Vue d'ensemble Impression 3D par jet de liant
L'impression 3D par jet de liant (BJ3DP) est un processus de fabrication additive de pointe qui se distingue par sa capacité à produire à grande échelle des pièces métalliques complexes et très résistantes. Contrairement à d'autres technologies d'impression 3D, l'impression à jet de liant n'implique pas la fusion du matériau, ce qui permet des temps de production plus rapides, une consommation d'énergie moindre et la possibilité de travailler avec une large gamme de matériaux, en particulier les poudres métalliques.
Cette technologie est particulièrement avantageuse dans les secteurs où la précision, l'efficacité et la flexibilité des matériaux sont essentielles. Qu'il s'agisse de l'aérospatiale, de l'automobile ou même de la santé, l'impression 3D par jet de liant fait des vagues en offrant une solution rentable et évolutive pour la production de composants métalliques complexes.
La science derrière l'impression 3D par jet de liant
Le principe de fonctionnement du Binder Jetting est relativement simple. Un liant - un adhésif liquide - est déposé sélectivement sur un lit de poudre, couche par couche. Les zones où le liant est appliqué durcissent pour former la forme souhaitée, tandis que la poudre environnante reste libre et peut être réutilisée. Une fois que l'objet est entièrement formé, il subit une étape de post-traitement, telle que le frittage, pour atteindre sa densité et sa résistance finales.
Comment fonctionne l'impression 3D par jet de liant ?
- Étape 1 : Superposition de la poudre: Une fine couche de poudre métallique est étalée sur la plate-forme de construction.
- Étape 2 : Reliure: Une tête d'impression dépose sélectivement du liant sur la poudre, formant ainsi la forme de la pièce.
- Étape 3 : Répétition: Le processus se répète, couche par couche, jusqu'à ce que la pièce entière soit construite.
- Étape 4 : Durcissement: La pièce est laissée à durcir, ce qui solidifie le liant.
- Étape 5 : Frittage: L'étape finale consiste à chauffer la pièce dans un four pour fusionner les particules de poudre et obtenir les propriétés mécaniques souhaitées.
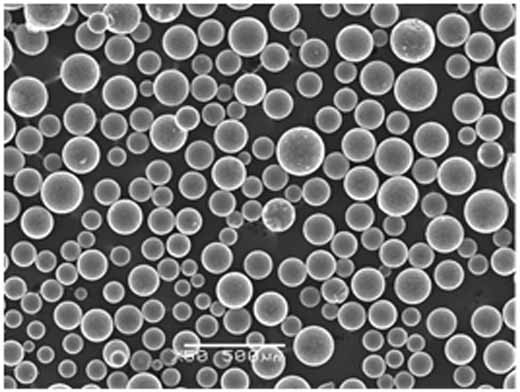
Principales caractéristiques de l'impression 3D à jet de liant
Caractéristique | Description |
---|---|
Polyvalence des matériaux | Fonctionne avec une large gamme de poudres métalliques, y compris l'acier inoxydable, le titane et l'Inconel. |
Vitesse | Plus rapide que les autres méthodes d'impression 3D de métaux, car elle ne nécessite pas de faire fondre le matériau. |
Rapport coût-efficacité | Réduction des coûts d'exploitation grâce à une moindre consommation d'énergie et à la possibilité de réutiliser la poudre. |
Finition de la surface | Nécessite généralement un post-traitement pour obtenir des finitions lisses. |
Résistance de la pièce | Comparable aux pièces fabriquées traditionnellement après le frittage. |
Évolutivité | Bien adapté à la production simultanée de plusieurs pièces. |
Avantages de la Impression 3D par jet de liant
- Efficacité de la production: Par rapport à des méthodes telles que le SLM (Selective Laser Melting), le Binder Jetting est plus rapide et consomme moins d'énergie, ce qui le rend idéal pour la production à grande échelle.
- Flexibilité des matériaux: Capable d'utiliser diverses poudres métalliques, y compris l'acier, l'aluminium et même les matériaux céramiques, ce qui le rend polyvalent pour différentes industries.
- Rentabilité: Avec des besoins énergétiques moindres et la possibilité de réutiliser la poudre non liée, le Binder Jetting est souvent plus économique que d'autres méthodes d'impression 3D.
- Impact sur l'environnement: Cette méthode génère moins de déchets et a une empreinte carbone plus faible, car elle ne fait pas appel à des lasers à haute énergie ou à des faisceaux d'électrons.
Poudres métalliques spécifiques utilisées dans l'impression 3D à jet de liant
Le jet de liant peut fonctionner avec une gamme impressionnante de poudres métalliques. Ci-dessous, nous explorons quelques modèles spécifiques :
Modèle de poudre métallique | Description |
---|---|
Acier inoxydable 316L | Connu pour son excellente résistance à la corrosion et ses propriétés mécaniques, il est idéal pour les applications marines et médicales. |
Acier inoxydable 17-4 PH | Offre une résistance et une dureté élevées, largement utilisées dans les secteurs de l'aérospatiale et de l'armée. |
Inconel 625 | Superalliage à base de nickel présentant une résistance exceptionnelle aux températures élevées, souvent utilisé dans l'industrie aérospatiale. |
Inconel 718 | Un autre alliage à base de nickel, très résistant à l'oxydation et à la corrosion, adapté aux environnements extrêmes. |
Cobalt-Chrome | Extrêmement durable et biocompatible, il est parfait pour les implants dentaires et orthopédiques. |
Cuivre | Offre une excellente conductivité électrique et thermique, utilisée dans l'électronique et les échangeurs de chaleur. |
Titane Ti6Al4V | Léger, très solide et résistant à la corrosion, il est couramment utilisé dans l'aérospatiale et les implants médicaux. |
Aluminium AlSi10Mg | Léger et durable, il est idéal pour les pièces automobiles et aérospatiales où la réduction du poids est essentielle. |
Bronze | Connu pour sa résistance à l'usure et sa faible friction, il est souvent utilisé dans les roulements et les coussinets. |
Tungstène | Haute densité et résistance à la température, convient aux applications nécessitant une grande stabilité thermique, comme dans l'aérospatiale. |
Composition des poudres d'impression 3D à jet de liant
Poudre métallique | Composants primaires | Propriétés |
---|---|---|
Acier inoxydable 316L | Fer, chrome, nickel, molybdène | Résistance élevée à la corrosion, bonne soudabilité. |
Acier inoxydable 17-4 PH | Fer, chrome, nickel, cuivre | Haute résistance, bonne dureté, résistance à la corrosion. |
Inconel 625 | Nickel, chrome, molybdène, niobium | Excellente résistance aux hautes températures et à la corrosion. |
Inconel 718 | Nickel, chrome, fer, niobium, titane | Résistance à l'oxydation, stabilité à haute température. |
Cobalt-Chrome | Cobalt, chrome, molybdène | Biocompatibilité, résistance à l'usure, haute résistance. |
Cuivre | Cuivre | Conductivité électrique et thermique élevée. |
Titane Ti6Al4V | Titane, aluminium, vanadium | Léger, résistant à la corrosion, biocompatible. |
Aluminium AlSi10Mg | Aluminium, Silicium, Magnésium | Léger, bonnes propriétés mécaniques. |
Bronze | Cuivre, étain | Faible friction, résistance à l'usure, anticorrosion. |
Tungstène | Tungstène | Point de fusion élevé, haute densité, résistance. |
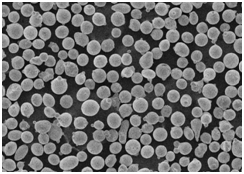
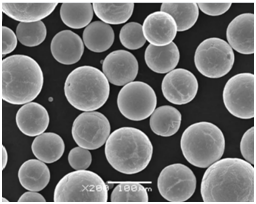
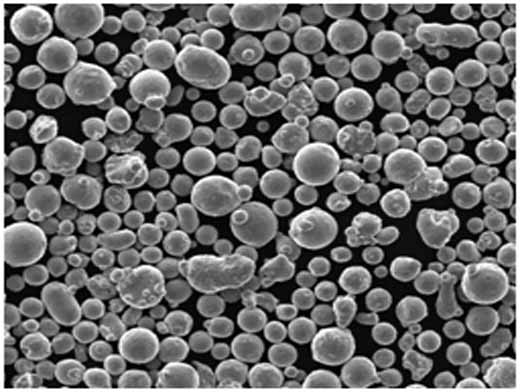
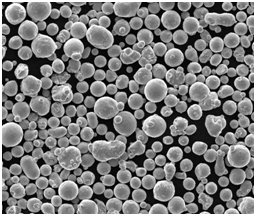
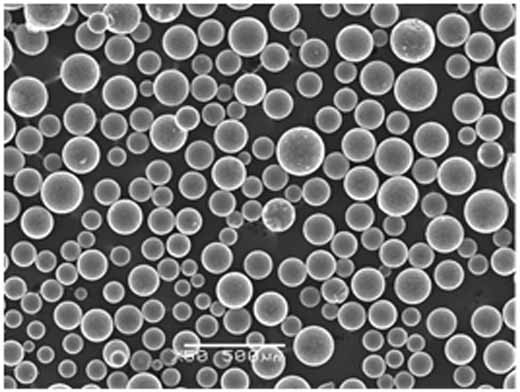
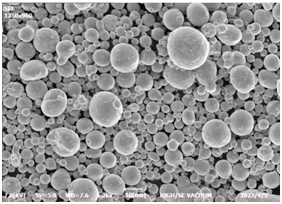
Applications de la Impression 3D par jet de liant
Le jet de liant est utilisé dans diverses industries, où chaque modèle de poudre métallique répond à des objectifs distincts.
L'industrie | application | Modèle de poudre métallique |
---|---|---|
Aérospatiale | Composants de moteurs, aubes de turbines | Inconel 625, Inconel 718 |
Automobile | Pièces légères, prototypes | Aluminium AlSi10Mg, Titane Ti6Al4V |
Médical | Implants orthopédiques, outils chirurgicaux | Titane Ti6Al4V, Cobalt-Chrome |
Marine | Pièces résistantes à la corrosion | Acier inoxydable 316L |
Électronique | Dissipateurs thermiques, connecteurs | Cuivre |
Militaire | Composants d'armes, armures | Acier inoxydable 17-4 PH |
L'énergie | Aubes de turbines, composants nucléaires | Inconel 625, Tungstène |
Bijoux | Bijoux en métal sur mesure | Bronze, Cobalt-Chrome |
Industrie | Roulements, bagues | Bronze, acier inoxydable 316L |
La construction | Pièces de structure, raccords | acier inoxydable 316L, aluminium AlSi10Mg |
Spécifications et normes pour les poudres métalliques
Il est essentiel de comprendre les spécifications, les tailles et les normes des poudres métalliques utilisées dans l'impression 3D par jet de liant pour s'assurer que le produit final répond aux critères de qualité et de performance requis.
Modèle de poudre métallique | Taille des particules (microns) | Densité (g/cm³) | Température de frittage (°C) | Normes |
---|---|---|---|---|
Acier inoxydable 316L | 15-45 | 7.9 | 1250-1400 | ASTM A276, A240 |
Acier inoxydable 17-4 PH | 20-53 | 7.7 | 1200-1300 | AMS 5604, ASTM A564 |
Inconel 625 | 15-45 | 8.4 | 1250-1400 | ASTM B443, B446 |
Inconel 718 | 15-53 | 8.19 | 1250-1400 | AMS 5596, ASTM B637 |
Cobalt-Chrome | 10-45 | 8.3 | 1150-1350 | ASTM F75 |
Cuivre | 15-45 | 8.96 | 1080-1125 | ASTM B152 |
Titane Ti6Al4V | 20-53 | 4.43 | 1250-1400 | ASTM F1472, AMS 4911 |
Aluminium AlSi10Mg | 20-63 | 2.67 | 555-630 | EN 1706, ISO 3522 |
Bronze | 10-45 | 8.7 | 900-950 | ASTM B505 |
Tungstène | 5-45 | 19.3 | 1500-1700 | ASTM B777 |
Impression 3D par jet de liant : Avantages et inconvénients
Pour bien comprendre les avantages et les limites de l'impression 3D par jet de liant, il est essentiel de peser le pour et le contre.
Avantages | Inconvénients |
---|---|
Vitesse: Processus de production rapide | Post-traitement: Nécessite des étapes supplémentaires pour la densification |
Flexibilité des matériaux: Large gamme de poudres utilisables | Finition de la surface: Nécessite souvent un usinage secondaire |
Rapport coût-efficacité: Faibles coûts opérationnels | La force: Les pièces peuvent être moins denses si elles ne sont pas frittées correctement |
Évolutivité: Adapté à la production de masse | Porosité: Possibilité d'une plus grande porosité par rapport à d'autres méthodes |
Impact sur l'environnement: Faible production de déchets | Contraintes de conception: Limité par la fluidité de la poudre et l'adhérence de la couche |
Principaux fournisseurs de poudres métalliques pour Impression 3D par jet de liant
La disponibilité de poudres métalliques de haute qualité est cruciale pour le succès de l'impression 3D par jet de liant. Vous trouverez ci-dessous quelques fournisseurs de premier plan et leurs tarifs.
Fournisseur | Modèles à poudre métallique disponibles | Fourchette de prix (USD/kg) | Localisation |
---|---|---|---|
Hoganas AB | acier inoxydable 316L, acier inoxydable 17-4 PH | 50-100 | Suède |
GKN Additive | Inconel 625, Inconel 718 | 200-400 | ÉTATS-UNIS |
Additif pour charpentier | Titane Ti6Al4V, Cobalt-Chrome | 250-500 | ÉTATS-UNIS |
Sandvik Osprey | Aluminium AlSi10Mg, Bronze | 60-150 | ROYAUME-UNI |
Technologie LPW | Tungstène, cuivre | 100-250 | ROYAUME-UNI |
AP&C | Titane Ti6Al4V, Inconel 718 | 300-600 | Canada |
Tekna | Aluminium AlSi10Mg, Cuivre | 50-200 | Canada |
Arcam AB | Cobalt-Chrome, Titane Ti6Al4V | 200-450 | Suède |
Erasteel | acier inoxydable 316L, bronze | 80-180 | France |
PyroGenesis | Tungstène, Inconel 625 | 150-300 | Canada |
Comparaison de l'impression 3D par jet de liant avec d'autres technologies d'impression 3D
Lorsque vous envisagez de recourir à la technique du jet de liant pour vos besoins de production, il est essentiel de la comparer à d'autres méthodes d'impression 3D populaires telles que la fusion sélective par laser (SLM) et la fusion par faisceau d'électrons (EBM).
Technologie | Vitesse | Gamme de matériaux | Finition de la surface | Coût | Applications typiques |
---|---|---|---|---|---|
Jetting de liant | Presque | Large (métaux, céramiques) | Rugueux, nécessite un post-traitement | Faible (en raison des économies d'énergie) | Production de masse, prototypage |
Fusion sélective par laser (SLM) | Modéré | Métaux | Lisse, détaillé | Élevée (en raison de la consommation d'énergie) | Aérospatiale, implants médicaux |
Fusion par faisceau d'électrons (EBM) | Slow | Limitée (principalement métaux) | Rugueux, mais très résistant | Élevé (en raison du coût de l'équipement) | Aérospatiale, pièces sur mesure |
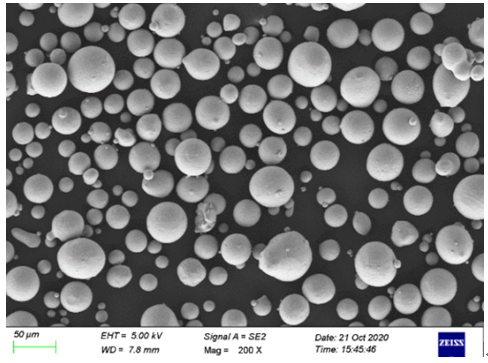
FAQ
Question | Réponse |
---|---|
Quels matériaux peuvent être utilisés dans l'impression 3D par jet de liant ? | Une large gamme de métaux, de céramiques et de composites peut être utilisée, y compris l'acier inoxydable, le titane et l'Inconel. |
Le Binder Jetting est-il plus rapide que les autres méthodes d'impression 3D de métaux ? | Oui, elle est généralement plus rapide car elle ne nécessite pas la fusion de matériaux, ce qui accélère considérablement le processus. |
L'impression 3D Binder Jet produit-elle des pièces solides ? | Oui, après un frittage adéquat, les pièces peuvent atteindre une résistance comparable à celle des pièces fabriquées selon les méthodes traditionnelles. |
Quelles sont les principales industries qui utilisent la projection de liant ? | L'aérospatiale, l'automobile, la médecine et l'électronique sont quelques-uns des secteurs clés qui utilisent cette technologie. |
Le post-traitement est-il toujours nécessaire dans le cas de la projection de liant ? | En général, oui. Un post-traitement tel que le frittage ou l'infiltration est nécessaire pour améliorer les propriétés mécaniques et la finition des pièces. |
Quel est le coût de l'injection de liant par rapport à d'autres méthodes ? | Elle est généralement plus rentable en raison des besoins énergétiques moindres et de la possibilité de réutiliser les poudres. |