소개: 구형 분말이 현대 제조에서 게임 체인저인 이유
구슬과 조약돌로 병을 채우려고 한다고 상상해 보세요. 매끄럽고 균일한 구슬은 쉽게 제자리에 미끄러져 들어가 틈이 거의 남지 않습니다. 이제 불규칙한 모양의 조약돌로 똑같은 작업을 한다고 상상해 보세요. 꽉 채우려고 애쓰겠죠? 이것이 바로 구형 분말— 효율적으로 흐르고 포장되어 항공 우주에서 생체 의학 공학에 이르기까지 산업에 혁명을 일으키는 작고 균일한 입자입니다.
이 기사에서는 구형 분말의 세계를 자세히 살펴보겠습니다. 다양한 유형을 탐구하고 고유한 특성을 자세히 살펴보고 고정밀 제조에 적합한 재료인 이유를 논의할 것입니다. 또한 다양한 모델을 비교하고 특정 용도를 설명하며 각 모델의 장단점을 안내합니다. 노련한 엔지니어든 최첨단 재료에 대해 궁금한 점이 있는 분이든 이 가이드에서 필요한 정보를 얻을 수 있습니다.
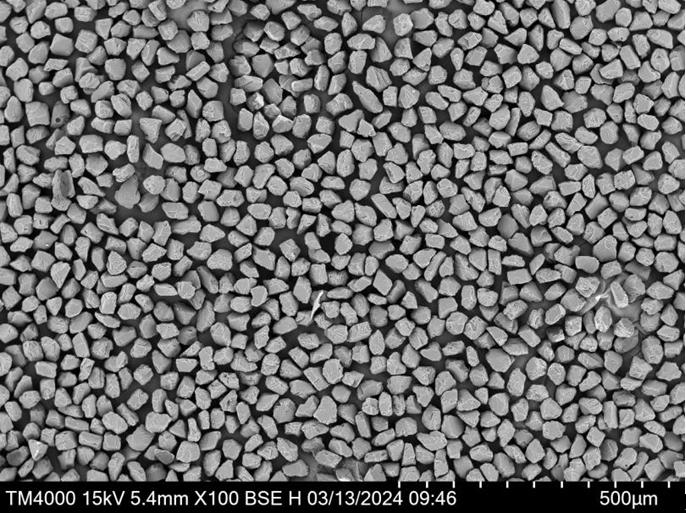
구형 분말 개요
구형 분말이란 정확히 무엇일까요?
구형 분말은 일반적으로 분무와 같은 공정을 사용하여 생성되는 미세하고 둥근 입자로 구성됩니다. 이러한 분말은 불규칙한 모양의 입자에 비해 우수한 유동성 및 충전 밀도로 인해 널리 사용됩니다. 금속, 세라믹 또는 폴리머에 관계없이 구형이면 작업 효율성이 더 높습니다.
모양이 중요한 이유
구형은 단순히 미적으로 보기 좋은 것 이상입니다. 균일한 코팅, 적층 제조의 정밀성, 심지어 제약과 같은 제품의 일관성을 달성하는 핵심입니다. 제조와 관련하여 균일성과 예측 가능성이 전부입니다. 모양과 크기가 모두 다른 재료로 케이크를 굽는다고 상상해 보세요. 일부 부분은 더 빨리 익고 다른 부분은 더 느리게 익어 고르지 않은 결과가 나올 것입니다. 구형 분말은 모든 '재료'가 균일하도록 보장하여 우수한 최종 제품을 만듭니다.
구형 분말의 조성
구형 분말의 종류 및 조성
다양한 산업에서는 각기 특정 응용 분야에 맞게 조정된 고유한 조성을 가진 다양한 유형의 구형 분말이 필요합니다. 가장 일반적인 유형 중 일부를 자세히 살펴보겠습니다.
구형 분말의 종류 | 기본 구성 | 특성 | 애플리케이션 |
---|---|---|---|
티타늄 구형 분말 | 티타늄(Ti) | 고강도, 경량, 내식성 | 항공우주, 생체의학 임플란트 |
알루미늄 구형 분말 | 알루미늄(Al) | 우수한 전도성, 경량 | 자동차, 전자, 적층 제조 |
구리 구형 분말 | 구리(Cu) | 높은 열 및 전기 전도성 | 전자, 방열판, 전도성 코팅 |
스테인리스강 구형 분말 | 철(Fe), 크롬(Cr), 니켈(Ni) | 내식성, 내구성 | 의료 기기, 자동차, 도구 |
니켈 구형 분말 | 니켈(Ni) | 고온 및 내식성 | 항공 우주, 에너지, 적층 제조 |
코발트-크롬 구형 분말 | 코발트(Co), 크롬(Cr) | 생체 적합성, 내마모성 | 의료 임플란트, 치과, 항공 우주 |
텅스텐 구형 분말 | 텅스텐(W) | 고밀도, 내열성 | 방사선 차폐, 항공 우주, 국방 |
철 구형 분말 | 철(Fe) | 자기적 특성, 경제성 | 자기 재료, 자동차, 적층 제조 |
아연 구형 분말 | 아연(Zn) | 내식성, 아연 도금 특성 | 아연 도금, 다이캐스팅, 전자 |
실리콘 구형 분말 | 실리콘(Si) | 반도체 특성, 내열성 | 전자, 태양 전지, 적층 제조 |
조성 이해 및 성능에 미치는 영향
구형 분말의 조성은 다양한 응용 분야에서 성능에 직접적인 영향을 미칩니다. 예를 들어 티타늄의 생체 적합성과 강도는 의료 임플란트에 이상적이며, 알루미늄의 경량성은 자동차 부품에 완벽합니다. 이러한 조성을 이해함으로써 제조업체는 특정 요구 사항에 맞는 올바른 분말을 선택할 수 있습니다.
구형 분말의 특성
구형 분말을 독특하게 만드는 주요 특성
무엇이 구형 분말 재료 과학 분야에서 두각을 나타냅니까? 주요 특성에 대한 분석은 다음과 같습니다.
속성 | 설명 | 중요한 이유 |
---|---|---|
흐름성 | 분말이 부드럽게 흐르는 능력 | 적층 제조 및 일관된 층 증착에 필수적입니다. |
충전 밀도 | 입자가 함께 포장되는 정도 | 밀도가 높을수록 더 강하고 균일한 재료가 생성됩니다. |
표면적 | 입자의 총 표면적 | 특히 화학 공정에서 반응성에 영향을 미칩니다. |
순도 | 오염 물질의 부재 | 의료 임플란트와 같이 높은 신뢰성이 필요한 응용 분야에 중요합니다. |
구형성 | 입자 모양이 완벽한 구에 얼마나 가까운지 | 구형도가 높을수록 유동성 및 충전 특성이 향상됩니다. |
다양한 구형 분말의 특성 비교
다양한 유형의 구형 분말은 이러한 특성을 다양한 정도로 나타냅니다. 예를 들어 알루미늄 구형 분말은 유동성이 우수하고 가벼워 적층 제조에 완벽합니다. 반대로 텅스텐 분말은 밀도가 매우 높고 내열성이 뛰어나 방사선 차폐와 같은 특수 응용 분야에 적합합니다.
구형 분말의 장점
구형 분말이 제조에서 우수한 이유
구형 분말을 사용하면 특히 정밀성과 효율성이 가장 중요한 산업에서 많은 이점을 얻을 수 있습니다. 그 이유는 다음과 같습니다.
- 유동성 향상: 구형 분말은 물처럼 흘러 금형과 캐비티를 쉽게 채우므로 적층 제조 및 금속 사출 성형(MIM)에 필수적입니다.
- 충전 밀도 향상: 입자가 더 촘촘하게 포장되기 때문에 최종 제품이 더 밀도가 높고 강합니다.
- 표면 마감 향상: 구형 입자는 더 매끄러운 표면을 생성하여 후처리 필요성을 줄입니다.
- 균일한 코팅: 열 분사 공정에서 구형 분말은 더 균일한 코팅을 생성하여 성능과 내구성을 향상시킵니다.
- 조성의 일관성: 입자의 균일성은 각 분말 배치가 예측 가능한 방식으로 작동하도록 보장하므로 생산 품질을 유지하는 데 중요합니다.
사례 연구: 항공 우주 제조의 구형 분말
구형 분말이 항공 우주 산업에 혁명을 일으키는 방식을 자세히 살펴보겠습니다. 예를 들어 터빈 블레이드 생산에서 니켈 구형 분말을 사용하면 극한의 온도와 응력을 견딜 수 있는 부품을 만들 수 있습니다. 분말의 균일성은 각 블레이드가 조성과 구조가 동일하도록 보장하며, 이는 사소한 결함이라도 치명적인 고장으로 이어질 수 있는 산업에서 매우 중요합니다.

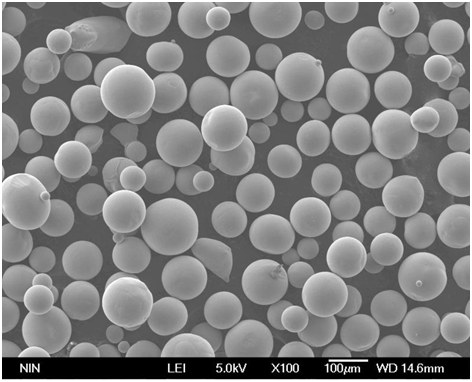
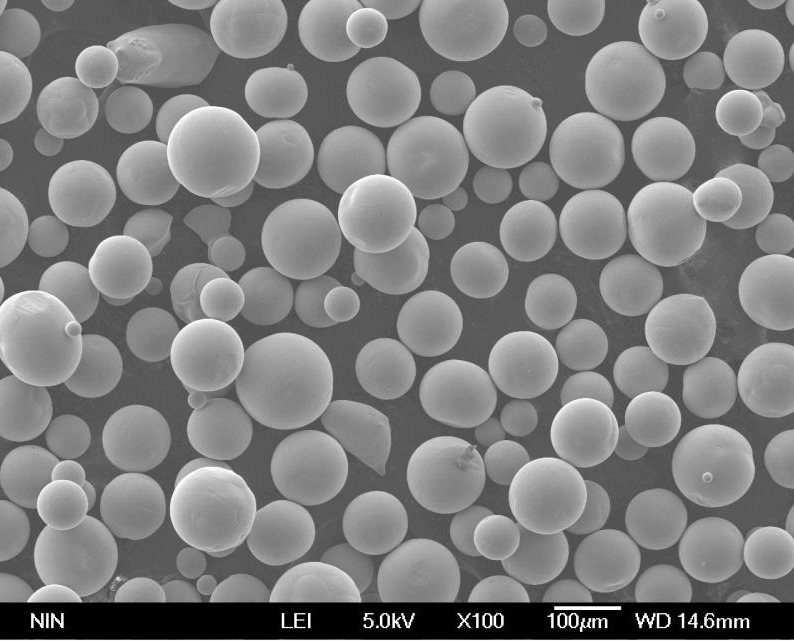
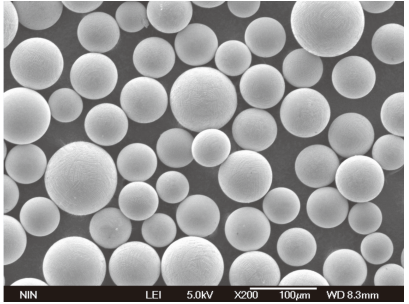
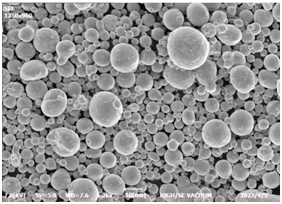
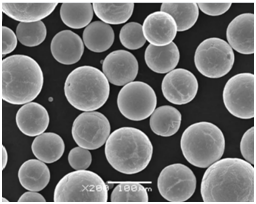
구형 분말의 응용
산업별 용도
구형 분말의 고유한 특성은 다양한 산업에서 매우 중요합니다. 다음은 다양한 부문에서 이 재료를 활용하는 방법입니다.
산업 | 애플리케이션 | 구형 분말 사용의 이점 |
---|---|---|
항공우주 | 터빈 블레이드, 로켓 부품 | 높은 중량 대비 강도, 내열성 |
자동차 | 엔진 구성 요소, 경량 구조 | 무게 감소, 연비 향상 |
의료 | 임플란트, 보철 | 생체 적합성, 적층 제조의 정밀성 |
전자 제품 | 전도성 잉크, 부품 | 높은 전기 전도성, 마이크로 제조의 정밀성 |
방어 | 갑옷, 탄약 | 방탄을 위한 밀도, 일관된 품질 |
에너지 | 원자력 발전소, 태양 전지판 | 고온 저항, 에너지 변환 효율 |
구형 분말이 적층 제조를 변화시키는 방법
적층 제조 또는 3D 프린팅은 구형 분말이 상당한 영향을 미치는 가장 흥미로운 분야 중 하나입니다. 이러한 분말의 균일성과 유동성은 기존 제조 방법으로는 불가능한 복잡한 설계와 복잡한 형상을 만드는 데 완벽합니다. 예를 들어 맞춤형 의료 임플란트 생산에서 구형 티타늄 분말은 환자의 해부학적 구조와 완벽하게 일치하는 구조를 만드는 데 사용되어 결과를 개선하고 회복 시간을 단축합니다.
다양한 구형 분말 모델 비교
10가지 구형 분말 모델의 상세 비교
특정 응용 분야에 구형 분말을 선택할 때는 특성, 조성 및 비용을 기준으로 다양한 모델을 비교하는 것이 중요합니다. 다음은 구형 분말의 10가지 모델을 비교하여 고유한 기능과 이상적인 용도를 강조하는 표입니다.
모델 | 재료 | 속성 | 최상의 대상 | 가격 범위(kg당) |
---|---|---|---|---|
TI-6AL-4V | 티타늄 합금 | 고강도, 생체 적합성 | 의료용 임플란트, 항공우주 | $350 – $450 |
AlSi10Mg | 알루미늄 합금 | 가볍고 우수한 열적 특성 | 자동차, 항공우주 | $100 – $150 |
316L | 스테인리스 스틸 | 부식 방지, 내구성 | 의료 기기, 도구 | $50 – $70 |
CuNi2SiCr | 구리 합금 | 높은 전기 전도성, 강도 | 전자 제품, 방열판 | $200 – $300 |
CoCrMo | 코발트-크롬-몰리브덴 | 생체 적합성, 내마모성 | 치과 임플란트, 정형외과 기기 | $400 – $500 |
NiCr20TiAl | 니켈 합금 | 높은 내열성, 강도 | 항공우주, 에너지 | $600 – $750 |
Fe2O3 | 산화철 | 자기적 특성, 경제성 | 전자, 자기 재료 | $20 – $40 |
WNiFe | 텅스텐-니켈-철 | 고밀도, 방사선 차폐 | 국방, 항공우주 | $500 – $600 |
구형 분말의 사양 및 표준
구형 분말의 주요 사양 및 표준
선택 시 구형 분말 다양한 응용 분야의 경우 품질과 성능을 보장하는 사양과 표준을 고려하는 것이 필수적입니다. 자세한 개요는 다음과 같습니다.
사양 | 설명 | 일반적인 표준 |
---|---|---|
입자 크기 | 일반적으로 마이크로미터(µm) 단위로 측정되는 분말 입자의 직경 | ASTM B3 |
파티클 모양 | 입자 구형도 또는 둥근 정도 | ASTM B212, ISO 19530 |
벌크 밀도 | 단위 부피당 분말 질량 | ASTM B329, ISO 3953 |
겉보기 밀도 | 벌크 상태의 분말 밀도 | ASTM B212, ISO 3923 |
순도 | 주재료 대 오염물의 비율 | ASTM E18, ISO 9001 |
흐름성 | 깔때기나 슈트를 통해 분말이 얼마나 쉽게 흐르는지 | ASTM B213, ISO 4490 |
화학 성분 | 분말에 존재하는 원소 또는 화합물 | ASTM E1621, ISO 6892 |
구형 분말의 일반적인 크기 및 등급
다양한 응용 분야에서는 특정 크기 및 등급의 구형 분말이 필요합니다. 다음은 몇 가지 일반적인 크기 및 등급을 간략하게 나타낸 표입니다.
크기(µm) | 등급 | 일반적인 용도 |
---|---|---|
10 – 20 | Fine | 정밀 코팅, 적층 제조 |
20 – 50 | Medium | 자동차 부품, 의료 임플란트 |
50 – 100 | 거친 | 산업 응용 분야, 대규모 제조 |
구형 분말 공급업체 및 가격
주요 공급업체 및 가격 정보
다음은 구형 분말의 주요 공급업체와 가격에 대한 간략한 정보입니다.
공급업체 | 파우더 유형 | 가격 범위(kg당) | 웹사이트 |
---|---|---|---|
Ametek | 티타늄, 알루미늄 | $300 – $500 | ametek.com |
샌드빅 | 스테인리스강, 코발트 | $50 – $200 | home.sandvik |
호가나스 | 철, 니켈, 구리 | $100 – $400 | hoganas.com |
ARC Group | 텅스텐, 아연 | $200 – $600 | arc-group.com |
Elementum | 실리콘, 몰리브덴 | $150 – $400 | elementum3d.com |
가격 결정 요인
구형 분말의 가격은 여러 요인에 따라 달라질 수 있습니다.
- 재료 유형: 티타늄 및 코발트-크롬 합금과 같은 고급 재료는 철 또는 알루미늄과 같은 표준 금속보다 비쌉니다.
- 입자 크기: 더 미세한 분말은 추가 가공이 필요하기 때문에 더 비싼 경향이 있습니다.
- 순도: 고순도 분말은 일반적으로 더 높은 가격을 받습니다.
구형 분말의 장단점 비교
구형 분말의 장점과 단점
구형 분말과 관련하여, 그 장점과 잠재적인 단점에 대해 알아야 할 사항은 다음과 같습니다.
측면 | 장점 | 제한 사항 |
---|---|---|
흐름성 | 제조를 위한 부드럽고 효율적인 흐름 | 특정 취급 기술이 필요할 수 있음 |
충전 밀도 | 더 높은 밀도는 더 강한 재료를 생성함 | 밀도가 높은 분말은 가공하기 더 어려울 수 있음 |
표면 마감 | 최소한의 후처리를 통한 우수한 표면 마감 | 가공 요구 사항으로 인한 더 높은 비용 |
균일성 | 일관된 품질 및 성능 | 균일한 구형 분말 생산은 비용이 많이 들 수 있음 |
비용 | 대량 생산에 경제적임 | 고품질 분말에 대한 초기 투자는 높을 수 있음 |
상세 비교: 구형 분말 대 불규칙 분말
- 구형 분말: 우수한 유동성 및 충전 밀도를 제공합니다. 정밀 제조 및 고품질 코팅에 이상적입니다. 그러나 가공 비용이 더 많이 들 수 있습니다.
- 불규칙 분말: 일반적으로 더 저렴하지만 일관되지 않은 흐름 및 충전 문제를 야기할 수 있습니다. 정밀도가 덜 중요한 응용 분야에 더 적합합니다.
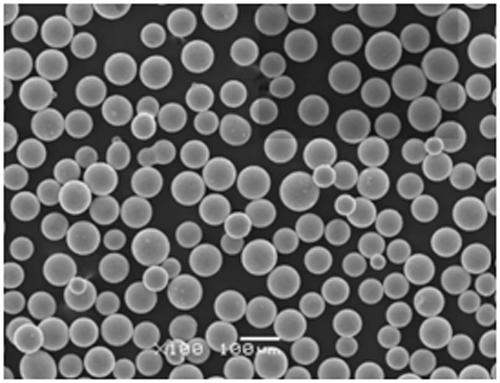
자주 묻는 질문
질문 | 답변 |
---|---|
구형 분말은 어디에 사용됩니까? | 구형 분말은 적층 제조, 자동차 부품, 의료 임플란트 및 전자 제품을 포함한 다양한 응용 분야에 사용됩니다. 균일성은 이러한 분야에서 고품질과 정밀도를 보장합니다. |
구형 분말은 어떻게 제조됩니까? | 구형 분말은 일반적으로 용융 금속 또는 기타 재료를 급속 냉각하여 구형 입자를 형성하는 분무 기술을 사용하여 생산됩니다. 다른 방법으로는 가스 분무 및 수분 분무가 있습니다. |
3D 프린팅에서 구형 분말을 사용하면 어떤 이점이 있습니까? | 구형 분말은 우수한 유동성 및 충전 밀도를 제공하여 3D 프린팅에서 더 일관된 층 증착과 더 나은 최종 제품 품질을 제공합니다. |
입자 크기는 구형 분말의 성능에 어떤 영향을 미칩니까? | 더 미세한 입자는 더 나은 해상도와 표면 마감을 제공하지만 취급이 더 어려울 수 있습니다. 더 거친 입자는 취급이 더 쉽지만 동일한 수준의 디테일과 마감을 제공하지 못할 수 있습니다. |
구형 분말을 재활용할 수 있습니까? | 예, 많은 유형의 구형 분말을 재활용할 수 있으며, 특히 적층 제조에서 그렇습니다. 그러나 재활용 공정은 분말이 품질과 특성을 유지하도록 해야 합니다. |
구형 분말의 일반적인 비용은 얼마입니까? | 비용은 재료, 입자 크기 및 순도에 따라 크게 다릅니다. 가격은 일반 재료의 경우 kg당 20달러에서 특수 합금의 경우 kg당 750달러 이상까지 다양할 수 있습니다. |
구형 분말은 어디에서 구입할 수 있습니까? | 구형 분말은 Ametek, Sandvik, Höganäs, ARC Group 및 Elementum과 같은 전문 공급업체에서 구입할 수 있습니다. 가격 및 가용성은 분말의 유형 및 사양에 따라 다릅니다. |