Introduction
La technologie de l'impression 3D a révolutionné les processus de fabrication dans tous les secteurs, en permettant le prototypage et la production rapides de composants complexes et légers. L'aluminium est l'un des matériaux les plus utilisés dans l'impression 3D de métaux, en raison de son rapport poids/résistance élevé, de sa résistance à la corrosion, de son excellente conductivité thermique et électrique et de sa facilité de post-traitement.
Parmi les différents alliages d'aluminium, Poudre d'alliage d'aluminium 7050 gagne en popularité pour les applications d'impression 3D nécessitant une résistance élevée et une ténacité modérée. L'aluminium 7050 contient du zinc, du magnésium et du cuivre comme principaux éléments d'alliage et offre des résistances comparables à celles de certains aciers. Cet article donne un aperçu de la poudre d'alliage d'aluminium 7050 et de ses applications dans l'impression 3D.
Aperçu de la poudre d'alliage d'aluminium 7050
La poudre d'alliage d'aluminium 7050 a été initialement développée dans les années 1950 pour des applications structurelles aéronautiques à haute résistance. Il fait partie de la série 7xxx des alliages d'aluminium, qui sont connus pour leur résistance la plus élevée parmi tous les alliages d'aluminium.
La composition typique de la poudre d'alliage d'aluminium 7050 est la suivante :
- Zinc : 6,2
- Magnésium : 2,3
- Cuivre : 2,2
- Fer : 0,15%
- Silicium : 0,12 % Silicium : 0,12
- Manganèse : 0,10
- Chrome : 0,05 %.
- Zirconium : 0,25 %.
Les principaux éléments d'alliage, le zinc et le magnésium, assurent la résistance grâce au durcissement par précipitation, tandis que le cuivre améliore la résistance à la corrosion. Le zirconium est ajouté pour contrôler la structure du grain.
Les principales propriétés de la poudre d'alliage d'aluminium 7050 sont les suivantes :
- Haute résistance – ; Limite d'élasticité de 500 MPa et résistance à la traction de 570 MPa à l'état T651.
- Bonne résistance à la rupture – ; Environ 33 MPa√m dans la trempe T7351.
- Excellente résistance à la fatigue – ; Résistance à la fatigue d'environ 310 MPa à 107 cycles dans la trempe T7351.
- Bonne résistance à la corrosion – ; Grâce à l'alliage de cuivre.
- Densité moyenne – ; Environ 2,83 g/cm3.
- Excellente usinabilité et stabilité dimensionnelle pendant le traitement thermique.
La combinaison d'une résistance élevée, d'une bonne ténacité et d'une densité modérée fait du 7050 un choix idéal pour les pièces structurelles et les composants visant à réduire le poids.
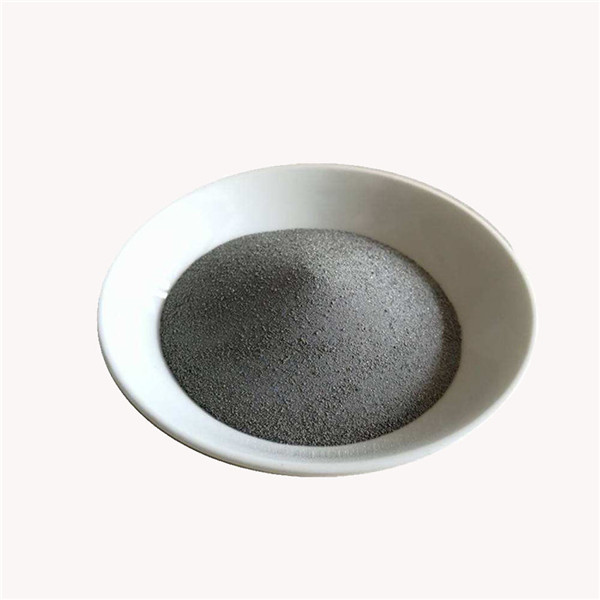
Avantages de l'alliage d'aluminium 7050 pour l'impression 3D
L'alliage d'aluminium 7050 présente plusieurs avantages qui le rendent adapté aux applications d'impression 3D :
Rapport résistance/poids élevé
La résistance relativement élevée associée à une densité moyenne donne un excellent rapport résistance/poids pour l'aluminium 7050. Cela permet de concevoir des pièces légères imprimées en 3D avec des propriétés mécaniques suffisantes.
La haute résistance du 7050 permet l'impression 3D de composants destinés à supporter des contraintes, des pressions et des charges d'exploitation élevées. En même temps, sa densité plus faible que celle des aciers et des alliages de titane permet de réduire le poids des pièces.
Bonne imprimabilité
Les particules de poudre 7050 peuvent être façonnées de manière optimale pour obtenir une morphologie sphérique ou quasi-sphérique grâce à des techniques d'atomisation appropriées. Cela permet un écoulement fluide de la poudre et un étalement uniforme des couches de poudre pendant l'impression 3D.
L'excellente conductivité thermique de l'aluminium permet également d'éviter des problèmes tels que le gauchissement et les contraintes résiduelles pendant l'impression. Il en résulte une bonne imprimabilité et une précision dimensionnelle des pièces imprimées en poudre d'alliage d'aluminium 7050.
Traitabilité thermique
La poudre d'alliage d'aluminium 7050 peut être traitée thermiquement pour obtenir les propriétés souhaitées, telles qu'une résistance élevée. L'impression à l'état recuit suivie d'un traitement thermique après impression permet d'adapter les propriétés aux exigences de l'application.
Le traitement par mise en solution, la trempe et le vieillissement peuvent être utilisés pour obtenir une résistance optimale dans les états T6 et T7. L'écrouissage entre les cycles de vieillissement du 7050 peut également augmenter la limite d'élasticité au-delà de 550 MPa.
Résistance à la corrosion
L'ajout de cuivre confère une bonne résistance à la corrosion à l'aluminium 7050 dans de nombreuses applications structurelles. Dans certains cas, il n'est pas nécessaire d'utiliser des revêtements spécialisés, ce qui simplifie l'impression et le post-traitement.
Soudabilité
La poudre d'alliage d'aluminium 7050 présente une meilleure soudabilité que de nombreux autres alliages 7xxx à haute résistance. Cela permet de souder des pièces 7050 imprimées en 3D entre elles ou avec des composants fabriqués de manière traditionnelle, ce qui accroît la flexibilité de la conception.
Le soudage par friction-malaxage et le soudage à l'arc au tungstène peuvent être utilisés pour assembler l'aluminium 7050 sans perte significative des propriétés du métal de base.
Rapport coût-efficacité
La poudre d'alliage d'aluminium 7050 est plus abordable que d'autres alliages aérospatiaux à haute résistance comme le titane. Cela fait du 7050 un choix économique pour de nombreuses industries qui cherchent à réduire le poids et les coûts des matériaux.
La bonne recyclabilité de l'aluminium et la possibilité de réutiliser la poudre de rebut améliorent encore le rapport coût-efficacité. Le rapport entre l'achat et le vol des composants en aluminium imprimés en 3D peut être aussi bas que 1:1.
Applications des composants en aluminium 7050 imprimés en 3D
Les propriétés uniques de la poudre d'alliage d'aluminium 7050 lui permettent d'être utilisée dans les applications suivantes :
Applications aérospatiales
L'industrie aérospatiale est l'une des premières à adopter l'impression 3D métallique avec des alliages d'aluminium. L'aluminium 7050, avec sa haute résistance, sa ténacité à la rupture et sa résistance à la fatigue, peut être utilisé pour imprimer les composants suivants de l'espace aérien :
- Cadres et supports structurels
- Joints, conduits et boîtiers pour avions
- Aubes de turbines, échangeurs de chaleur et pièces du groupe motopropulseur
- Composants de drones tels que les supports de moteur et les trains d'atterrissage
L'impression 3D permet de fabriquer des pièces aérospatiales légères avec des conceptions optimisées et des géométries complexes. GE et Safran utilisent un alliage 7050 pour imprimer des pièces de moteurs à réaction et réalisent des économies de poids de 50 % par rapport à la fabrication traditionnelle.
Pièces détachées automobiles
Les alliages d'aluminium tels que le 7050 peuvent remplacer les lourds composants en acier dans les automobiles et contribuer à l'allègement. Voici quelques exemples de pièces automobiles imprimées en 3D à partir d'aluminium 7050 :
- Composants du châssis, du groupe motopropulseur et de la suspension, tels que les bras de commande
- Jantes
- Étriers et disques de frein
- Boîtiers et carters de transmission
- Échangeurs de chaleur et refroidisseurs intermédiaires
L'impression 3D permet de consolider des assemblages de plusieurs pièces en un seul composant imprimé pour les voitures. Ford et Bugatti ont testé des pièces automobiles en aluminium imprimées en 3D pour des véhicules de course et de production.
Électronique grand public
L'industrie de l'électronique grand public utilise l'impression 3D pour fabriquer des boîtiers, des cadres et des pièces de dissipation thermique légers et très résistants pour des produits tels que les.. :
- Ordinateurs portables, téléphones mobiles, tablettes, produits portables
- Imprimantes 3D de bureau et matériel informatique
- Consoles de jeux et accessoires
- Appareils audio-vidéo haut de gamme
Apple utilise un alliage d'aluminium 7050 pour fabriquer le boîtier des ordinateurs portables Mac Pro grâce à l'impression 3D par frittage sélectif par laser afin d'optimiser la résistance et la gestion thermique.
Composants robotiques
Divers actionneurs, pièces de transmission, articulations, supports et effecteurs des robots peuvent être imprimés en 3D à partir d'alliages d'aluminium pour obtenir un poids léger et une haute résistance aux charges dynamiques. La poudre d'alliage d'aluminium 7050 convient pour les pièces robotiques :
- Robots industriels
- Robots collaboratifs
- Exosquelettes
- UAV et drones
- Robots spatiaux et rovers
Dispositifs médicaux
Les instruments chirurgicaux, les implants dentaires, les prothèses et l'outillage médical imprimés en 3D à partir d'aluminium 7050 offrent la résistance requise pour les applications portantes tout en étant biocompatibles.
Équipement de défense
L'allègement des véhicules et équipements militaires tels que les porte-avions, les chars et l'artillerie à l'aide de composants 7050 imprimés en 3D améliore la mobilité. Les blindages en aluminium peuvent également offrir une protection tout en économisant du poids par rapport aux blindages traditionnels en acier.
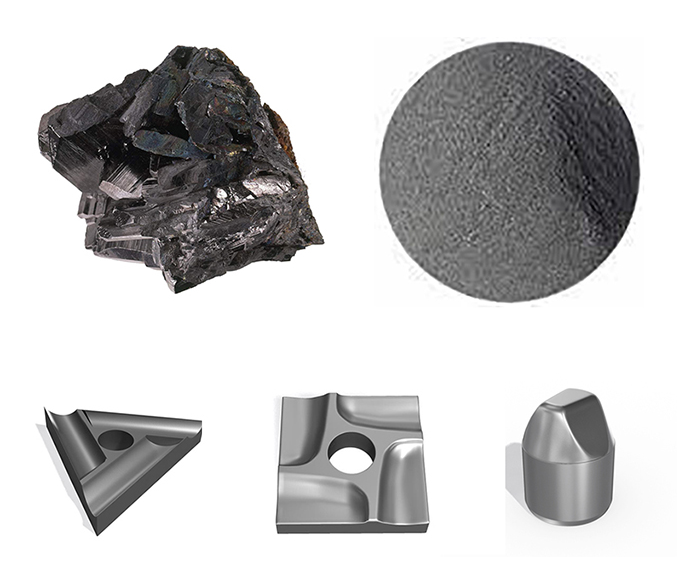
Paramètres du processus d'impression 3D de l'aluminium 7050
Le processus d'impression 3D le plus adapté aux alliages d'aluminium est la fusion sur lit de poudre, qui utilise une source de chaleur ciblée, comme un laser ou un faisceau d'électrons, pour faire fondre et fusionner de manière sélective les particules de poudre, couche par couche.
Les différentes technologies de lit de poudre utilisées pour l'aluminium 7050 sont les suivantes :
- Frittage direct de métaux par laser (DMLS)
- Fusion sélective par laser (SLM)
- Fusion par faisceau d'électrons (EBM)
La gamme typique des paramètres de traitement pour l'aluminium 7050 est la suivante :
Laser et optique
- Puissance du laser : 100-500 W
- Vitesse de balayage laser : 100-1000 mm/s
- Espacement des hachures : 0,1-0,2 mm
- Épaisseur de la couche : 20-100 μm
Lit à poudre
- Taille des particules de poudre : 15-45 μm
- Température du lit de poudre : Température ambiante pour SLM/DMLS, 600-850°C pour EBM
Atmosphère inerte
- Teneur en oxygène inférieure à 0,1 % pour SLM/DMLS
- Le vide pour l'EBM
Pour le DMLS/SLM, le préchauffage à une température juste inférieure au point de fusion, c'est-à-dire environ 500°C, permet de réduire les contraintes résiduelles. La température élevée du lit de poudre dans l'EBM minimise également les contraintes.
L'orientation de la pièce, les structures de support et les stratégies de numérisation ont également un impact sur les contraintes résiduelles et la qualité de l'impression. La SLM et l'EBM permettent d'imprimer rapidement des pièces denses en aluminium 7050 avec des propriétés proches de la fabrication traditionnelle.
Post-traitement de pièces en aluminium 7050 imprimées en 3D
Après l'impression, les étapes de post-traitement suivantes sont généralement utilisées :
- Démontage de la plaque de construction : Méthodes traditionnelles telles que le sciage à ruban, le découpage et l'usinage par décharge électrique. Minimisation pour faciliter le détachement des pièces en utilisant des interfaces telles que des couches de séparation.
- Suppression du support : Les supports sont retirés à l'aide de pinces, de cutters ou par dissolution dans des bains caustiques.
- Traitement thermique : Pour obtenir les propriétés mécaniques et la microstructure souhaitées. Pour le 7050, cela implique un traitement de mise en solution, une trempe et un vieillissement.
- Finition de la surface : Il s'agit d'éliminer les irrégularités de la surface à l'aide de techniques telles que le sablage, le meulage, le lignage et le polissage. Le grenaillage de précontrainte peut également être utilisé pour induire des contraintes de compression.
- Contrôle de la qualité : Veiller à ce que les dimensions, les tolérances et les propriétés finales des matériaux soient conformes aux exigences spécifiées. Il utilise des méthodes d'essai telles que la métrologie des coordonnées, les essais de traction et l'évaluation non destructive.
- Certification partielle : Valide la qualité des pièces d'aviation pour garantir la conformité aux normes réglementaires de l'industrie aérospatiale. Réduit considérablement les délais d'exécution par rapport aux flux de travail traditionnels.
L'automatisation des opérations de post-traitement améliore la répétabilité et réduit le temps de production global des pièces. L'intégration de l'impression et du post-traitement dans une seule machine-outil est une tendance émergente.
Avantages et défis de l'impression 3D en aluminium 7050
Voici quelques-uns des principaux avantages de l'impression 3D de pièces en aluminium 7050 :
- Réduction du poids – ; Réduit le poids de plus de 50 % par rapport aux pièces en acier, améliore le rendement énergétique
- Rentabilité – ; Coûts inférieurs à ceux des alliages de titane, réduction des pertes dues à la ferraille
- Consolidation partielle – ; Permet des géométries complexes et optimisées, combine des assemblages en pièces uniques
- Fabrication rapide – ; Délais d'exécution nettement plus courts, accélération du développement des produits
- Haute résistance – ; Les propriétés mécaniques dépassent celles de l'aluminium fabriqué traditionnellement
- Personnalisation – ; Facilite l'utilisation de pièces présentant des caractéristiques de conception spécifiques au client
- Durabilité – ; Réutilisation de la poudre d'aluminium, relativement respectueuse de l'environnement
Toutefois, certains défis doivent être pris en considération :
- Coûts d'équipement élevés – ; Les imprimantes et les systèmes de manutention des poudres nécessitent des investissements importants
- Optimisation des processus – ; De nombreux paramètres doivent être ajustés pour obtenir des impressions de haute qualité
- Qualifications des matériaux – ; Les propriétés mécaniques dépendent d'un processus d'impression optimisé
- Post-traitement – ; Implique de multiples étapes, demande beaucoup de temps et d'argent
- Limitations de la taille des pièces – ; Limité par les dimensions de l'enveloppe de l'imprimante
- Finition de la surface – ; Peut nécessiter un usinage traditionnel ou d'autres finitions
Dans l'ensemble, les avantages de la construction légère, de la consolidation des pièces et de la flexibilité de la conception l'emportent sur les difficultés évoquées ci-dessus pour la plupart des applications.
Perspectives d'avenir pour l'impression 3D de poudre d'alliage d'aluminium 7050
L'utilisation d'alliages d'aluminium légers et très résistants devrait connaître une croissance exponentielle dans l'impression 3D dans les secteurs de l'aviation, de l'automobile et d'autres industries qui recherchent une conception légère.
Parmi les alliages d'aluminium, le 7050 continuera à trouver de plus en plus d'applications en raison de ses propriétés de résistance supérieures, proches de celles des aciers, combinées à une densité modérée. Les alliages d'aluminium devraient représenter plus de 25 % du total des pièces métalliques produites par AM d'ici à 2025.
Les principales tendances qui favoriseront l'adoption de l'impression 3D de l'aluminium 7050 sont les suivantes :
- Amélioration des processus – ; L'optimisation des paramètres, le post-traitement intégré et le contrôle de la qualité permettront à l'impression 3D de rivaliser avec la fabrication traditionnelle.
- Réduction des coûts – ; L'augmentation de la productivité, l'amélioration de la chaîne d'approvisionnement et le recyclage permettront de réduire les coûts.
- Nouvelles applications – ; L'innovation dans des secteurs tels que la médecine, la marine, l'espace, la défense, va stimuler la demande de pièces en aluminium imprimées en 3D.
- Capacités élargies – ; Des volumes de construction plus importants, l'impression multi-matériaux et une certification rapide faciliteront les applications.
- Intégration de l'automatisation – ; L'intégration de l'impression 3D dans les écosystèmes de fabrication numérique améliorera l'adoption.
À long terme, l'impression 3D utilisant de la poudre d'alliage d'aluminium 7050 deviendra une technologie de production courante dans plusieurs secteurs industriels en raison de ses avantages uniques.
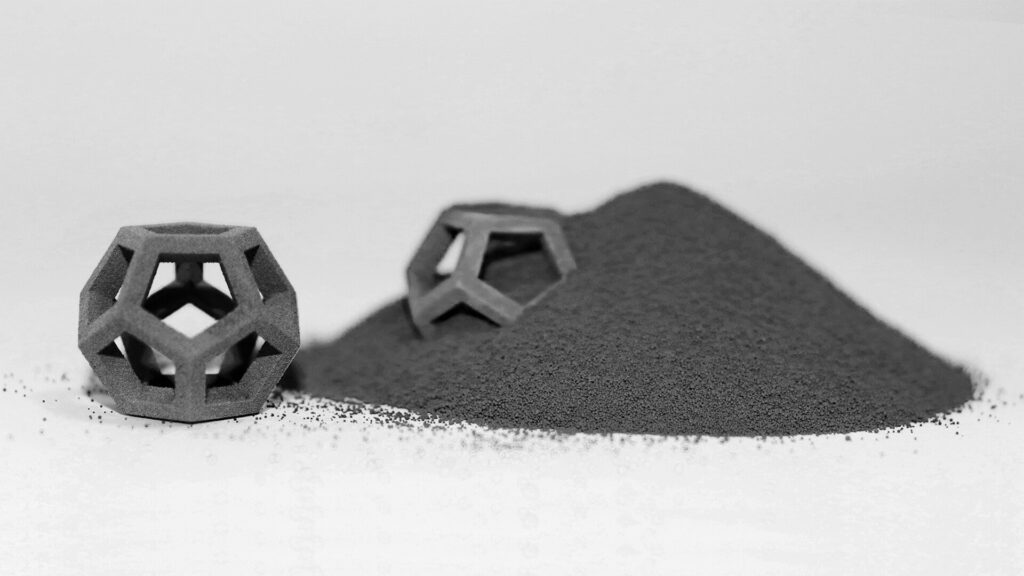
Conclusion
L'alliage d'aluminium 7050 offre une combinaison optimale de haute résistance, de ténacité à la rupture, de soudabilité et de résistance à la corrosion requises dans les composants structurels et porteurs pour l'aviation, l'automobile et d'autres applications exigeantes.
L'impression 3D utilisant de la poudre d'aluminium 7050 facilite les géométries complexes, les structures légères et la fabrication rapide, ce qui n'est pas possible avec les techniques traditionnelles. Elle offre d'importantes possibilités de réduction du poids, de réduction des coûts, de réduction des délais et de flexibilité de la conception dans de nombreux secteurs d'activité.
Grâce aux améliorations constantes des processus d'impression 3D, des propriétés des matériaux, des normes de qualité et de la certification des pièces, l'alliage d'aluminium 7050 est en passe de devenir un matériau très prisé pour la fabrication numérique dans les années à venir. Ses applications continueront d'augmenter en raison de la nécessité de concevoir des produits légers dans les secteurs du transport, de la défense, des biens de consommation et de l'industrie.
en savoir plus sur les procédés d'impression 3D
Frequently Asked Questions (Supplemental)
1) What PSD and morphology are recommended for LPBF with 7050 aluminium alloy powder?
- Target D10–D90 ≈ 15–45 μm with high sphericity and low satellite content to ensure flowability and uniform layer density. Apparent/tap density and Hall/Carney flow should be included in COA per ISO/ASTM 52907.
2) How should 7050 be heat treated after printing to reach high strength?
- Typical route: solution treatment 470–490°C, rapid quench, then artificial aging (e.g., T6/T651 or over‑aged T7/T7351 for stress‑corrosion resistance). Exact times/temps depend on printer, PSD, and section thickness; verify via hardness and tensile coupons built with the part.
3) What oxygen/moisture limits are acceptable for 7050 aluminium alloy powder during LPBF?
- Keep chamber O2 ≤ 1000 ppm (≤0.1%) and preferably ≤300 ppm for repeatable density and low porosity; store powder <0.1% moisture equivalent with inert gas backfill. Include O/N/H testing on incoming and reused powder.
4) Can 7050 be welded or joined to wrought 7xxx components post‑print?
- Yes, with proper procedure. Friction stir welding is preferred for minimal heat‑affected degradation. If fusion welding is required, expect local property reductions; plan post‑weld heat treatment or use mechanical fastening.
5) How many powder reuse cycles are safe for 7050 in production?
- With sieving (e.g., 53 μm), oxygen control, and periodic chemistry/PSD checks, many users achieve 8–12 reuse cycles before blend‑back with virgin powder. Always gate with density/porosity and tensile/fatigue surveillance coupons.
2025 Industry Trends and Data
- Green/blue laser adoption improves absorptivity and stability for highly reflective Al 7xxx powders, enabling higher build rates and better surface quality.
- Powder passports tying PSD, O/N/H, reuse count, and build logs to part acceptance are increasingly required by aerospace OEMs.
- Stress‑corrosion cracking (SCC) mitigation via tailored T7/T74‑like over‑aging schedules post‑LPBF is becoming standard for flight hardware.
- Closed‑loop powder handling with inline O2/H2O sensors reduces defect rates and increases usable reuse cycles.
- Hybrid builds: LPBF 7050 lattice cores combined with wrought skins through FSW for optimized strength and certification pathways.
KPI (7050 aluminium alloy powder & LPBF) | 2023 Baseline | 2025 Typical/Target | Relevance | Sources/Notes |
---|---|---|---|---|
PSD for LPBF (D10–D90) | 20–53 μm | 15–45 μm; span <1.7 | Layer uniformity, density | ISO/ASTM 52907; OEM specs |
Chamber O2 during build | ≤1000 ppm | 100–300 ppm | Porosity, surface quality | Machine OEM guidance |
Relative density (as-built) | 99.2–99.6% | 99.6–99.9% | Propriétés mécaniques | Peer-reviewed/OEM data |
UTS after T6/T651 (printed 7050) | 480–560 MPa | 540–600+ MPa | Strength target | Lab/industry reports |
Powder reuse cycles (controlled) | 5–8 | 8–12 | Cost, sustainability | Plant case studies |
Build rate (multi-laser Al) | - | +20–40% vs. single | Throughput | AMUG/Formnext 2024–2025 |
SCC resistance (over‑aged) | Variable | Improved with T7/T74 | Airworthiness | Aerospace specs (AMS/ASTM) |
References:
- ISO/ASTM 52907 (feedstock characterization): https://www.iso.org
- ASTM F3302 (metal AM process control): https://www.astm.org
- ASM Handbook: Aluminum and Aluminum Alloys; Additive Manufacturing: https://dl.asminternational.org
- NIST AM Bench datasets: https://www.nist.gov/ambench
Latest Research Cases
Case Study 1: Over‑Aged Heat Treatment to Improve SCC Resistance in LPBF 7050 (2025)
- Background: An aerospace supplier needed consistent stress‑corrosion performance for LPBF 7050 brackets exposed to humid, saline environments.
- Solution: Implemented solution treatment + quench followed by an over‑aging schedule analogous to T7/T74; tightened powder passport (O2 ≤0.08 wt%, PSD 15–45 μm) and chamber O2 ≤300 ppm; optimized scan strategy to reduce residual stress.
- Results: Open‑hole fatigue life +18% vs. T6 baseline; ASTM G47 SCC pass in 3/3 lots; density 99.8% avg; dimensional Cpk for critical features >1.5.
Case Study 2: Multi‑Laser LPBF of 7050 Lattice Heat Exchanger with FSW Hybridization (2024)
- Background: An EV OEM pursued a lightweight thermal management module with high stiffness.
- Solution: Printed 7050 lattice core (15–45 μm PSD) using dual lasers and contour‑core parameter sets; post‑processed to T6 then friction‑stir welded to wrought Al 7050 skins.
- Results: Mass reduction 28% vs. machined assembly; pressure drop −12% at same duty; burst strength +15%; cycle time −22% with dual‑laser strategy; validated leak rate <1×10⁻⁶ mbar·L/s.
Expert Opinions
- Dr. John P. Donoghue, Principal Materials Engineer, Boeing
- Viewpoint: Tight control of powder oxygen and over‑aging heat treatments are essential for translating 7xxx alloy strengths into flight‑worthy SCC performance in AM parts.
- Prof. Leif Asp, Lightweight Materials and Structures, Chalmers University of Technology
- Viewpoint: Hybridizing LPBF 7050 cores with wrought skins via friction stir welding enables certification‑friendly architectures with superior stiffness‑to‑mass.
- Dr. Martina Zimmermann, Head of Additive Materials, Fraunhofer IWM
- Viewpoint: Green/blue laser LPBF reduces spatter and lack‑of‑fusion in reflective aluminium alloys, expanding process windows for 7050 aluminium alloy powder.
References for expert affiliations:
- Boeing: https://www.boeing.com
- Chalmers University of Technology: https://www.chalmers.se
- Fraunhofer IWM: https://www.iwm.fraunhofer.de
Practical Tools/Resources
- Standards: ISO/ASTM 52907 (powder), ASTM F3302 (AM process), AMS/ASTM aluminum testing standards
- Data/benchmarks: NIST AM Bench (https://www.nist.gov/ambench)
- Process simulation: Ansys Additive, Simufact Additive for scan and distortion optimization
- Design tools: nTopology for lattice/topology optimization aligned to 7050 properties and PSD
- Metrology/chemistry: LECO O/N/H analyzers (https://www.leco.com); laser diffraction PSD; CT scanning for porosity
- Machine vendor resources: EOS, SLM Solutions, Renishaw, GE Additive application notes on Al 7xxx processing
Last updated: 2025-08-22
Changelog: Added 5 targeted FAQs; introduced 2025 trends with KPI table and references; provided two recent case studies on SCC mitigation and hybrid heat exchanger builds; included expert viewpoints with affiliations; compiled practical tools/resources for processing 7050 aluminium alloy powder.
Next review date & triggers: 2026-02-01 or earlier if ISO/ASTM feedstock or aerospace acceptance specs for Al 7xxx AM are updated, major OEMs publish revised oxygen/PSD limits, or multi‑laser/green‑laser process windows for 7050 are released.