概要 不活性ガス噴霧
不活性ガスアトマイズは、均一なサイズ、形状、優れた特性を持つ金属粉末を製造するために使用される魅力的な方法です。航空宇宙、自動車、積層造形などの産業で広く採用されているこの技術は、厳しい仕様を満たす高品質の粉末を保証します。しかし、不活性ガスアトマイゼーションとは一体何なのだろうか?このプロセスの複雑さを深く掘り下げ、様々な金属粉末モデルを探求し、その用途や仕様などを理解しましょう。
不活性ガスアトマイゼーションとは?
不活性ガスアトマイゼーションは、高圧不活性ガス(通常はアルゴンまたは窒素)を用いて溶融金属を微粉末にするプロセスである。金属はるつぼの中で溶かされ、溶融流は高速ガス流によって液滴に分解される。これらの液滴は、冷却されると微細な球状の粉末粒子に凝固する。不活性ガスを使用することにより、酸化やコンタミネーションを防ぎ、高純度の金属粉末の製造を保証します。
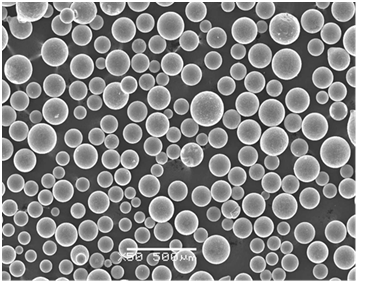
プロセス概要
について 不活性ガス噴霧 プロセスはいくつかの重要なステップに分けることができる:
- 溶ける: 金属はるつぼの中で、しばしば誘導加熱を使って溶かされる。
- アトマイゼーション: 溶融金属はノズルから注がれ、高速の不活性ガス流によって分解される。
- 固化: 金属液滴は冷えて固まり、粉末粒子になる。
- コレクション: 粉末は集められ、ふるいにかけられ、大きさによって分類される。
金属粉末の種類と特徴 不活性ガス噴霧
不活性ガスアトマイゼーションを用いて製造される金属粉末の種類は多岐にわたり、それぞれが特定の用途に合わせたユニークな組成と特性を持っています。ここでは、注目すべき10種類の金属粉末を紹介する:
金属粉モデル | 構成 | プロパティ | 特徴 |
---|---|---|---|
316Lステンレス鋼 | 鉄-クロム-ニッケル-モリブデン | 高耐食性、優れた延性 | 微細な球状粒子、均一な粒度分布 |
Inconel 625 | ニッケル-クロム-モリブデン | 高強度、耐酸化性 | 優れた高温性能 |
チタン Ti-6Al-4V | Ti-Al-V | 優れた強度対重量比 | 生体適合性があり、医療用インプラントに最適 |
AlSi10Mg | Al-Si-Mg系 | 良好な熱伝導性、軽量 | 高い強度重量比、良好な鋳造性 |
コバルト・クロム | コバルト-クロム | 高い耐摩耗性と耐食性 | 歯科および整形外科用インプラントに使用される生体適合性 |
H13工具鋼 | 鉄-クロム-モリブデン | 高硬度、優れた耐摩耗性 | 金型製作に最適 |
銅-Cr-Zr | Cu-Cr-Zr | 高い導電性 | 優れた強度と熱伝導性 |
マレージング鋼 | Fe-Ni-Co-Mo | 超高強度、優れた靭性 | 航空宇宙と工具に使用 |
アルミニウム6061 | Al-Mg-Si | 良好な機械的特性、溶接性 | 多用途、構造部品に使用 |
ニッケル718 | ニッケル-クロム-鉄-モリブデン | 高強度、耐食性 | 高温用途に適している |
不活性ガスアトマイズ金属粉末の用途
不活性ガスアトマイズされた金属粉末は、様々な産業で使用されており、それぞれが最適な性能を発揮するために、これらの材料のユニークな特性を活用しています。以下は、様々な用途を紹介する詳細な表です:
申し込み | 金属粉モデル | 産業 | メリット |
---|---|---|---|
付加製造 | チタン Ti-6Al-4V | 航空宇宙、医療 | 軽量、高強度、生体適合性 |
溶射コーティング | Inconel 625 | エネルギー, 海洋 | 高耐食性、優れた接着性 |
金属射出成形 | 316Lステンレス鋼 | 自動車、医療 | 複雑な形状、高精度、優れた耐食性 |
粉末冶金 | H13工具鋼 | 工具、自動車 | 高硬度、耐摩耗性、工具寿命の延長 |
電気部品 | 銅-Cr-Zr | エレクトロニクス | 高い導電性、熱管理 |
構造部品 | アルミニウム6061 | 航空宇宙、自動車 | 軽量、優れた機械的特性、加工の容易さ |
整形外科インプラント | コバルト・クロム | メディカル | 生体適合性、高い耐摩耗性 |
高温部品 | ニッケル718 | 航空宇宙、電力 | 高強度、耐酸化性、高温安定性 |
自動車部品 | マレージング鋼 | 自動車、航空宇宙 | 超高強度、強靭性、耐疲労性 |
熱交換器 | AlSi10Mg | HVAC、自動車 | 良好な熱伝導性、軽量 |
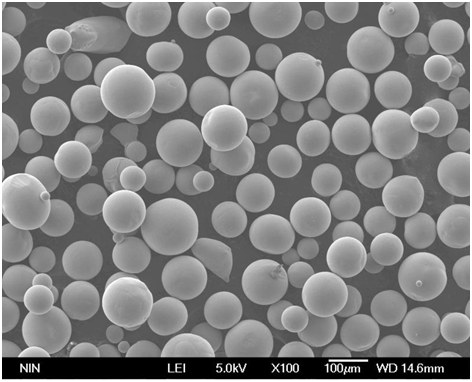
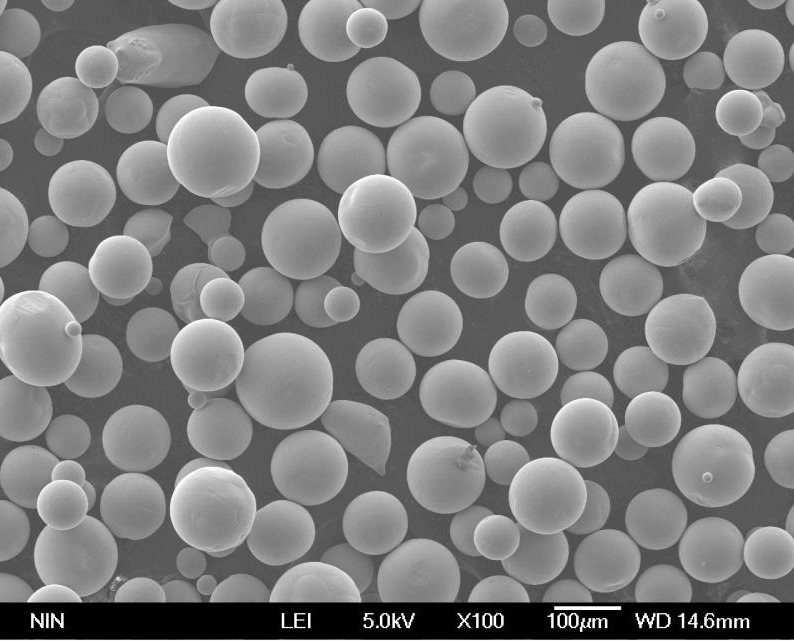
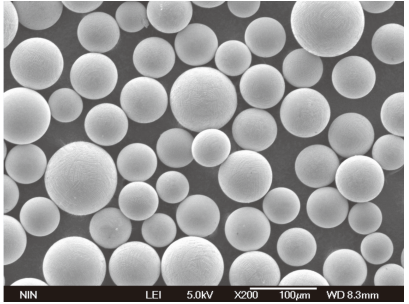
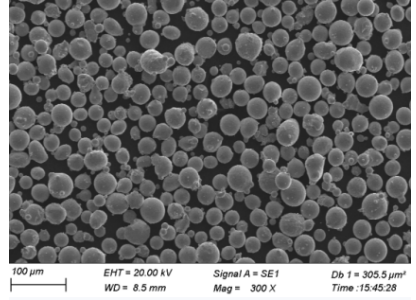

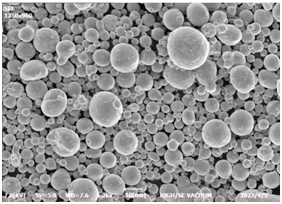
不活性ガスアトマイズ金属粉末の仕様、サイズ、等級および規格
金属粉に関しては、仕様、サイズ、等級、規格が安定した品質と性能を保証するために非常に重要です。ここに、これらの情報が記載された詳細な表を示します:
金属粉モデル | 粒子径範囲 | グレード | 規格 |
---|---|---|---|
316Lステンレス鋼 | 15-45 µm | ASTM F138 | ISO 5832-1 |
Inconel 625 | 15-53 µm | AMS 5666 | UNS N06625 |
チタン Ti-6Al-4V | 20-45 µm | グレード5 | ASMB348、AMS4928 |
AlSi10Mg | 10-50 µm | A360 | ISO 3522 |
コバルト・クロム | 15-45 µm | ASTM F75 | ISO 5832-4 |
H13工具鋼 | 20-63 µm | AISI H13 | ASTM A681 |
銅-Cr-Zr | 10-45 µm | C18150 | ASTM B937 |
マレージング鋼 | 15-53 µm | 18ニッケル(250) | AMS 6521 |
アルミニウム6061 | 20-63 µm | 6061-T6 | ASTM B209 |
ニッケル718 | 15-53 µm | AMS 5662 | UNS N07718 |
不活性ガス噴霧金属粉末の納入業者と価格詳細
金属粉末の調達には、適切なサプライヤーを見つけ、価格設定の詳細を理解することが不可欠です。ここに、いくつかの主要サプライヤーとおおよその価格表を示します:
サプライヤー | 金属粉モデル | 価格(USD/kg) | 追加情報 |
---|---|---|---|
ヘガネスAB | 316Lステンレス鋼 | 50-70 | グローバルリーダー、高品質の金属粉 |
サンドビック・マテリアル | Inconel 625 | 90-110 | 高性能合金に特化 |
GKN粉末冶金 | チタン Ti-6Al-4V | 200-250 | 豊富なポートフォリオ、高度な製造技術 |
LPWテクノロジー | AlSi10Mg | 30-50 | アディティブ・マニュファクチャリング用パウダーに注力 |
カーペンター・テクノロジー | コバルト・クロム | 100-130 | 高性能および特殊合金で知られる |
エラメ・グループ | H13工具鋼 | 25-40 | 様々な工具鋼と高性能合金の提供 |
ヴァーレ社 | 銅-Cr-Zr | 15-25 | ニッケルおよび銅合金の最大級の生産者 |
オベール&デュバル | マレージング鋼 | 70-90 | 高性能鋼と合金のエキスパート |
アメテック・スペシャリティ・メタル | アルミニウム6061 | 20-30 | 様々なアルミニウム合金を提供 |
ATIメタルズ | ニッケル718 | 80-100 | 高強度耐食合金 |
の利点と限界 不活性ガス噴霧
どんなプロセスにも長所と短所があり、不活性ガス噴霧も例外ではありません。以下に、利点と限界を比較するための比較表を示します:
アスペクト | メリット | 制限事項 |
---|---|---|
純度 | 高純度、最小限のコンタミネーション | 不活性ガスの供給が必要 |
粒子形状 | 球状粒子、優れた流動性 | サイズ分布に制限がある場合がある |
プロセス制御 | 粒子径と粒度分布の精密制御 | 高い初期設定費用 |
用途 | 幅広い用途に対応 | すべての金属が霧化に適しているわけではない |
スケーラビリティ | 大量生産に対応する拡張性 | エネルギー集約型プロセス |
一貫性 | 一貫した品質と再現性 | 定期的なメンテナンスと監視が必要 |
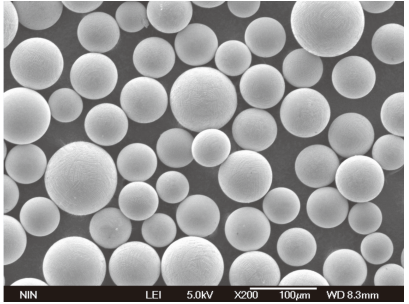
よくある質問
不活性ガス噴霧に関するよくある質問をいくつか取り上げ、疑問を解消してみましょう:
質問 | 回答 |
---|---|
不活性ガスアトマイゼーションの主な利点は何ですか? | 主な利点は、均一なサイズの高純度球状金属粉末の製造である。 |
この工程でよく使われる不活性ガスは? | アルゴンと窒素は最も一般的に使用される不活性ガスである。 |
この方法ですべての金属を霧化できますか? | すべての金属が適しているわけではなく、このプロセスは融点の高い金属に最適である。 |
この技術から最も恩恵を受ける産業は? | 航空宇宙産業、自動車産業、医療産業、付加製造産業が大きな恩恵を受ける。 |
不活性ガス噴霧と水噴霧の比較は? | 不活性ガスアトマイゼーションは、より純度が高く球状の粒子を提供するが、水アトマイゼーションは酸化や不規則な形状につながる可能性がある。 |
不活性ガス噴霧は環境に優しいか? | 特に水や他の反応性媒体を使用するプロセスと比較すると、比較的環境に優しい。 |
製造される典型的な粒子径は? | 粒子径は通常10~63μmで、材料とプロセスパラメーターによって異なる。 |
粉体の品質管理はどのように行われていますか? | 品質管理は、ガスフロー、温度、粒子捕集を注意深く監視することによって行われる。 |
アトマイズされた粉体には特別な保管条件がありますか? | はい、酸化や汚染を防ぐため、乾燥した不活性雰囲気で保管する必要があります。 |
不活性ガス噴霧技術にはどのような進歩がありますか? | 進歩には、プロセス制御の改善、新素材、拡張性の向上などがある。 |
結論
不活性ガスアトマイゼーションは、高品質の金属粉末を製造する上で極めて重要な技術であり、現代の製造業の厳しい要求に応えています。高純度で均一な球状粒子を製造するその能力は、様々な産業で不可欠なものとなっています。私たちがこのプロセスの革新と改良を続けることで、金属粉末製造の未来は驚くほど有望になり、高度な応用と材料特性の向上への新たな道が開かれるでしょう。
今度、なめらかな航空宇宙部品や頑丈な医療用インプラントに出くわしたら、それを可能にした溶融金属と不活性ガスの複雑なダンスを思い出してほしい。ハッピー・アトマイジング!