金属射出成形 (MIM)は、複雑で高精度の金属部品を製造するために使用される高度な製造プロセスです。この方法は、プラスチック射出成形の汎用性と金属の強度と完全性を兼ね備えています。MIMがどのように機能するのか、どのような用途に使われるのか、なぜ様々な産業でMIMが選ばれるようになったのか、興味がおありでしたら、このページをご覧ください。さっそく見ていきましょう!
概要 金属射出成形
金属射出成形(MIM)は、微粉末の金属をバインダー材と混合し、射出成形で成形・固化できる原料を作るプロセスです。成形された部品は、その後、バインダーを除去し、金属を緻密化するために焼結され、優れた機械的特性と複雑な形状を持つ最終製品が得られます。
MIMの主な利点:
- 高い精度と複雑なディテール
- 高い生産率
- 幅広い素材選択
- 材料廃棄の削減
- 優れた機械的特性
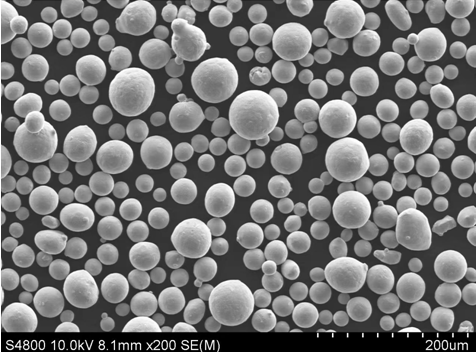
応用例 金属射出成形:
MIMは、自動車、医療機器、電子機器、航空宇宙、消費者向け製品など、さまざまな業界で広く使用されている。複雑な形状を高い精度で製造できるため、強力な機械的特性を必要とする小型で複雑な部品に最適です。
MIMに使用される金属粉末の種類
金属射出成形に関しては、使用される金属粉末の種類が最終製品の特性を決定する上で重要な役割を果たします。ここでは、MIMで一般的に使用される金属粉末を紹介します:
金属粉 | 構成 | プロパティ | 特徴 |
---|---|---|---|
ステンレススチール316L | Fe、Cr、Ni、Mo | 耐食性、高強度 | 医療および食品産業で一般的 |
ステンレス鋼 17-4 PH | Fe、Cr、Ni、Cu | 高強度、良好な耐食性 | 航空宇宙、自動車 |
カルボニル鉄 | Fe | 高純度、優れた磁気特性 | エレクトロニクス、自動車 |
タングステン | W | 高密度、高融点 | 航空宇宙、防衛用途に最適 |
チタン Ti-6Al-4V | Ti、Al、V | 高い強度対重量比、耐食性 | 医療用インプラント、航空宇宙 |
ニッケル合金 IN718 | Ni、Cr、Fe | 高温強度、耐食性 | ガスタービン、航空宇宙用 |
銅合金 C18150 | 銅、クロム | 高い電気伝導性と熱伝導性 | 電気部品に使用 |
工具鋼 M2 | Fe、C、W、Mo | 高硬度、耐摩耗性 | 切削工具、金型に使用 |
コバルト・クロム合金 | Co、Cr | 高強度、生体適合性 | 歯科、医療用インプラントで一般的 |
アルミニウム合金6061 | Al、Mg、Si | 軽量、優れた機械的特性 | 自動車、家電製品に使用 |
組成と特性 金属射出成形
MIM材料の組成と特性を理解することは、用途に適したタイプを選択する上で非常に重要です。ここでは、その詳細について説明する:
素材 | 構成 | プロパティ | 用途 |
---|---|---|---|
ステンレススチール316L | 16-18% Cr, 10-14% Ni, 2-3% Mo, Bal.Fe | 耐食性、優れた強度 | 医療機器、食品加工機器 |
ステンレス鋼 17-4 PH | 15-17% Cr, 3-5% Ni, 3-5% Cu, Bal.鉄 | 高強度、耐食性 | 航空宇宙、自動車部品 |
カルボニル鉄 | 鉄99 | 高純度、磁気特性 | エレクトロニクス、自動車部品 |
タングステン | 99%W | 高密度、熱安定性 | 航空宇宙、防衛機器 |
チタン Ti-6Al-4V | 90% Ti, 6% Al, 4% V | 軽量、高強度 | 医療用インプラント、航空宇宙部品 |
ニッケル合金 IN718 | 50-55% Ni, 17-21% Cr, Bal.Fe | 高温強度 | ガスタービン、航空宇宙部品 |
銅合金 C18150 | 98-99%Cu、0.5-1%Cr | 導電率、熱特性 | 電気コネクター、ヒートシンク |
工具鋼 M2 | 0.75-1.1% C, 4.0-6.0% Mo, 5.5-6.75% W, Bal.Fe | 硬度、耐摩耗性 | 切削工具、金型 |
コバルト・クロム合金 | Co60~65%、Cr27~30 | 強度、生体適合性 | 歯科用インプラント、整形外科用器具 |
アルミニウム合金6061 | 0.8-1.2% Mg, 0.4-0.8% Si, Bal.Al | 軽量、加工性 | 自動車部品、家電製品 |
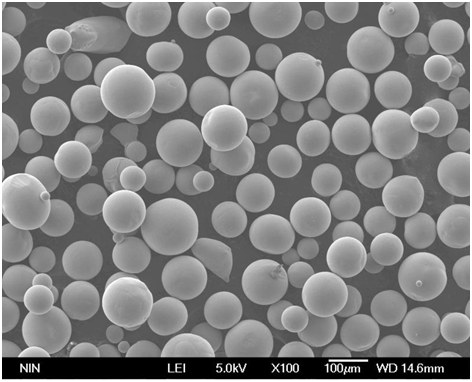
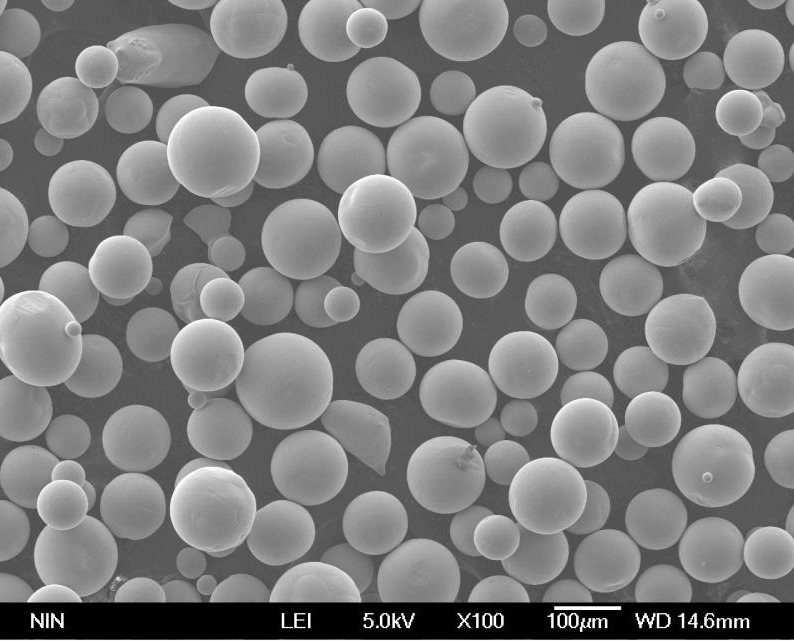
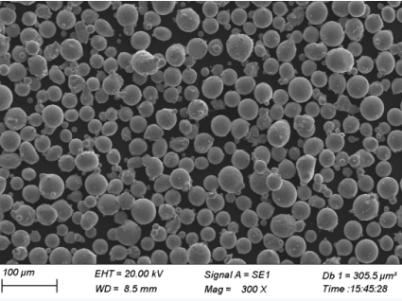
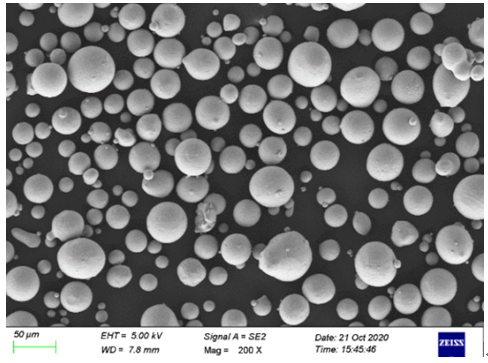
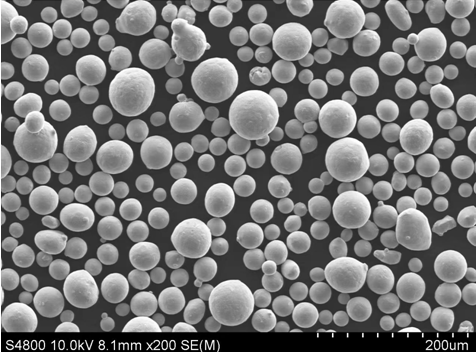
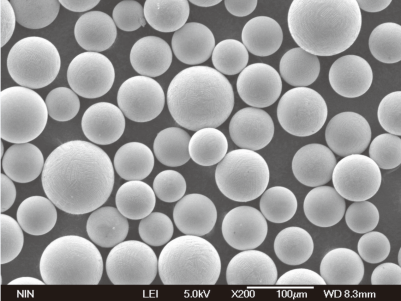
金属射出成形の用途
金属射出成形は汎用性があり、様々な産業で応用されています。主な用途を表にまとめました:
産業 | 用途 |
---|---|
自動車 | 燃料噴射装置部品、ターボチャージャー部品、ギアボックス |
医療機器 | 手術器具、矯正用ブラケット、インプラント |
エレクトロニクス | コネクター、センサー、携帯電話部品 |
航空宇宙 | タービンブレード、燃料ノズル、ファスナー |
消費者製品 | 時計ケース、メガネフレーム、金物工具 |
ディフェンス | 武器部品、徹甲弾 |
インダストリアル | 切削工具、ポンプ、バルブ |
MIMの仕様、サイズ、規格
最終製品が要求される性能基準を満たすためには、適切な仕様、サイズ、規格を選択することが重要です。ここでは、その詳細を紹介する:
仕様 | 説明 |
---|---|
ASTM規格 | ASTM F2885-11、ASTM B883-10 (MIM材料用) |
ISO規格 | ISO 22068, ISO 13320 粉体粒度分布測定用 |
サイズ | 複雑さに応じて、0.1mmから100mmまでのサイズに対応。 |
公差 | 通常、寸法の±0.3%だが、±0.05%まで厳しくできる。 |
表面仕上げ | 材料とプロセスに応じてRa 0.8~1.6マイクロメートルを達成可能 |
密度 | 通常、焼結後の密度は理論密度の95%から99%である。 |
サプライヤーと価格 金属射出成形
適切なサプライヤーを選択することは、MIMコンポーネントのコストと品質に大きく影響します。ここでは、注目すべきサプライヤーを推定価格詳細とともにご紹介します:
サプライヤー | 素材 | 価格 | 地域 |
---|---|---|---|
スミス・メタル・プロダクツ | ステンレススチール、チタン | 0.10ドル – グラムあたり0.50ドル | アメリカ |
高度な金属加工の実践 | さまざまな金属粉末 | 0.08ドル –グラム当たり0.45ドル | アメリカ |
パルマテック株式会社 | ステンレス鋼、工具鋼 | 0.12ドル –グラム当たり0.55ドル | アメリカ |
インドMIM | ステンレススチール、タングステン | 0.09ドル – グラムあたり0.50ドル | インド |
ARCグループ・ワールドワイド | ニッケル合金、銅合金 | 0.10ドル – グラムあたり0.60ドル | アメリカ |
CNIマニュファクチャリング | ステンレススチール、アルミニウム | 0.08ドル –グラム当たり0.48ドル | 中国 |
キネティクス・クライマックス | 工具鋼、コバルト合金 | 0.12ドル –グラム当たり0.58ドル | アメリカ |
CMGテクノロジーズ | ステンレススチール、チタン | 0.11ドル –グラム当たり0.52ドル | 英国 |
GKNシンターメタルズ | ステンレス鋼、工具鋼 | 0.09ドル –グラム当たり0.49ドル | ドイツ |
MPPイノベーション | さまざまな金属粉末 | 0.10ドル –グラム当たり0.47ドル | アメリカ |
金属射出成形の長所と短所を比較する
金属射出成形を検討する場合、その利点と限界を比較することが不可欠です。ここで比較してみましょう:
アスペクト | メリット | 制限事項 |
---|---|---|
精密 | 高い寸法精度、複雑な形状 | 中小部品に限定 |
材料効率 | 材料の無駄が少なく、粉体を効率的に使用 | 高い初期材料費 |
機械的特性 | 優れた特性を持つ丈夫で耐久性のある部品 | 焼結工程で気孔が生じる可能性がある |
生産量 | 大量生産に適している | 少量生産ではコスト効率が悪い |
複雑さ | 非常に複雑な形状の製造が可能 | 特定の部品サイズと形状に限定 |
表面仕上げ | 優れた表面仕上げが可能 | 特定の用途には二次加工が必要な場合がある。 |
汎用性 | 幅広い素材に対応 | 従来の方法に比べてリードタイムが長い |
コスト | 大量生産に適したコスト効率 | 高額な初期金型費用とセットアップ費用 |
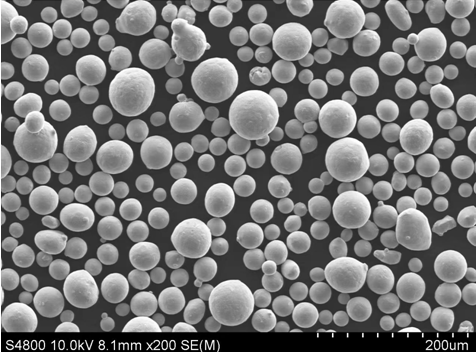
よくある質問
Q: 金属射出成形(MIM)とは何ですか?
A: 金属射出成形は、金属を組み合わせて成形する製造プロセスである。
粉末をバインダーで固め、射出成形技術を使って非常に精密で複雑な金属部品を製造する。
Q: MIMにはどのような材料が使用できますか?
A: MIMには、ステンレス鋼、工具鋼、チタン合金、タングステン、ニッケル合金、銅合金など、さまざまな材料が使用できる。
Q:MIMの主な利点は何ですか?
A: 主な利点は、高精度、複雑な形状、高い生産速度、材料の無駄の削減、優れた機械的特性などである。
Q: MIMはどのような産業でよく使われていますか?
A: MIMは、自動車、医療機器、電子機器、航空宇宙、消費者製品、防衛、産業用途で使用されている。
Q: MIMで達成可能な典型的なサイズと公差は?
A: サイズは0.1mmから100mmまであり、公差は一般的に寸法の±0.3%前後、場合によっては±0.05%まで厳しい。
Q: 焼結プロセスはMIM部品にどのような影響を与えますか?
A: 焼結によってバインダーが除去され、金属が緻密化されるため、気孔が生じる可能性があるが、部品の機械的特性も大幅に向上する。
Q: MIMは少量生産に費用対効果がありますか?
A: いいえ、MIMは一般的に、初期工具とセットアップのコストが高いため、少量生産では費用対効果が高くありません。むしろ大量生産に向いています。
Q: MIMは高い表面仕上げの部品を製造できますか?
A: はい、MIMは優れた表面仕上げを実現できますが、用途によっては最適な結果を得るために二次的な仕上げ工程が必要になる場合があります。
Q: MIMで製造できる形状に制限はありますか?
A: MIMは非常に複雑な形状を作ることができるが、特定の部品サイズに限られており、非常に大きな部品には適さない場合がある。
Q:MIM部品のサプライヤーを選ぶ際に考慮すべきことは何ですか?
A: 材料に関する専門知識、生産能力、価格設定、地域的な立地、高品質のMIM部品を供給してきたサプライヤーの実績などの要素を考慮してください。
結論
金属射出成形は、複雑で高精度の金属部品を製造するための多くの利点を提供する汎用性と非常に効率的な製造プロセスです。自動車から航空宇宙まで、その用途は広大かつ多様であり、現代の製造業における貴重な技術となっています。MIMの材料の種類、仕様、および利点を理解することで、このプロセスが特定のニーズに適しているかどうかをよりよく評価することができます。
MIMをその精度、材料効率、複雑な形状の製造能力のいずれで検討しているかにかかわらず、この革新的なプロセスが多くのことを提供することは明らかです。技術と材料が進歩し続けるにつれて、金属射出成形の可能性はますます大きくなり、製造と設計の新たな可能性が開かれるでしょう。