プラズマ霧化 プラズマアトマイズは、金属粉末の製造に利用される高度な技術であり、その精度と効率の高さで知られている。この記事では、プラズマアトマイゼーションの複雑さを深く掘り下げ、その様々な側面、アプリケーション、この方法で製造される金属粉末の特定のモデルを探ります。この包括的なガイドを読み終える頃には、プラズマアトマイゼーションと、それが現代の製造業に与える重要な影響について完全に理解することができるだろう。
プラズマ霧化の概要
プラズマアトマイズは、高温プラズマトーチを適用して金属ワイヤーを微粒子に変換することにより、高品質の金属粉末を製造するために使用されるプロセスである。この方法は、積層造形、航空宇宙、医療機器などの用途に不可欠な、粒度分布の狭い球状粉末を製造できることから好まれている。
主な内容
- プロセス:プラズマトーチによる金属線の粉末化
- 用途:積層造形、航空宇宙、医療機器
- メリット:粒度分布の狭い高品質の球状粉末
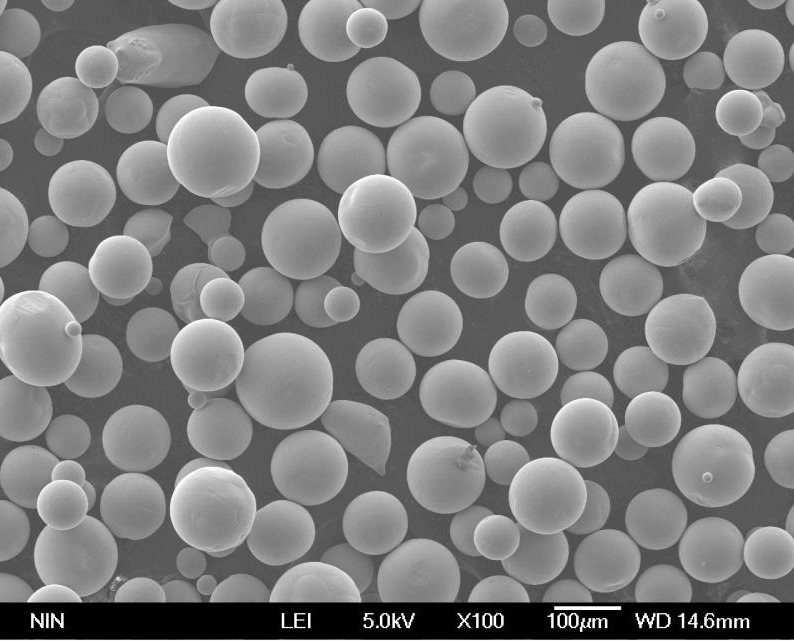
金属粉末の種類 プラズマ霧化
表:金属粉末の種類と特徴
金属粉モデル | 構成 | プロパティ | 特徴 |
---|---|---|---|
Ti-6Al-4V | AlとVを含むチタン合金 | 高強度、耐食性 | 航空宇宙および医療用途に最適 |
316Lステンレス鋼 | 鉄、クロム、ニッケル、モリブデン | 高耐食性、優れた機械的特性 | 医療および海洋環境で使用 |
Inconel 718 | ニッケル・クロム合金 | 優れた高温強度 | 航空宇宙用タービンに最適 |
AlSi10Mg | シリコン入りアルミニウム、マグネシウム | 軽量、優れた熱特性 | 自動車および航空宇宙分野で一般的 |
CoCrMo | コバルト・クロム・モリブデン合金 | 高い耐摩耗性、生体適合性 | 医療用インプラントに使用 |
Hastelloy X | ニッケル基合金 | 高耐酸化性、高強度 | 高温環境に最適 |
CuNi2SiCr | 銅-ニッケル-シリコン-クロム | 高強度、導電性 | 電気および船舶用途に使用 |
Ti-48Al-2Cr-2Nb | チタン-アルミニウム合金 | 高温および耐酸化性 | タービンブレードや自動車に最適 |
316Fステンレス鋼 | 鉄、クロム、ニッケル、硫黄 | 快削、高耐食性 | 医療用具および部品に優遇 |
NiCrMo-4 | ニッケル-クロム-モリブデン合金 | 高耐食性、良好な溶接性 | 化学処理装置に使用 |
プラズマアトマイズ金属粉末の用途
テーブル用途と使用例
アプリケーションエリア | 具体的な用途 |
---|---|
付加製造 | 複雑なコンポーネント、プロトタイプ、カスタムパーツの3Dプリント |
航空宇宙 | タービンブレード、構造部品、エンジン部品 |
医療機器 | インプラント、手術器具、補綴物 |
自動車 | 軽量部品、エンジン部品、熱交換器 |
マリン | 耐食部品、プロペラ、バルブ |
電気 | 導電材料、コネクター、熱管理 |
化学処理 | 高温反応器、耐食機器 |
仕様と規格 プラズマ霧化 金属粉末
表:仕様、サイズ、等級、規格
金属粉モデル | 仕様 | サイズ | グレード | 規格 |
---|---|---|---|---|
Ti-6Al-4V | ASMB348、AMS4928 | 15~45μm、45~106μm | グレード5 | ASTM、AMS |
316Lステンレス鋼 | A276, A240 | 20~53μm、53~150μm | グレード316L | ASTM、AMS、ISO |
Inconel 718 | 午前5662、午前5596 | 15~45μm、45~106μm | グレード718 | AMS、ASTM、ISO |
AlSi10Mg | ISO 3522, DIN EN 1706 | 20~63μm、63~150μm | グレード A360 | ISO、DIN |
CoCrMo | アストレムF75、アストレムF1537 | 15~45μm、45~106μm | グレード1 | ASTM、ISO |
Hastelloy X | 午前5536、午前5754 | 15~45μm、45~106μm | グレードX | AMS、ASTM、ISO |
CuNi2SiCr | アストレムB151、アストレムB122 | 20~53μm、53~150μm | グレード1 | ASTM、ISO |
Ti-48Al-2Cr-2Nb | ASMB988、AMS4911 | 15~45μm、45~106μm | グレード1 | ASTM、AMS |
316Fステンレス鋼 | A276, A240 | 20~53μm、53~150μm | グレード316F | ASTM、AMS、ISO |
NiCrMo-4 | アストレムB575、アストレムB619 | 15~45μm、45~106μm | グレード4 | ASTM、ISO |
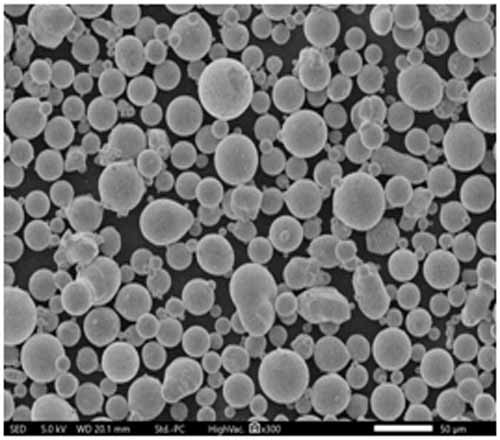
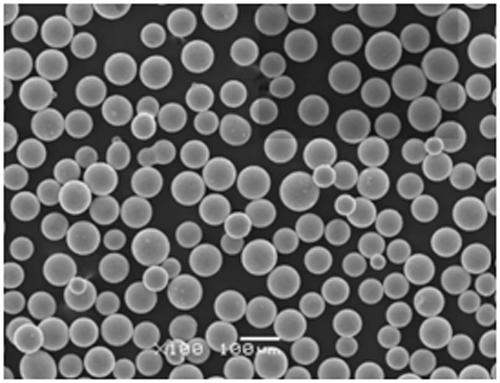
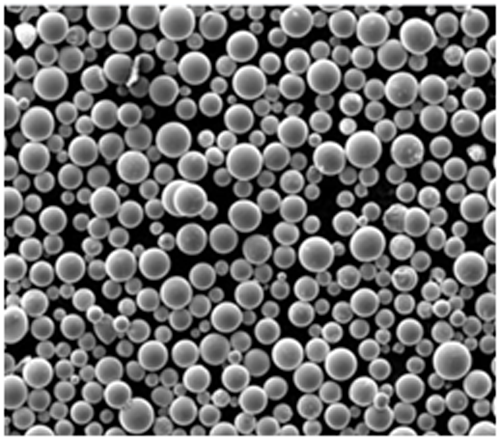
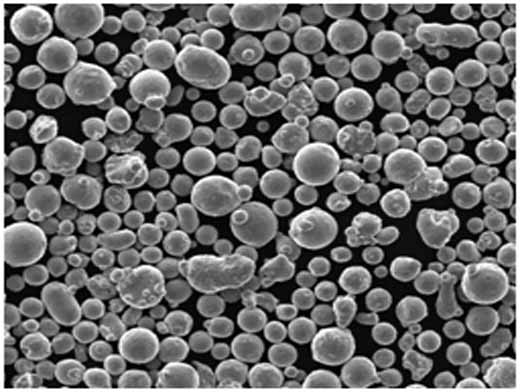
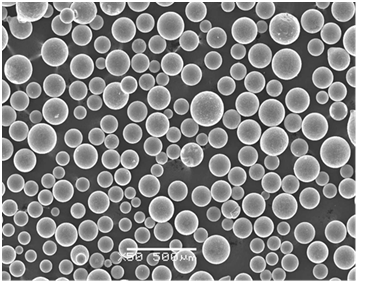
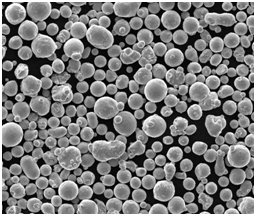
サプライヤーと価格詳細
表:サプライヤーと価格
サプライヤー | 金属粉モデル | 価格(1kgあたり) | 追加サービス |
---|---|---|---|
GKNアディティブ | Ti-6Al-4V、316Lステンレス鋼、インコネル718 | $300 – $500 | カスタムパウダー製造 |
ヘガネスAB | AlSi10Mg、CoCrMo、ハステロイX | $250 – $450 | 技術サポート、研究開発サービス |
LPWテクノロジー | CuNi2SiCr、Ti-48Al-2Cr-2Nb、316Fステンレス鋼 | $350 – $600 | 粉体特性評価、試験 |
カーペンター添加剤 | NiCrMo-4、Ti-6Al-4V、インコネル718 | $280 – $550 | アプリケーション・エンジニアリング・サポート |
AP&C(GEアディティブ) | Ti-6Al-4V、AlSi10Mg、CoCrMo | $320 – $480 | 大量生産、品質管理 |
サンドビック・オスプレイ | 316Lステンレス鋼、ハステロイX | $260 – $470 | 金属粉リサイクルサービス |
プラクセア・サーフェス・テクノロジー | AlSi10Mg, CuNi2SiCr, NiCrMo-4 | $270 – $500 | 高度なコーティング、表面処理 |
オベール&デュバル | Ti-48Al-2Cr-2Nb、316Fステンレス鋼 | $290 – $520 | 特注合金、特殊グレード |
アルカムAB(GEアディティブ) | Ti-6Al-4V、インコネル718 | $310 – $530 | 積層造形ソリューション |
バキュームシュメルツ社 | CoCrMo、ハステロイX、NiCrMo-4 | $300 – $490 | 高純度金属粉 |
の利点と限界 プラズマ霧化
表:長所と短所の比較
アスペクト | メリット | 制限事項 |
---|---|---|
パウダーの品質 | 高い真球度、均一な粒子径 | 初期設定費用が高い |
素材範囲 | 幅広い金属と合金の加工が可能 | 材料によっては、特定のプラズマ設定が必要な場合があります。 |
生産効率 | 高い歩留まり、無駄の少なさ | エネルギー集約型プロセス |
アプリケーションの多様性 | 様々なハイテク用途に最適 | 熟練した操作とメンテナンスが必要 |
スケーラビリティ | 工業生産に適した拡張性 | 設備およびメンテナンス費用 |
環境への影響 | 他の方法に比べて廃棄物が少ない | 依然として再生不可能なエネルギー源に依存 |
プラズマアトマイズ金属粉末の特性
表:構成と特徴
金属粉モデル | 構成 | 特徴 |
---|---|---|
Ti-6Al-4V | 90% Ti, 6% Al, 4% V | 高い強度対重量比、耐食性 |
316Lステンレス鋼 | 64% Fe, 18% Cr, 14% Ni, 2% Mo | 優れた耐食性、生体適合性 |
Inconel 718 | 50-55% Ni, 17-21% Cr, 4.75-5.5% Nb, 2.8-3.3% Mo | 高温性能、耐酸化性 |
AlSi10Mg | 89% Al, 10% Si, 1% Mg | 軽量、良好な熱伝導性 |
CoCrMo | Co60~65%、Cr26~30%、Mo5~7 | 高い耐摩耗性、生体適合性 |
Hastelloy X | 47% Ni, 22% Cr, 18% Fe, 9% Mo | 優れた高温強度 |
CuNi2SiCr | 97% Cu, 2% Ni, 0.6% Si, 0.4% Cr | 高導電性、耐食性 |
Ti-48Al-2Cr-2Nb | 48% Ti, 48% Al, 2% Cr, 2% Nb | 高温および耐酸化性 |
316Fステンレス鋼 | 64% Fe, 18% Cr, 14% Ni, 2% Mo, 0.15% S | 快削、高耐食性 |
NiCrMo-4 | 56-60%ニッケル、20-22%クロム、8-10%モリブデン | 耐食性、良好な溶接性 |
比較 プラズマ霧化 他の方法へ
プラズマアトマイズは、ガスアトマイズやメカニカルミリングといった他の粉末製造方法の中でも、高品質で均一な粉末を製造できる点で際立っています。しかし、その真価はどこにあるのでしょうか?
表:プラズマアトマイゼーションと他の方法との比較
方法 | プラズマ霧化 | ガス噴霧 | 機械加工 |
---|---|---|---|
パウダーの品質 | 高い真球度、狭い粒度分布 | 良好な真球度、より広いサイズ範囲 | 不規則な形状、幅広いサイズ分布 |
素材の多様性 | 幅広い金属と合金 | 範囲は広いが、いくつかの制限がある | 特定の素材に限定 |
効率性 | 高い歩留まり、無駄の少なさ | 中程度の収量、若干の廃棄物 | 歩留まりの低下、大きな廃棄物 |
スケーラビリティ | 工業生産に適した拡張性 | スケーラブルだが、大規模では効率が落ちる | 限られた拡張性 |
コスト | 高い初期設定、低い運用コスト | 適度なセットアップと運用コスト | セットアップコストは低く、運用コストは高い |
エネルギー消費 | エネルギー集約型 | プラズマよりエネルギー消費が少ない | 適度なエネルギー消費 |
用途 | ハイテク・アプリケーション | ハイテクを含む幅広いラインナップ | ハイテク用途には不向き |
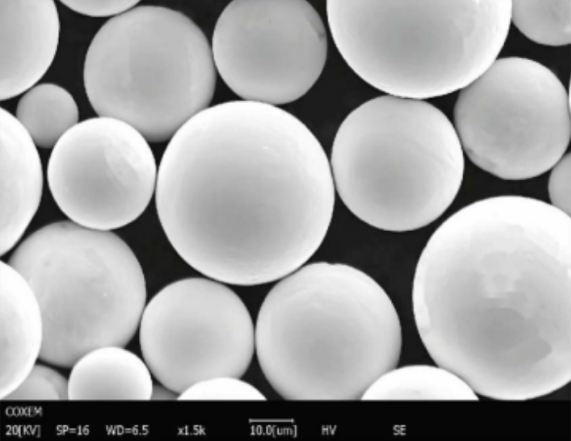
よくある質問
表:プラズマ霧化に関するFAQ
質問 | 回答 |
---|---|
プラズマ霧化とは? | 高温のプラズマ・トーチを使って金属線を微粉末にするプロセスである。 |
プラズマ霧化の利点は? | 高度な製造アプリケーションに理想的な、粒度分布の狭い高品質な球状粉末を製造します。 |
どのような産業がプラズマ化粉末を使用するのか? | 航空宇宙、医療機器、自動車、海洋、電気、化学処理産業。 |
プラズマ霧化は他の方法と比べてどうですか? | 真球度や均一性に優れた高品質の粉末が得られるが、初期設定コストが高くなる。 |
プラズマアトマイゼーションで処理できる材料は? | チタン合金、ステンレス鋼、ニッケル合金、アルミニウム合金など幅広い。 |
プラズマ霧化は環境に優しいか? | 他の方法に比べて廃棄物は少ないが、再生不可能なエネルギー源に頼るため、エネルギー集約的である。 |
プラズマ霧化は大量生産に対応できるか? | そう、工業生産用に拡張可能で、大量生産に適している。 |
プラズマ霧化の限界は? | 高い初期設定コスト、エネルギー消費、熟練した操作とメンテナンスの必要性。 |
プラズマアトマイズによる粉末の品質は、積層造形にどのようなメリットをもたらすのか? | 高い真球度と均一な粒子径は、3Dプリント部品の一貫性と品質を向上させる。 |
プラズマ霧化には安全上の懸念はありますか? | 高温とエネルギーを伴うため安全対策は必要だが、適切な手順を踏めば安全だ。 |