Vue d'ensemble du dépôt de métal en fusion (MMD)
Dépôt de métal en fusion (MMD) est une technique de fabrication additive de pointe utilisée pour créer des pièces métalliques complexes et performantes. Ce procédé consiste à déposer des couches de métal en fusion pour construire un composant à partir de la base, offrant ainsi une précision et une résistance inégalées. La fabrication additive est particulièrement appréciée dans des secteurs tels que l'aérospatiale, l'automobile et la médecine, où la demande de composants complexes et robustes ne cesse de croître.
Dans ce guide, nous allons nous pencher sur les spécificités du MMD, y compris les types de poudres métalliques utilisées, leurs propriétés, leurs applications, etc. À la fin, vous comprendrez parfaitement pourquoi le MMD révolutionne la fabrication et comment il peut être appliqué à diverses industries.
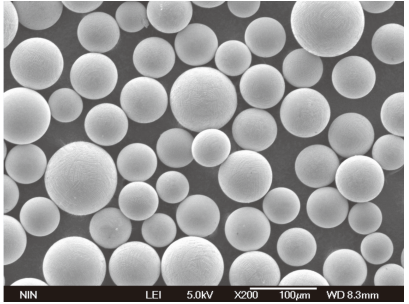
Types de poudres métalliques utilisées en MMD
Il est essentiel de comprendre les différentes poudres métalliques utilisées en MMD pour sélectionner le matériau adéquat pour des applications spécifiques. Vous trouverez ci-dessous un aperçu détaillé de dix modèles de poudres métalliques spécifiques couramment utilisées dans le MMD, ainsi que leurs compositions et caractéristiques.
Modèle de poudre métallique | Composition | Propriétés | Caractéristiques |
---|---|---|---|
Titane Ti-6Al-4V | 90% Titane, 6% Aluminium, 4% Vanadium | Rapport résistance/poids élevé, résistance à la corrosion | Largement utilisé dans l'aérospatiale, biocompatible pour les implants médicaux |
Acier inoxydable 316L | Fer, chrome, nickel, molybdène | Excellente résistance à la corrosion, grande ténacité | Idéal pour les applications marines et médicales |
Aluminium AlSi10Mg | Aluminium, Silicium, Magnésium | Léger, bonnes propriétés thermiques | Convient aux composants automobiles et aérospatiaux |
Inconel 718 | Nickel, chrome, fer, niobium | Résistance aux hautes températures, bonne résistance à l'oxydation | Utilisé dans les turbines à gaz et les moteurs de fusée |
Cobalt-Chrome | Cobalt, chrome | Résistance élevée à l'usure et à la corrosion, biocompatibilité | Fréquent dans les implants dentaires et orthopédiques |
Acier à outils H13 | Fer, chrome, molybdène, vanadium | Dureté et ténacité élevées | Utilisé dans les moules et les matrices pour le moulage par injection de plastique |
Cuivre CuNi2SiCr | Cuivre, nickel, silicium, chrome | Conductivité thermique et électrique élevée | Utilisé dans les composants électriques et les échangeurs de chaleur |
Acier maraging (1.2709) | Fer, nickel, cobalt, molybdène | Très haute résistance, bonne ténacité | Utilisé dans l'outillage et les pièces de haute performance |
Alliage de nickel 625 | Nickel, chrome, molybdène, niobium | Excellente résistance à la corrosion et à l'oxydation | Idéal pour la marine et le traitement chimique |
Bronze CuSn10 | Cuivre, étain | Bonne résistance à l'usure, facile à couler | Utilisé dans les roulements, les coussinets et les sculptures artistiques |
Applications de la Dépôt de métal en fusion (MMD)
La polyvalence du MMD lui permet de s'adapter à un large éventail d'applications. Le tableau ci-dessous résume les diverses applications du MMD dans différents secteurs d'activité.
L'industrie | Applications | Avantages |
---|---|---|
Aérospatiale | Composants du moteur, pièces structurelles | Légèreté, résistance élevée, géométries complexes |
Automobile | Pièces de moteur, composants de châssis | Amélioration des performances, réduction du poids, conceptions personnalisées |
Médical | Implants, instruments chirurgicaux | Biocompatibilité, personnalisation, prototypage rapide |
Marine | Hélices, composants structurels | Résistance à la corrosion, durabilité |
L'énergie | Aubes de turbines, échangeurs de chaleur | Résistance aux hautes températures, efficacité |
Électronique | Connecteurs, dissipateurs thermiques | Conductivité élevée, précision |
Outillage | Moules, matrices | Haute résistance, résistance à l'usure, précision |
Art et bijoux | Sculptures, bijoux sur mesure | Modèles complexes, variété des matériaux |
Équipement industriel | Composants de machines, engrenages | Durabilité, résistance, solutions personnalisées |
La construction | Éléments structurels, fixations | Solidité, résistance à la corrosion, formes complexes |
Spécifications, tailles, qualités et normes
Pour garantir la cohérence et la qualité des MMD, des normes, des tailles et des qualités spécifiques sont respectées. Le tableau ci-dessous présente ces spécifications.
Matériau | Spécifications | Dimensions (mm) | Notes | Normes |
---|---|---|---|---|
Titane Ti-6Al-4V | ASTM B348, AMS 4911 | 1-50 | 5e année | ASTM, AMS, ISO |
Acier inoxydable 316L | ASTM A240, AMS 5507 | 0.5-100 | Grade 316L | ASTM, AMS, ISO |
Aluminium AlSi10Mg | EN 1706, ISO 3522 | 0.5-50 | AlSi10Mg | EN, ISO |
Inconel 718 | AMS 5662, ASTM B637 | 1-50 | UNS N07718 | AMS, ASTM |
Cobalt-Chrome | ASTM F75, ISO 5832-4 | 1-20 | CoCrMo | ASTM, ISO |
Acier à outils H13 | ASTM A681, SAE J437 | 1-100 | H13 | ASTM, SAE |
Cuivre CuNi2SiCr | DIN 17670, ASTM B505 | 0.5-100 | CuNi2SiCr | DIN, ASTM |
Acier maraging (1.2709) | AMS 6514, DIN 1.2709 | 1-50 | Grade 300 | AMS, DIN |
Alliage de nickel 625 | AMS 5599, ASTM B443 | 1-50 | UNS N06625 | AMS, ASTM |
Bronze CuSn10 | ASTM B505, SAE J461 | 1-100 | CuSn10 | ASTM, SAE |
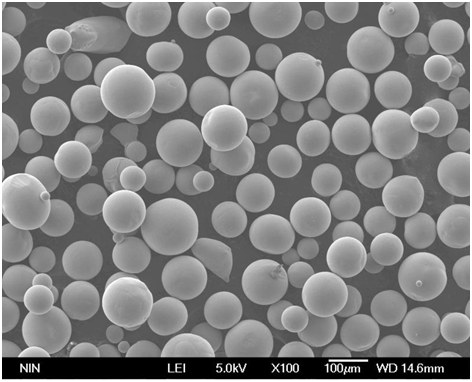
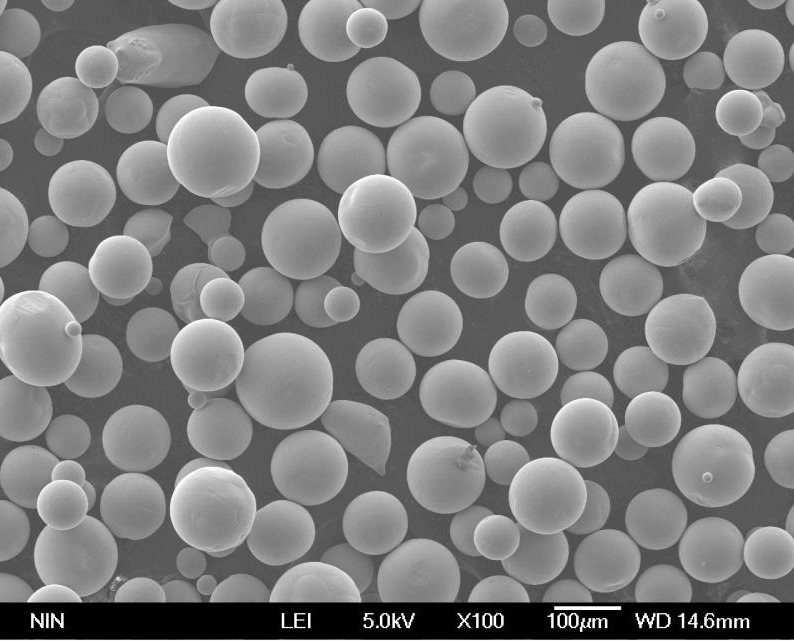
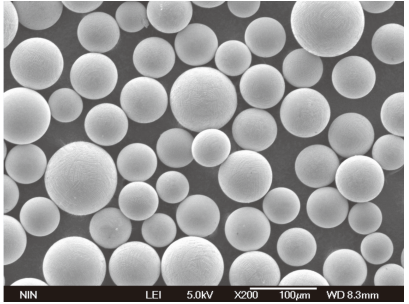
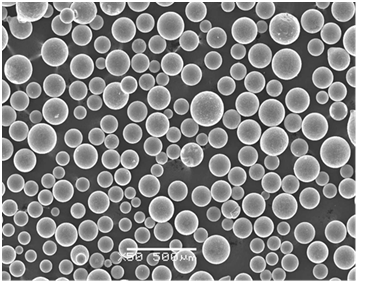
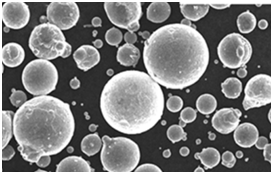
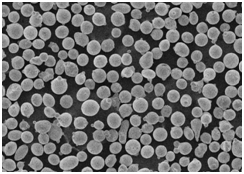
Fournisseurs et détails des prix
Il est essentiel de savoir où s'approvisionner en poudres métalliques et quel est leur coût pour établir un budget et planifier les activités de MMD. Voici un tableau avec des détails sur les fournisseurs et les prix.
Fournisseur | Localisation | Matériaux disponibles | Prix (USD/kg) |
---|---|---|---|
EOS GmbH | Allemagne | Ti-6Al-4V, 316L, AlSi10Mg, Inconel 718 | 150-400 |
Technologie des charpentiers | ÉTATS-UNIS | Cobalt-Chrome, H13, Acier maraging | 200-500 |
Sandvik | Suède | 316L, CuNi2SiCr, Inconel 625 | 100-300 |
AP&C | Canada | Ti-6Al-4V, 316L, AlSi10Mg | 180-350 |
GKN Hoeganaes | ÉTATS-UNIS | Bronze CuSn10, 316L, acier maraging | 120-400 |
Praxair | ÉTATS-UNIS | Ti-6Al-4V, 316L, Inconel 718, CuNi2SiCr | 200-450 |
Hoganas AB | Suède | Aciers inoxydables, aciers à outils, bronzes | 150-400 |
Technologie LPW | ROYAUME-UNI | 316L, AlSi10Mg, Inconel 625 | 180-360 |
Arcam AB | Suède | Ti-6Al-4V, CoCrMo, Inconel 718 | 250-500 |
Systèmes plasma Tekna | Canada | 316L, Ti-6Al-4V, Inconel 718 | 200-450 |
Avantages et limites du MMD
Chaque technologie a ses avantages et ses inconvénients. Voici une comparaison détaillée des avantages et des limites du MMD.
Aspect | Avantages | Limites |
---|---|---|
Précision | Grande précision dans la création de géométries complexes | Nécessite un contrôle et un étalonnage précis |
Propriétés des matériaux | Excellentes propriétés et performances mécaniques | Limité à certains métaux et alliages |
Personnalisation | Modèles hautement personnalisables | La complexité de la conception peut augmenter les coûts et les délais |
Vitesse | Production plus rapide pour les petits et moyens lots | Plus lent pour la production à grande échelle |
Coût | Réduction des déchets de matériaux, rentabilité pour les prototypes | Investissement initial élevé dans l'équipement |
Solidité et durabilité | Production de pièces solides et durables | Certains matériaux peuvent nécessiter un post-traitement |
Durabilité | Déchets minimaux, matériaux recyclables | Processus à forte intensité énergétique |
Polyvalence | Large éventail d'applications dans tous les secteurs d'activité | Ne convient pas à tous les types de composants |
Intégration | Peut être intégré à d'autres processus de fabrication | Requiert des connaissances et des compétences spécialisées |
L'innovation | Permet des conceptions innovantes et un prototypage rapide | Limitée par les avancées technologiques actuelles |
Principales caractéristiques des Dépôt de métal en fusion (MMD)
Examinons les principales caractéristiques du MMD qui en font un processus de fabrication unique et précieux.
Précision et exactitude
L'une des principales caractéristiques du MMD est sa précision. En déposant le métal en fusion couche par couche, le MMD permet d'obtenir des détails complexes que les méthodes traditionnelles risquent d'ignorer. Ce haut niveau de précision est essentiel pour les industries où le moindre écart peut entraîner des problèmes importants, comme dans l'aérospatiale ou les applications médicales.
Polyvalence des matériaux
Le MMD est compatible avec une grande variété de métaux et d'alliages, chacun offrant des propriétés uniques. Qu'il s'agisse du rapport poids/résistance élevé du titane ou de l'excellente résistance à la corrosion de l'acier inoxydable, le MMD peut répondre à divers besoins, ce qui en fait une technique de fabrication très polyvalente.
Solidité et durabilité
Les composants produits par MMD sont réputés pour leur résistance et leur durabilité supérieures. Cela est particulièrement utile dans des secteurs tels que l'automobile et l'aérospatiale, où les pièces sont soumises à des conditions extrêmes et doivent conserver leur intégrité au fil du temps.
Personnalisation et flexibilité
Le MMD permet une personnalisation importante, ce qui permet aux fabricants de produire des pièces adaptées à des exigences spécifiques. Cette flexibilité est inestimable dans les applications où des solutions sur mesure sont nécessaires, telles que les implants médicaux personnalisés ou les composants aérospatiaux spécialisés.
Efficacité et durabilité
Le MMD est un processus efficace qui minimise les déchets, car il n'utilise que les matériaux nécessaires à la création de la pièce. En outre, de nombreux matériaux utilisés dans le cadre du MMD sont recyclables, ce qui contribue à la durabilité du processus de fabrication.
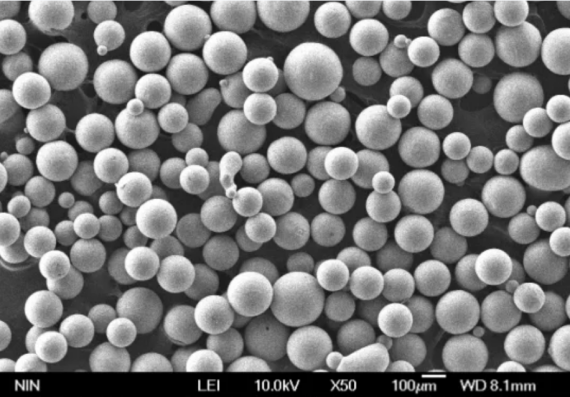
FAQ
Qu'est-ce que le dépôt de métal en fusion (MMD) ?
Q : Qu'est-ce que le dépôt de métal en fusion (MMD) ?
R : Le dépôt de métal en fusion (MMD) est un procédé de fabrication additive qui permet de construire des pièces métalliques couche par couche à l'aide de métal en fusion. Il permet d'obtenir des géométries précises et complexes et des composants très performants.
Comment le MMD se compare-t-il aux autres méthodes de fabrication additive ?
Q : En quoi le MMD diffère-t-il des autres techniques d'impression 3D ?
R : Contrairement à d'autres méthodes de fabrication additive qui peuvent utiliser du plastique ou de la résine, le MMD utilise du métal, ce qui lui confère une résistance et une durabilité supérieures. Elle est particulièrement utile pour les applications nécessitant des pièces métalliques de haute performance.
Quels sont les matériaux qui peuvent être utilisés dans le cadre du MMD ?
Q : Quels sont les types de métaux et d'alliages couramment utilisés dans les MMD ?
R : Les métaux couramment utilisés dans les MMD comprennent le titane Ti-6Al-4V, l'acier inoxydable 316L, l'aluminium AlSi10Mg, l'Inconel 718 et le cobalt-chrome, entre autres. Chaque matériau offre des propriétés uniques adaptées à différentes applications.
Quels sont les avantages de l'utilisation du MMD ?
Q : Pourquoi devrais-je envisager d'utiliser MMD pour la fabrication ?
R : Le MMD offre une grande précision, d'excellentes propriétés matérielles, une personnalisation, une efficacité et une durabilité. Il est particulièrement intéressant pour la production de pièces complexes et de haute performance.
Y a-t-il des limites au MMD ?
Q : Quels sont les inconvénients ou les limites du MMD ?
R : Bien que la technique MMD soit très polyvalente et précise, elle peut être coûteuse à mettre en place et nécessite des connaissances spécialisées. En outre, elle peut ne pas convenir à tous les types de composants et certains matériaux peuvent nécessiter un post-traitement.
Comment puis-je commencer à travailler avec MMD ?
Q : De quoi ai-je besoin pour commencer à utiliser MMD pour mes projets ?
R : Pour commencer avec le MMD, vous devez avoir accès à une machine MMD, aux poudres métalliques appropriées et connaître le processus. Un partenariat avec des fournisseurs et des fabricants expérimentés peut également contribuer à rationaliser l'adoption du MMD.
Où puis-je me procurer des poudres métalliques pour le MMD ?
Q : Où puis-je acheter des poudres métalliques pour le MMD et quels sont les éléments à prendre en compte ?
R : Les poudres métalliques pour MMD peuvent être obtenues auprès de fournisseurs tels que EOS GmbH, Carpenter Technology et Sandvik. Tenez compte de facteurs tels que les propriétés du matériau, le coût et la fiabilité du fournisseur lorsque vous faites votre choix.