Poudres faiblement alliées jouent un rôle crucial dans diverses industries, de l'automobile à l'aérospatiale. Leur polyvalence, associée à des propriétés uniques, les rend indispensables à la fabrication de composants de haute performance. Dans ce guide complet, nous explorerons tout ce que vous devez savoir sur les poudres faiblement alliées, de leur composition à leurs applications, leurs propriétés, etc. Que vous soyez un expert de l'industrie ou un lecteur curieux, cet article est conçu pour fournir des connaissances approfondies tout en restant conversationnel et engageant.
Aperçu des poudres faiblement alliées
Les poudres faiblement alliées sont des poudres métalliques techniques qui contiennent un faible pourcentage d'éléments d'alliage tels que le chrome, le molybdène ou le nickel. Ces poudres sont spécifiquement conçues pour améliorer les propriétés mécaniques, la résistance à l'usure et la ténacité du métal de base. Elles sont couramment utilisées dans la métallurgie des poudres pour fabriquer des pièces qui nécessitent une résistance élevée, une grande durabilité et des dimensions précises.
Les poudres faiblement alliées sont populaires dans les applications qui exigent des matériaux aux propriétés mécaniques supérieures à celles des métaux purs ou des matériaux fortement alliés. La sélection minutieuse des éléments d'alliage dans les poudres faiblement alliées garantit que le produit final peut résister à des conditions extrêmes, telles que des températures élevées, des environnements corrosifs et des charges lourdes.
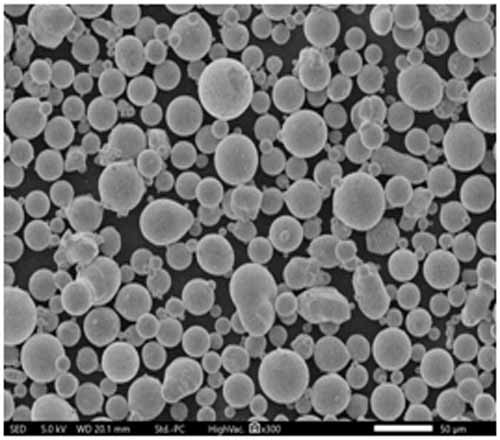
Principales caractéristiques des poudres faiblement alliées
Paramètres | Description |
---|---|
Composition | Métal de base avec des éléments d'alliage 1-5% tels que Mo, Cr, Ni |
Propriétés | Haute résistance, résistance à l'usure, ténacité et dureté améliorées |
Applications courantes | Composants automobiles, pièces pour l'aérospatiale, outils et machines lourdes |
Processus de fabrication | Atomisation, frittage et pressage isostatique à chaud (HIP) |
Éléments d'alliage typiques | Chrome, molybdène, nickel, manganèse, vanadium, titane |
Avantages | Propriétés mécaniques améliorées, rentables, polyvalentes |
Composition des poudres faiblement alliées
Il est essentiel de comprendre la composition des poudres faiblement alliées pour sélectionner le matériau adéquat pour une application spécifique. Le métal de base de ces poudres est généralement le fer, mais d'autres métaux comme le nickel et le titane peuvent également être utilisés. Les éléments d'alliage, ajoutés en petites quantités, influencent considérablement les propriétés de la poudre.
Tableau : Éléments d'alliage courants dans les poudres faiblement alliées
Élément d'alliage | Concentration typique (%) | Objectif |
---|---|---|
Chrome (Cr) | 1-3% | Améliore la résistance à la corrosion et la dureté |
Molybdène (Mo) | 0.5-2% | Améliore la résistance aux températures élevées, la résistance à l'usure |
Nickel (Ni) | 1-5% | Augmente la ténacité et la ductilité |
Vanadium (V) | 0.1-1% | Améliore l'affinage du grain et la résistance à l'usure |
Titane (Ti) | 0.1-0.5% | Améliore la solidité et la résistance à la corrosion |
Manganèse (Mn) | 0.5-2% | Augmente la trempabilité, la résistance à l'usure |
Pourquoi ces éléments ?
- Chrome (Cr): Connu pour son excellente résistance à la corrosion, le chrome est un élément clé des poudres faiblement alliées conçues pour les environnements difficiles. Il améliore également la dureté, ce qui rend le produit final plus durable.
- Molybdène (Mo): Cet élément est essentiel pour les applications nécessitant une résistance élevée à des températures élevées. Le molybdène améliore la résistance à l'usure, garantissant la longévité des composants tels que les engrenages et les arbres.
- Nickel (Ni): Le nickel améliore la ténacité et la ductilité des poudres faiblement alliées, ce qui les rend adaptées aux pièces qui subissent des contraintes ou des déformations importantes.
- Vanadium (V): Le vanadium est essentiel à l'affinage du grain, qui améliore les propriétés mécaniques générales du matériau, y compris la résistance à l'usure.
- Titane (Ti): L'ajout de titane aux poudres faiblement alliées renforce la solidité tout en maintenant la résistance à la corrosion, ce qui le rend idéal pour les applications aérospatiales.
Caractéristiques des Poudre faiblement alliée
Les caractéristiques des poudres faiblement alliées sont adaptées grâce à une sélection minutieuse des éléments d'alliage et à un contrôle précis du processus de fabrication. Ces caractéristiques déterminent l'adéquation de la poudre à diverses applications.
Tableau : Caractéristiques de la poudre faiblement alliée
Caractéristique | Description |
---|---|
Haute résistance | Les poudres faiblement alliées sont conçues pour produire des pièces d'une résistance supérieure. |
Résistance à l'usure | Résistance accrue à l'usure grâce à la présence d'éléments tels que le Mo et le Cr. |
Solidité | L'amélioration de la ténacité permet d'obtenir de meilleures performances dans les applications exigeantes. |
Résistance à la corrosion | Les éléments d'alliage tels que le Cr et le Ti offrent une excellente résistance à la corrosion. |
Stabilité dimensionnelle | Les pièces fabriquées à partir de poudres faiblement alliées conservent leurs dimensions même sous contrainte. |
Résistance à la fatigue | L'excellente résistance à la fatigue rend ces poudres idéales pour les charges cycliques. |
Pourquoi ces caractéristiques sont-elles importantes ?
- Haute résistance: La résistance est une considération primordiale dans les applications où les pièces sont soumises à de lourdes charges ou à des pressions élevées. Les poudres faiblement alliées sont conçues pour produire des composants qui peuvent résister à ces conditions sans défaillance.
- Résistance à l'usure: Dans les industries telles que l'automobile et l'outillage, les pièces subissent souvent des frottements et de l'usure. La résistance à l'usure des poudres faiblement alliées permet de prolonger la durée de vie des pièces, réduisant ainsi la nécessité de les remplacer fréquemment.
- Solidité: La ténacité est la capacité d'un matériau à absorber l'énergie et à se déformer sans se rompre. Cette propriété est essentielle pour les pièces qui doivent supporter des chocs ou des contraintes sans se fracturer.
- Résistance à la corrosion: La corrosion peut réduire considérablement la durée de vie d'un composant. Les poudres faiblement alliées contenant des éléments tels que le chrome offrent une résistance supérieure à la corrosion, ce qui les rend idéales pour une utilisation dans des environnements difficiles.
- Stabilité dimensionnelle: Le maintien de dimensions précises est essentiel dans des industries telles que l'aérospatiale et l'automobile, où même des écarts mineurs peuvent entraîner des problèmes importants. Les poudres faiblement alliées garantissent la stabilité des pièces dans des conditions variables.
- Résistance à la fatigue: La résistance à la fatigue est vitale pour les composants qui subissent des cycles de charge répétés. Les poudres faiblement alliées sont conçues pour résister à ces conditions sans succomber à la fatigue.
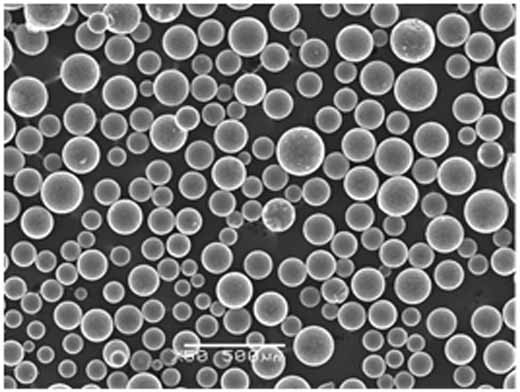
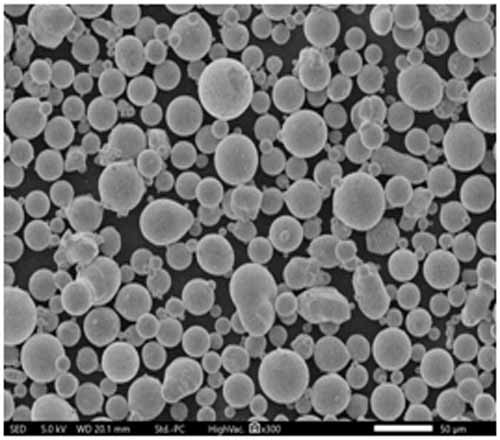
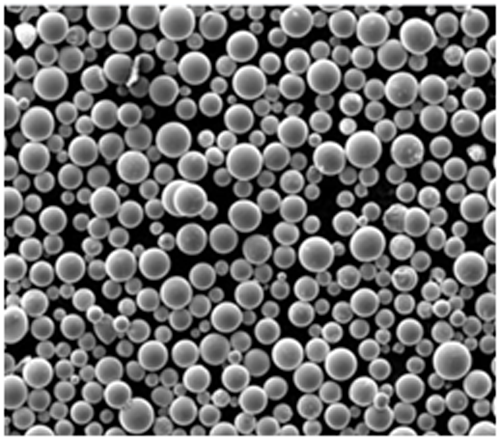
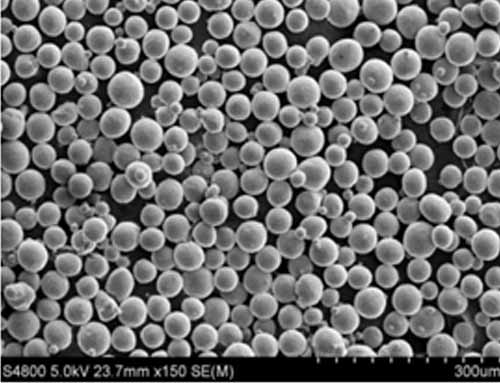
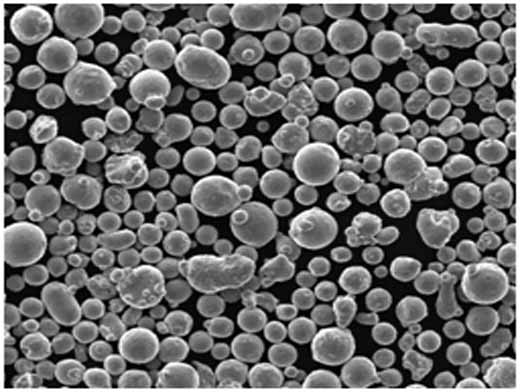
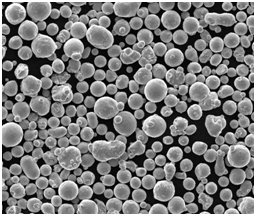
Applications des poudres faiblement alliées
Les poudres faiblement alliées sont incroyablement polyvalentes et sont utilisées dans un large éventail d'industries. Leur capacité à améliorer les propriétés mécaniques les rend idéales pour les applications nécessitant résistance, durabilité et précision.
Tableau : Applications courantes des poudres faiblement alliées
L'industrie | application | Avantages |
---|---|---|
Automobile | Engrenages, roulements, arbres à cames, bielles | Haute résistance, résistance à l'usure, résistance à la fatigue |
Aérospatiale | Aubes de turbines, composants de moteurs, pièces de structure | Légèreté, haute résistance, résistance à la corrosion |
Outillage | Outils de coupe, moules, matrices | Résistance à l'usure, ténacité, précision |
Machines lourdes | Boîtes de vitesses, composants hydrauliques | Solidité, durabilité, résistance à la corrosion |
Pétrole et gaz | Trépans, vannes, pipelines | Résistance élevée, résistance à l'usure et à la corrosion |
Médical | Implants, outils chirurgicaux | Biocompatibilité, solidité, résistance à la corrosion |
Défense | Véhicules blindés, systèmes d'armes | Ténacité, résistance à l'usure, solidité |
Électronique | Connecteurs, boîtiers | Stabilité dimensionnelle, résistance à la corrosion |
L'énergie | Composants d'éoliennes, pièces de réacteurs nucléaires | Solidité, résistance à la fatigue, résistance à la corrosion |
Marine | Hélices, composants du moteur | Résistance à la corrosion, résistance à l'usure, ténacité |
Exemples concrets
- Automobile: Dans l'industrie automobile, les poudres faiblement alliées sont utilisées pour fabriquer des composants critiques tels que les engrenages et les arbres à cames. Ces pièces nécessitent une résistance élevée et une grande résistance à l'usure pour supporter les contraintes du fonctionnement du moteur.
- Aérospatiale: Les aubes de turbines des moteurs à réaction sont souvent fabriquées à partir de poudres faiblement alliées en raison de leur capacité à conserver leur résistance et leur stabilité à des températures élevées, garantissant ainsi un fonctionnement sûr et efficace.
- Médical: Les outils chirurgicaux et les implants doivent être à la fois solides et biocompatibles. Les poudres faiblement alliées au titane sont couramment utilisées pour répondre à ces exigences et fournir des dispositifs médicaux durables et sûrs.
Avantages de la poudre faiblement alliée
Les poudres faiblement alliées offrent une combinaison unique de propriétés qui les rendent très avantageuses dans diverses applications. Examinons les avantages spécifiques qui distinguent ces poudres des autres matériaux.
Tableau : Avantages de la poudre faiblement alliée
Avantage | Description |
---|---|
Rapport coût-efficacité | Les poudres faiblement alliées sont généralement plus abordables que les poudres fortement alliées. |
Polyvalence | Convient à un large éventail d'applications dans différentes industries. |
Propriétés mécaniques améliorées | Amélioration de la solidité, de la résistance à l'usure et de la ténacité par rapport aux métaux purs. |
Adaptabilité | La composition peut être ajustée pour répondre aux exigences spécifiques de l'application. |
Précision dimensionnelle | Idéal pour la fabrication de pièces aux dimensions précises et aux tolérances serrées. |
Résistance à l'environnement | Offre une excellente résistance à la corrosion, à la chaleur et à l'usure dans les environnements difficiles. |
Pourquoi ces avantages sont-ils importants ?
- Rapport coût-efficacité: Les poudres faiblement alliées constituent une solution rentable pour la fabrication de composants à haute performance. Comparées aux poudres fortement alliées, elles offrent des avantages similaires à un prix inférieur, ce qui en fait une option attrayante pour les industries soucieuses de leurs coûts.
- Polyvalence: La possibilité d'utiliser des poudres faiblement alliées dans une variété d'industries - de l'automobile à l'aérospatiale - démontre leur polyvalence. Cela en fait un matériau de choix pour les fabricants qui cherchent à optimiser les performances dans différentes applications.
- Propriétés mécaniques améliorées: L'ajout d'éléments d'alliage améliore considérablement les propriétés mécaniques du métal de base. Il en résulte des composants plus solides et plus durables, capables de résister à des conditions difficiles.
- Adaptabilité: L'un des principaux avantages des poudres faiblement alliées est la possibilité d'adapter leur composition à des exigences spécifiques. Cela permet aux fabricants d'optimiser le matériau pour des applications particulières, qu'il s'agisse d'une meilleure résistance à l'usure, d'une plus grande solidité ou d'une meilleure résistance à la corrosion.
- Précision dimensionnelle: Les poudres faiblement alliées sont idéales pour la production de pièces aux tolérances serrées et aux dimensions précises. Ceci est particulièrement important dans des industries telles que l'aérospatiale et l'automobile, où même des écarts mineurs peuvent entraîner des problèmes importants.
- Résistance à l'environnement: Dans les applications où les composants sont exposés à des environnements difficiles, tels que des températures élevées ou des substances corrosives, les poudres faiblement alliées offrent une résistance supérieure, garantissant une durée de vie plus longue et des coûts de maintenance réduits.
Inconvénients et limites des poudres faiblement alliées
Si les poudres faiblement alliées offrent de nombreux avantages, elles présentent également certaines limites qui doivent être prises en compte lors de la sélection des matériaux pour des applications spécifiques.
Tableau : Inconvénients et limites de la poudre faiblement alliée
Inconvénient | Description |
---|---|
Gamme limitée d'éléments d'alliage | Le pourcentage d'éléments d'alliage est limité, ce qui peut restreindre les propriétés. |
Ne convient pas aux environnements extrêmes | Des poudres fortement alliées peuvent être nécessaires pour des conditions plus extrêmes. |
Complexité de traitement | Nécessite un contrôle précis lors de la fabrication pour obtenir les propriétés souhaitées. |
Risque de fragilité | Certaines poudres faiblement alliées peuvent devenir cassantes si elles ne sont pas traitées correctement. |
Résistance limitée à la corrosion | Bien qu'améliorée, la résistance à la corrosion peut ne pas atteindre celle des aciers inoxydables. |
L'importance de ces limitations
- Gamme limitée d'éléments d'alliage: La gamme d'éléments d'alliage dans les poudres faiblement alliées est limitée à environ 1-5%. Cela peut limiter la capacité du matériau à atteindre certaines propriétés, en particulier par rapport aux poudres fortement alliées qui peuvent contenir des pourcentages plus élevés d'éléments d'alliage.
- Ne convient pas aux environnements extrêmes: Pour les applications dans des conditions extrêmement difficiles, telles que les environnements à haute température ou les atmosphères hautement corrosives, les poudres fortement alliées peuvent constituer un meilleur choix. Les poudres faiblement alliées peuvent ne pas fournir la protection ou les performances nécessaires dans ces scénarios.
- Complexité de traitement: Le processus de fabrication des poudres faiblement alliées nécessite un contrôle précis pour obtenir les propriétés souhaitées. Tout écart dans le processus peut aboutir à un produit qui ne répond pas aux spécifications requises, entraînant des défaillances potentielles ou des performances réduites.
- Risque de fragilité: Si elles ne sont pas traitées correctement, les poudres faiblement alliées peuvent devenir cassantes, ce qui les rend susceptibles de se fissurer ou de se briser sous l'effet d'une contrainte. Ce phénomène est particulièrement préoccupant dans les applications où la ténacité est essentielle.
- Résistance limitée à la corrosion: Si les poudres faiblement alliées offrent une meilleure résistance à la corrosion que les métaux purs, elles peuvent néanmoins ne pas offrir la même protection que des matériaux tels que l'acier inoxydable, en particulier dans les environnements très corrosifs.
Modèles spécifiques de poudre métallique
Les poudres faiblement alliées se déclinent en différents modèles, chacun étant conçu pour répondre à des exigences spécifiques. Voici dix exemples de modèles populaires de poudres faiblement alliées, avec leur description et leurs applications.
Tableau : Modèles populaires de poudres faiblement alliées
Modèle | Composition | Propriétés | Applications |
---|---|---|---|
FeMo10 | Fe + 10% Mo | Haute résistance, excellente résistance à l'usure | Engrenages automobiles, composants aérospatiaux |
FeNi5 | Fe + 5% Ni | Ténacité et ductilité accrues | Pièces structurelles, connecteurs |
FeCr3 | Fe + 3% Cr | Résistance accrue à la corrosion, bonne dureté | Composants marins, outils |
FeV1 | Fe + 1% V | Amélioration de la résistance à l'usure, affinage du grain | Outils de coupe, pièces soumises à de fortes contraintes |
FeMn2 | Fe + 2% Mn | Meilleure trempabilité, meilleure résistance à l'usure | Roulements, arbres, engrenages |
FeMo2Ni4 | Fe + 2% Mo + 4% Ni | Résistance et robustesse équilibrées | Pièces structurelles pour l'aérospatiale, l'automobile |
FeCrMoNi | Fe + Cr + Mo + Ni (ratios personnalisables) | Propriétés polyvalentes, adaptées à des applications spécifiques | Multitude d'industries |
FeTi0,5 | Fe + 0,5 % Ti | Solidité accrue, bonne résistance à la corrosion | Fixations aérospatiales, implants médicaux |
FeMnCrNiV | Fe + Mn + Cr + Ni + V (mélange personnalisé) | Résistance à l'usure, ténacité et résistance à la corrosion supérieures | Des composants performants |
FeMoCrNi2V1 | Fe + Mo + Cr + Ni + V | Haute résistance, excellente résistance à l'usure et à la corrosion | Pétrole et gaz, composants aérospatiaux |
Descriptions détaillées
- FeMo10: Ce modèle contient du fer avec 10 % de molybdène, ce qui lui confère une grande solidité et une excellente résistance à l'usure. Il est couramment utilisé dans les industries automobile et aérospatiale pour des composants tels que les engrenages et les pièces structurelles qui doivent résister à de fortes contraintes et à l'usure.
- FeNi5: Composé de 5 % de nickel, le FeNi5 offre une résistance et une ductilité accrues, ce qui le rend idéal pour les pièces structurelles et les connecteurs qui requièrent durabilité et flexibilité.
- FeCr3: Avec 3 % de chrome, ce modèle offre une meilleure résistance à la corrosion et une bonne dureté. Il convient parfaitement aux composants marins et aux outils qui doivent résister à des environnements corrosifs.
- FeV1: Avec 1% de vanadium, le FeV1 améliore la résistance à l'usure et favorise l'affinement du grain, ce qui en fait un choix populaire pour les outils de coupe et les pièces soumises à de fortes contraintes.
- FeMn2: Ce modèle contient 2 % de manganèse, ce qui améliore la trempabilité et la résistance à l'usure. Il est souvent utilisé dans les roulements, les arbres et les engrenages où ces propriétés sont cruciales.
- FeMo2Ni4: Mélange équilibré de 2 % de molybdène et de 4 % de nickel, ce modèle offre un bon équilibre entre résistance et ténacité, ce qui le rend adapté aux pièces structurelles de l'aérospatiale et aux applications automobiles.
- FeCrMoNi: Ce modèle personnalisable permet d'obtenir des propriétés sur mesure en ajustant les ratios de chrome, de molybdène et de nickel. Il est utilisé dans de nombreuses industries où des propriétés spécifiques sont requises.
- FeTi0,5: Avec 0,5 % de titane, ce modèle offre une solidité accrue et une bonne résistance à la corrosion, ce qui le rend idéal pour les fixations aérospatiales et les implants médicaux.
- FeMnCrNiV: Mélange personnalisé de manganèse, de chrome, de nickel et de vanadium, ce modèle offre une résistance à l'usure, une ténacité et une résistance à la corrosion supérieures, adaptées aux composants de haute performance.
- FeMoCrNi2V1: Combinant le molybdène, le chrome, le nickel et le vanadium, ce modèle offre une grande solidité et une excellente résistance à l'usure et à la corrosion, ce qui le rend parfait pour les applications exigeantes dans les secteurs du pétrole, du gaz et de l'aérospatiale.
Spécifications, tailles et normes
Les poudres faiblement alliées sont disponibles en différentes tailles et qualités, conformément aux normes industrielles qui garantissent la qualité et la cohérence. Les spécifications de ces poudres sont essentielles pour déterminer si elles conviennent à des applications spécifiques.
Tableau : Spécifications, tailles et normes des poudres faiblement alliées
Spécifications | Description |
---|---|
Taille des particules | Gamme de 10 à 150 microns, en fonction de l'application |
La pureté | Généralement >99%, avec un contrôle strict des impuretés |
Grade | Varie selon l'application, y compris les qualités standard comme ASTM F75 |
Densité | Typiquement 7,8 g/cm³ pour les poudres à base de fer |
Capacité d'écoulement | Mesuré à l'aide d'un débitmètre à effet Hall, généralement 30-50 s/50g |
Normes | ASTM B213, ASTM B962, ISO 4497, ISO 3923 |
Emballage | Disponible en sacs de 25 kg, en fûts ou en emballages personnalisés |
Pourquoi les spécifications sont importantes
- Taille des particules: La taille des particules de poudre est essentielle pour déterminer le comportement de la poudre au cours du traitement. Les petites particules sont généralement utilisées pour des applications nécessitant des détails et une précision plus fins, tandis que les grosses particules peuvent être préférées pour des composants plus volumineux.
- La pureté: Une pureté élevée est essentielle pour garantir que la poudre fonctionne comme prévu, en particulier dans les applications critiques telles que l'aérospatiale ou les dispositifs médicaux. Les impuretés peuvent entraîner des défauts ou des défaillances dans le produit final.
- Grade: La qualité de la poudre détermine son adéquation à des applications spécifiques. Par exemple, l'ASTM F75 est une norme commune pour les alliages de cobalt-chrome-molybdène utilisés dans les implants médicaux.
- Densité: La densité de la poudre affecte son comportement d'emballage et la densité finale du produit fritté. Une densité constante est importante pour obtenir des propriétés uniformes dans la pièce finie.
- Capacité d'écoulement: La fluidité est une mesure de la facilité avec laquelle la poudre s'écoule dans les trémies et autres équipements. Une bonne fluidité est cruciale pour un traitement cohérent et des produits finaux de haute qualité.
- Normes: Le respect des normes industrielles garantit que la poudre répond aux exigences de qualité et de performance nécessaires. Ceci est particulièrement important dans les industries réglementées telles que l'aérospatiale et les appareils médicaux.
- Emballage: Un emballage approprié est important pour protéger la poudre pendant le transport et le stockage. Il permet également de s'assurer que la poudre est livrée dans un état prêt à l'emploi.
Fournisseurs et détails des prix
Choisir le bon fournisseur pour poudre d'alliage faible est essentielle pour garantir la qualité, la cohérence et la fiabilité. Voici un aperçu de quelques-uns des principaux fournisseurs et d’un des plus grands fabricants d’équipements d’information
une vue d'ensemble des tendances en matière de prix.
Tableau : Fournisseurs et détails des prix
Fournisseur | Localisation | Modèles disponibles | Prix (par kg) | Quantité minimale de commande |
---|---|---|---|---|
Hoganas AB | Suède | FeMo10, FeCr3, FeV1 | $25-$40 | 100 kg |
Métallurgie des poudres GKN | ROYAUME-UNI | FeNi5, FeMn2, FeMoCrNi | $30-$50 | 200 kg |
Technologie des charpentiers | ÉTATS-UNIS | FeMo2Ni4, FeTi0,5 | $35-$55 | 50 kg |
Sandvik AB | Suède | FeMnCrNiV, FeMoCrNi2V1 | $40-$60 | 100 kg |
ATI Powder Metals | ÉTATS-UNIS | FeCrMoNi, FeV1 | $30-$45 | 150 kg |
Kennametal | ÉTATS-UNIS | FeCr3, FeMo10 | $35-$50 | 100 kg |
Comprendre la tarification
- Variation de la tarification: Le prix des poudres faiblement alliées peut varier considérablement en fonction de facteurs tels que la composition, la pureté et la localisation du fournisseur. Des pourcentages plus élevés d'éléments d'alliage tels que le molybdène ou le nickel augmentent généralement le prix.
- Quantité minimale de commande (MOQ): Le MOQ est un facteur important pour les entreprises, en particulier pour les plus petites d'entre elles. Les fournisseurs exigent généralement des commandes plus importantes pour justifier les coûts de production et d'expédition, mais certains d'entre eux offrent une plus grande souplesse en proposant des QMo moins élevés.
- Considérations géographiques: La localisation du fournisseur peut également avoir une incidence sur les prix en raison des frais d'expédition, des droits d'importation/d'exportation et des réglementations locales. Par exemple, les fournisseurs européens peuvent pratiquer des prix plus élevés en raison de réglementations environnementales plus strictes.
Comparaison des avantages et des inconvénients des poudres faiblement alliées
Lors du choix d'une poudre faiblement alliée, il est essentiel de peser le pour et le contre des différents modèles. Voici une comparaison qui vous aidera à prendre une décision en connaissance de cause.
Tableau : Comparaison des options de poudres faiblement alliées
Modèle | Pour | Cons |
---|---|---|
FeMo10 | Haute résistance, excellente résistance à l'usure | Coût plus élevé en raison de la teneur en molybdène |
FeNi5 | Ténacité et ductilité accrues | Résistance à la corrosion inférieure à celle des modèles FeCr |
FeCr3 | Bonne résistance à la corrosion, dureté | Ténacité limitée, peut nécessiter un alliage supplémentaire |
FeV1 | Amélioration de la résistance à l'usure, affinage du grain | Peut être cassant s'il n'est pas traité correctement |
FeMn2 | Amélioration de la trempabilité, rentabilité | Résistance inférieure à celle des modèles FeMo ou FeNi |
FeMo2Ni4 | Résistance et robustesse équilibrées | Prix moyen, peut ne pas offrir une résistance extrême à la corrosion |
FeCrMoNi | Propriétés personnalisables, application polyvalente | Traitement complexe, coût plus élevé |
FeTi0,5 | Solidité accrue, bonne résistance à la corrosion | Limité aux applications nécessitant une faible ténacité |
FeMnCrNiV | Résistance supérieure à l'usure et à la corrosion | Coût plus élevé, traitement complexe |
FeMoCrNi2V1 | Haute résistance, excellente résistance à l'usure et à la corrosion | Traitement le plus coûteux et le plus complexe |
Quel est le modèle qui vous convient ?
- Si vous avez besoin d'une résistance élevée et d'une résistance à l'usure, considérez FeMo10. Toutefois, il faut s'attendre à un coût légèrement plus élevé en raison de la teneur en molybdène.
- Pour les applications nécessitant ténacité et ductilité, FeNi5 est un choix solide, bien qu'il n'offre pas le même niveau de résistance à la corrosion que les modèles à plus forte teneur en chrome.
- Vous recherchez une résistance à la corrosion ? FeCr3 est une excellente option, bien qu'il faille envisager un alliage supplémentaire si vous avez besoin d'une plus grande résistance.
- Si la résistance à l'usure est votre principale préoccupation, FeV1 offre de meilleures performances, mais il faut se méfier de la fragilité si elle n'est pas traitée correctement.
- Pour une solution économique avec une bonne trempabilité, FeMn2 vaut la peine d'être envisagé, même s'il n'atteint pas la puissance des modèles plus onéreux.
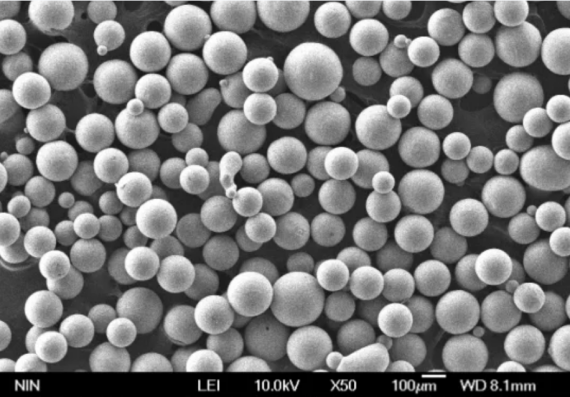
FAQ
Question | Réponse |
---|---|
À quoi sert la poudre faiblement alliée ? | Les poudres faiblement alliées sont utilisées dans des industries telles que l'automobile, l'aérospatiale et l'outillage pour fabriquer des composants durables à haute résistance. |
Comment la poudre d'alliage faible est-elle fabriquée ? | Les poudres faiblement alliées sont généralement fabriquées par atomisation, suivie d'un frittage ou d'un pressage isostatique à chaud (HIP). |
Quels sont les avantages de l'utilisation de poudre faiblement alliée ? | Les avantages sont notamment l'amélioration des propriétés mécaniques, la rentabilité et la polyvalence dans diverses applications. |
Quelles sont les limites de la poudre faiblement alliée ? | Les limites sont notamment une gamme restreinte d'éléments d'alliage, une fragilité potentielle et une adaptation limitée aux environnements extrêmes. |
Comment choisir la bonne poudre faiblement alliée ? | Lors du choix d'une poudre faiblement alliée, il faut tenir compte de facteurs tels que la résistance requise, la résistance à l'usure, la résistance à la corrosion et le coût. |
Les poudres faiblement alliées peuvent-elles être personnalisées ? | Oui, les poudres faiblement alliées peuvent être adaptées en ajustant la composition des éléments d'alliage pour répondre à des exigences spécifiques. |
Les poudres faiblement alliées sont-elles chères ? | Le prix varie en fonction de la composition et du fournisseur, mais les poudres faiblement alliées sont généralement plus abordables que les poudres fortement alliées. |
Quelles sont les industries qui utilisent des poudres faiblement alliées ? | Les principales industries sont l'automobile, l'aérospatiale, le pétrole et le gaz, l'outillage et les dispositifs médicaux. |
Les poudres faiblement alliées sont-elles adaptées aux environnements difficiles ? | Bien qu'elles offrent une meilleure résistance à l'usure et à la corrosion, les poudres faiblement alliées peuvent ne pas convenir à des environnements extrêmement difficiles, où des poudres fortement alliées pourraient être nécessaires. |
Comment la qualité de la poudre faiblement alliée est-elle garantie ? | La qualité est assurée par le respect des normes industrielles telles que ASTM et ISO, ainsi que par un contrôle strict de la pureté et de la taille des particules. |
Conclusion
Poudres faiblement alliées sont des matériaux indispensables à la fabrication moderne, offrant une combinaison unique de propriétés qui les rend aptes à une large gamme d'applications. Des pièces automobiles aux composants aérospatiaux, ces poudres offrent la solidité, la durabilité et la précision nécessaires aux industries de haute performance d'aujourd'hui.
En comprenant la composition, les caractéristiques et les applications des poudres faiblement alliées, ainsi que les avantages et les limites des différents modèles, vous pouvez prendre des décisions éclairées sur le matériau le mieux adapté à vos besoins spécifiques. Que vous cherchiez à optimiser les performances, à réduire les coûts ou à assurer la longévité, les poudres faiblement alliées offrent une solution polyvalente qui peut être adaptée à vos besoins.
N'oubliez pas de prendre en compte tous les facteurs, y compris la composition, le coût, la fiabilité du fournisseur et les besoins spécifiques de l'application, lorsque vous choisissez la poudre faiblement alliée adaptée à votre projet. En faisant le bon choix, vous pouvez obtenir des résultats supérieurs et assurer la réussite de vos projets de fabrication.