atomisation du gaz est un procédé de métallurgie des poudres utilisé pour produire de fines poudres métalliques. Il consiste à faire fondre un alliage métallique et à désintégrer la matière fondue en fines gouttelettes à l'aide d'un jet de gaz à grande vitesse. Les gouttelettes se solidifient rapidement en poudres à la morphologie sphérique et à la distribution granulométrique contrôlée. Les poudres atomisées ont des propriétés uniques qui les rendent adaptées à des applications spécialisées dans diverses industries.
Comment fonctionne l'atomisation des gaz ?
Le processus d'atomisation au gaz commence par la fusion de l'alliage souhaité dans un creuset ou un four à induction. Le métal liquide est ensuite versé en un mince filet dans la chambre d'atomisation. Des jets de gaz à haute pression (généralement de l'azote ou de l'argon) placés autour du flux de métal le désintègrent en fines gouttelettes. Lorsque les gouttelettes tombent dans la tour d'atomisation, elles se solidifient rapidement en poudres sphériques en raison du rapport élevé entre la surface et le volume. Les poudres sont recueillies au bas de la tour et classées en fonction de la taille des particules à l'aide de tamis.
La taille des poudres produites dépend des débits de gaz et de métal. Des pressions de gaz plus élevées et des débits de métal plus faibles donnent des poudres plus fines. D'autres paramètres du procédé, tels que l'angle d'injection du gaz et la conception de la buse d'atomisation, affectent également les caractéristiques des poudres.
Quels sont les avantages des poudres atomisées au gaz ?
Par rapport aux poudres fabriquées par d'autres méthodes telles que l'atomisation à l'eau, les poudres atomisées au gaz présentent les avantages suivants :
- Morphologie des particules hautement sphériques
- Distribution granulométrique serrée
- Faible absorption d'oxygène et d'azote lors de l'atomisation
- Capacité à atomiser des alliages à haute température de fusion
- Flexibilité pour modifier les paramètres du processus et personnaliser les caractéristiques de la poudre
La forme sphérique améliore l'écoulement de la poudre et la densité de l'emballage. La distribution contrôlée de la taille des particules permet un contrôle précis des propriétés finales de la pièce. L'atmosphère d'atomisation inerte empêche la contamination des alliages chimiques réactifs. Ces avantages permettent aux poudres atomisées au gaz de répondre aux exigences des procédés avancés d'AM métal comme la fusion laser sur lit de poudre et le jet de liant. Leur grande pureté les rend également adaptées aux applications de métallurgie des poudres telles que le moulage par injection de métaux, où la contamination peut dégrader les propriétés.
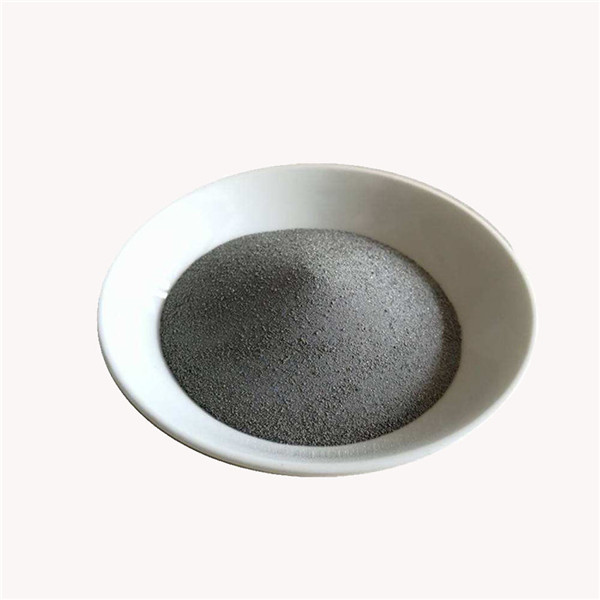
Quels sont les métaux et les alliages qui sont couramment atomisés au gaz ?
Parmi les métaux et alliages courants qui sont atomisés au gaz, on peut citer
- Alliages de titane comme le Ti-6Al-4V
- Superalliages à base de nickel comme l'Inconel 718, l'Inconel 625
- Alliages de cobalt et de chrome
- Aciers à outils comme le H13
- Aciers inoxydables tels que 316L, 17-4PH
- Alliages d'aluminium
- Alliages de cuivre
Les alliages à haute température à base de titane, de nickel et de cobalt sont particulièrement bien adaptés à l'atomisation gazeuse. L'atmosphère de gaz inerte empêche l'accumulation excessive d'oxygène dans ces poudres élémentaires réactives. Les métaux réfractaires comme le tungstène sont également atomisés au gaz car leur point de fusion élevé rend l'atomisation à l'eau difficile.
Globalement, l'atomisation gazeuse peut produire de fines poudres sphériques à partir de n'importe quel alliage qui fond sans se décomposer. Le procédé peut être personnalisé pour atomiser de nouveaux alliages conçus pour des applications avancées.
Quelles sont les applications des poudres atomisées ?
Les principaux domaines d'application des poudres d'alliage atomisées au gaz sont les suivants :
Fabrication additive métallique
- La fusion laser sur lit de poudre utilise des poudres atomisées au gaz en raison de leur morphologie sphérique et de leur distribution de taille contrôlée. Ces caractéristiques garantissent un bon écoulement et un bon conditionnement dans le lit de poudre.
- La projection de liant utilise également des poudres atomisées au gaz pour produire des propriétés isotropes dans les pièces imprimées. La forme sphérique et le contrôle précis de la taille améliorent la densité de l'emballage et l'étalement de la poudre.
Métallurgie des poudres
- Le moulage par injection de métaux repose sur des poudres d'alimentation atomisées au gaz dont la taille des particules est contrôlée. Cela permet une charge de poudre élevée et un rétrécissement uniforme.
- Le pressage et le frittage de poudres utilisent des poudres pré-alliées atomisées pour produire des composants automobiles, des outils de coupe et d'autres pièces structurelles.
Pulvérisation thermique
- Les poudres atomisées au gaz introduites dans les systèmes de pulvérisation thermique par plasma, flamme ou oxy-combustible à haute vitesse (HVOF) produisent des revêtements de qualité supérieure en raison de leur morphologie sphérique.
Soins de santé
- Les structures poreuses fabriquées à partir de poudres de titane et de cobalt-chrome atomisées au gaz sont utilisées pour les implants orthopédiques.
- Les poudres fines d'acier inoxydable sont utilisées pour fabriquer des instruments chirurgicaux par moulage par injection de métal.
La combinaison de la pureté, de la répétabilité et des caractéristiques des particules fait que les poudres atomisées au gaz sont idéales pour ces applications critiques dans toutes les industries.
Quelle est la distribution granulométrique utilisée pour les différentes applications ?
La distribution optimale de la taille des particules dépend de l'application envisagée :
- Pour la fusion laser sur lit de poudre, la plage typique est de 15 à 45 microns. Les poudres très fines, inférieures à 10 microns, peuvent poser des problèmes de manipulation. Une fourchette de 25 à 35 microns est couramment utilisée.
- Le jet de liant utilise des poudres plus fines, de l'ordre de 5 à 25 microns, pour améliorer le frittage. L'épaisseur de la couche détermine également la taille minimale des particules.
- Le moulage par injection des métaux utilise des distributions bimodales avec des tailles de poudre inférieures à 25 microns. Cela permet d'améliorer la densité et l'écoulement de l'emballage.
- La pulvérisation thermique nécessite des particules plus grosses, supérieures à 45 microns, pour un meilleur transfert d'énergie et une meilleure densité de revêtement. Les gammes de tailles comprises entre 45 et 100 microns sont couramment utilisées.
- Pour les implants orthopédiques, des poudres de taille inférieure à 75 microns favorisent la croissance des tissus dans la structure poreuse.
Les paramètres du processus d'atomisation du gaz peuvent être optimisés pour produire des poudres ayant la distribution granulométrique souhaitée pour l'application envisagée.
Quels sont les derniers développements en matière de technologie d'atomisation du gaz ?
Parmi les dernières avancées dans le domaine de la technologie des procédés d'atomisation du gaz, on peut citer les suivantes :
- L'atomisation à couplage étroit utilise un four à électrodes consommables intégré à la buse d'atomisation pour un processus plus contrôlé. La propreté de la matière fondue s'en trouve améliorée.
- Plusieurs injecteurs de gaz disposés de manière concentrique peuvent produire des distributions de taille de particules uniques. La variation de la pression du gaz entre les injecteurs augmente la flexibilité de l'atomisation.
- Les atomiseurs à pré-filmage utilisent un film liquide fin pour générer des gouttelettes atomisées plus fines que les flux de métal en chute libre. Cela permet de traiter des poudres de moins de 10 microns.
- Les systèmes de contrôle par rétroaction utilisant des capteurs optiques permettent un ajustement dynamique des pressions de gaz et du débit de métal afin de maintenir la distribution de la taille des poudres. L'homogénéité s'en trouve améliorée.
- L'atomisation par induction utilise la lévitation électromagnétique et des bobines d'induction pour contrôler avec précision le bain de fusion. Cela permet un processus d'atomisation très uniforme et sans contact.
- La fabrication additive est utilisée pour fabriquer des géométries complexes de buses d'atomiseurs qui ne sont pas possibles avec l'usinage conventionnel. Cela permet un meilleur contrôle de l'atomisation.
Ces innovations élargissent les systèmes d'alliage et les caractéristiques des particules réalisables par atomisation gazeuse.
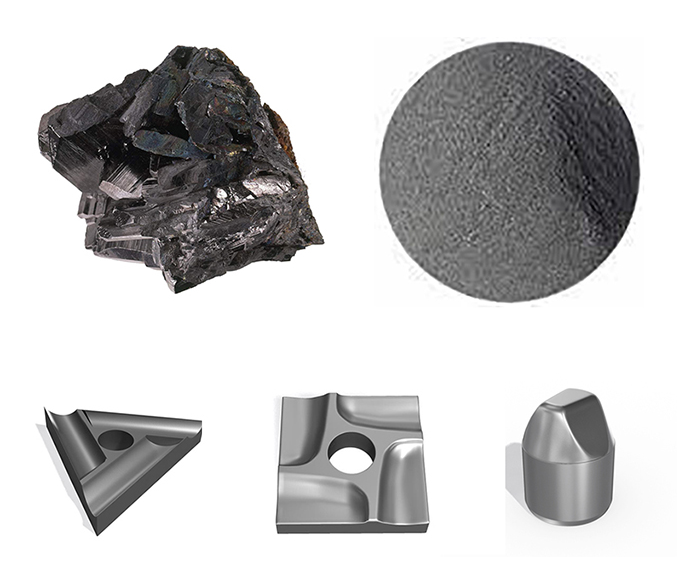
Quels sont les défis à relever en matière d'atomisation du gaz ?
Voici quelques-uns des principaux défis associés à l'atomisation du gaz :
- Contamination des alliages réactifs par le ramassage de l'oxygène et de l'azote – ; L'utilisation de gaz inertes de grande pureté et de chambres à vide permet de minimiser ce phénomène.
- Formation de satellites pendant l'atomisation en raison de la formation de ligaments entre les gouttelettes – ; l'optimisation de la géométrie de la buse et du flux de gaz réduit les satellites.
- Production de formes de particules irrégulières et non sphériques – ; Un contrôle minutieux des paramètres du processus garantit une morphologie sphérique lisse.
- Atteindre des taux de refroidissement uniformes entre les grandes et les petites particules – ; La conception modifiée des buses permet d'égaliser les taux de solidification des gouttelettes.
- Manipulation de poudres chaudes à haute réactivité et oxydation en dessous du point de fusion – ; La manipulation de poudres sous atmosphère inerte supprime l'oxydation.
- Coût et complexité associés à l'utilisation de systèmes de gaz à haute pression – ; Des innovations récentes améliorent la productivité et réduisent les coûts.
La recherche continue est axée sur la compréhension et le contrôle de la physique de l'atomisation de la matière fondue afin d'améliorer encore la qualité et l'uniformité de la poudre atomisée au gaz.
Quelles sont les alternatives à l'atomisation du gaz ?
Parmi les procédés de production de poudres alternatifs à l'atomisation au gaz, on peut citer
- Atomisation à l'eau – ; Peu coûteuse mais provoquant une oxydation et des formes de poudres irrégulières
- Atomisation par plasma – ; Produit des poudres hautement sphériques mais avec une très faible productivité
- Atomisation du gaz de fusion par induction de l'électrode – ; Bon pour les alliages réactifs, mais ramassage plus important de l'O2
- Procédé à électrode rotative – ; prometteur pour la production de poudres métalliques sphériques, mais encore en développement
- Sphéroïdisation par plasma – ; Sphéroïdisation de poudres irrégulières mais ne produit pas de poudre d'alliage fraîche
- Broyage mécanique – ; Contamination de la poudre par attrition et abrasion
Pour la plupart des applications, l'atomisation au gaz constitue le meilleur équilibre entre le coût, la productivité et la qualité de la poudre. Mais de nouvelles techniques d'atomisation continuent d'apparaître comme des alternatives pour des applications de niche.
Quel est l'avenir des poudres atomisées au gaz ?
Les poudres atomisées au gaz vont continuer à gagner en importance avec la croissance de la fabrication additive métallique. Le contrôle précis des caractéristiques de la poudre que permet l'atomisation du gaz est essentiel pour les applications exigeantes de la fabrication additive dans les domaines de l'aérospatiale et de la médecine. C'est ce qui explique l'importance des investissements et des innovations dans le domaine de la technologie d'atomisation.
Outre l'AM, l'utilisation croissante de la métallurgie des poudres dans l'industrie automobile et d'autres secteurs accélérera également l'adoption de l'atomisation au gaz. L'utilisation de matières premières sous forme de poudres métalliques permet d'obtenir des géométries de composants complexes et des compositions d'alliages impossibles à réaliser avec des produits corroyés.
L'atomisation des gaz permettra également de créer de nouveaux matériaux tels que des poudres d'alliages amorphes aux propriétés uniques. Le contrôle des taux de refroidissement pendant l'atomisation peut produire des alliages personnalisés et des phases métastables.
Dans l'ensemble, les améliorations en termes de qualité et de rentabilité permettront à l'avenir d'étendre la pulvérisation de gaz à un plus grand nombre de systèmes de matériaux et d'applications industrielles.
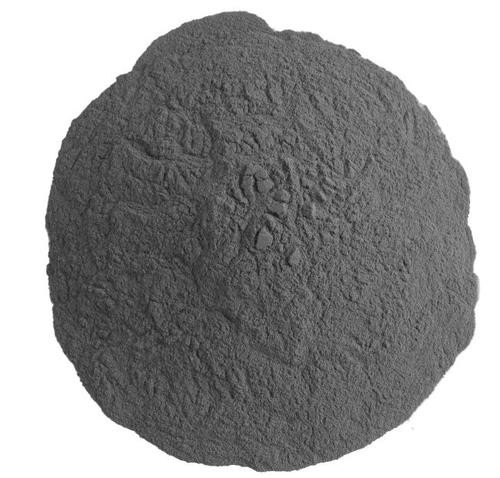
FAQ
Quelle est la plus petite taille de particule pouvant être produite par atomisation de gaz ?
L'atomisation au gaz peut produire des poudres d'une taille inférieure à 5 microns. Des buses spéciales utilisant un flux de pré-filtrage ont généré des particules d'une taille inférieure au micron. Mais la production à l'échelle inférieure à 10 microns reste un défi.
Comment l'atomisation du gaz permet-elle d'obtenir des particules aussi sphériques ?
La tension superficielle élevée des gouttelettes de métal, combinée à une solidification rapide dans l'atmosphère de gaz inerte, préserve la forme sphérique. Les ligaments entre les gouttelettes, qui causent des irrégularités, sont minimisés grâce à des paramètres d'atomisation optimaux.
Quel est l'avantage d'une distribution étroite des tailles ?
Une distribution étroite permet d'obtenir des propriétés et des performances constantes dans l'application finale. Par exemple, une fusion et un écoulement uniformes pendant le traitement par AM des métaux. Les problèmes de ségrégation et de porosité sont évités.
Quel est le taux de production maximal pour les poudres atomisées au gaz ?
Les taux de production des atomiseurs à gaz commerciaux sont généralement compris entre 5 et 20 kg de poudre par minute. Avec des systèmes optimisés, des taux de production allant jusqu'à 100 kg/min ont été rapportés pour certains alliages à bas point de fusion.
Comment les matériaux réactifs tels que le gaz d'aluminium sont-ils atomisés ?
Des gaz inertes très purs (argon, azote) doivent être utilisés pour éviter une accumulation excessive d'oxygène et de nitrure. La manipulation et la collecte sous atmosphère protectrice sont également essentielles. Des chambres à vide peuvent également être utilisées.
Existe-t-il des moyens de produire des poudres atomisées au gaz de manière plus économique ?
Des innovations récentes telles que les buses à couplage étroit, les atomiseurs de pré-filtration avancés, l'injection de gaz multiples et les creusets d'électrodes améliorent l'efficacité énergétique. La fabrication additive de buses permet également de réduire les coûts. Des taux de production plus élevés permettent d'améliorer les économies d'échelle.
La pulvérisation de gaz permet-elle d'obtenir les propriétés des produits corroyés ?
Avec un traitement optimisé, les poudres atomisées au gaz peuvent atteindre des propriétés mécaniques proches des alliages corroyés conventionnels dans certains matériaux. Mais les propriétés sont toujours limitées par la porosité résiduelle dans les produits de la métallurgie des poudres.
Quelles sont les industries qui consomment le plus de poudres atomisées aujourd'hui ?
Actuellement, les secteurs de l'aérospatiale et de la médecine sont les plus gros consommateurs de poudres atomisées au gaz pour la fabrication additive et le moulage par injection de métaux. L'utilisation dans les applications automobiles augmente également rapidement.
L'atomisation gazeuse permet-elle d'obtenir des compositions d'alliage qui ne peuvent pas être traitées de manière conventionnelle ?
Oui, l'atomisation au gaz a des taux de refroidissement très élevés qui peuvent supprimer les réactions de décomposition et permettre des phases d'alliage métastables et amorphes. Elle permet également de produire sous forme de poudres des compositions d'alliages dont la coulabilité ou l'ouvrabilité est médiocre.
en savoir plus sur les procédés d'impression 3D
Additional FAQs About Gas Atomization
1) What CoA data should buyers require for gas atomized powders?
- Chemistry, PSD (D10/D50/D90), flow (Hall/Carney), apparent/tap density, O/N/H, moisture, and for AM grades: image‑based sphericity/satellite %, CT‑measured hollow fraction, and lot traceability with test methods (ASTM/ISO).
2) How do gas‑to‑metal ratio and melt superheat affect PSD and satellites?
- Higher gas‑to‑metal ratio and adequate superheat generally reduce D50 and narrow PSD, while stable superheat and optimized nozzle/plume alignment lower ligament formation, cutting satellite content.
3) When is vacuum gas atomization (VGA/EIGA) preferred over inert gas atomization?
- For reactive alloys (Ti, Al, Mg) and aerospace/medical grades requiring very low O/N/H and minimal inclusions; VGA/EIGA often yields fewer hollows and better sphericity than standard inert gas atomization.
4) Can gas atomized powders be reused in AM, and what should be monitored?
- Yes, commonly 5–10 cycles with sieving. Track PSD shift, flow, apparent/tap density, and O/N/H; monitor satellite/hollow fractions via image analysis/CT; refresh with virgin powder when thresholds drift.
5) How does gas atomization compare to water atomization for binder jetting?
- Water‑atomized powders are cheaper and common in BJ steels/Cu but have higher oxide and irregular shapes. Gas atomized variants offer better packing and lower impurity pickup, helping achieve higher sintered density or reduced HIP reliance.
2025 Industry Trends for Gas Atomization
- CoA transparency: Growing inclusion of sphericity, satellite %, and CT hollow fraction alongside O/N/H and PSD for AM‑grade lots.
- Energy and argon savings: Argon recirculation and heat recovery cut Ar consumption by 15–30% and total energy 5–12% in modern atomizers.
- Regional supply: New atomization lines in NA/EU/APAC shorten lead times for Ti/Ni/SS AM powders.
- Advanced controls: Closed‑loop gas‑to‑metal ratio, melt superheat control, and plume vision reduce satellites and improve yield.
- Binder jet adoption: Engineered bimodal PSD steels achieve 97–99.5% sintered density; HIP used selectively for critical parts.
2025 Market and Technical Snapshot (Gas Atomization)
Metric (2025) | Typical Value/Range | YoY Change | Notes/Source |
---|---|---|---|
Gas‑atomized 316L price | $10–$18/kg | −2–5% | Supplier/distributor indices |
Gas‑atomized 17‑4PH price | $12–$20/kg | −2–5% | PSD/alloy dependent |
Ti‑6Al‑4V (VGA/EIGA) | $150–$280/kg | −3–7% | Aerospace/medical grades |
Common AM PSD cuts (LPBF/BJ/DED) | 15–45 or 20–63 µm / 20–80+ µm / 53–150 µm | Stable | OEM guidance |
Sphericity (image analysis) | ≥0.93–0.98 | Slightly up | Supplier CoAs |
Satellite fraction (image) | ≤3–6% | Down | Process tuning |
CT hollow particle fraction | 0.5–1.5% | Down | VGA/EIGA + CT QC |
Argon use reduction (recirc) | 15–30% | Up | Energy/LCA initiatives |
Indicative sources:
- ISO/ASTM 52907 (Metal powders), 52908 (AM process qualification): https://www.iso.org | https://www.astm.org
- ASTM B214/B213/B212/B962 (powder tests), MPIF references: https://www.astm.org | https://www.mpif.org
- NIST AM Bench and powder metrology: https://www.nist.gov
- ASM Handbooks (Powder Metallurgy; Additive Manufacturing): https://www.asminternational.org
- NFPA 484 (Combustible metal dusts): https://www.nfpa.org
Latest Research Cases
Case Study 1: Closed‑Loop Plume Control Cuts Satellites in 316L (2025)
Background: An AM service bureau reported recoater jams tied to high satellite content from a key supplier’s gas atomized 316L.
Solution: Supplier implemented real‑time plume imaging, closed‑loop gas‑to‑metal ratio, and tighter melt superheat; added post‑classification air elutriation.
Results: Satellite fraction reduced from 8.1% to 3.1% (image analysis); Hall flow +14%; LPBF relative density rose from 99.4% to 99.8%; unplanned stoppages −40%.
Case Study 2: VGA with CT Screening for Ti‑6Al‑4V Fatigue Scatter Reduction (2024)
Background: An aerospace OEM needed lower hollow particle fraction to improve fatigue consistency in PBF Ti‑6Al‑4V.
Solution: Vacuum gas atomization (EIGA electrodes), in‑line oxygen monitoring, and lot‑level CT to cap hollows ≤1.0%; argon recirculation to lower cost.
Results: Median hollows 0.6%; O = 0.12 wt% ±0.01; HIP’d coupons showed ~2× reduction in HCF scatter band; powder cost −6% via gas reuse.
Expert Opinions
- Prof. Diran Apelian, Distinguished Professor (emeritus), Metal Processing
Key viewpoint: “Melt cleanliness plus stable gas‑to‑metal ratio and superheat set the quality ceiling in gas atomization—post‑screening can’t fully recover poor plume dynamics.” - Dr. John Slotwinski, Additive Manufacturing Metrology Expert (former NIST)
Key viewpoint: “Reporting sphericity, satellite %, and CT‑quantified hollows on CoAs is now a leading indicator of PBF defect propensity—buyers should require these metrics.” - Prof. Tresa Pollock, Distinguished Professor of Materials, UC Santa Barbara
Key viewpoint: “For reactive alloys, vacuum/inert control during atomization fundamentally influences downstream fatigue and corrosion performance, even after HIP.”
Note: Viewpoints synthesized from public talks and publications; affiliations are publicly known.
Practical Tools and Resources
- Standards and testing
- ISO/ASTM 52907, 52908; ASTM B214 (sieves), B213 (flow), B212 (apparent density), B962 (tap density): https://www.iso.org | https://www.astm.org
- Safety and compliance
- NFPA 484 combustible metal dust guidance; ATEX/DSEAR resources for Dust Hazard Analysis: https://www.nfpa.org
- Metrology and QC
- NIST powder characterization; LECO O/N/H analyzers; industrial CT for hollow/satellite quantification: https://www.nist.gov
- Technical references
- ASM Digital Library (Powder Metallurgy; Additive Manufacturing; Stainless/Titanium/Nickel): https://www.asminternational.org
- Buyer’s QC checklist
- CoA completeness (chemistry, PSD, flow, densities, O/N/H, sphericity, satellites, hollows), genealogy/traceability, SPC dashboards, sample builds/sinter coupons, local inventory and refresh policies
Last updated: 2025-08-26
Changelog: Added 5 targeted FAQs; inserted 2025 market/technical snapshot table with sources; provided two recent gas atomization case studies; compiled expert viewpoints; curated practical tools/resources
Next review date & triggers: 2026-02-01 or earlier if ISO/ASTM/MPIF standards update, major OEMs revise AM powder specs, or new NIST/ASM datasets link morphology/interstitials to AM defect rates and fatigue performance