Le moulage par injection de métal (MIM) est un procédé d'usinage des métaux utilisé pour fabriquer de petites pièces complexes à partir de poudre de métal et de plastique. Le MIM combine la souplesse de conception du moulage par injection de plastique avec la résistance et l'intégrité des métaux usinés. Il permet la fabrication rentable de composants dont les dimensions varient de 1 à 500 grammes.
Les Processus MIM produit des pièces présentant d'excellentes propriétés mécaniques, des tolérances de précision et des finitions de surface lisses. Le MIM convient donc à la fabrication de petits composants métalliques complexes de forme nette en grandes quantités pour des industries telles que l'automobile, le médical, l'aérospatiale, l'électronique, etc.
Ce guide offre une vue d'ensemble complète du processus MIM, de ses applications, de ses avantages, des considérations de conception, de l'équipement, des matériaux, du post-traitement, du contrôle de la qualité et de l'analyse des coûts. Il comprend des tableaux détaillés et des comparaisons pour aider les ingénieurs, les concepteurs de produits et les responsables des achats à se familiariser avec le procédé MIM et à l'évaluer.
Aperçu du processus MIM
Le moulage par injection de métal combine les techniques de moulage par injection de plastique et les procédés de métallurgie des poudres. Les étapes de base du processus MIM sont les suivantes :
- Mixage : Mélange d'une fine poudre métallique avec un liant plastique pour créer un produit de départ homogène
- Moulage par injection : Chauffer et injecter la matière première dans un moule pour former une pièce verte façonnée
- Débouclage : Élimination du liant plastique de la pièce verte moulée au moyen de solvants ou de procédés thermiques
- Frittage : Chauffer la pièce débobinée juste en dessous du point de fusion de la poudre pour densifier la pièce par diffusion atomique et former une pièce métallique solide.
Le tableau suivant résume les principales étapes du processus de MIM :
Stage | Description |
---|---|
Mélange | Mélange d'une fine poudre métallique avec des liants dans un produit de départ homogène |
Moulage par injection | Chauffer et injecter la matière première dans un moule pour former une pièce verte |
Débouclage | Élimination du liant par solvant ou par procédé thermique |
Frittage | Chauffage de la pièce ébarbée pour densifier la poudre et former la pièce métallique |
Le procédé MIM permet de produire des composants métalliques cohérents et de haute qualité, adaptés à la fabrication en grande série. Le processus est hautement reproductible et permet de créer des géométries complexes avec des tolérances étroites qui ne sont pas possibles avec d'autres techniques de fabrication.
Applications et utilisation industrielle des pièces MIM
Le MIM est utilisé dans de nombreuses industries pour fabriquer de petits composants métalliques complexes de forme nette avec des tolérances serrées.
Le tableau suivant présente les principaux domaines d'application et des exemples de pièces fabriquées par MIM :
L'industrie | Exemples d'applications |
---|---|
Automobile | Engrenages, pignons, culbuteurs, bielles |
Aérospatiale | Aubes de turbines, roues, buses, valves |
Médical | Brackets orthodontiques, instruments chirurgicaux, implants |
Électronique | Connecteurs, micro-barrettes, écrans, buses d'imprimantes |
Armes à feu | Détentes, marteaux, sécurités, éjecteurs |
Montres | Engrenages, pignons, aiguilles de montres |
Le MIM permet de produire de petites pièces de précision aux géométries complexes qui nécessiteraient autrement un usinage important ou d'autres opérations secondaires. Il offre une liberté de conception, une consolidation des pièces et une réduction du poids par rapport à d'autres solutions de fabrication.
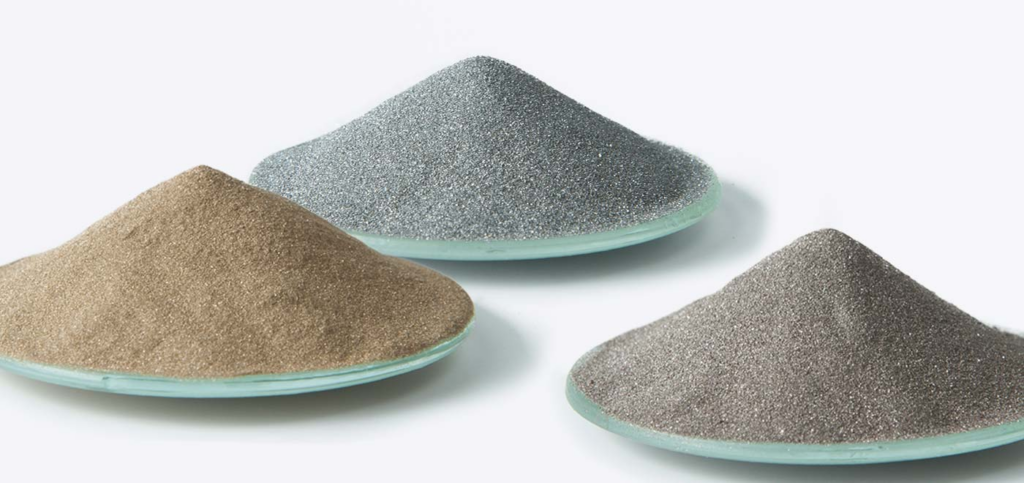
Avantages et bénéfices du MIM
Le MIM présente plusieurs avantages par rapport aux autres procédés de fabrication de petites pièces métalliques :
Liberté de conception
- Il est possible de mouler des géométries et des formes complexes en 3D, ce qui est difficile, voire impossible, avec d'autres méthodes.
- Des caractéristiques complexes telles que des filets, des cavités et des trous peuvent être facilement incorporées dans les conceptions MIM.
- Permet la consolidation des pièces et la réduction des assemblages par rapport à l'usinage de plusieurs composants.
Précision et tolérances
- Le MIM permet d'obtenir une précision dimensionnelle constante et des tolérances allant jusqu'à ±0,1 %.
- Il est possible de réaliser des détails fins avec de bons états de surface jusqu'à 0,5 μm Ra.
Propriétés des matériaux
- Les pièces frittées en MIM atteignent généralement 95 à 99 % de la densité des métaux corroyés.
- Une large gamme de matériaux tels que l'acier inoxydable, l'acier à outils, les alliages de titane et les alliages de tungstène peuvent être utilisés.
- Excellentes propriétés mécaniques avec la rigidité, la solidité, la dureté et la résistance à l'usure des métaux moulés.
Productivité et coûts
- Des taux de production élevés sont possibles avec des temps de cycle rapides grâce au MIM.
- Coût des pièces inférieur à celui de l'usinage CNC pour les volumes moyens et élevés.
- Coûts inférieurs à ceux du moulage à la cire perdue pour les conceptions complexes à plusieurs composants.
- Élimine les opérations d'usinage secondaires nécessaires pour les pièces métalliques fabriquées.
Durabilité
- Déchets de matériaux minimes puisque le MIM utilise un traitement proche de la forme d'un filet.
- Le procédé de métallurgie des poudres consomme moins d'énergie que l'usinage ou le moulage des métaux.
- Permet d'alléger le poids en optimisant les géométries, ce qui réduit l'empreinte écologique.
Le tableau suivant résume les principaux avantages de la MIM et la compare à d'autres procédés :
Avantage | Comparaison avec d'autres processus |
---|---|
Liberté de conception | Plus de flexibilité que l'usinage ou le moulage des métaux |
Précision | Beaucoup plus élevé que le moulage en sable ou le moulage sous pression |
Propriétés des matériaux | Approche des métaux corroyés différente de la métallurgie des poudres |
Productivité | Volumes plus importants que ceux de l'usinage CNC |
Rapport coût-efficacité | Coûts inférieurs à ceux de l'usinage CNC ou du moulage à la cire perdue pour les volumes moyens et supérieurs |
Durabilité | Moins de déchets que les procédés soustractifs tels que l'usinage CNC |
Le MIM associe la liberté géométrique du moulage par injection plastique aux propriétés des matériaux proches de celles des métaux entièrement denses. Cela permet aux concepteurs de produits de consolider les assemblages, d'optimiser les composants et de fabriquer des pièces métalliques complexes et de grande valeur à des coûts compétitifs.
Considérations relatives à la conception des pièces MIM
Une bonne conception des pièces est essentielle pour maximiser les avantages du processus MIM. Voici quelques-unes des principales considérations en matière de conception :
Epaisseurs des parois – ; Des épaisseurs de paroi modérées comprises entre 0,8 mm et 5 mm sont recommandées. Des sections trop épaisses ou trop fines peuvent entraîner des défauts.
Tolérances - Des tolérances de précision de ±0,1 % des dimensions sont possibles, mais il faut tenir compte du retrait du frittage.
Finitions de surface - Des états de surface fins inférieurs à 1 μm Ra sont possibles en fonction de la surface de l'outil, des géométries et des opérations de post-moulage.
Géométrie – ; Il est important d'éviter les géométries trop délicates et de maintenir l'intégrité structurelle pour prévenir les défauts. Les angles de dépouille minimaux supérieurs à 1-2° sont préférables.
Caractéristiques - Des trous d'un diamètre allant jusqu'à 0,5 mm, des filetages et des caractéristiques internes complexes peuvent être incorporés dans la conception MIM.
Taille de la pièce - Les petites pièces de 0,5 à 500 grammes sont idéales pour le traitement MIM. Les pièces plus grandes peuvent nécessiter un usinage CNC.
Assembly - Concevoir pour la consolidation des pièces en combinant des composants et des assemblages complexes en pièces uniques MIM.
Une bonne conception des composants MIM permet d'optimiser la fabricabilité, de minimiser les défauts et de tirer parti des principaux avantages du processus MIM. Il est fortement recommandé de consulter les fournisseurs de MIM pendant la phase de conception.
Équipement et outillage pour le MIM
Des équipements spécialisés sont utilisés pour la préparation des matières premières, le moulage, le déliantage et le frittage dans le cadre du processus MIM :
Mélange et préparation des matières premières
- Mélangeurs – ; Mélangeurs à haute intensité pour l'homogénéité des matières premières
- Broyeurs – ; Broyeurs à panier ou à cylindres pour la réduction de la taille des particules fines
- Régulateurs de température – ; Pour réguler les températures des matières premières
- Dégazage – ; Unités de vide pour éliminer les bulles d'air piégées
Moulage par injection
- Machines de moulage par injection – ; Machines modifiées pour traiter les matières premières MIM
- Moules – ; Généralement fabriqués en acier à outils/acier inoxydable traité thermiquement pour résister au frittage
- Contrôles de la température des moules – ; Pour réguler les températures des moules pendant le moulage
Débouclage
- Chambres de déliantage à solvant – ; Pour l'extraction de liants par solvant
- Autoclaves de déliantage à la vapeur – ; Pour les processus de déliantage à la vapeur
- Fours de déliantage thermique – ; Pour l'élimination des liants par des procédés thermiques
Frittage
- Fours de frittage – ; Fours à vide, à hydrogène ou à azote
- Systèmes de contrôle de l'atmosphère – ; Pour réguler l'atmosphère des fours
- Commandes de profilage de la température – ; pour l'exécution de cycles de frittage optimisés
Une configuration et un étalonnage corrects de l'équipement de MIM sont essentiels pour obtenir des composants de haute qualité et exempts de défauts. L'étape du moulage par injection requiert l'équipement le plus spécialisé, comme les moules à haute température.
Matériaux MIM
Un large éventail de métaux, d'alliages et de céramiques peuvent être traités à l'aide de la technologie MIM. Voici quelques-uns des matériaux MIM les plus courants :
Métaux
- Aciers inoxydables (316L, 17-4PH, 410)
- Aciers à outils (H13, P20, D2)
- Aciers faiblement alliés (4140)
- Alliages magnétiques
- Alliages de cuivre
- Alliages de titane
- Alliages lourds de tungstène
Céramique
- Alumine
- Zircone
- Nitrure de silicium
- Carbures
Le choix du matériau dépend de facteurs tels que les températures de frittage, le coût, les propriétés mécaniques et physiques et les besoins de traitement secondaire. L'acier inoxydable 316L est le matériau MIM le plus courant en raison de son excellente aptitude au frittage.
Le tableau ci-dessous présente les matériaux MIM les plus courants et leurs applications typiques :
Matériau | Applications |
---|---|
Acier inoxydable 316L | Instruments chirurgicaux, pompes, valves |
Arbre de l'outil H13 | Moulage par injection, extrusion, filières |
Titane Ti-6Al-4V | Aérospatiale, implants médicaux |
Alliages lourds de tungstène | Protection contre les rayonnements, amortissement des vibrations |
Alliages de cuivre | Contacts électriques, gestion thermique |
Céramique | Outils de coupe, pièces d'usure, balistique |
Le MIM permet d'utiliser des matériaux de haute performance tels que le titane et les alliages d'acier à outils dans la conception de petits composants complexes. Il élargit les possibilités de conception pour les applications médicales, aérospatiales, automobiles et industrielles.
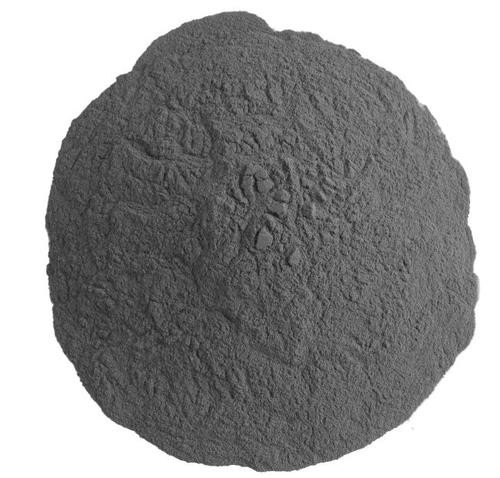
Opérations de post-traitement
Des étapes de traitement secondaire sont souvent nécessaires après le frittage du MIM pour obtenir la pièce finale :
- Recuit – ; Traitement thermique de détente
- Durcissement – ; Processus de durcissement thermique comme l'austempering
- Usinage – ; Caractéristiques d'usinage CNC telles que la précision des diamètres d'alésage
- Adhésion – ; Soudage au laser, brasage ou collage époxy de sous-composants
- Finition – ; Placage, peinture, passivation ou autre finition de surface
Le tableau ci-dessous présente les processus post-MIM les plus courants et leurs objectifs :
Post-Process | Objectif |
---|---|
Recuit | Réduction des contraintes, ductilité |
Durcissement | Amélioration de la dureté et de la résistance |
Usinage | Dimensions et ajustements critiques |
Adhésion | Assemblage de produits en plusieurs parties |
Finition | Aspect, résistance à la corrosion |
Le post-traitement élargit les possibilités d'amélioration des propriétés et d'usinage de précision. Cela élargit encore les possibilités d'utilisation du MIM dans des applications exigeantes.
Contrôle de la qualité et inspection
Une qualité constante et un contrôle dimensionnel sont essentiels pour les composants MIM. Les tests typiques de contrôle de la qualité sont les suivants
- Analyse chimique – ; Pour la composition en utilisant la spectroscopie d'émission optique ou de fluorescence des rayons X
- Mesures de densité – ; méthode d'Archimède ou pycnométrie à gaz pour déterminer la densité du fritté
- Essais mécaniques – ; dureté, résistance à la traction et à la fatigue selon les normes ASTM
- Microscopie – ; pour l'analyse de la microstructure, de la porosité, de la taille des grains et des défauts
- Analyse dimensionnelle – ; Scanner optique ou tomodensitométrique pour les dimensions et la conformité GD&T
- Analyse de surface – ; tests de rugosité, de corrosion et de revêtement, le cas échéant
Le tableau suivant présente les principaux tests de qualité effectués à différents stades de la transformation du MIM :
Stage | Tests de qualité typiques |
---|---|
Matières premières | Viscosité, couple, humidité |
Partie verte | Dimensions, inspection des défauts |
Débouclage | Perte de poids, résidus |
Frittage | Densité, essais chimiques |
Finition | Dimensions, microscopie, propriétés mécaniques |
Un contrôle de qualité et une inspection complets à toutes les étapes du MIM sont nécessaires pour obtenir des composants sans défaut répondant aux exigences de l'application.
Analyse des coûts
Les facteurs suivants déterminent l'économie du processus MIM :
- Outillage - Les coûts initiaux de l'outillage sont élevés en fonction de la géométrie des pièces. Les cavités multiples dans les outils permettent de répartir les coûts sur des volumes plus importants.
- Mise en place - Coûts initiaux importants de réglage des machines et de mise au point des procédés.
- Matériau – ; Les poudres métalliques représentent 10 à 15 % du coût total de la pièce. Ce pourcentage est élevé pour les matériaux coûteux tels que les alliages de titane.
- Travail - Une certaine main-d'œuvre qualifiée est nécessaire, mais elle est moins importante que pour l'usinage CNC. Plus faible pour les volumes importants.
- Transformation secondaire - Peut augmenter considérablement les coûts si un usinage ou une finition importants sont nécessaires.
- Volume Idéal pour les volumes de production moyens à élevés, de 10 000 à des millions de pièces. Offre un avantage optimal en termes de coûts par rapport à d'autres procédés dans cette gamme.
Le tableau suivant présente des facteurs de coût indicatifs pour la fabrication de MIM :
Élément de coût de la MIM | Détails |
---|---|
Outillage | De 5 000 à 100 000 dollars, en fonction de la complexité de la pièce |
Mise en place | 10 000 à 50 000 dollars pour le développement de processus |
Matériaux | 10-15% du coût de la pièce, plus élevé pour les alliages coûteux |
Travail | Contribution inférieure à celle de l'usinage CNC |
Transformation secondaire | 2 à 20 dollars par pièce en fonction des opérations |
Volume | Idéal pour plus de 10 000 pièces, moins coûteux que les autres solutions |
Le MIM offre un avantage de coût par rapport à l'usinage et au moulage pour les volumes de production moyens à élevés, à condition que le traitement secondaire soit minimal. Le processus offre les avantages économiques les plus importants pour les conceptions complexes à plusieurs composants regroupés en une seule pièce MIM.
Choisir un fournisseur ou un partenaire MIM
Le choix d'un fournisseur de MIM compétent est la clé d'une production rentable de composants de haute qualité. Voici quelques critères d'évaluation des fournisseurs de MIM :
- Expérience – ; Nombre d'années d'activité et expertise en matière de MIM. Les acteurs de longue date ont tendance à être plus fiables.
- Matériaux -Diversité des matériaux proposés, y compris les principaux alliages nécessaires. Les capacités des nanopoudres améliorent les propriétés.
- Qualité - Programme de qualité solide et certifications telles que ISO 9001 et ISO 13485. Preuve du contrôle des processus.
- Capacités d'outillage - L'offre d'un outillage complet en interne permet une meilleure intégration des coûts et réduit les problèmes.
- Transformation secondaire - La disponibilité de processus complémentaires tels que l'usinage et la finition CNC améliore la commodité.
- Prototypage – ; La capacité de prototypage rapide en MIM réduit les délais et les coûts.
- Compétence en matière de recherche et de développement - Forte expertise en matière de recherche et d'ingénierie pour l'innovation des processus.
Le choix d'un fournisseur établi disposant de vastes capacités internes offre une solution solide et transparente pour les projets MIM complexes. La proximité géographique permet également d'améliorer la collaboration et la communication.
Le MIM comparé à d'autres procédés
MIM et usinage CNC
- Coût - Le MIM est moins coûteux pour les volumes moyens et élevés, le CNC est rentable pour les faibles volumes.
- Conception - Une plus grande complexité et un meilleur potentiel de consolidation avec le MIM
- Matériaux - Le MIM permet d'élargir la gamme des matériaux, y compris les aciers à outils et les alliages de titane.
- Vitesse - Des taux de production plus élevés avec le MIM, des temps de cycle plus lents pour l'usinage CNC
- Gaspillage - Forme nette proche Le MIM permet de réduire les pertes de matière par rapport à l'usinage CNC.
MIM et moulage des métaux
- Résolution - Une résolution plus élevée et des détails plus fins sont possibles avec le MIM
- Complexité - Complexité géométrique accrue grâce au MIM
- Tolérances - Tolérances dimensionnelles beaucoup plus étroites grâce au MIM
- Cohérence - Propriétés et performances des matériaux plus cohérentes grâce au MIM
- Usinage secondaire - L'usinage secondaire nécessaire pour les pièces MIM est généralement moins important.
MIM et impression 3D
- Coût – ; Le MIM est actuellement moins coûteux pour la production de volumes moyens et supérieurs
- Matériaux – ; Plus large gamme d'alliages à hautes performances, tels que les aciers à outils, disponibles dans le MIM
- Tolérances – ; Tolérances dimensionnelles plus précises possibles avec le MIM
- Propriétés mécaniques – ; Propriétés généralement meilleures et plus cohérentes que celles des métaux imprimés en 3D
- Qualification – ; Contrairement à l'impression 3D, le procédé MIM est déjà qualifié pour les applications aérospatiales et médicales
Le MIM offre des avantages en termes de complexité, de cohérence et de coût par rapport à d'autres procédés de fabrication métallique pour les petites pièces de haute précision fabriquées à des volumes moyens ou supérieurs.
Limites et défis de la MIM
Les principales limites et les principaux inconvénients du processus MIM sont les suivants :
- Les coûts élevés d'investissement initial dans l'outillage dissuadent de produire des séries courtes
- Capacité de taille limitée, pas idéal pour les pièces de plus de 500 grammes
- Géométrie restreinte en raison de la nécessité d'ébavurer et de fritter les composants
- Il est difficile d'obtenir des tolérances très serrées inférieures à ±0,5 %.
- Non recommandé pour les alliages exotiques difficiles à fritter.
- Un usinage secondaire peut être nécessaire pour obtenir des ajustements et des dimensions critiques.
- Une grande expertise des processus est nécessaire pour la prévention des défauts pendant le moulage.
- Les coûts d'équipement des machines de MIM peuvent être considérables
Pour surmonter les limites du MIM, il faut faire des compromis au niveau de la conception, des exigences de tolérance et des besoins de traitement secondaire. Le processus est plus adapté aux petits composants complexes et de haute précision qu'aux géométries de base ou de très grande taille.
Développements de la technologie MIM
Les développements récents de la technologie MIM qui augmentent les capacités et l'adoption sont les suivants :
- Matières premières des nanopoudres - Amélioration de la résistance et de la microstructure du fritté
- Outillage rapide – ; Réduction des coûts et des délais de fabrication des moules grâce aux inserts imprimés en 3D
- Jetting de liant - Permettre l'impression puis le frittage dans l'impression 3D de métaux
- MIM du titane – ; Développement de composants en titane rentables
- Injection à basse pression - Pour des pièces MIM plus grandes avec des contraintes d'outillage réduites
- MIM de la céramique - Élargissement aux céramiques techniques/structurelles au-delà de l'alumine
- Intégration de l'industrie 4.0 - Automatisation et optimisation du contrôle de la qualité
L'innovation permanente dans le processus MIM permet de remédier aux limitations, d'élargir les capacités des matériaux et d'étendre les applications à de nouvelles industries. Cela permet au MIM d'être compétitif en tant que technologie de fabrication de composants métalliques de précision.
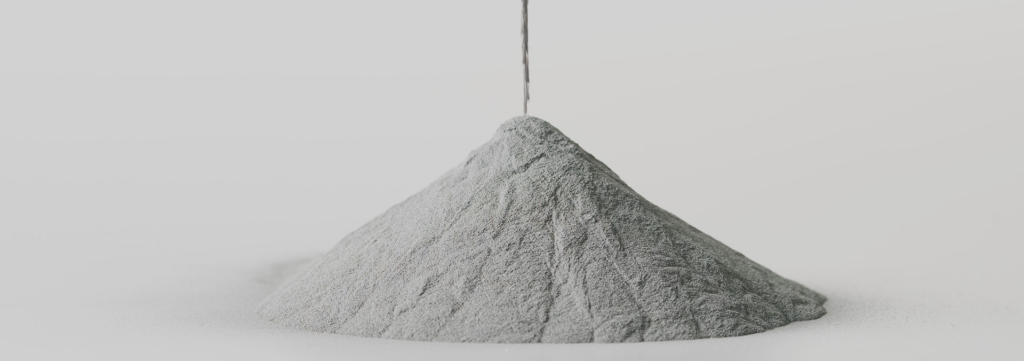
FAQ
Voici les réponses aux questions les plus fréquemment posées sur le processus de moulage par injection de métal :
Q : Quels types de métaux peuvent être utilisés dans le MIM ?
R : La technologie MIM permet de traiter une large gamme de métaux et d'alliages, notamment les aciers inoxydables, les aciers à outils, les alliages magnétiques, les alliages de titane, les alliages lourds de tungstène et les alliages de cuivre. Les matériaux courants sont l'acier inoxydable 316L et 17-4PH, l'acier à outils H13 et le titane Ti-6Al-4V.
Q : Quelles sont les dimensions des composants qui peuvent être fabriqués par MIM ?
R : La taille idéale pour le MIM se situe entre 0,5 et 500 grammes. Il est possible d'obtenir des pièces plus petites ou plus grandes, mais cela n'est pas forcément rentable. Les pièces miniatures de moins de 0,5 gramme peuvent poser des problèmes de manipulation et de traitement secondaire. Les pièces plus grandes, au-dessus de 500 grammes, nécessitent des contraintes d'outillage plus importantes et des temps de cycle plus longs.
Q : Quelles sont les précisions et les tolérances dimensionnelles possibles avec le MIM ?
R : Le MIM permet d'obtenir de très bonnes tolérances dimensionnelles jusqu'à ±0,1 % des dimensions. Toutefois, les tolérances de ±0,5 % sont plus courantes pour les composants à tolérance moyenne. Les tolérances inférieures à ±0,005 pouce (+/- 0,127 mm) nécessitent un usinage secondaire. Des tolérances doivent être prévues pour le retrait de frittage.
Q : Quelle est la différence entre le MIM et le moulage par injection de plastique ?
R : Le procédé MIM est basé sur le moulage par injection de plastique, mais il utilise des poudres métalliques plutôt que des résines plastiques. Le MIM permet de produire des composants métalliques complexes et très résistants en utilisant ce procédé de moulage par injection adapté avec une étape supplémentaire de frittage.
Q : Quelles sont les finitions de surface qui peuvent être produites dans les pièces MIM ?
R : Le MIM est capable de produire des finitions de surface fines jusqu'à 0,5 micron Ra, comparables aux surfaces usinées. Des facteurs tels que le système de liant, la finition de l'outil de moulage, la géométrie et le traitement secondaire déterminent la rugosité de surface finale réalisable.
Q : Quels types de géométries complexes le MIM peut-il fabriquer ?
R : Les géométries complexes avec des parois minces, des angles de dépouille négatifs, des contre-dépouilles, des cavités aveugles et des formes non conventionnelles peuvent être facilement moulées avec le MIM, car le mélange poudre-liant s'écoule comme un liquide dans le moule.
Q : Le MIM est-il adapté à la fabrication de pièces prototypes ?
R : Le MIM n'est pas idéal pour le prototypage en raison des coûts d'outillage et des délais élevés qu'il implique. D'autres procédés tels que l'usinage CNC, l'impression 3D ou le moulage par injection d'aluminium sont mieux adaptés aux prototypes de faible volume avant de s'engager dans l'outillage MIM.
en savoir plus sur les procédés d'impression 3D
Frequently Asked Questions (Supplemental)
1) What feedstock solids loading is optimal in the MIM Process?
- Typically 58–64 vol% metal powder in the binder. Higher loading reduces shrinkage and distortion but increases viscosity; tune via capillary rheometry.
2) How do I control shrinkage and dimensional scatter in sintering?
- Use consistent PSD (D50 ≈ 12–20 μm), spherical morphology, tight O/N/H limits, uniform debind, and sinter setters/fixtures. Apply SPC on green density and use master shrinkage curves per alloy.
3) Can MIM achieve medical and aerospace qualifications?
- Yes. Implement ISO 13485 or AS9100 QMS, material traceability, validated debind/sinter cycles, and biocompatibility testing (ISO 10993) for relevant alloys; report properties per ASTM F2885 and F3122.
4) When is HIP recommended for MIM parts?
- For fatigue‑critical, leak‑tight, or thick‑section components (e.g., 17‑4PH, Ti‑6Al‑4V). HIP raises density to ≥99.7%, reducing internal porosity; follow with appropriate aging/anneal.
5) What are common root causes of MIM defects and how to mitigate?
- Jetting/short shots: adjust gate, viscosity, mold temps. Blisters/cracks: incomplete debind—extend solvent or thermal stage. Warpage: unbalanced cooling or nonuniform green density—optimize tooling, packing, and fixtures.
2025 Industry Trends and Data
- Digital powder passports: Chemistry, PSD, O/N/H, apparent/tap density, and lot history are now standard in RFQs, reducing incoming variability.
- Micro‑MIM growth: Wearables and micro‑mechanisms drive use of ultra‑fine powders (D50 5–10 μm) with low‑viscosity binders and precision tooling vents.
- Sustainability focus: Solvent recovery loops, lower‑energy sintering profiles, and recycled powder content disclosures (15–30%) gain traction.
- In‑process analytics: Cavity pressure/temperature sensors and inline viscosity checks cut scrap by double digits.
- Hybrid routes: Print‑then‑sinter (binder jet) and MIM share furnaces/inspection cells for mixed‑technology factories.
KPI (MIM Process Performance), 2025 | 2023 Baseline | 2025 Typical/Target | Why it matters | Sources/Notes |
---|---|---|---|---|
Solids loading (vol%) | 56–62 | 58–64 | Shrinkage control, strength | Vendor guides; rheometry |
Hausner ratio (–) | 1.22–1.28 | 1.12–1.20 | Flow stability | ASTM B212/B213 |
Oxygen in 316L MIM powder (wt%) | 0.25–0.45 | 0.15–0.30 | Corrosion, density | ASTM E1019 |
Green density Cpk | 1.1–1.3 | ≥1.5 | Dimensional capability | Plant SPC |
Post‑HIP density (%) | 99.5–99.7 | 99.7–99.9 | Fatigue/leak‑tightness | OEM data |
Scrap reduction with cavity sensing | - | 10–20% | Yield improvement | Vendor app notes |
Recycled content disclosed (%) | Limitée | 15–30 | ESG, cost | EPD/LCA reports |
Standards and references:
- ASTM F2885 (MIM components), ASTM B212/B213/B214/B822 (density/flow/PSD), ASTM E1019 (O/N/H), ASTM F3122 (mechanical property reporting): https://www.astm.org
- ISO 22068 (MIM powders/components), ISO 13485 (medical QMS): https://www.iso.org
- EPMA MIM Guide and Design for MIM: https://www.epma.com
- ASM Handbook, Powder Metallurgy and MIM: https://dl.asminternational.org
Latest Research Cases
Case Study 1: Micro‑MIM 17‑4PH Latching Mechanism with Cavity Pressure Control (2025)
- Background: A wearable OEM required sub‑2 mm latches with tight tolerances and high fatigue strength.
- Solution: Spherical 17‑4PH powder (D50 ≈ 9 μm, O = 0.18 wt%); low‑viscosity binder; multi‑cavity mold with cavity pressure sensors; two‑step debind; vacuum sinter + H900 aging; optional HIP.
- Results: Post‑HIP density 99.85%; dimensional Cpk 1.7 on critical features; fatigue life +28% vs. 2023 baseline; scrap −19%.
Case Study 2: Solvent‑Recovery Debind and Low‑Energy Sintering of 316L MIM Surgical Components (2024)
- Background: A medical supplier targeted ESG goals while maintaining corrosion resistance.
- Solution: Closed‑loop solvent debind with >95% solvent recovery; optimized ramp‑hold sintering profile in H2 to limit grain growth; passivation per ASTM A967.
- Results: Energy use −14% per kg; density 98.8–99.2%; pitting potential improved 10% vs. prior cycle; annual solvent purchases −60%.
Expert Opinions
- Prof. Randall M. German, Powder Metallurgy Scholar and Author
- Viewpoint: “In the MIM Process, packing—set by powder PSD and solids loading—drives shrinkage predictability more than marginal sintering tweaks.”
- Dr. Martina Zimmermann, Head of Additive Materials, Fraunhofer IWM
- Viewpoint: “Lot‑level powder passports and in‑mold sensing are now essential for regulated sectors, cutting qualification time and scrap.”
- Dr. Paul J. Davies, EPMA MIM Expert Group
- Viewpoint: “Micro‑MIM success hinges on ultra‑fine powders with tight oxygen control and tooling vent design to prevent binder‑rich defects.”
Affiliation links:
- Fraunhofer IWM: https://www.iwm.fraunhofer.de
- EPMA: https://www.epma.com
- ASM International: https://www.asminternational.org
Practical Tools/Resources
- QC/Standards: ASTM F2885, ISO 22068, ASTM B212/B213/B214/B822, ASTM E1019
- Metrology: LECO inert‑gas fusion (https://www.leco.com); laser diffraction PSD; helium pycnometry (ASTM B923); CT for internal defects; surface profilometry
- Process control: Capillary rheometers; cavity pressure/temperature sensors; SPC templates for shrinkage and dimensions
- Design: EPMA Design for MIM guide; MPIF standards (https://www.mpif.org); ASM Handbook MIM chapters
- Costing/DFM: aPriori for MIM cost models; vendor DFM checklists for gate/runner, venting, and ejection
Last updated: 2025-08-22
Changelog: Added 5 supplemental FAQs; inserted 2025 KPI table and trend notes; included two case studies (micro‑MIM 17‑4PH latch; ESG‑focused 316L flow); added expert viewpoints with affiliations; compiled standards, metrology, process control, and design resources for the MIM Process.
Next review date & triggers: 2026-02-01 or earlier if ASTM/ISO standards update, major suppliers change O/N/H or PSD specs, or new datasets on micro‑MIM capability and solvent‑recovery debinding are published.