개요
첨단 재료는 제조, 엔지니어링 및 기술 분야를 혁신하고 있습니다. 3D 프린팅에 사용되는 금속 분말부터 항공 우주 분야의 첨단 복합 재료에 이르기까지, 이러한 재료는 기존 재료로는 따라올 수 없는 향상된 특성을 제공합니다. 이를 통해 제조업체는 더 가볍고, 더 강하며, 더 내구성이 뛰어난 제품을 만들 수 있으며, 동시에 효율성을 개선하고 비용을 절감할 수 있습니다.
이 기사에서는 금속 분말에 초점을 맞춰 첨단 재료의 세계를 탐구할 것입니다. 유형, 구성, 특성 및 응용 분야에 대해 자세히 알아볼 것입니다. 또한, 다양한 금속 분말을 비교하고, 장단점을 분석하며, 자세한 사양 및 가격 정보를 제공할 것입니다.
이 가이드는 엔지니어, 디자이너 및 미래를 만들어가는 최첨단 기술에 관심 있는 모든 사람에게 특히 유용할 것입니다.
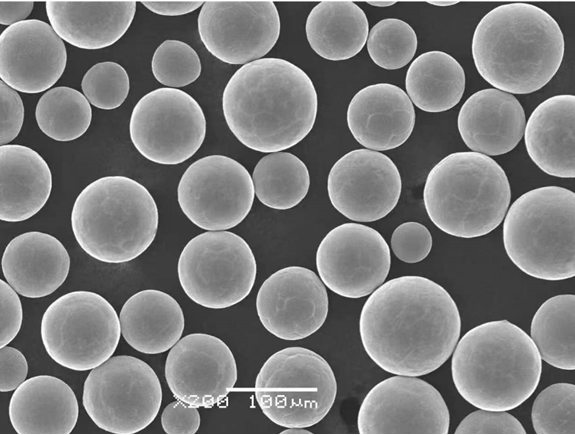
첨단 금속 분말의 유형 및 구성
첨단 금속 분말은 항공 우주, 자동차, 의료 및 전자 등 다양한 산업 분야에서 사용됩니다. 이러한 분말은 미세하게 분할된 금속으로, 작은 크기와 높은 표면적으로 인해 독특한 특성을 나타냅니다.
현대 제조를 선도하는 10가지 특정 금속 분말 모델을 살펴보겠습니다.
금속 분말 모델 | 구성 | 속성 | 애플리케이션 | 제조 방법 |
---|---|---|---|---|
알루미늄 6061 분말 | Al, Mg, Si | 경량, 내식성, 고강도 | 항공 우주, 자동차 부품, 구조 부품 | 가스 분무 |
스테인리스 스틸 316L 파우더 | Fe, Cr, Ni, Mo | 우수한 내식성, 고강도, 우수한 용접성 | 의료 임플란트, 식품 가공 장비, 해양 응용 분야 | 물 분무 |
티타늄 Ti-6Al-4V 분말 | Ti, Al, V | 높은 강도 대 중량비, 생체 적합성, 내식성 | 항공 우주, 의료 임플란트, 군사 응용 분야 | 플라즈마 분무 |
인코넬 718 파우더 | Ni, Cr, Fe, Nb | 고온 저항성, 내식성, 고온에서 강도 유지 | 가스 터빈, 원자로, 항공 우주 부품 | 가스 분무 |
구리 C11000 분말 | Cu | 우수한 전기 전도성, 우수한 열 전도성, 내식성 | 전기 부품, 열 교환기, 자동차 라디에이터 | 전해 정제 |
코발트-크롬(Co-Cr) 분말 | Co, Cr, Mo | 높은 내마모성, 생체 적합성, 내식성 | 치과 임플란트, 정형외과 임플란트, 항공 우주 | 가스 분무 |
알루미늄 AlSi10Mg 분말 | Al, Si, Mg | 경량, 고강도, 우수한 열 전도성 | 자동차, 항공 우주, 툴링 | 가스 분무 |
니켈 625 파우더 | Ni, Cr, Mo, Nb | 우수한 내식성, 우수한 용접성, 고강도 | 해양 응용 분야, 화학 처리, 항공 우주 | 가스 분무 |
텅스텐 W 분말 | W | 고밀도, 높은 융점, 우수한 내마모성 | 방위 응용 분야, 전자 제품, 방사선 차폐 | 수소 감축 |
마그네슘 AZ91D 분말 | Mg, Al, Zn | 경량, 우수한 강도 대 중량비, 내식성 | 자동차 부품, 전자 제품, 항공 우주 | 가스 분무 |
첨단 재료의 구성
첨단 재료, 특히 금속 분말의 구성은 특성 및 응용 분야에 큰 영향을 미칩니다. 특정 응용 분야에 적합한 재료를 선택하려면 원소 구성을 이해하는 것이 중요합니다.
알루미늄 6061 분말: 주로 알루미늄으로 구성되며, 마그네슘과 실리콘이 합금 원소로 사용됩니다. 이 조합은 재료의 강도와 내식성을 향상시켜 구조 부품에 이상적입니다.
스테인리스 스틸 316L 파우더: 철, 크롬, 니켈 및 몰리브덴의 합금입니다. 크롬은 우수한 내식성을 제공하는 반면, 니켈은 인성과 강도를 더하여 의료 및 해양 환경에 적합하게 만듭니다.
티타늄 Ti-6Al-4V 분말: 알루미늄과 바나듐을 포함하는 인기 있는 티타늄 합금입니다. 이 합금은 높은 강도 대 중량비를 제공하며 생체 적합성이 뛰어나 항공 우주 및 의료 임플란트에 적합합니다.
인코넬 718 파우더: 니켈, 크롬 및 철로 구성되며, 강화를 위해 니오브와 같은 추가 원소가 포함됩니다. 이 합금은 극한의 온도와 부식성 환경을 견딜 수 있어 가스 터빈 및 원자로에 이상적입니다.
구리 C11000 분말: 우수한 전기 및 열 전도성으로 알려진 순수 구리 분말입니다. 이는 전기 부품 및 열 교환기에 필수적입니다.
코발트-크롬(Co-Cr) 분말: 코발트, 크롬 및 몰리브덴의 혼합물입니다. 내마모성과 생체 적합성으로 알려져 의료 임플란트 및 고마모 항공 우주 부품에 적합합니다.
알루미늄 AlSi10Mg 분말: 실리콘과 마그네슘을 함유한 알루미늄 합금으로, 우수한 강도와 열 전도성을 제공하며 자동차 및 항공 우주 응용 분야에 일반적으로 사용됩니다.
니켈 625 파우더: 니켈, 크롬, 몰리브덴 및 니오브의 합금으로, 우수한 내식성과 고강도를 제공하며 해양 및 화학 처리 산업에서 사용됩니다.
텅스텐 W 분말: 고밀도와 높은 융점으로 알려진 순수 텅스텐으로, 방위, 전자 및 방사선 차폐 응용 분야에 사용됩니다.
마그네슘 AZ91D 분말: 알루미늄과 아연을 함유한 마그네슘 합금으로, 자동차 및 항공 우주 부품에 사용되는 우수한 강도를 가진 경량 솔루션을 제공합니다.
첨단 재료의 특성
이러한 첨단 금속 분말의 특성을 이해하는 것은 특정 응용 분야에 대한 적합성을 결정하는 데 매우 중요합니다. 주요 특성에 대한 분석은 다음과 같습니다.
금속 분말 모델 | 밀도(g/cm³) | 녹는점(°C) | 열 전도성(W/m-K) | 인장 강도(MPa) |
---|---|---|---|---|
알루미늄 6061 분말 | 2.70 | 582 – 652 | 167 | 310 – 350 |
스테인리스 스틸 316L 파우더 | 7.99 | 1371 – 1399 | 16 | 485 – 620 |
티타늄 Ti-6Al-4V 분말 | 4.43 | 1604 – 1660 | 6.7 | 900 – 1200 |
인코넬 718 파우더 | 8.19 | 1290 – 1350 | 11.4 | 965 – 1185 |
구리 C11000 분말 | 8.96 | 1085 | 401 | 210 – 300 |
코발트-크롬(Co-Cr) 분말 | 8.29 | 1330 – 1400 | 14.1 | 655 – 1045 |
알루미늄 AlSi10Mg 분말 | 2.68 | 570 – 660 | 151 | 320 – 360 |
니켈 625 파우더 | 8.44 | 1290 – 1350 | 9.8 | 827 – 1034 |
텅스텐 W 분말 | 19.25 | 3422 | 173 | 1510 – 1960 |
마그네슘 AZ91D 분말 | 1.81 | 595 – 640 | 76 | 160 – 230 |
밀도 및 강도
밀도와 인장 강도는 특정 응용 분야에 적합한 재료를 선택하는 데 중요한 매개변수입니다. 예를 들어, 텅스텐 W 분말 는 매우 높은 밀도(19.25g/cm³)와 인장 강도(1510 – 1960MPa)를 가지고 있어 방위 및 방사선 차폐와 같은 고성능 응용 분야에 이상적입니다. 반면에, 마그네슘 AZ91D 분말 는 밀도가 1.81g/cm³로 가장 가벼운 옵션 중 하나이므로 경량 자동차 부품에 적합합니다.
열 속성
열 전도성은 또 다른 중요한 특성입니다. 구리 C11000 분말 은 열 전도성이 401W/m·K로 이 분야에서 선두를 달리고 있어 열 교환기 및 전기 응용 분야에 가장 적합한 선택입니다. 반대로, 인코넬 718 파우더 그리고 니켈 625 파우더 는 낮은 열 전도성을 제공하지만 고온 저항성이 뛰어나 항공 우주 및 화학 처리 산업에 적합합니다.
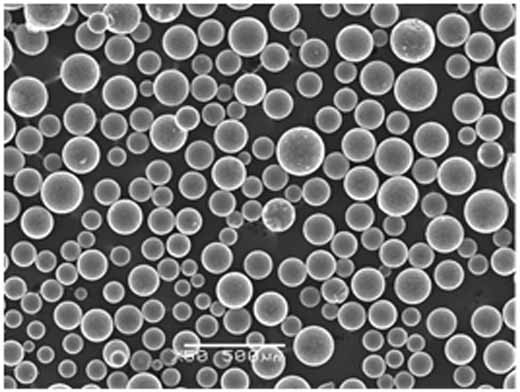
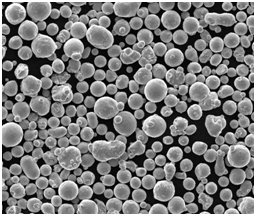
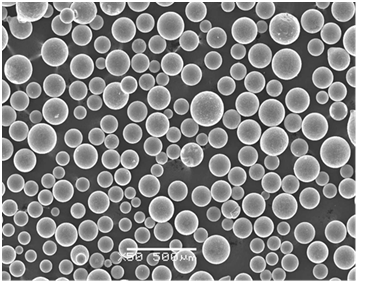
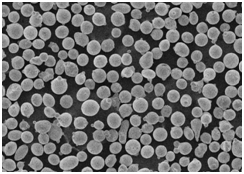
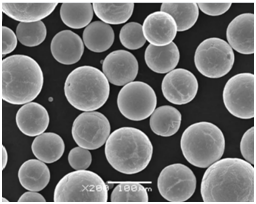
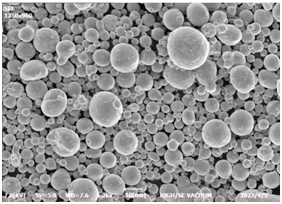
첨단 금속 분말의 응용 분야
첨단 금속 분말은 고유한 특성으로 인해 다양한 산업 분야에서 응용 분야를 찾습니다. 다음은 이러한 분말이 다양한 분야에서 활용되는 방식입니다.
산업 | 사용된 금속 분말 모델 | 애플리케이션 |
---|---|---|
항공우주 | 티타늄 Ti-6Al-4V, 인코넬 718, 알루미늄 AlSi10Mg | 구조 부품, 엔진 부품, 랜딩 기어 |
자동차 | 알루미늄 6061, 마그네슘 AZ91D, 스테인리스강 316L | 엔진 블록, 섀시 부품, 배기 시스템 |
헬스케어 | 스테인리스강 316L, 티타늄 Ti-6Al-4V, 코발트-크롬 | 의료 임플란트, 치과 보철물, 수술 도구 |
전자 제품 | 구리 C11000, 텅스텐 W, 알루미늄 AlSi10Mg | 전기 접점, 방열판, 인쇄 회로 기판 |
해양 | 니켈 625, 스테인리스강 316L, 알루미늄 6061 | 프로펠러, 해양 패스너, 열 교환기 |
방어 | 텅스텐 W, 인코넬 718, 티타늄 Ti-6Al-4V | 관통탄, 군용 차량, 방탄 |
에너지 | 인코넬 718, 니켈 625, 구리 C11000 | 터빈 블레이드, 원자로, 열 교환기 |
툴링 | 코발트-크롬, 스테인리스강 316L, 알루미늄 6061 | 절삭 공구, 금형, 금형 |
항공우주 애플리케이션
항공 우주 산업은 우수한 강도, 경량성 및 고온 저항성으로 인해 첨단 금속 분말에 크게 의존합니다. 예를 들어, 티타늄 Ti-6Al-4V 분말 는 강도와 무게가 가장 중요한 엔진 부품 및 랜딩 기어와 같은 중요한 부품에 사용됩니다. 인코넬 718 파우더 는 극한의 온도를 견딜 수 있는 능력으로 인해 터빈 블레이드에 사용됩니다.
자동차 애플리케이션
자동차 산업에서는 연비와 성능을 향상시키기 위해 경량 및 내구성이 뛰어난 재료가 필요합니다. 알루미늄 6061 분말 그리고 마그네슘 AZ91D 분말 는 엔진 블록 및 섀시 부품에 널리 사용되어 강도와 무게의 균형을 잘 유지합니다. 스테인리스 스틸 316L 파우더 는 내식성을 위해 배기 시스템에 사용됩니다.
사양, 크기 및 표준
적절한 금속 분말을 선택하려면 사양, 크기를 이해하고 산업 표준을 준수해야 합니다. 자세한 개요는 다음과 같습니다.
금속 분말 모델 | 일반적인 입자 크기(µm) | 표준 | 사용 가능한 성적 |
---|---|---|---|
알루미늄 6061 분말 | 20 – 63 | ASTM B928/B928M | AA 6061, AlMg1SiCu |
스테인리스 스틸 316L 파우더 | 15 – 45 | ASTM A240/A240M | 316L, 1.4404 |
티타늄 Ti-6Al-4V 분말 | 25 – 75 | ASTM F1472 | 5학년, 23학년 |
인코넬 718 파우더 | 10 – 53 | ASTM B637 | N07718 |
구리 C11000 분말 | 45 – 150 | ASTM B187 | C11000, ETP |
코발트-크롬(Co-Cr) 분말 | 10 – 63 | ASTM F75 | CoCr28Mo6, CoCr29Mo |
알루미늄 AlSi10Mg 분말 | 15 – 63 | ISO 8062 | AlSi10Mg(A) |
니켈 625 파우더 | 15 – 45 | ASTM B443 | N06625 |
텅스텐 W 분말 | 1 – 5 | ASTM B777 | W1, W2, W4 |
마그네슘 AZ91D 분말 | 20 – 63 | ASTM B93/B93M | AZ91D, MgAl9Zn1 |
입자 크기 및 표준
입자 크기는 적층 제조와 같은 제조 공정에서 금속 분말의 거동에 중요한 역할을 합니다. 예를 들어, 티타늄 Ti-6Al-4V 분말 는 ASTM F1472 표준을 준수하는 25~75µm 범위의 입자 크기로 제공되어 항공 우주 응용 분야의 일관성과 신뢰성을 보장합니다.
등급 및 품질
금속 분말의 등급은 특정 응용 분야에서의 성능에 영향을 미칩니다. 예를 들어, 스테인리스 스틸 316L 파우더 는 의료 임플란트에 이상적인 저탄소 함량과 향상된 내식성으로 알려진 316L 등급으로 제공됩니다.
다양한 금속 분말의 장단점 비교
적절한 금속 분말을 선택하려면 각 옵션의 장단점을 비교해야 합니다. 비교는 다음과 같습니다.
금속 분말 모델 | 장점 | 단점 |
---|---|---|
알루미늄 6061 분말 | 경량, 내식성, 비용 효율성 | 다른 합금에 비해 강도가 낮고, 고온 응용 분야에 적합하지 않음 |
스테인리스 스틸 316L 파우더 | 우수한 내식성, 우수한 용접성, 생체 적합성 | 높은 비용, 낮은 열 전도성 |
티타늄 Ti-6Al-4V 분말 | 높은 강도 대 중량비, 생체 적합성, 내식성 | 비싸고 기계 가공이 어려운 제품 |
인코넬 718 파우더 | 고온 및 내식성, 고온에서 강도 유지 | 높은 비용, 어려운 처리 |
구리 C11000 분말 | 우수한 전기 및 열 전도성, 내식성 | 고밀도, 산화되기 쉬움 |
코발트-크롬(Co-Cr) 분말 | 높은 내마모성, 생체 적합성, 내식성 | 비싸고 기계 가공이 어려운 제품 |
알루미늄 AlSi10Mg 분말 | 경량, 고강도, 우수한 열 전도성 | 낮은 피로 강도, 연성 부족 |
니켈 625 파우더 | 우수한 내식성, 우수한 용접성, 고강도 | 고가, 낮은 열 전도성 |
텅스텐 W 분말 | 고밀도, 높은 융점, 우수한 내마모성 | 처리하기 어렵고 비용이 많이 듭니다. |
마그네슘 AZ91D 분말 | 경량, 우수한 강도 대 중량비, 내식성 | 다른 금속에 비해 강도가 낮고, 분말 형태에서 가연성 |
장점과 단점
각 금속 분말은 고유한 장점과 잠재적인 단점을 제공합니다. 예를 들어, 티타늄 Ti-6Al-4V 분말 는 강도 대 중량비와 생체 적합성으로 인해 항공 우주 및 의료 응용 분야에 이상적입니다. 그러나 비용이 많이 들고 가공이 어려워 특정 프로젝트에 제약이 될 수 있습니다.
구리 C11000 분말 은 타의 추종을 불허하는 전기 및 열 전도성을 제공하여 전자 제품에 필수적입니다. 그러나 높은 밀도와 산화되기 쉬운 특성은 무게와 부식이 문제가 되는 응용 분야에서 단점이 될 수 있습니다.
공급업체 및 가격 세부 정보
공급업체 선택 및 가격 책정은 금속 분말의 품질과 비용 효율성을 보장하는 데 매우 중요합니다. 다음은 주요 공급업체 및 가격 세부 정보에 대한 개요입니다.
공급업체 | 사용 가능한 금속 분말 모델 | 가격 범위(kg당) | 위치 | 스페셜티 |
---|---|---|---|---|
호가나스 AB | 스테인리스강 316L, 인코넬 718, 알루미늄 AlSi10Mg | $50 – $300 | 스웨덴 | 적층 제조용 고품질 금속 분말 |
카펜터 기술 | 티타늄 Ti-6Al-4V, 코발트-크롬, 니켈 625 | $200 – $600 | 미국 | 항공 우주 및 의료 응용 분야를 위한 프리미엄 합금 |
샌드빅 재료 기술 | 텅스텐 W, 스테인리스강 316L, 인코넬 | $100 – $500 | 스웨덴 | 에너지 및 항공우주용 고성능 소재 |
LPW Technology (Carpenter Additive) | 알루미늄 6061, 티타늄 Ti-6Al-4V, 스테인리스강 316L | $150 – $450 | UK | 적층 제조에 맞춤화된 금속 분말 |
GKN 첨가제 | 알루미늄 AlSi10Mg, 스테인리스강 316L, 니켈 625 | $80 – $400 | 독일 | 적층 제조 솔루션 및 금속 분말 |
AP&C(GE 애디티브) | 티타늄 Ti-6Al-4V, 인코넬 718, 스테인리스강 316L | $180 – $550 | 캐나다 | 3D 프린팅 및 적층 제조용 고품질 분말 |
케나메탈 | 텅스텐 W, 코발트-크롬, 니켈 625 | $120 – $600 | 미국 | 내마모성 응용 분야를 위한 특수 분말 |
PyroGenesis Additive | 알루미늄 6061, 티타늄 Ti-6Al-4V, 스테인리스강 316L | $160 – $500 | 캐나다 | 플라즈마 분무를 이용한 적층 제조용 금속 분말 |
텍나 플라즈마 시스템 | 티타늄 Ti-6Al-4V, 스테인리스강 316L, 인코넬 718 | $180 – $550 | 캐나다 | 플라즈마 기술을 사용한 고품질 분말 |
Arcam EBM (GE Additive) | 코발트-크롬, 티타늄 Ti-6Al-4V, 인코넬 718 | $200 – $650 | 스웨덴 | 항공우주 및 의료 산업용 전자빔 용융 분말 |
가격 및 공급업체 선택
가격은 금속 분말 모델 및 공급업체에 따라 크게 다릅니다. 예를 들어, 티타늄 Ti-6Al-4V 분말 Carpenter Technology 및 AP&C와 같은 공급업체의 경우 kg당 200달러에서 600달러까지 다양할 수 있으며, 이는 항공우주 및 의료 분야에서 높은 수요를 반영합니다. 반면에, 알루미늄 6061 분말 은(는) kg당 50달러에서 300달러로 더 저렴하여 자동차 및 일반 제조 분야에 적합합니다.
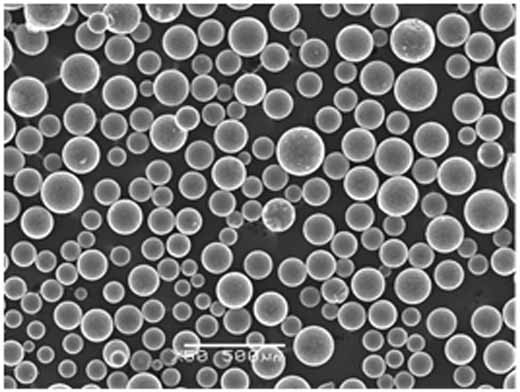
첨단 금속 분말의 장점과 한계
첨단 금속 분말은 수많은 이점을 제공하지만, 특정 한계도 있습니다. 이를 이해하면 정보에 입각한 결정을 내리는 데 도움이 될 수 있습니다.
장점
- 사용자 지정: 첨단 금속 분말은 특정 응용 분야에 맞게 조정할 수 있어 설계 및 제조 유연성을 제공합니다.
- 경량 및 고강도: 알루미늄 및 티타늄 합금과 같은 많은 금속 분말은 항공우주 및 자동차 산업에 필수적인 우수한 강도 대 중량비를 제공합니다.
- 고온 내성: 인코넬 718과 같은 분말은 극한 온도를 견디도록 설계되어 가스 터빈 및 원자로에 이상적입니다.
- 생체 적합성: 티타늄 및 코발트-크롬과 같은 재료는 생체 적합성이 뛰어나 의료용 임플란트에 적합합니다.
- 내식성: 스테인리스강 및 니켈 기반 분말은 해양 및 화학 처리 응용 분야에 필수적인 우수한 내식성을 제공합니다.
제한 사항
- 비용: 첨단 금속 분말은 특히 티타늄 또는 텅스텐과 같이 희귀하거나 가공하기 어려운 재료로 만들어진 경우 비쌀 수 있습니다.
- 처리 과제: 일부 분말은 가공이 어려워 특수 장비와 전문 지식이 필요하므로 생산 비용이 증가할 수 있습니다.
- 산화 및 인화성: 마그네슘과 같은 특정 금속 분말은 산화 및 인화성이 높아 취급 및 보관 시 안전 위험을 초래합니다.
- 가용성: 특정 첨단 금속 분말의 가용성은 공급업체 및 위치에 따라 제한될 수 있으며, 이는 생산 지연으로 이어질 수 있습니다.
자주 묻는 질문
질문 | 답변 |
---|---|
첨단 소재란 무엇인가요? | 첨단 소재는 기존 소재에 비해 더 높은 강도, 더 나은 내구성, 극한 조건에 대한 향상된 저항성과 같은 우수한 특성을 제공하는 새롭고 혁신적인 소재를 말합니다. 금속 분말은 특히 제조 및 3D 프린팅 분야에서 첨단 소재 내에서 중요한 범주입니다. |
금속 분말이 현대 제조에서 중요한 이유는 무엇인가요? | 금속 분말은 복잡한 모양을 만드는 정밀도를 허용하고, 폐기물을 줄이며, 더 가볍고 강하며 효율적인 부품 생산을 가능하게 하므로 현대 제조에서 매우 중요합니다. 항공우주, 자동차, 의료, 전자 등 산업에서 필수적입니다. |
금속 분말을 생산하는 일반적인 방법은 무엇인가요? | 일반적인 방법으로는 가스 분무, 수분 분무, 플라즈마 분무, 전해 정련 등이 있습니다. 각 방법은 입자 크기 및 분포와 같은 분말의 특성에 영향을 미치며, 이는 특정 응용 분야에 대한 적합성에 영향을 미칩니다. |
내 용도에 맞는 금속 분말을 선택하려면 어떻게 해야 하나요? | 올바른 금속 분말을 선택하려면 재료의 조성, 입자 크기, 밀도, 융점 및 특정 응용 분야의 요구 사항과 같은 요소를 고려해야 합니다. 또한 공급업체의 평판, 가격 및 산업 표준 준수 여부를 평가하는 것도 중요합니다. |
금속 분말을 취급하는 것이 안전한가요? | 금속 분말은 일반적으로 안전하지만, 마그네슘이나 알루미늄과 같은 특정 분말은 인화성 또는 반응성으로 인해 위험할 수 있습니다. 위험을 최소화하려면 적절한 취급, 보관 및 안전 예방 조치가 필수적입니다. |
첨단 금속 분말의 가장 큰 수혜 산업은 무엇인가요? | 항공우주, 자동차, 의료, 전자, 방위 산업 및 에너지와 같은 산업은 높은 강도 대 중량비, 내식성 및 생체 적합성과 같은 고유한 특성으로 인해 첨단 금속 분말의 혜택을 크게 받습니다. |
3D 프린팅은 금속 분말을 어떻게 사용하나요? | 3D 프린팅 또는 적층 제조는 금속 분말을 사용하여 부품을 층별로 제작하여 기존 제조 방법으로는 달성하기 어렵거나 불가능한 복잡한 형상을 만들 수 있습니다. 티타늄, 알루미늄 및 스테인리스강과 같은 금속 분말은 항공우주, 자동차 및 의료 응용 분야에서 3D 프린팅에 일반적으로 사용됩니다. |
금속 분말 사용의 환경적 영향은 무엇인가요? | 금속 분말 사용의 환경적 영향은 긍정적일 수도 있고 부정적일 수도 있습니다. 긍정적인 측면으로는 제조 공정에서 재료 폐기물을 줄일 수 있습니다. 그러나 금속 분말 생산은 에너지 집약적일 수 있으며, 특정 분말의 취급은 적절하게 관리하지 않으면 환경적 위험을 초래할 수 있습니다. |
결론
첨단 소재, 특히 금속 분말은 항공우주에서 의료에 이르기까지 다양한 산업에 전례 없는 기능을 제공하며 현대 제조의 최전선에 있습니다. 이러한 재료의 유형, 조성, 특성 및 응용 분야를 이해하는 것은 필요에 맞는 올바른 분말을 선택하는 데 필수적입니다.
다양한 금속 분말의 장점과 한계를 비교하고 공급업체 평판 및 가격과 같은 요소를 고려함으로써 제조업체는 더 나은 제품, 향상된 효율성, 궁극적으로 각 분야에서 더 큰 성공을 거둘 수 있는 정보에 입각한 결정을 내릴 수 있습니다.
기술이 계속 발전함에 따라 첨단 소재의 역할은 더욱 커져 혁신을 주도하고 제품을 설계하고 제조하는 방식을 변화시킬 것입니다.