Étude sur le rechargement par laser d'un revêtement en poudre à base de nickel
Introduction
Revêtement par laser est l'utilisation de la technologie laser pour revêtir la surface du substrat afin d'obtenir les propriétés requises. Le système d'alliage du revêtement laser comprend principalement les alliages à base de fer, les alliages à base de nickel, les alliages à base de cobalt et les cermets. Le revêtement laser de poudre d'alliage à base de fer convient aux pièces qui doivent être partiellement usées et faciles à déformer. Le substrat du revêtement en alliage à base de fer est principalement la fonte et l'acier à faible teneur en carbone. Les revêtements d'alliages à base de nickel conviennent aux pièces qui nécessitent une résistance partielle à l'usure, une résistance à la corrosion à chaud et une résistance à la fatigue thermique, et la densité de puissance laser requise est légèrement supérieure à celle du revêtement d'alliages à base de fer. Les revêtements en alliage à base de cobalt conviennent aux pièces qui nécessitent une résistance à l'usure, à la corrosion et à la fatigue thermique. Le revêtement céramique présente une résistance élevée à haute température, une bonne stabilité thermique, une grande stabilité chimique et une large gamme de matériaux de matrice. Cet article traite des matériaux en poudre d'alliage autofusible à base de nickel utilisés pour le rechargement par laser.
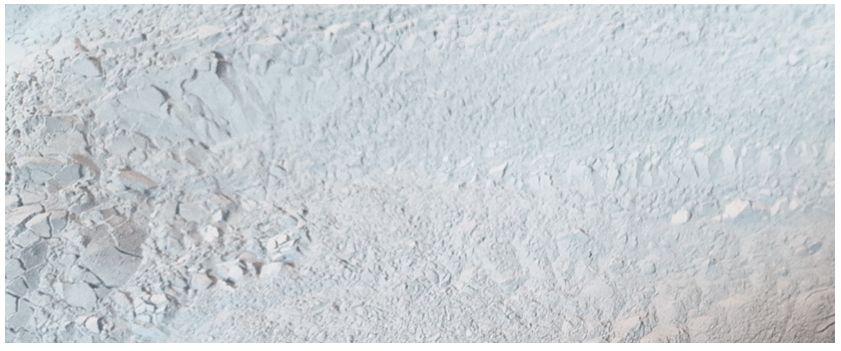
Matériels et méthodes
Les poudre d'alliage d'autofusion à base de nickel utilisée dans cette expérience a été préparée et fondue par atomisation au gaz. Les facteurs à prendre en compte dans la conception de la composition de la poudre et de la formulation de la matière première de fusion sont principalement les suivants : en ce qui concerne les performances de la poudre et le processus de revêtement par laser, la poudre doit avoir un point de fusion et une teneur en oxygène faibles. Afin d'éviter la fissuration du revêtement, la couche de revêtement et le substrat doivent être adaptés autant que possible, c'est-à-dire que le coefficient de dilatation thermique du revêtement et du substrat doit être aussi proche que possible. La mouillabilité et la réaction de la poudre doivent être bonnes.
Sur la base des facteurs susmentionnés, la conception répétée de la composition des matériaux et les essais de performance du processus de soudage par pulvérisation ont permis d'obtenir la poudre d'alliage autofusible à base de nickel suivante BNi-3 (AMS 4778) avec une taille de particule de 45-105um est choisi comme matériau de revêtement laser (fraction de masse %), sa composition chimique est indiquée dans le tableau ci-dessous. Tableau 1. Le matériau de base pour le rechargement au laser est l'acier à teneur moyenne en carbone. L'épaisseur de la couche de revêtement est de 0,6 mm.
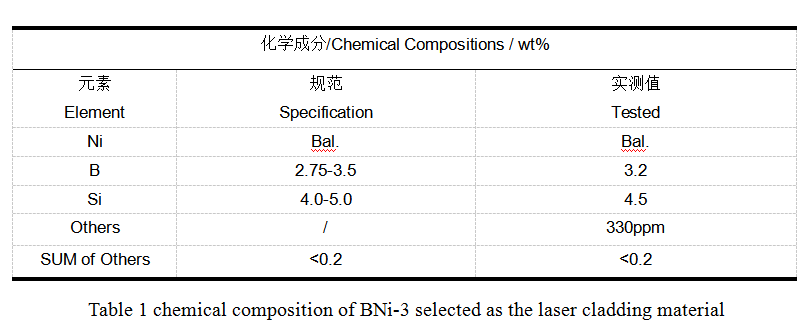
Figure 1 montre la morphologie des particules de BNi-3 choisi comme matériau de revêtement laser. On peut voir que les particules de poudre sont sphériques. La poudre sphérique confère à la poudre une bonne fluidité, de sorte que la poudre peut atteindre la surface de la pièce uniformément et en douceur à partir du chargeur de poudre sans bloquer la buse de poudre. Si la forme de la poudre est complexe, la fluidité est médiocre, ce qui entraîne facilement le transport de la poudre par pulsation. En outre, si la surface de la poudre augmente, la poudre sera oxydée lorsqu'elle est chauffée à haute température, ce qui affectera la qualité de la couche de revêtement.
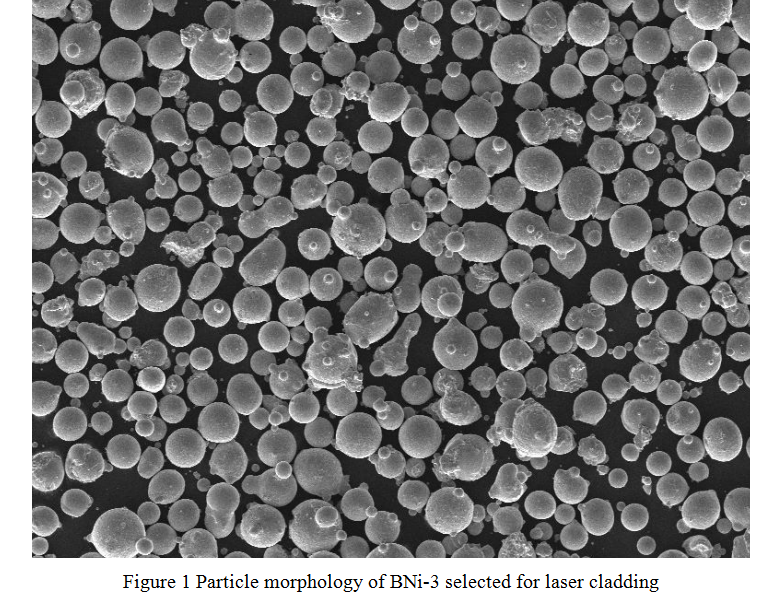
Le test de processus montre que le nickel confère à la poudre de bonnes performances en matière de placage et peut améliorer les performances à haute température et la résistance à la fissuration de la poudre. Le silicium contenu dans l'alliage augmente la dureté du revêtement. Le silicium et le bore peuvent rendre la poudre d'alliage autofusible. Dans la poudre d'alliage autofusible, le bore et le silicium peuvent former des scories par eux-mêmes, ce qui a un effet d'autoprotection. L'analyse montre que le Ni2B et le Ni3B à bas point de fusion sont formés à partir du bore et du nickel, ce qui réduit le point de fusion de l'alliage et améliore les performances de la poudre. Toutefois, si la teneur en bore de l'alliage est trop élevée, il y aura plus de composés de bore et de composés d'oxyde de silicate fragiles dans le joint de grain, de sorte que la plasticité et la ténacité du revêtement seront réduites, la fragilité sera accrue et la couche de revêtement sera sujette à des fissures ; la teneur en bore doit donc être contrôlée dans une fourchette appropriée.
Figure2 montre la section transversale de la couche de revêtement. De la couche de surface au noyau, la zone de la couche de revêtement, la zone affectée thermiquement et la matrice se succèdent. La zone de la couche de revêtement est une zone brillante très étroite, plus étroite que la zone de liaison métallurgique obtenue par pulvérisation thermique, soudage en surface et autres méthodes. La zone affectée thermiquement est équivalente au traitement thermique dû à la conduction de la chaleur. Avec l'augmentation de la distance de la zone de la couche de revêtement, la température de chauffage diminue continuellement, de sorte que la zone de transition de phase, une partie de la zone de transition de phase, et enfin la structure originale de la matrice.
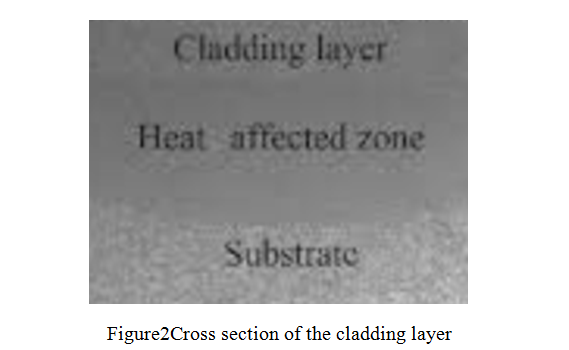
Dans ce projet, la résistance à l'usure de l'échantillon revêtu de cette poudre a été comparée au bloc d'essai standard AISI 52100 avec 62 HRC dans les conditions d'essai de la machine d'essai d'usure domestique MM-200, à une vitesse de 380 r/min, frottement sec, durée 1,5 h. La résistance à l'usure est déterminée en mesurant la perte de poids des échantillons après l'usure. Les résultats ont montré que la résistance à l'usure de la couche de renforcement de la surface du revêtement laser de l'acier inoxydable était supérieure à celle de la couche de renforcement de la surface de l'acier inoxydable. poudre BNi-3 à base de nickel est meilleure que celle de l'AISI 52100, de sorte que la durée de vie des pièces résistantes à l'usure sera considérablement améliorée.