | Cher, disponibilité limitée |
Cobalt-Chrome | Résistant à l'usure, biocompatible | Coûteux, difficile à traiter |
Alliage de cuivre | Excellente conductivité, résistant à la corrosion | Plus doux, moins durable |
poudre de fer | Rentable et polyvalent | Risque de rouille en l'absence de traitement adéquat |
Carbure de tungstène | Extrêmement dur, résistant à l'usure | Très fragile, difficile à travailler |
Inconel | Résistant à l'oxydation, haute résistance | Très cher, fournisseurs limités |
Acier à outils | Dureté élevée, résistance à l'usure | Sujet à la corrosion, nécessite un traitement thermique |
En pesant le pour et le contre, les fabricants peuvent sélectionner la poudre la mieux adaptée à leurs besoins spécifiques, garantissant ainsi des performances et une rentabilité optimales.
Avantages de l'utilisation des poudres REP
Pourquoi devrait-on envisager d'utiliser les poudres REP en premier lieu ? Examinons leurs principaux avantages :
- Amélioration des performances : Les poudres REP sont conçues pour offrir des propriétés mécaniques supérieures, améliorant ainsi les performances du produit final.
- Polyvalence : Avec une large gamme de compositions, les poudres REP peuvent être utilisées dans diverses industries, de l'aérospatiale aux biens de consommation.
- Précision : Ces poudres permettent une fabrication de haute précision, cruciale pour des applications telles que les implants médicaux et les composants aérospatiaux.
- Efficacité : Les poudres REP permettent souvent d'accélérer les temps de production et de réduire les pertes de matériaux, ce qui contribue à la réduction des coûts et à la durabilité.
- Qualité : Les produits fabriqués à partir des poudres REP présentent une qualité constante et répondent aux normes et spécifications rigoureuses de l'industrie.
Ces avantages font des poudres REP un choix intéressant pour la fabrication moderne, favorisant l'innovation et l'efficacité.
Caractéristiques des poudres REP
Les poudres REP possèdent des caractéristiques uniques qui les distinguent des autres matériaux. En voici un aperçu :
Caractéristique | Description |
---|---|
Taille des particules | La distribution uniforme de la taille des particules garantit des propriétés et des performances constantes. |
Capacité d'écoulement | L'excellente fluidité permet une manipulation et un traitement faciles dans la fabrication. |
La pureté | Des niveaux de pureté élevés minimisent le risque de contamination et de défauts dans les produits finaux. |
Densité | Une densité optimale assure la solidité et la durabilité des composants fabriqués. |
Morphologie | Formes sphériques ou irrégulières adaptées à des processus de fabrication spécifiques. |
Surface | Le contrôle de la surface affecte la réactivité et le comportement de frittage de la poudre. |
La compréhension de ces caractéristiques aide les fabricants à choisir la bonne poudre REP pour leurs applications spécifiques, garantissant ainsi des résultats optimaux.
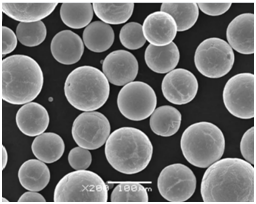
FAQ
Question | Réponse |
---|---|
A quoi servent les poudres REP ? | Les poudres REP sont utilisées dans diverses industries pour la fabrication de composants de haute performance, notamment dans les secteurs de l'aérospatiale, de l'automobile et de la médecine. |
Comment les poudres REP sont-elles fabriquées ? | Les poudres REP sont généralement produites par atomisation, c'est-à-dire que le métal fondu est pulvérisé en une fine poudre. |
Quels sont les avantages de l'utilisation des poudres REP ? | Les avantages sont notamment l'amélioration des performances, la polyvalence, la précision, l'efficacité et une qualité constante. |
Comment choisir la bonne poudre REP ? | Tenez compte de l'application spécifique, des propriétés requises et du coût pour sélectionner la poudre la plus appropriée. |
Les poudres REP sont-elles chères ? | Les prix varient en fonction de la composition et du fournisseur, mais les poudres REP peuvent être plus chères en raison de leurs propriétés supérieures. |
Les poudres REP peuvent-elles être personnalisées ? | Oui, les poudres REP peuvent être adaptées à des compositions et des tailles de particules spécifiques pour répondre à des exigences particulières. |
Quels sont les défis liés à l'utilisation des poudres REP ? | Les défis à relever sont notamment les coûts plus élevés, les difficultés de traitement et la nécessité de garantir une qualité constante. |
Comment les poudres REP se comparent-elles aux matériaux traditionnels ? | Les poudres REP offrent de meilleures performances et une plus grande précision, mais leur coût peut être plus élevé. |
Où puis-je acheter des poudres REP ? | Plusieurs fournisseurs dans le monde proposent des poudres REP, notamment Praxair, Höganäs et Carpenter Technology. |
Quelles sont les industries qui bénéficient le plus des poudres REP ? | Les industries aérospatiale, automobile, médicale et électronique bénéficient considérablement des propriétés uniques des poudres REP. |
En conclusion, les poudres REP changent la donne dans le monde de la fabrication, car elles offrent des propriétés et une polyvalence inégalées. En comprenant leurs types, leurs applications et leurs caractéristiques, les fabricants peuvent exploiter tout leur potentiel pour stimuler l'innovation et l'efficacité de leurs processus. Que vous travailliez dans l'aérospatiale, le médical ou toute autre industrie, les poudres REP offrent la qualité et les performances nécessaires pour rester en tête sur le marché concurrentiel d'aujourd'hui.