개요
직접 에너지 증착 (DED)는 재료를 한 층씩 정밀하게 증착하여 고품질의 금속 부품을 제작하는 최첨단 적층 제조 기술입니다. 레이저, 전자 빔 또는 플라즈마 아크와 같은 집중된 에너지원을 사용하여 재료를 녹인 다음 기판 또는 기존 부품에 증착합니다. DED는 복잡한 형상을 제작하고 손상된 부품을 수리하며 우수한 기계적 특성을 가진 고성능 금속 부품을 제작할 수 있는 것으로 잘 알려져 있습니다.
DED는 다목적성과 효율성으로 인해 항공우주, 자동차, 의료, 에너지 등 다양한 산업 분야에서 널리 사용되고 있습니다. 이 기술은 재료 낭비 감소, 생산 시간 단축, 다른 방법으로는 달성하기 어려운 복잡한 디자인 제작 능력 등 기존 제조 방식에 비해 상당한 이점을 제공합니다.
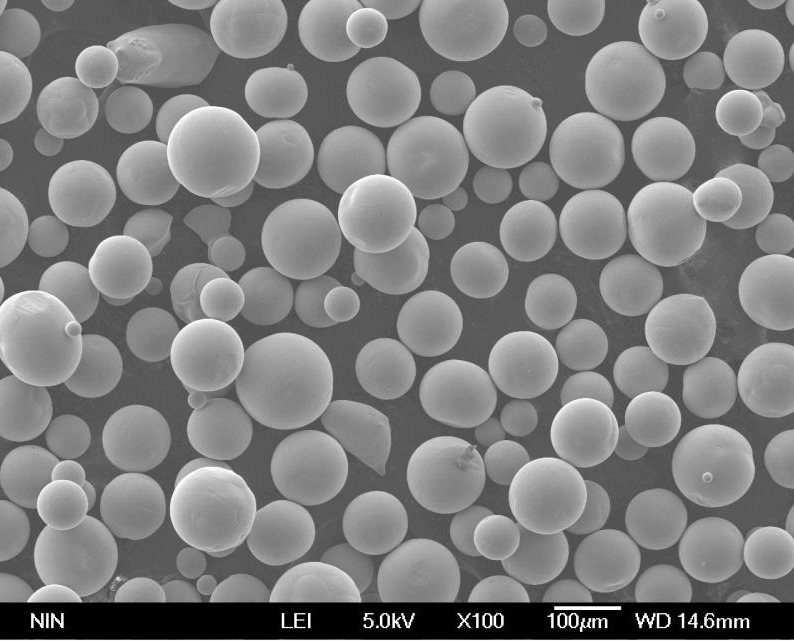
DED에 사용되는 금속 분말의 종류
DED용 일반 금속 분말
금속 분말 모델 | 구성 | 속성 | 애플리케이션 |
---|---|---|---|
인코넬 625 | 니켈, 크롬, 몰리브덴 | 고강도, 내식성 | 항공우주, 해양, 화학 공정 |
TI-6AL-4V | 티타늄, 알루미늄, 바나듐 | 높은 중량 대비 강도, 생체 적합성 | 항공우주, 의료용 임플란트, 자동차 |
스테인리스 스틸 316L | 철, 크롬, 니켈, 몰리브덴 | 높은 내식성, 우수한 기계적 특성 | 식품 가공, 의료 기기, 해양 애플리케이션 |
하스텔로이 X | 니켈, 몰리브덴, 크롬 | 산화 방지, 고온 내구성 | 항공우주, 산업용 가스터빈 |
CoCrMo | 코발트, 크롬, 몰리브덴 | 내마모성, 고강도 | 의료용 임플란트, 치과 보철물 |
AlSi10Mg | 알루미늄, 실리콘, 마그네슘 | 가볍고 우수한 열 전도성 | 자동차, 항공우주, 전자 |
마레이징 스틸(18Ni-300) | 철, 니켈, 코발트, 몰리브덴 | 높은 강도, 뛰어난 인성 | 툴링, 항공우주, 고성능 부품 |
구리 | 순수 구리 | 뛰어난 열 및 전기 전도성 | 전기 부품, 열교환기 |
공구강(H13) | 철, 크롬, 몰리브덴, 바나듐 | 높은 경도, 우수한 내열 피로 저항성 | 툴링, 다이캐스팅, 사출 성형 |
니켈 합금 718 | 니켈, 크롬, 철 | 고강도, 내식성 | 항공우주, 발전, 석유 및 가스 |
DED의 애플리케이션
DED 기술의 일반적인 애플리케이션
애플리케이션 | 산업 | 혜택 |
---|---|---|
구성 요소 수리 | 항공우주, 자동차 | 비용 효율적이고 부품 수명 연장 |
프로토타이핑 | 모든 산업 | 신속한 설계 반복, 리드 타임 단축 |
복잡한 지오메트리 | 의료, 항공우주 | 복잡한 디자인, 경량 구조 지원 |
기능 부품 | 제조, 산업 | 고성능, 맞춤형 구성 요소 |
툴링 및 금형 | 자동차, 제조 | 내구성이 뛰어난 고정밀 도구 |
재료 연구 | 학술, 산업 | 맞춤형 재료 특성, 실험 연구 |
DED 사양 및 표준
DED의 일반적인 금속 분말 사양
금속 분말 모델 | 입자 크기(μm) | 밀도(g/cm³) | 녹는점(°C) | ASTM 표준 |
---|---|---|---|---|
인코넬 625 | 15-45 | 8.44 | 1290-1350 | ASTM B443 |
TI-6AL-4V | 15-45 | 4.43 | 1604-1660 | ASTM B348 |
스테인리스 스틸 316L | 15-45 | 7.99 | 1375-1400 | ASTM A276 |
하스텔로이 X | 15-45 | 8.22 | 1260-1355 | ASTM B435 |
CoCrMo | 15-45 | 8.29 | 1330-1390 | ASTM F75 |
AlSi10Mg | 15-45 | 2.67 | 570-580 | ISO 3522 |
마레이징 스틸(18Ni-300) | 15-45 | 8.00 | 1413 | ASTM A538 |
구리 | 15-45 | 8.96 | 1083 | ASTM B216 |
공구강(H13) | 15-45 | 7.80 | 1426 | ASTM A681 |
니켈 합금 718 | 15-45 | 8.19 | 1260-1336 | ASTM B637 |
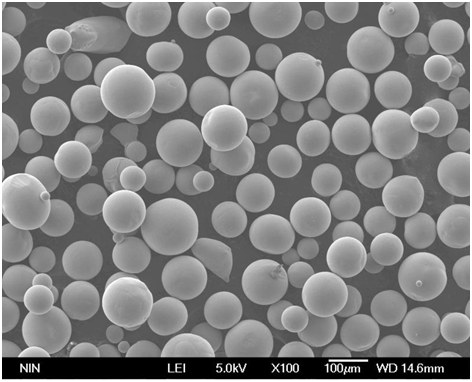
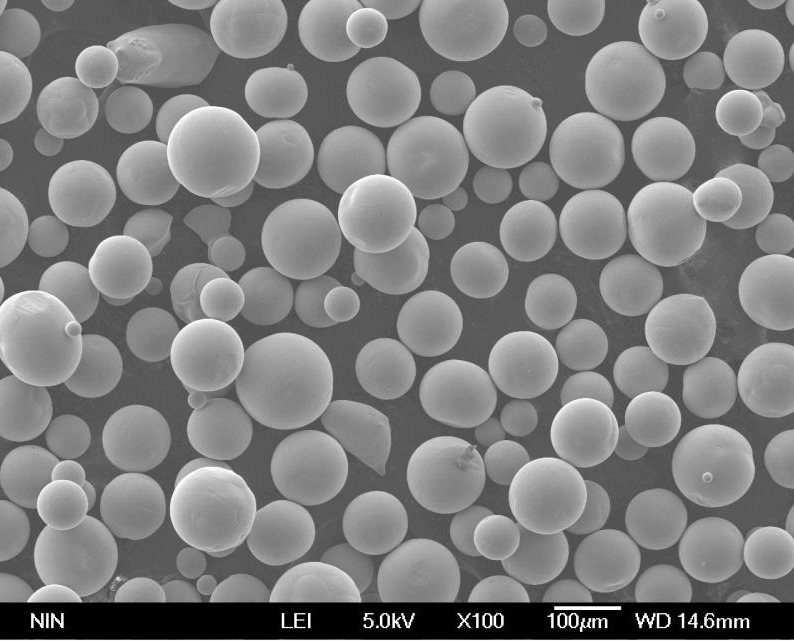
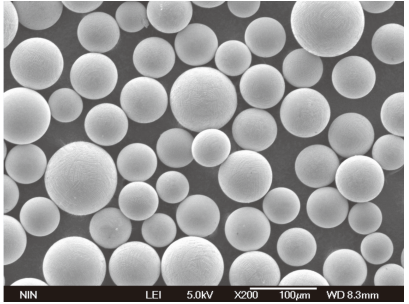
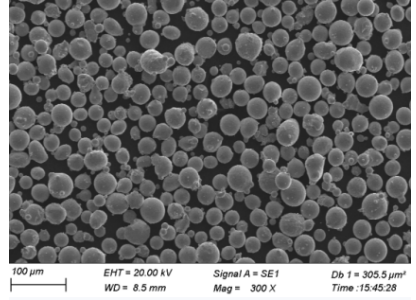
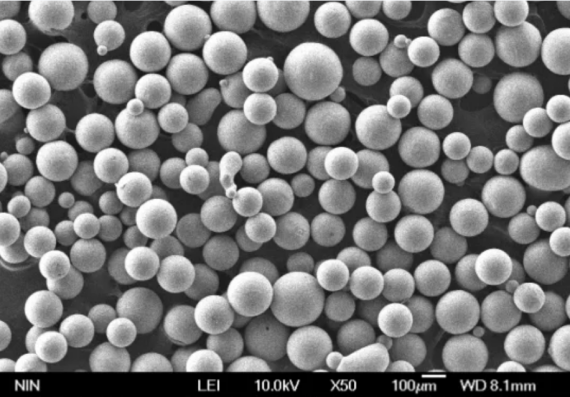
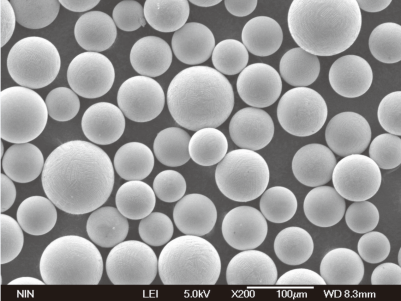
공급업체 및 가격 세부 정보
DED의 금속 분말 공급업체 및 가격
공급업체 | 금속 분말 모델 | kg당 가격(USD) | 위치 | 연락처 |
---|---|---|---|---|
카펜터 기술 | 인코넬 625 | $100 | 미국 | www.carpentertechnology.com |
Arcam AB | TI-6AL-4V | $200 | 스웨덴 | www.arcam.com |
GKN 회가나에스 | 스테인리스 스틸 316L | $50 | 미국 | www.gknpm.com |
HC 스탁 | 하스텔로이 X | $150 | 독일 | www.hcstarck.com |
샌드빅 | CoCrMo | $120 | 스웨덴 | www.materials.sandvik |
LPW 기술 | AlSi10Mg | $80 | UK | www.lpwtechnology.com |
오베르 & 듀발 | 마레이징 스틸(18Ni-300) | $180 | 프랑스 | www.aubertduval.com |
Tekna | 구리 | $60 | 캐나다 | www.tekna.com |
호가나스 AB | 공구강(H13) | $90 | 스웨덴 | www.hoganas.com |
VSMPO-AVISMA | 니켈 합금 718 | $170 | 러시아 | www.vsmpo.ru |
DED 기술의 장단점 비교
DED 기술의 장점과 한계
측면 | 장점 | 제한 사항 |
---|---|---|
재료 효율성 | 낭비 최소화, 높은 재료 활용도 | 높은 초기 재료 비용 |
복잡한 지오메트리 | 복잡한 디자인 제작 가능 | 기계 해상도 및 정확도에 따른 제한 |
수리 기능 | 고가 부품의 효율적인 수리 | 숙련된 운영자와 정밀한 제어가 필요합니다. |
생산 속도 | 기존 방식에 비해 더 빠른 생산 | 다른 적층 제조 방법보다 느림 |
기계적 특성 | 고성능, 사용자 지정 가능한 속성 | 잔류 스트레스 및 결함 가능성 |
다용도성 | 다양한 소재 사용 가능 | 재료 공급원료 가용성에 따라 제한됨 |
DED용 금속 분말의 상세 분석
인코넬 625
인코넬 625는 고온에서도 우수한 기계적 특성과 내식성으로 잘 알려진 니켈 기반 초합금입니다. 니켈, 크롬, 몰리브덴이 다량 함유되어 있어 강도와 안정성이 뛰어납니다. 이 소재는 부품이 열악한 환경과 높은 스트레스를 견뎌야 하는 항공우주, 해양 및 화학 처리 분야에 이상적입니다.
TI-6AL-4V
5등급 티타늄으로도 알려진 Ti-6Al-4V는 높은 중량 대비 강도 비율과 생체 적합성으로 인해 DED에 널리 사용되는 소재입니다. 티타늄, 알루미늄, 바나듐으로 구성된 이 합금은 기계적 특성과 내식성이 우수하여 항공우주, 의료용 임플란트, 자동차 부품에 적합합니다.
스테인리스 스틸 316L
스테인리스 스틸 316L은 높은 내식성과 우수한 기계적 특성으로 잘 알려진 오스테나이트계 스테인리스 스틸입니다. 몰리브덴을 첨가하면 특히 염화물 및 기타 산업용 용매에 대한 내식성이 향상됩니다. 일반적으로 식품 가공, 의료 기기 및 해양 분야에 사용됩니다.
하스텔로이 X
하스텔로이 X는 내산화성과 고온 강도가 뛰어난 니켈 기반 초합금입니다. 니켈, 몰리브덴, 크롬이 함유되어 있어 고온에서 우수한 기계적 특성을 제공합니다.
이 소재는 항공우주 및 산업용 가스 터빈에 널리 사용됩니다.
CoCrMo
코발트-크롬-몰리브덴 합금인 CoCrMo는 내마모성이 뛰어나고 강도가 높은 것으로 알려져 있습니다. 이 소재는 생체 적합성과 내구성으로 인해 의료용 임플란트 및 치과 보철에 일반적으로 사용됩니다.
AlSi10Mg
AlSi10Mg는 열전도율이 우수하고 가벼운 특성을 가진 알루미늄 합금입니다. 실리콘과 마그네슘을 첨가하면 기계적 특성이 향상되어 자동차, 항공우주 및 전자 애플리케이션에 적합합니다.
마레이징 스틸(18Ni-300)
마레이징강(18Ni-300)은 인성과 경도가 뛰어난 고강도 강철 합금입니다. 철, 니켈, 코발트, 몰리브덴으로 구성되어 있으며 공구, 항공우주 및 고성능 부품에 사용됩니다.
구리
구리는 열 및 전기 전도성이 뛰어난 것으로 잘 알려져 있습니다. DED에서 순수 구리는 전기 부품, 열교환기 및 기타 높은 전도도가 필요한 애플리케이션에 사용됩니다.
공구강(H13)
공구강 H13은 경도가 높고 열 피로 저항성이 우수한 크롬-몰리브덴-바나듐 강입니다. 툴링, 다이캐스팅 및 사출 성형 분야에 널리 사용됩니다.
니켈 합금 718
니켈 합금 718은 높은 강도와 내식성으로 잘 알려진 니켈-크롬 합금입니다. 항공우주, 발전, 석유 및 가스 산업에서 일반적으로 사용됩니다.
DED의 장점
선택해야 하는 이유 직접 에너지 증착?
- 자료 효율성: DED는 재료를 효율적으로 사용하여 낭비를 최소화하고 활용도를 최적화합니다. 재료 손실이 큰 기존의 감산 방식과 달리 DED는 필요한 곳에만 재료를 추가하기 때문에 더욱 지속 가능한 옵션입니다.
- 복잡한 지오메트리: 이 기술을 사용하면 기존 제조 방식으로는 달성하기 어렵거나 불가능한 복잡한 디자인과 복잡한 형상을 만들 수 있습니다. 이를 통해 혁신적인 디자인과 경량 구조의 새로운 가능성이 열립니다.
- 복구 기능: DED는 터빈 블레이드 및 항공우주 부품과 같은 고가의 부품을 수리하는 데 매우 효과적입니다. 이를 통해 이러한 부품의 수명을 크게 연장하여 비용과 가동 중단 시간을 줄일 수 있습니다.
- 생산 속도: 기존 제조 방식에 비해 DED는 특히 중소형 부품의 경우 부품을 더 빠르게 생산할 수 있습니다. 따라서 리드 타임이 단축되고 신속한 프로토타이핑과 반복이 가능합니다.
- 기계적 속성: DED 부품은 재료 증착 공정을 정밀하게 제어할 수 있기 때문에 강도와 내구성이 높아지는 등 우수한 기계적 특성을 보이는 경우가 많습니다. 그 결과 엄격한 산업 표준을 충족하는 고성능 부품을 제작할 수 있습니다.
- 다용도성: DED는 금속, 세라믹, 복합재 등 다양한 재료에 사용할 수 있습니다. 이러한 다용도성 덕분에 여러 산업 분야의 다양한 애플리케이션에 적합합니다.
DED의 한계
직접 에너지 증착의 도전 과제는 무엇인가요?
- 높은 초기 비용: DED 장비와 재료에 대한 초기 투자 비용이 높기 때문에 일부 기업에게는 장벽이 될 수 있습니다. 그러나 장기적인 이점은 특히 고부가가치 애플리케이션의 경우 이러한 비용보다 더 큰 경우가 많습니다.
- 머신 해상도 및 정확도: DED는 복잡한 형상을 만들 수 있지만, 기계의 해상도와 정확도에 따라 제한이 있습니다. 미세한 디테일과 엄격한 허용 오차를 달성하는 것은 어려울 수 있습니다.
- 숙련된 운영자가 필요합니다: DED 시스템을 운영하려면 증착 공정을 정밀하게 제어할 수 있는 숙련된 작업자가 필요합니다. 이는 운영 비용과 복잡성을 증가시킬 수 있습니다.
- 잠재적 잔류 스트레스: DED의 빠른 가열 및 냉각 주기는 부품에 잔류 응력 및 잠재적 결함을 초래할 수 있습니다. 이러한 문제를 완화하려면 적절한 공정 제어 및 후처리 기술이 필요합니다.
- 재료 공급원 가용성: DED는 다양한 재료와 함께 사용할 수 있지만 특정 공급 원료의 가용성이 제한될 수 있습니다. 이로 인해 특정 애플리케이션에 대한 재료 선택이 제한될 수 있습니다.
- 일부 애디티브 방식보다 느립니다: 파우더 베드 용융과 같은 다른 적층 제조 방식에 비해 DED는 특정 응용 분야에서는 속도가 느릴 수 있습니다. 이는 대량 생산에 적합성에 영향을 미칠 수 있습니다.
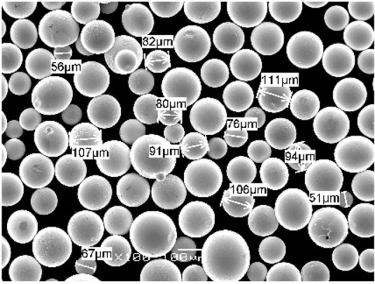
자주 묻는 질문
질문 | 답변 |
---|---|
지향성 에너지 증착(DED)이란 무엇인가요? | 방향성 에너지 증착(DED)은 집중된 에너지를 사용하여 재료를 한 층씩 녹이고 증착하여 부품을 만드는 적층 제조 공정입니다. |
DED에 어떤 자료를 사용할 수 있나요? | DED는 금속, 세라믹, 복합재 등 다양한 소재에 사용할 수 있습니다. 일반적인 금속으로는 인코넬 625, Ti-6Al-4V, 스테인리스 스틸 316L 등이 있습니다. |
DED의 장점은 무엇인가요? | DED의 장점으로는 재료 효율성, 복잡한 형상 제작 능력, 효과적인 수리 기능, 빠른 생산 속도, 고성능 부품 등이 있습니다. |
DED의 한계는 무엇인가요? | 높은 초기 비용, 기계 해상도 및 정확도 제약, 숙련된 작업자의 필요성, 잠재적 잔류 응력, 재료 공급 원료 가용성 등의 제약이 있습니다. |
어떤 산업에서 DED를 사용하나요? | DED를 사용하는 산업으로는 항공우주, 자동차, 의료, 에너지, 제조 등이 있습니다. |
DED는 다른 적층 제조 방법과 어떻게 다른가요? | DED는 재료 효율성과 수리 기능에서 이점을 제공하지만 파우더 베드 퓨전과 같은 다른 첨가제 방법에 비해 속도가 느리고 비용이 더 많이 들 수 있습니다. |
DED가 기존 구성 요소를 복구할 수 있나요? | 예, DED는 기존의 고가 부품을 수리하여 수명을 연장하고 비용을 절감하는 데 매우 효과적입니다. |
DED는 대규모 생산에 적합한가요? | DED는 프로토타입 제작, 중소형 부품 및 수리에는 탁월하지만 다른 방식에 비해 대량 생산에는 적합하지 않을 수 있습니다. |
DED 기술의 미래는 어떻게 될까요? | 재료, 공정 제어 및 기계 기능의 지속적인 발전으로 다양한 산업 분야에서 DED 기술의 도입이 추진되고 있어 미래가 유망해 보입니다. |
DED에 적합한 금속 분말을 선택하려면 어떻게 해야 하나요? | 올바른 금속 분말을 선택하는 것은 기계적 특성, 내식성, DED 공정과의 호환성 등 구체적인 적용 요건에 따라 달라집니다. 공급업체 및 전문가와 상담하면 최선의 선택을 하는 데 도움이 될 수 있습니다. |