poudre métallique atomisée au gaz s'est imposée comme une méthode de production privilégiée pour les poudres d'alliage sphériques aux attributs contrôlés, idéales pour la fabrication additive, le moulage par injection de poudre et d'autres applications de pointe. Ce guide fournit un aperçu complet des compositions, des propriétés, des processus de fabrication, des fournisseurs clés et des avantages comparatifs des poudres atomisées au gaz par rapport aux alternatives telles que les matériaux atomisés à l'eau.
Chimie des alliages pour les poudres métalliques atomisées au gaz
L'atomisation au gaz permet de transformer presque n'importe quel alliage en poudre, y compris :
Superalliages de nickel avec une résistance élevée due au renforcement en solution solide par des métaux réfractaires tels que le tantale, le tungstène, le molybdène, etc. Largement utilisé dans les composants aérospatiaux.
Superalliages au cobalt avec une excellente résistance à la chaleur et à l'usure. Les grades biocompatibles sont utilisés dans les implants dentaires et les dispositifs médicaux.
Alliages d'acier à outils comme le H13 amélioré avec du vanadium, du molybdène et du tungstène pour conserver la dureté à haute température. Essentiel pour les outils de formage des métaux.
Poudres d'acier inoxydable y compris les grades 304, 316 et 17-4 à durcissement par précipitation pour une combinaison de résistance à la corrosion et de performance mécanique.
Alliages de cuivre tels que le cuivre au béryllium ou le cuivre au chrome et au zirconium, largement formulés en sphères pour les applications de gestion thermique exploitant la conductivité thermique.
Alliages d'aluminium comme 2024, 6061 et 7075 sont des options économiques pour les composants structurels légers fabriqués par fusion sur lit de poudre ou par moulage par injection de métal.
Alliages exotiques y compris les métaux lourds en tungstène, les verres métalliques en vrac et les métaux précieux tels que l'or et le platine bénéficient des taux de trempe rapides de l'atomisation au gaz pour geler dans des phases métastables non équilibrées propres aux poudres.
Matières réactives comme le titane et le tantale, qui ont une grande affinité pour l'oxygène et l'azote, peuvent être atomisés sous vide à l'aide de gaz inertes de grande pureté qui empêchent toute contamination.
Caractéristiques des Poudres métalliques atomisées au gaz
Attribut | Valeurs typiques | Importance |
---|---|---|
Forme des particules | Principalement sphérique | Améliore l'écoulement de la poudre et la densité de l'emballage |
Satellite fraction | <5% | L'impression sur lit de poudre est plus efficace si elle est plus basse |
Gamme de tailles | 10 à 150 microns | Adaptable à la méthode d'application |
Distribution | gaussien | Cohérent d'un lot à l'autre |
Oxygène ppm | 500 ppm | Prévient les inclusions d'oxyde dans la pièce finale |
Oxydes de surface | Fine couche passivée | Maintient la recyclabilité de la poudre |
La combinaison de la propreté, de la morphologie sphérique et de la distribution optimisée de la taille des particules permet aux poudres atomisées d'offrir des performances supérieures à la plupart des techniques de métallurgie des poudres et d'additifs par rapport à d'autres solutions.
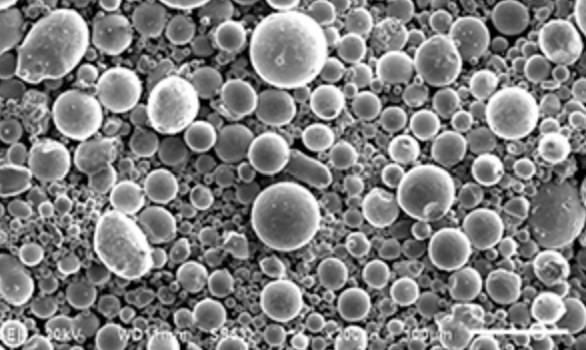
Fonctionnement de la production de poudres par atomisation gazeuse
Les poudres atomisées au gaz sont fabriquées à partir de lingots d'alliages corroyés. Le métal est fondu par induction sous vide ou sous atmosphère inerte, puis il est éjecté sous la forme d'un mince filet dans des jets d'argon ou d'azote à grande vitesse. La puissance du gaz supersonique impactant le métal en fusion brise le flux en fines gouttelettes qui se solidifient rapidement pendant le vol en dessous du point de fusion. La vitesse de refroidissement dépasse 106 °C par seconde, ce qui transforme l'alliage en particules de poudre solide qui s'accumulent dans les trémies de collecte situées sous la tour d'atomisation. En ajustant la pression du gaz, les paramètres de débit et la géométrie des buses, la distribution de la taille des particules peut être adaptée à différentes applications. Le gaz inerte empêche l'oxydation et limite la contamination. Après classification pour éliminer les particules trop grosses, la poudre est emballée sous vide et prête à l'emploi.
Applications industrielles des poudres métalliques atomisées au gaz
L'industrie | Utilisations et composants | Attributs critiques |
---|---|---|
Aérospatiale | Aubes de turbines, profils aérodynamiques | Haute résistance, résistance au fluage |
Médical | Implants et dispositifs orthopédiques | Biocompatibilité, résistance à la corrosion |
Automobile | Bielles, engrenages | Résistance à l'usure, durée de vie |
Fabrication additive | Pièces imprimées en 3D pour le prototypage de la forme et de l'ajustement, l'inventaire numérique, les essais fonctionnels | Morphologie sphérique, fluidité |
Moulage par injection de métal | Petites pièces complexes telles que buses, attaches, etc. | Spécification cohérente de la poudre |
Pulvérisation thermique | Revêtements résistants à l'usure sur les surfaces de roulement | Distribution contrôlée de la taille des particules |
Les poudres atomisées au gaz répondent à des besoins spécifiques dans cette large gamme d'applications, bénéficiant de propriétés telles que la propreté, la forme sphérique, une métallurgie stable, une taille de particule contrôlée et des lots de poudres reproductibles.
Préciser Poudres métalliques atomisées au gaz
Les utilisateurs industriels et les concepteurs choisissent les poudres atomisées au gaz en fonction de paramètres tels que :
Gamme de taille des particules - Les poudres sont généralement comprises entre 10 et 150 microns, en fonction de la taille de la pièce finale et des limites de la méthode de production. Les poudres plus petites s'emballent mieux mais présentent des risques d'explosion ou d'inhalation de poussières. Les particules plus grosses nuisent à la finition de la surface.
Chimie - composition de l'alliage adaptée à l'environnement d'exploitation. Tenir compte de la résistance, de la dureté, de la résistance à la corrosion, de la biocompatibilité, etc. Adapter la poudre aux spécifications de l'application prévue.
Méthode de production - compatible avec la taille et la forme des particules visées. Les systèmes à lit laser nécessitent des poudres sphériques de moins de 100 microns. Les pièces MIM utilisent des poudres de 10 à 25 microns comme matière première.
Normes de qualité - Les normes internationales relatives aux matériaux spécifient les fourchettes admissibles des niveaux d'impureté, les statistiques sur les particules, les méthodes de fabrication, etc. Les normes les plus courantes sont les normes ISO, ASTM, ASME qui régissent le contrôle de la qualité pendant l'atomisation.
Taille du terrain - les tailles de lots typiques de 25 à 500 kg influencent la fixation des prix. Équilibrer les coûts de détention des stocks.
Budget - Les alliages spéciaux à distribution serrée coûtent beaucoup plus cher que les poudres d'acier inoxydable de base. Il convient de hiérarchiser les attributs indispensables en fonction des besoins de performance et de les valider par des essais.
Analyse comparative - Atomisation à gaz et atomisation à l'eau
Paramètres | Gaz Atomisé | Eau pulvérisée |
---|---|---|
Coût | Plus coûteux en raison de l'utilisation de gaz inerte et de buses spécialisées | Réduction des coûts d'exploitation |
Productivité | Rendement inférieur en kg/heure | Possibilité de volumes très élevés |
Forme des particules | Principalement sphérique | Irrégulier en forme d'éclaboussure |
Taille des particules | Minimum environ 10 microns | Descendre en dessous d'un micron |
Répartition par taille | Un contrôle et un réglage plus serrés | Une plus grande variabilité |
Flexibilité de l'alliage | Excellente atmosphère inerte | Limité pour les compositions réactives |
Contamination | Captage minimal d'oxygène | Teneur en oxygène plus élevée |
L'atomisation au gaz excelle dans la production de poudres sphériques à partir d'alliages exotiques ou réactifs nécessaires à la fabrication additive. L'atomisation à l'eau est limitée par les formes irrégulières et les choix de matériaux, mais elle est économique pour les poudres à haut volume de plus de 30 microns pour les procédés traditionnels de pressage et de frittage.
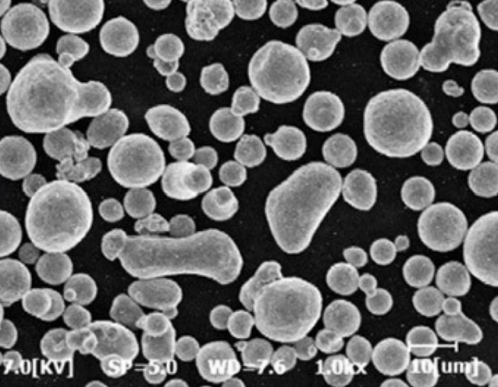
FAQ
Quel est le coût de la poudre atomisée au gaz par rapport aux formes de produits corroyés ?
Les coûts unitaires sont de 2 à 4 fois supérieurs à ceux des produits moulés ou corroyés par kilogramme. Mais la très faible perte de ferraille et la capacité de mise en forme nette de la métallurgie des poudres permettent de réduire le coût global des pièces de grande valeur.
Quelles sont les causes des variations d'un lot à l'autre dans les poudres atomisées au gaz ?
Le contrôle des paramètres du processus, tels que la pression du gaz, la dynamique du flux et la stabilité du flux de matière fondue, est essentiel pour assurer la cohérence. La composition peut dériver sur de longues séries de production. Un échantillonnage et des tests périodiques sont essentiels pour valider la qualité de la poudre par rapport aux spécifications avant d'expédier les lots aux clients.
Comment déterminer le gaz optimal pour l'atomisation ?
L'azote est le moins cher, mais il peut réagir avec des alliages comme le titane. L'argon est inerte, mais des goulets d'étranglement dans l'approvisionnement ont récemment fait grimper les prix. On utilise souvent les deux - atomisation à l'azote, puis à l'argon pour le transport. L'hydrogène fragilise certains alliages. L'hélium est cher et sa disponibilité est limitée.
Comment la poudre est-elle manipulée pour les applications de pulvérisation thermique ?
Cela dépend de la conception du système d'alimentation. La plupart des systèmes hvof et certains systèmes plasma utilisent des trémies avec injection de poudre par gravité/mécanique. Les torches à plasma plus sophistiquées utilisent l'injection de poudre par gaz porteur pour un meilleur transfert de chaleur et une meilleure accélération des particules. Des particules plus grosses sont généralement nécessaires.
Quels sont les problèmes techniques courants liés aux poudres atomisées au gaz ?
Contrôle de la cohérence de la distribution de la taille des particules d'un lot à l'autre. Prévenir la surchauffe des buses. Séparation des fractions fines et grossières. Gestion du comportement pyrophorique. Gérer les effets de la perte d'éléments mineurs par vaporisation. Atténuation de la génération de particules satellites.
Conclusion
En résumé, les poudres métalliques atomisées au gaz offrent une forme sphérique unique des particules, une flexibilité des alliages et une ultra-propreté vitale pour la production contemporaine de métallurgie des poudres dans diverses applications de pointe. La collaboration avec des fournisseurs experts pendant les phases de spécification et d'essai des poudres garantit l'obtention de lots de poudres personnalisés réellement optimisés pour le processus de fabrication de l'utilisation finale et les exigences de performance des composants.