金属射出成形(MIM) は、製造業に革命をもたらしている。プラスチック射出成形の多用途性と金属の強度と完全性を組み合わせたMIMは、金属部品の製造において比類のない精度と複雑さを提供する最先端技術です。この記事では、熟練したエンジニアであろうと、単に現代の製造業の複雑さに興味があるだけであろうと、MIMの世界を深く掘り下げ、洞察、技術仕様、実用的なアプリケーションを提供します。さあ、シートベルトを締めて、金属射出成形の魅力的な世界を探検する準備をしましょう!
金属射出成形(MIM)の概要
金属粉末射出成形(MIM)は、金属粉末の利点とプラスチック射出成形技術を融合させたプロセスです。この方法によって、従来の金属加工技術では不可能ではないにせよ、困難な複雑な形状を持つ小型で複雑な金属部品の製造が可能になります。
MIMの主な利点:
- 高精度で複雑な設計
- 効率的な大量生産能力
- 大量生産に適したコスト効率
- プラスチック部品に比べて優れた機械的特性
- 幅広い素材に対応
プロセスの概要
- 原料の準備 金属粉末を熱可塑性バインダーと混合して原料を形成する。
- モールディング: 原料は金型に注入され、所望の形状に成形される。
- 脱バインダー: 部品からバインダーを取り除く。
- 焼結: 金属部品は高温に加熱され、金属粒子同士が結合し、緻密な固形部品となる。
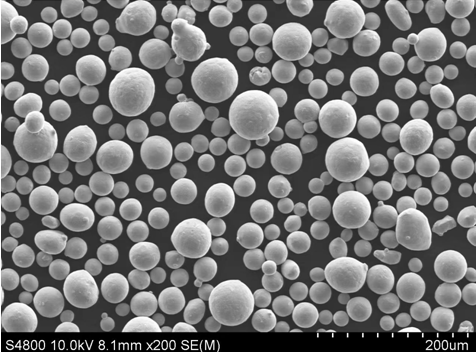
MIMに使用される金属粉末の種類
MIMは汎用性があり、様々な種類の金属粉末を使用することができる。以下に、MIMで一般的に使用される10種類の金属粉末とその説明を示します:
金属粉 | 説明 |
---|---|
316Lステンレス鋼 | 優れた耐食性と高い引張強度で知られる。医療、食品加工用途に最適。 |
17-4 PHステンレス鋼 | 強度と耐食性を兼ね備えた析出硬化鋼。航空宇宙や機械部品に使用される。 |
カルボニル鉄粉 | 高純度の鉄で粒径が細かく、高い強度と磁気特性を必要とする部品に使用される。 |
M2工具鋼 | 耐摩耗性と靭性に優れた高速度鋼。切削工具や金型によく使用される。 |
チタン Ti-6Al-4V | 軽量で高強度、耐食性。航空宇宙、医療用インプラント、スポーツ用品に好まれている。 |
コバルトクロム(CoCr)合金 | 非常に硬く、耐摩耗性に優れ、歯科インプラントや整形外科器具に適している。 |
Inconel 625 | 高い強度と高温での耐酸化性、耐食性で知られるニッケル基超合金。航空宇宙や化学処理に使用される。 |
銅合金 90/10 | 優れた熱伝導性と電気伝導性で知られる。電気部品や熱交換器に使用される。 |
ニッケル718 | ニッケルクロム合金で、特に高温で高い強度と耐食性を発揮する。タービンエンジンや原子炉に使用される。 |
アルミニウム合金6061 | 軽量で機械的特性と耐食性に優れる。自動車や家電製品によく使用される。 |
金属射出成形(MIM)の組成と特性
MIMに使用される材料の組成と特性を理解することは、お客様の用途に適した金属粉末を選択する上で極めて重要です。以下は、いくつかの一般的なMIM材料の組成、特性、および特徴を強調した詳細な表です。
MIM材料の組成と特性
素材 | 構成 | プロパティ | 特徴 |
---|---|---|---|
316Lステンレス鋼 | Fe、Cr、Ni、Mo | 耐食性、高強度 | 非磁性、生体適合性 |
17-4 PHステンレス鋼 | Fe、Cr、Ni、Cu | 高強度、耐食性 | 磁性、熱処理可能 |
カルボニル鉄粉 | Fe | 高純度、磁気特性 | 高強度、優れた耐摩耗性 |
M2工具鋼 | Fe、C、Mo、W、Cr、V | 高い耐摩耗性、靭性 | 高速アプリケーションに最適 |
チタン Ti-6Al-4V | Ti、Al、V | 軽量、高強度 | 生体適合性、耐食性 |
コバルトクロム(CoCr)合金 | Co、Cr、Mo | 非常に硬く、耐摩耗性がある | 生体適合性、耐食性 |
Inconel 625 | Ni、Cr、Mo、Nb | 高強度、耐酸化性 | 高温用途に適している |
銅合金 90/10 | 銅、ニッケル | 優れた熱伝導性、電気伝導性 | 良好な耐食性 |
ニッケル718 | Ni、Cr、Fe、Nb | 高強度、耐食性 | 高温に強い |
アルミニウム合金6061 | Al、Mg、Si | 軽量、優れた機械的特性 | 耐食性に優れ、機械加工が容易 |
金属射出成形(MIM)の用途
MIMは、その汎用性と高品質で複雑な部品を製造する能力により、幅広い産業で使用されています。ここでは、MIMの一般的な用途についてご紹介します:
MIM材料の産業応用
産業 | 申し込み | 使用素材 |
---|---|---|
メディカル | 外科用器具、歯科用インプラント、整形外科用器具 | 316Lステンレス鋼、CoCr合金、Ti-6Al-4V |
航空宇宙 | タービンブレード、ファスナー、構造部品 | インコネル625、チタンTi-6Al-4V、17-4 PHステンレス鋼 |
自動車 | 燃料噴射装置、ターボチャージャー、トランスミッション部品 | M2工具鋼、17-4 PHステンレス鋼、アルミニウム合金6061 |
コンシューマー・エレクトロニクス | コネクター、ハウジング、ヒートシンク | 銅合金 90/10、アルミニウム合金 6061 |
ディフェンス | 銃器部品、タクティカルギア | カルボニル鉄粉、17-4 PHステンレス鋼、M2工具鋼 |
産業機械 | 切削工具、金型、歯車 | M2工具鋼、17-4 PHステンレス鋼、カルボニル鉄粉 |
エネルギー | 原子炉部品、石油・ガス部品 | ニッケル718、インコネル625、17-4 PHステンレス鋼 |
ジュエリー | 時計ケース、留め具、装飾品 | 316Lステンレス鋼、チタンTi-6Al-4V |
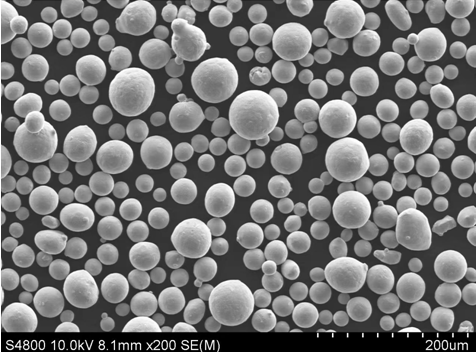
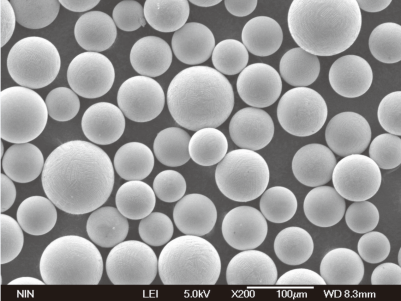
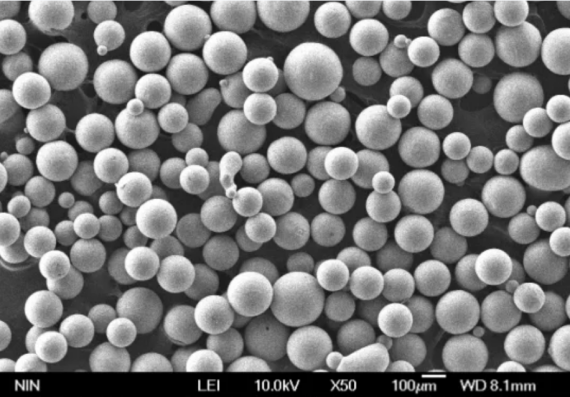
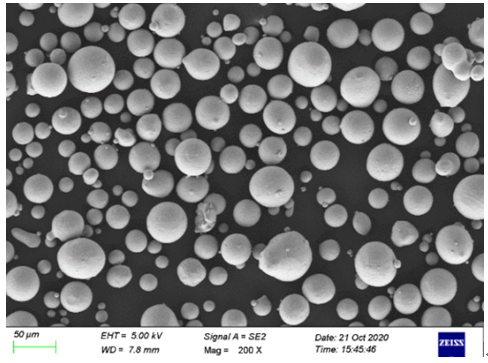
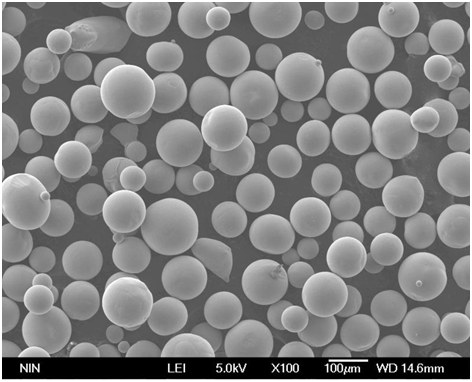
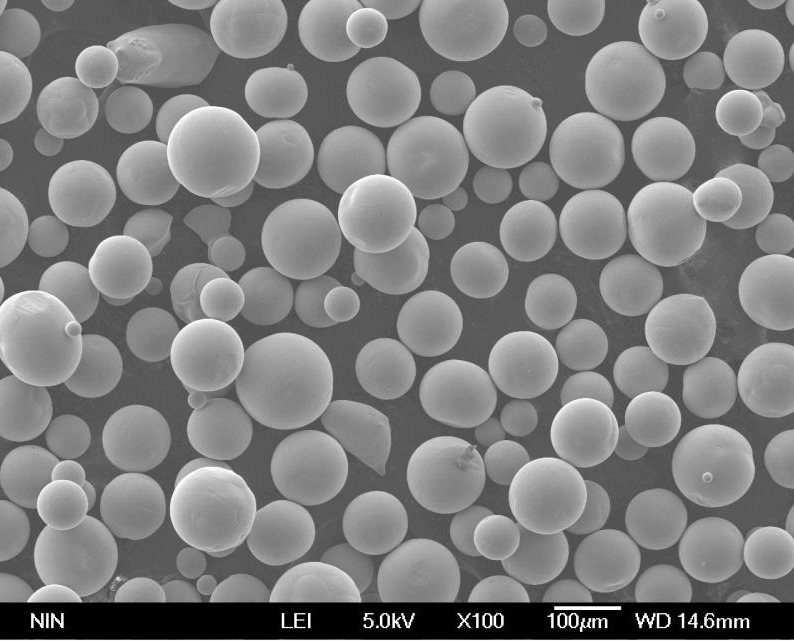
MIMの仕様、サイズ、グレード、規格
MIMに関しては、仕様、サイズ、グレード、規格が、それぞれの用途に適した適合性と性能を確保するために非常に重要です。ここでは、いくつかの一般的なMIM材料について、これらの側面を詳しく見てみましょう。
MIM材料の仕様と規格
素材 | 仕様 | サイズ | グレード | 規格 |
---|---|---|---|---|
316Lステンレス鋼 | A276, ISO 5832-1 | 0.1mm~100mm | マリングレード | ASTM F138 |
17-4 PHステンレス鋼 | ASTM A564 | 0.1mm~100mm | H900、H1025 | AMS 5643 |
カルボニル鉄粉 | ASTM A131 | 0.1mm~50mm | 該当なし | ASTM A848 |
M2工具鋼 | ASTM A600 | 0.1mm~50mm | T1、T2、T4 | ISO 4957 |
チタン Ti-6Al-4V | ASTM B348 | 0.1mm~100mm | グレード5 | ASTM F136 |
コバルトクロム(CoCr)合金 | ASTM F75 | 0.1mm~50mm | 該当なし | ISO 5832-4 |
Inconel 625 | ASTM B443 | 0.1mm~50mm | 該当なし | AMS 5666 |
銅合金 90/10 | ASTM B111 | 0.1mm~100mm | C70600 | ASME SB111 |
ニッケル718 | ASTM B670 | 0.1mm~50mm | 該当なし | AMS 5662 |
アルミニウム合金6061 | ASTM B221 | 0.1mm~200mm | T6、T651 | AMS 4150 |
MIM材料のサプライヤーと価格詳細
適切なサプライヤーを見つけ、コストの影響を理解することは、あらゆる製造プロセスにとって不可欠です。以下は、評判の良いサプライヤーのリストと、一般的なMIM材料の参考価格です。
MIM材料のサプライヤーと価格
素材 | サプライヤー | 価格帯(kgあたり) | 備考 |
---|---|---|---|
316Lステンレス鋼 | カーペンター・テクノロジー、サンドビック | $20 – $30 | 量と純度によって異なる |
17-4 PHステンレス鋼 | アレゲニー・テクノロジーズ、プレシジョン・キャストパーツ・コーポレーション | $25 – $35 | 価格は熱処理条件によって異なる |
カルボニル鉄粉 | BASF、ヘガネスAB | $15 – $25 | 粒子径と純度による |
M2工具鋼 | ボーラー・ウドホルム、日立金属 | $30 – $45 | 価格は合金元素によって変動する |
チタン Ti-6Al-4V | VSMPO-AVISMA、ATIメタルズ | $50 – $70 | 価格はフォームとグレードによって異なる |
コバルトクロム(CoCr)合金 | アルカムAB、カーペンター・テクノロジー | $80 – $100 | 医療および航空宇宙分野で高い需要 |
Inconel 625 | 特殊金属、ヘインズ・インターナショナル | $40 – $60 | コストは形状(パウダー、バーなど)によって異なる。 |
銅合金 90/10 | ヴィーランド・グループ、ミューラー・インダストリーズ | $10 – $20 | 価格は銅市場によって変動する可能性がある |
ニッケル718 | ATIメタルズ, VDMメタルズ | $50 – $70 | 価格はニッケル含有量に影響される |
アルミニウム合金6061 | カイザーアルミニウム、ハイドロ押出材 | $5 – $10 | 広く使用されているため、競争力のある価格設定 |
金属射出成形(MIM)の長所と短所を比較する
どの製造プロセスにも利点と限界があります。MIMの長所と短所を整理して、MIMの長所と短所を理解しましょう。
MIMの利点と限界
アスペクト | メリット | 制限事項 |
---|---|---|
デザインの柔軟性 | 複雑な形状の製造が可能 | 部品のサイズと重量による制限 |
素材の多様性 | 幅広い金属 | 高価な素材もある |
精度と公差 | 高精度を実現 | プロセスパラメーターの正確な制御が必要 |
生産量 | 大量生産に適したコスト効率 | 少量の場合は不経済 |
機械的特性 | 優れた機械的特性 | 特性は材料と工程管理に依存する |
表面仕上げ | 滑らかな仕上げが可能 | 非常に繊細な仕上げには後処理が必要な場合がある。 |
環境への影響 | 効率的な材料使用、廃棄物の削減 | 特に焼結にエネルギー集約的なプロセス |
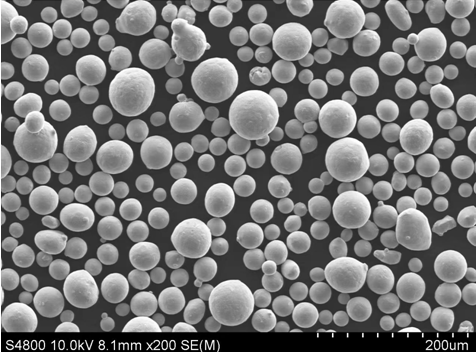
よくある質問
質問 | 回答 |
---|---|
金属射出成形(MIM)とは? | MIMは、金属粉末とプラスチック射出成形技術を組み合わせて複雑な金属部品を作る製造プロセスである。 |
MIMの主なメリットは? | MIMは、高精度、複雑な設計、大量生産に対するコスト効率、優れた機械的特性を提供する。 |
MIMを最も使用している産業は? | MIMは、医療、航空宇宙、自動車、家電、防衛、産業機械、エネルギー、宝飾などの産業で広く使用されている。 |
MIMに使用できる材料は? | MIMには、ステンレス鋼、工具鋼、チタン、ニッケル合金、コバルトクロムなど、さまざまな材料が使用できる。 |
MIMは従来の金属加工と比べてどうですか? | MIMは、従来の多くの方法よりも複雑な設計と高い精度を可能にする。しかし、少量生産ではコストが高くなる可能性がある。 |
MIMの限界とは? | MIMは、部品のサイズと重量、材料コストによって制限され、精密なプロセス制御を必要とする。 |
MIMは環境に優しいのか? | MIMは廃棄物を少なくして効率的に材料を使用するが、そのプロセス、特に焼結にはエネルギーを必要とする。 |
結論
金属射出成形(MIM) MIMは、複雑で高精度な金属部品の製造において比類のない利点を提供し、現代の製造業を変革する技術として際立っています。MIMの材料、プロセス、アプリケーション、および限界を理解することで、製造業者は、革新と業務の効率化を推進するための情報に基づいた意思決定を行うことができます。医療用インプラント、航空宇宙部品、複雑な産業用工具の製造など、MIMは多用途で効果的なソリューションを提供します。MIMの世界に飛び込み、この技術がいかに貴社の製造能力を新たな高みへと引き上げることができるかを探ってみてください。