Si vous vous plongez dans le monde des poudres métalliques, en particulier celles utilisées dans des applications avancées telles que la résistance à l'usure, Poudre de NiCrBSi est quelque chose que vous rencontrerez. Il s'agit d'une poudre d'alliage puissante, souvent utilisée pour la projection thermique, le soudage et diverses techniques de revêtement. Mais pourquoi est-elle si spéciale ? Qu'est-ce qui fait que le NiCrBSi se distingue des autres poudres métalliques ? Aujourd'hui, nous allons vous présenter tout ce que vous devez savoir sur la poudre NiCrBSi, de sa composition à ses diverses applications et avantages.
Aperçu de la poudre de NiCrBSi
La poudre NiCrBSi est une poudre d'alliage autofluidifiant composée principalement de nickel (Ni), de chrome (Cr), de bore (B), de silicium (Si) et de fer (Fe). Cette combinaison lui confère une grande résistance à l'usure, à l'oxydation et à la corrosion, ce qui la rend idéale pour diverses applications industrielles. La poudre est généralement appliquée par pulvérisation thermique, par revêtement laser ou par soudage, ce qui confère aux surfaces une excellente couche protectrice.
Composant | Gamme de composition |
---|---|
Nickel (Ni) | 60-80% |
Chrome (Cr) | 10-20% |
Bore (B) | 2-4% |
Silicium (Si) | 3-5% |
Fer (Fe) | 2-6% |
Maintenant que nous connaissons la composition de base, explorons quelques-uns des modèles spécifiques de poudre de NiCrBSi, leurs utilisations et les raisons pour lesquelles cette poudre est si importante dans certaines industries.
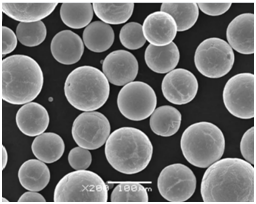
Composition de la poudre de NiCrBSi
La poudre de NiCrBSi est composée de plusieurs éléments qui travaillent ensemble pour améliorer ses performances globales dans les applications industrielles. Décortiquons chaque composant et comprenons comment ils contribuent à la fonctionnalité de la poudre :
- Nickel (Ni) : Le nickel est la base de l'alliage et offre une excellente résistance à la corrosion. Il contribue également à lier les autres composants entre eux, assurant ainsi une répartition uniforme des propriétés.
- Chrome (Cr) : Le chrome est ajouté pour améliorer la résistance à l'oxydation et la dureté. Il contribue à créer une couche d'oxyde protectrice, en particulier lorsque la poudre est utilisée dans des environnements à haute température.
- Bore (B) : Le bore agit comme un agent fondant, réduisant le point de fusion et aidant la poudre à se lier plus efficacement au matériau de base.
- Silicium (Si) : Le silicium contribue également aux propriétés de fluxage de la poudre et améliore sa dureté et sa résistance à l'usure.
- Fer (Fe) : Le fer peut être présent en petites quantités et peut contribuer à améliorer la résistance mécanique.
Cette combinaison unique d'éléments fait de la poudre de NiCrBSi une option polyvalente pour le revêtement de surfaces nécessitant une résistance élevée à l'usure et à la corrosion.
Caractéristiques de la poudre de NiCrBSi
Qu'est-ce qui distingue la poudre de NiCrBSi des autres poudres métalliques ? Voici quelques-unes des principales caractéristiques qui en font un matériau de grande valeur :
- Autofluorescence : Grâce à la présence de bore et de silicium, les poudres de NiCrBSi sont autofluidifiantes. Cela signifie qu'elles peuvent créer un revêtement lisse et uniforme sans qu'il soit nécessaire d'utiliser des flux externes pendant le processus d'application.
- Excellente résistance à l'usure : Les revêtements NiCrBSi sont durs et peuvent résister à une usure importante, ce qui les rend idéaux pour les composants qui subissent une forte friction.
- Résistance élevée à la corrosion et à l'oxydation : La teneur en chrome et en nickel permet à la poudre de résister à la corrosion et à l'oxydation, même à des températures élevées.
- Facilité d'application : La poudre de NiCrBSi est généralement appliquée à l'aide de méthodes de pulvérisation thermique ou de revêtement par laser, ce qui la rend facile à utiliser dans divers environnements industriels.
Modèles spécifiques de Poudre de NiCrBSi
Lors du choix d'une poudre de NiCrBSi, il est essentiel de comprendre les différents modèles disponibles sur le marché. Chaque modèle possède des propriétés spécifiques adaptées à différentes applications. Examinons de plus près quelques-uns des modèles les plus courants de poudre de NiCrBSi et leurs caractéristiques uniques :
Modèle | Composition | Dureté (HRC) | Point de fusion (°C) | Applications |
---|---|---|---|---|
Metco 16C | NiCrBSi | 40-45 | 1020-1060 | Revêtements généraux résistants à l'usure |
Colmonoy 88 | NiCrBSi+Mo | 55-60 | 1040-1080 | Applications à haute température et à forte usure |
Amdry 1371 | NiCrBSi | 50-55 | 1025-1070 | Composants pour l'aérospatiale et les turbines |
Stellite 1 | NiCrBSi+Co | 50-55 | 1170-1200 | Environnements d'usure et de corrosion sévères |
Duramite 211 | NiCrBSi | 45-50 | 1010-1065 | Roulements, engrenages et autres composants mécaniques |
Deloro 55 | NiCrBSi+Fe | 52-56 | 1030-1085 | Outils de coupe et vannes industrielles |
Metco 31 | NiCrBSi | 48-52 | 1050-1100 | Pièces automobiles et rouleaux industriels |
Colmonoy 5 | NiCrBSi | 45-50 | 1025-1070 | Arbres, turbines et composants mécaniques |
Amdry 105 | NiCrBSi+Al | 52-57 | 1040-1085 | Tubes d'échangeurs de chaleur et équipements de fours |
Deloro 60 | NiCrBSi | 55-60 | 1035-1080 | Environnements d'usure extrême, outils miniers |
Chacune de ces poudres est conçue pour des applications et des environnements spécifiques. Le choix de la bonne poudre dépendra donc de vos besoins en matière de résistance à l'usure, de protection contre la corrosion ou de plage de température de fonctionnement.
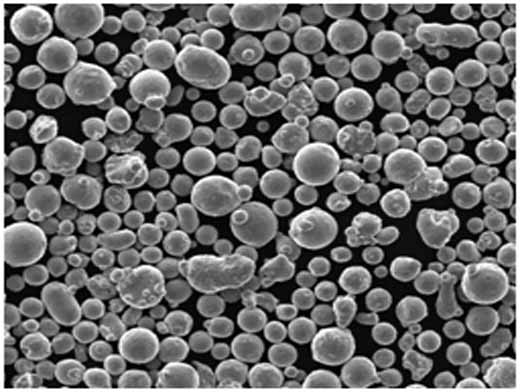
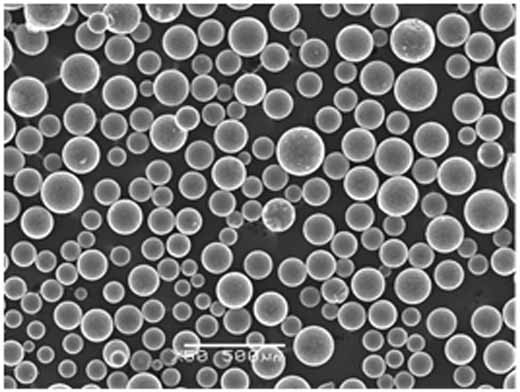
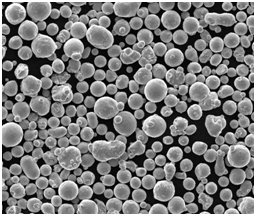
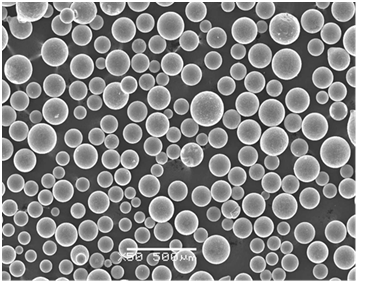
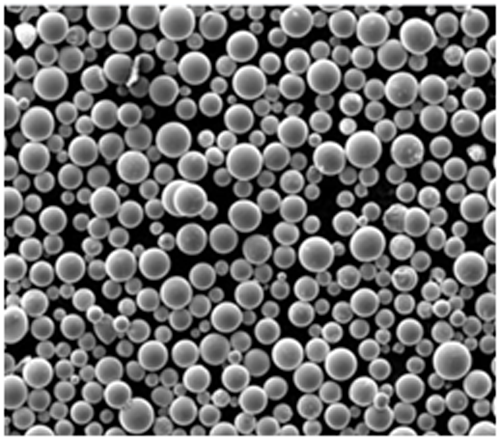
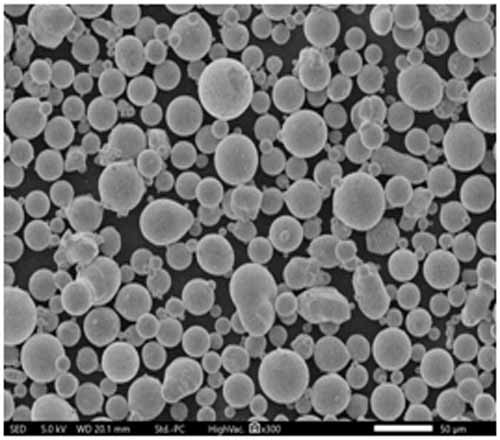
Applications de la poudre de NiCrBSi
La poudre de NiCrBSi est incroyablement polyvalente et est utilisée dans un large éventail d'industries. De la protection des composants mécaniques à l'augmentation de la durée de vie des pièces soumises à de fortes contraintes, ses applications sont vastes.
L'industrie | application | Pourquoi le NiCrBSi est-il utilisé ? |
---|---|---|
Aérospatiale | Aubes de turbines, pièces de moteurs | Résistance élevée à la chaleur et à la corrosion |
Automobile | Sièges de soupapes, engrenages et arbres | Résistance à l'usure et longévité accrue |
Pétrole et gaz | Outils de forage, sièges de soupape, pompes | Résistance à la corrosion dans les environnements difficiles |
Exploitation minière | Composants de concassage de roches, pièces de convoyeurs | Résistance extrême à l'usure et aux chocs |
Production d'électricité | Chaudières, turbines et échangeurs de chaleur | Résistance à l'oxydation à haute température |
Industrie textile | Rouleaux et autres éléments mobiles | Résistance au frottement et à l'usure |
Transformation des aliments | Lames et outils de mélange | Résistance à la corrosion et à l'usure pour les équipements hygiéniques |
Traitement des métaux | Rouleaux de four, filières d'extrusion | Résistance à l'usure dans les environnements à haute température |
Ces industries exigent des matériaux capables de résister à des pressions intenses, à la chaleur ou à l'usure, et la poudre de NiCrBSi est à la hauteur de ces exigences.
Spécifications, tailles, qualités et normes
Lorsque l'on sélectionne Poudre de NiCrBSi pour une application particulière, il est essentiel de comprendre les spécifications. Examinons les tailles et les qualités disponibles, ainsi que les normes auxquelles elles répondent.
Qualité de la poudre | Taille (µm) | Standard |
---|---|---|
Metco 16C | -106 +45 | ASTM B243 |
Colmonoy 88 | -106 +45 | AMS 4775 |
Amdry 1371 | -125 +45 | ISO 14919 |
Stellite 1 | -106 +38 | AWS A5.21 |
Duramite 211 | -106 +45 | ISO 14920 |
Deloro 55 | -125 +45 | AMS 4782 |
Metco 31 | -106 +38 | ASTM F305 |
Colmonoy 5 | -106 +38 | ASTM B528 |
Amdry 105 | -125 +45 | ISO 9001 |
Deloro 60 | -106 +45 | AMS 4776 |
Le choix de la bonne qualité dépend des normes industrielles et de l'application spécifique que vous visez.
Fournisseurs et prix de la poudre de NiCrBSi
Si vous êtes à la recherche de poudre de NiCrBSi, le fournisseur que vous choisissez peut faire une différence significative en termes de qualité et de prix. Voici quelques-uns des fournisseurs les plus courants, ainsi que leurs prix moyens :
Fournisseur | Modèle | Prix (par kg) | Quantité minimale de commande (kg) |
---|---|---|---|
Oerlikon Metco | Metco 16C | $80 | 5 |
Kennametal Stellite | Stellite 1 | $95 | 10 |
Höganäs | Colmonoy 88 | $100 | 20 |
Praxair Surface Technologies | Amdry 1371 | $110 | 15 |
Mur Colmonoy | Colmonoy 5 | $90 | 5 |
Technologies de pulvérisation de flammes | Duramite 211 | $78 | 8 |
Powder Alloy Corporation | Deloro 55 | $85 | 10 |
Le prix peut varier en fonction de facteurs tels que la quantité, la pureté et la situation géographique du fournisseur, il est donc intéressant de faire le tour des magasins pour obtenir la meilleure offre.
Avantages de la poudre de NiCrBSi
Il existe de nombreuses raisons pour lesquelles les industries choisissent la poudre de NiCrBSi pour leurs besoins en matière de revêtement. Voici quelques-uns des principaux avantages :
- Durabilité : Les revêtements NiCrBSi offrent une excellente résistance à l'usure, prolongeant la durée de vie des pièces soumises à une forte friction.
- Résistance à la corrosion : La teneur élevée en nickel et en chrome en fait un produit idéal pour les environnements où la corrosion est un problème, comme dans les industries du pétrole et du gaz ou dans la marine.
- Stabilité à haute température : La poudre se comporte bien dans les environnements à haute température, conservant ses propriétés même lorsqu'elle est exposée à la chaleur.
- Rentable : Si le coût initial de la poudre de NiCrBSi peut être plus élevé que celui d'autres options, sa durabilité et sa durée de vie prolongée en font une solution rentable à long terme. En réduisant le besoin de remplacements ou de réparations fréquents, elle aide les industries à économiser sur les coûts d'exploitation.
- Polyvalence : Avec différentes qualités et compositions disponibles, la poudre de NiCrBSi peut être adaptée à un large éventail d'applications dans différentes industries. Que vous ayez besoin d'un revêtement de haute dureté ou d'une résistance à la corrosion, il existe probablement une formulation de NiCrBSi qui répond à vos besoins.
- Propriétés d'auto-flux : La nature autofluidifiante de la poudre rend le processus d'application plus efficace. Une fois appliquée, elle crée une surface uniforme et lisse sans nécessiter de flux externes, ce qui réduit le nombre d'étapes supplémentaires dans le processus de revêtement.
Inconvénients de la poudre de NiCrBSi
Aussi impressionnante que soit la poudre de NiCrBSi, elle n'est pas sans limites. Examinons quelques-uns des inconvénients potentiels :
- Coût initial élevé : Si le NiCrBSi permet de réaliser des économies au fil du temps en raison de sa durabilité, les coûts initiaux sont plus élevés que pour d'autres matériaux de revêtement. Cela peut constituer un inconvénient pour les entreprises qui cherchent à minimiser les dépenses d'investissement initiales.
- Complexité de l'application : L'application de poudre de NiCrBSi nécessite souvent des équipements spécialisés tels que des pistolets de pulvérisation thermique ou des machines de revêtement au laser, qui ne sont pas toujours disponibles dans toutes les installations. Cela peut augmenter les coûts d'exploitation et nécessiter une formation spécialisée du personnel.
- Ne convient pas aux applications à basse température : La poudre de NiCrBSi est fantastique dans les environnements à haute température, mais si votre application fonctionne à basse température, elle risque de ne pas être aussi performante, notamment en termes de dureté et de propriétés d'adhérence.
- Exigences en matière de préparation de la surface : Les revêtements de NiCrBSi nécessitent une surface bien préparée pour garantir une adhérence optimale. Cela nécessite des étapes supplémentaires dans le processus de revêtement, telles que le préchauffage ou le nettoyage de la surface, ce qui peut prendre beaucoup de temps.
Comparaison : Poudre de NiCrBSi par rapport à d'autres poudres de revêtement
Pour mieux comprendre pourquoi la poudre de NiCrBSi est privilégiée dans tant d'industries, comparons-la à d'autres poudres couramment utilisées, comme le carbure de tungstène, le carbure de chrome et les poudres d'acier inoxydable.
Type de poudre | Résistance à l'usure | Résistance à la corrosion | Plage de température | Coût | Meilleure application |
---|---|---|---|---|---|
Poudre de NiCrBSi | Haut | Excellent | 1020-1200°C | Modérée-élevée | Environnements à haute température et à forte usure |
Carbure de tungstène | Très élevé | Bon | 800-1000°C | Très élevé | Outils de coupe, résistance extrême à l'abrasion |
Carbure de chrome | Haut | Excellent | 800-1000°C | Haut | Revêtements résistants à l'usure et à la corrosion |
acier inoxydable | Modéré | Excellent | 650-900°C | Modéré | Transformation des aliments, outils médicaux, usage général |
- NiCrBSi vs. carbure de tungstène : Le carbure de tungstène offre une meilleure résistance à l'usure que le NiCrBSi, mais il est beaucoup plus cher et sa plage de températures est plus étroite.
- NiCrBSi vs. carbure de chrome : Le carbure de chrome est également très résistant à l'usure et à la corrosion, mais il n'est pas aussi performant à des températures extrêmes que le NiCrBSi.
- NiCrBSi vs. acier inoxydable : Les poudres d'acier inoxydable sont moins résistantes à l'usure et ne donnent pas d'aussi bons résultats à haute température, mais elles sont moins chères et très résistantes à la corrosion dans des environnements plus doux.
Poudre de NiCrBSi dans les applications de pulvérisation thermique et de soudage
L'une des applications les plus courantes de la poudre de NiCrBSi est la suivante Pulvérisation thermique et soudage. Ces procédés sont utilisés pour appliquer la poudre sur un substrat, formant ainsi un revêtement protecteur qui améliore la résistance à l'usure et à la corrosion.
Pulvérisation thermique
Dans la projection thermique, la poudre de NiCrBSi est fondue et projetée sur la surface d'un composant, formant un revêtement dense et bien lié. Le processus fait appel à la pulvérisation à la flamme, à la pulvérisation au plasma ou à la pulvérisation à l'oxygène à haute vitesse (HVOF). Le résultat est une couche uniforme qui protège le composant contre les facteurs environnementaux difficiles.
- Avantages de la pulvérisation thermique :
- Permet une application précise des revêtements.
- L'apport minimal de chaleur dans le matériau de base réduit le risque de déformation.
- Convient pour les grandes surfaces ou les pièces qui ne peuvent pas être chauffées de manière intensive.
Soudage (rechargement au laser ou soudage PTA)
Dans les applications de soudage, la poudre de NiCrBSi est fondue à l'aide d'un laser ou d'une torche à plasma et fusionnée directement au substrat. Cela crée une couche métallurgique qui offre une résistance supérieure à l'usure et à la corrosion.
- Avantages du soudage :
- Crée une liaison plus forte avec le matériau de base par rapport à la pulvérisation thermique.
- Le revêtement peut être plus épais, ce qui renforce la protection.
- Convient aux pièces soumises à une forte usure, telles que les outils d'exploitation minière et les arêtes de coupe.
Avantages et inconvénients des techniques de revêtement par poudre du NiCrBSi
Lorsqu'il s'agit d'appliquer de la poudre de NiCrBSi, plusieurs options s'offrent à vous, comme la pulvérisation thermique, le rechargement au laser et le soudage à l'arc par transfert de plasma (PTA). Chaque technique a ses avantages et ses inconvénients :
Technique | Avantages | Inconvénients |
---|---|---|
Pulvérisation thermique | Application rapide, apport de chaleur minimal | Force d'adhérence inférieure à celle du soudage |
Revêtement par laser | Forte liaison métallurgique, revêtements plus épais | Coût plus élevé, application plus lente |
PTA Soudage | Haute précision, excellente résistance à l'usure | Nécessite un équipement et une expertise spécialisés |
Le choix de la bonne méthode d’application dépend des exigences de la pièce, notamment de sa taille, de sa forme et de l’environnement auquel elle sera exposée.
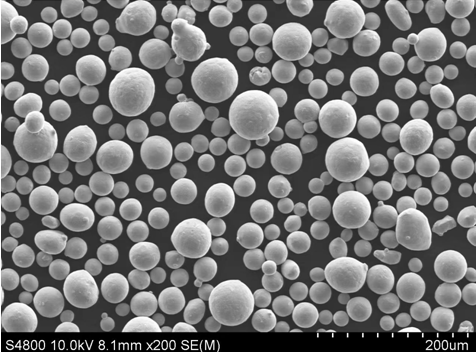
FAQ
Pour conclure, nous allons aborder certaines des questions les plus fréquemment posées au sujet de la poudre de NiCrBSi. Cette section vous aidera à clarifier toute incertitude persistante que vous pourriez avoir.
Question | Réponse |
---|---|
À quoi sert principalement la poudre de NiCrBSi ? | La poudre de NiCrBSi est utilisée pour les revêtements résistants à l'usure, la protection contre la corrosion et les applications à haute température. |
La poudre de NiCrBSi est-elle facile à appliquer ? | Elle nécessite des équipements spécialisés tels que des pistolets de pulvérisation thermique ou des machines de revêtement par laser, mais elle est relativement simple si l'on dispose de l'équipement adéquat. |
Quelles sont les industries qui utilisent couramment la poudre de NiCrBSi ? | Les industries aérospatiale, automobile, pétrolière et gazière, minière et de production d'énergie utilisent fréquemment la poudre de NiCrBSi. |
Comment le NiCrBSi se compare-t-il aux autres poudres métalliques ? | Le NiCrBSi offre un équilibre entre la résistance à l'usure et à la corrosion et la stabilité à haute température, surpassant certaines poudres dans des conditions difficiles. |
La poudre NiCrBSi peut-elle être utilisée dans des environnements à basse température ? | Alors qu'il excelle dans les applications à haute température, il peut ne pas être aussi efficace à des températures extrêmement basses. |
Quelle est la durée de conservation de la poudre de NiCrBSi ? | Correctement stockée, la poudre de NiCrBSi peut durer plusieurs années, mais il est essentiel de la conserver dans un environnement sec pour éviter l'oxydation. |
Quels sont les principaux avantages des revêtements NiCrBSi ? | Durabilité accrue, réduction des coûts de maintenance et excellente résistance à l'usure et à la corrosion. |
La poudre de NiCrBSi est-elle chère ? | Elle est plus chère que certaines autres poudres métalliques, mais sa durabilité et ses performances la rendent rentable à long terme. |
Conclusion
Poudre de NiCrBSi est un matériau remarquable utilisé dans les revêtements de haute performance pour les industries qui exigent une résistance à l'usure et à la corrosion. Grâce à sa composition unique de nickel, de chrome, de bore et de silicium, il offre durabilité, fiabilité et performance, en particulier dans les environnements difficiles. Que vous cherchiez à prolonger la durée de vie de pièces mécaniques dans le secteur aérospatial ou à améliorer la résistance à l'usure d'outils dans l'industrie minière, la poudre de NiCrBSi est un excellent choix.
De la pulvérisation thermique au revêtement laser, cette poudre polyvalente peut être appliquée de différentes manières, en fonction de vos besoins. Bien que son coût initial soit plus élevé, ses avantages à long terme, tels que l'augmentation de la durée de vie des pièces et la réduction de la maintenance, en font un investissement précieux pour de nombreuses applications industrielles.
La poudre de NiCrBSi continue d'être un choix populaire dans les industries critiques en raison de sa capacité à résister à des conditions extrêmes et de sa rentabilité globale. Que vous soyez un fabricant cherchant à améliorer ses processus ou un ingénieur à la recherche de matériaux fiables pour des applications difficiles, la poudre de NiCrBSi pourrait bien être la solution que vous recherchez.